Restoring Worn-Out Components with Additive Manufacturing (AM) Technology: A Cost-Effective Solution for Industrial Repair
Table of Contents
1. Introduction: The Growing Demand for Component Restoration in Industrial Sectors
In today’s industrial landscape, equipment reliability and operational uptime are more critical than ever. Across sectors like aerospace, automotive, energy, and manufacturing, the failure of a single component can lead to costly downtime, production delays, and even safety risks. Traditional methods of component repair or full replacement are often time-intensive, expensive, and limited by supply chain constraints.
This is where Additive Manufacturing (AM)—commonly referred to as metal 3D printing—is reshaping the way worn-out components are restored. Rather than scrapping valuable parts, industries can now repair, rebuild, and reinforce components with precision-engineered metal layers, restoring them to like-new condition or even enhancing their original properties.
The Traditional Repair Challenge
Repair Method | Limitations |
---|---|
Welding/Brazing | Inconsistent quality, heat distortion, limited to surface repair |
Machining | Material waste, not suitable for complex geometries |
Part Replacement | Long lead times, high costs, especially for custom or legacy components |
Why Additive Manufacturing is a Game-Changer
- Restores parts to original specifications or better
- Minimizes downtime with faster turnaround times
- Reduces cost compared to procuring new components
- Eco-friendly by extending the lifecycle of parts
As industrial maintenance evolves, component restoration via AM is becoming a strategic tool for cost control, sustainability, and operational efficiency.
2. Market Trends: How Additive Manufacturing is Transforming Equipment Maintenance
The adoption of metal additive manufacturing is surging, not only for prototyping and production but also for repairing high-value, mission-critical components. According to industry reports, the global market for 3D printing in maintenance and repair is growing at over 20% CAGR, with increasing applications in aerospace, automotive, oil & gas, and power generation.
Key Statistics
Metric | Value |
---|---|
Global AM Repair Market Size (2023) | $1.2 Billion+ |
Expected Market Size by 2028 | $3.5 Billion |
Average Cost Savings per Repaired Component | 30%–70% |
Reduction in Lead Time Compared to New Parts | Up to 90% |
Industries Leading Adoption
- Aerospace: Repairing turbine blades, combustion chambers, and brackets
- Automotive: Restoring molds, dies, and engine components
- Oil & Gas: Refurbishing impellers, pump housings, and valves
- Industrial Manufacturing: Rebuilding worn jigs, fixtures, and tools
Emerging Trends in AM Repair
- Digital Twin Integration: Scanning worn parts to create digital models enables precise restoration.
- On-Demand Spare Parts: Companies are building digital warehouses of printable parts.
- Sustainable Repair Models: Using AM reduces scrap and contributes to circular manufacturing.
🌐 Want to learn more about how additive manufacturing supports industrial transformation? Visit Metal3DP’s metal 3D printing solutions.
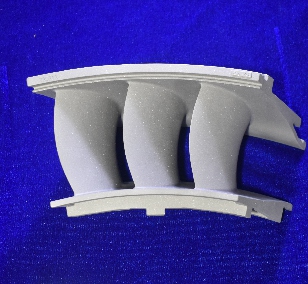
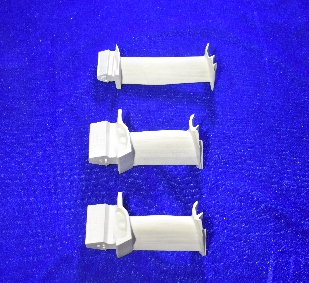
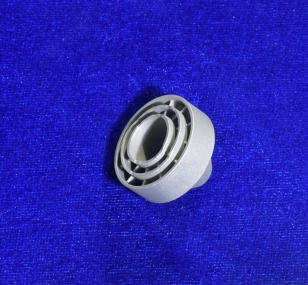
3. Key Benefits of Using Additive Manufacturing for Repair Applications
Additive manufacturing offers a paradigm shift from reactive maintenance to proactive, precision-based restoration. For B2B buyers and industrial stakeholders, the advantages go far beyond basic repair.
✅ Major Benefits of AM-Based Component Restoration
- Lower Downtime & Maintenance Costs
- Avoid long procurement cycles for replacement parts
- Quick turnaround with local or in-house AM repair capacity
- Restoration of Obsolete or Discontinued Parts
- Rebuild components no longer available from OEMs
- Extend the usable life of expensive equipment
- Superior Mechanical Properties
- Metallurgical bonding ensures high strength and durability
- Multi-material capabilities allow for enhanced wear resistance
- Precision & Complexity
- Rebuild parts with complex geometries and tight tolerances
- Ideal for aerospace and medical components
- Sustainability & Material Efficiency
- Minimal material waste compared to subtractive methods
- Supports circular manufacturing models
🛠 Real-World Examples of AM Repair Benefits
Application | Traditional Method | AM-Based Restoration | Cost Savings | Lead Time Reduction |
---|---|---|---|---|
Turbine Blade | Replacement | Laser Metal Deposition | 60% | 80% |
Pump Impeller | Machining | Directed Energy Deposition | 45% | 75% |
Injection Mold | Welding | Powder Bed Fusion | 35% | 60% |
🏭 Looking for a reliable AM partner? Learn more about Metal3DP’s full capabilities in metal 3D printing equipment and powder technology.
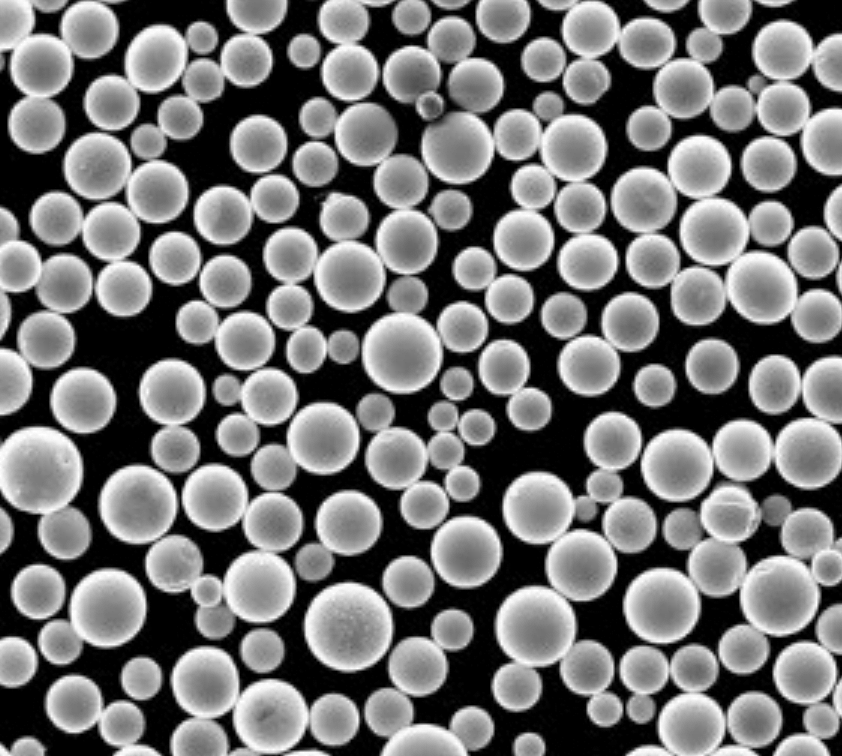
4. Top Industries Leveraging AM for Component Restoration
Additive Manufacturing (AM) is not limited to prototyping or small-batch custom parts. Today, it’s a mainstream industrial solution for restoring worn or damaged components across a range of critical sectors. Below is an industry-specific look at how AM is transforming maintenance, repair, and overhaul (MRO) workflows.
🛫 Aerospace Industry
The aerospace sector was one of the earliest adopters of AM for restoration due to its need for tight tolerances, lightweight parts, and high performance under extreme conditions.
- Common Restored Components:
- Turbine blades
- Engine combustion liners
- Fuel nozzles
- Brackets and mounts
- Benefits:
- Maintain airworthiness of critical parts
- Reduce aircraft downtime
- Eliminate the need to scrap expensive components
🚗 Automotive Industry
OEMs and Tier 1 suppliers are using AM to rebuild tooling, molds, and engine parts, especially in motorsport and high-performance applications.
- Common Restored Components:
- Die-casting molds
- Engine blocks and cylinder heads
- Tooling inserts and jigs
- Benefits:
- Extend tool life
- Improve thermal performance through conformal cooling
- Quick turnaround during production cycles
⚙️ Industrial Manufacturing
From robotics to heavy equipment, AM supports just-in-time maintenance by enabling the restoration of worn-out factory components.
- Common Restored Components:
- Gearboxes
- Shafts
- Rollers
- Bearings housings
- Benefits:
- Reduce spare part inventory
- Restore obsolete parts
- Improve mechanical properties with custom alloys
⚡ Energy Sector (Oil & Gas, Power Generation)
In harsh environments where wear and corrosion are common, AM helps rebuild high-value parts with corrosion-resistant alloys, increasing uptime and safety.
- Common Restored Components:
- Impellers, valves, diffusers
- Turbine casings
- Pump housings
- Benefits:
- Reduce replacement costs
- Enhance wear and corrosion resistance
- Reduce lead times for large, complex components
5. Why Additive Manufacturing Outperforms Traditional Repair Methods
Traditional component repair methods like welding, machining, and brazing have served engineers for decades—but they have limitations when it comes to precision, repeatability, and material integrity. In contrast, AM-based repair techniques offer a data-driven, digitally controlled process that delivers consistent, high-quality results.
⚖️ Side-by-Side Comparison: AM vs. Traditional Repair
Factor | Traditional Repair Methods | Additive Manufacturing Repair |
---|---|---|
Precision and Tolerance | Limited | Ultra-precise (micron-scale) |
Heat-Affected Zone | Large, risk of warping | Minimal, localized heating |
Material Compatibility | Limited | Wide range of alloys |
Surface Finish | May require extensive machining | Near-net-shape possible |
Design Flexibility | Low | High (complex geometries) |
Data Traceability | Manual Documentation | Digital Workflow & QA Logs |
🔧 Metallurgical Bonding Advantages
Unlike cladding or welding, AM processes often achieve metallurgical bonding between the deposition and the substrate. This leads to:
- Higher fatigue life
- Better mechanical integrity
- Seamless material integration
🧪 Enhanced Properties Through Alloy Selection
AM allows engineers to tailor the material composition during the repair process. For example:
- Use of Ti6Al4V for aerospace parts with high strength-to-weight ratio
- CoCrMo alloys for wear-resistant energy components
- Nickel-based superalloys for high-temperature turbine repairs
Met3DP offers a full catalog of high-performance metal powders optimized for various repair applications. These include:
- Ti, TiAl, TiNbZr, and TiTa alloys
- CoCrMo, stainless steels, and superalloys
- Custom alloy development for industry-specific needs
🔗 Explore Met3DP’s product portfolio of high-quality metal powders for industrial applications.
6. Why Choose Metal3DP for Additive Component Restoration
With decades of expertise and a full-stack AM ecosystem, Metal3DP stands out as a trusted partner for industrial component restoration. Whether you’re a maintenance engineer, procurement manager, or OEM distributor, Metal3DP offers the technology, materials, and support to make AM-based repair practical and profitable.
🏭 What Sets Metal3DP Apart
Feature | Metal3DP Advantage |
---|---|
🇨🇳 Headquartered in Qingdao, China | Global reach with local expertise |
🖨️ Large-Format SEBM Printers | High precision, high volume, and high repeatability |
⚗️ Advanced Powder Production | PREP + Gas Atomization = Spherical powders with excellent flowability |
🧪 Custom Alloy Development | Tailored solutions for aerospace, medical, and energy sectors |
🔍 Application Consulting | End-to-end support from scanning to post-processing |
💡 Metal3DP Capabilities Snapshot
- Additive Manufacturing Equipment: SEBM and PBF systems built for industrial scale
- Metal Powders: Titanium alloys, superalloys, stainless steels, and custom blends
- Repair Services: Engineering support for reverse engineering and component restoration
- Quality Assurance: Fully traceable production with ISO-grade standards
🧠 Learn more about Metal3DP’s industry-leading equipment and powder solutions on the Printing Methods page.
📈 Partnering for Growth
Metal3DP collaborates with:
- Aerospace OEMs on turbine blade restoration
- Automotive suppliers for tool and mold life extension
- Energy companies on high-wear component rebuilds
Whether you’re looking to build in-house AM capability or outsource restoration, Metal3DP is your strategic partner.
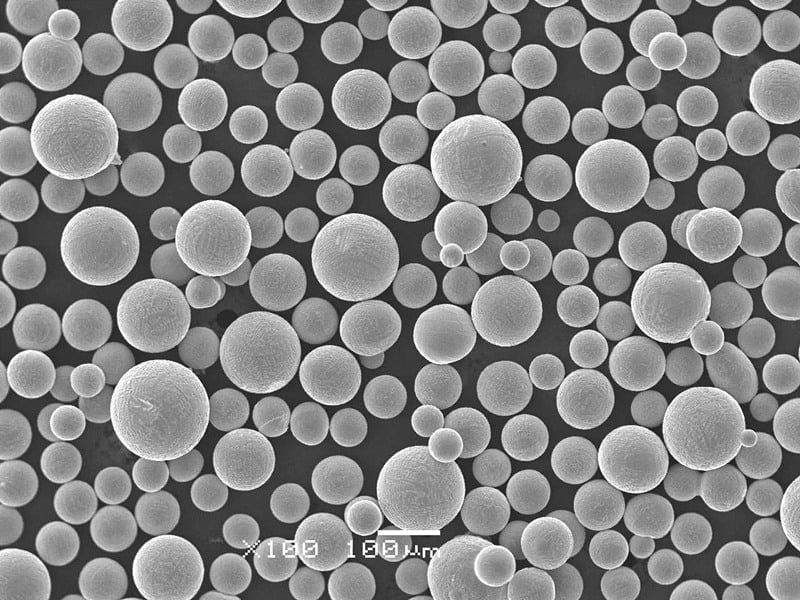
7. How to Implement AM-Based Repairs in Your Supply Chain
For many B2B companies—especially in aerospace, automotive, and industrial sectors—the shift to AM-based component restoration isn’t just a technical upgrade; it’s a strategic move to reduce downtime, control costs, and improve sustainability.
Metal3DP makes it easy for OEMs, MROs, and industrial maintenance teams to integrate AM into their repair workflows. Whether you’re outsourcing to a service provider or investing in in-house capabilities, here’s how the process works.
🛠 Step-by-Step AM Repair Workflow
Step | Description | Tools & Tech |
---|---|---|
1. Damage Inspection | Identify wear or failure zones using NDT or CT scanning | X-ray CT, 3D scanning |
2. Digital Modeling | Create or modify CAD models using reverse engineering | CAD software, digital twin |
3. Material Selection | Choose optimal alloy based on application & performance | Ti6Al4V, CoCrMo, Ni alloys |
4. Additive Repair Printing | Rebuild worn areas layer by layer using SEBM/PBF | Metal3DP printers |
5. Post-Processing | Heat treatment, CNC machining, surface finishing | HIP, EDM, polishing |
6. QA & Certification | Inspect and validate to ISO, ASTM or OEM standards | CMMs, metallurgical testing |
🧩 Choosing the Right Repair Modality
Different AM technologies offer unique benefits for repairs. Metal3DP supports the following methods:
Method | Best Use Cases | Advantages |
---|---|---|
SEBM (Selective Electron Beam Melting) | Aerospace, medical implants | High-density, fast build, minimal residual stress |
PBF (Powder Bed Fusion) | Automotive, molds, dental | Fine detail, high accuracy |
DED (Directed Energy Deposition) | Large components, energy sector | Ideal for adding material to existing parts |
🔍 Want to learn which AM method is best for your components? Visit our overview of AM printing methods to compare capabilities.
📦 How to Get Started with Metal3DP
- Contact our engineering team for a free consultation
- Send your worn components or 3D scans for evaluation
- Choose from our catalog of industrial-grade printers and powders
- Start restoring high-value parts with confidence
8. Success Stories: Real-World Use Cases of AM in Component Repair
Additive manufacturing for repair isn’t just theoretical—it’s actively transforming maintenance programs in some of the world’s most demanding industries. Here are real-world examples of how companies have leveraged Metal3DP’s technology for high-impact results.
✈️ Aerospace: Turbine Blade Repair
Challenge:
A Tier 1 aerospace supplier faced high costs and long lead times for turbine blade replacements (Ti6Al4V alloy).
Solution:
Using Metal3DP’s SEBM technology and high-purity Ti6Al4V powder, the worn edges of the blade were rebuilt layer by layer, achieving metallurgical bonding and OEM-spec geometry.
Results:
- 70% cost savings
- 85% reduction in downtime
- 100% pass rate in quality inspection
⚙️ Automotive: Mold Core Refurbishment
Challenge:
An automotive OEM needed to extend the life of injection mold cores that suffered thermal cracking and wear.
Solution:
Metal3DP provided CoCrMo spherical powder, and the customer used PBF printing to restore the damaged regions. Post-processing included polishing and CNC finishing.
Results:
- Increased mold life by 40%
- Reduced retooling costs
- Improved thermal performance
⚡ Oil & Gas: Pump Impeller Restoration
Challenge:
A refinery required urgent repair of a custom impeller. OEM replacement would take 12 weeks and cost over $40,000.
Solution:
Metal3DP reverse-engineered the impeller, printed the damaged region using Ni-based superalloy, and delivered it within 10 days.
Results:
- Saved over $25,000
- Avoided shutdown penalties
- Improved corrosion resistance
📘 Ready to explore more case studies or discuss your project? Visit our main website to get in touch with our application team.
9. FAQs: Common Questions About Using AM for Industrial Component Repair
Below are frequently asked questions from industrial buyers, engineers, and procurement teams considering additive manufacturing for component restoration.
❓ What types of damage can be repaired using AM?
- Surface wear and erosion
- Cracks and pitting
- Dimensional degradation
- Missing material due to impact or corrosion
❓ Which materials are compatible with AM repair?
Metal3DP offers powders for:
- Titanium alloys (Ti6Al4V, TiAl, TiNbZr, TiTa)
- Stainless steels (316L, 17-4PH)
- Nickel-based superalloys
- Cobalt-chromium (CoCrMo)
- Aluminum alloys (AlSi10Mg)
❓ What part sizes can be restored?
Our SEBM printers support large-format builds and complex geometries, making them suitable for:
- Small precision tools (medical, dental)
- Mid-size automotive molds and dies
- Large aerospace and energy components
❓ How long does the repair process take?
Typical turnaround times range from:
- 48–72 hours for small parts
- 1–2 weeks for complex or custom components
- Same-day service available for emergency cases (contact us)
❓ How does AM repair affect part strength?
AM repairs often restore or exceed original mechanical properties when using proper post-processing and heat treatment. Metal3DP ensures ISO and ASTM compliance across all projects.
🏭 Curious about Metal3DP’s full-scale powder production capabilities? Read how our advanced powder-making systems ensure flowability, purity, and consistent particle morphology.
🏁 Conclusion & Call to Action
As industries face rising maintenance costs, supply chain disruptions, and sustainability demands, Additive Manufacturing for component restoration is no longer optional—it’s a competitive necessity.
Metal3DP empowers OEMs, MROs, and industrial buyers to:
✅ Restore high-value parts with precision
✅ Reduce downtime and operational risk
✅ Extend tool and equipment life cycles
✅ Use optimized powders and world-class AM equipment
✅ Build a smarter, more sustainable supply chain
📞 Ready to Transform Your Repair Strategy?
Visit Metal3DP.com or contact our team to:
- Schedule a component evaluation
- Request a quote for your next repair project
- Consult with our materials and AM experts
🔗 Internal Links Summary:
Anchor Text | Target URL |
---|---|
Metal3DP’s metal 3D printing solutions | https://met3dp.com/metal-3d-printing/ |
Learn more about Metal3DP’s full capabilities | https://met3dp.com/about-us/ |
High-quality metal powders | https://met3dp.com/product/ |
Overview of AM printing methods | https://met3dp.com/printing-methods/ |
Main website | https://met3dp.com/ |
Share On
MET3DP Technology Co., LTD is a leading provider of additive manufacturing solutions headquartered in Qingdao, China. Our company specializes in 3D printing equipment and high-performance metal powders for industrial applications.
Inquiry to get best price and customized Solution for your business!
Related Articles
About Met3DP
Recent Update
Our Product
CONTACT US
Any questions? Send us message now! We’ll serve your request with a whole team after receiving your message.
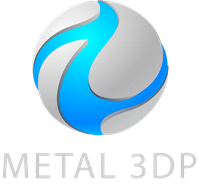
Metal Powders for 3D Printing and Additive Manufacturing