Lightweight Aerospace Fasteners via Additive Manufacturing
Table of Contents
Introduction: Revolutionizing Aerospace Connections with Additive Manufacturing
The aerospace industry operates at the pinnacle of engineering, demanding components that offer uncompromising performance, extreme reliability, and minimal weight. Every gram saved translates into significant fuel efficiency gains or increased payload capacity over an aircraft’s or spacecraft’s lifespan. Fasteners – the bolts, screws, nuts, and rivets that hold critical structures together – are ubiquitous yet often overlooked contributors to overall vehicle weight and complexity. Traditionally manufactured through subtractive methods like machining or forging, aerospace fasteners face limitations in geometric complexity, material utilization, and production lead times, especially for custom or low-volume requirements. However, a paradigm shift is underway, driven by the maturation of additive manufacturing (AM), commonly known as metal 3D printing.
This advanced manufacturing technique offers a transformative approach to producing custom aerospace fasteners, enabling the creation of lightweight components with intricate geometries previously impossible or prohibitively expensive to achieve. By building parts layer by layer directly from digital models using high-performance metal powders, AM unlocks unprecedented design freedom, facilitates rapid iteration, and allows for part consolidation, fundamentally changing how engineers approach fastener design and procurement. For aerospace engineering suppliers and manufacturers, metal 3D printing presents a powerful tool to meet the stringent demands of the industry, offering enhanced performance, reduced lead times for specialized hardware, and the potential for significant weight savings without compromising structural integrity.
The aerospace sector, encompassing commercial aviation, defense, and space exploration, relentlessly pursues innovation. From fuel-efficient commercial airliners and high-performance military jets to reusable rockets and deep-space probes, the need for lighter, stronger, and more complex components is ever-present. Fasteners, while seemingly simple, play a critical role in ensuring the safety and reliability of these complex systems. They must withstand extreme temperatures, high vibrations, significant mechanical loads, and potentially corrosive environments. Traditional manufacturing processes, while mature and reliable, often involve significant material waste (subtractive machining) or require expensive tooling and long setup times (forging), making them less ideal for the highly customized, low-to-medium volume needs often encountered in aerospace development and specialized production runs.
Enter metal additive manufacturing. Technologies like Selective Laser Melting (SLM), Electron Beam Melting (EBM), and Direct Energy Deposition (DED) provide engineers with the ability to:
- Optimize Topology: Design fasteners based on functional requirements and load paths, removing unnecessary material to create organically shaped, highly efficient structures that minimize weight while maximizing strength. This goes beyond simple material substitution; it enables a fundamental rethinking of the fastener’s form.
- Integrate Functionality: Combine multiple components into a single, 3D printed part, reducing part count, assembly time, and potential failure points. Imagine a fastener with integrated locking features or sensor housings, printed as one monolithic piece.
- Utilize Advanced Materials: Process high-performance alloys like Titanium (e.g., Ti-6Al-4V) and high-strength Stainless Steels (e.g., 17-4PH) that are ideally suited for demanding aerospace environments but can be challenging or wasteful to machine conventionally. AM often allows for better material utilization, especially with expensive aerospace-grade metals.
- Enable Rapid Prototyping and Customization: Quickly produce prototypes for fit checks and functional testing, accelerating the design iteration cycle. Manufacture highly customized fasteners tailored to specific applications or unique interfaces without the need for costly tooling changes. This is invaluable for research and development, repairs, and small-batch production.
- Facilitate On-Demand Production: Produce fasteners closer to the point of need, potentially reducing inventory levels and mitigating supply chain disruptions. The digital nature of AM allows designs to be stored electronically and printed when required.
Met3dp, headquartered in Qingdao, China, stands at the forefront of this manufacturing revolution. As a leading provider of comprehensive metal additive manufacturing solutions, Met3dp specializes in developing and supplying both state-of-the-art 3D printing equipment (including SEBM systems known for industry-leading print volume, accuracy, and reliability) and high-performance metal powders optimized for demanding industrial applications, particularly in aerospace. Our expertise in advanced powder production techniques, such as gas atomization and Plasma Rotating Electrode Process (PREP), ensures the highest quality spherical metal powders – like Ti-6Al-4V and 17-4PH – essential for printing dense, reliable, high-strength aerospace components. We partner with aerospace leaders to integrate AM, transforming their approach to designing and manufacturing critical parts like lightweight fasteners. This blog post will delve into the specifics of leveraging AM for aerospace fasteners, exploring applications, benefits, materials, design considerations, quality aspects, and supplier selection criteria, empowering engineers and procurement managers to harness the full potential of this groundbreaking technology.
Applications: Where are Custom 3D Printed Aerospace Fasteners Used?
The utility of custom metal 3D printed fasteners in the aerospace industry spans a wide range of applications, driven by the need for weight reduction, complex geometries, rapid availability, or enhanced performance that traditional methods struggle to deliver cost-effectively. While standard, high-volume fasteners will likely continue to be produced conventionally for the foreseeable future due to established economies of scale, AM shines in areas requiring specialization, optimization, and agility. Procurement managers sourcing B2B aerospace parts and engineers designing next-generation aircraft and spacecraft are increasingly turning to AM for specific fastener needs.
Here are key application areas where custom 3D printed aerospace fasteners are making a significant impact:
- Highly Optimized Structural Connections:
- Topology-Optimized Bolts/Screws: In primary and secondary structures where weight is absolutely critical (e.g., wing spars, fuselage frames, landing gear components), fasteners can be redesigned using topology optimization software. This results in organic, web-like structures that follow stress paths, removing material from low-stress regions while maintaining strength in critical areas. AM is the only practical way to manufacture these complex, non-standard shapes.
- Integrated Fastening Systems: Combining a fastener with its mating part or bracket into a single printed component. This reduces part count, eliminates potential assembly errors, simplifies inventory, and can improve load transfer efficiency. Examples include brackets with integrated threaded bosses or captive nuts.
- Specialized Aerospace Hardware for Extreme Environments:
- High-Temperature Fasteners: For engine components, exhaust systems, or thermal protection systems, fasteners made from superalloys (like Inconel 718 or 625, also processable via AM) or refractory metals are required. AM allows for the creation of fasteners from these challenging materials with potentially improved microstructures or unique cooling channel integration if needed, although Ti-6Al-4V and 17-4PH cover a significant portion of moderate-to-high temperature applications.
- Cryogenic Fasteners: For spacecraft fuel tanks or scientific instruments operating at extremely low temperatures, materials must maintain ductility and strength. Certain titanium alloys and stainless steels suitable for these conditions can be processed via AM, allowing for custom fastener designs optimized for thermal cycling and minimal thermal conductivity where required.
- Satellite Components and Space Systems:
- Lightweight Brackets and Mounts with Integrated Fastening Points: Satellites have extremely strict mass budgets. Printing brackets or mounting interfaces with integrated, optimized threaded holes or captive nuts reduces the need for separate fasteners and adhesives, saving valuable grams and simplifying assembly in cleanroom environments.
- Custom Fasteners for Deployable Structures: Mechanisms like solar arrays, antennas, or booms often require unique, non-standard fasteners that facilitate deployment or lock structures in place. AM enables the rapid production of these bespoke components.
- Waveguide and RF Component Fasteners: Specialized fasteners designed to minimize electromagnetic interference or integrate with specific RF components can be additively manufactured.
- Aircraft Interior and Secondary Structures:
- Customized Cabin Attachments: Fasteners for attaching seats, overhead bins, galley components, or partitions can be optimized for weight and aesthetics. While perhaps less structurally critical than airframe fasteners, the sheer volume of these components means weight savings accumulate significantly.
- Access Panel Fasteners: Designing quick-release or specialized fasteners for access panels that are lighter or easier to operate can improve maintenance efficiency.
- Rapid Prototyping and Development:
- Fit-Check Prototypes: Quickly printing fastener prototypes to verify geometry, thread engagement, and clearance within complex assemblies before committing to expensive tooling or large-scale production.
- Functional Prototypes: Creating functional fasteners from the target material (e.g., Ti-6Al-4V) for early-stage performance testing (e.g., vibration, initial load tests) to validate designs faster.
- Maintenance, Repair, and Overhaul (MRO) and Obsolescence:
- On-Demand Replacement Parts: For aging aircraft or systems where original fastener suppliers no longer exist or minimum order quantities are prohibitively high, AM allows for the on-demand production of dimensionally accurate replacement fasteners based on digital scans or drawings.
- Custom Repair Solutions: Designing unique fasteners required for specific repair schemes where standard parts may not fit or function correctly.
Target Industries & Use Cases Summary Table:
Industry Segment | Specific Application Examples | Key Driver(s) for Using AM Fasteners | Relevant Keywords for Procurement |
---|---|---|---|
Commercial Aviation | Optimized airframe fasteners, Engine component bolts (moderate temp), Interior attachment hardware, Lightweight brackets with integrated threads | Weight reduction, Fuel efficiency, Part consolidation | Aircraft structural fasteners, Aerospace grade hardware |
Defense / Military | High-G load fasteners, Stealth application components, Custom hardware for specific platforms, Rapid deployment spares | Performance, Weight, Customization, Rapid availability | Military spec fasteners, Custom aerospace components |
Space / Satellites | Ultra-lightweight fasteners, Cryogenic/High-temp bolts, Integrated mounting solutions, Deployable structure hardware | Extreme weight sensitivity, Customization, Reliability | Satellite component suppliers, Space-grade fasteners |
UAV / Drones | Miniature lightweight fasteners, Vibration-resistant hardware, Integrated airframe connectors | Weight, Miniaturization, Performance | UAV hardware suppliers, Lightweight drone components |
Aerospace R&D | Prototype fasteners, Custom test rig hardware, Iterative design validation | Speed, Design freedom, Low volume production | Rapid prototyping aerospace, Custom test hardware |
Aerospace MRO | Obsolete fastener replacement, Custom repair fasteners, On-demand spares | Availability, Low volume, Customization | Aircraft MRO parts, Aerospace replacement hardware |
Export to Sheets
The decision to use AM for a specific fastener application hinges on a careful analysis of factors like performance requirements, weight sensitivity, geometric complexity, production volume, lead time constraints, and cost comparison with traditional methods. As AM technologies mature and material databases expand, the range of applications for specialized aerospace hardware produced additively will undoubtedly continue to grow, offering significant advantages to agile and forward-thinking aerospace organizations.
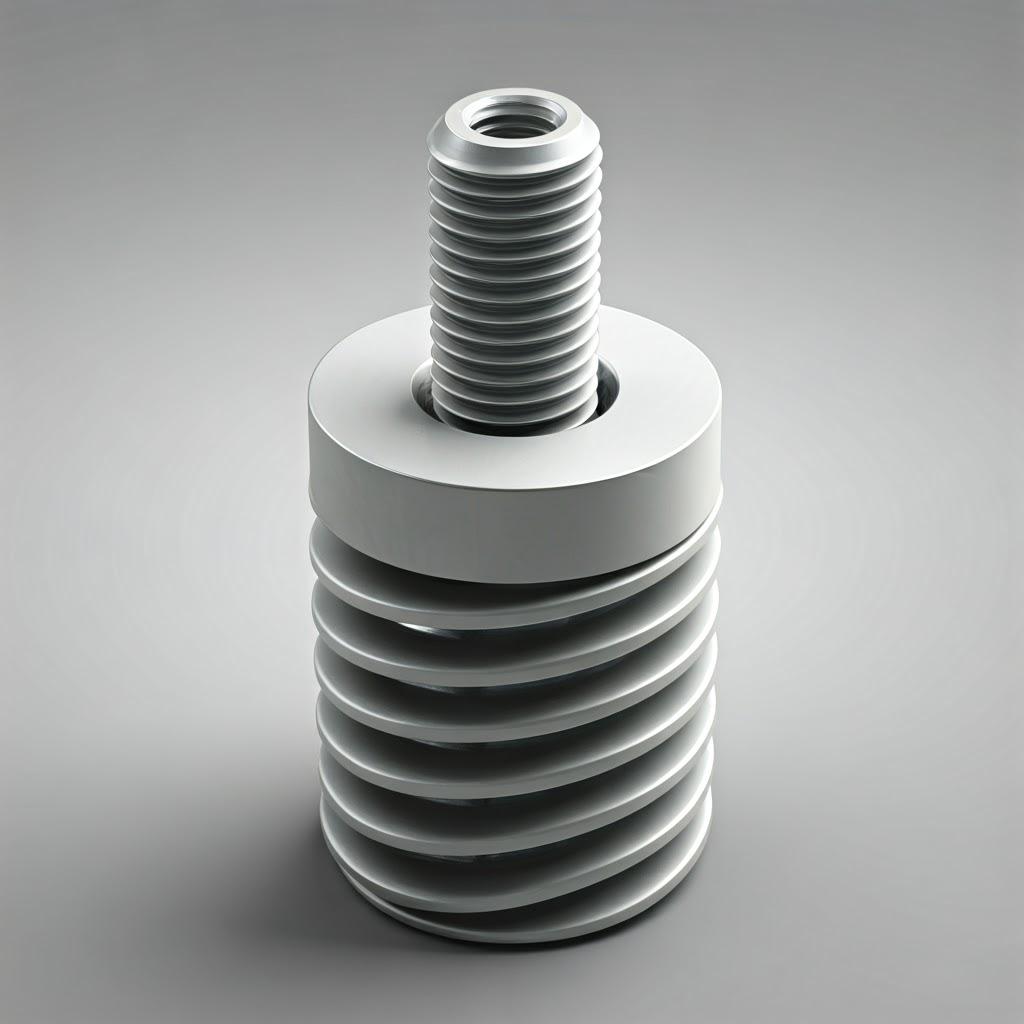
The Additive Advantage: Why Metal 3D Printing for Aerospace Fasteners?
Choosing metal additive manufacturing over traditional methods like machining, forging, or casting for aerospace fasteners isn’t merely about adopting a novel technology; it’s about unlocking tangible engineering and supply chain benefits crucial to the aerospace industry. While conventional manufacturing remains the standard for high-volume, standardized fasteners, AM offers compelling advantages, particularly when dealing with complex designs, lightweighting initiatives, rapid development cycles, and specialized materials. Understanding these benefits of additive manufacturing is key for engineers and procurement managers evaluating on-demand aerospace parts manufacturing solutions.
Let’s break down the key advantages:
- Unprecedented Design Freedom and Complexity:
- Geometric Liberation: Traditional manufacturing methods are constrained by tool access, draft angles, and mold limitations. AM builds parts layer by layer, allowing for highly complex internal channels, intricate external features, non-axisymmetric shapes, and organic forms derived from topology optimization. For fasteners, this means:
- Internal Locking Mechanisms: Designing features within the fastener itself (e.g., internal deformable elements) to prevent loosening under vibration, potentially eliminating the need for lock wire or secondary locking elements.
- Optimized Thread Forms: Creating non-standard thread profiles tailored for specific load conditions or material properties, potentially improving fatigue life or sealing capabilities.
- Integrated Features: Combining the fastener head with a washer, incorporating sealing features, or integrating sensor housings directly into the fastener body.
- Topology Optimization for Lightweighting: This is arguably one of the most significant advantages for lightweighting aerospace components. Engineers can define load cases and boundary conditions, and software algorithms determine the most efficient material distribution to meet performance requirements. This often results in hollow, lattice-filled, or organically shaped fasteners that are significantly lighter (often 20-50% or more) than their solid, conventionally manufactured counterparts while maintaining or even exceeding required strength and stiffness. AM is often the only viable way to produce these optimized shapes.
- Geometric Liberation: Traditional manufacturing methods are constrained by tool access, draft angles, and mold limitations. AM builds parts layer by layer, allowing for highly complex internal channels, intricate external features, non-axisymmetric shapes, and organic forms derived from topology optimization. For fasteners, this means:
- Significant Weight Reduction:
- As mentioned above, topology optimization enabled by AM is a primary driver of weight savings.
- Even without full topology optimization, AM allows for designs with internal voids or lattice structures within the fastener shank or head, removing non-load-bearing material.
- The ability to precisely place material only where needed minimizes the “over-engineering” often required in subtractive manufacturing to ensure sufficient material remains after machining.
- For industries where every gram counts (like satellite manufacturing or high-performance aircraft), the cumulative weight savings from hundreds or thousands of optimized fasteners can be substantial, leading to improved fuel efficiency, increased payload, or enhanced maneuverability.
- Rapid Prototyping and Accelerated Development:
- Speed from CAD to Part: AM allows engineers to go directly from a 3D CAD model to a physical metal part in a matter of days, sometimes hours, depending on the part size and complexity. This drastically shortens the rapid prototyping aerospace cycle compared to waiting weeks or months for machined prototypes or tooling for forged parts.
- Iterative Design: The speed of AM enables multiple design iterations to be printed and tested quickly. Engineers can identify flaws, test variations (e.g., different thread pitches, head designs), and refine the fastener design much faster, leading to a more optimized final product and reduced development costs.
- Reduced Tooling Costs: For custom or low-volume fasteners, AM eliminates the need for expensive molds, dies, or specialized cutting tools required by traditional methods. This significantly lowers the barrier to entry for producing bespoke fastener designs.
- Part Consolidation:
- AM enables the integration of multiple components into a single, monolithic part. For fastening applications, this could mean:
- Printing a bracket with integrated threaded bosses, eliminating the need for separate fasteners and nuts.
- Combining a specialized bolt with a custom washer or spacer.
- Creating captive fasteners integrated directly into a larger component.
- Benefits include reduced part count, simplified assembly, lower inventory management overhead, elimination of potential failure points at joints, and often, further weight reduction.
- AM enables the integration of multiple components into a single, monolithic part. For fastening applications, this could mean:
- Material Efficiency and Suitability for Advanced Alloys:
- Reduced Material Waste: Subtractive manufacturing, especially machining, can generate significant material waste (swarf), particularly when starting with expensive aerospace-grade materials like titanium billets. AM is an additive process, using only the material needed to build the part (plus support structures, which are often recyclable), resulting in much higher material utilization (buy-to-fly ratio).
- Processing Difficult-to-Machine Materials: High-performance aerospace alloys like Ti-6Al-4V or nickel-based superalloys can be challenging and costly to machine due to their hardness and work-hardening properties. AM processes like SLM and EBM are well-suited for these materials, melting and fusing powders layer by layer. Met3dp’s expertise in producing high-quality, spherical aerospace grade metal powders using advanced Gas Atomization and PREP technologies ensures optimal feedstock for reliable printing of these demanding materials.
- On-Demand Production and Supply Chain Flexibility:
- Digital Inventory: Fastener designs can be stored as digital files, allowing for on-demand aerospace parts manufacturing. Parts can be printed when needed, reducing the need for large physical inventories of specialized fasteners, particularly for MRO or low-volume production runs.
- Decentralized Manufacturing: Printing can potentially occur closer to the point of use, reducing shipping times and costs and enhancing supply chain resilience, especially for critical spares in remote locations or during AOG (Aircraft on Ground) situations.
- Mitigating Obsolescence: AM provides a lifeline for obtaining fasteners for legacy systems where original tooling is lost or suppliers no longer exist.
Comparison Table: AM vs. Traditional Manufacturing for Aerospace Fasteners
Feature | Metal Additive Manufacturing (AM) | Traditional Manufacturing (Machining/Forging) | Key Aerospace Implications |
---|---|---|---|
Design Complexity | Very High (Complex geometries, internal features) | Limited (Constrained by tooling, molds, access) | Enables topology optimization, part consolidation, innovation |
Lightweighting | Excellent (Topology optimization, internal voids) | Limited (Primarily material substitution) | Significant weight savings potential |
Lead Time (Proto) | Fast (Days) | Moderate to Slow (Weeks/Months for tooling) | Accelerates development cycles, faster iteration |
Lead Time (Prod.) | Moderate (Batch size dependent) | Fast (High volume), Slow (Low volume/custom) | Good for custom/low-medium volume, on-demand spares |
Tooling Cost | None / Minimal (Supports) | High (Dies, molds, fixtures, custom tools) | Lowers barrier for custom designs, economical for low volumes |
Material Waste | Low (Additive process) | High (Subtractive – machining), Moderate (Forging flash) | Better buy-to-fly ratio, cost savings on expensive alloys |
Part Consolidation | High Potential | Limited | Reduced part count, simplified assembly, improved reliability |
Material Options | Growing range of weldable alloys (Ti, SS, Ni, Al) | Wide range of established alloys | AM excels with Ti-6Al-4V, 17-4PH, Superalloys |
Cost (Low Volume) | Often Lower | Often Higher (due to tooling/setup) | Economical for prototypes, custom parts, MRO |
Cost (High Volume) | Often Higher | Often Lower (Economies of scale) | AM cost-effectiveness improving, best for value-added parts |
Standardization | Emerging standards | Highly standardized (MS, NAS, etc.) | AM requires rigorous qualification for critical apps |
Export to Sheets
While AM offers numerous advantages, it’s crucial to acknowledge that it’s not a universal replacement for traditional methods. Factors like the need for extremely high volumes of standard parts, specific material requirements not yet fully validated for AM, or achieving the absolute lowest cost for simple geometries might still favor conventional processes. However, for applications demanding lightweight aerospace fasteners, complex designs, rapid customization, and utilization of advanced materials like Ti-6Al-4V and 17-4PH, metal 3D printing provides a compelling and increasingly indispensable manufacturing solution. Partnering with an experienced provider like Met3dp, with deep knowledge of both AM processes and high-quality powder production, is key to successfully leveraging these advantages.
Material Focus: Ti-6Al-4V and 17-4PH for High-Performance Fasteners
The performance, reliability, and environmental resistance of an aerospace fastener are fundamentally determined by the material from which it is made. Additive manufacturing allows for the processing of various high-performance metals, but two stand out for their frequent use in demanding aerospace applications, including fasteners: Titanium alloy Ti-6Al-4V (Grade 5) and Precipitation Hardening Stainless Steel 17-4PH. The selection between these aerospace grade metal powders depends critically on the specific requirements of the application, including strength-to-weight ratio, operating temperature, corrosion resistance, and cost.
Understanding the properties and benefits of these materials is crucial for engineers designing AM fasteners and procurement managers sourcing high-strength fastener materials.
1. Titanium Alloy Ti-6Al-4V (Grade 5): The Aerospace Workhorse
Ti-6Al-4V is arguably the most widely used titanium alloy, accounting for more than 50% of all titanium tonnage worldwide, with a significant portion dedicated to aerospace. Its popularity stems from an exceptional combination of properties that make it ideal for demanding environments.
- Key Properties & Benefits:
- Excellent Strength-to-Weight Ratio: This is the hallmark advantage of Ti-6Al-4V. It offers strength comparable to many steels but at roughly 56% of the density. This directly translates to significant weight savings in aerospace structures, making Ti-6Al-4V aerospace fasteners highly desirable for weight-critical applications.
- High Strength: Exhibits high tensile and yield strength, both at room temperature and moderately elevated temperatures (up to around 315°C / 600°F). Post-print heat treatments (solution treatment and aging) can further optimize mechanical properties.
- Superb Corrosion Resistance: Forms a stable, protective oxide layer, providing outstanding resistance to corrosion in various environments, including seawater, oxidizing acids, and industrial chemicals. This is crucial for fasteners exposed to atmospheric conditions, de-icing fluids, or other corrosive agents.
- Good Fatigue Strength: Performs well under cyclic loading conditions, essential for fasteners subject to vibration and repeated stress cycles in aircraft structures.
- Biocompatibility: While less relevant for most fasteners, its biocompatibility makes it suitable for medical implants, showcasing its inert nature.
- Good Elevated Temperature Performance: Retains useful strength up to approximately 315°C (600°F), suitable for many airframe and some cooler engine section applications.
- Considerations for AM:
- Processability: Ti-6Al-4V is readily processable using common powder bed fusion techniques like Selective Laser Melting (SLM) and Electron Beam Melting (EBM). EBM, a technology utilized in some of Met3dp’s advanced systems, is often preferred for titanium due to its high processing temperatures (reducing residual stress) and vacuum environment (preventing oxidation).
- Powder Quality: Achieving optimal mechanical properties relies heavily on the quality of the Ti-6Al-4V powder. High sphericity, controlled particle size distribution, low oxygen/nitrogen content, and good flowability are critical. Met3dp’s advanced gas atomization and PREP powder production methods are specifically designed to produce Met3dp metal powders meeting these stringent requirements, ensuring density and reliability in the final printed fastener.
- Post-Processing: Typically requires stress relief heat treatment after printing to reduce internal stresses built up during the rapid heating and cooling cycles. Solution treatment and aging (STA) may be applied to achieve specific strength and ductility targets. Hot Isostatic Pressing (HIP) can be used to close any residual internal porosity and further improve fatigue life for critical applications. Support structure removal can also be challenging due to titanium’s strength.
- Typical Aerospace Fastener Applications:
- Airframe structural bolts and screws (fuselage, wings, empennage)
- Landing gear components
- Engine pylon attachments
- Satellite structures
- High-performance racing and automotive components (where weight is critical)
2. Precipitation Hardening Stainless Steel 17-4PH: Strength and Versatility
17-4PH (AISI 630, UNS S17400) is a chromium-nickel-copper precipitation-hardening martensitic stainless steel. It offers a different balance of properties compared to Ti-6Al-4V, providing high strength and hardness combined with good corrosion resistance and excellent processability via AM.
- Key Properties & Benefits:
- High Strength and Hardness: Achieves high strength and hardness levels through a single, low-temperature heat treatment (aging/precipitation hardening) after printing (or solution annealing followed by aging). Different heat treatment conditions (e.g., H900, H1025, H1075, H1150) allow tailoring of properties, trading strength for toughness. Condition H900 offers the highest strength.
- Good Corrosion Resistance: Offers corrosion resistance generally superior to standard martensitic stainless steels (like 410) and approaching that of austenitic grades like 304 in many environments. Suitable for applications exposed to atmospheric corrosion or mild chemical environments.
- Good Toughness: Especially in higher aging temperature conditions (e.g., H1025 and above), 17-4PH exhibits good toughness and ductility.
- Wear Resistance: Its high hardness contributes to good wear resistance, beneficial for certain fastener applications involving relative motion or clamping forces.
- Magnetic: Unlike austenitic stainless steels (e.g., 316L) or titanium, 17-4PH is ferromagnetic.
- Cost-Effective: Generally less expensive than titanium alloys, making 17-4PH stainless steel fasteners a more economical choice when the extreme lightweighting of titanium is not the primary driver.
- Considerations for AM:
- Processability: 17-4PH is well-suited for SLM and Binder Jetting AM processes. Careful parameter control is needed to manage the martensitic transformation during cooling and minimize residual stress.
- Powder Quality: As with titanium, high-quality powder with controlled chemistry (especially Cr, Ni, Cu levels), particle size, and morphology is essential for achieving consistent properties and dense parts. Met3dp ensures its 17-4PH powders meet these demanding specifications for reliable additive manufacturing.
- Heat Treatment: Post-print heat treatment is critical for 17-4PH to achieve its desired mechanical properties. Parts are typically printed in a state closer to solution annealed (though the rapid cooling of AM introduces complexities) and then subjected to a specific aging cycle (e.g., heating to 482°C / 900°F for H900 condition) to precipitate hardening phases. Stress relief may also be necessary.
- Typical Aerospace Fastener Applications:
- Structural components requiring high strength where the weight penalty compared to titanium is acceptable.
- Actuation system components.
- Landing gear components (where high hardness/wear is needed).
- Engine components (moderate temperature applications).
- Fixtures, tooling, and jigs used in aerospace manufacturing.
- Applications requiring higher strength than standard austenitic stainless steels.
Material Selection Guide: Ti-6Al-4V vs. 17-4PH for AM Fasteners
Feature | Ti-6Al-4V (Grade 5) | 17-4PH Stainless Steel | Selection Criterion |
---|---|---|---|
Primary Advantage | Strength-to-Weight Ratio | High Strength / Hardness & Cost | Choose Ti-6Al-4V for maximum weight savings. |
Density | ~4.43 g/cm³ | ~7.8 g/cm³ | 17-4PH is ~76% heavier. |
Tensile Strength (Typical) | High (depends on heat treat) | Very High (esp. H900, depends on HT) | Both offer high strength; specific values vary with HT. |
Max Service Temp. | ~315°C (600°F) | ~315°C (600°F) (varies with HT/load) | Similar moderate temperature capability. |
Corrosion Resistance | Excellent (Superior in many media) | Good (Better than martensitic SS) | Ti-6Al-4V preferred for harsh corrosive environments. |
Hardness / Wear | Moderate | High (Especially H900) | 17-4PH preferred for wear resistance applications. |
Cost | Higher | Lower | 17-4PH is more economical if weight is less critical. |
AM Process Suitability | Excellent (SLM, EBM) | Excellent (SLM, Binder Jetting) | Both well-suited; EBM often favored for Ti. |
Post-Processing | Stress Relief / STA / HIP often needed | Solution Anneal + Aging required | Both require thermal post-processing. |
Magnetic Properties | Non-magnetic | Magnetic | Important consideration for specific applications (EMI). |
Export to Sheets
Conclusion on Materials:
Both Ti-6Al-4V and 17-4PH are exceptional engineering materials that, when combined with the geometric freedom of additive manufacturing, enable the production of high-performance, lightweight aerospace fasteners. The choice depends on a careful trade-off between the unparalleled weight savings offered by titanium and the high strength, hardness, and cost-effectiveness of 17-4PH stainless steel. Partnering with a knowledgeable AM service provider like Met3dp, who not only possesses advanced printing capabilities but also manufactures high-quality, optimized aerospace grade metal powders, ensures that the selected material performs to its maximum potential in the final fastener application. Their expertise guides material selection and processing to meet the stringent demands of the aerospace industry. Sources and related content
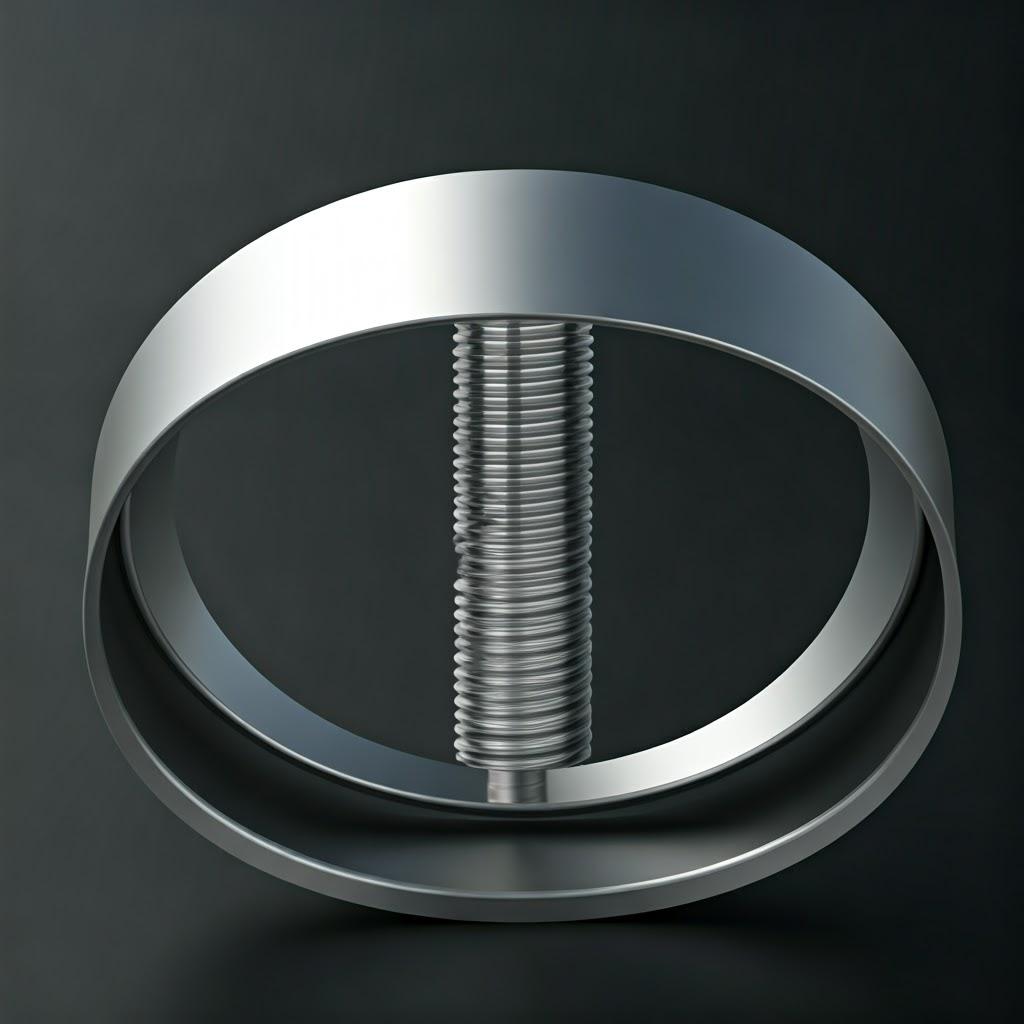
Design for Additive Manufacturing (DfAM): Optimizing Fastener Geometries
Simply replicating a conventionally designed fastener using additive manufacturing often fails to capture the technology’s true potential and can even lead to suboptimal results. To fully harness the benefits of AM – particularly lightweighting, part consolidation, and enhanced functionality – engineers must embrace Design for Additive Manufacturing (DfAM) principles. DfAM is not just about creating complex shapes; it’s a holistic approach that considers the unique possibilities and constraints of the layer-by-layer building process, the chosen material, and the specific AM technology (like SLM or EBM). Applying DfAM aerospace methodologies is crucial for developing next-generation, high-performance fasteners.
Key DfAM Principles for AM Fasteners:
- Topology Optimization:
- Concept: This is a computational method where material is iteratively removed from a design space based on defined load conditions, constraints, and performance objectives (e.g., minimize mass, maximize stiffness). The result is often an organic, load-path-optimized structure.
- Application to Fasteners: Instead of a solid cylindrical shank and standard head, topology optimization can yield fasteners with hollowed-out sections, internal lattice structures, or variable cross-sections, drastically reducing weight while meeting or exceeding the mechanical requirements of the original solid design. This is a cornerstone for creating truly lightweight aerospace fasteners via additive manufacturing.
- Workflow: Typically involves defining the design space (maximum allowable volume for the fastener), applying expected loads (tension, shear, vibration), defining keep-out zones (e.g., thread interfaces, head seating surface), setting manufacturing constraints (e.g., minimum feature size printable by the AM machine), and running the optimization algorithm. The resulting complex geometry is then refined in CAD for manufacturability.
- Example: Optimizing a high-strength bolt for a wing-spar connection might result in a design where the shank has a complex internal truss structure and the head is sculpted to efficiently transfer load, saving potentially 30-60% of the weight compared to a standard machined bolt.
- Feature Geometry Considerations:
- Overhangs and Support Structures: Powder Bed Fusion (PBF) processes like SLM and EBM build parts layer by layer. Features that overhang significantly relative to the build plate (typically angles less than 45 degrees from the horizontal) require support structures to anchor them during the build and prevent them from collapsing or warping due to gravity and thermal stresses.
- Fastener Heads: The underside of bolt heads or nut flanges often represents a significant overhang. Designing with self-supporting angles (>= 45 degrees) or incorporating built-in chamfers can minimize the need for supports. Where supports are unavoidable, their location must be carefully considered for ease of removal without damaging critical surfaces.
- Threads: External and internal threads present a major DfAM challenge. Standard sharp V-threads often have low overhang angles that require extensive internal or external supports, which are extremely difficult, if not impossible, to remove cleanly, especially for internal threads. Strategies include:
- Designing Self-Supporting Threads: Modifying thread profiles (e.g., using profiles closer to buttress or custom trapezoidal forms with >45-degree flanks) can sometimes allow threads to be printed without supports, though this deviates from standards.
- Printing Oversize & Post-Machining: A common and often necessary approach is to print the threaded section slightly oversized or undersized (depending on internal/external) without thread details, and then machine the threads accurately after printing. This ensures thread form accuracy and surface finish critical for fastener function.
- Orientation: Printing fasteners vertically (axis perpendicular to the build plate) generally results in better thread quality for external threads than printing horizontally, but may require more supports for the head. Horizontal printing might be better for features along the length but compromises circularity and thread form.
- Minimum Wall Thickness & Feature Size: AM processes have limitations on the minimum thickness of walls and the smallest features they can reliably produce. This depends on the machine, laser/beam spot size, and powder particle size. Typical minimum printable wall thicknesses are around 0.4-0.8 mm. This must be considered when designing thin sections or fine details in optimized fasteners.
- Hole Orientation and Size: Small holes, especially those printed horizontally, can be challenging to produce accurately due to the layer-wise approximation and potential powder sintering. Holes below a certain diameter (often < 1-2 mm, machine dependent) might require drilling or reaming after printing for accuracy. Vertical holes generally print with better accuracy.
- Fillets and Radii: Sharp internal corners can act as stress concentrators and are also difficult to print accurately. Incorporating fillets and radii at junctions (e.g., between head and shank) improves stress distribution and printability.
- Overhangs and Support Structures: Powder Bed Fusion (PBF) processes like SLM and EBM build parts layer by layer. Features that overhang significantly relative to the build plate (typically angles less than 45 degrees from the horizontal) require support structures to anchor them during the build and prevent them from collapsing or warping due to gravity and thermal stresses.
- Part Consolidation:
- Concept: Leveraging AM’s geometric freedom to combine multiple adjacent components into a single printed part.
- Application to Fasteners:
- Integrated Washer Heads: Designing bolts or screws with integrated, non-rotating washer features.
- Captive Fasteners: Designing components (e.g., access panels, brackets) with integrated features that retain a fastener (e.g., a screw within a captured sleeve), simplifying assembly and preventing lost hardware.
- Bracket with Integrated Threads: Printing a structural bracket with precisely located threaded holes, eliminating the need for separate nuts or threaded inserts.
- Benefits: Reduced part count, simplified Bill of Materials (BOM), faster assembly, lower inventory, potential for further weight reduction, and elimination of joint interfaces which can be failure points.
- Lattice Structures:
- Concept: Incorporating internal lattice or cellular structures within solid volumes to reduce mass while maintaining significant structural integrity. Various lattice types (e.g., cubic, octet truss, gyroid) offer different mechanical properties (stiffness, energy absorption).
- Application to Fasteners: Filling the internal volume of a fastener shank or head (where stresses are lower) with a lightweight lattice structure. This requires careful engineering analysis (FEA) to ensure the lattice provides sufficient support and doesn’t compromise overall strength or fatigue life. Powder removal from complex internal lattices can also be a challenge.
- Orientation Strategy:
- Impact: How a part is oriented on the build plate significantly impacts print time, support requirements, surface finish on different faces, and potentially mechanical properties (due to anisotropic behavior in some AM processes/materials).
- Fastener Considerations:
- Vertical (Axis Perpendicular to Plate): Often best for shank circularity and external threads (if self-supporting or to be machined). Requires supports under the head. Potentially better Z-direction strength.
- Horizontal (Axis Parallel to Plate): Minimizes Z-height (faster print for single parts, but less efficient packing). Can lead to “stair-stepping” on curved surfaces (shank). May require supports along the shank length. Often results in anisotropic properties along the fastener axis vs. perpendicular to it.
- Optimization: Selecting the optimal orientation involves balancing these factors to minimize supports (especially on critical surfaces), optimize surface finish where needed, ensure critical features are printable, and potentially align layers favorably with expected load directions.
DfAM Guidelines Summary Table for AM Fasteners:
DfAM Principle | Key Consideration for Fasteners | Benefit(s) | Potential Challenge(s) |
---|---|---|---|
Topology Optimization | Redesign shank/head based on load paths | Major weight reduction, High stiffness-to-weight | Complex geometry, Requires FEA validation |
Overhangs/Supports | Head underside, Thread profiles (<45°) | Reduced post-processing, Improved surface finish | Design constraints, Potential need for machining |
Threads | Difficulty printing standard profiles accurately/support-free | Functional threads | Requires modified profiles or post-machining |
Min. Feature Size | Thin walls in optimized designs, Fine details | Enables lightweighting | Printability limits, Feature resolution |
Part Consolidation | Integrate washers, brackets, captive features | Reduced part count, Simplified assembly, Weight | Increased complexity of single part |
Lattice Structures | Internal filling of shank/head | Weight reduction, Tunable properties | FEA needed, Powder removal, Fatigue properties |
Orientation | Vertical vs. Horizontal placement | Optimize supports, surface finish, properties | Anisotropy, Support marks, Packing density |
Fillets & Radii | Sharp internal corners (head-shank junction) | Reduced stress concentration, Improved printability | Minor design adjustment |
Export to Sheets
Engaging with an AM service provider like Met3dp early in the design process is highly beneficial. Their engineers possess deep expertise in DfAM aerospace applications and understand the nuances of their specific printing methods (e.g., SEBM for titanium) and material behaviors. They can provide crucial feedback on design manufacturability, suggest optimizations for weight reduction and performance, and help navigate the complexities of support strategy and orientation, ensuring the final fastener design is truly optimized for additive manufacturing.
Achieving Precision: Tolerance, Surface Finish, and Dimensional Accuracy in AM Fasteners
While additive manufacturing offers incredible geometric freedom, achieving the tight tolerances, smooth surface finishes, and high dimensional accuracy required for aerospace fasteners demands careful process control, material understanding, and often, post-processing steps. Engineers and procurement managers must understand the typical precision levels achievable with metal AM and how they compare to conventional manufacturing to set realistic expectations and specify requirements appropriately. Aerospace fastener tolerances and surface finish are critical for proper fit, load distribution, and fatigue life.
Factors Influencing Precision in Metal AM:
- AM Process: Different metal AM processes inherently offer varying levels of precision.
- Powder Bed Fusion (PBF – SLM/EBM): Generally offer the best accuracy and finest feature resolution among common metal AM techniques. SLM (Selective Laser Melting) typically provides slightly better surface finish and finer detail than EBM (Electron Beam Melting), while EBM often results in lower residual stress (especially with Ti-6Al-4V) due to the higher processing temperatures.
- Direct Energy Deposition (DED): Often produces parts closer to near-net shape with rougher surfaces and lower accuracy compared to PBF, usually requiring significant post-machining for precise features. Less common for small, intricate parts like fasteners.
- Binder Jetting (BJ): Creates a “green” part that requires subsequent sintering. Shrinkage during sintering must be precisely predicted and controlled, which can be challenging, affecting final tolerances. Can achieve good surface finish after sintering.
- Machine Calibration & Condition: Regular calibration of the laser/electron beam system, scanner accuracy, and build platform leveling is crucial for consistent dimensional accuracy. Machine wear and tear can also impact precision.
- Material Properties: Different metal powders behave differently during melting and solidification (e.g., thermal expansion/contraction, reflectivity/absorptivity). Process parameters must be optimized for each specific material (e.g., Ti-6Al-4V vs. 17-4PH).
- Powder Quality: Particle size distribution, morphology (sphericity), and flowability of the metal powder influence packing density in the powder bed and melting behavior, impacting surface finish and feature resolution. Using high-quality powders, like those produced by Met3dp using advanced atomization techniques, contributes significantly to achievable precision.
- Process Parameters: Laser/beam power, scan speed, layer thickness, hatch spacing, and scan strategy all significantly influence the melt pool dynamics, cooling rates, and ultimately, the dimensional accuracy and surface finish of the part.
- Thermal Effects: Residual stresses built up during the rapid heating and cooling cycles can cause warping and distortion, affecting final dimensions. Build strategy, support structures, and sometimes post-print stress relief are used to mitigate these effects.
- Part Size and Geometry: Larger parts or parts with significant changes in cross-section are generally more prone to distortion. Complex geometries with fine features are harder to produce accurately.
- Orientation: As discussed in DfAM, orientation affects how features are approximated layer-by-layer, influencing circularity, flatness, and surface finish on different faces.
Typical Tolerances and Surface Finish (As-Built PBF):
It’s important to note that achievable tolerances are highly dependent on the specific machine, material, part geometry, and orientation. However, general guidelines for as-built PBF (SLM/EBM) parts are:
- Dimensional Accuracy:
- Typically in the range of ±0.1 mm to ±0.3 mm (±0.004″ to ±0.012″) for smaller dimensions (e.g., up to 100 mm).
- For larger dimensions, accuracy is often expressed as a percentage, e.g., ±0.1% to ±0.3% of the nominal dimension.
- Achieving tighter tolerances often requires post-machining critical features.
- Surface Finish (Roughness – Ra):
- Side Walls (Vertical): Generally rougher due to layer lines and partially melted powder particles adhering to the surface. Typical Ra values range from 6 µm to 20 µm (240 µin to 800 µin).
- Top Surfaces (Upward-Facing): Often smoother as they represent the last solidified melt pools. Ra values can be in the range of 5 µm to 15 µm (200 µin to 600 µin).
- Bottom Surfaces (Downward-Facing/Supported): Tend to be the roughest, especially where support structures were attached. Ra values can exceed 20 µm (>800 µin) and often show witness marks from support removal.
- Internal Channels/Features: Surface finish is generally difficult to control and measure, often being quite rough.
Comparison with Conventional Machining:
Feature | Metal AM (PBF As-Built) | Conventional Machining (CNC) | Implication for Fasteners |
---|---|---|---|
Tolerance | ±0.1 to ±0.3 mm (Typical) | ±0.01 to ±0.05 mm (Common) | AM often requires post-machining for critical fastener dimensions (threads, shanks, seating surfaces). |
Surface Finish (Ra) | 6 – 20+ µm | 0.4 – 6.3 µm (Common) | As-built AM surfaces usually too rough for thread engagement or fatigue-critical areas; post-finishing needed. |
Feature Resolution | Good (Down to ~0.4mm walls) | Excellent (Very fine details) | AM suitable for optimized shapes, machining better for sharp edges/very fine standard features. |
Export to Sheets
Achieving Required Precision for AM Fasteners:
Given that standard aerospace fastener tolerances (e.g., for thread profiles, shank diameters, head concentricity) and surface finish requirements (especially for fatigue resistance and proper preload) are often tighter than as-built AM capabilities, a hybrid approach is typically necessary:
- Print Near-Net Shape: Use AM to create the complex, optimized overall shape of the fastener, leveraging DfAM for lightweighting and complexity. Leave extra material (machining allowance, typically 0.5-1.0 mm) on critical surfaces and features.
- Post-Machining: Use precision CNC machining to finish critical dimensions and surfaces after printing and heat treatment. This includes:
- Machining threads (internal and external) to meet standard specifications (e.g., UNJ, MJ profiles for aerospace).
- Turning shank diameters to precise tolerances.
- Machining head seating surfaces (underhead fillet, bearing surface) for flatness and perpendicularity.
- Drilling/reaming small holes.
- Surface Finishing: Employ secondary finishing processes (discussed in the next section) like tumbling, blasting, or polishing to improve overall surface roughness, especially for fatigue-sensitive areas not addressed by machining.
Met3dp’s Role in Precision:
Achieving high precision starts with the right foundation. Met3dp contributes significantly through:
- High-Accuracy Printers: Our printers are engineered for industry-leading accuracy and reliability, providing a stable platform for precise builds. Features like advanced thermal management and precise beam control contribute to dimensional stability.
- Quality Metal Powders: Our meticulously produced Ti-6Al-4V, 17-4PH, and other aerospace-grade powders ensure consistent melting behavior and high packing density, leading to better surface finish and feature definition.
- Process Expertise: Our team understands the intricate relationship between process parameters, material behavior, and achievable precision, optimizing print strategies for dimensional accuracy and surface quality.
While AM might not match the inherent tolerance and finish of machining in an as-built state, its strength lies in creating complex geometries efficiently. By strategically combining AM for the overall shape with targeted post-machining and finishing for critical features, manufacturers can produce dimensionally accurate AM parts like fasteners that meet stringent aerospace fastener tolerances and performance requirements.
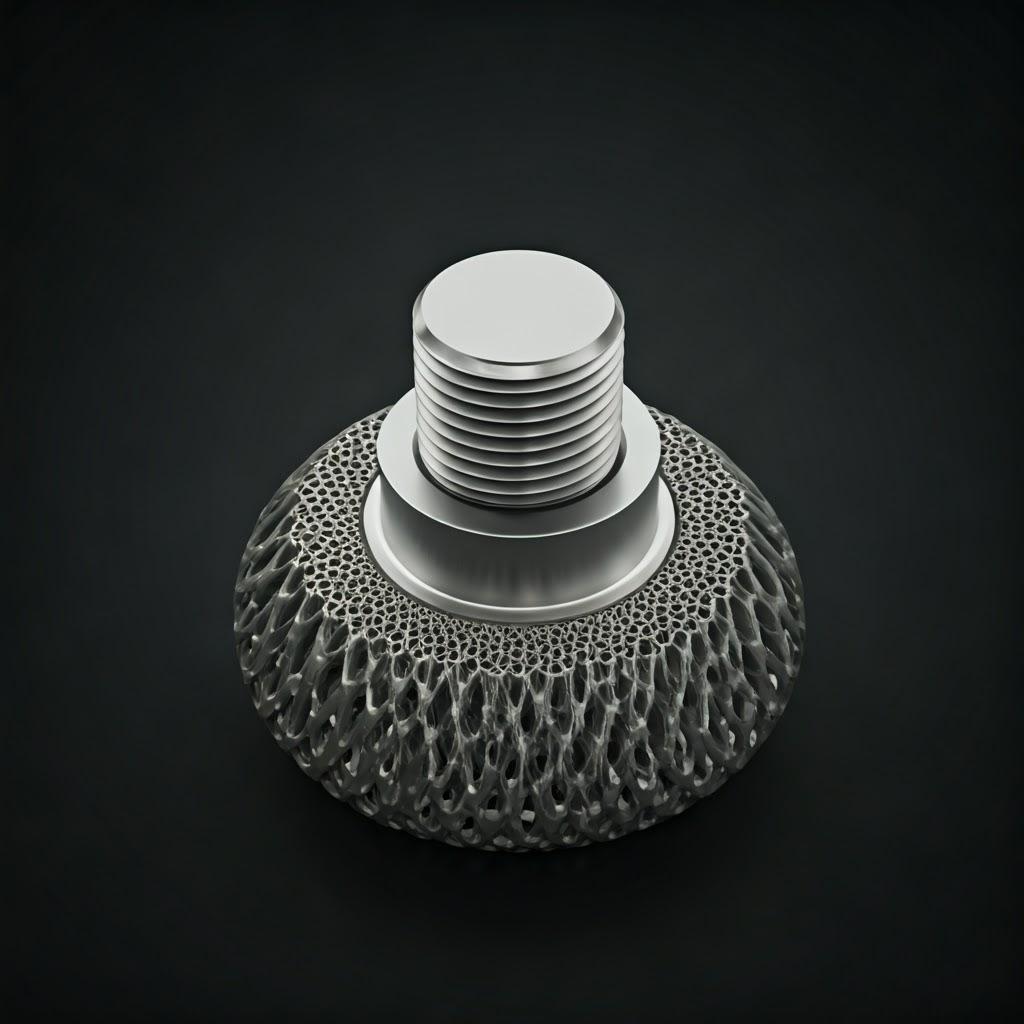
Beyond the Print: Essential Post-Processing for Aerospace Fasteners
The journey of an additively manufactured aerospace fastener doesn’t end when the printer stops. A series of crucial post-processing steps are typically required to transform the as-built part into a functional, reliable component ready for assembly. These steps are essential to relieve internal stresses, achieve the desired mechanical properties, remove support structures, attain critical tolerances and surface finishes, and verify part integrity. Understanding these post-processing requirements is vital for planning production workflows and ensuring the final fastener meets aerospace specifications.
Common Post-Processing Steps for AM Aerospace Fasteners:
- Powder Removal / Depowdering:
- Goal: Remove all unfused metal powder trapped within the build volume, especially from internal channels, complex lattice structures, or enclosed voids in optimized fastener designs.
- Methods: Manual brushing, compressed air blowing, vibration, ultrasonic cleaning baths, specialized powder handling stations. Complete powder removal is critical to avoid adding dead weight and potential contamination. For complex internal geometries, designing for depowderability (e.g., including drainage holes) during the DfAM phase is crucial.
- Stress Relief:
- Goal: Reduce the high residual stresses induced by the rapid heating and cooling cycles inherent in PBF processes. These stresses can cause distortion during or after printing, cracking, or premature failure under load.
- Method: Heating the parts (often while still attached to the build plate) in a controlled furnace atmosphere (vacuum or inert gas like argon to prevent oxidation) to a specific temperature below the material’s transformation or aging temperature, holding for a period, and then slowly cooling.
- Parameters: Specific temperatures and times depend on the material (e.g., ~650-800°C for Ti-6Al-4V, ~500-600°C for 17-4PH prior to aging) and part geometry. This is often the first thermal step performed.
- Part Removal from Build Plate:
- Goal: Separate the printed fasteners from the metal build plate they were fused to during printing.
- Methods: Typically done using wire EDM (Electrical Discharge Machining) or a bandsaw. Care must be taken not to damage the parts.
- Support Structure Removal:
- Goal: Remove the temporary support structures required during printing for overhangs and complex features.
- Methods: Supports are designed to be weaker than the main part but often require significant effort to remove. Methods include manual breaking/clipping (for accessible supports), CNC machining, grinding, or sometimes wire EDM.
- Considerations: Support removal can leave witness marks or rough surfaces (“support scars”) on the part, often requiring further finishing. Access for removal tools must be considered during DfAM.
- Heat Treatment (Solution Annealing, Aging, STA):
- Goal: Optimize the microstructure and achieve the final desired mechanical properties (strength, ductility, hardness, fatigue life) specified for the aerospace application. This is distinct from stress relief.
- Methods: Performed in calibrated furnaces with controlled atmospheres (vacuum or inert gas). Specific cycles depend heavily on the alloy and desired properties:
- Ti-6Al-4V: Often undergoes Solution Treatment and Aging (STA). Solution treatment involves heating to a high temperature (beta phase region, e.g., ~900-950°C), quenching, followed by aging at a lower temperature (e.g., ~500-600°C) to precipitate strengthening phases. Different STA cycles yield different balances of strength and ductility.
- 17-4PH: Typically requires solution annealing (if not sufficiently achieved during printing/stress relief) followed by precipitation hardening (aging). Aging involves heating to a specific temperature (e.g., H900 = 482°C/900°F, H1025 = 552°C/1025°F, etc.) for a set time (often 1-4 hours) to precipitate copper-rich phases that significantly increase strength and hardness. The chosen condition (H900, H1075, etc.) dictates the final properties.
- Importance: Proper heat treatment aerospace fasteners is absolutely critical for performance and safety. It must be performed according to validated aerospace specifications (e.g., AMS standards).
- Hot Isostatic Pressing (HIP):
- Goal: Close any residual internal microscopic pores or voids that might remain after printing, improving material density (approaching 100% theoretical density), enhancing fatigue properties, and increasing ductility and fracture toughness.
- Method: Subjecting the parts to high temperature (below melting point) and high isostatic pressure (using an inert gas like Argon) simultaneously in a specialized HIP vessel.
- Application: Often specified for fatigue-critical aerospace components, including high-performance fasteners, to ensure maximum material integrity. It adds cost but significantly improves reliability for demanding applications.
- Machining (CNC):
- Goal: Achieve tight tolerances, specific surface finishes, and precise geometric features that cannot be reliably produced by AM alone.
- Application for Fasteners: As discussed previously, CNC machining 3D printed parts is essential for:
- Creating accurate thread forms (internal/external).
- Finishing shank diameters.
- Ensuring flatness and perpendicularity of head bearing surfaces.
- Creating precise locating features or interfaces.
- Considerations: Requires careful fixture design to hold the potentially complex AM part geometry. Machining allowances must be included in the DfAM stage.
- Surface Finishing:
- Goal: Improve the as-built or post-machined surface roughness for better aesthetics, fatigue life (smooth surfaces reduce crack initiation sites), sealing, or preparation for coating.
- Methods:
- Tumbling/Vibratory Finishing: Parts are placed in a tub with media (e.g., ceramic, plastic) that vibrates or tumbles, gradually smoothing surfaces and edges. Good for batch processing but less precise.
- Abrasive Blasting (Sand/Grit/Bead Blasting): Propelling abrasive particles at the surface to clean, deburr, or create a uniform matte finish. Can slightly improve fatigue life by inducing compressive stress but doesn’t significantly reduce deep roughness peaks.
- Polishing/Lapping: Mechanical or electrochemical polishing to achieve very smooth, mirror-like finishes (low Ra values). Often targeted at specific critical areas.
- Electropolishing: An electrochemical process that removes material preferentially from peaks, smoothing and brightening the surface. Good for complex shapes but material specific.
- Non-Destructive Testing (NDT):
- Goal: Verify the internal and external integrity of the finished fastener without damaging it, ensuring it is free from critical defects like cracks, porosity, or inclusions. NDT aerospace protocols are stringent.
- Methods:
- Visual Inspection (VT): Basic inspection for external defects, surface finish issues.
- Dimensional Inspection: Using calipers, micrometers, CMMs (Coordinate Measuring Machines), or 3D scanners to verify tolerances.
- Computed Tomography (CT) Scanning: X-ray based method providing a 3D view of the internal structure, capable of detecting internal pores, voids, and density variations. Increasingly used for critical AM parts.
- Fluorescent Penetrant Inspection (FPI): Detects surface-breaking cracks or defects.
- Ultrasonic Testing (UT): Can detect internal flaws but access and geometry can be challenging for complex fasteners.
- Coating / Plating:
- Goal: Enhance surface properties like wear resistance, corrosion protection, lubricity, or thermal resistance.
- Methods: Various fastener coating solutions can be applied, such as PVD coatings (e.g., TiN, CrN), plating (e.g., Cadmium – though usage is declining, Zinc-Nickel), dry film lubricants (e.g., MoS2), or specialized aerospace paints/primers. Compatibility with the base AM material and prior surface preparation are key.
Process Flow Considerations:
The exact sequence and necessity of these steps depend on the specific fastener, its application, material, and required specifications. For example, HIP might be done after stress relief but before final heat treatment or machining. Machining might occur before or after final heat treatment depending on the hardness achieved. Partnering with an experienced AM provider like Met3dp ensures that a robust and validated post-processing workflow is established and followed, often leveraging their network of qualified partners for specialized services like certified heat treatment, HIP, NDT, and coating. This comprehensive approach guarantees that the final AM fastener meets all necessary aerospace quality and performance standards.
Navigating Challenges: Common Issues and Solutions in AM Fastener Production
While metal additive manufacturing offers tremendous potential for aerospace fasteners, it’s not without its challenges. Producing high-quality, reliable fasteners consistently requires careful control over the entire process chain, from design and powder handling to printing and post-processing. Awareness of potential metal AM print failures and common issues allows engineers and manufacturers to implement mitigation strategies and ensure robust aerospace quality assurance.
Common Challenges and Mitigation Strategies:
- Warping and Distortion:
- Issue: Uneven heating and cooling during the layer-by-layer fusion process generate internal residual stresses. If these stresses exceed the material’s yield strength at elevated temperatures, the part can warp, distort, or even detach from the build plate. This is particularly prevalent in parts with large cross-sections, thin walls, or significant overhangs.
- Causes: High thermal gradients, insufficient support, inappropriate scan strategies, material properties (high thermal expansion).
- Mitigation / Solutions:
- Thermal Simulation: Using process simulation software during DfAM to predict stress accumulation and distortion, allowing for design modifications or optimized orientation/support strategies before printing.
- Optimized Orientation: Orienting the fastener to minimize large flat areas parallel to the build plate or sections with abrupt thickness changes.
- Robust Support Structures: Designing effective supports to anchor the part firmly to the build plate and act as heat sinks.
- Optimized Scan Strategy: Using specific scan patterns (e.g., island scanning, alternating hatch directions) to distribute heat more evenly and reduce localized stress peaks.
- Process Parameter Adjustment: Modifying laser/beam power, scan speed, or layer thickness (within limits) to control thermal input.
- Platform Heating (EBM): EBM processes operate at higher ambient temperatures, significantly reducing thermal gradients and residual stress, making it advantageous for materials like Ti-6Al-4V prone to cracking/warping.
- Post-Print Stress Relief: Performing stress relief heat treatment immediately after printing, often before removing the part from the build plate, is crucial.
- Support Structure Issues:
- Issue: Supports are necessary but can be difficult to remove completely, leave undesirable witness marks on the part surface, or fail during the build leading to part collapse. Removing supports from internal channels or complex geometries (like internal threads if attempted) can be nearly impossible.
- Causes: Poor DfAM planning, overly dense supports, difficult-to-access locations, inadequate support strength.
- Mitigation / Solutions:
- DfAM for Support Minimization: Designing parts with self-supporting angles (>45°) wherever possible. Using chamfers instead of sharp overhangs.
- Optimized Support Design: Using simulation tools or expert knowledge to generate efficient support structures (e.g., tree supports, conical supports, block supports) that are strong enough but easier to remove (potentially with engineered break-points). Placing supports on non-critical surfaces.
- Planning for Removal: Ensuring adequate access for tools (manual or CNC) during the design phase.
- Post-Processing Techniques: Utilizing appropriate removal methods (manual, CNC, grinding) followed by surface finishing to minimize witness marks. For critical surfaces, avoid placing supports there entirely if possible.
- Porosity:
- Issue: Small voids or pores trapped within the printed material. Porosity can significantly degrade mechanical properties, particularly fatigue life, and act as crack initiation sites. Aerospace standards typically have strict limits on allowable porosity.
- Causes:
- Gas Porosity: Trapped gas (e.g., Argon shield gas, dissolved gas in powder) within the melt pool.
- Keyhole Porosity: Instability in the melt pool due to excessive energy density, causing vapor depression collapse.
- Lack-of-Fusion Porosity: Insufficient energy density leading to incomplete melting between layers or scan tracks.
- Powder Quality: Entrapped gas within powder particles, irregular powder shapes leading to poor packing density.
- Mitigation / Solutions:
- Optimized Process Parameters: Precisely controlling laser/beam power, scan speed, hatch spacing, and focus to ensure stable melting and complete fusion without excessive energy input. Parameter development is key.
- High-Quality Powder: Using high-purity, spherical powders with low internal gas content and controlled particle size distribution, such as those from Met3dp’s advanced production systems (Gas Atomization, PREP). Proper powder handling and storage to prevent moisture absorption are also critical. Explore Met3dp’s high-quality metal powder products.
- Appropriate Shielding Gas Flow: Ensuring proper inert gas flow in the build chamber to remove processing fumes and prevent oxidation/contamination.
- Hot Isostatic Pressing (HIP): The most effective way to eliminate residual porosity (Lack-of-Fusion and Gas, less so Keyhole) and achieve full density, often mandated for critical aerospace fasteners.
- Surface Finish Roughness:
- Issue: As-built surfaces, particularly side walls and down-facing surfaces, are inherently rougher than machined surfaces, which can negatively impact fatigue life, sealing, and fit.
- Causes: Layer-wise building process (“stair-stepping”), adherence of partially melted powder particles, support structure contact points.
- Mitigation / Solutions:
- Orientation Optimization: Printing critical surfaces as upward-facing or vertical where possible, although vertical walls still have layer lines.
- Parameter Tuning: Finer layer thicknesses can reduce stair-stepping but increase print time. Contour scanning parameters can sometimes improve side-wall finish.
- Post-Processing: Utilizing appropriate surface finishing techniques (machining, tumbling, blasting, polishing) targeted at critical areas requiring smooth finishes.
- Cracking:
- Issue: Cracks can form during printing (hot cracking) or after cooling (cold cracking) due to high residual stresses, particularly in certain alloys or complex geometries.
- Causes: High thermal gradients, material susceptibility (e.g., some aluminum or nickel alloys are more prone), high residual stress, inappropriate heat treatments.
- Mitigation / Solutions:
- Material Selection: Choosing alloys less prone to cracking if possible (Ti-6Al-4V and 17-4PH are generally manageable with good process control).
- Process Control: Utilizing platform heating (EBM), optimized scan strategies, and appropriate stress relief cycles immediately after printing.
- Design Modification: Avoiding sharp internal corners, incorporating generous fillets, designing for more uniform heat distribution.
- Appropriate Heat Treatment: Following validated heat treatment cycles precisely.
- Dimensional Inaccuracy:
- Issue: Parts deviating from the intended CAD dimensions beyond acceptable tolerances.
- Causes: Warping/distortion, inaccurate machine calibration, incorrect shrinkage compensation (especially Binder Jetting), thermal expansion effects.
- Mitigation / Solutions:
- Machine Calibration: Regular and thorough calibration of the AM system.
- Simulation & Compensation: Using simulation to predict shrinkage/distortion and applying compensation factors to the CAD model.
- Process Stability: Ensuring consistent powder quality, shielding gas, and process parameters throughout the build.
- Post-Machining: Planning for finish machining of critical dimensions.
Quality Assurance Framework:
Addressing these challenges requires a robust quality assurance framework encompassing:
- Powder Control: Incoming powder inspection (chemistry, PSD, morphology, flowability), proper storage, and traceability.
- Process Monitoring: In-situ monitoring capabilities (melt pool monitoring, thermal imaging) can help detect anomalies during the build.
- Post-Build Metrology: Thorough dimensional inspection using CMMs or 3D scanners.
- Material Testing: Regular testing of tensile properties, hardness, and microstructure from witness coupons printed alongside parts.
- NDT: Rigorous non-destructive testing (e.g., CT scanning for internal defects) appropriate for the criticality of the fastener.
- Documentation & Traceability: Maintaining detailed records for powder batches, machine parameters, build logs, post-processing steps, and inspection results for full aerospace traceability.
Successfully mitigating warping 3D printing issues, preventing porosity, and managing support structures are key to producing reliable AM aerospace fasteners. It requires a deep understanding of materials science, process physics, and diligent quality control. Partnering with suppliers like Met3dp, who invest heavily in process control, advanced equipment, high-quality powder production, and rigorous quality management systems, significantly reduces the risk associated with these challenges and ensures the delivery of fasteners meeting the demanding standards of the aerospace industry.
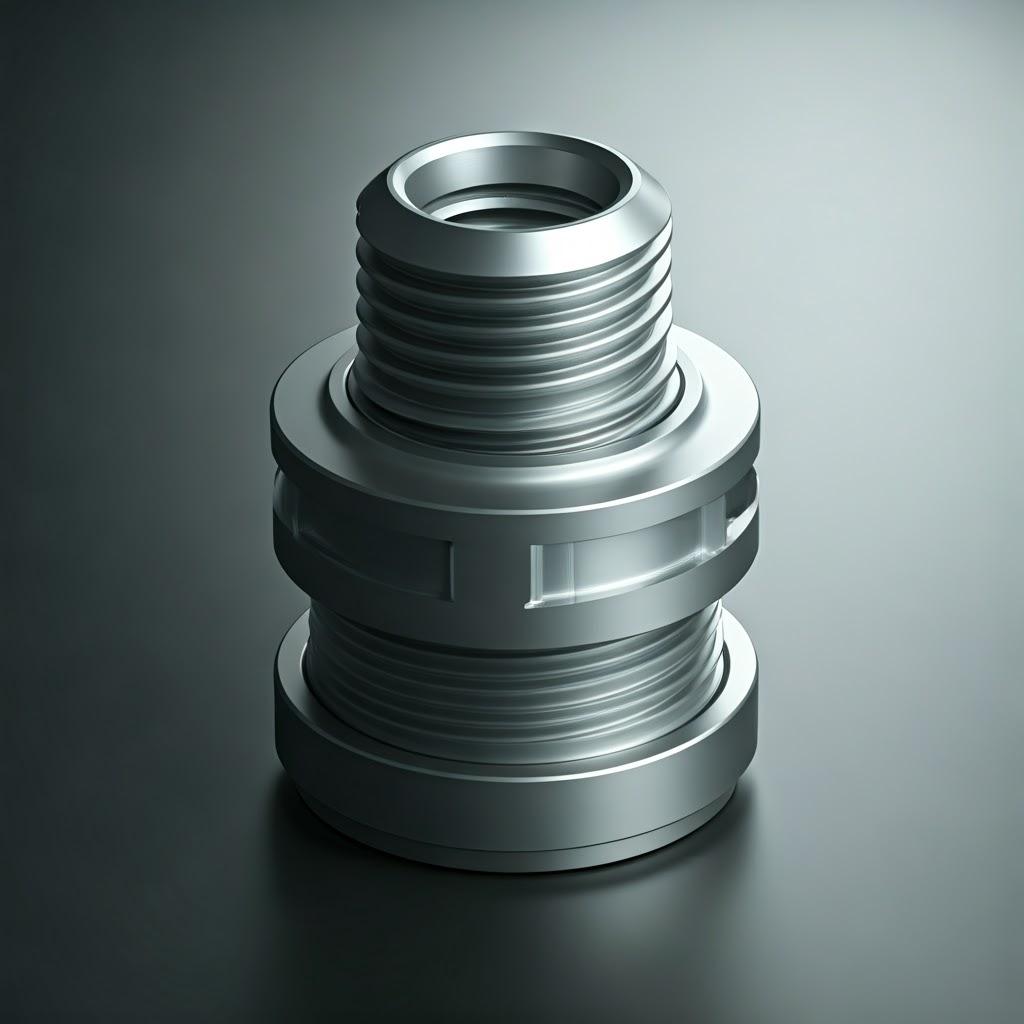
Supplier Selection: Choosing the Right Metal AM Partner for Aerospace Fasteners
The success of implementing additively manufactured fasteners in demanding aerospace applications hinges critically on the capabilities, expertise, and quality systems of your chosen manufacturing partner. Selecting the right aerospace additive manufacturing services provider is a crucial decision for both engineering teams designing the parts and procurement managers responsible for sourcing reliable, high-quality components. The unique aspects of AM require evaluating potential suppliers on criteria beyond those used for traditional machining or forging vendors.
When selecting metal 3D printing suppliers for critical components like aerospace fasteners, consider the following key factors:
- Technical Expertise and Engineering Support:
- DfAM Proficiency: Does the supplier have engineers experienced in Design for Additive Manufacturing, specifically for aerospace applications? Can they provide meaningful feedback on your designs to optimize for lightweighting, manufacturability, support minimization, and performance? Can they assist with topology optimization or complex geometry challenges?
- Materials Science Knowledge: Do they possess deep expertise in the specific materials required (e.g., Ti-6Al-4V, 17-4PH)? Do they understand the nuances of processing these materials via AM, including microstructure development, heat treatment response, and potential defects?
- Process Understanding: Are they experts in the specific AM technology (SLM, EBM) they operate? Do they have well-defined and validated process parameters for the required materials? Can they explain how their process control ensures part consistency?
- Problem-Solving Skills: Additive manufacturing can present unexpected challenges. Does the supplier have a proven ability to troubleshoot issues related to printability, quality, or post-processing?
- Equipment Capabilities and Technology:
- Machine Fleet: What types of metal AM systems do they operate (e.g., SLM, EBM)? Does the technology align with the requirements of your material and application (e.g., EBM’s advantages for stress-prone Ti-6Al-4V parts)?
- Build Volume: Do their machines have sufficient build volume to accommodate your fastener size and potentially allow for efficient batch production?
- Machine Maintenance & Calibration: Do they have rigorous procedures for machine maintenance and calibration to ensure consistent accuracy and performance?
- Powder Handling: What are their procedures for handling, storing, sieving, and recycling metal powders to prevent contamination and ensure powder quality throughout its lifecycle?
- Material Portfolio and Validation:
- Available Materials: Do they offer the specific aerospace-grade alloys you need (Ti-6Al-4V, 17-4PH, potentially others like Inconel 718/625, Aluminum alloys)?
- Material Validation: Have they validated their processes for these materials according to relevant aerospace standards? Can they provide material data sheets with mechanical properties derived from their specific machines and processes? Are they using high-quality powders with certified chemistry?
- Powder Sourcing & Quality: Do they source powders from reputable suppliers, or ideally, do they have control over powder production? Met3dp, for instance, stands out by not only providing printing services but also manufacturing its own high-quality, spherical metal powders using advanced Gas Atomization and PREP technologies. This integrated approach ensures optimal powder characteristics specifically tailored for AM, enhancing process stability and final part quality. Knowing the provenance and quality control behind the powder is critical.
- Quality Management System and Certifications:
- Aerospace Certification (AS9100): This is paramount for suppliers manufacturing flight-critical hardware. AS9100 certification demonstrates a robust quality management system tailored to the stringent requirements of the aerospace industry, covering aspects like traceability, process control, risk management, and configuration management. Ask potential suppliers about their certification status or their timeline for achieving it.
- ISO 9001: A fundamental quality management certification, indicating standardized processes and a commitment to quality.
- Traceability: Can the supplier provide full traceability from raw powder batch to the finished, shipped fastener, including all process parameters, post-processing steps, and inspection results? This is non-negotiable in aerospace.
- Inspection Capabilities: Do they have in-house capabilities for dimensional inspection (CMM, 3D scanning), surface finish measurement, and ideally, NDT (or strong partnerships with certified NDT providers)?
- Post-Processing Capabilities:
- In-House vs. Outsourced: Does the supplier perform critical post-processing steps like stress relief, heat treatment, HIP, machining, and surface finishing in-house, or do they rely on external partners?
- Control & Qualification: If outsourced, how do they qualify and manage their post-processing vendors to ensure consistency and adherence to specifications? Do they manage the entire workflow seamlessly?
- Expertise: Do they have expertise in the specific post-processing requirements for your chosen material and application (e.g., complex heat treatment cycles for Ti-6Al-4V, precision machining of AM parts)?
- Track Record and Experience:
- Aerospace Experience: Have they successfully produced parts, particularly fasteners or similar components, for other aerospace customers? Can they share (non-confidential) case studies or references?
- Project Management: Do they have a clear process for project management, communication, and reporting? How responsive are they to inquiries and technical questions?
- Capacity and Scalability: Can they handle your required production volumes, from prototypes to potentially larger batches? Do they have plans for capacity expansion if needed?
- Cost and Lead Time:
- Transparent Quoting: Is their quoting process clear and detailed, breaking down costs associated with printing, materials, supports, post-processing, and quality assurance?
- Competitive Pricing: Are their prices competitive relative to the value, quality, and expertise they offer? (Note: The cheapest option is rarely the best for critical aerospace parts).
- Reliable Lead Times: Can they provide realistic and reliable lead time estimates for prototyping and production runs? What is their track record for on-time delivery?
Evaluating Potential Suppliers – Key Questions:
Evaluation Area | Key Questions for Potential Suppliers | Why It Matters for Aerospace Fasteners |
---|---|---|
Technical Expertise | Describe your DfAM experience for aerospace. How do you validate material properties? Explain your process control for [Material X]. | Ensures optimized design, reliable material performance, print success. |
Quality & Certs | Are you AS9100 certified? Describe your traceability process. What NDT methods do you use/manage for fasteners? | Guarantees adherence to aerospace standards, ensures part integrity. |
Materials & Powder | Where do you source your [Material X] powder? What are your powder QC procedures? Can you share typical powder characteristics? | Powder quality directly impacts final part properties and consistency. |
Capabilities | What AM machines do you use? What is your build volume? What post-processing is done in-house vs. outsourced? | Ensures they have the right tools and control over the entire process. |
Experience | Can you share examples of similar aerospace parts you’ve produced? How do you handle project communication? | Demonstrates capability and reliability in a demanding industry. |
Cost & Lead Time | Provide a detailed cost breakdown. What factors influence lead time? What is your typical OTD rate? | Allows for accurate budgeting and project planning. |
Export to Sheets
Choosing a partner like Met3dp offers distinct advantages. With decades of collective expertise in metal AM, Met3dp provides comprehensive solutions spanning state-of-the-art SEBM printers, advanced metal powders manufactured in-house, and dedicated application development services. Our integrated approach, combining deep material science knowledge (especially in producing high-quality Ti-6Al-4V, 17-4PH, and novel alloys) with advanced printing technology, ensures a controlled and optimized path from design to finished fastener. We partner closely with organizations in aerospace and other demanding sectors to implement AM effectively and drive manufacturing innovation.
Understanding Costs and Timelines: Factors Influencing AM Fastener Production
While metal additive manufacturing unlocks significant performance and design benefits, understanding the associated costs and production timelines is crucial for project planning and budgeting. Both metal 3D printing cost aerospace applications and additive manufacturing lead times are influenced by a complex interplay of factors, distinct from those governing traditional manufacturing.
Factors Influencing Cost:
- Material Type and Consumption:
- Powder Cost: Aerospace-grade metal powders (especially Ti-6Al-4V, refractory metals, or specialized alloys) are significantly more expensive than standard engineering metals. The raw material cost is a major driver. 17-4PH is generally more cost-effective than Ti-6Al-4V.
- Part Volume & Weight: The actual amount of material used to print the fastener directly impacts cost. Larger or denser fasteners consume more expensive powder.
- Support Structure Volume: Material used for support structures also adds to the cost. Efficient DfAM aims to minimize support needs.
- Powder Recycling/Refresh Rate: Suppliers factor in the costs associated with powder handling, sieving, testing, and refreshing (mixing used powder with virgin powder) to maintain quality.
- Machine Time (Print Time):
- Part Height (Z-Height): Print time is heavily influenced by the number of layers required, meaning taller parts (oriented vertically) generally take longer to print than shorter parts, regardless of volume.
- Part Volume/Complexity: While height is primary, the area scanned per layer also affects time. Very complex geometries might require slower scan speeds for accuracy.
- Machine Hourly Rate: AM service providers have operational costs (machine depreciation, energy, labor, facility) factored into an hourly rate for machine usage.
- Build Preparation and Setup:
- CAD File Preparation: Time spent by engineers to check CAD files, perform DfAM analysis, generate support structures, slice the model, and create the build layout.
- Machine Setup: Time required to load powder, prepare the build plate, and initialize the printing process. These setup costs are amortized over the number of parts in a build.
- Post-Processing Requirements:
- Complexity & Labor: Each post-processing step (powder removal, stress relief, support removal, heat treatment, HIP, machining, finishing) adds labor and equipment time, contributing significantly to the final cost.
- Machining: CNC machining critical features can be a substantial cost component, depending on the complexity and number of features requiring machining.
- HIP: Hot Isostatic Pressing is an expensive process due to the specialized equipment and long cycle times, reserved for parts requiring the highest integrity.
- Finishing: The level of surface finishing required (e.g., basic tumbling vs. multi-stage polishing) impacts cost.
- Quality Assurance and Inspection:
- NDT Level: The extent and type of non-destructive testing required (e.g., visual vs. FPI vs. CT scanning) significantly affect cost. CT scanning, while providing invaluable internal inspection, is costly.
- Dimensional Inspection: Time required for CMM or 3D scanning inspection.
- Documentation: Generating comprehensive quality documentation and traceability reports required for aerospace adds overhead.
- Production Volume and Batching:
- Economies of Scale: AM costs per part generally decrease with larger batch sizes. Setup costs are amortized over more parts, and build platforms can be packed efficiently (nesting multiple parts) to maximize machine utilization. This is relevant for bulk custom fasteners pricing, although AM typically doesn’t reach the economies of scale seen in traditional high-volume fastener production.
- Prototypes vs. Production: Prototype costs per part are usually higher due to one-off setup and preparation efforts.
Factors Influencing Lead Time:
- Design and Pre-Processing:
- File Preparation: Time for DfAM checks, support generation, slicing, and build layout optimization (typically 1-3 days, depending on complexity).
- Quoting and Order Confirmation: Administrative time.
- Machine Queue:
- Waiting Time: Perhaps the most variable factor. Lead time depends on the supplier’s current machine backlog and job scheduling. This can range from days to several weeks.
- Print Time:
- Build Height & Volume: As discussed, taller builds take longer. A build containing multiple fasteners might run for anywhere from 12 hours to several days continuously.
- Machine Reliability: Unforeseen machine downtime can impact schedules.
- Post-Processing Time:
- Sequential Steps: Each post-processing step adds time (e.g., stress relief: hours; heat treatment: hours to days including furnace time; HIP: typically 1-2 days including cycle time; machining: hours to days depending on complexity; finishing: hours to days).
- Logistics: Time required to move parts between different processing stations or external vendors (if outsourcing).
- Vendor Queues: If post-processing steps like heat treatment or HIP are outsourced, lead times depend on the external vendor’s backlog.
- Inspection and Quality Control:
- Inspection Time: Time for dimensional checks, NDT, and report generation (can range from hours to days depending on requirements).
- Shipping:
- Transit Time: Time required for transportation from the supplier to the customer.
Typical Lead Time Ranges (Estimates):
- Prototypes (Simple): 1-2 weeks
- Prototypes (Complex, extensive post-processing): 2-4 weeks
- Low-Volume Production (Batch): 3-6 weeks (highly dependent on batch size, complexity, and post-processing)
Cost vs. Traditional Comparison:
- Low Volume / High Complexity: AM fasteners are often cost-competitive or even cheaper than traditionally manufactured counterparts due to the elimination of tooling costs and suitability for complex geometries.
- High Volume / Simple Geometry: Traditional methods (cold heading, machining) are typically much more cost-effective for standard, high-volume fasteners.
- Value Proposition: The decision often comes down to the value AM provides – weight savings, performance improvements, consolidation, rapid availability for custom parts – which can outweigh a potentially higher per-part cost compared to a standard fastener.
Understanding these cost and lead time drivers allows for better planning and communication with your AM supplier. Providing clear requirements, well-prepared CAD models, and realistic expectations helps streamline the process. Engaging with experienced providers like Met3dp early can help optimize designs not just for performance but also for manufacturing efficiency, potentially reducing both cost and lead time.
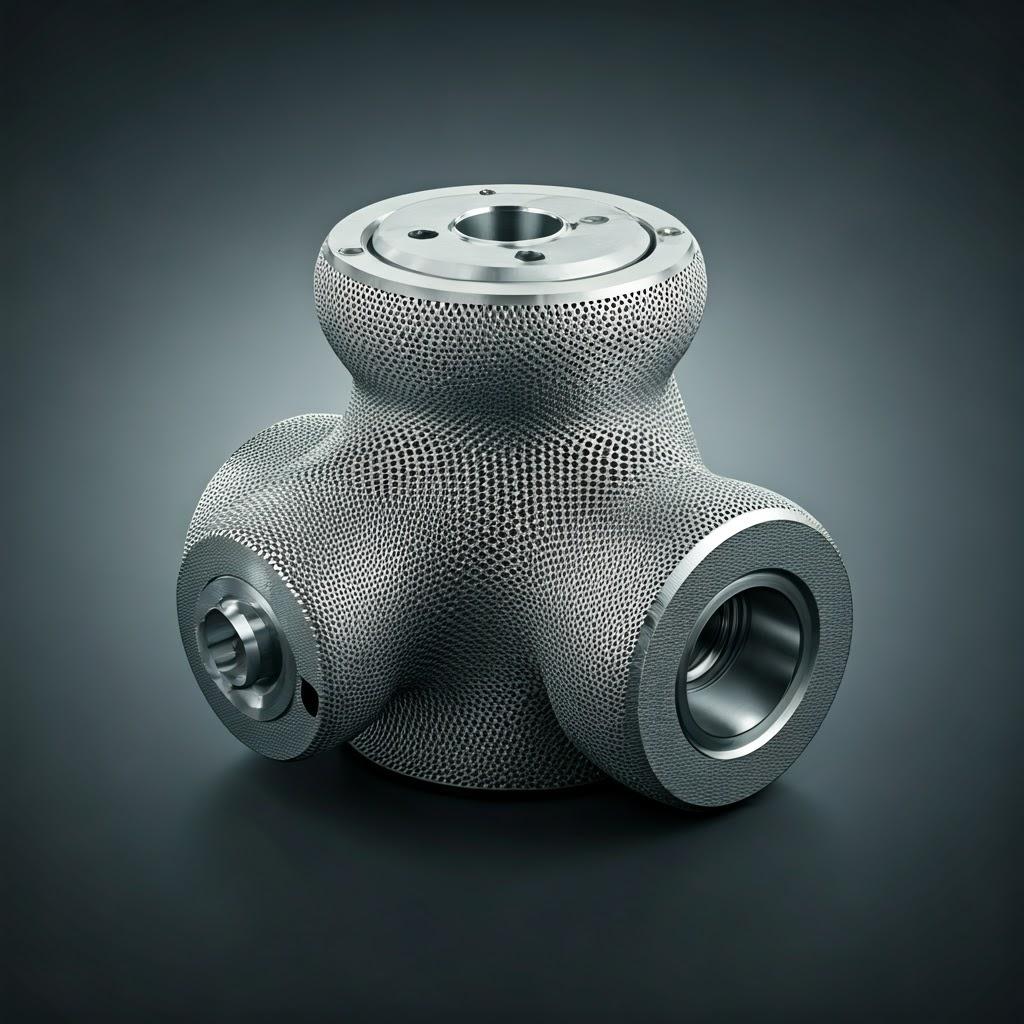
FAQ: Frequently Asked Questions about 3D Printed Aerospace Fasteners
As metal additive manufacturing becomes more prevalent in aerospace, engineers, designers, and procurement managers often have questions about the capabilities, limitations, and implementation of 3D printed fasteners. Here are answers to some frequently asked questions:
- Are 3D printed metal fasteners as strong and reliable as traditionally forged or machined fasteners?
- Answer: Yes, when produced correctly using qualified processes, materials, and post-processing, 3D printed metal fasteners can meet or even exceed the strength and reliability specifications of their traditional counterparts. Key factors include:
- Material Properties: Using high-quality, aerospace-grade powders (like Ti-6Al-4V or 17-4PH) and achieving near-full density (>99.5%, often enhanced by HIP) results in bulk material properties comparable to wrought or forged materials after appropriate heat treatment.
- Process Control: Strict control over printing parameters is essential to avoid defects like porosity or lack of fusion.
- Heat Treatment: Correct thermal post-processing (stress relief, STA, aging) is critical to develop the required microstructure and mechanical properties (tensile strength, yield strength, fatigue life).
- Design (DfAM): While AM allows lightweighting, the design must still account for stress concentrations and load paths. Optimized designs are validated through FEA and testing.
- Qualification: For critical applications, rigorous testing and qualification programs (following standards like MMPDS, CMH-17, or specific OEM requirements) are necessary to validate performance and ensure reliability, just as with any manufacturing process. Met3dp’s focus on high-quality powders and reliable printing systems provides a strong foundation for achieving these properties.
- Answer: Yes, when produced correctly using qualified processes, materials, and post-processing, 3D printed metal fasteners can meet or even exceed the strength and reliability specifications of their traditional counterparts. Key factors include:
- How is the quality and airworthiness of 3D printed aerospace fasteners certified?
- Answer: Certification of 3D printed aerospace parts, including fasteners, follows a rigorous, multi-faceted approach, often more complex than for traditional parts initially. Certification 3D printed aerospace parts involves:
- Process Qualification: The entire manufacturing process (specific machine, material batch, parameter set, post-processing steps) must be stringently qualified and locked. This involves demonstrating process stability and repeatability.
- Material Qualification: Extensive testing (tensile, fatigue, fracture toughness, microstructure analysis) is performed on witness coupons printed alongside parts and on initial qualification parts to establish material property allowables, often adhering to industry standards (e.g., AMS specifications for AM materials) or specific OEM requirements.
- Part Qualification: Specific fastener designs undergo testing (dimensional checks, NDT, proof load tests, vibration tests, fatigue tests) to verify they meet all performance requirements.
- Quality Management System: The manufacturer must operate under a certified QMS, ideally AS9100 for aerospace, ensuring traceability, process control, configuration management, and operator qualification.
- Regulatory Approval: Depending on the criticality (e.g., flight-critical vs. secondary structure), approval from regulatory bodies like the FAA or EASA is required, often based on demonstrating equivalence or superiority to existing certified parts or through a dedicated certification plan.
- Answer: Certification of 3D printed aerospace parts, including fasteners, follows a rigorous, multi-faceted approach, often more complex than for traditional parts initially. Certification 3D printed aerospace parts involves:
- What is the typical cost difference between custom aerospace fasteners made by AM versus traditional machining?
- Answer: The cost comparison is highly dependent on several factors:
- Complexity: For highly complex, topology-optimized, or functionally integrated fasteners that are difficult or impossible to machine, AM is often the only viable option, making direct cost comparison less relevant than evaluating the value added (e.g., weight savings).
- Volume: For very low volumes (e.g., prototypes, 1-10 parts), AM is frequently cheaper than machining due to the absence of setup/tooling costs associated with traditional methods. For medium volumes (tens to hundreds), the costs can be comparable, depending on complexity. For high volumes (thousands), traditional machining or forging of simpler designs is almost always significantly cheaper.
- Material: Machining expensive materials like titanium results in significant waste (poor buy-to-fly ratio), making AM’s better material utilization more cost-effective in some scenarios, despite higher powder costs.
- Specific Design: A simple standard bolt is cheaper to machine; a custom lightweight bracket with integrated threads is likely cheaper via AM.
- Rule of Thumb: AM is most cost-effective for high-complexity, low-to-medium volume custom fasteners, especially when lightweighting or part consolidation provides significant system-level benefits. Always obtain quotes for both methods if feasible for a direct comparison based on your specific part.
- Answer: The cost comparison is highly dependent on several factors:
- What information does an AM service provider need to provide an accurate quote for printing aerospace fasteners?
- Answer: To get an accurate quote, provide as much detail as possible:
- 3D CAD Model: A high-quality CAD model in a standard format (e.g., STEP, IGES).
- Material Specification: Clearly define the required alloy (e.g., Ti-6Al-4V Grade 5, 17-4PH Condition H900) and any relevant material standards (e.g., AMS).
- Technical Drawing: A 2D drawing specifying critical dimensions, tolerances, surface finish requirements (Ra values) for specific surfaces, thread specifications (e.g., UNJF-3A), and any geometric dimensioning and tolerancing (GD&T).
- Quantity: Number of parts required (for prototypes and potential production volumes).
- Post-Processing Requirements: Specify all required steps: stress relief, heat treatment condition (e.g., STA, H1025), HIP (if needed), specific machining operations, surface finish requirements, NDT methods (VT, FPI, CT), and any coating/plating needs.
- Quality & Certification Requirements: Detail any specific quality standards (e.g., AS9100), required documentation (Certificates of Conformance, material certs, inspection reports), and traceability needs.
- Application Context (Optional but helpful): Briefly describing the fastener’s application can help the provider understand criticality and offer better DfAM advice.
- Answer: To get an accurate quote, provide as much detail as possible:
Conclusion: Elevating Aerospace Design and Performance with AM Fasteners
The aerospace industry’s relentless pursuit of lighter, faster, and more efficient aircraft and spacecraft demands continuous innovation in materials and manufacturing. Metal additive manufacturing has emerged as a transformative technology, offering unprecedented capabilities for producing lightweight aerospace fasteners and other critical components. By moving beyond the constraints of traditional manufacturing, AM enables engineers to design and create fasteners optimized for specific load paths, integrated with other functionalities, and produced from high-performance alloys like Ti-6Al-4V and 17-4PH with remarkable efficiency, especially for custom and low-volume requirements.
The advantages are clear: significant weight reduction through topology optimization and DfAM, accelerated prototyping and development cycles, the ability to consolidate multiple parts into single complex components, and enhanced supply chain flexibility through on-demand production. While challenges related to precision, post-processing, and quality assurance exist, they are being systematically addressed through advancements in technology, materials science, process control, and the development of robust industry standards.
Successfully leveraging AM for aerospace fasteners requires a holistic approach – embracing DfAM principles early in the design phase, carefully selecting the optimal material for the application, understanding the necessary post-processing steps, and implementing rigorous quality control measures. Crucially, it involves partnering with the right aerospace additive manufacturing services provider – one with proven expertise, validated processes, certified quality systems, and the right technological capabilities.
Met3dp is committed to being such a partner. Our unique position as both a manufacturer of industry-leading metal AM systems (like SEBM printers optimized for aerospace alloys) and a producer of high-quality spherical metal powders allows us to offer comprehensive, integrated Met3dp additive manufacturing solutions. We collaborate with aerospace companies to push the boundaries of design and manufacturing, helping them realize the full potential of AM for fasteners and beyond. From initial concept and DfAM consultation to powder selection, printing, post-processing, and quality validation, we provide the expertise and capabilities needed to navigate the complexities of AM and deliver reliable, high-performance components.
The future of aerospace manufacturing is undoubtedly intertwined with additive technologies. As AM continues to mature, offering greater speed, precision, and material options, its role in producing not just prototypes but flight-certified production parts, including advanced fastener technology, will only expand. By embracing AM, aerospace companies can unlock new levels of design freedom, enhance vehicle performance, reduce lead times, and build more resilient supply chains, ultimately shaping the next generation of flight.
Explore how Met3dp’s capabilities can power your organization’s additive manufacturing goals by visiting our website at https://met3dp.com/.
Share On
MET3DP Technology Co., LTD is a leading provider of additive manufacturing solutions headquartered in Qingdao, China. Our company specializes in 3D printing equipment and high-performance metal powders for industrial applications.
Inquiry to get best price and customized Solution for your business!
Related Articles
About Met3DP
Recent Update
Our Product
CONTACT US
Any questions? Send us message now! We’ll serve your request with a whole team after receiving your message.
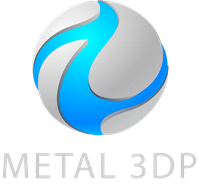
Metal Powders for 3D Printing and Additive Manufacturing