Aluminum Additive Manufacturing
Table of Contents
Overview of Aluminum Additive Manufacturing
Aluminum additive manufacturing, also known as 3D printed aluminum, refers to the process of creating aluminum parts layer by layer using 3D printing technologies. It allows for the creation of complex geometries and customized aluminum parts without the need for traditional machining methods.
Some key details about aluminum additive manufacturing:
- Used across industries like aerospace, automotive, medical, consumer products for prototypes, tooling, and end-use parts
- Provides design freedom, reduces weight, consolidates assemblies into one piece
- Produces strong, durable aluminum parts with material properties similar to traditional manufacturing
- Uses metal 3D printing technologies like powder bed fusion, directed energy deposition
- Aluminum alloys like AlSi10Mg, Scalmalloy, Al6061 are commonly used
- Post-processing like hot isostatic pressing, CNC machining required to achieve final part quality
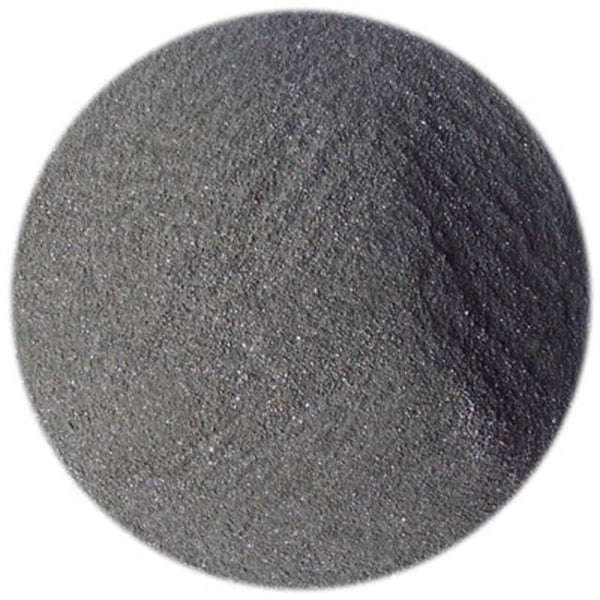
Aluminum Additive Manufacturing Equipment Types
Equipment Type | Description | Materials | Build Size | Accuracy | Surface Finish | Cost |
---|---|---|---|---|---|---|
Powder Bed Fusion | Uses laser or electron beam to selectively melt and fuse metallic powder layers | Aluminum alloys, titanium, steels, superalloys | Small to medium | High (up to 0.1mm) | Rough as-printed, good after machining | High (>$500K machine) |
Directed Energy Deposition | Focuses energy source like laser/electron beam on specific spots while filler metal powder is added to build the part | Aluminum alloys, titanium, steels, superalloys | Medium to large | Medium (0.5mm to 1mm) | Rough as-printed, fair after machining | High (>$500K machine) |
Binder Jetting | Binds metallic powder using liquid bonding agent, sinters part after printing | Aluminum alloys, steels | Medium | Medium (0.5mm to 1mm) | Rough (requires infiltrating alloy) | Lower ($150K to $300K machine) |
Applications of Aluminum Additive Manufacturing
Industry | Application Examples | Benefits |
---|---|---|
Aerospace | Aircraft and rocket engine parts, brackets, supportive structures | Lightweighting, custom geometries |
Automotive | Custom brackets, heat exchangers, jigs and fixtures | Consolidated assemblies, rapid prototyping |
Medical | Dental copings, orthopedic implants, surgical instruments | Biocompatible, customized sizing |
Consumer products | Drone frames, sporting goods, fashion accessories | Short run production, rapid design iteration |
Tooling | Injection molds, jigs, fixtures, gauges | Faster and cheaper than traditional tooling |
Aluminum Additive Manufacturing Specifications
Parameter | Details |
---|---|
Materials | Aluminum alloys: AlSi10Mg, Al6061, Scalmalloy, custom alloys |
Part Sizes | Up to 500mm x 500mm x 500mm for powder bed fusion <br> 1m x 1m x 1m for directed energy deposition |
Layer Resolution | 20 microns to 100 microns typical |
Surface Finish | As-printed: Ra 10-25 microns <br> Machined: Ra 0.4 – 6.3 microns |
Mechanical Properties | Tensile strength: 330-470 MPa <br> Yield strength: 215-350 MPa <br> Elongation at break: 3-8% |
Accuracy | ± 100 microns for powder bed fusion <br> ± 300 microns for binder jetting <br>± 500 microns for directed energy deposition |
Design Standards | ISO/ASTM 52900: Additive manufacturing design requirements <br> ISO/ASTM 52921: Standard for metal powder bed fusion process |
Aluminum Additive Manufacturing Suppliers and Costs
Supplier | Equipment Brands | Average Part Cost |
---|---|---|
3D Systems | DMP, Figure 4 | $8-$12 per cm3 |
EOS | EOS M series | $6-$10 per cm3 |
GE Additive | Concept Laser M2, X Line 2000R | $8-$15 per cm3 |
Velo3D | Velo3D Sapphire | $20+ per cm3 |
Part costs depend on build rates, materials used, geometric complexity, post-processing needs, and order quantities. In general, aluminum additive manufacturing provides cost savings for low volume production, typically less than 10,000 units.
Aluminum Additive Manufacturing Installation Requirements
Parameter | Requirements |
---|---|
Facility Type | Dedicated metal AM facility with climate control, powder handling stations |
Power Supply | 200V to 480V, 30 to 150 kW, 30 to 70A per machine |
Gas Supply | Argon, nitrogen for powder bed fusion <br> Argon for directed energy deposition |
Exhaust Systems | Fume extraction systems, HEPA filters for powder particulates |
Software | CAD, AM machine control software like Materialise Magics, Autodesk Netfabb |
Post-Processing | Hot isostatic press, blast booth, CNC machining |
A clean, temperature-controlled environment between 15-30°C is recommended for metal additive manufacturing. Proper facilities for powder storage, handling, and waste management must also be provisioned.
Aluminum Additive Manufacturing Operation and Maintenance
Activities | Frequency |
---|---|
Calibration | Daily laser power checks, quarterly calibration |
Material management | Checking powder Sieve analysis, morphology quarterly |
Equipment service | Clean optics, filters, daily to weekly <br> Replace consumables like wipers, filters <br> Preventive maintenance per OEM schedule |
Software updates | Regular firmware, software updates |
Facility maintenance | Check heating, cooling, exhaust systems <br> Clean powder handling stations |
Daily cleaning of equipment and monitoring of all systems is critical. Staff training and PPE for handling metal powders is mandatory. Follow OEM guidelines for preventive maintenance and calibration.
Choosing an Aluminum Additive Manufacturing Partner
When selecting an AM service provider for aluminum parts, consider the following:
- AM process experience – look for years in business, case studies in aluminum specifically
- Materials and post-processing capabilities – aluminum alloys, HIP, heat treatments, machining
- Quality certifications – ISO 9001, ISO/IEC 17025, Nadcap
- Design expertise – can they optimize parts for AM?
- Equipment installed – modern, well-maintained machines
- Post-processing equipment – what do they have in-house?
- Quick turnaround for prototyping needs
- Scalability for production – can they meet volumes?
- Location and logistics – helpful if close by
- Cost competitiveness – transparent quoting, economical for project scope
- Customer reviews – search online or ask for references
Pros and Cons of Aluminum Additive Manufacturing
Advantages | Disadvantages |
---|---|
Complex geometries, consolidates assemblies | Limited size based on build volume |
Lightweighting, reduced part count | Post-processing increases lead time |
Rapid prototyping, digital inventory | Higher cost than traditional methods for large volumes |
Design freedom, optimized shapes | Lower elongation compared to wrought alloys |
Minimal material waste | Anisotropic properties in horizontal vs vertical |
Shorten development timelines | Porosity issues may require hot isostatic pressing |
Toolless manufacturing, no fixtures needed | Specific training and facilities for metal AM |
Aluminum AM provides benefits like design flexibility, part consolidation, and rapid turnaround times. But it also requires specialized equipment and expertise. Thorough process understanding is must to produce end-use parts.
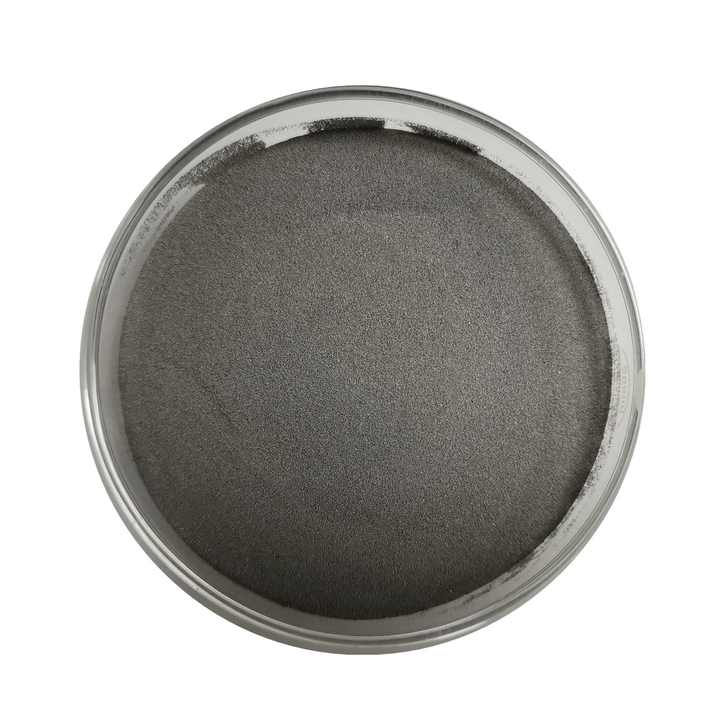
FAQs
What are the different aluminum alloys used in additive manufacturing?
Some common aluminum alloys used are:
- AlSi10Mg – Excellent strength and surface finish. Most popular aluminum alloy in AM.
- Al6061 – Higher strength alloy with good corrosion resistance. Readily available.
- Scalmalloy – Aluminum alloy developed by Airbus with high strength and ductility.
- Custom alloys – Can be designed to optimize certain properties. Requires R&D.
What post-processing is required for aluminum AM parts?
Common post-processing steps include:
- Remove from build plate
- Shot peening or bead blasting to smooth surface
- Hot isostatic pressing to improve density
- Heat treatments for optimal mechanical properties
- CNC machining – drilling, tapping, milling for dimensional accuracy
- Surface treatments – anodizing, powder coating for aesthetics
How does the cost of aluminum AM compare to CNC machining?
For low volume production (under 100 parts), AM is generally more cost effective than CNC machining. There is no tooling required and lead times are faster. For higher volumes above 1000 units, CNC machining has lower costs due to material waste with AM. Hybrid approaches combining AM and machining can provide cost-effective solutions for medium volumes.
What size aluminum parts can be built with metal 3D printing?
For powder bed technologies like DMLS and EBM, maximum part size is around 500mm x 500mm x 500mm. Large format machines exceed 1m x 1m x 1m build dimensions. Binder jetting and directed energy deposition have fewer size limitations, with some machines allowing meter-scale parts.
What surface finish can be expected with aluminum additive manufacturing?
The as-printed surface finish with AM is relatively rough at around Ra 10-25 microns. Various finishing operations can improve this significantly:
- CNC machining – Ra 0.4 to 6.3 microns
- Polishing – Ra < 1 micron
- Anodizing – smooth uniform surface for enhanced corrosion resistance
With the right post-processing, aluminum AM parts can achieve a smooth surface finish comparable to traditional manufacturing.
What industries use aluminum additive manufacturing?
Key industries adopting aluminum AM include:
- Aerospace – Aircraft components, brackets, engine parts
- Automotive – Heat exchangers, custom supports, tooling
- Medical – Dental copings, implants, surgical instruments
- Consumer goods – Drone components, sporting equipment, gadgets
- Industrial – End-use jigs, fixtures for manufacturing and assembly
Aluminum AM enables lightweight, optimized designs across these segments.
What expertise is required for in-house aluminum AM?
Successfully implementing in-house aluminum AM requires:
- AM engineers to optimize builds and qualify processes
- Technicians for equipment operation and maintenance
- Quality team to validate parts and procedures
- Powder handling technicians trained in health and safety
- Facilities team to provision power, cooling, gas supply and exhaust
- Software, network support for AM data management
A cross-functional team approach is recommended to build AM expertise across the organization.
What standards apply to aluminum additive manufacturing?
Key standards include:
- ISO/ASTM 52900 – Standard terminology for AM
- ISO/ASTM 52921 – Standard for powder bed fusion process equipment
- ASTM F3001 – Standard for AM medical parts
- ASTM F3301 – Standard for directed energy deposition AM metals
- ASTM F3302 – Standard for binder jetting AM metals
Certifying parts to these standards demonstrates quality management and compliance.
Conclusion
Aluminum additive manufacturing enables lightweight, optimized aluminum components across aerospace, automotive, medical and consumer goods sectors. With the right process knowledge and expertise, end-use aluminum parts can be produced using the layer-based flexibility of 3D printing. As aluminum AM technology matures, costs will decrease and adoption will continue rising for this versatile metal material.
Share On
MET3DP Technology Co., LTD is a leading provider of additive manufacturing solutions headquartered in Qingdao, China. Our company specializes in 3D printing equipment and high-performance metal powders for industrial applications.
Inquiry to get best price and customized Solution for your business!
Related Articles
About Met3DP
Recent Update
Our Product
CONTACT US
Any questions? Send us message now! We’ll serve your request with a whole team after receiving your message.
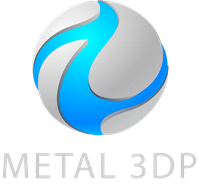
Metal Powders for 3D Printing and Additive Manufacturing