Additive Manufacturing Copper
Table of Contents
additive manufacturing copper demonstrate expanding use across additive manufacturing methods, enabling fabrication of highly conductive parts with useful mechanical performance. As one of few metal options across powder bed fusion, binder jetting and directed energy deposition processes, understanding key powder attributes promises growth in applications.
Overview of additive manufacturing copper
Additive manufacturing using copper promises:
- Electrical and thermal conductivity exceeding other metals
- Density similar to common engineering alloys
- Improved ductility over materials like steel or nickel
- Range of alloying choices to tune properties
- Antimicrobial behavior securing hygienic use
- Recyclability supporting sustainability goals
Parts with fine details, complex geometries and lightweight conformal channels become manufacturable with properties tailored to thermal, electrical or mechanical stresses through optimal alloy and process selection.
Potential applications span electronics cooling, radio frequency components, casting molds with conformal cooling, and custom implants. As additive platforms scale up build volumes in copper materials, adoption will increase across sectors.
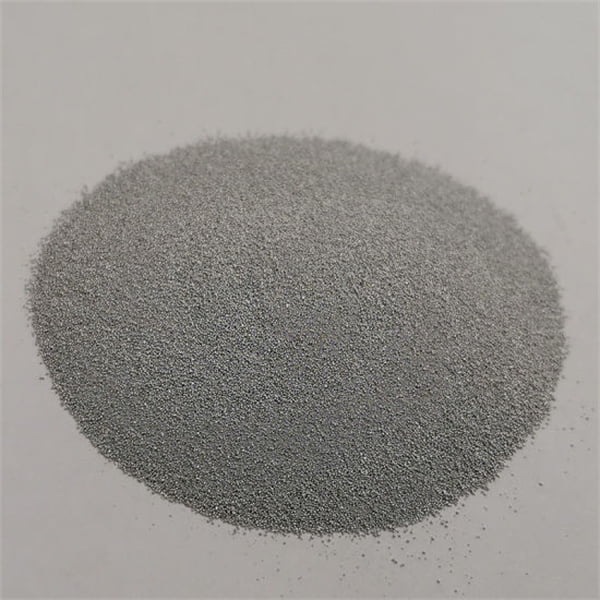
Types of Copper Powder
Various powder feedstock types are available based on production method, characteristics and alloy family:
Type | Description | Particle Size | Morphology | Apparent density |
---|---|---|---|---|
Gas atomized | Inert gas atomized elemental copper | 20-63 μm | Rounded, spherical | 3-4 g/cc |
Water atomized | Water broken copper particles | 45-150 μm | Irregular, porous | ∼2 g/cc |
Electrolytic | Copper powder from electrolytic process | 5-200 μm | Flaky, spongy | 1-3 g/cc |
Alloy powders | Prealloyed gas-atomized CuCr1Zr, CuCo2Be etc. | 20-45 μm | Near spherical | 3-4 g/cc |
Gas atomized and alloy powders have flowability and shape characteristics suitable for AM needs.
additive manufacturing copper Composition
Various copper material options for additive:
Material | Alloy Additions | Characteristics |
---|---|---|
Pure copper | – | High conductivity, soft |
Brass | 15-45% Zn | Stronger, machinable alloy |
Bronze | 5-12% Sn, | Improved strength with some lead bronzes |
Copper-nickel | 10-30% Ni | Controlled expansion, good corrosion performance |
Trace elements like Pb, Fe, Sb help modify properties and processability. Specific compositions are tuned for desired electrical, thermal, mechanical performance permutations.
Properties of additive manufacturing copper
Novel copper AM capabilities build on useful physical and functional attributes:
Physical Properties
Property | Pure Copper | Value | Unit |
---|---|---|---|
Density | – | 8.9 | g/cm<sup>3</sup> |
Melting Point | – | 1085 | °C |
Thermal Conductivity | – | 385 | W/m-K |
Electrical Resistivity | – | 1.72 x 10<sup>-6</sup> | ohm-cm |
CTE | – | ∼17 | μm/m-K |
Density lies between aluminum and mild steels while exceptional conductivity exceeds alternative metal options.
Mechanical Properties
Varying with alloying additions after heat treatment:
Property | Yield Strength | Tensile Strength | Elongation | Hardness |
---|---|---|---|---|
Pure copper | ∼215 MPa | ∼280 MPa | ∼35% | ∼60 HB |
Brass | ∼450 MPa | ∼650 MPa | ∼35% | ∼150 HB |
Bronze | ∼275 MPa | ∼480 MPa | ∼15% | ∼120 HB |
Copper-nickel | ∼550 MPa | ∼750 MPa | ∼30% | ∼180 HB |
Functional Attributes
Parameter | Rating | Units |
---|---|---|
Electrical conductivity | Excellent | %IACS |
Thermal conductivity | Excellent | W/m-K |
Corrosion resistance | Moderate | – |
Biofunctionality | Antimicrobial efficacy | – |
Thermal fatigue resistance | Good | Cycles |
Damping properties | Very good | – |
These characteristics help target electrical contacts, leadframes, heat exchangers etc. leveraging AM nimbleness.
Production of additive manufacturing copper
Commercial feedstock powder production setup:
1. Melting – Pure copper cathode is induction melted in controlled atmosphere
2. Atomization – High pressure inert gas breaks up molten stream into fine droplets
3. Powder cooling and collection – Powder particle shaping and solidification
4. Sieving – Multi-step classification yields application-specific fractions
5. Packaging – Sealed containers with inert gas retention ensures storage stability
Specialty alloys undergo vacuum induction melting before atomization. Scrap recycling also provides suitable powder.
additive manufacturing copper Applications
Emerging application spaces benefitting from copper AM capabilities:
Electronics
Excellent thermal conductivity aids heat removal from packages while minimizing expansion issues. Features like customizable printed heat sinks or shields become feasible.
Electrical components
Low resistivity allows lightweight inductors, busbars, RF shielding manufactured through additive manufacturing.
Wear parts
Surface roughness improvements through AM support abrasion resistance in applications like bearings, bushings etc.
Automotive
Combined strength-ductility benefits thin-wall heat exchanger geometries needed for electric vehicle battery thermal management.
Aerospace
Learnings from rocket engine chamber jacketing carry over into aircraft heat rejection systems like vapor chambers.
Biomedical
Antimicrobial behavior encourages customized implants and prosthetics tailored to biological interfaces.
additive manufacturing copper Specifications
Key powder characteristics and metrics around copper for AM:
Grades
Per MPIF standard 115 for additive manufacturing powders:
Type | Size Range | Particle Shape | Apparent Density | Flow Rate |
---|---|---|---|---|
Ultrafine | 15-25 μm | Rounded | ≥ 2.5 g/cc | Fair |
Very Fine | 25-45 μm | Rounded | ≥ 3 g/cc | Good |
Fine | 45-75 μm | Rounded | ≥ 3.5 g/cc | Good |
Relatively Coarse | 75-100 μm | Rounded | ≥ 4 g/cc | Very good |
Smaller sizes offer better resolution and surface finish while larger particles provide build rate economies.
Standards of additive manufacturing copper
Key powder test protocols include:
- MPIF 115 – Additive Manufacturing for Powder Metallurgy Structural Parts
- ASTM B243 – Standard Test Method for Powder Metallurgy Copper and Copper Alloy Powders and Compacts
- ISO 4490 – Determination of particle size distribution for metal powders by laser diffraction
- BSI PAS 139 – Specification for Additively Manufactured parts in Metals
These help benchmark feedstock quality for optimal printed part reproducibility and reliability.
additive manufacturing copper Pricing
Representative pricing, 2023:
Type | Price |
---|---|
Gas Atomized | $12-18 per kg |
Water Atomized | $8-12 per kg |
Specialty Alloy | $30-50 per kg |
Higher density distribution, smaller and uniform particles command premium over irregular morphologies and coarse sizes.
Pros and Cons
Advantages
- Very high electrical and thermal conductivity
- Useful combination of strength and ductility
- Antimicrobial surface characteristics
- Excellent biofunctionality and biocompatibility
- Dimensional stability across operating temperatures
- Faster heat transfer from thin sections
- Suitable for food, liquid, gas contact
Disadvantages
- Inferior high temperature capability than ferrous alloys
- Lower hardness than iron, cobalt or nickel alloys
- Heavy compared to lightweight metals like aluminum, magnesium
- Higher material costs than steel counterparts
- Sensitive to hydrogen embrittlement in certain conditions
Understanding unique strengths and limitations promises optimal application across industries where copper unlocks value.
additive manufacturing copper Suppliers
Leading global sources offering copper powder for additive manufacturing:
Company | HQ Location |
---|---|
Sandvik Osprey | UK |
Makin Metal Powders | UK |
Höganäs | Sweden |
ECKA Granules | Germany |
Kymera International | USA |
Shanghai CNPC | China |
These established metal powder producers now cater growing copper demand from industrial 3D printing markets with customized grades. Bespoke toll processing services augment capacity scalability for copper AM powder feedstock.
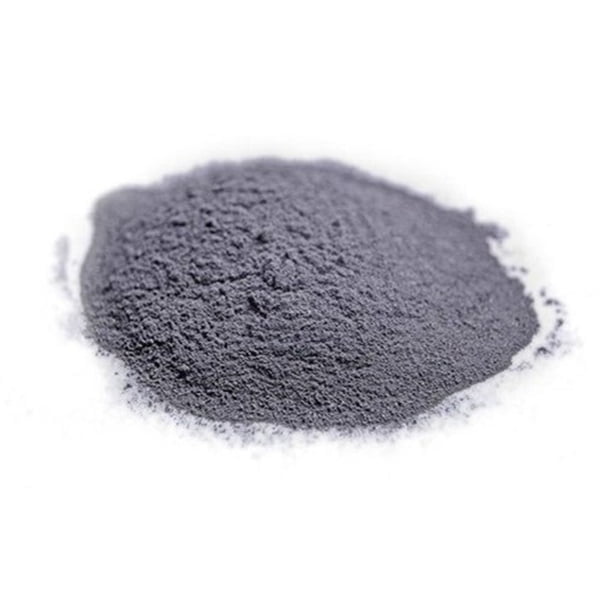
FAQs
Question | Answer |
---|---|
What is meant by additive manufacturing copper? | Building up components from metallic copper powder as part of layered powder bed fusion or directed energy deposition |
What different types of copper powder are available for AM? | Gas-atomized, water-atomized and electrolytic along with prealloyed brass, bronze powders |
Why choose copper material for additive manufacturing? | To exploit excellent electrical and thermal conductivity while retaining useful strength |
What particle size copper powder is optimal for laser AM processes? | Typically the very fine grade from 25 to 45 microns size |
What postprocessing steps are needed on as-printed copper components? | Hot isostatic pressing helps achieve ∼100% density followed by heat treatment for optimal microstructure |
Does UNS standards cover copper grades for additive manufacturing? | Yes, UNS C10100 for pure copper among others like UNS C87850 for CuCr1Zr alloy |
How to improve surface finish of additively manufactured copper parts? | Combination of fine powder sizes, optimized layer thicknesses, post-machining and electroplating |
Are there any special safety precautions while handling copper powder? | Yes, appropriate personnel protective equipment recommended along with measures avoiding airborne fine powder |
Summary
Additive manufacturing markedly expands production flexibility for copper components, liberating new geometries and enabling lightweight multifunctional assemblies across electronics, electrical and thermal management domains. As powder quality endorsement backs reliable mechanical performance on par with conventional routes, larger mission-critical parts will adopt AM productivity at commercial scales.
New alloy variants extrapolated from promising CuCrZr and CuCo capabilities point to uncharted property combinations for space applications. Meanwhile high-value sectors like medical leverage biofunctionality driving customized heat exchangers and implants via AM construction. Ubiquitous copper thereby enters newer terrain on the back of powder bed fusion and directed energy deposition versatility as utilities harness shape complexities with useful conductivities.
Share On
MET3DP Technology Co., LTD is a leading provider of additive manufacturing solutions headquartered in Qingdao, China. Our company specializes in 3D printing equipment and high-performance metal powders for industrial applications.
Inquiry to get best price and customized Solution for your business!
Related Articles
About Met3DP
Recent Update
Our Product
CONTACT US
Any questions? Send us message now! We’ll serve your request with a whole team after receiving your message.
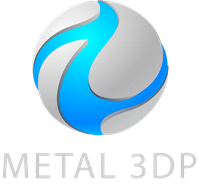
Metal Powders for 3D Printing and Additive Manufacturing