introduction to Binder Jetting
Table of Contents
Imagine a 3D printer that builds objects layer by layer, not with melted plastic or lasers, but with a sprinkling of powder and a strategic squirt of glue. That’s the magic of binder jetting, an additive manufacturing (AM) technique rapidly gaining traction for its speed, affordability, and diverse material compatibility.
This guide dives deep into the fascinating world of binder jetting, exploring its core principles, the fascinating world of metal powders it utilizes, its applications, advantages, limitations, and more. So, buckle up and get ready to witness a revolution in 3D printing, one printed layer at a time.
Binder Jetting: A Layered Approach to 3D Printing
Binder jetting operates on a surprisingly simple principle. Here’s a breakdown of the process:
- Powder Bed Preparation: A layer of fine metal powder, like grains of sand on a beach, is spread evenly across a platform.
- Binder Deposition: An inkjet printhead, similar to those in your home printer, scans the digital design and selectively deposits a liquid binder onto the powder bed, adhering the desired particles together.
- Layer by Layer: The platform lowers slightly, and a fresh layer of powder is deposited. The printing process repeats, building the object one layer at a time.
- Post-Processing: Once complete, the unbound powder is removed, leaving behind the 3D printed object. This “green” part is then sintered, a high-heat treatment that strengthens and densifies the metal particles.
Think of binder jetting like building a sandcastle on steroids. Instead of using your hands to mold the wet sand, a high-tech printer precisely binds the particles to create intricate and robust structures.
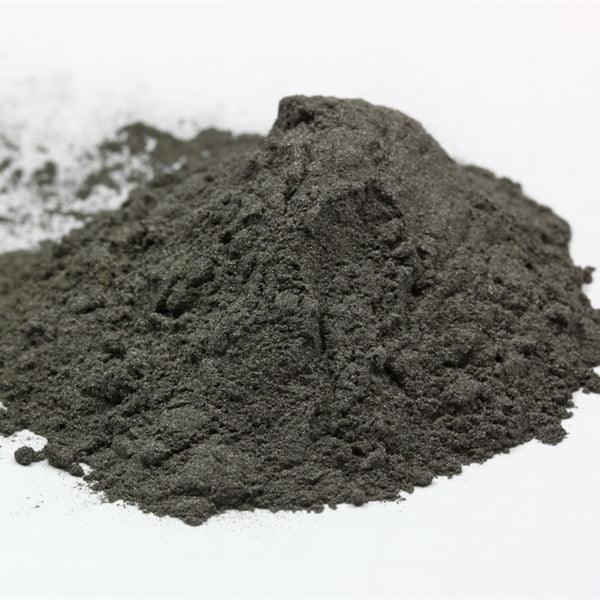
Unveiling the Metal Powder Arsenal: A Look at 10 Key Players
Binder jetting’s versatility truly shines in the vast array of metal powders it can utilize. Each powder boasts unique properties, catering to specific applications. Here’s a closer look at 10 prominent metal powders in the binder jetting arena:
1. Stainless Steel 316L: The undisputed champion, 316L stainless steel offers excellent corrosion resistance, making it ideal for applications like medical implants, marine components, and food processing equipment.
2. Inconel 625: Known for its high-temperature strength and resistance to harsh environments, Inconel 625 finds favor in aerospace, gas turbines, and chemical processing applications where heat resistance is paramount.
3. Titanium 6Al-4V: This lightweight and biocompatible powder is a game-changer in the medical and aerospace industries. Its exceptional strength-to-weight ratio makes it perfect for prosthetics, implants, and high-performance aircraft components.
4. Maraging Steel: Combining high strength with good ductility (the ability to bend without breaking), maraging steel caters to applications requiring exceptional toughness, such as tooling and weapon components.
5. Aluminum: Lightweight and readily available, aluminum powders are a cost-effective option for prototyping and applications where weight reduction is crucial, such as automotive and aerospace components.
6. Nickel: Offering a unique blend of electrical and thermal conductivity, nickel powders are well-suited for electronic components, electrodes, and heat exchangers.
7. Copper: Highly conductive and malleable, copper powders are a go-to choice for electrical components, heat sinks, and applications requiring excellent thermal management.
8. Kovar: With a thermal expansion coefficient that closely matches glass, Kovar powders are ideal for creating glass-to-metal seals in electronics and scientific instruments.
9. Tungsten: This high-density and heat-resistant powder is perfect for applications requiring exceptional wear resistance and high-temperature performance, such as crucibles and armor components.
10. Tooling Steel: Offering excellent wear resistance and hardness, tooling steel powders are ideal for creating molds, dies, and other tooling components.
The Advantages and Trade-Offs of Binder Jetting
Choosing the right metal powder for your project depends on the desired properties. Here’s a quick comparison of some key considerations:
- Strength & Toughness: Stainless steel 316L and maraging steel reign supreme for these properties.
- Corrosion Resistance: Stainless steel 316L is the undisputed champion for battling the elements.
- High-Temperature Performance: Inconel 625 takes the crown for withstanding extreme heat.
- Lightweight: Aluminum and Titanium 6Al-4V are the clear winners when weight matters.
- Cost-Effectiveness: Aluminum takes the cake for budget-conscious projects.
Binder jetting isn’t just a fancy party trick for metal powders. It finds application in a surprising range of industries, each capitalizing on its unique strengths. Here’s a glimpse into the diverse world of binder jetting applications:
Manufacturing:
- Prototyping: Binder jetting excels at creating rapid prototypes due to its speed and ability to handle complex geometries. This allows manufacturers to test designs quickly and iterate before committing to expensive traditional manufacturing processes.
- Low-Volume Production: For small batch production runs, binder jetting offers a cost-effective alternative to traditional techniques like casting or machining. The ability to print multiple parts simultaneously further enhances its production efficiency.
- Tooling: Binder jetting can create complex molds, dies, and jigs for various manufacturing processes. The ability to produce intricate features with good dimensional accuracy makes it ideal for creating specialized tooling.
Medical & Healthcare:
- Prosthetics & Implants: Customized prosthetics and implants made from biocompatible materials like Titanium 6Al-4V are revolutionizing patient care. Binder jetting allows for personalized designs that improve fit, comfort, and functionality.
- Surgical Instruments: Complex surgical instruments with intricate features can be produced using binder jetting, offering surgeons more precise and efficient tools.
- Dental Applications: Custom dental crowns, bridges, and other dental prosthetics can be created with high accuracy using binder jetting, improving patient outcomes and aesthetics.
Aerospace & Defense:
- Lightweight Components: Aircraft components made from lightweight materials like aluminum and titanium can be produced using binder jetting, contributing to overall fuel efficiency and performance.
- Heat Resistant Parts: Inconel 625 finds application in creating heat-resistant components for jet engines and other high-temperature applications.
- Prototyping & Development: The rapid prototyping capabilities of binder jetting are invaluable for developing and testing new aerospace components.
Other Applications:
- Jewelry & Art: Binder jetting allows for the creation of intricate and unique jewelry pieces with intricate details and complex geometries.
- Consumer Goods: Functional and aesthetic components for consumer products like electronics housings and sporting goods can be produced using this versatile technique.
The Future of Binder Jetting
Binder jetting is a rapidly evolving technology with immense potential. Here’s a peek into what the future holds for this innovative 3D printing technique:
- Material Advancements: New and improved metal powders with enhanced properties are constantly being developed, expanding the range of applications for binder jetting.
- Multi-Material Printing: The ability to combine different metal powders within a single print could pave the way for the creation of parts with unique property gradients.
- Increased Automation: Automation of post-processing steps such as debinding and sintering could streamline the binder jetting process, making it even more efficient and cost-effective.
- Mass Production: As the technology matures, binder jetting could potentially be used for mass production of certain metal parts, blurring the lines between traditional and additive manufacturing.
the Pros and Cons of Binder Jetting
No technology is perfect, and binder jetting is no exception. Let’s delve into the advantages and limitations of this 3D printing technique:
Advantages of Binder Jetting:
- Speed: Binder jetting is significantly faster than many other 3D printing techniques, making it ideal for rapid prototyping and low-volume production.
- Cost-Effectiveness: Compared to traditional manufacturing methods, binder jetting can be a cost-effective option, especially for complex geometries.
- Design Freedom: Binder jetting allows for the creation of intricate and complex designs that are difficult or impossible to achieve with traditional techniques.
- Material Versatility: A wide range of metal powders can be used with binder jetting, catering to diverse application needs.
- Scalability: Binder jetting systems can be scaled to accommodate various production volumes, making them suitable for both prototyping and production runs.
Limitations of Binder Jetting:
- Resolution: Compared to some other 3D printing techniques, binder jetting offers a lower resolution, resulting in a slightly rougher surface finish.
- Post-Processing: Binder jetting parts require post-processing steps like debinding and sintering, which can add time and complexity to the overall process.
- Material Properties: The properties of binder jetted parts may not always be on par with those of traditionally manufactured metal parts due to residual porosity.
- Limited Color Options: Currently, binder jetting offers limited color options for metal parts.
Is Binder Jetting Right for You?
The decision to use binder jetting depends on your specific project requirements. If you need a fast, cost-effective way to create complex prototypes
Binder jetting isn’t a one-size-fits-all solution. To make informed decisions, understanding the technical specifications is crucial. Here’s a breakdown of key parameters to consider:
Metal Powder Properties:
Property | Description |
---|---|
Particle Size & Distribution | The size and distribution of metal powder particles significantly impact the resolution, surface finish, and mechanical properties of the final part. Finer powders generally result in smoother finishes and potentially better mechanical properties, but may also be more challenging to process. |
Sphericity | The roundness of the powder particles influences packing density and flowability. More spherical particles pack more efficiently, leading to denser parts and potentially improved strength. |
Apparent Density | This refers to the bulk density of the powder, which can affect the amount of material required for printing and the overall cost. |
Printing Parameters:
Parameter | Description |
---|---|
Layer Thickness | The thickness of each printed layer directly impacts the resolution and build time. Thicker layers are faster to print but result in a rougher surface finish. |
Binder Jetting Resolution | This refers to the minimum feature size that can be accurately printed. It depends on the printhead nozzle size and the properties of the metal powder. |
Build Volume | The maximum size of the part that can be printed in a single build depends on the specific binder jetting system. |
Post-Processing Parameters:
Parameter | Description |
---|---|
Debinding Process | The method used to remove the unbound binder material from the printed part. This can involve thermal or chemical debinding techniques, each with its own advantages and limitations. |
Sintering Parameters | Sintering involves heating the part to a high temperature below the melting point, causing the metal particles to bond together. Sintering temperature, time, and atmosphere all play a crucial role in the final properties of the part. |
Part Properties:
Property | Description |
---|---|
Density | The density of the final part directly impacts its mechanical properties. Binder jetted parts typically have some porosity due to the presence of residual pores from the powder particles. |
Mechanical Properties | The mechanical properties of binder jetted parts, such as tensile strength, yield strength, and elongation, depend on the chosen metal powder, printing parameters, and post-processing steps. |
Surface Finish | Binder jetted parts typically have a slightly rougher surface finish compared to some other 3D printing techniques. Surface finishing techniques can be used to improve the aesthetics and functionality of the part. |
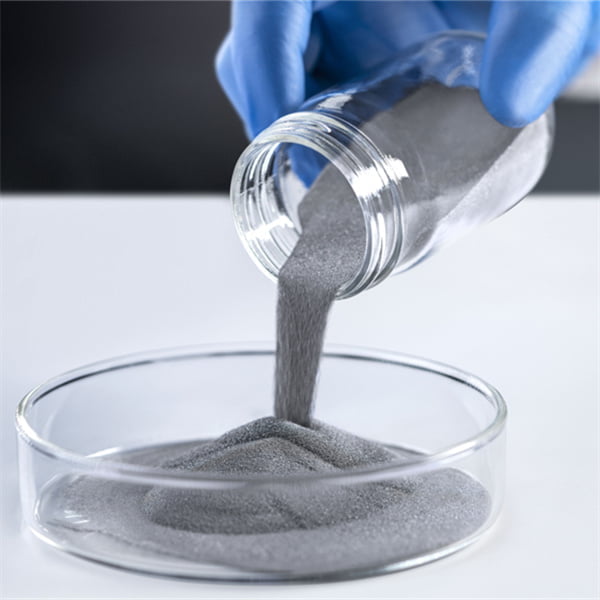
Exploring the Price Landscape
The cost of binder jetting depends on several factors, including:
- Material Costs: The cost of the metal powder is a significant factor, with some exotic powders being more expensive than others.
- Part Complexity: Complex geometries with a high volume of material will generally cost more to print than simpler parts.
- Post-Processing Costs: The cost of debinding and sintering can vary depending on the chosen methods and the size and complexity of the parts.
- Machine Availability & Throughput: The cost per part can be lower for high-volume production runs utilizing dedicated binder jetting systems.
While it’s challenging to provide a definitive price quote without specific project details, binder jetting can be a cost-effective option for prototyping and low-volume production runs of complex metal parts.
FAQ
Here’s a breakdown of some frequently asked questions (FAQs) about binder jetting:
Question | Answer |
---|---|
What are the advantages of binder jetting compared to other 3D printing techniques? | Binder jetting offers several advantages, including speed, affordability, design freedom, and material versatility. |
What are the limitations of binder jetting? | Binder jetting has limitations in resolution, post-processing requirements, and the potential for slightly lower material properties compared to some traditional manufacturing techniques. |
What types of metal powders can be used with binder jetting? | A wide range of metal powders can be used with binder jetting, including stainless steel, Inconel, titanium, and aluminum. |
What are the applications of binder jetting? | Binder jetting finds application in prototyping, low-volume production, tooling, medical & healthcare, aerospace & defense, and even jewelry & art. |
Is binder jetting suitable for mass production? | While not currently a mainstream mass production technique, binder jetting has the potential to be used for mass production of certain metal parts as the technology matures. |
Share On
MET3DP Technology Co., LTD is a leading provider of additive manufacturing solutions headquartered in Qingdao, China. Our company specializes in 3D printing equipment and high-performance metal powders for industrial applications.
Inquiry to get best price and customized Solution for your business!
Related Articles
About Met3DP
Recent Update
Our Product
CONTACT US
Any questions? Send us message now! We’ll serve your request with a whole team after receiving your message.
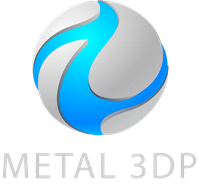
Metal Powders for 3D Printing and Additive Manufacturing