Guide of Arc Welding Electrode
Table of Contents
Arc welding electrodes are an essential component in the welding process, serving as the medium that facilitates the flow of electrical current, which melts the workpieces and forms a strong joint. If you’re diving into the world of welding or looking to deepen your knowledge, understanding arc welding electrodes is crucial. Let’s break down everything you need to know about them in this comprehensive guide.
Overview of Arc Welding Electrodes
Arc welding electrodes come in various types, each suited for different welding processes and materials. These electrodes are made of different materials and have specific coatings to enhance their performance. Choosing the right electrode can make a significant difference in the quality and efficiency of your welds.
Key Details:
- Definition: Arc welding electrodes are rods that conduct electrical current to the arc, facilitating the melting and fusion of metals.
- Purpose: They are used to maintain the arc, transfer the current, and add filler material to the weld joint.
- Types: There are several types, including consumable and non-consumable electrodes, each with distinct characteristics.
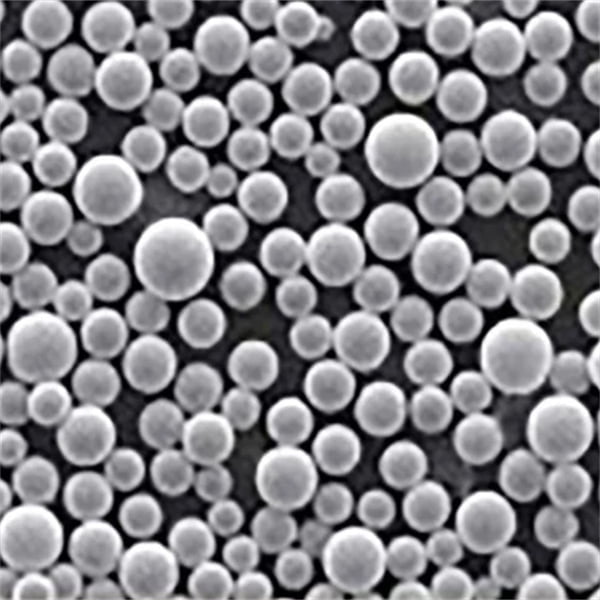
Types of Arc Welding Electrodes
Understanding the different types of arc welding electrodes is essential for selecting the right one for your project. Here’s a breakdown of the main types:
Type | Composition | Properties | Characteristics |
---|---|---|---|
Mild Steel Electrodes | Iron core with mild steel | Good ductility, moderate tensile strength | Suitable for general-purpose welding, easy to use, widely available |
Low Hydrogen Electrodes | Iron core with low hydrogen | Low hydrogen content to prevent cracking, high tensile strength | Ideal for high-strength steels, offers better control over the welding process |
Stainless Steel Electrodes | Stainless steel core | Corrosion-resistant, high-temperature strength | Used for welding stainless steel, offers resistance to oxidation and scaling at high temperatures |
Aluminum Electrodes | Aluminum core | Lightweight, corrosion-resistant | Designed for welding aluminum and aluminum alloys, offers good electrical conductivity |
Nickel Electrodes | Nickel core | High resistance to heat and corrosion | Used for welding nickel and nickel alloys, suitable for applications involving high temperatures and corrosive environments |
Cast Iron Electrodes | Cast iron core | High carbon content, brittle | Suitable for repairing cast iron parts, requires preheating to prevent cracking |
Hardfacing Electrodes | Various alloys | High hardness, wear-resistant | Used for overlaying hard surfaces to resist abrasion and impact, often used in heavy machinery repair |
Titanium Electrodes | Titanium core | Lightweight, high strength-to-weight ratio, corrosion-resistant | Ideal for aerospace and marine applications, offers excellent resistance to corrosion in seawater environments |
Copper Electrodes | Copper core | Excellent electrical and thermal conductivity | Used for welding copper and copper alloys, offers good resistance to corrosion |
Silver Electrodes | Silver core | High electrical conductivity, low melting point | Used in specialized applications requiring excellent electrical conductivity, such as electronics and electrical connections |
Applications of Arc Welding Electrodes
Different arc welding electrodes are suitable for various applications depending on their properties and characteristics. Let’s explore where these electrodes are typically used:
Electrode Type | Applications |
---|---|
Mild Steel Electrodes | Construction, automotive repair, fabrication of steel structures, general-purpose welding projects |
Low Hydrogen Electrodes | Structural welding, shipbuilding, pressure vessels, pipelines, heavy machinery |
Stainless Steel Electrodes | Food and beverage industry, chemical processing, petrochemical plants, architectural applications, medical equipment |
Aluminum Electrodes | Aerospace industry, automotive manufacturing, marine structures, fabrication of aluminum frames and structures |
Nickel Electrodes | Power generation, chemical processing, aerospace applications, high-temperature environments |
Cast Iron Electrodes | Repairing cast iron engine blocks, machinery parts, agricultural equipment, and other cast iron components |
Hardfacing Electrodes | Mining equipment, earthmoving machinery, agricultural tools, industrial rollers, hammers, and other high-wear components |
Titanium Electrodes | Aerospace components, marine applications, medical implants, chemical processing equipment |
Copper Electrodes | Electrical connections, plumbing, heat exchangers, roofing, and decorative metalwork |
Silver Electrodes | Electrical and electronic connections, jewelry making, specialized electrical components |
Specifications, Sizes, Grades, and Standards
When selecting an arc welding electrode, it’s crucial to consider specifications, sizes, grades, and standards to ensure you choose the right one for your application.
Electrode Type | Specifications | Sizes (inches) | Grades | Standards |
---|---|---|---|---|
Mild Steel Electrodes | AWS E6010, E6011, E7018 | 1/16, 3/32, 1/8, 5/32 | E6010, E6011, E7018 | AWS, ISO, BS EN |
Low Hydrogen Electrodes | AWS E7018, E7016, E7015 | 3/32, 1/8, 5/32, 3/16 | E7018, E7016, E7015 | AWS, ISO, BS EN |
Stainless Steel Electrodes | AWS E308L, E316L, E309L | 1/16, 3/32, 1/8, 5/32 | E308L, E316L, E309L | AWS, ISO, BS EN |
Aluminum Electrodes | AWS E4043, E5356 | 1/16, 3/32, 1/8, 5/32 | E4043, E5356 | AWS, ISO, BS EN |
Nickel Electrodes | AWS ENiCrFe-3, ENiCu-7 | 3/32, 1/8, 5/32, 3/16 | ENiCrFe-3, ENiCu-7 | AWS, ISO, BS EN |
Cast Iron Electrodes | AWS ENiFe-CI, ESt | 3/32, 1/8, 5/32, 3/16 | ENiFe-CI, ESt | AWS, ISO, BS EN |
Hardfacing Electrodes | AWS EFeMn-A, EFeCr-A1 | 1/8, 5/32, 3/16 | EFeMn-A, EFeCr-A1 | AWS, ISO, BS EN |
Titanium Electrodes | AWS ERTi-1, ERTi-2 | 1/16, 3/32, 1/8 | ERTi-1, ERTi-2 | AWS, ISO, BS EN |
Copper Electrodes | AWS ERCu, ERCuSi-A | 1/16, 3/32, 1/8 | ERCu, ERCuSi-A | AWS, ISO, BS EN |
Silver Electrodes | AWS EAg, EAgCuZn-A | 1/16, 3/32, 1/8 | EAg, EAgCuZn-A | AWS, ISO, BS EN |
Suppliers and Pricing Details
To make an informed decision, it’s essential to consider suppliers and pricing details. Here are some popular suppliers and the average price range for different arc welding electrodes:
Supplier | Electrode Type | Price Range (per lb) |
---|---|---|
Lincoln Electric | Mild Steel, Low Hydrogen, Aluminum | $3 – $15 |
ESAB | Stainless Steel, Nickel, Hardfacing | $5 – $20 |
Hobart | Cast Iron, Titanium, Copper | $4 – $18 |
Miller Electric | Mild Steel, Stainless Steel, Nickel | $3 – $16 |
Thermadyne (Tweco) | Low Hydrogen, Aluminum, Hardfacing | $4 – $17 |
Sandvik | Stainless Steel, Nickel | $6 – $22 |
Select-Arc | Mild Steel, Low Hydrogen | $3 – $14 |
Forney Industries | Aluminum, Copper, Cast Iron | $5 – $19 |
Kobelco | Stainless Steel, Hardfacing | $7 – $23 |
Eutectic Castolin | Nickel, Titanium, Silver | $8 – $25 |
Comparing Pros and Cons of Different Arc Welding Electrodes
Selecting the right electrode involves weighing the pros and cons. Let’s compare some key aspects of different electrodes:
Electrode Type | Advantages | Disadvantages |
---|---|---|
Mild Steel Electrodes | Easy to use, affordable, versatile | Moderate tensile strength, not suitable for high-strength applications |
Low Hydrogen Electrodes | High tensile strength, prevents cracking, better control over welding | Requires careful storage to avoid moisture absorption, slightly more expensive |
Stainless Steel Electrodes | Corrosion-resistant, high-temperature strength | Higher cost, requires careful handling to avoid contamination |
Aluminum Electrodes | Lightweight, corrosion-resistant, good conductivity | Can be challenging to weld, requires precise control of welding parameters |
Nickel Electrodes | High resistance to heat and corrosion, suitable for high-temperature environments | Expensive, can be brittle |
Cast Iron Electrodes | Suitable for repairing cast iron, high carbon content | Brittle, requires preheating, can be challenging to weld |
Hardfacing Electrodes | High hardness, wear-resistant, extends the life of components | Expensive, requires skilled application, can create a brittle weld |
Titanium Electrodes | High strength-to-weight ratio, corrosion-resistant | Very expensive, requires specialized welding techniques |
Copper Electrodes | Excellent conductivity, corrosion-resistant | Expensive, requires precise control over welding parameters |
Silver Electrodes | Excellent electrical conductivity, low melting point | Very expensive, limited to specialized applications |
Specific Metal Powder Models for Arc Welding Electrodes
Here are ten specific metal powder models used in the formulation of arc welding electrodes, along with their descriptions:
- FeSi (Ferrosilicon): Used in mild steel electrodes, enhances deoxidation and improves weld quality.
- FeMn (Ferromanganese): Increases tensile strength and ductility, commonly used in low hydrogen and hardfacing electrodes.
- FeCr (Ferrochrome): Enhances corrosion resistance, used in stainless steel and hardfacing electrodes.
- Ni (Nickel): Provides high resistance to heat and corrosion, used in nickel and stainless steel electrodes.
- Cu (Copper): Enhances electrical conductivity and corrosion resistance, used in copper and aluminum electrodes.
- TiO2 (Titanium Dioxide): Improves arc stability and slag formation, used in mild steel and stainless steel electrodes.
- Mo (Molybdenum): Increases tensile strength and resistance to high temperatures, used in low hydrogen and stainless steel electrodes.
- W (Tungsten): Enhances hardness and wear resistance, used in hardfacing electrodes.
- Al (Aluminum): Improves arc stability and reduces spatter, used in aluminum and copper electrodes.
- Ag (Silver): Provides excellent electrical conductivity, used in silver electrodes for specialized applications.
Advantages of Arc Welding Electrodes
Arc welding electrodes offer numerous advantages that make them a popular choice in various welding applications:
Versatility
Arc welding electrodes are highly versatile, suitable for welding a wide range of metals and alloys. Whether you’re working on mild steel, stainless steel, aluminum, or nickel, there’s an electrode that fits your needs.
Ease of Use
Many arc welding electrodes are designed for ease of use, making them accessible even to novice welders. They offer good arc stability and smooth weld bead formation, which simplifies the welding process.
Cost-Effectiveness
Compared to other welding methods, arc welding with electrodes is often more cost-effective. The equipment is relatively inexpensive, and the electrodes themselves are affordable, especially for general-purpose welding.
Portability
Arc welding equipment is generally portable, allowing welders to work in various locations, including outdoor and remote sites. This portability makes it ideal for construction, maintenance, and repair work.
High-Quality Welds
With the right electrode and proper technique, arc welding can produce high-quality welds with excellent strength and durability. Specialized electrodes can achieve specific properties like corrosion resistance or high-temperature strength.
Disadvantages of Arc Welding Electrodes
Despite their advantages, arc welding electrodes also have some disadvantages:
Skill Requirement
While some electrodes are user-friendly, achieving high-quality welds with certain types requires skill and experience. For example, welding with low hydrogen or aluminum electrodes can be challenging without proper training.
Slag Removal
Arc welding with certain electrodes, such as flux-coated ones, produces slag that must be removed after welding. This adds an extra step to the process and can be time-consuming.
Limited to Certain Metals
While arc welding electrodes are versatile, they are not suitable for all metals. For instance, welding titanium or other exotic alloys may require specialized techniques and equipment.
Moisture Sensitivity
Low hydrogen electrodes are sensitive to moisture and must be stored carefully to prevent hydrogen-induced cracking. This requires additional storage and handling precautions.
Spatter
Arc welding can produce spatter, small molten metal droplets that are ejected during welding. This can create a mess and require additional cleanup, especially in precision welding applications.
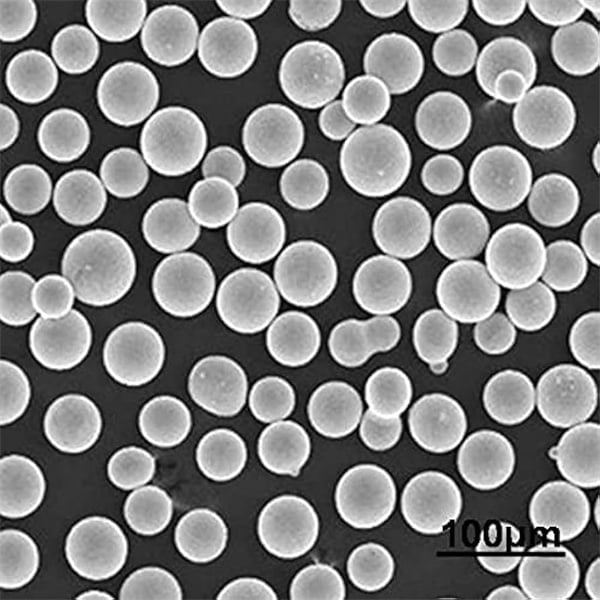
FAQ
To address common questions about arc welding electrodes, here is a comprehensive FAQ section:
Question | Answer |
---|---|
What is an arc welding electrode? | An arc welding electrode is a rod that conducts electrical current to the arc, melting and fusing metals to create a weld joint. |
What are the different types of arc welding electrodes? | There are several types, including mild steel, low hydrogen, stainless steel, aluminum, nickel, cast iron, hardfacing, titanium, copper, and silver electrodes. |
How do I choose the right electrode for my project? | Consider the base material, desired properties of the weld, welding position, and specific application requirements when choosing an electrode. |
What are the advantages of using low hydrogen electrodes? | Low hydrogen electrodes offer high tensile strength, prevent cracking, and provide better control over the welding process. |
Why is preheating required for cast iron electrodes? | Preheating reduces the risk of cracking by lowering the cooling rate and reducing thermal stress during welding. |
What are hardfacing electrodes used for? | Hardfacing electrodes are used to overlay hard surfaces to resist abrasion, impact, and wear, extending the life of components. |
Can I use arc welding electrodes for all metals? | While arc welding electrodes are versatile, they are not suitable for all metals. Specialized techniques and equipment may be needed for exotic alloys. |
How should I store low hydrogen electrodes? | Store low hydrogen electrodes in a dry environment and in sealed containers to prevent moisture absorption and hydrogen-induced cracking. |
What is the role of flux in arc welding electrodes? | Flux creates a protective gas shield, stabilizes the arc, and forms slag to protect the weld pool from contamination. |
How can I improve weld quality with arc welding electrodes? | Ensure proper electrode selection, maintain clean base materials, use correct welding techniques, and follow manufacturer guidelines for best results. |
In conclusion, understanding arc welding electrodes is essential for achieving high-quality welds in various applications. By choosing the right electrode and following best practices, you can ensure strong, durable, and reliable welds. Whether you’re working on a construction project, repairing machinery, or fabricating metal structures, the right arc welding electrode can make all the difference.
Share On
MET3DP Technology Co., LTD is a leading provider of additive manufacturing solutions headquartered in Qingdao, China. Our company specializes in 3D printing equipment and high-performance metal powders for industrial applications.
Inquiry to get best price and customized Solution for your business!
Related Articles
About Met3DP
Recent Update
Our Product
CONTACT US
Any questions? Send us message now! We’ll serve your request with a whole team after receiving your message.
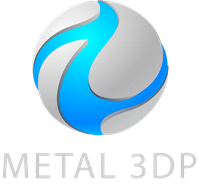
Metal Powders for 3D Printing and Additive Manufacturing