Batch-based debinded sinter equipment industry
Table of Contents
Overview of Batch-Based Debinded Sinter Equipment
Batch-based debinded sinter equipment plays a crucial role in the manufacturing processes of various industries, particularly in metallurgy and materials science. This equipment is designed to enhance the properties of metal powders by subjecting them to a controlled thermal treatment. The process involves debinding, which removes binder agents, and sintering, which consolidates the powder into a solid form through heat. This article provides a comprehensive look at the industry, including specific metal powder models, applications, specifications, suppliers, and more.
Introduction to Batch-Based Debinded Sinter Equipment
The batch-based debinded sinter equipment industry is vital for producing high-quality metal components. This equipment is used to process metal powders by heating them to a temperature below their melting points, causing particles to bond together. The process includes two main stages: debinding, where binders are removed, and sintering, where the material is solidified. These steps are essential for manufacturing parts with high density, strength, and precision.
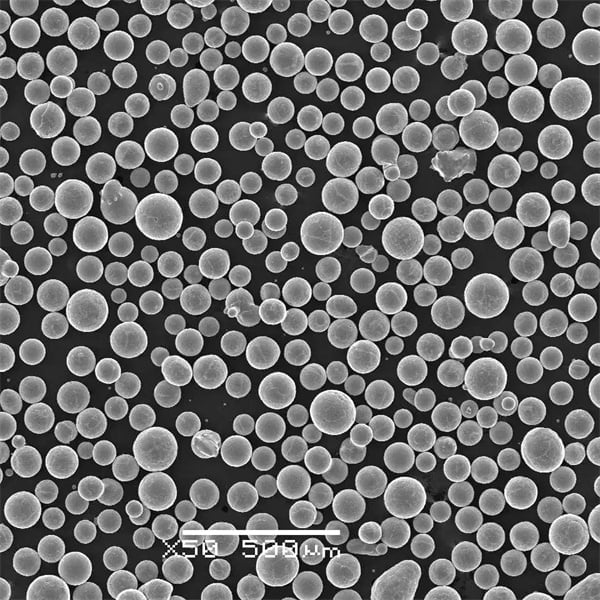
Specific Metal Powder Models
When discussing the batch-based debinded sinter equipment, it’s essential to mention specific metal powder models frequently used in the process. Below is a list of ten notable metal powder models:
- 316L Stainless Steel Powder
- Description: Known for its excellent corrosion resistance and high tensile strength.
- Applications: Medical implants, aerospace components, automotive parts.
- 17-4 PH Stainless Steel Powder
- Description: Precipitation-hardened steel offering a combination of strength and corrosion resistance.
- Applications: Aerospace, petrochemical, and general engineering.
- Ti-6Al-4V Titanium Alloy Powder
- Description: A high-strength, lightweight titanium alloy.
- Applications: Biomedical implants, aerospace structures, automotive components.
- Inconel 718 Powder
- Description: A nickel-chromium alloy with excellent high-temperature strength.
- Applications: Gas turbines, rocket engines, aerospace.
- AlSi10Mg Aluminum Alloy Powder
- Description: Combines good mechanical properties with low density.
- Applications: Automotive, aerospace, and consumer electronics.
- Copper Powder
- Description: Offers high thermal and electrical conductivity.
- Applications: Electrical components, heat sinks, conductive parts.
- H13 Tool Steel Powder
- Description: Known for its toughness and resistance to thermal fatigue.
- Applications: Tool and die making, automotive components, aerospace.
- Cobalt-Chromium Alloy Powder
- Description: Provides excellent wear resistance and biocompatibility.
- Applications: Medical implants, dental prosthetics, aerospace.
- Nickel 625 Powder
- Description: High-strength alloy with excellent corrosion resistance.
- Applications: Marine, chemical processing, aerospace.
- Tungsten Carbide Powder
- Description: Known for its hardness and wear resistance.
- Applications: Cutting tools, mining equipment, wear-resistant parts.
Types, Composition, Properties, and Characteristics
Metal Powder Model | Composition | Properties | Characteristics |
---|---|---|---|
316L Stainless Steel Powder | Fe, Cr, Ni, Mo | High corrosion resistance, good mechanical properties | Suitable for harsh environments, non-magnetic |
17-4 PH Stainless Steel Powder | Fe, Cr, Ni, Cu | High strength, good corrosion resistance, heat-treatable | Versatile, used in diverse applications |
Ti-6Al-4V Titanium Alloy Powder | Ti, Al, V | High strength-to-weight ratio, biocompatibility | Ideal for aerospace and medical industries |
Inconel 718 Powder | Ni, Cr, Fe, Nb, Mo | Excellent high-temperature strength, oxidation resistance | Used in extreme environments |
AlSi10Mg Aluminum Alloy Powder | Al, Si, Mg | Lightweight, good thermal conductivity | Suitable for lightweight structures |
Copper Powder | Cu | High thermal and electrical conductivity | Used in electrical and thermal management applications |
H13 Tool Steel Powder | Fe, Cr, Mo, V | High toughness, thermal fatigue resistance | Ideal for tool and die applications |
Cobalt-Chromium Alloy Powder | Co, Cr | Excellent wear resistance, biocompatibility | Preferred for medical implants and dental prosthetics |
Nickel 625 Powder | Ni, Cr, Mo, Nb | High strength, excellent corrosion resistance | Suitable for marine and chemical processing environments |
Tungsten Carbide Powder | WC | Extreme hardness, wear resistance | Used in cutting tools and wear-resistant applications |
Applications and Uses
Industry | Applications | Examples of Metal Powders Used |
---|---|---|
Aerospace | Jet engine components, turbine blades | Inconel 718, Ti-6Al-4V |
Medical | Implants, surgical instruments | 316L Stainless Steel, Ti-6Al-4V |
Automotive | Engine parts, structural components | AlSi10Mg, 17-4 PH Stainless Steel |
Electronics | Heat sinks, conductive components | Copper, AlSi10Mg |
Tool and Die Making | Cutting tools, molds, dies | H13 Tool Steel, Tungsten Carbide |
Energy | Turbine components, heat exchangers | Inconel 718, Nickel 625 |
Chemical Processing | Pumps, valves, fittings | Nickel 625, Cobalt-Chromium Alloy |
Marine | Propellers, shafts, underwater components | Nickel 625, Inconel 718 |
Consumer Products | Electronics housings, sports equipment | AlSi10Mg, 316L Stainless Steel |
Mining | Drilling equipment, wear-resistant parts | Tungsten Carbide, H13 Tool Steel |
Specifications, Sizes, Grades, and Standards
Metal Powder Model | Specifications | Sizes (µm) | Grades | Standards |
---|---|---|---|---|
316L Stainless Steel Powder | ASTM A276, ASTM A240 | 15-45 | 316L | ISO 5832-1, ASTM F138 |
17-4 PH Stainless Steel Powder | ASTM A693 | 20-53 | 17-4 PH | AMS 5643, ASTM A564 |
Ti-6Al-4V Titanium Alloy Powder | ASTM B348, ASTM F1472 | 10-45 | Ti-6Al-4V | ASTM F136, ISO 5832-3 |
Inconel 718 Powder | ASTM B670 | 15-53 | 718 | AMS 5662, ASTM B637 |
AlSi10Mg Aluminum Alloy Powder | ISO 209-1 | 20-63 | AlSi10Mg | DIN 1706, ASTM B85 |
Copper Powder | ASTM B212 | 10-45 | Cu | ASTM F15, ISO 4288 |
H13 Tool Steel Powder | ASTM A681 | 20-50 | H13 | ASTM A681 |
Cobalt-Chromium Alloy Powder | ASTM F75, ASTM F1537 | 15-45 | Co-Cr | ISO 5832-4, ASTM F799 |
Nickel 625 Powder | ASTM B443 | 15-53 | 625 | AMS 5666, ASTM B446 |
Tungsten Carbide Powder | ASTM B777 | 10-45 | WC | ISO 9001, ASTM F2792 |
Suppliers and Pricing Details
Supplier | Metal Powder Models Available | Pricing (per kg) | Notes |
---|---|---|---|
Höganäs AB | 316L, 17-4 PH, Ti-6Al-4V, Inconel 718 | $100 – $300 | Wide range of high-quality metal powders |
Carpenter Technology | 316L, 17-4 PH, Ti-6Al-4V, H13 Tool Steel | $150 – $350 | Specializes in high-performance materials |
Sandvik | AlSi10Mg, Inconel 718, Nickel 625, Tungsten Carbide | $200 – $400 | Extensive experience in powder metallurgy |
Kennametal | Tungsten Carbide, H13 Tool Steel, 17-4 PH, Cobalt-Chromium | $180 – $380 | Focus on tooling and wear-resistant solutions |
ATI Metals | 316L, Ti-6Al-4V, Inconel 718, Cobalt-Chromium | $120 – $320 | Advanced specialty materials supplier |
GKN Additive | AlSi10Mg, Ti-6Al-4V, Copper, Nickel 625 | $130 – $330 | Expertise in additive manufacturing |
Praxair Surface Technologies | Copper, AlSi10Mg, 316L, Inconel 718 | $140 – $340 | Leading provider of metal powders |
LPW Technology | Ti-6Al-4V, Inconel 718, Nickel 625, Cobalt-Chromium | $160 – $360 | Focus on high-purity metal powders |
EOS GmbH | AlSi10Mg, 316L, 17-4 PH, H13 Tool Steel | $170 – $370 | Comprehensive additive manufacturing solutions |
Carpenter Additive | Ti-6Al-4V, Inconel 718, Cobalt-Chromium, Nickel 625 | $190 – $390 | Emphasis on innovation in powder technology |
Advantages and Limitations of Batch-Based Debinded Sinter Equipment
Aspect | Advantages | Limitations |
---|---|---|
Quality Control | Consistent, high-quality output | Requires precise control of parameters |
Material Properties | Enhanced mechanical properties, improved density | Some materials may be sensitive to the process |
Versatility | Suitable for a wide range of materials and applications | Initial setup and calibration can be complex |
Cost Efficiency | Reduces material waste, lower production costs | Higher initial investment in equipment |
Design Flexibility | Complex geometries achievable | Limited to certain part sizes and shapes |
Environmental Impact | Energy-efficient process, reduced carbon footprint | Waste management of binders can be challenging |
Lead Time | Shorter production cycles | Longer setup times for new materials |
Surface Finish | Smooth surfaces with minimal post-processing required | Surface porosity may require additional treatments |
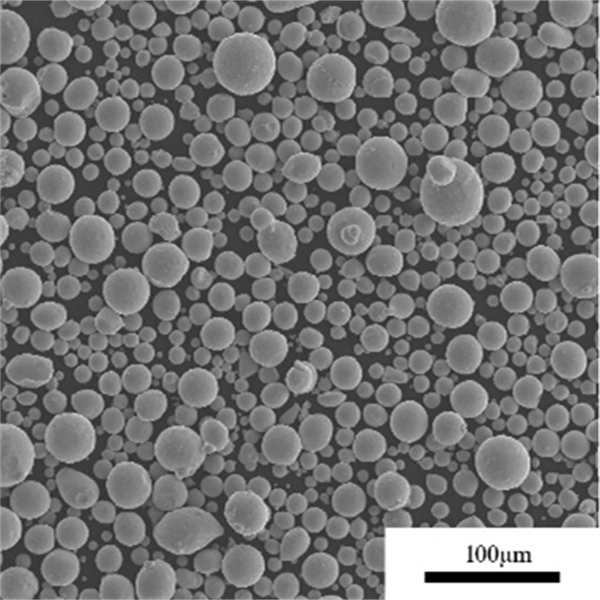
FAQ
Q: What are the key benefits of using batch-based debinded sinter equipment?
A: Batch-based debinded sinter equipment offers several advantages, including precise control over material properties, enhanced mechanical strength, and the ability to produce complex geometries. It also reduces material waste and lowers production costs by optimizing the use of raw materials.
Q: What are some challenges associated with batch-based debinded sinter equipment?
A: One of the main challenges is the initial setup and calibration required for each new material or part design. Additionally, managing the removal of binders and ensuring uniform sintering across batches can be complex. Some materials may also be sensitive to the thermal processing involved.
Q: How does batch-based debinded sinter equipment contribute to sustainability?
A: This equipment contributes to sustainability by reducing material waste through precise control over the sintering process. It also promotes energy efficiency and has a lower carbon footprint compared to traditional manufacturing methods. However, managing and disposing of binders used in the debinding process can pose environmental challenges.
Q: What industries benefit the most from batch-based debinded sinter equipment?
A: Industries such as aerospace, medical, automotive, and electronics benefit significantly from batch-based debinded sinter equipment. These sectors require parts with high strength-to-weight ratios, complex geometries, and excellent mechanical properties, which can be efficiently produced using this technology.
Conclusion
The batch-based debinded sinter equipment industry plays a pivotal role in modern manufacturing, offering advanced solutions for producing high-performance metal components. By leveraging precise control over the debinding and sintering processes, manufacturers can achieve superior material properties and complex part geometries. As technology advances, the versatility and efficiency of this equipment continue to expand, catering to diverse applications across various industries.
In conclusion, understanding the specific metal powder models, their compositions, properties, applications, and supplier details is crucial for optimizing the use of batch-based debinded sinter equipment in industrial settings. This comprehensive overview provides insights into how these materials and processes are transforming manufacturing capabilities worldwide.
Share On
MET3DP Technology Co., LTD is a leading provider of additive manufacturing solutions headquartered in Qingdao, China. Our company specializes in 3D printing equipment and high-performance metal powders for industrial applications.
Inquiry to get best price and customized Solution for your business!
Related Articles
About Met3DP
Recent Update
Our Product
CONTACT US
Any questions? Send us message now! We’ll serve your request with a whole team after receiving your message.
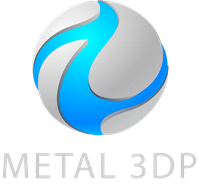
Metal Powders for 3D Printing and Additive Manufacturing