Electron Beam Melting Materials : How to Choose?
Table of Contents
Imagine shaping complex metal parts layer by layer, with unparalleled precision and strength. This isn’t science fiction, but the reality of Electron Beam Melting (EBM), a revolutionary 3D printing technology that’s transforming various industries. But what fuels this process? The answer lies in the heart of EBM materials, a diverse range of metal powders specifically engineered to unlock the full potential of this technology.
Delving deeper into the world of EBM materials, we’ll explore their unique properties, delve into their diverse applications, and unveil the key considerations when selecting the perfect material for your project. Buckle up, as we embark on a journey into the fascinating world of these powerful building blocks!
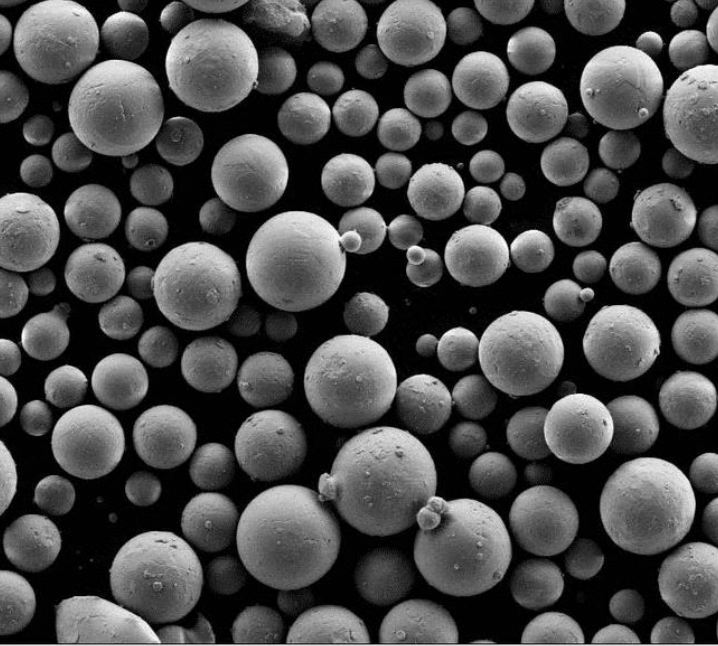
EBM Materials: A Spectrum of Possibilities
EBM materials encompass a wide array of metallic powders, each boasting distinct characteristics and functionalities. Understanding these individual strengths is crucial for unlocking the full potential of EBM technology. Here’s a glimpse into some of the most prominent EBM materials:
Material | Composition | Key Properties | Applications |
---|---|---|---|
Titanium (Ti) | Pure titanium or various alloys with elements like aluminum, vanadium, or oxygen | High strength-to-weight ratio, excellent biocompatibility, corrosion resistance | Aerospace components, biomedical implants, dental prosthetics |
Cobalt-Chrome (CoCr) | Cobalt and chromium alloy, often with molybdenum or tungsten | Exceptional wear resistance, high strength, biocompatibility | Biomedical implants, dental prosthetics, cutting tools |
Nickel Alloys | Varied compositions, including Inconel and Hastelloy, with elements like nickel, chromium, molybdenum, and iron | High-temperature resistance, excellent corrosion resistance, superior strength | Turbine blades, heat exchangers, chemical processing equipment |
Stainless Steel | Various compositions, primarily iron, chromium, and nickel, with additional elements like molybdenum or nitrogen | Corrosion resistance, good mechanical properties, affordability | Medical instruments, aerospace components, automotive parts |
Copper (Cu) | Pure copper or copper-based alloys | Excellent thermal and electrical conductivity, high ductility | Heat sinks, electrical components, thermal management applications |
Tool Steel | Diverse compositions, often containing elements like chromium, vanadium, tungsten, and molybdenum | High hardness, wear resistance, excellent dimensional stability | Cutting tools, molds and dies, wear-resistant components |
Inconel 625 | Nickel-chromium-based superalloy with molybdenum and niobium | Outstanding high-temperature strength, oxidation resistance, creep resistance | Turbine blades, rocket engine components, heat exchangers |
Hastelloy C-276 | Nickel-chromium-molybdenum alloy with tungsten and iron | Exceptional corrosion resistance to a wide range of chemicals, high strength | Chemical processing equipment, pumps, valves, heat exchangers |
MP1 (Maraging Steel) | Nickel-steel alloy with low carbon content and high molybdenum | High strength-to-weight ratio, excellent toughness and dimensional stability, good corrosion resistance | Aerospace components, defense applications, high-performance racing parts |
Tantalum (Ta) | Pure tantalum or tantalum alloys with elements like tungsten | High melting point, excellent biocompatibility, corrosion resistance | Biomedical implants, capacitors, crucibles for high-temperature applications |
It’s important to note that this is just a snapshot of the vast array of EBM materials available. New and innovative materials are constantly being developed, pushing the boundaries of what’s possible with this technology.
Applications of EBM Materials
The unique properties of EBM materials unlock a spectrum of possibilities across various industries. Here’s a glimpse into some of the exciting applications:
Industry | Applications | Benefits of EBM |
---|---|---|
Aerospace | Turbine blades, landing gear components, lightweight structural parts | High strength-to-weight ratio, complex geometries, design freedom |
Biomedical | Hip and knee implants, dental prosthetics, surgical instruments | Biocompatible materials, excellent fatigue strength, porosity for bone ingrowth |
Automotive | High-performance engine components, lightweight car parts | Lighter weight for improved fuel efficiency, complex geometries for enhanced performance |
Energy | Heat exchangers, turbine blades, components for nuclear reactors | High-temperature resistance, corrosion resistance, specific properties for demanding environments |
Defense | Weapon components, armor parts, custom tools | High strength, lightweight materials, ability to create complex shapes |
EBM technology allows for the creation of highly complex geometries that were previously impossible with traditional manufacturing techniques.
Specifications, Suppliers, and Costs of EBM Materials
Understanding the technical specifications, suppliers, and pricing of EBM materials is crucial for making informed decisions in your projects. Let’s delve deeper into these aspects:
Specifications:
EBM materials come in various particle sizes, grades, and standards. These factors significantly impact the final properties of the printed parts. Here’s a breakdown:
Specification | Description | Impact |
---|---|---|
Particle Size | The average diameter of individual powder particles | Affects surface finish, density, and mechanical properties of the printed parts. Finer particles generally lead to smoother surfaces, higher density, but may be more challenging to process. |
Grade | Refers to the purity and chemical composition of the powder | Directly influences the final properties of the printed part, such as mechanical strength, corrosion resistance, and biocompatibility. |
Standards | Set by organizations like ASTM International, these define the specific requirements for EBM materials regarding composition, particle size distribution, and other parameters. | Ensures consistency and quality of the material, allowing comparison between different suppliers and contributing to achieving desired part properties. |
Here’s a table outlining specific examples of EBM materials with their corresponding specifications:
Material | Particle Size (µm) | Grade | Standard |
---|---|---|---|
Ti-6Al-4V | 45-100 | Grade 23 | ASTM F2992 |
CoCrMo | 20-50 | ASTM F75 | ASTM F1855 |
Inconel 625 | 20-50 | AMS 5662 | ASTM F2992 |
316L Stainless Steel | 45-90 | 316L | ASTM F316L |
Suppliers:
Several leading companies supply EBM materials, each offering a range of options and expertise. Here are some prominent suppliers:
Supplier | Website | Materials Offered |
---|---|---|
MET3DP | https://met3dp.com/ | Ti, CoCr, Ni alloys, Stainless Steel |
Höganäs | https://www.hoganas.com/en/ | Ti, Ni alloys, Stainless Steel, Tool Steel |
Carpenter Additive | https://www.carpenteradditive.com/ | Inconel, Hastelloy, MP1 |
LPW Technology | https://www.carpenteradditive.com/news-events/lpw-technology-am-metal-powder-manufacturing | Ti, CoCr, Ni alloys, Stainless Steel, Tool Steel |
It’s crucial to research and compare offerings from various suppliers considering factors like material availability, specific requirements, and pricing.
Price Range:
The cost of EBM materials varies significantly depending on the specific material, grade, quantity, and supplier. Generally, high-performance materials like Inconel or Hastelloy tend to be more expensive compared to standard grades of titanium or stainless steel. Additionally, the quantity purchased can influence pricing, with larger quantities often attracting bulk discounts.
Here’s a table presenting a general price range for some common EBM materials:
Material | Price Range (USD/kg) |
---|---|
Ti-6Al-4V | $100-200 |
CoCrMo | $150-250 |
Inconel 625 | $300-500 |
316L Stainless Steel | $50-100 |
Remember, these are just rough estimates. Contacting suppliers for specific quotes based on your project requirements is recommended.
Weighing the Options: Pros and Cons of EBM Materials
EBM materials offer a unique set of advantages and limitations compared to traditional manufacturing materials. Understanding both sides of the coin is crucial for making informed choices.
Pros:
- High strength-to-weight ratio: EBM materials offer exceptional strength while being lightweight, making them ideal for applications like aerospace and transportation.
- Complex geometries: EBM technology allows for the creation of intricate and complex shapes, previously impossible with traditional techniques.
- Material properties: EBM materials boast exceptional properties like high-temperature resistance, corrosion resistance, and biocompatibility, suitable for demanding applications.
- Design freedom: EBM enables designers to create intricate internal structures and features, leading to innovative product design and functionality.
Cons:
- Limited material selection: While the range of EBM materials is expanding, it’s still not as comprehensive as traditional manufacturing options. This can limit its applicability for certain projects requiring specific material properties.
- Surface finish: EBM parts typically have a rougher surface finish compared to other additive manufacturing processes like Selective Laser Melting (SLM). This may require additional post-processing steps, increasing cost and lead time.
- Build size limitations: Due to the nature of the EBM process, the build size of parts can be limited compared to some other 3D printing technologies. This might not be suitable for applications requiring large-scale components.
- Environmental considerations: The EBM process involves high temperatures and a vacuum environment, raising concerns about energy consumption and potential emissions. Companies implementing EBM technology need to address these environmental factors responsibly.
FAQs about EBM Materials
1. What are the advantages of EBM over other 3D printing technologies?
EBM offers several advantages, including:
- High strength-to-weight ratio: Ideal for applications where weight reduction is crucial, like aerospace and transportation.
- Excellent mechanical properties: EBM parts boast good strength, fatigue resistance, and wear resistance.
- Biocompatibility: Certain EBM materials like titanium are biocompatible, making them suitable for biomedical implants.
- Complex geometries: EBM allows for the creation of intricate shapes impossible with traditional manufacturing.
2. What are the disadvantages of EBM compared to other options?
The main drawbacks of EBM include:
- Higher cost: EBM materials and equipment tend to be more expensive compared to other 3D printing technologies.
- Limited material selection: The range of EBM materials is not as vast as other options, restricting its applicability in some cases.
- Rougher surface finish: EBM parts may require additional post-processing for smoother surfaces, adding to costs and lead time.
3. What are the typical applications of EBM materials?
EBM finds applications in various industries, including:
- Aerospace: Turbine blades, landing gear components, lightweight structural parts.
- Biomedical: Hip and knee implants, dental prosthetics, surgical instruments.
- Automotive: High-performance engine components, lightweight car parts.
- Energy: Heat exchangers, turbine blades, components for nuclear reactors.
- Defense: Weapon components, armor parts, custom tools.
4. How much do EBM materials cost?
The cost of EBM materials varies depending on the specific material, grade, quantity, and supplier. Generally, expect a range of $50-500 per kilogram. Contacting suppliers for specific quotes is recommended.
5. Where can I find EBM materials?
Several reputable companies supply EBM materials, including:
- AP Alloys
- Höganäs
- Carpenter Additive
- LPW Technology
It’s important to compare offerings from various suppliers based on your specific needs and budget.
Conclusion
EBM materials offer a unique combination of high strength, complex geometries, and valuable properties like biocompatibility and high-temperature resistance. However, it’s crucial to consider the limitations, such as cost, limited material selection, and potential environmental concerns. By carefully weighing the pros and cons and understanding the available materials and their suppliers, you can make informed decisions about whether EBM technology is the right choice for your project.
Share On
MET3DP Technology Co., LTD is a leading provider of additive manufacturing solutions headquartered in Qingdao, China. Our company specializes in 3D printing equipment and high-performance metal powders for industrial applications.
Inquiry to get best price and customized Solution for your business!
Related Articles
About Met3DP
Recent Update
Our Product
CONTACT US
Any questions? Send us message now! We’ll serve your request with a whole team after receiving your message.
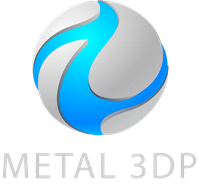
Metal Powders for 3D Printing and Additive Manufacturing