Lightweight Antenna Mounts via Aluminum 3D Printing
Table of Contents
Introduction: Revolutionizing Antenna Mounts with Lightweight Aluminum 3D Printing
In countless applications across aerospace, automotive, telecommunications, and defense industries, antennas are the critical link for communication, navigation, and sensing. However, the performance of these antennas often depends significantly on their mounting structures. Traditional antenna mounts, typically manufactured through methods like CNC machining from billet or casting, often face limitations in terms of weight, design complexity, production speed, and cost-effectiveness, especially for low-to-medium volume or highly customized requirements. Heavy mounts can negatively impact the overall system performance, particularly in weight-sensitive applications like satellites, unmanned aerial vehicles (UAVs), and high-performance vehicles. Furthermore, complex geometries required for optimal positioning, signal integrity, or integration into tight spaces can be difficult or prohibitively expensive to achieve using conventional techniques. Procurement managers and engineers constantly seek innovative manufacturing solutions that address these challenges, enabling lighter, stronger, and more functional component designs while optimizing supply chain efficiency and reducing total cost of ownership.
Enter the transformative power of metal additive manufacturing (AM), specifically using advanced aluminum alloys. Metal 3D printing, often referred to as techniques like Selective Laser Melting (SLM) or Direct Metal Laser Sintering (DMLS) – both forms of Powder Bed Fusion (PBF-LB) – offers a paradigm shift in how antenna mounts are designed, developed, and produced. By building parts layer by layer directly from metal powder, AM unlocks unprecedented design freedom, enabling the creation of highly complex, topology-optimized, and lightweight structures that were previously impossible or impractical to manufacture. Aluminum alloys, particularly high-performance formulations like AlSi10Mg and Scalmalloy®, are ideal candidates for these applications due to their inherent low density combined with excellent mechanical properties achievable through AM processes. This combination allows engineers to design antenna mounts that significantly reduce overall system weight – a critical factor in aerospace and automotive sectors – without compromising structural integrity or performance requirements. For B2B clients, including wholesale buyers and distributors looking for reliable component suppliers, aluminum 3D printing offers a compelling value proposition: customized solutions, rapid prototyping capabilities, consolidated parts leading to simpler assembly, and the potential for on-demand production, mitigating inventory risks and shortening lead times.
Companies like Met3dp are at the forefront of this manufacturing revolution. Headquartered in Qingdao, China, Met3dp is not just a service provider but a comprehensive solutions partner specializing in industrial metal 3D printing equipment and the development and production of high-performance metal powders. Leveraging decades of collective expertise and employing advanced powder production techniques like gas atomization and Plasma Rotating Electrode Process (PREP), Met3dp ensures the highest quality spherical metal powders, crucial for achieving dense, reliable, and high-performance printed parts. Our printers boast industry-leading build volumes, precision, and reliability, making them suitable for mission-critical components. By partnering with Met3dp, companies gain access to cutting-edge technology, material science expertise, and application development support, enabling them to fully harness the benefits of aluminum 3D printing for demanding applications like lightweight, high-performance antenna mounts. Whether you are an engineer designing next-generation communication systems or a procurement manager seeking a dependable supplier for bulk orders of custom antenna mounts, understanding the capabilities of aluminum AM is crucial for staying competitive and achieving optimal system performance. This article will delve deep into the applications, advantages, materials, design considerations, and procurement aspects of using aluminum 3D printing for antenna mounts, providing valuable insights for technical and purchasing decision-makers.
Applications & Industries: Where are 3D Printed Antenna Mounts Deployed?
The unique advantages offered by aluminum 3D printing – lightweighting, design complexity, and customization – make it exceptionally well-suited for antenna mounts across a diverse range of demanding industries and applications. Procurement teams sourcing components for these sectors increasingly recognize the value AM brings, moving beyond traditional supply chain constraints. The ability to tailor designs for specific RF performance characteristics, environmental conditions, or integration requirements is a key driver for adoption.
Here’s a breakdown of key application areas and industries benefiting from 3D printed aluminum antenna mounts:
1. Aerospace & Defense:
- Satellites (LEO/MEO/GEO): Mass is paramount in satellite design, as launch costs are directly tied to weight. 3D printed aluminum mounts (especially using high-strength alloys like Scalmalloy®) allow for significant weight reduction for RF antennas, telemetry antennas, and sensor mounts, directly translating to lower launch costs or increased payload capacity. The ability to create complex, organically shaped brackets optimized via topology analysis is invaluable for maximizing stiffness-to-weight ratios.
- Unmanned Aerial Vehicles (UAVs / Drones): From small reconnaissance drones to large High-Altitude Long Endurance (HALE) platforms, minimizing weight extends flight duration and increases payload capabilities. Custom 3D printed mounts can perfectly integrate antennas into the aerodynamic profile of the UAV, housing communication links, GPS antennas, and various sensor payloads. Rapid prototyping allows for quick iteration of mount designs to optimize signal reception and minimize interference.
- Aircraft: Commercial and military aircraft utilize numerous antennas for communication (VHF/UHF/Satcom), navigation (GPS/VOR/ILS), and radar systems. Lightweight AM mounts contribute to fuel efficiency and allow for optimized placement, sometimes integrating mounts directly into complex airframe structures. Part consolidation reduces assembly time and potential points of failure.
- Missiles and Munitions: Space is extremely limited, and components must withstand high G-forces and vibration. Custom-designed, robust AM mounts ensure antenna survivability and reliable performance in harsh operating environments.
2. Automotive:
- Advanced Driver-Assistance Systems (ADAS): Modern vehicles incorporate multiple radar and lidar sensors, often requiring precise mounting for accurate perception. 3D printing allows for custom brackets tailored to specific sensor models and vehicle integration points, facilitating optimal placement and performance. Lightweighting also contributes marginally to overall vehicle efficiency.
- Vehicle Connectivity (V2X, Infotainment): Antennas for cellular (4G/5G), Wi-Fi, Bluetooth, and GPS need secure and optimally positioned mounts. AM enables the creation of integrated antenna mounting solutions within dashboards, roof modules, or mirror housings, often consolidating multiple brackets into a single, complex part.
- Motorsport: In racing, every gram counts. 3D printed aluminum mounts provide lightweight, high-strength solutions for telemetry, radio communication, and sensor antennas, optimized for aerodynamic performance and resistance to extreme vibration.
3. Telecommunications:
- Base Station Antennas: While mass production often favors traditional methods, custom or specialized antenna deployments (e.g., small cells, temporary deployments, specific beamforming arrays) can benefit from the design flexibility of AM for mounting structures, especially where complex shapes are needed for precise alignment or wind load reduction.
- Microwave & RF Systems: Custom brackets for mounting waveguide components, specialized dish antennas, or RF filters can be rapidly prototyped and produced in low volumes using AM, offering faster development cycles for niche communication hardware suppliers.
4. Marine:
- Shipboard and Offshore Platforms: Mounting antennas for satellite communication (VSAT), radar, and VHF radio requires resistance to harsh saltwater environments and high winds. While stainless steels or other alloys might be chosen for corrosion resistance, aluminum AM (potentially with appropriate coatings) can offer lightweight solutions for specific applications, particularly on smaller vessels or weight-sensitive superstructures. AlSi10Mg offers reasonable corrosion resistance, enhanced by post-processing treatments.
5. Industrial IoT & Robotics:
- Automated Systems: Robots and automated guided vehicles (AGVs) often require wireless communication and positioning antennas. Custom 3D printed mounts allow for seamless integration onto complex robot arms or vehicle chassis, ensuring reliable connectivity within manufacturing or logistics environments.
Why AM is Compelling for Procurement & Supply Chain:
- Reduced Lead Times for Custom Parts: B2B buyers needing unique mount geometries no longer face long tooling lead times associated with casting or injection molding.
- On-Demand Production: Reduces the need for large inventory holdings, especially for diverse or low-volume parts. Suppliers like Met3dp can print parts as needed.
- Supply Chain Resilience: AM offers a digital manufacturing alternative, potentially mitigating risks associated with traditional supply chains or geographically concentrated suppliers.
- Consolidated Bills of Materials (BOM): Printing a single complex mount instead of assembling multiple simpler brackets simplifies procurement, inventory management, and assembly processes.
- Facilitating RFQs for Complex Geometries: Requesting quotes for topology-optimized or highly complex mounts becomes straightforward with digital CAD files suitable for AM.
The versatility and targeted benefits ensure that 3D printed aluminum antenna mounts are not just a niche technology but a growing solution across industries where performance, weight, and customization are key design drivers. Companies looking to source these advanced components need reliable suppliers with expertise in both the printing process and material science, capable of handling requirements from single prototypes to wholesale production runs.
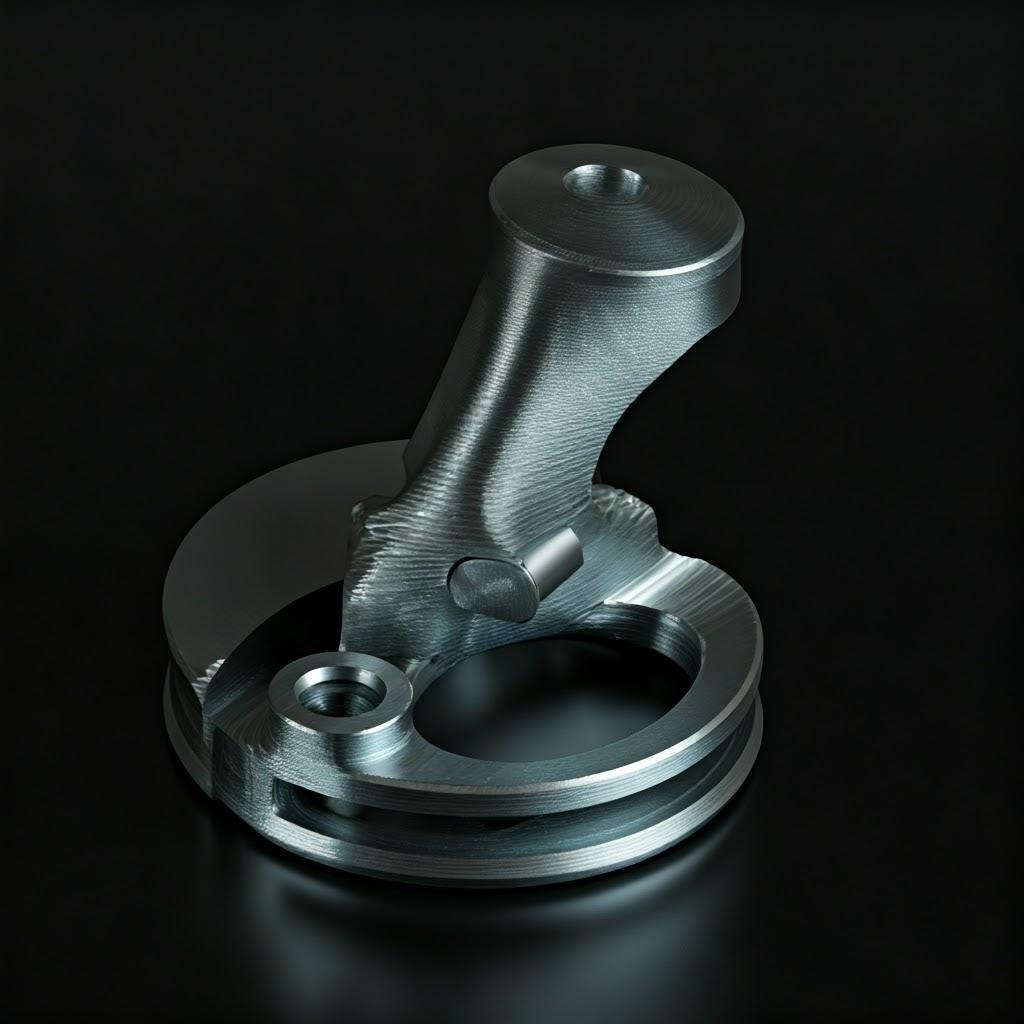
The Additive Advantage: Why Choose Metal 3D Printing for Antenna Mount Production?
While traditional manufacturing methods like CNC machining, casting, and sheet metal fabrication have long served the industry, metal additive manufacturing presents a compelling suite of advantages specifically beneficial for antenna mount production. These advantages resonate strongly with engineers seeking performance enhancements and procurement managers aiming for supply chain optimization and cost-effectiveness, particularly for complex or low-to-mid-volume components. Understanding these benefits is key to justifying the adoption of AM and selecting the right manufacturing partner. Let’s explore the key reasons why aluminum 3D printing, using printing methods like Powder Bed Fusion (PBF-LB), stands out:
1. Unmatched Design Freedom & Complexity:
- Traditional Limitations: CNC machining is subtractive, making complex internal features, thin walls, and organic shapes difficult or impossible to create efficiently. Casting requires molds, limiting complexity and making design changes costly and time-consuming.
- AM Capability: AM builds parts layer-by-layer, allowing for intricate internal channels (e.g., for cooling or cable routing), complex lattice structures for lightweighting, and highly organic shapes derived from topology optimization software. This enables engineers to design mounts that are perfectly tailored to the antenna’s RF requirements, structural loads, and integration constraints, often leading to superior performance. For instance, mounts can be designed with specific resonant frequencies or vibration damping characteristics built-in.
2. Significant Lightweighting Potential:
- Traditional Approach: Weight reduction often involves extensive machining (material waste) or using thinner materials (potentially compromising strength).
- AM Capability: AM excels at creating lightweight structures without sacrificing strength. Topology optimization algorithms can remove material from low-stress areas, resulting in bio-inspired, efficient designs. Furthermore, the use of internal lattice structures can dramatically reduce mass while maintaining or even increasing stiffness in critical directions. Combined with low-density aluminum alloys like AlSi10Mg or Scalmalloy®, weight savings of 30-60% or more compared to traditionally machined parts are achievable, which is a game-changer in aerospace, drone, and automotive applications.
3. Part Consolidation:
- Traditional Approach: Complex assemblies often require multiple individual components (brackets, fasteners, spacers) to be manufactured and then assembled, increasing part count, assembly time, potential failure points, and inventory management complexity.
- AM Capability: AM allows multiple functional components to be consolidated into a single, monolithic printed part. An antenna mount might integrate features like cable guides, connector interfaces, or even heat sinks directly into the design. This simplification reduces assembly labor, shortens the Bill of Materials (BOM), improves structural integrity by eliminating joints, and streamlines the procurement process for wholesale buyers.
4. Rapid Prototyping and Iteration:
- Traditional Approach: Creating prototypes via machining can be time-consuming, and generating casting molds is expensive and slow, hindering rapid design iteration.
- AM Capability: AM allows engineers to go directly from a CAD file to a physical metal prototype in a matter of days. This accelerates the design-build-test cycle dramatically. Multiple design variations for an antenna mount can be printed and evaluated quickly, leading to optimized performance and faster time-to-market for the final product. This agility is highly valuable in fast-moving sectors like telecommunications and consumer electronics integration.
5. Cost-Effectiveness for Low-to-Medium Volumes & Customization:
- Traditional Approach: Tooling costs (molds for casting, complex fixtures for machining) can be substantial, making low-volume production runs or highly customized parts economically unviable. Setup times for complex CNC jobs can also be significant.
- AM Capability: AM is a tool-less process. The primary cost drivers are material consumption, machine time, and post-processing. This makes it highly cost-effective for producing one-off prototypes, small batches of specialized mounts, or customized designs tailored to specific end-user requirements without incurring high upfront tooling investments. This is attractive for B2B suppliers offering tailored solutions or managing diverse product portfolios.
6. Material Efficiency & Sustainability:
- Traditional Approach: Subtractive manufacturing, especially CNC machining, can generate significant material waste (chips or swarf), sometimes exceeding the weight of the final part.
- AM Capability: AM utilizes material primarily where it’s needed in the part structure. While some support structures are required and removed post-print, the overall material utilization is generally much higher than traditional subtractive methods. Unused powder in the build chamber can often be recycled and reused, contributing to more sustainable manufacturing practices. Companies like Met3dp focus on efficient powder utilization and recycling protocols.
Comparison Table: AM vs. Traditional Methods for Antenna Mounts
Feature | Metal Additive Manufacturing (PBF-LB) | CNC Machining | Casting | Sheet Metal Fabrication |
---|---|---|---|---|
Design Complexity | Very High (Internal channels, lattices, organic shapes) | Moderate to High (Limited by tool access) | Moderate (Limited by mold design) | Low to Moderate |
Lightweighting | Excellent (Topology optimization, lattices) | Good (Material removal, but can be wasteful) | Fair (Wall thickness limitations) | Fair (Limited by material gauge) |
Part Consolidation | Excellent | Limited | Limited | Very Limited |
Prototyping Speed | Very Fast | Moderate to Fast | Slow (Requires mold) | Fast |
Low-Volume Cost | Competitive (No tooling) | Moderate to High (Setup time) | Very High (Tooling cost dominates) | Competitive |
High-Volume Cost | Higher (Process speed) | Competitive | Very Competitive | Very Competitive |
Material Waste | Low (Powder recycling) | High (Subtractive process) | Moderate (Gates, runners) | Moderate (Offcuts) |
Lead Time (New Design) | Short | Moderate | Long | Moderate |
Export to Sheets
Choosing aluminum 3D printing through experienced providers like Met3dp empowers engineering teams to break free from traditional manufacturing constraints, enabling the creation of next-generation antenna mounts that are lighter, stronger, more integrated, and faster to develop. For procurement professionals, it offers a flexible, efficient, and increasingly cost-effective sourcing solution for complex and customized components, adaptable to fluctuating demand and diverse application requirements.
Material Spotlight: AlSi10Mg and Scalmalloy® for High-Performance Antenna Mounts
The choice of material is fundamental to the success of any engineering component, and 3D printed antenna mounts are no exception. While various metals can be additively manufactured, aluminum alloys are often the preferred choice due to their inherent low density, good thermal conductivity, and favorable RF characteristics (generally low signal loss, though specific performance depends on frequency and geometry). Within the aluminum family, two materials stand out for high-performance antenna mount applications produced via Powder Bed Fusion (PBF-LB) processes: AlSi10Mg and Scalmalloy®. Understanding their distinct properties and benefits is crucial for engineers making design decisions and for procurement managers sourcing these components.
AlSi10Mg: The Versatile Workhorse
AlSi10Mg is one of the most widely used aluminum alloys in additive manufacturing. It’s essentially a casting alloy formulation adapted for AM, known for its excellent processability, good strength-to-weight ratio, and good thermal properties.
- Key Properties & Characteristics:
- Composition: Primarily aluminum (Al), with significant additions of Silicon (Si, ~9-11%) and Magnesium (Mg, ~0.2-0.45%). Silicon improves fluidity and reduces solidification shrinkage during printing, while Magnesium enables strengthening through heat treatment (precipitation hardening).
- Mechanical Properties (As-Built & Heat Treated): In the as-built state, AlSi10Mg offers moderate strength. However, it responds well to stress relief and T6 heat treatment (solutionizing and artificial aging), significantly increasing its yield strength and ultimate tensile strength, making it comparable to or exceeding common cast aluminum alloys (e.g., A356). It offers good ductility in the as-built state, which decreases after T6 treatment.
- Thermal Properties: Good thermal conductivity, which can be beneficial if the mount needs to help dissipate heat generated by antenna electronics.
- Corrosion Resistance: Offers decent corrosion resistance, suitable for many environments, though potentially requiring surface treatments (e.g., anodizing, chromate conversion coating) for harsh marine or industrial atmospheres.
- Processability: Excellent printability via PBF-LB processes (SLM/DMLS), allowing for fine features and relatively smooth surfaces. It’s widely available and well-characterized.
- Why Choose AlSi10Mg for Antenna Mounts?
- Balance of Properties: Offers a good combination of strength, stiffness, low weight, and thermal conductivity at a relatively lower cost compared to specialty AM alloys.
- Maturity & Availability: It’s a well-understood material with established print parameters and post-processing protocols. Many service providers, including Met3dp, offer high-quality AlSi10Mg powder and printing services. You can find more about Met3dp’s high-quality metal powders on our product page.
- Cost-Effectiveness: Generally more economical than higher-performance alloys like Scalmalloy®.
- Suitability: Ideal for a wide range of applications where moderate strength and significant weight savings are required, such as automotive sensor brackets, drone components (where extreme performance isn’t the primary driver), and certain aerospace or telecommunication fixtures.
Scalmalloy®: The High-Performance Aerospace Champion
Scalmalloy® is a patented high-performance aluminum-magnesium-scandium (Al-Mg-Sc) alloy specifically developed by APWORKS (an Airbus subsidiary) for additive manufacturing. It pushes the boundaries of what’s possible with aluminum AM, offering properties that rival some titanium alloys at a much lower density.
- Key Properties & Characteristics:
- Composition: Aluminum alloyed with Magnesium (Mg), Scandium (Sc), and Zirconium (Zr). The Scandium addition is key, forming Al3Sc precipitates that create an extremely fine-grained microstructure during printing and enable exceptional strength.
- Mechanical Properties: Exhibits very high yield and ultimate tensile strength, significantly exceeding AlSi10Mg and even some 7000-series aluminum alloys (traditionally considered high-strength but difficult to weld/print). It maintains good ductility relative to its strength and possesses excellent fatigue strength, making it ideal for components subjected to cyclic loading and vibration.
- Microstructure Stability: Retains its strength well at moderately elevated temperatures compared to other AM aluminum alloys.
- Weldability: Generally considered weldable, which can be useful for post-print assembly or modifications if needed.
- Corrosion Resistance: Offers good corrosion resistance, often superior to AlSi10Mg in certain environments.
- Processability: Requires carefully controlled PBF-LB parameters due to its composition but yields excellent results with high density and fine microstructure when processed correctly by experienced providers like Met3dp.
- Why Choose Scalmalloy® for Antenna Mounts?
- Maximum Lightweighting: Its exceptionally high strength-to-weight ratio allows for the most aggressive lightweighting strategies through topology optimization, critical for satellite, high-performance drone, and motorsport applications where every gram is scrutinized.
- Superior Strength & Fatigue Life: Ideal for mounts subjected to high structural loads, vibration (e.g., aircraft engine proximity, launch vehicles), or demanding operational environments.
- Performance Critical Applications: When the absolute highest performance is required and cost is a secondary factor to achieving mission objectives (e.g., deep space probes, critical defense systems).
- Replacing Heavier Materials: Can potentially replace heavier materials like titanium or steel in certain bracket applications, offering significant weight savings.
Material Property Comparison (Typical Values after appropriate Heat Treatment):
Property | AlSi10Mg (T6 Condition) | Scalmalloy® | Unit | Notes |
---|---|---|---|---|
Density | ~2.67 | ~2.66 | g/cm³ | Both offer significant lightweighting |
Yield Strength (Rp0.2) | 230 – 300 | 480 – 520 | MPa | Scalmalloy® is significantly stronger |
Ultimate Tensile Strength | 330 – 430 | 520 – 540 | MPa | Scalmalloy® has much higher ultimate strength |
Elongation at Break | 3 – 10 | 8 – 15 | % | Scalmalloy® maintains good ductility |
Modulus of Elasticity | ~70 | ~70 | GPa | Similar stiffness |
Fatigue Strength (R=-1) | Moderate | High | MPa | Scalmalloy® excels in fatigue performance |
Max Service Temperature | ~100-150 | ~200-250 | °C | Scalmalloy® better at elevated temps |
Relative Cost | Lower | Higher | – | Scalmalloy® powder and licensing cost more |
Export to Sheets
Met3dp’s Role in Material Excellence:
Choosing the right material is only part of the equation. The quality of the metal powder and the precision of the printing process are paramount to achieving the desired material properties in the final part. Met3dp utilizes industry-leading gas atomization and PREP technologies to produce highly spherical metal powders with controlled particle size distribution and high purity, essential for defect-free printing. Our expertise extends to optimizing print parameters for both AlSi10Mg and advanced alloys like Scalmalloy®, ensuring customers receive antenna mounts that meet stringent performance requirements. Whether sourcing standard AlSi10Mg components in bulk or requiring cutting-edge performance with Scalmalloy®, partnering with a knowledgeable supplier like Met3dp ensures material quality and process reliability. We can advise on the optimal material choice based on your specific application requirements, balancing performance, cost, and manufacturability.
The selection between AlSi10Mg and Scalmalloy® depends heavily on the specific performance demands, budget constraints, and operating environment of the antenna mount. AlSi10Mg provides a robust and cost-effective solution for many applications, while Scalmalloy® offers unparalleled performance for the most demanding weight-critical and high-strength scenarios
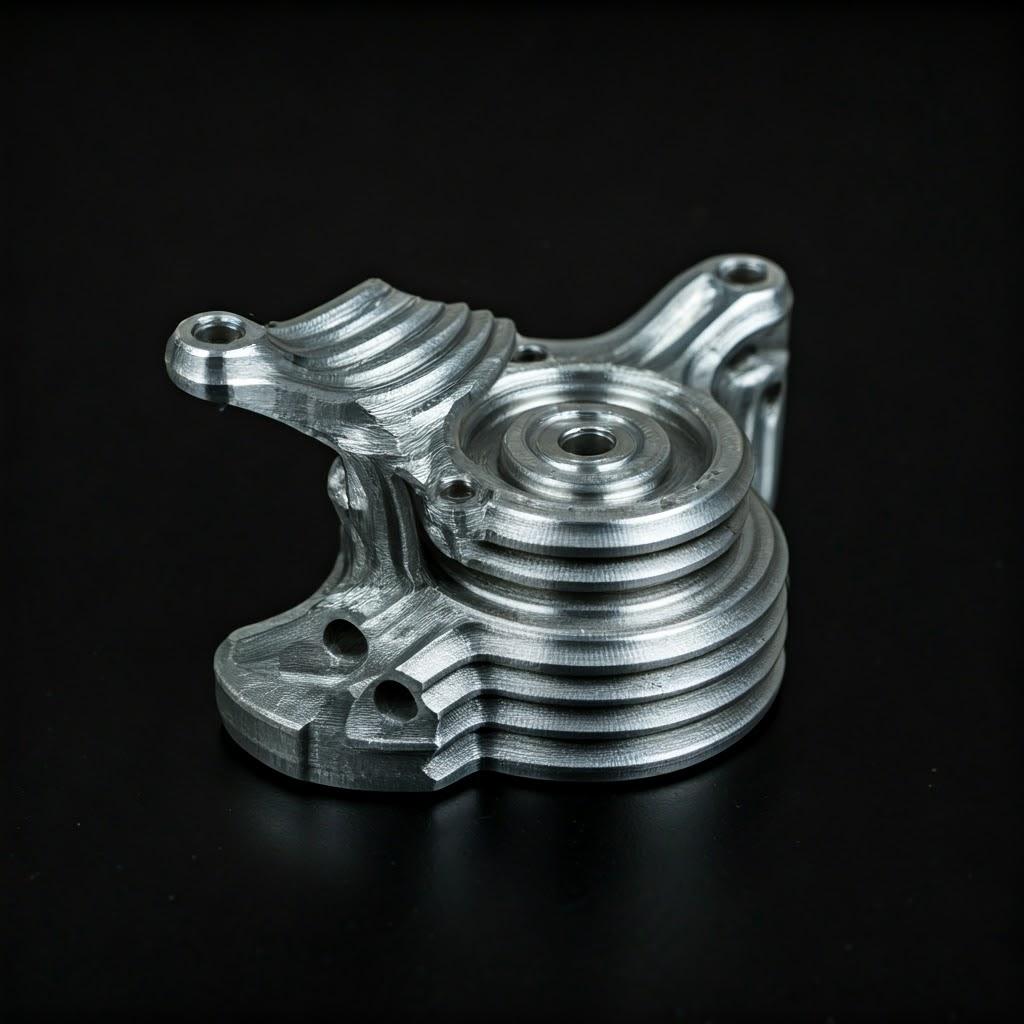
Design for Additive Manufacturing (DfAM): Optimizing Antenna Mounts for 3D Printing
Simply replicating a design intended for traditional manufacturing often fails to leverage the full potential of metal additive manufacturing and can even lead to suboptimal results or print failures. To truly harness the lightweighting, performance, and cost benefits of aluminum 3D printing for antenna mounts, engineers must embrace Design for Additive Manufacturing (DfAM) principles. DfAM is not just a suggestion; it’s a critical methodology that considers the unique opportunities and constraints of the layer-by-layer PBF-LB process right from the initial concept phase. For procurement managers evaluating quotes (RFQs) and sourcing bulk orders, understanding DfAM is important, as well-optimized designs generally translate to lower print times, reduced material consumption, minimized post-processing, and ultimately, lower costs and more reliable components from their chosen supplier.
Effective DfAM for aluminum antenna mounts involves several key considerations:
1. Leveraging Topology Optimization and Generative Design:
- Concept: These software tools use algorithms (like Finite Element Analysis – FEA) to iteratively remove material from areas of low stress while ensuring the part meets predefined structural requirements (loads, stiffness, vibration constraints).
- Benefit for Antenna Mounts: This is the primary driver for achieving maximum lightweighting. Instead of blocky, machined shapes, topology optimization often yields organic, lattice-like structures that are incredibly strong yet use minimal material. This is ideal for aerospace, drone, and satellite applications where mass reduction is paramount. Generative design can explore hundreds or thousands of design variations based on constraints, offering novel solutions engineers might not have conceived manually.
- Implementation: Engineers define load cases, keep-out zones (where material must not intrude, e.g., near antenna elements or connector paths), and target mass reduction or stiffness goals. The software generates an optimized geometry that can then be refined in CAD for manufacturability.
2. Designing for Self-Supporting Angles and Overhangs:
- Concept: In PBF-LB, each layer is fused onto the previous one. Steep overhangs or horizontal features require support structures underneath them during the build to prevent collapse or distortion due to gravity and thermal stresses. However, support structures add print time, consume material, require removal (labor-intensive), and can negatively impact surface finish.
- DfAM Strategy: Design parts with angles typically greater than 45 degrees relative to the build plate wherever possible. These are generally considered “self-supporting.” Orienting the part strategically on the build platform during print preparation is also crucial. Consider incorporating fillets or chamfers instead of sharp horizontal overhangs. Teardrop shapes for horizontal holes are often better than perfectly circular ones, as the top surface of the circle is self-supporting.
- Antenna Mount Relevance: Careful orientation and design modifications can minimize supports needed for complex bracket arms or mounting flanges, reducing post-processing time and cost for wholesale production.
3. Minimum Feature Sizes and Wall Thickness:
- Concept: The laser spot size, powder particle size, and layer thickness inherent in the PBF-LB process dictate the minimum size of features (walls, pins, holes) that can be reliably printed. Trying to print features below these limits can lead to incomplete formation or poor resolution.
- Typical Limits (Aluminum PBF-LB): Minimum wall thicknesses are often around 0.4-0.8 mm, and minimum hole diameters might be similar, though these depend heavily on the specific machine, parameters, and feature orientation.
- DfAM Guideline: Ensure all structural walls, ribs, and features adhere to the minimum printable size recommended by the AM service provider. Consult with your supplier, like Met3dp, early in the design phase to understand their specific machine capabilities and material recommendations. Thicker walls may be needed for structural integrity, but unnecessarily thick sections add weight and print time.
4. Incorporating Escape Holes for Trapped Powder:
- Concept: Hollow sections or internal cavities are excellent for lightweighting but can trap unfused metal powder inside after the print is complete. This trapped powder adds weight, can be a source of contamination, and is difficult to remove completely.
- DfAM Solution: Design strategically placed “escape holes” in hollow sections or complex internal geometries. These holes allow the loose powder to be easily removed during post-processing (typically via vibration or compressed air). The size and placement should ensure efficient powder removal without compromising the part’s structural integrity.
- Importance for Procurement: Incomplete powder removal can lead to parts being heavier than specified or failing quality checks. Ensure designs submitted for RFQ incorporate necessary escape routes.
5. Designing for Support Structure Removal:
- Concept: Even with optimized designs, some support structures are often unavoidable, especially for complex geometries or specific orientations needed to manage thermal stress. These supports must be removed after printing.
- DfAM Strategy: Design features with support removal access in mind. Avoid placing critical surfaces or delicate features where supports will attach, as removal can leave witness marks or minor surface imperfections. Ensure there is physical access for tools (manual breaking, cutting, wire EDM) to remove the supports without damaging the main part structure. Discussing support strategy with the AM provider is crucial.
6. Part Consolidation Strategy:
- Concept: As mentioned previously, AM allows combining multiple components into one. DfAM involves identifying opportunities for consolidation during the design phase.
- Application: Can separate brackets, fasteners mounts, and cable guides for an antenna system be integrated into a single, complex printed mount? This simplifies assembly, reduces inventory, and potentially improves overall system reliability.
Collaborating with Your AM Supplier:
Engaging with an experienced AM supplier like Met3dp early in the design process is highly beneficial. Our engineers can provide valuable DfAM feedback based on extensive experience with aluminum PBF-LB, material characteristics, and machine capabilities. This collaborative approach helps optimize the design for manufacturability, performance, and cost-effectiveness before committing to production, especially important when planning for bulk or wholesale orders. We can assist with topology optimization analysis, recommend optimal build orientations, advise on achievable tolerances, and ensure the design aligns with efficient post-processing workflows. This partnership ensures that the final antenna mounts meet all technical specifications while fully leveraging the advantages of additive manufacturing. Explore more about us and our collaborative approach.
By implementing these DfAM principles, engineers can create aluminum antenna mounts that are not only significantly lighter and perform better but are also optimized for efficient and reliable additive manufacturing, leading to successful outcomes for both technical performance and supply chain management.
Precision & Performance: Understanding Tolerances, Surface Finish, and Accuracy in AM Antenna Mounts
While metal additive manufacturing offers incredible design freedom, achieving the required level of precision, surface quality, and dimensional accuracy is critical for the functionality of antenna mounts. These components often interface with other parts of a system (the antenna itself, the main structure, connectors), requiring specific tolerances for proper fit and alignment. Furthermore, surface finish can impact fatigue life and, in some RF applications, potentially influence signal performance at very high frequencies, although this is less common for mounting structures compared to waveguide components. Both engineers specifying requirements and procurement managers evaluating supplier capabilities must have a clear understanding of what PBF-LB processes can typically achieve and what factors influence the final part quality.
Dimensional Accuracy and Tolerances:
- Concept: Dimensional accuracy refers to how closely the printed part conforms to the nominal dimensions specified in the CAD model. Tolerance defines the permissible range of variation for a given dimension.
- Typical AM Capabilities (PBF-LB Aluminum):
- General Tolerances: As-built parts typically achieve tolerances in the range of ±0.1 mm to ±0.3 mm for smaller features (e.g., up to 50-100 mm), with potentially larger deviations (e.g., ±0.1-0.2% of the dimension) for larger parts. These values are highly dependent on the machine, calibration, material (AlSi10Mg vs. Scalmalloy® may have different shrinkage factors), part geometry, orientation, and support strategy.
- Critical Tolerances: For mating surfaces, hole diameters/positions, or features requiring high precision, as-built tolerances may not be sufficient. These features often require secondary machining operations (CNC milling, turning, drilling) during post-processing to achieve tighter tolerances, potentially reaching ±0.01 mm to ±0.05 mm or better, comparable to traditional machining.
- Factors Influencing Accuracy:
- Thermal Stress & Shrinkage: The repeated heating and cooling during the layer-wise process induces internal stresses and material shrinkage, which can cause warping or deviation from the intended geometry. Optimized build parameters and support strategies are crucial for mitigation.
- Build Orientation: The orientation of the part on the build platform significantly impacts accuracy due to the anisotropic nature of the layer-wise buildup and thermal gradients.
- Support Structures: How supports are designed and attached influences the final geometry, especially after removal.
- Machine Calibration: Regular calibration of the laser system, scanners, and powder recoating mechanism is essential for consistent accuracy.
- Geometric Dimensioning and Tolerancing (GD&T): For complex parts like antenna mounts with critical interfaces, using GD&T on engineering drawings is essential. GD&T provides a standardized language to define not just size tolerances but also tolerances for form, orientation, location, and profile of features, ensuring functional requirements are met. Suppliers like Met3dp are experienced in interpreting and achieving GD&T specifications, often utilizing post-print machining for critical callouts.
Surface Finish (Roughness):
- Concept: Surface finish, typically quantified by average roughness (Ra), describes the texture of the part’s surfaces. PBF-LB processes inherently produce rougher surfaces compared to machining or polishing due to the partially melted powder particles adhering to the surface and the layered nature of the build.
- Typical Ra Values (PBF-LB Aluminum):
- As-Built Surfaces: Ra values typically range from 6 µm to 20 µm (approx. 240-800 µin), depending on the surface orientation (upward-facing, downward-facing, vertical walls), build parameters, and powder characteristics. Downward-facing surfaces requiring supports tend to be rougher after support removal.
- Post-Processed Surfaces: Various finishing techniques can significantly improve surface roughness:
- Abrasive Blasting (Bead/Sand): Can achieve Ra 3 µm – 10 µm, providing a uniform matte finish.
- Tumbling/Vibratory Finishing: Can smooth surfaces and edges, reaching Ra 1 µm – 5 µm depending on media and time.
- Machining: Can achieve Ra < 1.6 µm or even < 0.8 µm on specific surfaces.
- Polishing: Can achieve very smooth, mirror-like finishes (Ra < 0.1 µm) but is typically labor-intensive and reserved for specific aesthetic or functional requirements.
- Importance for Antenna Mounts: While extreme smoothness is rarely required for the mount itself (unless it’s an integrated RF surface), controlling roughness on mating interfaces is important for fit. A uniform finish via blasting is common for aesthetics and consistency. Anodizing or coating adhesion can also be affected by surface preparation.
Ensuring Performance and Quality:
- Process Control: Reliable AM suppliers like Met3dp employ rigorous process monitoring and control, including laser power monitoring, thermal imaging (where available), and meticulous powder quality management (sieving, testing, controlled recycling) to ensure consistency from build to build.
- Quality Inspection: Post-print inspection is critical. This typically involves:
- Visual Inspection: Checking for defects, complete support removal, and general appearance.
- Dimensional Measurement: Using calipers, micrometers, Coordinate Measuring Machines (CMMs), or 3D scanners to verify dimensions and GD&T callouts against the drawing.
- Material Testing (Coupon): Often, test coupons are printed alongside the main parts and subjected to tensile testing or density analysis to verify material properties meet specifications.
- Non-Destructive Testing (NDT): For critical components (especially aerospace), CT scanning might be used to detect internal porosity or defects.
- Clear Specifications for Procurement: When issuing RFQs for wholesale antenna mount orders, clearly define:
- Critical dimensions and their tolerances (using GD&T where appropriate).
- Required surface finish (Ra values for specific surfaces or overall finish).
- Any required material certifications or testing (e.g., density, tensile properties).
- Inspection methods and acceptance criteria.
By understanding the achievable precision and surface characteristics of aluminum AM processes, and by clearly specifying requirements, engineers and procurement managers can work effectively with capable suppliers like Met3dp to obtain high-performance antenna mounts that meet demanding functional and quality standards. Addressing these aspects early ensures that the final components fit correctly, perform reliably, and leverage the full benefits of additive manufacturing technology.
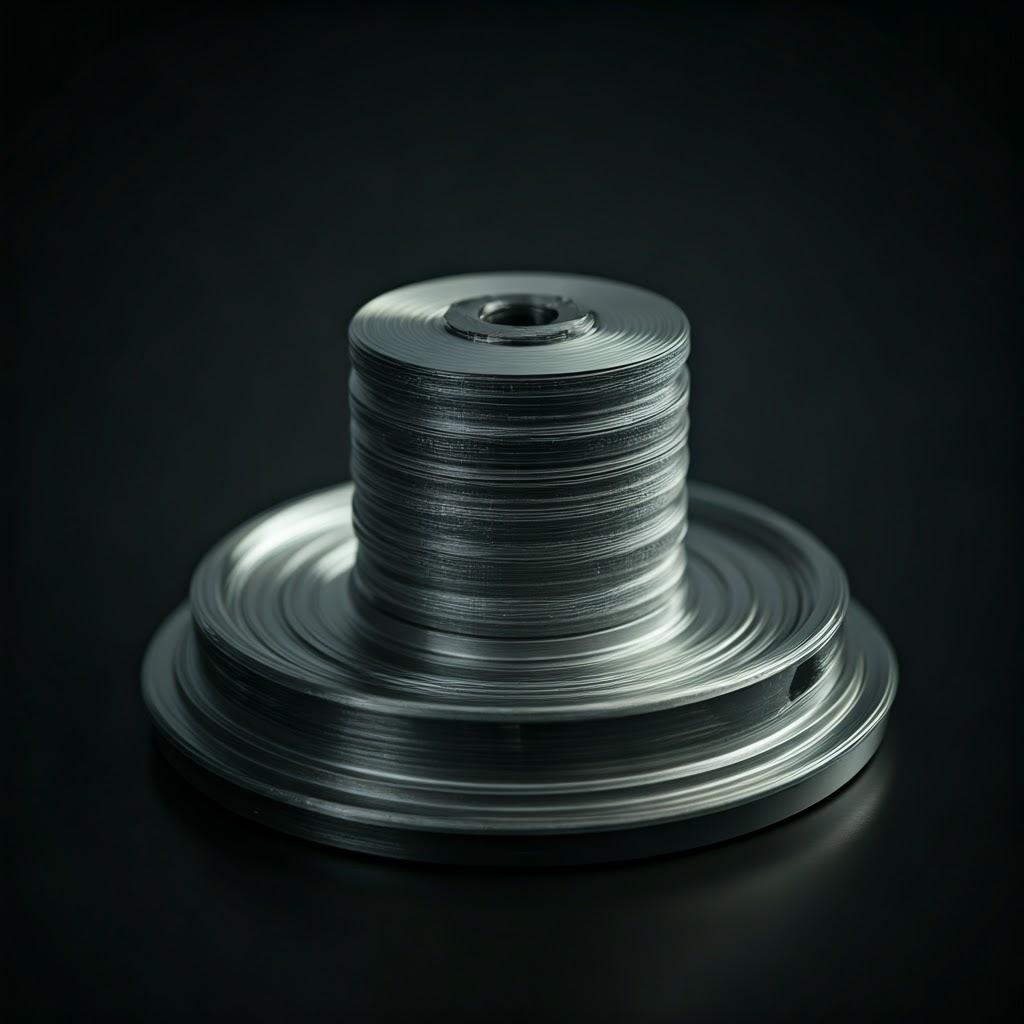
Beyond the Print: Essential Post-Processing Steps for Functional Antenna Mounts
The journey of a 3D printed metal part doesn’t end when the printer stops. For aluminum antenna mounts produced via PBF-LB, several crucial post-processing steps are typically required to transform the raw printed part into a functional, reliable component ready for assembly and deployment. These steps are essential for relieving internal stresses, achieving final dimensions and surface finish, enhancing material properties, and ensuring long-term performance. Understanding this workflow is vital for engineers designing the part and for procurement managers factoring in total lead time and cost when evaluating supplier quotes (RFQs). Different applications may require a subset or all of these steps, tailored to the specific performance needs.
Here’s a breakdown of common post-processing stages for 3D printed aluminum antenna mounts:
1. De-powdering:
- Purpose: Removing the loose, unfused metal powder surrounding the printed parts within the build chamber and from internal channels or cavities.
- Method: Typically done manually or semi-automatically using brushes, vacuum systems, compressed air, and vibration within a controlled environment to safely collect the valuable powder for potential recycling. Thoroughness is key, especially for designs with complex internal features (requiring well-designed escape holes as per DfAM).
- Importance: Ensures parts are clean for subsequent steps and maximizes powder recovery. Incomplete de-powdering adds unwanted weight and can interfere with heat treatments or surface finishes.
2. Stress Relief:
- Purpose: The rapid heating and cooling inherent in the PBF-LB process create significant residual stresses within the printed part. These stresses can cause distortion (especially after removal from the build plate), reduce fatigue life, and potentially lead to cracking. Stress relief is a heat treatment performed at a moderate temperature to relax these internal stresses without significantly altering the microstructure.
- Method: Parts (often while still attached to the build plate) are heated in a furnace under a controlled atmosphere (e.g., Argon) to a specific temperature (below the aging temperature for heat-treatable alloys like AlSi10Mg or Scalmalloy®), held for a period, and then slowly cooled.
- Importance: Critical for maintaining dimensional stability throughout the subsequent post-processing steps and ensuring the part’s long-term structural integrity.
3. Part Removal from Build Plate:
- Purpose: Separating the printed antenna mounts from the metal build plate they were fused onto during the printing process.
- Method: Commonly done using wire Electrical Discharge Machining (wire EDM) or a bandsaw. Wire EDM offers higher precision and a cleaner cut, minimizing stress on the part, but is slower. Bandsawing is faster but less precise and may require a subsequent machining step to flatten the base surface.
- Consideration: The removal method can influence downstream finishing requirements for the base surface of the mount.
4. Support Structure Removal:
- Purpose: Removing the temporary support structures that were printed to anchor the part and support overhangs.
- Method: This can be a labor-intensive process, often involving a combination of manual breaking (for easily accessible supports), cutting tools (pliers, grinders), or sometimes CNC machining or wire EDM for complex or hard-to-reach supports.
- Importance: Supports must be removed completely without damaging the part surface. DfAM plays a crucial role here – designing supports for easier removal significantly reduces post-processing time and cost, a key factor for wholesale production efficiency. Witness marks left by supports may require further finishing.
5. Heat Treatment (Hardening/Aging):
- Purpose: For heat-treatable alloys like AlSi10Mg and Scalmalloy®, this step significantly enhances mechanical properties (strength, hardness). It’s often essential to meet the performance requirements of demanding applications.
- Method: Typically involves a T6 cycle:
- Solutionizing: Heating the part to a high temperature (e.g., ~500-540°C for Al alloys) to dissolve alloying elements into a solid solution.
- Quenching: Rapidly cooling the part (e.g., in water or polymer) to trap the elements in solution.
- Artificial Aging: Reheating the part to a lower temperature (e.g., ~150-200°C) for several hours, allowing fine precipitates (like Mg2Si in AlSi10Mg or Al3Sc in Scalmalloy®) to form, which strengthen the material.
- Importance: Tailors the material properties to the application’s needs. Precise control over temperatures and times is critical, requiring calibrated furnace equipment and expertise.
6. Hot Isostatic Pressing (HIP) – Optional but Recommended for Critical Parts:
- Purpose: To eliminate internal microporosity that can sometimes remain after the PBF-LB process. Porosity can act as a stress concentrator, negatively impacting fatigue life and potentially mechanical strength.
- Method: Parts are subjected to both high temperature (below melting point but typically near solutionizing temps) and high inert gas pressure (e.g., Argon at 100 MPa or more) simultaneously within a specialized HIP vessel. The pressure collapses internal voids, diffusion bonding the material across the void interfaces.
- Importance: Dramatically improves fatigue performance, ductility, and consistency of mechanical properties. Highly recommended for critical aerospace, defense, or medical components. Adds cost and lead time but significantly enhances reliability. Met3dp can advise if HIP is beneficial for your specific antenna mount application.
7. Machining (CNC Finishing):
- Purpose: To achieve tight tolerances on critical features, create precise mating surfaces, drill/tap threads, or improve surface finish on specific areas where the as-built AM part doesn’t meet requirements.
- Method: Using standard CNC milling, turning, or drilling operations. Requires careful fixture design to hold the potentially complex AM part geometry securely without distortion.
- Importance: Essential for ensuring proper fit, alignment, and interfacing with other components. Often required for bearing surfaces, bolt holes, or RF connector interfaces on antenna mounts.
8. Surface Finishing:
- Purpose: To improve surface roughness, enhance corrosion resistance, provide specific aesthetic qualities, or prepare the surface for coating/painting.
- Methods:
- Abrasive Blasting (Bead, Sand, etc.): Provides a uniform matte finish, cleans surfaces, and can remove minor imperfections.
- Tumbling/Vibratory Finishing: Smooths surfaces and edges, especially for batches of smaller parts.
- Anodizing (for Aluminum): Creates a hard, corrosion-resistant oxide layer. Can be dyed various colors. Type II (decorative/corrosion) and Type III (hardcoat) are common.
- Chromate Conversion Coating (Alodine/Iridite): Provides corrosion resistance and an excellent base for paint adhesion.
- Painting/Powder Coating: For specific colors or additional environmental protection.
- Importance: Tailors the final appearance and environmental resistance of the antenna mount to the application’s needs.
Supplier Capability & Quoting:
A full-service AM provider like Met3dp manages this entire post-processing chain, either in-house or through qualified partners. When requesting quotes (RFQs), especially for wholesale volumes, ensure the supplier details which post-processing steps are included in the price and lead time. Clearly specifying requirements for heat treatment, HIP, machining tolerances, and surface finishes is crucial for receiving accurate quotes and ensuring the final parts meet all functional and quality criteria. The complexity of post-processing significantly impacts the final cost and delivery schedule.
Understanding this comprehensive workflow highlights that metal 3D printing is more than just the printing operation itself; it’s an integrated manufacturing process requiring expertise across multiple stages to deliver high-quality, functional aluminum antenna mounts.
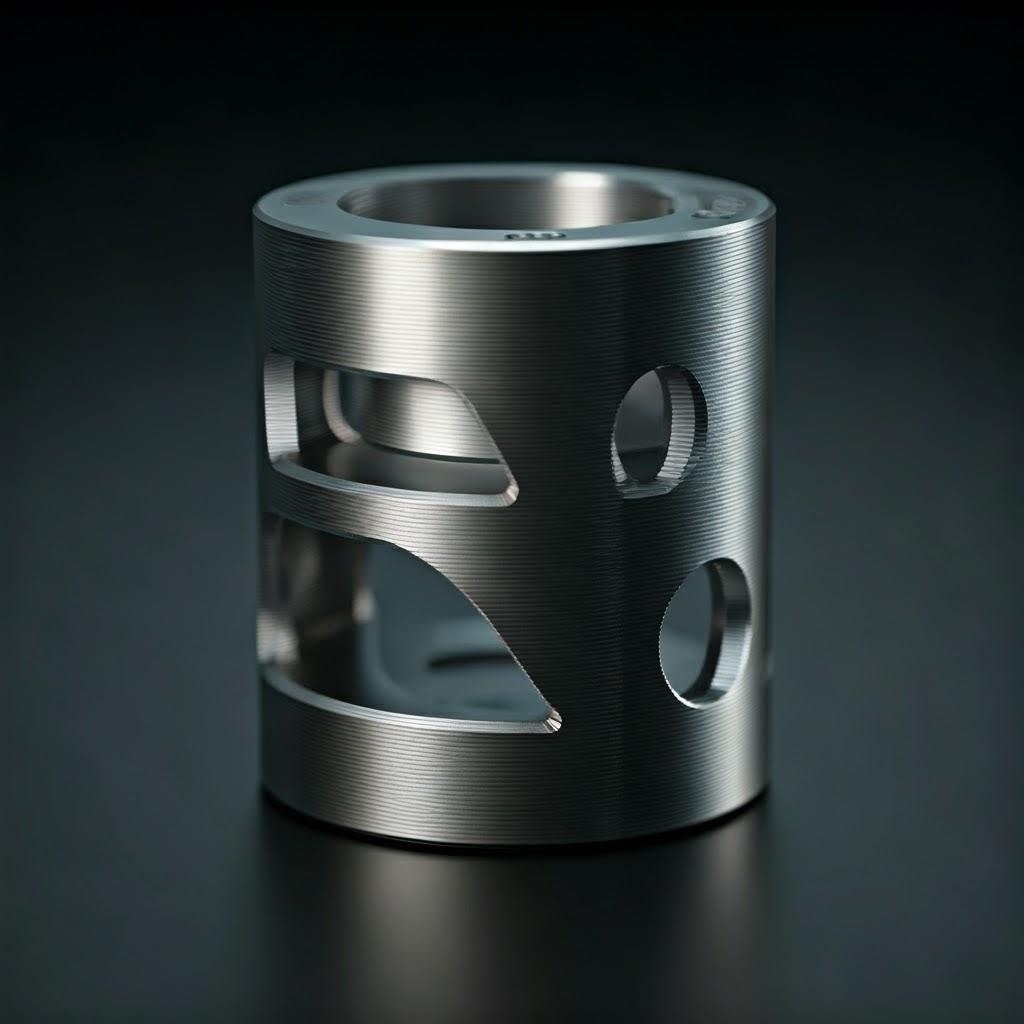
Navigating Challenges: Overcoming Hurdles in Metal AM for Antenna Mounts
While aluminum additive manufacturing offers significant advantages for producing lightweight and complex antenna mounts, it’s not without its challenges. Successfully implementing this technology, particularly for demanding applications or wholesale production, requires acknowledging potential hurdles and partnering with an experienced supplier equipped to mitigate them. Engineers designing parts and procurement managers selecting vendors should be aware of these common challenges and the strategies employed to overcome them.
1. Warping and Distortion (Residual Stress):
- Challenge: The intense, localized heat of the laser followed by rapid cooling creates significant thermal gradients within the part during the PBF-LB process. This leads to the buildup of internal residual stresses. If not properly managed, these stresses can cause the part to warp or distort, especially thin or large flat sections, either during the build or after removal from the build plate.
- Mitigation Strategies:
- Optimized Build Orientation: Orienting the part to minimize large flat surfaces parallel to the build plate and reduce thermal gradients.
- Effective Support Structures: Designing robust support structures not only for overhangs but also to anchor the part firmly to the build plate, acting as heat sinks and restraining movement.
- Optimized Scan Strategies: Using specific laser scanning patterns (e.g., island scanning, chessboard patterns) to distribute heat more evenly and reduce localized stress accumulation.
- Process Parameter Control: Fine-tuning laser power, scan speed, and layer thickness for the specific alloy (AlSi10Mg and Scalmalloy® behave differently).
- Stress Relief Heat Treatment: Performing this step immediately after printing (ideally before part removal) is critical to relax internal stresses and stabilize the geometry.
- Simulation: Advanced simulation software can predict stress buildup and potential distortion, allowing for adjustments to orientation or supports before printing. Met3dp utilizes simulation and empirical data to optimize build setups.
2. Support Structure Removal Difficulties:
- Challenge: Supports are necessary but can be difficult, time-consuming, and costly to remove, especially from intricate internal channels or delicate features. Removal can also damage the part surface or leave undesirable witness marks.
- Mitigation Strategies:
- DfAM Principles: Designing parts to be as self-supporting as possible (using angles >45°, optimizing orientation).
- Smart Support Design: Using specialized support structures (e.g., tree supports, block supports with perforation) designed for easier breakaway or access for tools. Minimizing the contact area between the support and the part.
- Appropriate Removal Techniques: Employing the right tools (manual, CNC, wire EDM) based on support complexity and location.
- Post-Removal Finishing: Planning for subsequent finishing steps (blasting, machining) to clean up witness marks if they occur on critical surfaces.
3. Porosity:
- Challenge: Small voids or pores can sometimes form within the printed material due to incomplete melting, gas entrapment (e.g., from moisture in the powder or shielding gas impurities), or keyholing (vapor depression instability at high laser power). Porosity can degrade mechanical properties, particularly fatigue strength.
- Mitigation Strategies:
- High-Quality Metal Powder: Using powder with high sphericity, controlled particle size distribution, low internal gas content, and proper handling to prevent moisture absorption. Met3dp’s advanced gas atomization and PREP technologies are key here.
- Optimized Print Parameters: Precise control over laser power, scan speed, hatch spacing, and layer thickness to ensure complete melting and stable melt pool dynamics.
- Inert Atmosphere Control: Maintaining a high-purity inert gas environment (Argon) in the build chamber to minimize oxidation and gas pickup.
- Hot Isostatic Pressing (HIP): As discussed previously, HIP is highly effective at closing internal pores, significantly improving material integrity for critical applications.
- Quality Control: Using CT scanning or metallographic analysis to detect and quantify porosity levels, ensuring they remain within acceptable limits for the application.
4. Achieving Consistent Material Properties:
- Challenge: Ensuring that the mechanical properties (strength, ductility, fatigue life) are consistent across the part and from build to build can be challenging due to the complex thermal history experienced by different sections of the component.
- Mitigation Strategies:
- Rigorous Process Control: Maintaining tight control over all print parameters and machine calibration.
- Powder Quality Management: Ensuring consistent powder feedstock quality, including careful recycling protocols.
- Standardized Post-Processing: Applying consistent heat treatment cycles (stress relief, T6, HIP) as required.
- Coupon Testing: Regularly printing and testing mechanical test coupons alongside production parts to verify properties meet specifications.
- Supplier Expertise: Partnering with a supplier with deep materials science knowledge and proven experience with the specific alloy (AlSi10Mg, Scalmalloy®). Met3dp’s focus on both equipment and materials provides this integrated expertise.
5. Surface Finish Limitations:
- Challenge: The as-built surface roughness of PBF-LB parts may not be suitable for all applications, particularly those requiring very smooth surfaces for sealing, sliding contact, or specific RF performance. Achieving very fine finishes requires additional post-processing steps.
- Mitigation Strategies:
- Orientation Optimization: Printing critical surfaces in orientations known to produce better finishes (e.g., vertical walls or upward-facing surfaces).
- Parameter Adjustment: Minor adjustments to contouring parameters can sometimes improve sidewall smoothness.
- Effective Post-Processing: Utilizing appropriate finishing techniques (blasting, tumbling, machining, polishing) targeted to the specific requirements of different surfaces on the antenna mount. Clearly defining surface finish requirements in the RFQ is essential.
6. Cost and Lead Time Management:
- Challenge: While AM eliminates tooling costs, machine time, material cost (especially for advanced alloys like Scalmalloy®), and extensive post-processing can make it more expensive than traditional methods for very high volumes. Lead times depend on print time, machine availability, and post-processing complexity.
- Mitigation Strategies:
- DfAM for Efficiency: Optimizing designs to reduce print volume, minimize supports, and simplify post-processing directly impacts cost and speed.
- Nesting & Build Planning: Efficiently arranging multiple parts on a single build plate (nesting) maximizes machine utilization.
- Choosing the Right Material: Selecting AlSi10Mg when Scalmalloy®’s extreme properties aren’t strictly necessary can significantly reduce costs.
- Clear Communication with Supplier: Discussing volume forecasts, lead time requirements, and cost targets early allows suppliers like Met3dp to optimize production planning and provide accurate quotes for wholesale orders.
Successfully navigating these challenges requires a combination of smart design (DfAM), robust process control, appropriate post-processing, rigorous quality assurance, and strong collaboration between the customer and the AM service provider. Choosing a knowledgeable and experienced supplier like Met3dp, with expertise spanning materials, equipment, and application engineering, is paramount to mitigating risks and realizing the full potential of aluminum 3D printing for high-performance antenna mounts.
Selecting Your Partner: How to Choose a Reliable Metal 3D Printing Supplier for Antenna Mounts
Choosing the right additive manufacturing partner is as critical as the design and material selection for ensuring the success of your 3D printed aluminum antenna mount project. Whether you are sourcing single prototypes or planning wholesale production runs, the capabilities, quality systems, and expertise of your supplier will directly impact the final component’s quality, cost, and delivery schedule. Procurement managers and engineers need a structured approach to evaluate potential metal AM service providers. Here are key criteria to consider when selecting a reliable supplier for your antenna mount needs:
1. Technical Expertise and Experience:
- Materials Knowledge: Does the supplier have demonstrated experience with the specific aluminum alloys you require (AlSi10Mg, Scalmalloy®)? Do they understand the nuances of processing these materials, including optimal print parameters and heat treatment protocols? Can they advise on material selection based on your application?
- DfAM Support: Does the supplier offer Design for Additive Manufacturing consultation? Can they review your designs and provide actionable feedback to optimize for printability, reduce cost, and enhance performance? Proactive DfAM support is invaluable, especially for complex antenna mount geometries.
- Process Control: What level of process monitoring and control do they employ? Ask about their methods for ensuring consistent laser power, inert atmosphere quality, and thermal management during the build.
- Application Experience: Have they successfully produced parts similar to antenna mounts or components for your specific industry (e.g., aerospace, automotive, telecommunications)? Case studies or references can be indicative of their capabilities. Met3dp prides itself on decades of collective expertise in metal additive manufacturing across various demanding sectors.
2. Equipment Capability and Capacity:
- Technology: Do they operate modern, well-maintained PBF-LB machines suitable for aluminum alloys? What is the manufacturer and model?
- Build Volume: Do their machines have a large enough build envelope to accommodate the size of your antenna mounts, potentially allowing for multiple parts per build (nesting) for efficiency? Met3dp operates printers with industry-leading build volumes.
- Capacity: Can they handle your required production volume, from single prototypes to ongoing wholesale orders? Do they have sufficient machine capacity to meet your lead time requirements? Discuss their production planning and scheduling processes.
- Maintenance & Calibration: What are their procedures for regular machine maintenance and calibration to ensure ongoing accuracy and reliability?
3. Quality Management Systems and Certifications:
- ISO 9001: This is a fundamental requirement, indicating a documented quality management system is in place.
- AS9100 (Aerospace): If your antenna mounts are for aerospace or defense applications, AS9100 certification is often mandatory. It signifies adherence to the rigorous quality management standards required by the aviation, space, and defense industries.
- Other Relevant Certifications: Depending on the industry (e.g., ISO 13485 for medical), specific certifications may be necessary.
- Quality Procedures: Inquire about their specific quality control procedures, including dimensional inspection methods (CMM, 3D scanning), material testing, and documentation practices.
4. Post-Processing Capabilities:
- In-House vs. Outsourced: Does the supplier perform critical post-processing steps (stress relief, heat treatment, HIP, CNC machining, surface finishing) in-house, or do they rely on external partners? In-house capabilities generally offer better control over the entire process, potentially shorter lead times, and clearer accountability.
- Range of Services: Can they provide the full suite of post-processing steps required for your antenna mounts (e.g., specific heat treatments like T6, precision CNC finishing, required coatings like anodizing or chromate conversion)?
- Quality Control for Post-Processing: How do they ensure the quality and consistency of these secondary operations, whether performed internally or externally?
5. Material Handling and Traceability:
- Powder Quality: How do they source, test, handle, and store their metal powders (AlSi10Mg, Scalmalloy®)? What are their procedures for powder recycling and ensuring traceability to prevent cross-contamination? Met3dp emphasizes its advanced powder production (gas atomization, PREP) and rigorous quality control.
- Material Certifications: Can they provide material certifications confirming the powder composition and properties?
- Lot Traceability: Do they maintain full traceability from the raw powder lot through printing and post-processing to the final shipped part? This is crucial for regulated industries.
6. Communication and Customer Service:
- Responsiveness: Are they responsive to inquiries and requests for quotes (RFQs)?
- Technical Communication: Can their engineering team communicate effectively with your design team regarding technical specifications, DfAM feedback, and project status?
- Project Management: Do they provide clear timelines, regular updates, and a dedicated point of contact for your projects?
7. Cost and Lead Time:
- Transparent Quoting: Do they provide detailed quotes that clearly break down costs associated with materials, printing, support removal, post-processing, inspection, and any NRE (Non-Recurring Engineering) charges?
- Competitive Pricing: Is their pricing competitive for the level of quality, expertise, and service offered? (Note: The lowest price isn’t always the best value, especially for critical components).
- Reliable Lead Times: Can they provide realistic and reliable lead time estimates based on their current capacity and the complexity of your project?
Evaluating potential suppliers against these criteria will help you identify a partner like Met3dp, who not only possesses the technical capabilities but also aligns with your quality expectations and business requirements. Investing time in supplier qualification is essential for establishing a successful long-term relationship for sourcing high-quality, 3D printed aluminum antenna mounts, especially for consistent wholesale supply.
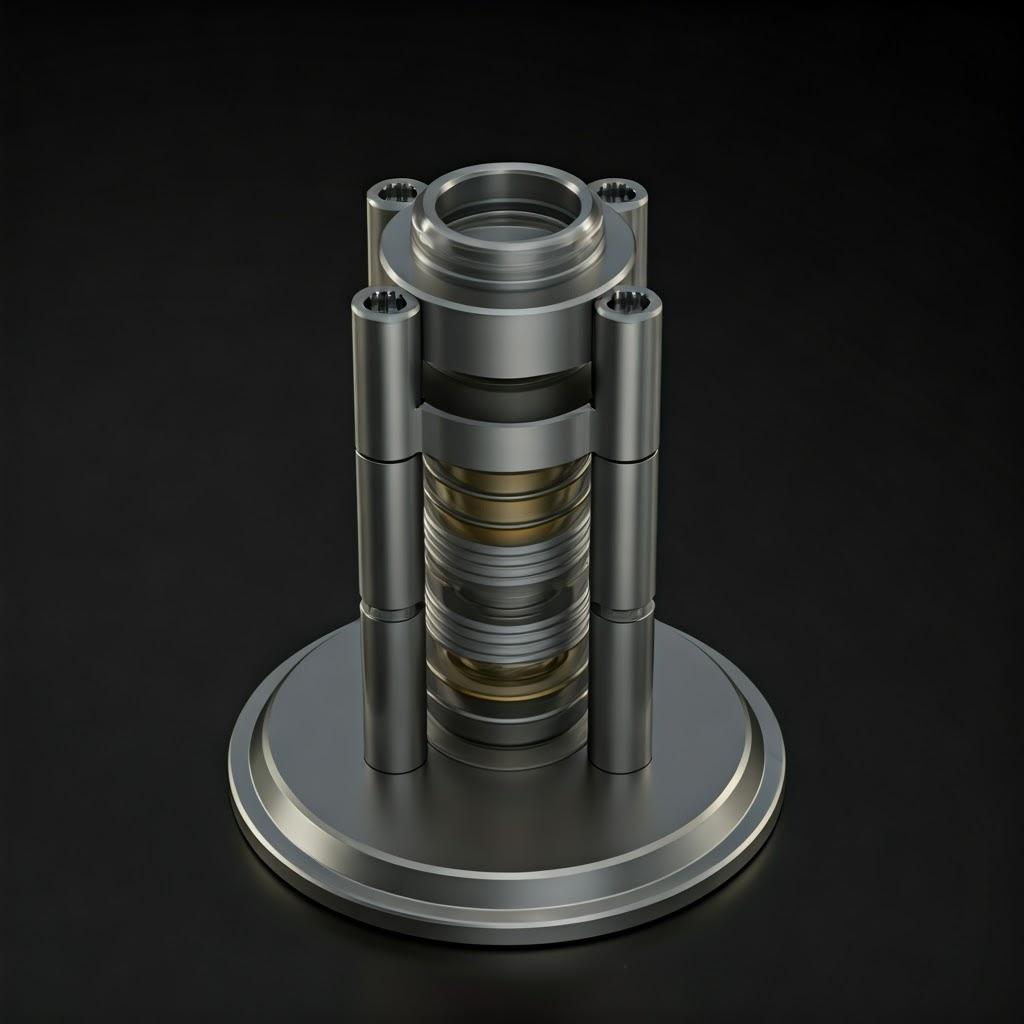
Cost Analysis & Lead Times: Budgeting for Wholesale 3D Printed Antenna Mount Orders
Understanding the cost structure and typical lead times associated with metal additive manufacturing is crucial for effective project planning and budgeting, particularly when considering wholesale or bulk orders of aluminum antenna mounts. Unlike traditional manufacturing where tooling often dominates initial costs, AM costs are primarily driven by material consumption, machine time, and post-processing labor. Procurement managers need to understand these drivers to accurately evaluate quotes (RFQs) and manage budgets.
Key Cost Factors for 3D Printed Aluminum Antenna Mounts:
- Material Consumption:
- Part Volume: The physical volume of the final part directly impacts the amount of expensive metal powder (AlSi10Mg or higher-cost Scalmalloy®) consumed. DfAM techniques like topology optimization significantly reduce material use and cost.
- Support Structures: Material used for support structures adds to the overall consumption. Optimized orientation and design minimize support volume.
- Powder Cost: The base cost per kilogram of the chosen aluminum alloy powder. Scalmalloy® is significantly more expensive than AlSi10Mg.
- Machine Time (Print Time):
- Part Height (Z-Height): Print time is strongly correlated with the number of layers required, meaning taller parts take longer to print, regardless of their width or depth. Orientation plays a key role here.
- Part Volume & Density: Larger or denser parts require more laser scanning time per layer. Intricate features or extensive lattice structures can also increase scan time.
- Nesting Efficiency: Printing multiple parts simultaneously (nesting) utilizes the machine more efficiently, reducing the effective machine time cost per part, especially beneficial for wholesale orders.
- Machine Hourly Rate: The operational cost of the PBF-LB machine, factoring in depreciation, energy, maintenance, labor, and inert gas consumption.
- Post-Processing Labor and Operations:
- Support Removal: Labor time required depends heavily on the complexity and quantity of support structures. Difficult-to-access supports increase time and cost.
- Heat Treatment: Costs associated with furnace time, energy, controlled atmosphere, and labor for stress relief, T6 aging, or HIP cycles. HIP is a significant additional cost.
- Machining: CNC machining time for critical tolerances or surfaces adds cost based on complexity, setup time, and machining duration.
- Surface Finishing: Costs for blasting, tumbling, anodizing, coating, etc., based on the process chosen, surface area, and labor involved.
- Quality Assurance and Inspection:
- The level of inspection required (visual, basic dimensional checks, CMM, 3D scanning, NDT like CT scanning, material coupon testing) adds cost based on the time and equipment needed. Stringent requirements for aerospace naturally incur higher inspection costs.
- Order Volume:
- Setup Costs: While AM is tool-less, there are setup costs for build preparation (file processing, orientation, support generation). These costs are amortized over the number of parts in a build.
- Economies of Scale: For wholesale or bulk orders, suppliers can often offer lower per-part pricing due to optimized machine utilization (full build plates through nesting) and more efficient batch processing in post- P&L stages.
Lead Time Components:
Lead time is the total time from order placement to parts shipment. It’s influenced by several factors:
- Queue Time: Time waiting for machine availability, which depends on the supplier’s current workload.
- Build Preparation: Time for final CAD checks, orientation optimization, support generation, and build file slicing. (Typically hours to a day).
- Printing Time: Actual time the parts are printing in the machine. (Can range from hours to several days depending on part height, volume, and quantity).
- Cooling Time: Parts need to cool down within the machine under inert atmosphere after the build finishes. (Typically several hours).
- Post-Processing: Time required for de-powdering, stress relief, part/support removal, heat treatment, HIP (if needed), machining, finishing, and inspection. This can often take longer than the print time itself, potentially ranging from a few days to several weeks depending on the complexity of the steps involved.
- Shipping: Transit time to your facility.
Indicative Lead Times (Aluminum PBF-LB):
- Prototypes: Typically 1-3 weeks, depending on complexity and post-processing.
- Low-Volume Production / Wholesale Batches: Often 3-6 weeks, heavily dependent on part complexity, quantity, post-processing requirements, and supplier capacity.
Budgeting and RFQ Considerations:
- Provide Clear Specifications: To get accurate quotes, provide a detailed 3D CAD model, 2D drawings with GD&T for critical tolerances, material specification (AlSi10Mg or Scalmalloy®), required heat treatment, surface finish requirements, inspection criteria, and desired quantity (including potential future volumes for wholesale pricing).
- Request Detailed Breakdowns: Ask suppliers to break down their quotes to show costs associated with material, printing, and key post-processing steps. This helps in comparing quotes and understanding value.
- Discuss Lead Time: Clearly communicate your required delivery dates and discuss the supplier’s ability to meet them based on their capacity and the defined workflow.
- Consider Total Cost of Ownership: Factor in potential savings from lightweighting (e.g., fuel savings in aerospace) or part consolidation (reduced assembly cost) when comparing AM to traditional methods, not just the per-part price.
By understanding these cost drivers and lead time components, procurement managers and engineers can better budget for aluminum 3D printed antenna mounts, engage effectively with suppliers during the RFQ process, and make informed decisions for both prototyping and wholesale production needs.
Frequently Asked Questions (FAQ) about Aluminum 3D Printed Antenna Mounts
Here are answers to some common questions engineers and procurement managers have about using aluminum additive manufacturing for antenna mounts:
1. What level of tolerance and precision can I realistically expect from 3D printed aluminum antenna mounts?
- As-Built: Typically, PBF-LB processes like SLM/DMLS achieve general tolerances of around ±0.1 mm to ±0.3 mm for smaller features, or roughly ±0.1-0.2% for larger dimensions. However, this is highly dependent on the part geometry, orientation, material (AlSi10Mg vs. Scalmalloy®), and the specific machine/process control.
- Critical Features: For tighter tolerances required on mating surfaces, interfaces, or hole positions/diameters, post-print CNC machining is almost always necessary. With machining, tolerances comparable to traditional methods (e.g., ±0.025 mm to ±0.05 mm or better) can be achieved on specific features.
- Recommendation: Clearly define critical tolerances using GD&T on your engineering drawings and discuss these requirements with your AM supplier (like Met3dp) early to determine the best approach (as-built vs. machined) and ensure feasibility.
2. Can functional threads be directly 3D printed in aluminum antenna mounts?
- Direct Printing Challenges: While it’s technically possible to print thread-like structures, directly printing small, standard threads (e.g., M3, M4, M5) often results in poor quality, insufficient strength, and rough surfaces due to the layer-wise process resolution and powder particle size. They may not meet standard thread specifications for reliable fastening. Larger, coarser threads might be printable but often lack precision.
- Recommended Solutions:
- Post-Print Tapping/Threading: The most common and reliable method is to print holes to the appropriate pilot diameter and then tap the threads using conventional machining methods during post-processing.
- Threaded Inserts: Designing pockets to accommodate standard threaded inserts (like Helicoils or PEM inserts) is another robust solution, providing strong, reusable threads, especially in softer aluminum alloys.
- Consultation: Discuss threading requirements with your supplier to determine the most practical and reliable method for your specific antenna mount design.
3. How does the cost of aluminum 3D printing compare to CNC machining for antenna mounts, especially considering prototypes vs. production?
- Prototypes & Low Volumes (1-50 parts): Metal 3D printing is often very cost-competitive or even cheaper than CNC machining, especially for complex geometries. This is because AM avoids the high setup costs and programming time associated with complex CNC jobs and eliminates the need for custom fixtures. The more complex the part, the greater the potential cost advantage for AM in low volumes.
- Medium Volumes (50-500 parts): The cost comparison becomes more nuanced. As volumes increase, the per-part cost of CNC machining tends to decrease more rapidly than AM due to amortization of setup costs and faster cycle times per part. However, if the antenna mount geometry is highly complex or topology-optimized (difficult/wasteful to machine), AM might remain competitive or preferable due to design advantages. Part consolidation via AM can also offset higher per-part print costs with lower assembly costs.
- High Volumes (500+ parts): For simpler geometries, traditional methods like casting or high-speed CNC machining are typically more cost-effective than AM due to faster cycle times. However, for extremely complex, highly optimized designs where AM’s unique capabilities provide significant performance benefits (e.g., extreme lightweighting), AM might still be considered despite a higher per-part cost.
- Key Takeaway: The crossover point depends heavily on part complexity, material choice, and required post-processing. Always get quotes for both methods if feasible, considering the total cost of ownership, including assembly and potential performance benefits.
4. What information does an AM supplier need for an accurate Request for Quote (RFQ)?
- 3D CAD Model: A native CAD file (e.g., STEP, Parasolid) is essential.
- 2D Engineering Drawing: Specify critical dimensions, tolerances (ideally using GD&T), required surface finishes (Ra values), material specification (AlSi10Mg or Scalmalloy®), and any specific feature requirements (e.g., tapped holes, required flatness).
- Material & Post-Processing: Clearly state the desired aluminum alloy and any required post-processing steps (e.g., T6 heat treatment, HIP, specific anodizing type, machining operations).
- Quantity: Specify the number of parts needed for this order and, if applicable, estimated annual volume or future batch sizes for wholesale pricing consideration.
- Quality & Inspection Requirements: Detail any specific inspection needs (e.g., CMM report, material certifications, NDT requirements).
- Application Context (Optional but helpful): Briefly describing the part’s function and operating environment can help the supplier provide better DfAM feedback or suggest optimal processing.
Providing comprehensive information enables suppliers like Met3dp to deliver accurate quotes and realistic lead times promptly.
Conclusion: The Future of Antenna Mounts is Lightweight, Strong, and Additively Manufactured
The landscape of component manufacturing is continually evolving, and for antenna mounts across demanding industries like aerospace, automotive, and telecommunications, aluminum additive manufacturing represents a significant leap forward. As we’ve explored, leveraging PBF-LB technology with advanced alloys like AlSi10Mg and Scalmalloy® unlocks possibilities that were previously out of reach with traditional methods. The ability to create highly complex, topology-optimized geometries allows for unprecedented lightweighting without compromising structural integrity – a critical advantage where every gram counts. Furthermore, the design freedom afforded by AM enables part consolidation, leading to simpler assemblies, reduced part counts, and potentially enhanced system reliability.
From rapid prototyping that accelerates development cycles to cost-effective low-volume production and the potential for on-demand manufacturing, aluminum 3D printing offers compelling benefits for both engineers striving for optimal performance and procurement managers seeking efficient and flexible supply chain solutions. While challenges related to design optimization (DfAM), precision control, post-processing complexity, and cost management exist, they are effectively navigated through careful planning, adherence to best practices, and partnership with experienced suppliers.
Successfully implementing aluminum AM for antenna mounts hinges on three key pillars: intelligent design tailored for the process (DfAM), appropriate material selection balancing performance and cost (AlSi10Mg vs. Scalmalloy®), and choosing a capable, quality-focused manufacturing partner. A reliable supplier brings not just printing capabilities but also crucial expertise in materials science, process control, comprehensive post-processing, and rigorous quality assurance.
Met3dp stands ready to be that partner. With our state-of-the-art PBF-LB printers, advanced powder manufacturing capabilities using gas atomization and PREP technologies, extensive experience with high-performance aluminum alloys, and a commitment to quality and customer collaboration, we offer comprehensive solutions for your antenna mount needs. We provide support from initial design consultation and DfAM feedback through to final inspection and delivery, whether for single prototypes or scalable wholesale production.
The future of high-performance antenna systems relies on components that are lighter, stronger, and more integrated. Aluminum additive manufacturing is a key enabler of this future.
Ready to explore how aluminum 3D printing can revolutionize your antenna mount designs?
Contact Met3dp today for a consultation or to request a quote for your project. Visit our website at https://met3dp.com/ to learn more about our capabilities and how we can power your organization’s additive manufacturing goals.
Share On
MET3DP Technology Co., LTD is a leading provider of additive manufacturing solutions headquartered in Qingdao, China. Our company specializes in 3D printing equipment and high-performance metal powders for industrial applications.
Inquiry to get best price and customized Solution for your business!
Related Articles
About Met3DP
Recent Update
Our Product
CONTACT US
Any questions? Send us message now! We’ll serve your request with a whole team after receiving your message.
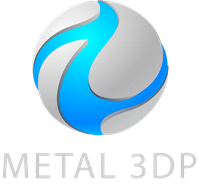
Metal Powders for 3D Printing and Additive Manufacturing