Lightweight Antenna Supports for Drones 3D Printed in Aluminum
Table of Contents
Introduction: The Critical Role of Lightweight Antenna Supports in Drone Performance
Unmanned Aerial Vehicles (UAVs), commonly known as drones, have rapidly transitioned from niche novelties to indispensable tools across countless industries. From aerial surveillance and precision agriculture to package delivery and cinematic videography, their applications continue to expand at an unprecedented rate. Central to the reliable and effective operation of any drone is its ability to maintain robust communication and navigation links. This hinges significantly on the performance and integrity of its antenna systems. While the antennas themselves are crucial, the structures supporting them – the antenna supports or mounts – play an equally vital, albeit often overlooked, role. These components must securely hold the antennas in optimal positions, withstand operational stresses, and, critically, contribute minimally to the overall weight of the aircraft. In the world of drone design and manufacturing, every gram counts. Weight directly impacts flight duration, payload capacity, maneuverability, and energy consumption. Therefore, the quest for high-strength, low-weight components is relentless, making the design and fabrication of antenna supports a significant engineering challenge.
Traditionally, manufacturing these components involved methods like CNC machining from billet aluminum or plastic injection molding. While effective, these methods often present limitations, particularly regarding geometric complexity, material waste (subtractive manufacturing), and the ability to achieve truly optimized lightweight structures. This is where the transformative power of metal 3D printing, also known as additive manufacturing (AM), enters the picture. By building parts layer by layer directly from metal powder, AM enables the creation of highly complex, topology-optimized geometries that were previously impossible or prohibitively expensive to produce. This technology allows engineers to place material precisely where it’s needed for strength and rigidity while eliminating it elsewhere, resulting in components that are significantly lighter than their traditionally manufactured counterparts without compromising structural integrity. For drone antenna supports, this means achieving the necessary stiffness and durability to maintain antenna alignment under vibration and G-forces, while drastically reducing weight – a win-win for overall drone performance. The ability to use high-performance aluminum alloys like AlSi10Mg and A7075, known for their excellent strength-to-weight ratios, further enhances the appeal of metal AM for this application. This article delves into the specifics of using metal 3D printing, particularly with AlSi10Mg and A7075 aluminum powders, to produce superior, lightweight antenna supports for a wide range of drone applications, exploring the benefits, design considerations, material choices, and manufacturing processes involved. We will also highlight how partnering with an experienced metal AM provider like Met3dp, with its advanced powder manufacturing and printing capabilities, can ensure the production of high-quality, reliable components for demanding UAV systems.
The integration of advanced materials and manufacturing techniques is paramount as drone technology continues to evolve. The demands placed on UAVs, whether for extended surveillance missions requiring maximum flight endurance or for agile cinematic drones needing high maneuverability, necessitate components that push the boundaries of performance. Antenna supports, seemingly simple components, become critical enablers in this context. A poorly designed or overly heavy support can compromise signal integrity through vibration or misalignment and penalize the drone’s primary performance metrics. Conversely, a well-designed, lightweight, additively manufactured support enhances communication reliability and contributes directly to longer flight times or increased payload capacity. Consider the cumulative effect: reducing the weight of multiple components, even by small amounts each, leads to substantial overall weight savings, unlocking significant performance improvements. Metal additive manufacturing provides the key to unlocking these savings for complex structural components like antenna supports, moving beyond the constraints of traditional methods and embracing designs dictated purely by functional requirements and optimization algorithms. The aerospace industry, a major driver and beneficiary of drone technology, has already widely adopted AM for lightweight structural brackets and components, recognizing its potential for performance enhancement and part consolidation. Applying these principles to antenna supports is a logical and highly beneficial progression, leveraging the inherent advantages of layer-by-layer fabrication to create parts optimized for the unique demands of UAV operation. Furthermore, the speed of AM allows for rapid design iteration and customization, enabling manufacturers to quickly adapt supports for new antenna types, different drone platforms, or specific mission requirements – a level of agility often difficult to achieve with traditional tooling-dependent processes. As we explore the specifics of this application, the compelling advantages of using advanced aluminum alloys and metal 3D printing will become increasingly clear.
What are Drone Antenna Supports Used For? Functionality Across Diverse UAV Applications
Drone antenna supports, also known as antenna mounts or brackets, are structural components designed with a primary, critical function: to securely hold and precisely position one or more antennas on a UAV platform. Their role extends beyond merely attaching the antenna; they are integral to ensuring the optimal performance and reliability of the drone’s communication, navigation, and data telemetry systems. The specific functions and design requirements can vary significantly depending on the type of drone, the antennas being used, and the operational environment.
Core Functions of Drone Antenna Supports:
- Secure Mounting: The most fundamental role is to provide a stable and secure attachment point for the antenna(s) to the drone’s airframe or fuselage. This prevents the antenna from detaching or shifting due to vibrations, aerodynamic forces, shock during landing, or general handling.
- Precise Positioning and Orientation: Antennas often have specific directional characteristics (gain patterns). The support must hold the antenna in the optimal orientation relative to the ground station, satellites (for GNSS), or other communication nodes to maximize signal strength and link quality. This orientation must be maintained consistently throughout the flight envelope.
- Vibration Isolation/Damping (Sometimes): In some high-performance or sensitive applications, the support may incorporate features or materials designed to dampen vibrations originating from the drone’s motors and propellers. Excessive vibration can degrade antenna performance and potentially damage sensitive antenna components or connections.
- Environmental Protection: The support contributes to shielding the antenna’s base and connectors from environmental factors like dust, moisture, and impacts, depending on its design and placement.
- Maintaining Ground Plane Integrity (If Applicable): Certain antenna types (e.g., monopole or patch antennas) rely on a ground plane for proper operation. The antenna support, especially if made of conductive metal, can influence or be part of this ground plane. Its design must ensure it doesn’t negatively interfere with the antenna’s required electromagnetic environment.
- Cable Management: Supports often incorporate features to route and secure antenna cables, preventing them from snagging, vibrating excessively, or interfering with other drone components or aerodynamics.
- Structural Integrity: The support must be strong enough to withstand the static and dynamic loads experienced during flight, including acceleration, deceleration, turns, vibration, and potential hard landings, without failing or deforming in a way that compromises antenna position.
Applications Across Drone Types:
The specific demands on antenna supports vary widely across different UAV categories:
- Consumer/Hobbyist Drones: Typically prioritize low cost and ease of manufacture. Supports might be simpler, often made from injection-molded plastics. However, even here, weight is critical for flight time, and ensuring proper orientation for Wi-Fi or remote control antennas is essential. As consumer drones become more sophisticated, the need for better materials and designs increases.
- Commercial/Industrial Drones: Used for mapping, inspection, agriculture, delivery, etc. These drones often carry multiple, higher-performance antennas for robust remote control, high-bandwidth video transmission, GNSS (GPS, GLONASS, etc.), and potentially specialized sensors (e.g., RTK antennas for high-precision positioning).
- Reliability is paramount. Antenna support failure could mean loss of control or mission failure, with significant financial or operational consequences.
- Weight is crucial for maximizing payload (sensors, cameras, packages) and endurance.
- Optimal positioning for multiple antennas without mutual interference is a key design challenge. Supports may need complex geometries to achieve this.
- Durability is needed to withstand frequent use in potentially harsh outdoor environments.
- Military/Surveillance UAVs: These platforms operate under the most demanding conditions and often carry highly sensitive and specialized antenna payloads for encrypted communication (COMINT), signals intelligence (SIGINT), electronic warfare (EW), high-resolution video, satellite communications (SATCOM), and precise navigation.
- Extreme reliability and survivability are non-negotiable. Supports must withstand high G-forces, extreme temperatures, and potentially harsh handling.
- Weight savings are critical for endurance, altitude ceilings, and payload capacity (often significant sensor suites).
- Stealth considerations (Low Observable) might influence material choice and design to minimize radar cross-section (RCS).
- Specific RF performance requirements necessitate precise positioning and minimal interference from the support structure. Supports might require complex shapes to integrate smoothly with the airframe’s aerodynamic profile.
- Fixed-Wing vs. Multirotor Drones:
- Multirotor drones experience significant high-frequency vibrations from motors, potentially requiring damping features in the supports. Landing gear integration might also be a factor.
- Fixed-wing drones experience different aerodynamic loads and vibration profiles. Supports might need to be designed for higher airspeeds and integrated into wings or fuselage sections.
Given this diversity, antenna supports are far from generic components. They require careful engineering tailored to the specific drone platform and its mission profile. The need for lightweight, strong, and potentially complex geometries makes them ideal candidates for optimization through metal additive manufacturing, particularly using high-strength aluminum alloys favored in aerospace applications. Companies specializing in drone manufacturing, UAV component suppliers, and aerospace engineering firms are constantly seeking improved solutions for these critical parts, making advanced manufacturing techniques like metal 3D printing increasingly attractive.
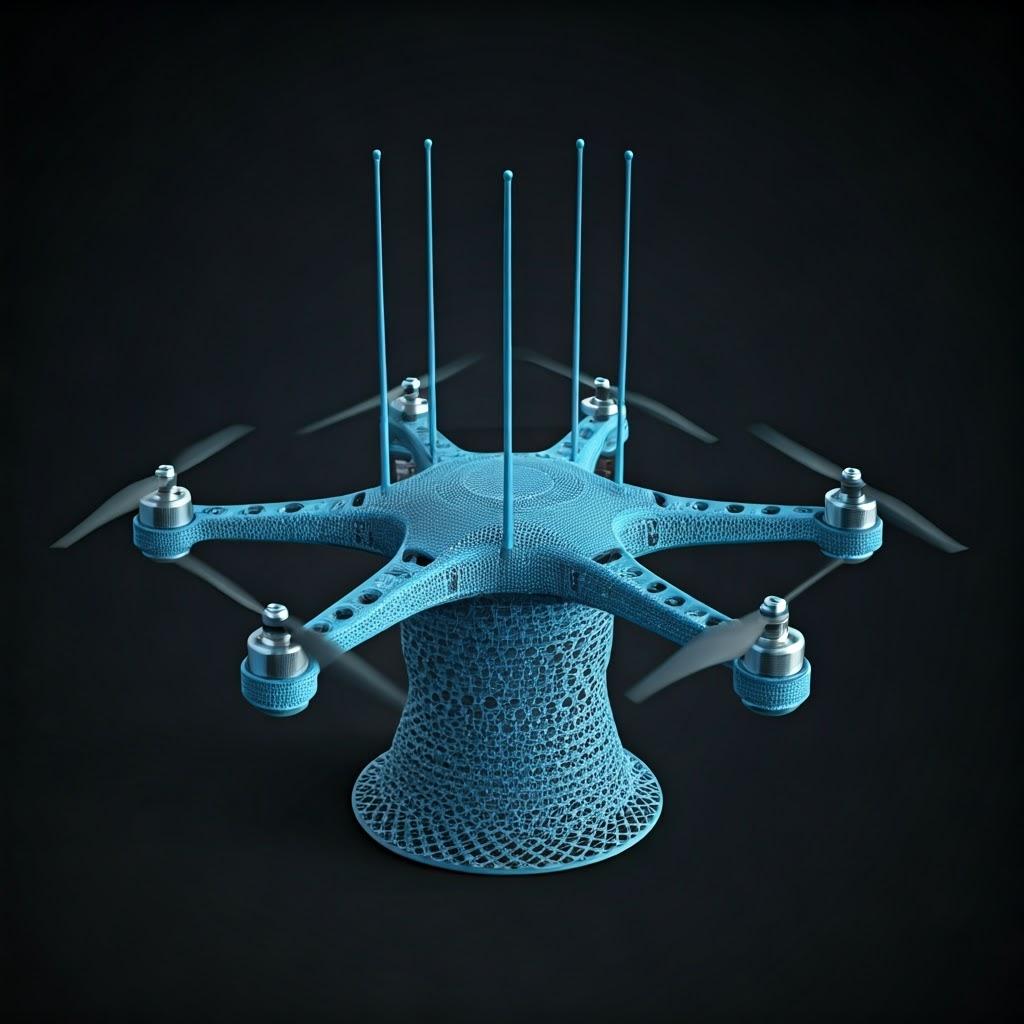
Why Use Metal 3D Printing for Drone Antenna Supports? Unlocking Design Freedom and Performance Gains
The decision to manufacture drone antenna supports using metal additive manufacturing (AM), specifically techniques like Selective Laser Melting (SLM) or Direct Metal Laser Sintering (DMLS) – both types of Laser Powder Bed Fusion (LPBF) – stems from a compelling set of advantages over traditional manufacturing methods like CNC machining, casting, or injection molding (for plastics). These benefits directly address the key challenges in drone design: weight reduction, performance optimization, and manufacturing agility.
1. Unparalleled Lightweighting through Design Optimization:
- Topology Optimization: This is arguably the most significant advantage. AM allows engineers to use software tools that optimize the geometry of a part based on specific load cases and constraints. Material is removed from areas where it isn’t contributing significantly to strength or stiffness, resulting in organic-looking, highly efficient structures. For an antenna support, this means creating a mount that provides the necessary rigidity and strength to hold the antenna securely and maintain its orientation under flight loads, but with the absolute minimum amount of material possible. Weight savings compared to traditionally designed and machined parts can often range from 30% to 60% or even more, directly translating to longer flight times, increased payload capacity, or improved maneuverability for the drone.
- Lattice Structures: AM makes it feasible to incorporate internal lattice or honeycomb structures within the solid walls of the support. These structures provide excellent stiffness and strength at a fraction of the weight of solid material. This is extremely difficult or impossible to achieve with subtractive methods like CNC machining.
- Material Choice: Metal AM enables the use of high-strength, low-density aerospace-grade materials like aluminum alloys (AlSi10Mg, A7075) and titanium alloys. While these can be machined, AM allows them to be formed into optimized shapes that maximize their inherent strength-to-weight benefits.
2. Geometric Complexity and Part Consolidation:
- Complex Shapes: AM builds parts layer by layer, freeing designers from many constraints imposed by traditional methods (e.g., tool access for CNC, draft angles for molding/casting). This allows for the creation of highly complex, intricate geometries needed to:
- Integrate seamlessly with curved or complex drone airframes.
- Position multiple antennas optimally to avoid interference.
- Incorporate internal channels for cable routing or cooling (if needed).
- Integrate damping features directly into the structure.
- Part Consolidation: A complex antenna mounting assembly that might traditionally require multiple individual parts (brackets, fasteners, spacers) can often be redesigned and printed as a single, integrated component. This reduces part count, eliminates fasteners (potential failure points), simplifies assembly, reduces overall weight, and improves structural integrity.
3. Rapid Prototyping and Design Iteration:
- Speed: AM allows engineers to move from a digital design file (CAD) to a physical metal prototype relatively quickly, often within days, without the need for expensive tooling (like molds or jigs). This accelerates the design iteration cycle dramatically. Multiple design variations for an antenna support can be printed and tested in a short period, allowing for rapid optimization of performance (e.g., vibration damping, antenna positioning) and weight.
- Customization: Drone platforms often require customized antenna setups depending on the mission or payload. AM makes it economically viable to produce small batches or even one-off custom antenna supports tailored to specific requirements without incurring high setup or tooling costs associated with traditional methods. This is ideal for specialized commercial or military UAVs.
4. Enhanced Performance Characteristics:
- Strength and Stiffness: Using high-performance metal powders like Aluminum A7075 (with appropriate post-processing) or specific Titanium grades allows for supports that are significantly stronger and stiffer than plastic alternatives and can match or exceed the performance of machined aluminum, often at a lower weight due to optimization. This ensures antenna stability under high G-loads and vibrations.
- Material Properties: Metal AM produces parts with excellent mechanical properties, often comparable or even superior (in certain aspects, like fatigue life due to fine microstructure) to wrought or cast materials, especially after appropriate post-processing like Hot Isostatic Pressing (HIP) and heat treatments. Providers like Met3dp utilize advanced powder manufacturing techniques (Gas Atomization, PREP) to ensure high-quality, spherical powders, which are crucial for printing dense, high-performance parts.
5. Manufacturing Efficiency and Reduced Waste:
- Near-Net Shape: AM is an additive process, meaning material is only added where it’s needed. This results in significantly less material waste compared to subtractive CNC machining, where often up to 80-90% of the initial material block can be machined away as chips (buy-to-fly ratio). While some support structures are needed in AM, the overall material utilization is typically much better, especially for complex parts.
- Tooling Elimination: AM eliminates the need for expensive and time-consuming tooling (molds, dies, jigs, fixtures) required for methods like injection molding, casting, or complex CNC setups. This reduces upfront costs and lead times, particularly for low-to-medium volume production runs common for specialized drone components.
Comparison Table: AM vs. Traditional Methods for Drone Antenna Supports
Feature | Metal AM (LPBF) | CNC Machining (Aluminum) | Injection Molding (Plastic) |
---|---|---|---|
Lightweighting | Excellent (Topology opt., lattices) | Good (Limited by tool access) | Fair (Lower density, lower strength) |
Geometric Complexity | Very High | Moderate to High (Multi-axis) | High (but requires complex molds) |
Part Consolidation | Excellent | Limited | Limited |
Strength-to-Weight | Excellent (High-strength Al/Ti alloys optimized) | Good (Bulk material properties) | Lower |
Rapid Prototyping | Excellent (Fast turnaround, no tooling) | Fair (Requires programming, setup) | Poor (Requires expensive tooling) |
Customization Cost | Low (Per part cost relatively stable) | High (Programming/setup per design) | Very High (Tooling cost dominates low volumes) |
Material Waste | Low (Near-net shape, powder recycling) | High (Subtractive process) | Low (but tooling intensive) |
Lead Time (Prototype) | Short | Moderate | Long (Tooling manufacture) |
Lead Time (Production) | Scalable, competitive for complex/low-vol parts | Good for high volume, less for complex/low-vol | Best for very high volume, simple parts |
Initial Investment | High (Machine cost), Low (No tooling per part) | Moderate (Machine cost), Moderate (Fixturing) | Very High (Tooling cost) |
Export to Sheets
In summary, metal 3D printing offers a compelling value proposition for manufacturing drone antenna supports, particularly when lightweighting, complex geometry, customization, and rapid development are key priorities. It empowers engineers to design components previously unachievable, directly contributing to enhanced drone performance, reliability, and capability across diverse applications, from commercial operations to demanding military missions. Leveraging the capabilities of specialized AM providers ensures access to the necessary expertise, equipment, and quality control for producing flight-ready components.
Recommended Aluminum Powders (AlSi10Mg & A7075) and Why They Excel for Drone Components
Choosing the right material is fundamental to the success of any engineering application, and this is especially true for critical components like drone antenna supports manufactured via additive manufacturing. Aluminum alloys are often the go-to choice for aerospace and drone applications due to their favorable combination of low density, good mechanical properties, corrosion resistance, and relatively lower cost compared to materials like titanium. Within the realm of metal 3D printing, two aluminum alloys stand out for such applications: AlSi10Mg and A7075. While both are aluminum-based, they offer distinct properties making them suitable for different requirements. Selecting the optimal powder requires understanding their characteristics and how they translate to performance in a UAV context.
Met3dp: Ensuring Powder Quality for Optimal Printing
Before diving into the specifics of each alloy, it’s crucial to emphasize the importance of powder quality. The final properties of a 3D printed metal part are intrinsically linked to the characteristics of the raw material powder. Factors like particle size distribution (PSD), sphericity, flowability, and chemical purity directly impact the density, microstructure, and mechanical performance of the printed component. Met3dp, leveraging its expertise and advanced powder production technologies like Vacuum Induction Melting Gas Atomization (VIGA) and Plasma Rotating Electrode Process (PREP), specializes in manufacturing high-quality, spherical metal powders optimized for additive manufacturing processes like Laser Powder Bed Fusion (LPBF). Using consistently high-quality powders from a reliable supplier like Met3dp is the first step towards achieving reliable, high-performance 3D printed drone components. Our powders are designed to ensure:
- High Sphericity & Good Flowability: Essential for uniform powder bed spreading, leading to consistent melt pool behavior and high part density.
- Controlled Particle Size Distribution: Optimized PSD ensures good packing density and resolution capabilities.
- Low Oxygen & Impurity Content: Minimizes defects like porosity and ensures predictable mechanical properties.
- Batch-to-Batch Consistency: Guarantees repeatable results for production runs.
1. AlSi10Mg: The Workhorse Aluminum Alloy for AM
AlSi10Mg is one of the most widely used and well-characterized aluminum alloys in metal additive manufacturing. It’s essentially an aluminum-silicon-magnesium casting alloy adapted for AM processes.
- Key Properties & Advantages for Drone Supports:
- Excellent Printability: AlSi10Mg is known for its relatively straightforward processing using LPBF. It has good fluidity in the molten state and lower tendency towards cracking during solidification compared to some other high-strength aluminum alloys. This translates to higher reliability and success rates during printing, especially for complex geometries.
- Good Strength-to-Weight Ratio: While not the highest-strength aluminum alloy, it offers a good balance of mechanical strength, stiffness, and low density (approx. 2.67 g/cm³). This makes it suitable for many drone components where weight reduction is important but extreme strength is not the sole driver.
- Good Thermal Properties: It exhibits good thermal conductivity, which can be beneficial if the antenna support is located near heat-generating components, helping to dissipate heat.
- Corrosion Resistance: Offers good resistance to atmospheric corrosion, suitable for drones operating in various environmental conditions.
- Post-Processing Options: Can be heat-treated (typically stress relief or T6-like treatments, though response differs from cast T6) to improve strength and ductility. It’s also readily machinable for critical features, weldable, and can be surface treated (e.g., anodizing, painting).
- Cost-Effectiveness: Generally, AlSi10Mg powder is more readily available and cost-effective compared to higher-strength alloys like A7075 tailored for AM.
- Considerations:
- Its strength (yield strength typically 230-300 MPa, UTS 350-450 MPa after stress relief/heat treatment) is lower than high-strength wrought alloys like A7075.
- Ductility (elongation at break) is typically moderate (around 5-10%), which might be a limitation in applications requiring high toughness or energy absorption.
- Ideal Applications for Drone Supports: General purpose antenna supports for commercial and hobbyist drones, supports where complex geometry and good printability are key, applications where moderate strength is sufficient, and cost is a significant factor.
2. A7075 (Aluminum 7075): High Strength for Demanding Applications
A7075 is a well-known high-strength aluminum-zinc-magnesium-copper alloy traditionally used in aerospace applications in its wrought form (e.g., aircraft structures). Adapting it for additive manufacturing has been more challenging due to its susceptibility to solidification cracking (hot tearing) during the rapid heating/cooling cycles of LPBF. However, advancements in alloy modification for AM, specialized powder production (like that employed by Met3dp), and optimized printing parameters have made it increasingly viable.
- Key Properties & Advantages for Drone Supports:
- Very High Strength-to-Weight Ratio: This is the primary advantage of A7075. After appropriate heat treatment (typically a T6 cycle), AM-produced A7075 can achieve mechanical properties (Yield Strength > 450-500 MPa, UTS > 520-570 MPa) approaching those of wrought A7075-T6. This makes it ideal for highly loaded structural components where minimizing weight while maximizing strength is critical.
- Excellent Strength & Stiffness: Significantly stronger and stiffer than AlSi10Mg, allowing for even thinner walls and more aggressive lightweighting for antenna supports subjected to higher loads or vibration.
- Fatigue Resistance: Generally exhibits good fatigue properties, important for components experiencing cyclic loading during flight.
- Considerations:
- Printability Challenges: Historically more difficult to print reliably than AlSi10Mg. It requires carefully controlled process parameters (laser power, scan speed, layer thickness, atmosphere control) and potentially modified alloy compositions specifically designed for AM to mitigate cracking. Partnering with an experienced AM provider like Met3dp, familiar with processing high-strength aluminum alloys, is crucial.
- Heat Treatment Requirement: Achieving the high-strength properties necessitates a specific multi-stage heat treatment (solution treatment, quenching, artificial aging – T6 cycle). This adds complexity and cost to the post-processing workflow.
- Corrosion Resistance: While generally good, A7075 can be more susceptible to stress corrosion cracking (SCC) than AlSi10Mg, especially in certain temper states and environments. Surface treatments like anodizing or painting are often recommended for protection.
- Cost: A7075 powder specifically designed and qualified for AM is typically more expensive than AlSi10Mg. The more complex printing and post-processing also contribute to a higher final part cost.
- Ideal Applications for Drone Supports: Supports for heavy or multiple antennas, components on high-performance military or aerospace UAVs, applications where the absolute minimum weight is required for a given strength requirement, parts subjected to high G-loads or significant vibration where maximum structural integrity is paramount.
Comparison Table: AlSi10Mg vs. A7075 for 3D Printed Drone Supports
Feature | AlSi10Mg (AM, Typical Heat Treated) | A7075 (AM, T6 Heat Treated) | Key Takeaway for Drone Supports |
---|---|---|---|
Density | ~2.67 g/cm³ | ~2.81 g/cm³ | Both are lightweight; A7075 slightly denser but much stronger. |
Yield Strength (Typical) | 230 – 300 MPa | 450 – 500+ MPa | A7075 offers significantly higher strength potential. |
Ultimate Tensile Strength (Typical) | 350 – 450 MPa | 520 – 570+ MPa | A7075 provides superior ultimate strength. |
Elongation at Break | 5 – 10% | 3 – 8% | Both have moderate to low ductility; AlSi10Mg often slightly better. |
Stiffness (Young’s Modulus) | ~70 GPa | ~72 GPa | Similar stiffness. |
Printability | Excellent | Moderate to Good (Requires Expertise) | AlSi10Mg is generally easier and more reliable to print. |
Heat Treatment | Optional (Stress Relief / T5/T6-like) | Required (T6 cycle for high strength) | A7075 requires mandatory, complex heat treatment for properties. |
Corrosion Resistance | Good | Fair to Good (Anodizing often recommended) | AlSi10Mg generally better; A7075 may need more protection. |
Cost (Powder & Process) | Lower | Higher | A7075 is a premium material with higher associated costs. |
Export to Sheets
Conclusion on Materials:
The choice between AlSi10Mg and A7075 for a 3D printed drone antenna support depends heavily on the specific application requirements.
- Choose AlSi10Mg when: Good strength-to-weight is needed, cost is a major driver, complex geometries require high printability confidence, and extreme mechanical strength is not the primary requirement. It’s an excellent general-purpose choice available from quality metal powder suppliers like Met3dp.
- Choose A7075 when: Maximum strength-to-weight ratio is paramount, the support is subjected to high loads or stresses, minimum weight is critical (e.g., military/aerospace UAVs), and the higher cost and processing complexity are justified by the performance gains. Success relies heavily on using high-quality AM-specific powder and partnering with a service provider experienced in processing this demanding alloy.
By carefully considering these material properties and leveraging the design freedom of additive manufacturing, engineers can create drone antenna supports that are lighter, stronger, and better integrated than ever before, pushing the performance boundaries of UAV technology.
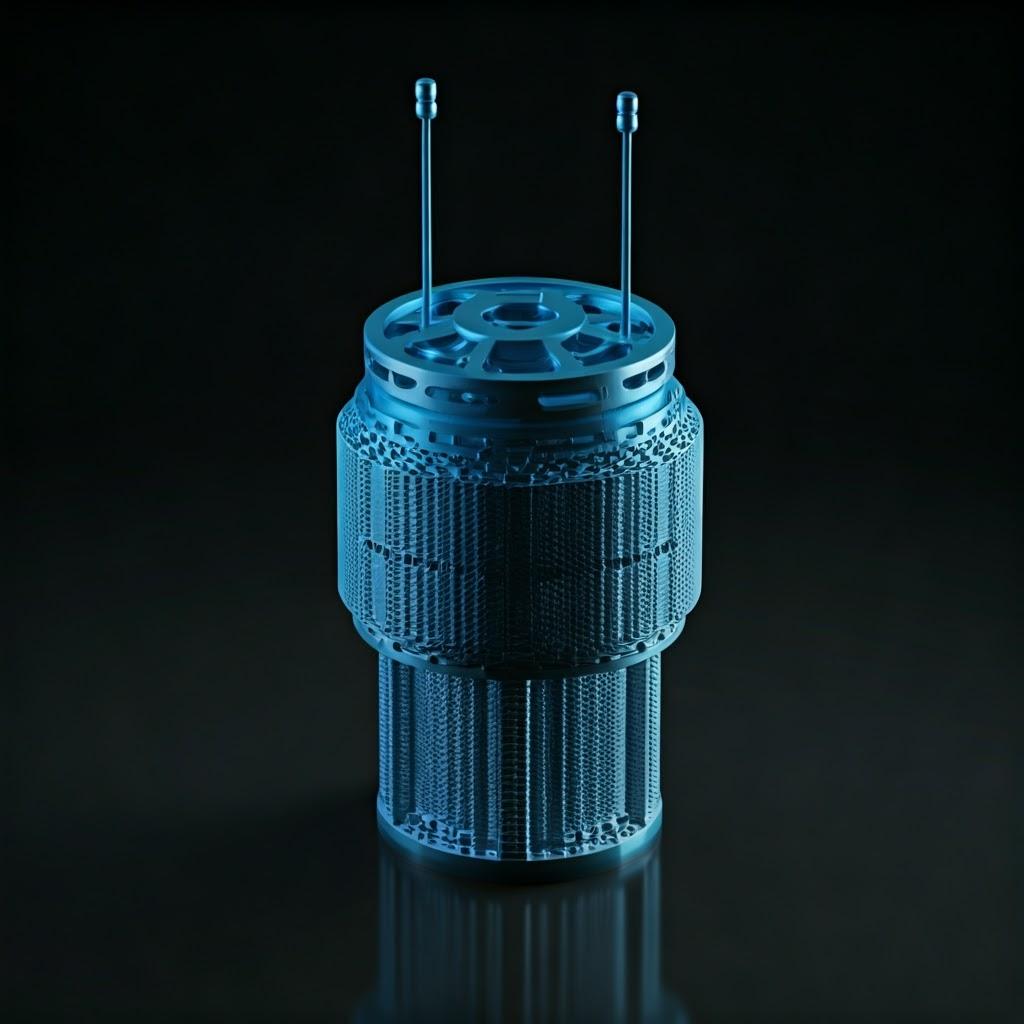
Design Considerations for Additively Manufactured Drone Antenna Supports
Leveraging the full potential of metal additive manufacturing, particularly Laser Powder Bed Fusion (LPBF), for drone antenna supports requires more than simply converting an existing design intended for CNC machining. To truly unlock the benefits of lightweighting, performance enhancement, and cost-efficiency, engineers must embrace Design for Additive Manufacturing (DfAM) principles. DfAM involves designing parts specifically with the capabilities and constraints of the chosen AM process in mind. For aluminum drone antenna supports printed via LPBF, several key design considerations are crucial for success. These considerations influence not only the final part’s performance and weight but also its manufacturability, cost, and reliability. Partnering with an experienced additive manufacturing service provider like Met3dp, who understands these nuances, can significantly streamline the design optimization process.
1. Topology Optimization: Designing for Function, Not Tradition:
- Concept: Topology optimization is a computational method that optimizes material layout within a defined design space for a given set of loads, boundary conditions, and constraints, aiming to maximize performance (e.g., minimize weight while maintaining stiffness). It often results in complex, organic-looking shapes that are highly efficient structurally.
- Workflow:
- Define Design Space: Specify the maximum allowable volume the antenna support can occupy.
- Apply Loads & Constraints: Define the forces the support will encounter (gravity, vibration, aerodynamic loads, antenna weight) and specify fixed points (mounting locations) and functional requirements (e.g., antenna position/orientation).
- Set Objectives: Typically, minimize mass/volume while constraining stress and deflection below allowable limits.
- Run Optimization: Software algorithms iteratively remove material from low-stress areas, converging on an optimized geometry.
- Interpret & Reconstruct: The raw output often requires interpretation and smoothing into a manufacturable CAD model, potentially incorporating additional DfAM considerations.
- Benefits for Antenna Supports: Enables dramatic weight reductions (30-60%+), ensuring the support adds minimal mass to the drone while fulfilling its structural role. Creates highly stiff structures ideal for maintaining precise antenna orientation under dynamic conditions.
- Tools: Software like Altair OptiStruct, Dassault Systèmes TOSCA, Ansys Mechanical.
2. Lattice and Generative Structures: Internal Lightweighting:
- Concept: Incorporating internal lattice structures (e.g., honeycomb, gyroid, stochastic foams) or complex internal ribbing within the solid sections of the support. These structures provide high stiffness and strength relative to their density.
- Implementation: Modern CAD and AM preparation software allow for easy integration of various lattice types. The type, cell size, and beam thickness can be tailored to meet specific stiffness, vibration damping, or energy absorption requirements.
- Advantages: Further reduces weight beyond topology optimization alone, allows for multi-functional design (e.g., vibration damping properties tuned by lattice type), and can improve manufacturability by reducing thermal mass in thick sections.
- Considerations: Requires careful analysis to ensure structural integrity, potential for trapped powder if cells are fully enclosed (requires design for powder removal), minimum beam/strut thickness limitations based on the AM process.
3. Minimum Feature Size and Wall Thickness:
- LPBF Constraints: The laser spot size, powder particle size, and melt pool dynamics impose limitations on the smallest features that can be reliably produced.
- Minimum Wall Thickness: Typically around 0.4 – 0.8 mm for aluminum alloys, depending on the wall height, geometry, and machine capabilities. Thinner walls risk incomplete melting or distortion.
- Minimum Hole Diameter: Small holes (typically < 0.5 – 1.0 mm) can be challenging to print accurately and may require post-drilling. Self-supporting angles influence the quality of overhanging holes.
- Minimum Feature/Pin Diameter: Small positive features also have limits, often similar to wall thickness constraints.
- Design Rule: Designers must adhere to minimum feature size guidelines provided by the AM service provider or based on machine specifications to ensure manufacturability and part integrity. Designing features slightly above the absolute minimum often improves robustness.
4. Build Orientation Strategy:
- Impact: The orientation of the part on the build plate significantly affects:
- Support Structures: Areas overhanging beyond a critical angle (typically ~45° for aluminum) require support structures, which consume extra material, increase build time, add post-processing effort (removal), and can mar the surface finish. Optimizing orientation minimizes the need for supports, especially on critical functional surfaces.
- Surface Finish: Up-facing and side-facing surfaces generally have better finish than down-facing surfaces supported by structures. Critical surfaces should ideally be oriented upwards or vertically.
- Dimensional Accuracy: Thermal stresses can cause slight variations; orientation affects the direction of greatest potential deviation.
- Mechanical Properties: While less pronounced in aluminum LPBF than some other materials/processes, slight anisotropy (direction-dependent properties) can exist. Critical load paths should ideally align with the direction of optimal properties (often XY plane).
- Build Time & Cost: Taller builds generally take longer. Fitting multiple parts efficiently on a build plate (nesting) depends on individual part orientation.
- Decision Process: Selecting the best orientation involves balancing these factors. Often, minimizing support structures on complex or critical surfaces is a primary driver for antenna supports. Collaboration with the AM provider during the design phase is beneficial.
5. Incorporating Integrated Features:
- Cable Management: Design channels, clips, or routing paths directly into the support structure to neatly manage antenna cables, preventing snags and vibration wear.
- Mounting Points: Integrate threaded inserts (via post-processing), specific interfaces for fasteners, or snap-fit features directly into the design.
- Vibration Damping: Explore complex geometries or integrated lattice structures specifically designed to dampen vibrations transmitted from the airframe to the antenna.
- Heat Sinks: If adjacent components generate heat, fins or other heat-dissipating features can potentially be integrated into the support design, leveraging aluminum’s thermal conductivity.
- Part Consolidation: Actively look for opportunities to combine adjacent brackets or mounting components into a single, multi-functional printed part.
6. Designing for Post-Processing:
- Support Removal Access: Ensure that areas requiring support structures are accessible for manual or tool-based removal after printing. Avoid deep, inaccessible internal cavities requiring support unless absolutely necessary and designed for powder removal.
- Machining Allowances: If certain surfaces require very tight tolerances, flatness, or specific finishes achievable only through machining, add extra “stock” material (e.g., 0.5 – 1.0 mm) to those features in the design to be removed during CNC finishing.
- Heat Treatment Considerations: Understand that heat treatment (especially T6 for A7075) can cause slight distortion. Design features robustly to accommodate minor potential warping, or plan for corrective machining post-heat treat.
- Inspection Access: Ensure critical features are accessible for measurement and inspection after manufacturing.
7. Stress Concentration Avoidance:
- Sharp Corners: Sharp internal corners act as stress raisers, potentially initiating cracks under load or fatigue. Use fillets and radii generously, especially at junctions between thin and thick sections or at load application points. AM allows for smooth, blended transitions more easily than traditional machining.
- Load Path Optimization: Ensure load paths flow smoothly through the structure without abrupt changes in cross-section. Topology optimization inherently helps with this.
By thoughtfully applying these DfAM principles, engineers can design aluminum drone antenna supports that are not just manufacturable via AM, but truly optimized for lightweight performance, functional integration, and reliability, maximizing the unique advantages offered by metal 3D printing technology.
Achievable Tolerance, Surface Finish, and Dimensional Accuracy in Aluminum 3D Printing
When specifying components for demanding applications like drones, understanding the achievable precision is critical. Engineers and procurement managers need realistic expectations regarding the dimensional tolerances, surface finish, and overall accuracy of parts produced via metal additive manufacturing, specifically Laser Powder Bed Fusion (LPBF) with aluminum alloys like AlSi10Mg and A7075. While AM offers incredible geometric freedom, it inherently has different precision characteristics compared to high-precision CNC machining. However, for many applications, the “as-built” accuracy is sufficient, and where tighter precision is needed, post-processing steps can be employed.
1. Dimensional Tolerances:
- General Expectations: The achievable dimensional accuracy in LPBF depends on several factors, including machine calibration, laser parameters, thermal stability during the build, powder quality, part size, geometry, and orientation.
- Typical Values: For well-controlled processes using high-quality equipment and materials (like powders from Met3dp), typical achievable tolerances for aluminum LPBF parts often fall within:
- Smaller parts (e.g., < 100 mm): ±0.1 mm to ±0.2 mm is often achievable for many features.
- Larger parts (e.g., > 100 mm): ±0.1% to ±0.2% of the nominal dimension is a common rule of thumb.
- ISO 2768 Comparison: While not directly equivalent, the achievable tolerances are often comparable to general tolerance grades like ISO 2768-m (medium) or sometimes -f (fine) for as-built parts. However, AM-specific tolerance standards (e.g., ISO/ASTM 52900 series) are evolving.
- Key Influencing Factors:
- Thermal Stress: The rapid heating and cooling can cause internal stresses leading to minor warping or distortion, especially in large or complex parts. Optimized scan strategies and support structures help mitigate this.
- Machine Calibration: Regular calibration of the laser system, scanners, and powder recoating mechanism is crucial for accuracy.
- Powder Quality: Consistent particle size distribution and morphology contribute to stable melting and solidification, improving accuracy.
- Orientation: As mentioned previously, orientation affects thermal behavior and potential deviation.
- Shrinkage Compensation: Software typically applies scaling factors to compensate for material shrinkage during cooling, but perfect prediction is challenging.
- Achieving Tighter Tolerances: For critical interfaces, mounting holes, or surfaces requiring precision beyond the standard as-built capabilities (e.g., tighter than ±0.1 mm), post-process CNC machining is the standard solution. Features requiring machining must be designed with appropriate stock material.
2. Surface Finish (Roughness):
- As-Built Condition: The surface finish of LPBF parts is inherently rougher than machined surfaces due to the layer-by-layer process and partially melted powder particles adhering to the surface. Surface roughness (typically measured as Ra – arithmetic average roughness) varies depending on the surface orientation relative to the build direction:
- Up-facing Surfaces: Generally smoother, often Ra 6 µm – 15 µm.
- Vertical/Side Walls: Moderate roughness, often Ra 8 µm – 18 µm, may show slight “stair-stepping” depending on layer thickness.
- Down-facing/Supported Surfaces: Roughest due to contact with support structures, often Ra 15 µm – 25 µm or higher. Removing supports also affects the finish.
- Improving Surface Finish: Several post-processing techniques can significantly improve the surface finish:
- Abrasive Blasting (Bead/Sand): Common method to achieve a uniform matte finish, typically reducing Ra to around 3 µm – 10 µm. Removes loose powder and reduces stress concentrations.
- Tumbling/Vibratory Finishing: Uses media to smooth surfaces and edges, effective for batches of smaller parts. Can achieve Ra values in the range of 1 µm – 5 µm.
- Machining: Provides the best surface finish, easily achieving Ra < 1.6 µm or even < 0.8 µm on specific features.
- Polishing: Manual or automated polishing can achieve very smooth, mirror-like finishes (Ra < 0.4 µm) for specific requirements, often at significant cost.
- Specification: It’s crucial to clearly specify required surface finishes on drawings, indicating which surfaces need improvement beyond the as-built state and the target Ra value or finish type (e.g., “Bead blast finish,” “Machine to Ra 1.6 µm”).
3. Dimensional Accuracy:
- Definition: Refers to the overall conformity of the printed part to the nominal dimensions specified in the CAD model, encompassing both tolerance deviations and potential warping or distortion.
- Factors: Influenced by all the elements affecting tolerance and surface finish, plus the effectiveness of thermal management during the build and stress relief post-processing.
- Verification: Dimensional accuracy is typically verified using metrology tools like calipers, micrometers, Coordinate Measuring Machines (CMMs), or 3D scanners. The level of inspection should be appropriate for the criticality of the part.
- Ensuring Accuracy: Requires a combination of:
- Robust DfAM practices (minimizing stress, optimizing orientation).
- High-quality, well-maintained AM equipment.
- Consistent, high-quality metal powder (emphasizing the importance of suppliers like Met3dp focused on AM-grade powders).
- Optimized process parameters tailored to the specific alloy (AlSi10Mg vs. A7075).
- Appropriate post-processing (stress relief, controlled support removal).
- Thorough quality control and inspection.
Summary Table: Typical Aluminum LPBF Precision
Parameter | As-Built Condition | After Standard Post-Processing (e.g., Blasting) | After Machining | Notes |
---|---|---|---|---|
Tolerance (Typical) | ±0.1 to ±0.2 mm (<100mm) | Unchanged | < ±0.05 mm achievable | Dependent on size, geometry, machine; Tighter requires machining. |
Tolerance (Typical) | ±0.1% to ±0.2% (>100mm) | Unchanged | < ±0.05 mm achievable | Dependent on size, geometry, machine; Tighter requires machining. |
Surface Roughness (Ra) | 6 µm – 25 µm (Varies by orientation) | 3 µm – 10 µm (Uniform matte finish) | < 1.6 µm achievable | Polishing can achieve < 0.4 µm. Supported surfaces are roughest. |
Smallest Hole | ~0.5 – 1.0 mm | Unchanged | Limited by tool size | Below threshold may require drilling. |
Min. Wall Thickness | ~0.4 – 0.8 mm | Unchanged | Limited by stability | Depends on height, geometry. |
Export to Sheets
Conclusion on Precision:
Metal 3D printing of aluminum alloys offers good dimensional accuracy and acceptable surface finish for many drone antenna support applications directly “as-built.” Understanding the typical achievable ranges and the factors influencing precision is key for designers. For applications demanding tighter tolerances or smoother finishes on specific features, integrating standard post-processing steps like CNC machining or abrasive blasting into the manufacturing workflow allows AM parts to meet even stringent requirements. Clear communication of tolerance and finish requirements on technical drawings is essential when working with any manufacturing provider.
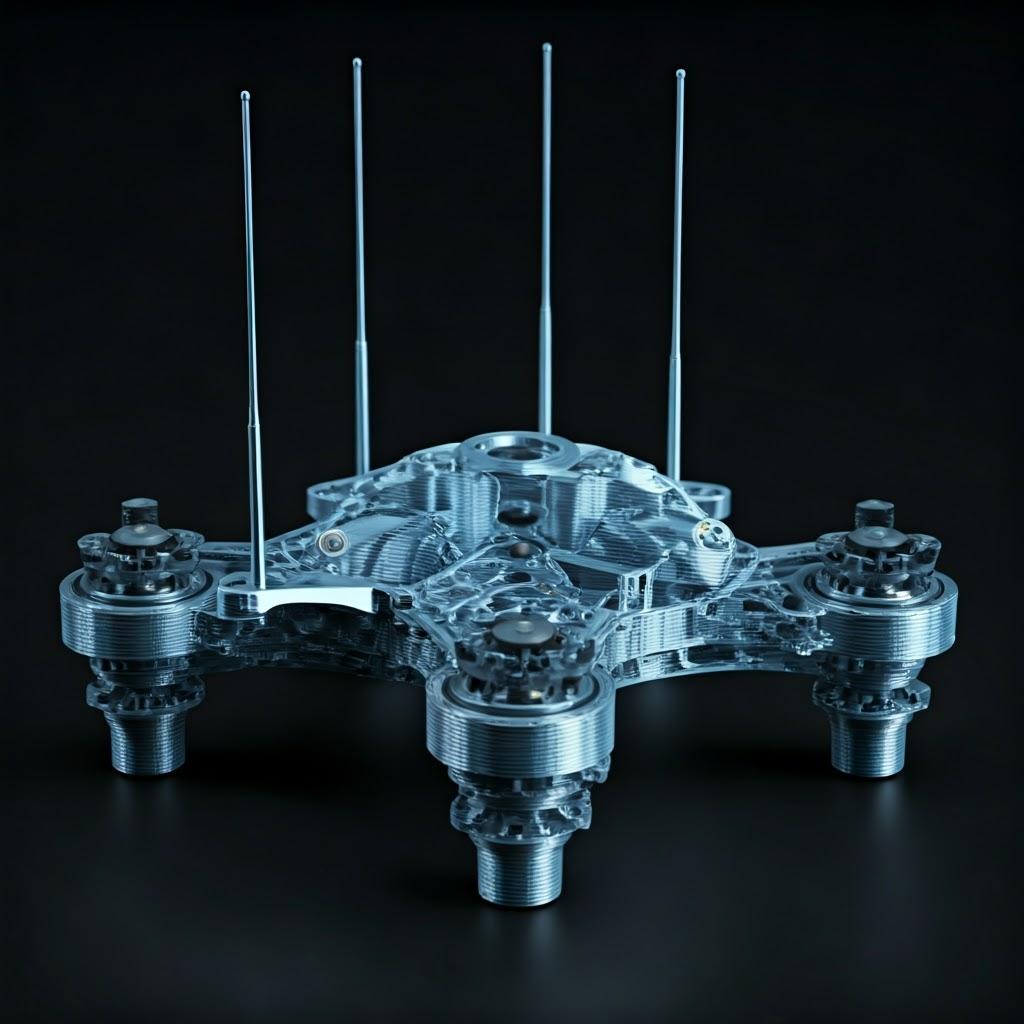
Essential Post-Processing Requirements for 3D Printed Antenna Supports
Producing a drone antenna support via Laser Powder Bed Fusion (LPBF) is rarely the end of the manufacturing journey. The “as-built” part, fresh off the printer, typically requires several crucial post-processing steps to achieve the desired material properties, dimensional accuracy, surface finish, and overall functionality. These steps are not optional extras but integral parts of the additive manufacturing workflow, especially when dealing with high-performance aluminum alloys like AlSi10Mg and A7075. Understanding these requirements is vital for engineers designing the parts and for procurement managers sourcing AM services, as they impact lead time, cost, and final part performance. A capable metal AM provider like Met3dp will either have these capabilities in-house or manage them through a network of trusted partners, offering a complete manufacturing solution.
1. Stress Relief:
- Why it’s Needed: The rapid, localized heating and cooling inherent in LPBF creates significant residual stresses within the printed part. These stresses can lead to distortion (warping) during or after removal from the build plate, reduced mechanical performance (especially fatigue life), and potential cracking.
- Process: Involves heating the part (while still attached to the build plate, if possible) in a furnace to a specific temperature below the alloy’s aging or solution treatment temperature, holding it for a period, and then cooling slowly. This allows the microstructure to relax, significantly reducing internal stresses.
- Typical Cycles:
- AlSi10Mg: Often stress-relieved at around 250-300°C for 1-2 hours.
- A7075: Stress relief might be performed around 200-250°C, but it must be carefully managed to avoid interfering with subsequent T6 heat treatment. Sometimes stress relief is combined with the solution treatment step.
- Importance: Considered a mandatory step for most functional metal AM parts, especially those with complex geometries or requiring dimensional stability.
2. Part Removal from Build Plate:
- Method: Parts are typically printed on a thick metal build plate. They need to be separated after printing (and usually after stress relief). Common methods include:
- Wire EDM (Electrical Discharge Machining): Precise method, good for complex or delicate parts, leaves a relatively smooth surface.
- Band Sawing: Faster and potentially cheaper for simpler geometries, but less precise and can induce mechanical stress if not done carefully.
- Machining: Milling or turning can also be used to separate parts.
- Consideration: The chosen method depends on part geometry, required precision at the base, and cost factors.
3. Support Structure Removal:
- Why Supports Exist: LPBF requires support structures for overhanging features (typically >45°) and to anchor the part to the build plate, preventing warping and conducting heat away. These are sacrificial structures made from the same material.
- Removal Methods:
- Manual Removal: Supports are often designed with specific weak points or perforation to allow them to be broken off manually using pliers, chisels, or other hand tools. Requires careful design and execution to avoid damaging the part.
- Machining: CNC machining (milling, grinding) can be used to remove supports precisely, especially from critical surfaces.
- Wire EDM: Can be used for supports in intricate or hard-to-reach areas.
- Challenges: Support removal can be labor-intensive and time-consuming, adding significant cost. Poorly designed supports can be difficult to remove or leave undesirable marks (“witness marks”) on the part surface. DfAM principles focus on minimizing the need for supports and designing them for easy removal.
4. Heat Treatment (Crucial for Properties):
- Purpose: To optimize the mechanical properties (strength, hardness, ductility, fatigue life) of the printed alloy by modifying its microstructure. The required treatment depends heavily on the alloy.
- AlSi10Mg:
- As-Built/Stress Relieved: Possesses moderate strength due to the fine microstructure from rapid solidification.
- T5/T6-like Treatments: Can undergo precipitation hardening treatments (e.g., aging at 160-200°C) to further increase strength and hardness, although the response may differ from cast AlSi10Mg T6 due to the unique AM microstructure. The specific cycle depends on desired properties.
- A7075:
- Mandatory T6 Treatment for High Strength: To achieve the desirable high-strength properties comparable to wrought A7075-T6, a full T6 heat treatment is essential. This involves:
- Solution Treatment: Heating to a high temperature (e.g., ~470-490°C) to dissolve alloying elements into a solid solution.
- Quenching: Rapidly cooling (typically in water or polymer) to trap the elements in solution. This step is critical and can induce distortion if not controlled.
- Artificial Aging: Reheating to a lower temperature (e.g., ~120-140°C) for an extended period (e.g., 24 hours) to precipitate fine hardening phases (MgZn2).
- Impact: The T6 cycle dramatically increases yield and ultimate tensile strength but typically reduces ductility compared to the as-built or annealed state. Careful process control is needed to achieve consistent results and minimize distortion.
- Mandatory T6 Treatment for High Strength: To achieve the desirable high-strength properties comparable to wrought A7075-T6, a full T6 heat treatment is essential. This involves:
- Equipment: Requires calibrated furnaces with precise temperature control and appropriate quenching capabilities.
5. Surface Finishing:
- Purpose: To improve surface smoothness, remove loose powder, achieve a desired aesthetic appearance, enhance fatigue life (by removing surface imperfections), or prepare the surface for coating.
- Common Methods (as discussed previously):
- Abrasive Blasting (Bead, Sand, Grit): Most common for a uniform matte finish.
- Tumbling/Vibratory Finishing: Good for deburring and smoothing batches of parts.
- Polishing: For very smooth or mirror finishes.
- Choice: Depends on the functional requirements (e.g., fatigue performance might benefit from blasting) and aesthetic needs.
6. Machining for Critical Dimensions:
- Purpose: To achieve tolerances, flatness, parallelism, or surface finishes on specific features that are tighter than what the as-built AM process can provide.
- Applications: Creating precise mating surfaces, bearing bores, threaded holes, O-ring grooves, or ensuring tight positional tolerances between features.
- Process: Standard CNC milling, turning, drilling, tapping, or grinding operations. Requires careful fixture design to hold the potentially complex AM part geometry.
7. Inspection and Quality Control (QC):
- Purpose: To verify that the finished part meets all specified requirements (dimensional, material, functional).
- Methods:
- Dimensional Inspection: Calipers, micrometers, CMM, 3D scanning.
- Material Verification: Chemical analysis (if required), hardness testing (post-heat treat).
- Non-Destructive Testing (NDT): X-ray or CT scanning can be used to detect internal defects like porosity or cracks, especially for critical aerospace components (though potentially expensive). Dye penetrant or magnetic particle inspection for surface crack detection.
- Importance: Essential for ensuring the reliability and safety of drone components. The level of inspection depends on the criticality.
8. Surface Coatings (Optional but Common):
- Purpose: To enhance corrosion resistance, improve wear resistance, provide electrical insulation/conductivity, or change the aesthetic appearance.
- Common Coatings for Aluminum:
- Anodizing (Type II & Type III Hardcoat): Excellent corrosion protection, improves wear resistance (especially Type III), can be dyed various colors. Common for aerospace aluminum parts.
- Chromate Conversion Coating (Alodine, Irridite): Provides good corrosion resistance and acts as an excellent primer for paint.
- Painting/Powder Coating: For specific colors or enhanced environmental protection.
- Consideration: The chosen coating process must be compatible with the aluminum alloy and the part’s geometry.
Conclusion on Post-Processing:
Post-processing is an indispensable part of producing functional, reliable 3D printed aluminum drone antenna supports. These steps transform the raw printed part into a finished component meeting stringent engineering requirements. When evaluating metal AM service providers, it is crucial to assess their capabilities and expertise in performing or managing these essential post-processing operations, particularly heat treatment (especially T6 for A7075), precision machining, and surface finishing, alongside robust quality control measures. Neglecting these steps can compromise the performance and integrity of the final drone component. Access to diverse material capabilities and powders is just the first step; comprehensive post-processing expertise completes the manufacturing solution.
Common Challenges in 3D Printing Aluminum Antenna Supports and Mitigation Strategies
While metal 3D printing offers significant advantages for producing lightweight and complex drone antenna supports, the process, particularly LPBF with reactive aluminum alloys, is not without its challenges. Understanding these potential hurdles and the strategies employed by experienced manufacturers like Met3dp to mitigate them is crucial for ensuring successful outcomes, consistent quality, and reliable parts. Engineers and procurement managers should be aware of these factors when designing parts and selecting suppliers.
1. Residual Stress and Warping:
- Challenge: The intense, localized heat input from the laser followed by rapid cooling creates steep thermal gradients within the part during the build. This leads to the buildup of internal residual stresses. If these stresses exceed the material’s yield strength at elevated temperatures, they can cause the part to warp or distort, either during the print process (pulling away from supports) or after removal from the build plate. Large flat sections or asymmetric designs are particularly susceptible.
- Mitigation Strategies:
- Optimized Process Parameters: Carefully controlling laser power, scan speed, layer thickness, and scan strategy (e.g., island scanning, alternating hatch directions) helps manage heat input and reduce thermal gradients.
- Effective Support Structures: Robust supports anchor the part firmly to the build plate, resist warping forces, and help conduct heat away more uniformly. Support design is critical.
- Platform Heating: Preheating the build platform reduces the temperature difference between the solidified material and the new layer, lowering residual stress accumulation.
- Thermal Stress Relief: Performing a stress relief heat treatment cycle immediately after printing and before removing the part from the build plate is highly effective in relaxing internal stresses.
- DfAM: Designing parts with more uniform wall thicknesses, avoiding large flat unsupported areas, and adding ribs or fillets can inherently reduce stress buildup.
2. Support Structure Removal Difficulty and Surface Impact:
- Challenge: While necessary, support structures must be removed. Depending on the design and location (e.g., internal channels, complex overhangs), removal can be difficult, time-consuming, and labor-intensive. Improper removal can damage the part surface, leave undesirable witness marks, or even cause localized cracking. Supports bonded too strongly require excessive force or aggressive machining.
- Mitigation Strategies:
- Optimized Support Design: Using specialized support structure types (e.g., tree supports, block supports with optimized interfaces), adjusting contact points, density, and perforation patterns to balance strength during the build with ease of removal. Software tools assist in generating optimized supports.
- Orientation Strategy: Orienting the part to minimize the number of supports needed, especially on critical or cosmetic surfaces.
- DfAM for Access: Designing the part with clear access paths for tools to reach and remove supports. Avoiding designs where supports are trapped internally unless absolutely necessary and accounting for powder removal.
- Appropriate Removal Techniques: Using the right tools and methods (manual breaking, careful grinding, wire EDM, specialized tooling) based on the support type and location.
- Surface Finishing: Post-removal surface finishing (blasting, tumbling, machining) helps remove witness marks and achieve the desired final surface quality.
3. Porosity:
- Challenge: Porosity refers to small voids or gas bubbles trapped within the solidified metal. Excessive porosity can significantly degrade mechanical properties, particularly fatigue life, impact strength, and fracture toughness, acting as crack initiation sites. Sources include gas trapped within the powder particles, gas dissolved in the melt pool (from imperfect shielding atmosphere), or keyholing (vapor depression collapse) due to incorrect process parameters.
- Mitigation Strategies:
- High-Quality Powder: Using powder with high sphericity, controlled particle size distribution, low internal porosity, and low gas content (especially hydrogen for aluminum) is paramount. This highlights the importance of powder manufacturers like Met3dp employing advanced atomization (VIGA, PREP) and handling techniques.
- Optimized Process Parameters: Fine-tuning laser power, scan speed, focus, and layer thickness to ensure stable melt pool dynamics and complete melting without excessive vaporization or keyholing.
- Inert Atmosphere Control: Maintaining a high-purity inert gas atmosphere (typically Argon) in the build chamber (<100-1000 ppm Oxygen) prevents oxidation and minimizes gas pickup by the melt pool.
- Hot Isostatic Pressing (HIP): For critical applications requiring maximum density and fatigue performance, HIP can be used as a post-processing step. It involves applying high temperature and high isostatic pressure to the part, effectively closing internal pores. (Adds significant cost).
- Quality Control: Implementing robust process monitoring and potentially NDT (CT scanning) for critical parts to detect and quantify porosity.
4. Achieving Fine Features and Thin Walls:
- Challenge: The LPBF process has inherent limitations on the minimum size of features (walls, pins, holes) that can be reliably produced due to laser spot size, melt pool dimensions, and powder particle size. Printing features below these limits can result in incomplete formation, poor resolution, or distortion.
- Mitigation Strategies:
- Adhering to Design Rules: Designers must respect the minimum feature size guidelines specific to the machine, material, and parameters being used (e.g., typical minimum wall ~0.4-0.8 mm).
- Machine Capability: Using high-resolution machines with smaller laser spot sizes can enable finer features, but potentially at the cost of build speed.
- Optimized Parameters: Specific parameter sets might be developed for fine feature resolution.
- Post-Machining: If extremely fine features or sharp edges are required beyond AM capability, designing the part slightly oversized and using micro-machining techniques post-print might be necessary.
5. Powder Handling and Safety:
- Challenge: Fine aluminum powders are reactive and pose potential fire and explosion hazards if not handled correctly, especially when exposed to air (forming oxides) or ignition sources (sparks). They also pose inhalation risks.
- Mitigation Strategies:
- Inert Atmosphere: Handling powder primarily under an inert gas (Argon) environment within the machine and dedicated powder handling stations.
- Grounding and Bonding: Ensuring all equipment is properly grounded to prevent static discharge.
- Personal Protective Equipment (PPE): Use of respirators, conductive clothing, gloves, and eye protection.
- Explosion-Proof Equipment: Using certified vacuum cleaners and avoiding ignition sources in powder handling areas.
- Proper Training: Ensuring personnel are thoroughly trained on safe powder handling procedures.
- Powder Management Systems: Utilizing automated or semi-automated systems for powder loading, sieving, and recycling to minimize operator exposure and ensure safety. Companies like Met3dp invest in safe and efficient powder handling infrastructure.
By acknowledging these challenges and actively implementing robust mitigation strategies grounded in DfAM, process optimization, quality materials, meticulous post-processing, and rigorous safety protocols, experienced additive manufacturing providers can consistently produce high-quality, reliable aluminum drone antenna supports that meet the demanding requirements of the UAV industry.
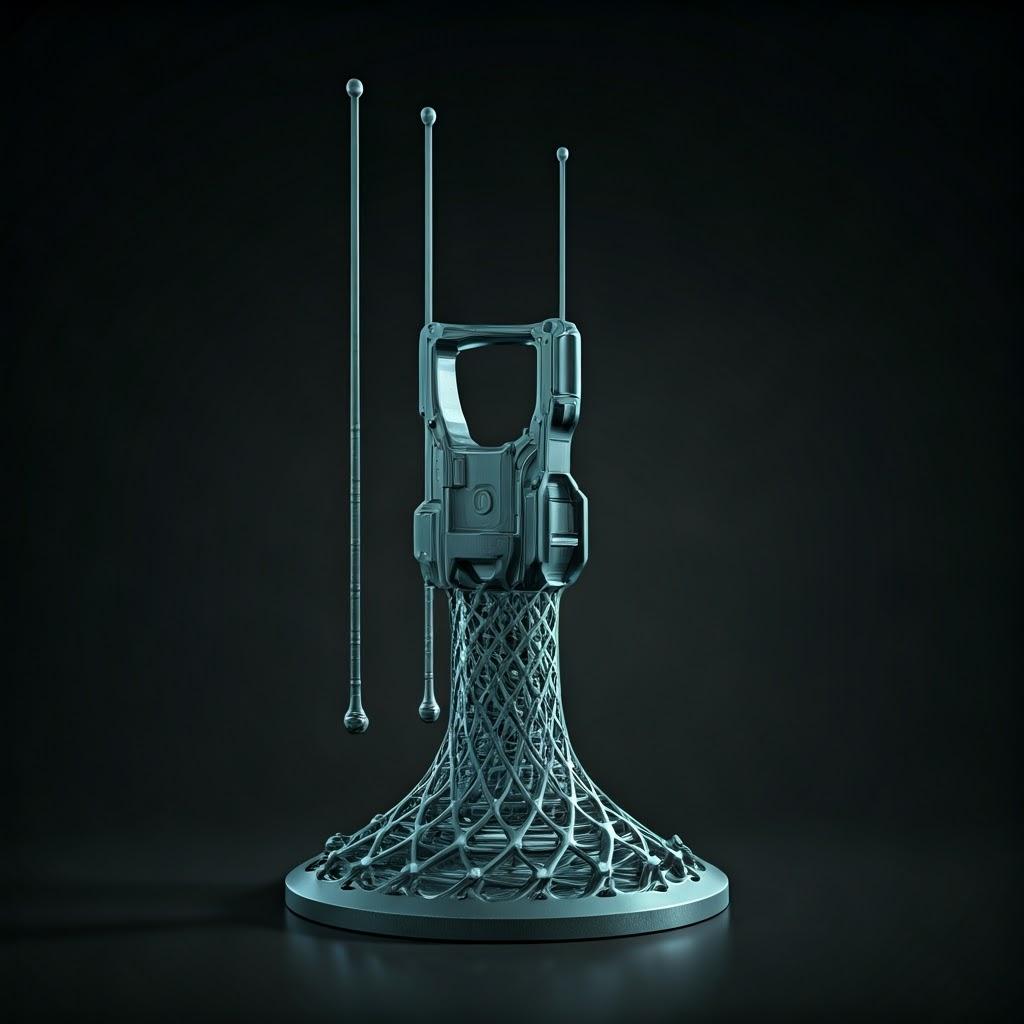
How to Choose the Right Metal 3D Printing Service Provider for Drone Components
Selecting the right manufacturing partner is as critical as perfecting the design or choosing the optimal material for your 3D printed drone antenna supports. The quality, reliability, cost-effectiveness, and timely delivery of your components hinge on the capabilities and expertise of your chosen metal additive manufacturing (AM) service provider. Given the demanding nature of drone applications, particularly in commercial, industrial, and aerospace sectors, the selection process requires careful evaluation beyond just comparing price quotes. Procurement managers and engineers need to assess potential suppliers across a range of technical and operational criteria to ensure they can consistently deliver high-quality aluminum (AlSi10Mg or A7075) parts that meet stringent performance requirements. Partnering with a knowledgeable and well-equipped provider, like Met3dp, significantly mitigates risks and enhances the likelihood of success.
Here are key factors to consider when evaluating potential metal 3D printing service providers for drone antenna supports:
1. Technical Expertise and Engineering Support:
- Materials Science Knowledge: Does the provider demonstrate deep understanding of the specific aluminum alloys (AlSi10Mg, A7075)? Do they understand the nuances of processing these materials via LPBF, including parameter optimization for density, microstructure, and mechanical properties? Can they advise on material selection based on your application requirements?
- DfAM Capability: Does the provider offer Design for Additive Manufacturing support? Can their engineers review your design, suggest optimizations for lightweighting (topology optimization, lattice structures), improve manufacturability (reducing supports, ensuring feature resolution), and ensure the design is suitable for post-processing? Proactive DfAM collaboration is invaluable.
- Process Optimization Experience: Do they have proven experience in developing and refining process parameters for aluminum alloys to achieve specific outcomes (e.g., high density, specific surface finish, consistent mechanical properties)? Are they familiar with the challenges of printing A7075 and possess strategies to mitigate issues like hot tearing?
- Application Experience: Have they previously manufactured parts for the drone/UAV industry or related aerospace/automotive sectors? Understanding the specific demands and quality expectations of these industries is a significant advantage.
2. Equipment, Technology, and Facility:
- Machine Park: What specific LPBF machines do they operate? Are they reputable brands known for quality and consistency? Do they have sufficient machine capacity to handle your potential volume and meet lead time requirements? What is the build volume of their machines? (Met3dp prides itself on industry-leading print volume, accuracy, and reliability).
- Machine Maintenance and Calibration: Is there evidence of rigorous machine maintenance schedules and regular calibration routines? Consistent machine performance is crucial for repeatable part quality and dimensional accuracy.
- Powder Handling and Management: How do they handle, store, sieve, and recycle aluminum powders? Do they have systems to prevent cross-contamination between alloys? Are they using high-quality, traceable powders specifically designed for AM? (Met3dp’s focus on producing high-quality spherical powders using advanced atomization is a key strength here). Do they monitor powder quality and characteristics over time?
- Facility Environment: Is the production environment clean, organized, and climate-controlled? Proper environmental control is important for sensitive AM processes.
3. In-House Post-Processing Capabilities:
- Comprehensive Services: Does the provider offer the necessary post-processing steps in-house, or do they rely on external partners? Key capabilities for aluminum antenna supports include:
- Stress Relief Furnaces
- Support Removal (Manual, EDM, Machining)
- Heat Treatment Furnaces (Calibrated for specific cycles like T6 for A7075)
- Surface Finishing (Blasting, Tumbling)
- CNC Machining (Multi-axis capabilities for finishing critical features)
- Inspection and Metrology Lab (CMM, Scanners, Hardness Testing)
- Partner Management: If relying on partners, how strong and well-managed is their supply chain for these services? Do they take full responsibility for the quality and lead time of outsourced operations? In-house capabilities often provide better control over the entire workflow.
4. Quality Management Systems (QMS) and Certifications:
- ISO 9001: This is a fundamental requirement, indicating a documented and audited QMS for consistent quality.
- AS9100 (Aerospace): If your drone components are for aerospace or defense applications, AS9100 certification is often mandatory. It signifies adherence to the rigorous quality standards of the aerospace industry. Choosing an AS9100 certified supplier provides higher assurance of process control, traceability, and documentation.
- Material Certifications: Can they provide material test certificates verifying the chemical composition and properties of the powder batches used?
- Traceability: Do they have systems in place to ensure full traceability from raw powder batch to the finished part, including process parameters and post-processing records?
5. Project Management and Communication:
- Responsiveness: How quickly and thoroughly do they respond to inquiries and requests for quotes?
- Technical Communication: Is it easy to communicate technical requirements and resolve design or manufacturing queries with their engineering team?
- Project Tracking: Do they provide clear timelines, regular updates on project status, and proactive communication regarding any potential delays or issues?
- Transparency: Are they open about their processes, capabilities, and limitations?
6. Capacity and Scalability:
- Prototype vs. Production: Are they primarily focused on prototyping, or do they have the capacity and systems in place to handle series production runs if your project scales up?
- Lead Time Reliability: Can they consistently meet quoted lead times for both prototypes and production volumes?
7. Case Studies, References, and Reputation:
- Proven Track Record: Can they provide examples or case studies of similar projects they have successfully completed, particularly involving aluminum alloys or drone/aerospace components?
- Customer References: Are they willing to provide references from satisfied customers?
- Industry Reputation: What is their reputation within the AM industry?
8. Cost and Value:
- Transparent Pricing: Is their pricing structure clear and detailed, breaking down costs where possible?
- Value Proposition: While cost is important, evaluate the overall value offered, considering technical expertise, quality assurance, reliability, lead time, and support, not just the price per part. The cheapest option may not offer the best value or lowest risk for critical components.
Evaluation Checklist Summary:
Criterion | Key Considerations | Importance (Drone Supports) |
---|---|---|
Technical Expertise | Al alloy knowledge, DfAM support, Process optimization, Application experience | Very High |
Equipment & Technology | Machine quality/capacity, Maintenance, Powder handling, Facility | Very High |
Post-Processing | In-house capabilities (Heat Treat, Machining, Finishing), Partner network | Very High |
Quality Systems & Certs | ISO 9001, AS9100 (if needed), Traceability, Material certs | Very High |
Project Mgmt & Comm. | Responsiveness, Technical clarity, Updates, Transparency | High |
Capacity & Scalability | Prototype and Production capability, Lead time reliability | Moderate to High |
Reputation & References | Case studies, Customer feedback, Industry standing | Moderate to High |
Cost & Value | Transparent pricing, Overall value (Quality, Reliability vs. Price) | High |
Export to Sheets
By systematically evaluating potential suppliers against these criteria, companies can identify a metal 3D printing partner that possesses the necessary technical prowess, robust quality systems, and reliable operational performance – like Met3dp – to successfully manufacture high-performance aluminum antenna supports for their drone platforms.
Cost Factors and Lead Time for 3D Printed Drone Antenna Supports
Understanding the factors that influence the cost and lead time of manufacturing drone antenna supports via metal additive manufacturing is essential for effective project planning, budgeting, and supply chain management. Unlike traditional high-volume manufacturing where tooling costs dominate, AM costs are more directly tied to material consumption, machine time, and labor involved in each part’s production. Here’s a breakdown of the key elements driving cost and lead time:
Key Cost Drivers:
- Material Cost:
- Powder Type: The specific aluminum alloy chosen significantly impacts cost. High-strength alloys like A7075, especially grades optimized for AM, are typically more expensive than standard AlSi10Mg powder.
- Part Volume & Support Volume: The total amount of powder consumed is directly related to the volume of the part itself plus the volume of the required support structures. Larger, bulkier parts or designs requiring extensive supports will naturally cost more. Topology optimization and DfAM are key to minimizing material usage.
- Powder Recycling Efficiency: The service provider’s ability to efficiently recycle unused powder affects the overall material cost attributed to each build. High recycling rates lower effective material costs. Met3dp’s investment in advanced powder production and management contributes to efficient material use.
- Powder Purchase Volume: Suppliers ordering powder in larger quantities may achieve better pricing.
- Machine Time:
- Build Preparation: Time required for slicing the CAD model, generating support structures, setting up the build layout (nesting parts), and preparing the machine.
- Printing Time: This is often the most significant time (and cost) factor. It’s primarily determined by the height of the build (number of layers) rather than just the volume. Taller parts take longer. Factors influencing print speed include layer thickness, laser power, scan speed, and hatching patterns. Efficiently nesting multiple parts within a single build is crucial for reducing per-part machine time costs.
- Machine Depreciation & Operating Rate: The cost of acquiring and maintaining expensive industrial metal AM systems is factored into an hourly operating rate. Higher-end, more capable machines typically have higher rates.
- Labor Costs:
- Engineering/DfAM Support: Time spent by engineers reviewing designs, providing DfAM feedback, or optimizing build layouts.
- Machine Operation: Skilled labor required for setting up, monitoring, and unloading the AM machines.
- Post-Processing Labor: This can be substantial. Includes manual support removal, part cleaning, furnace loading/unloading for heat treatment, CNC machine setup and operation, manual finishing/polishing, and inspection tasks. Complex parts requiring extensive post-processing will incur higher labor costs.
- Post-Processing Costs:
- Specific Steps Required: Each post-processing step (stress relief, support removal method, heat treatment cycle, type of surface finish, extent of machining, coating type) adds cost based on the equipment, consumables, and labor involved.
- Complexity: Complex heat treatments (like T6 for A7075) are more costly than simple stress relief. Extensive multi-axis CNC machining is more expensive than simple blasting.
- Quality Assurance & Inspection Costs:
- Level of Inspection: Basic dimensional checks are standard. More rigorous inspection involving CMM, 3D scanning, NDT (X-ray/CT), material testing, or detailed documentation packages increases costs. The required level depends on the criticality of the drone component. AS9100 compliance involves higher inherent QA costs.
- Order Volume:
- Economies of Scale: While AM doesn’t have the steep tooling amortization of injection molding, some economies of scale exist. Larger batch sizes allow for more efficient build nesting, potentially dedicated parameter optimization, and streamlined post-processing workflows, which can reduce the per-part price compared to single prototypes. Wholesale 3D printing quotes for larger quantities will typically reflect this.
- Design Complexity:
- Support Structure Needs: Designs requiring extensive, complex, or difficult-to-remove supports increase material use, print time, and post-processing labor/risk, thus increasing cost.
- Build Success Rate: Very complex or delicate designs may have a lower first-time build success rate, potentially requiring reprints, which can factor into overall costs or risk assessment.
Typical Lead Time Breakdown:
Lead time refers to the total time from order placement to parts shipment. It can vary significantly based on provider workload, part complexity, required post-processing, and order quantity.
- Quoting & Order Confirmation: (1-3 days) Initial review of requirements, quote generation, and order processing.
- Build Preparation & Scheduling: (1-5 days) Detailed review, DfAM checks (if needed), build layout optimization, and scheduling the job onto a machine based on availability. Can be longer if significant design feedback is required.
- Printing: (1-7+ days) Actual time the part spends printing in the machine. Highly dependent on part height and the number of parts nested in the build. A tall antenna support might take several days.
- Cooling & Depowdering: (0.5-1 day) Allowing the build chamber and parts to cool safely before removing loose powder.
- Post-Processing: (2-10+ days) This often contributes significantly to the overall lead time.
- Stress Relief: ~1 day (including furnace time and cooling)
- Part Removal/Support Removal: 0.5-2 days (depending on complexity)
- Heat Treatment (e.g., T6): 1-3 days (including furnace cycles, quenching, aging)
- Machining: 1-5+ days (depending on complexity and machine shop scheduling)
- Surface Finishing/Coating: 1-3 days
- Quality Inspection: (0.5-2 days) Depending on the level required.
- Packing & Shipping: (1 day)
Total Estimated Lead Time: For a moderately complex aluminum drone antenna support requiring heat treatment and some finishing, typical lead times might range from 2 to 4 weeks for prototypes or small batches. This can be shorter for simpler parts/processes or longer for very complex parts, large orders, or providers with heavy backlogs. Expedited options are often available at a premium cost.
Factors Influencing Lead Time:
- Provider’s current workload and machine availability.
- Complexity of the part and required support structures.
- Number and complexity of required post-processing steps (especially heat treatment and extensive machining).
- Order quantity.
- Efficiency of the provider’s workflow and supply chain management (for outsourced processes).
- Clarity and completeness of the initial technical documentation provided.
By understanding these cost drivers and lead time components, customers can better estimate budgets, plan project timelines, and have more informed discussions with potential AM service providers to optimize their drone component manufacturing strategy.
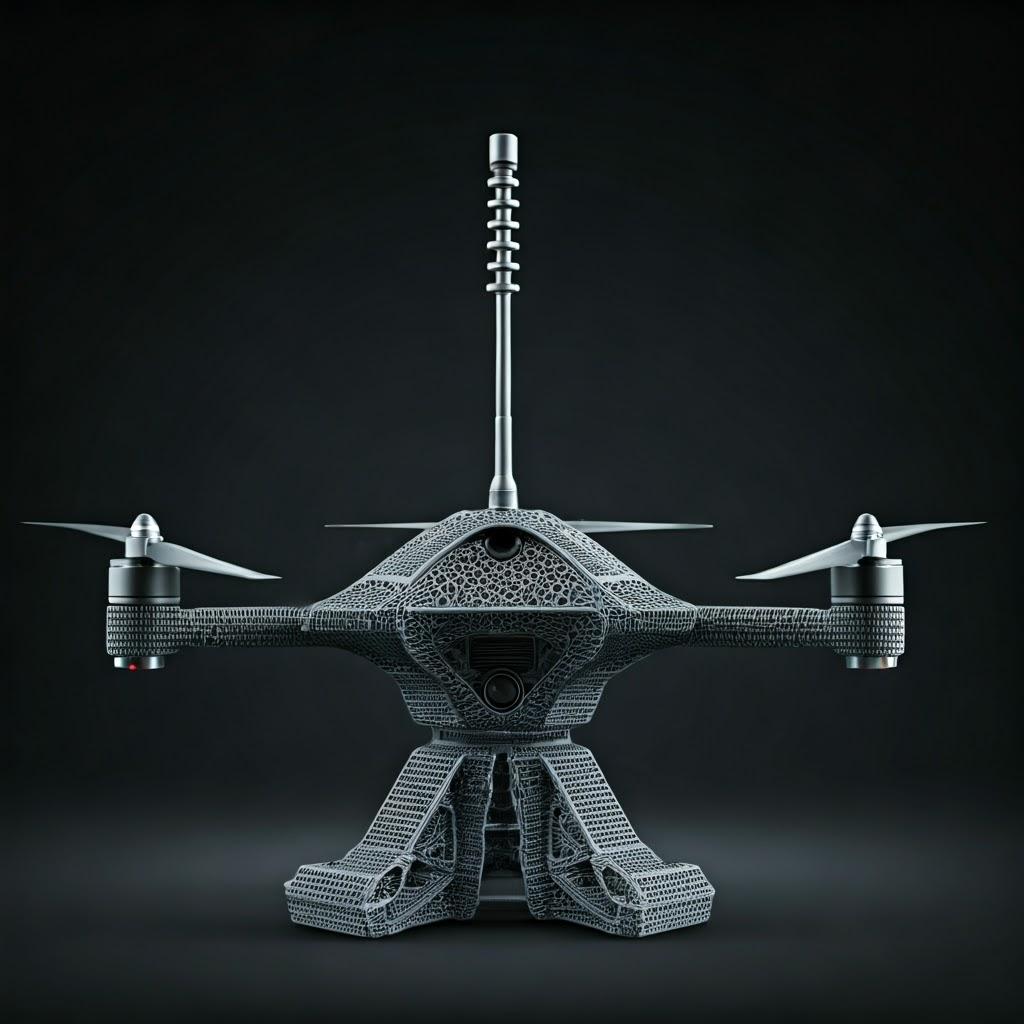
Frequently Asked Questions (FAQ) about 3D Printed Drone Antenna Supports
Here are answers to some common questions regarding the use of metal 3D printing for drone antenna supports using aluminum alloys:
1. How does the strength of a 3D printed aluminum antenna support compare to a traditionally CNC machined one?
- The comparison depends heavily on the specific alloys and post-processing involved.
- AlSi10Mg: When 3D printed and appropriately heat treated, AlSi10Mg typically achieves good strength, often comparable to mid-range cast aluminum alloys, but generally lower than high-strength wrought alloys like 6061-T6 or 7075-T6 that might be used for machining. However, the ability of AM to create optimized shapes means a 3D printed AlSi10Mg support can often meet or exceed the functional strength requirements of a bulkier machined part, but at a significantly lower weight.
- A7075: When 3D printed using optimized parameters with high-quality powder (like those from Met3dp) and subjected to a proper T6 heat treatment cycle, A7075 can achieve mechanical properties (yield strength, ultimate tensile strength) that closely approach, and in some cases meet, those of traditionally wrought A7075-T6. In this case, a 3D printed A7075 support can offer comparable or even superior strength to a machined counterpart, especially when combined with topology optimization for maximum efficiency.
- Key takeaway: While as-printed properties might differ, the combination of AM design freedom (optimization) and appropriate material/post-processing selection allows 3D printed supports to meet demanding strength requirements, often with significant weight advantages over machined alternatives.
2. What are the typical weight savings achievable by using metal 3D printing for drone antenna supports?
- Significant weight savings are one of the primary drivers for using AM in this application. Compared to a traditionally designed and manufactured component (e.g., machined from billet), typical weight reductions achievable through topology optimization, lattice structures, and part consolidation enabled by AM often range from 30% to 60%, and sometimes even higher.
- The actual saving depends on the original design’s efficiency, the complexity of the load cases, and how aggressively DfAM principles are applied. Even replacing a relatively simple machined bracket with a topology-optimized AM version can yield substantial savings, which directly translates to improved drone flight time, payload capacity, or agility.
3. Is 3D printed A7075 aluminum reliable enough for critical aerospace or military drone applications?
- Yes, provided that stringent process controls, qualification, and quality assurance procedures are followed. While historically challenging to print, advancements in AM-specific A7075 powder formulations, optimized process parameters, and robust post-processing (especially controlled T6 heat treatment and potentially HIP) allow for the production of high-density parts with predictable, high-performance mechanical properties suitable for demanding applications.
- Critical Factors for Reliability:
- Using high-quality, certified A7075 powder specifically designed for AM.
- Partnering with an AM provider with proven expertise and validated processes for printing A7075 (often demonstrated through certifications like AS9100).
- Implementing rigorous process monitoring and quality control, including potential NDT for critical parts.
- Performing the required T6 heat treatment correctly and verifying mechanical properties through testing.
- Thorough design validation and component testing (e.g., vibration, load testing) specific to the drone application.
- Many aerospace companies are increasingly adopting additively manufactured components, including those made from high-strength aluminum alloys, for flight applications after rigorous qualification.
4. What information do I need to provide to get an accurate quote and lead time for a 3D printed antenna support?
- To receive the most accurate quote and realistic lead time estimate from a metal AM service provider, you should provide as much detailed information as possible, including:
- 3D CAD Model: In a standard format (e.g., STEP, STL – though STEP is often preferred for measurement and analysis).
- Material Specification: Clearly state the desired aluminum alloy (e.g., AlSi10Mg or A7075).
- Technical Drawing (Recommended): Include critical dimensions, required tolerances (using GD&T if necessary), surface finish requirements (Ra values for specific surfaces), and locations for any post-machining or specific features (e.g., threaded holes).
- Post-Processing Requirements: Specify required heat treatment (e.g., Stress Relief only, T6 cycle for A7075), surface finishing (e.g., Bead Blast, Anodize Type II Black), and any necessary machining operations.
- Quantity: Specify the number of parts required (prototype vs. production volume).
- Application Details: Briefly describe the intended use (e.g., antenna support for commercial inspection drone), which helps the provider understand the context and criticality.
- Quality/Inspection Requirements: Mention any specific inspection needs (e.g., CMM report, material certification, AS9100 compliance).
- Providing comprehensive information upfront minimizes ambiguity and allows the service provider to quote accurately and plan production effectively.
Conclusion: Elevating Drone Capabilities with Advanced Aluminum Additive Manufacturing
The relentless pursuit of enhanced performance, extended operational range, and increased payload capacity in the rapidly evolving drone industry demands innovative approaches to component design and manufacturing. Drone antenna supports, though seemingly simple, are critical components where weight, strength, and precision directly impact the core functionality and mission success of the UAV. As we’ve explored, metal additive manufacturing, particularly using high-performance aluminum alloys like AlSi10Mg and the high-strength A7075, offers a transformative solution for producing these vital parts.
By unshackling designers from the constraints of traditional manufacturing, metal 3D printing enables the creation of antenna supports that are:
- Significantly Lighter: Through topology optimization and lattice structures, achieving weight reductions of 30-60% or more compared to conventional designs, directly boosting drone endurance and payload capacity.
- Highly Complex and Integrated: Allowing for intricate geometries that seamlessly integrate with the airframe, optimally position multiple antennas, incorporate features like cable routing, and consolidate assemblies into single, robust parts.
- Strong and Reliable: Utilizing aerospace-grade aluminum alloys and appropriate post-processing (like T6 heat treatment for A7075) to deliver mechanical properties suitable for demanding operational loads and vibrations.
- Rapidly Prototyped and Customized: Facilitating quick design iterations and cost-effective production of customized supports tailored to specific drone platforms or mission requirements.
However, realizing these benefits requires a holistic approach. Success hinges on embracing Design for Additive Manufacturing (DfAM) principles, carefully selecting the appropriate aluminum alloy (balancing the printability and cost-effectiveness of AlSi10Mg against the superior strength of A7075), understanding the critical role of post-processing steps like stress relief and heat treatment, and mitigating potential manufacturing challenges through process control and quality assurance.
Crucially, partnering with the right metal AM service provider is paramount. Expertise in processing aluminum alloys, investment in high-quality equipment and powders, comprehensive in-house post-processing capabilities, robust quality management systems (including certifications like AS9100 where needed), and strong engineering support are all essential attributes of a capable supplier. Companies like Met3dp, a leader in metal AM equipment and materials, embody these qualities, offering advanced powder manufacturing technologies and comprehensive additive manufacturing solutions to help organizations leverage the full potential of 3D printing.
In conclusion, metal additive manufacturing is not just an alternative but often a superior method for producing next-generation drone antenna supports. By strategically employing aluminum AM, drone manufacturers and component suppliers can achieve significant performance gains, accelerate development cycles, and ultimately elevate the capabilities of their UAV platforms, pushing the boundaries of what’s possible in aerial operations across commercial, industrial, and defense sectors.
Share On
MET3DP Technology Co., LTD is a leading provider of additive manufacturing solutions headquartered in Qingdao, China. Our company specializes in 3D printing equipment and high-performance metal powders for industrial applications.
Inquiry to get best price and customized Solution for your business!
Related Articles
About Met3DP
Recent Update
Our Product
CONTACT US
Any questions? Send us message now! We’ll serve your request with a whole team after receiving your message.
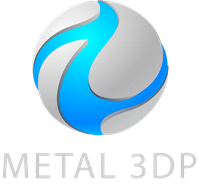
Metal Powders for 3D Printing and Additive Manufacturing