The application of aluminum alloy 3D metal powder in the aerospace
Table of Contents
The quest for lighter, stronger, and more efficient aircraft has been a constant theme in the history of aerospace engineering. In this relentless pursuit, aluminum alloys have long been a champion. However, traditional manufacturing techniques often present limitations in terms of design complexity and material waste. This is where 3D metal printing, also known as Additive Manufacturing (AM), steps in – and aluminum alloy 3D metal powder becomes the gamechanger.
Aluminum Alloy 3D Metal Powder: A Recipe for Innovation
Aluminum alloy 3D metal powder is a revolutionary material specifically designed for use in 3D printing processes. It consists of fine, spherical aluminum alloy particles produced through various techniques like gas atomization or water atomization. These meticulously crafted particles are the building blocks for creating complex, lightweight, and high-performance aerospace components.
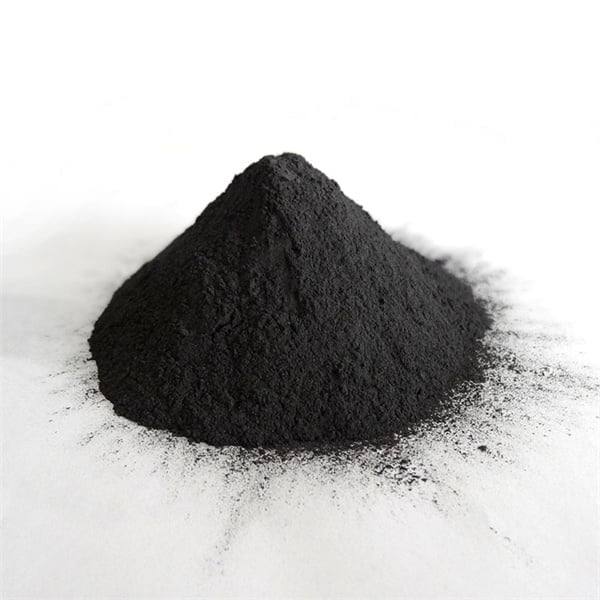
Common Aluminum Alloy 3D Metal Powders and their Properties
Aluminum Alloy Powder | Description | Properties | Applications in Aerospace |
---|---|---|---|
AA2024 | A widely used aluminum-copper-magnesium alloy known for its good strength-to-weight ratio and machinability. | – High strength – Good fatigue resistance – Moderate corrosion resistance | – Aircraft wings and fuselages (non-critical components) – Wing ribs and stringers – Aerospace ducting |
AA6061 | A versatile aluminum-magnesium-silicon alloy known for its excellent formability, weldability, and corrosion resistance. | – Good strength – Excellent corrosion resistance – Good machinability | – Non-structural aircraft components – Housings and brackets – Interior components |
AA7075 | A high-strength aluminum-zinc-magnesium alloy offering superior strength-to-weight ratio but lower corrosion resistance compared to AA2024 and AA6061. | – Very high strength – Excellent fatigue resistance – Moderate corrosion resistance | – Landing gear components – High-stress wing components – Aerospace fasteners |
Scalmalloy | A proprietary aluminum-scandium alloy developed by Airbus, offering exceptional strength-to-weight ratio and improved performance at elevated temperatures. | – Superior strength-to-weight ratio compared to AA7075 – Excellent high-temperature performance – Good weldability | – Highly stressed aerospace components – Fighter jet components – Spacecraft structural elements |
AMSL 319 | A silicon-based aluminum alloy specifically formulated for Laser Beam Melting (LBM) 3D printing, offering good mechanical properties and castability. | – Excellent castability – Good strength and ductility – Relatively low melting point | – Engine crankcases and cylinder heads – Heat exchanger components – Missile bodies |
Maraging Aluminum | A family of high-strength aluminum alloys containing elements like copper, titanium, and zirconium, offering exceptional strength after heat treatment. | – Extremely high strength – Good ductility – Excellent corrosion resistance | – Highly stressed aerospace components – Landing gear components – Military aircraft structures |
AlSi10Mg | A widely used aluminum-silicon-magnesium alloy known for its good castability, machinability, and weldability. | – Good castability – Excellent machinability – Moderate strength | – Non-structural aerospace components – Housings and brackets – Heat exchanger components |
AlSi7Mg0.3 | Another variant of the AlSi family, offering a good balance between castability and mechanical properties. | – Good castability – Moderate strength and ductility – Improved corrosion resistance compared to AlSi10Mg | – Non-structural aerospace components – Housings and brackets – Engine components |
A357 | A silicon-aluminum alloy with excellent castability and wear resistance, suitable for LBM 3D printing. | – Excellent castability – Good wear resistance – Moderate strength | – Engine components – Cylinder heads and pistons – Wear-resistant components |
HX200 | A novel aluminum alloy developed by Norsk Titanium, offering a unique combination of high strength, good ductility, and excellent fatigue performance. | – Exceptional strength and ductility – Superior fatigue resistance – Good weldability | – Highly stressed aerospace components – Critical wing and fuselage structures – Spacecraft components |
Unveiling the Advantages: Why Aluminum Alloy 3D Metal Powder Takes Flight
The marriage of aluminum alloys and 3D printing technology unlocks a treasure trove of benefits for the aerospace industry. Here’s a closer look at why aluminum alloy 3D metal powder is soaring high:
- Lightweight Design: Aluminum itself is a lightweight metal, but 3D printing takes it a step further. Unlike traditional manufacturing methods that generate significant scrap, 3D printing allows for the creation of intricate, hollow structures with minimal material waste. This translates to lighter aircraft components, which in turn, reduces fuel consumption, increases payload capacity, and extends flight range. Imagine a scenario where an airplane could carry more passengers or cargo further, thanks to lighter components made possible by 3D printed aluminum alloy powder.
- Design Freedom and Complexity: Traditional manufacturing techniques like machining and forging can be restrictive when it comes to complex geometries. 3D printing breaks these shackles, allowing engineers to design intricate lattice structures, internal channels, and weight-optimized components that were previously impossible to manufacture. This design freedom opens doors for enhanced aerodynamics, improved heat dissipation, and even the creation of multifunctional components that integrate multiple functionalities within a single piece.
- Faster Time to Market: The traditional development cycle for new aircraft involves lengthy prototyping and tooling phases. 3D printing disrupts this timeline by enabling rapid prototyping of complex parts. This allows engineers to iterate on designs quickly, test them virtually, and move to production faster. Faster time to market translates to quicker response times to market demands and a competitive edge for aerospace manufacturers.
- Material Efficiency and Reduced Waste: As mentioned earlier, 3D printing minimizes material waste by building components layer-by-layer with minimal leftover material. This not only reduces costs but also aligns with the growing focus on sustainable manufacturing practices within the aerospace industry.
- Inventory Optimization: 3D printing eliminates the need for extensive warehousing of pre-manufactured parts. Aerospace companies can leverage 3D printing to produce parts on-demand, reducing storage requirements and simplifying logistics. Imagine a scenario where spare parts for an aircraft can be 3D printed at the maintenance hangar itself, minimizing downtime and streamlining operations.
Where Aluminum Alloy 3D Metal Powder Takes Shape in Aerospace
The potential applications of aluminum alloy 3D metal powder in aerospace are vast and ever-expanding. Here are some key areas where this technology is making significant strides:
- Aircraft Engine Components: Aluminum alloy 3D metal powder is finding its way into various engine components, including crankcases, cylinder heads, and heat exchangers. The ability to create complex internal channels for improved cooling and lightweight design makes it an ideal choice for optimizing engine performance.
- Aircraft Fuselage Skin: Certain non-critical sections of the aircraft fuselage can be manufactured using 3D printed aluminum alloy panels. These panels can be lighter and potentially integrate functionalities like heat dissipation channels, reducing the need for additional components.
- Aircraft Landing Gear: Landing gear components experience significant stress during take-off and landing. High-strength aluminum alloys like Scalmalloy and Maraging Aluminum can be 3D printed to create lightweight yet robust landing gear components.
- Aerospace Ducting: The intricate network of ducts within an aircraft plays a crucial role in managing airflow and temperature. 3D printing allows for the creation of lightweight, complex ducting systems with optimized flow characteristics.
- Interior Components: From lightweight brackets and housings to customized passenger amenities, 3D printed aluminum alloy components can enhance the functionality and aesthetics of aircraft interiors.
Considering the Challenges: A Reality Check
While the potential of aluminum alloy 3D metal powder in aerospace is undeniable, there are challenges to consider:
- Powder Qualification and Consistency: The quality and consistency of the 3D metal powder play a vital role in the final product’s properties. Ensuring consistent powder flow and adherence to strict quality control measures is crucial.
- Machine Capability and Expertise: 3D printing aluminum alloys requires specialized printers and skilled operators. Investing in the right equipment and training personnel is essential for successful implementation.
- Post-Processing Requirements: 3D printed aluminum parts may require post-processing steps like heat treatment or surface finishing to achieve the desired mechanical properties.
- Part Qualification and Certification: Aerospace components are subject to stringent regulations and certification processes. Qualifying 3D printed aluminum parts for flight use requires rigorous testing and approval procedures.
The Future of Aluminum Alloy 3D Metal Powder in Aerospace
The future of aluminum alloy 3D metal powder in aerospace is bright. As the technology matures, we can expect to see:
- Development of New and Improved Aluminum Alloys: Material scientists are continuously developing new aluminum alloys specifically optimized for 3D printing, offering even better strength-to-weight ratios, improved printability, and enhanced performance at high temperatures.
- Standardization and Certification Streamlining: Regulatory bodies are working on streamlining the qualification and certification process for 3D printed aerospace components. This will encourage wider adoption of the technology by reducing time and cost associated with part approval.
- Advancements in 3D Printing Technology: Continuous advancements in 3D printing technology, including faster printing speeds, larger build volumes, and multi-material printing capabilities, will further unlock the potential of aluminum alloy 3D metal powder in aerospace applications.
- Integration with Design and Manufacturing workflows: Seamless integration of 3D printing with design and manufacturing software will create a more efficient workflow, allowing engineers to design, simulate, and print complex aluminum components directly from within their design environment.
- Cost Reduction and Wider Adoption: As the technology matures and production volumes increase, the cost of 3D printed aluminum components is expected to decrease. This will make 3D printing a more viable option for a wider range of aerospace applications.
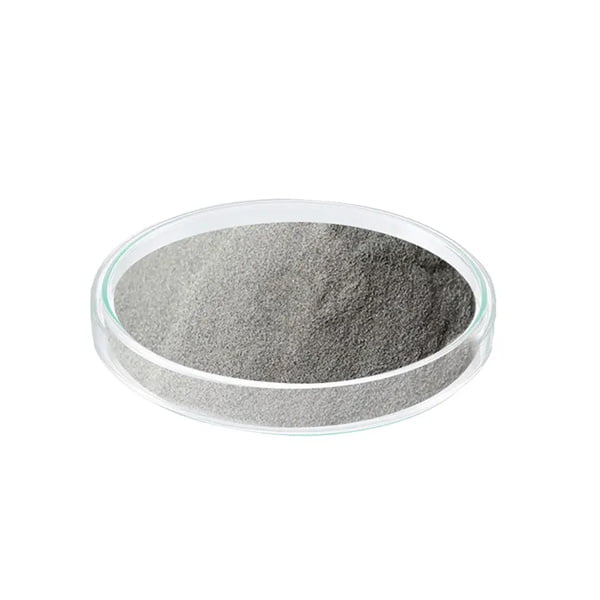
FAQ
Q: What are the advantages of using aluminum alloy 3D metal powder in aerospace compared to traditional manufacturing techniques?
A: Aluminum alloy 3D metal powder offers several advantages, including:
- Lighter weight components leading to improved fuel efficiency and increased payload capacity.
- Design freedom for creating complex geometries and multifunctional components.
- Faster time to market through rapid prototyping and on-demand production.
- Reduced material waste for a more sustainable manufacturing process.
- Optimized inventory management through on-demand part production.
Q: What are the limitations of using aluminum alloy 3D metal powder in aerospace?
A: Some limitations to consider include:
- The need for strict quality control measures to ensure consistent powder properties.
- Investment in specialized 3D printers and training for skilled operators.
- Potential post-processing requirements to achieve desired mechanical properties.
- Stringent part qualification and certification processes for flight use.
Q: What are some of the future trends for aluminum alloy 3D metal powder in aerospace?
A: The future is promising with potential for:
- Development of new and improved aluminum alloys specifically designed for 3D printing.
- Streamlined certification processes for faster adoption of 3D printed components.
- Advancements in 3D printing technology for faster speeds, larger build volumes, and multi-material capabilities.
- Improved integration with design and manufacturing workflows for a more efficient process.
- Cost reduction leading to wider adoption of 3D printed aluminum components across various aerospace applications.
In Conclusion
Aluminum alloy 3D metal powder is revolutionizing the way aircraft are designed and manufactured. By leveraging the unique advantages of this technology, the aerospace industry can achieve significant advancements in lightweight design, part complexity, production efficiency, and sustainability. As the technology matures and challenges are addressed, we can expect to see aluminum alloy 3D metal powder playing an even greater role in shaping the future of flight.
Share On
MET3DP Technology Co., LTD is a leading provider of additive manufacturing solutions headquartered in Qingdao, China. Our company specializes in 3D printing equipment and high-performance metal powders for industrial applications.
Inquiry to get best price and customized Solution for your business!
Related Articles
About Met3DP
Recent Update
Our Product
CONTACT US
Any questions? Send us message now! We’ll serve your request with a whole team after receiving your message.
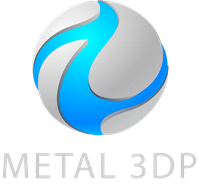
Metal Powders for 3D Printing and Additive Manufacturing