the Advantages of Binder Jetting
Table of Contents
Binder jetting, a revolutionary 3D printing technology, is rapidly transforming the manufacturing landscape. Imagine a process that brings complex metal parts to life at high speeds, with minimal waste and a wider material palette than ever before. That’s the magic of binder jetting, and this comprehensive guide delves into its numerous advantages, explores a variety of metal powder options, and answers all your burning questions.
Binder Jetting: A Technical Deep Dive
Binder jetting operates on a surprisingly simple yet powerful principle. A layer of fine metal powder is spread across a platform. Then, a printhead selectively jets a binding agent onto the powder, adhering particles together and defining the part’s geometry. Layer by layer, the object takes shape, surrounded by unbound powder that acts as natural support. After printing, the unbound powder is removed, and the part undergoes additional processes like infiltration (filling pores with metal) and sintering (fusing particles) to achieve its final properties.
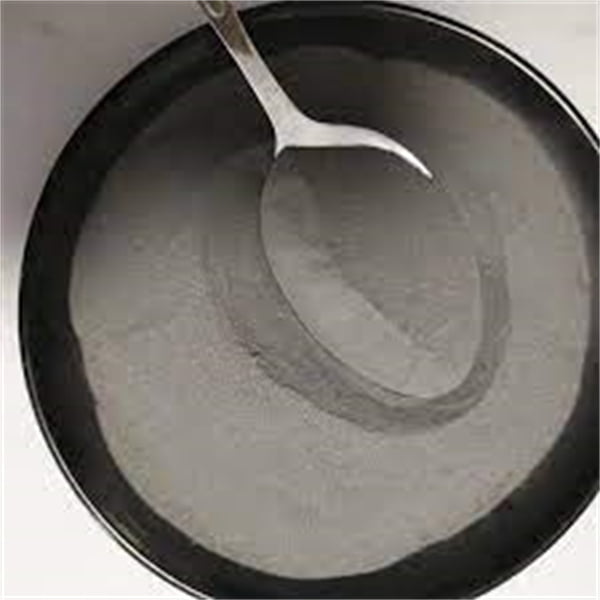
The Advantages of Binder Jetting
Binder jetting boasts a compelling list of advantages that make it a frontrunner in the 3D printing race. Let’s explore some of the most impactful benefits:
- Binder Jetting Has Fast Printing Speed: Compared to other metal additive manufacturing methods like laser sintering, binder jetting excels in speed. Its single-pass printing technology allows for the creation of hundreds of metal parts per day, significantly accelerating production times.
Imagine the implications for industries like aerospace and automotive, where rapid prototyping and low-volume production runs are crucial. Binder jetting cuts down on lead times, enabling companies to bring products to market faster and respond to evolving market demands with greater agility.
- The Cost of Binder Jetting is Low: Binder jetting offers a cost-effective approach to metal 3D printing. Here’s why:
- Reduced Material Waste: Unlike other techniques that require support structures, binder jetting utilizes the unbound powder bed as natural support. This minimizes material waste, a significant cost factor in metal additive manufacturing.
- Simplified Process: Binder jetting involves fewer processing steps compared to other methods, leading to lower overall production costs.
Think of it this way. With binder jetting, you’re not just printing parts; you’re printing efficiency. Reduced waste and streamlined processes translate to significant cost savings, making binder jetting an attractive option for companies seeking to optimize their production budgets.
- Binder Jetting Offers a Wide Range of Material Choices: One of the most exciting aspects of binder jetting is its versatility when it comes to materials. Unlike laser-based methods that struggle with certain materials due to high heat requirements, binder jetting operates at room temperature. This opens the door to a broader material selection, including:
- Stainless Steel: A popular choice for its excellent corrosion resistance and mechanical properties. Binder jetting allows for the creation of intricate stainless steel parts for applications ranging from medical implants to industrial components.
- Inconel: Renowned for its high-temperature strength and resistance to harsh environments, Inconel is ideal for parts used in jet engines, turbines, and other demanding applications.
- Tool Steel: Binder jetting enables the production of complex tool steel parts with good wear resistance, perfect for molds, dies, and cutting tools.
- Copper: This highly conductive metal finds applications in heat exchangers, electrical components, and more. Binder jetting opens doors for the creation of intricate copper parts with superior conductivity.
- Aluminum: Known for its lightweight yet strong properties, aluminum is a valuable material for aerospace, automotive, and consumer goods. Binder jetting allows for the creation of complex aluminum parts with excellent weight-to-strength ratios.
- Titanium: A biocompatible and high-strength metal, titanium is widely used in medical implants and aerospace components. Binder jetting facilitates the production of intricate titanium parts for demanding applications.
This diverse material selection empowers designers and engineers to create parts with the perfect properties for their specific needs. No longer are they limited by the constraints of traditional manufacturing methods.
- The Printing Size of Binder Jetting is Large: Binder jetting systems can accommodate large build volumes, allowing for the production of sizable metal parts in a single print run. This eliminates the need for complex assembly processes and reduces overall production time.
Imagine the possibilities for industries like construction and shipbuilding. Binder jetting can create large, one-piece components, streamlining the manufacturing process and potentially leading to lighter and more robust structures.
Beyond the Advantages: Considerations for Binder Jetting
While binder jetting offers a compelling array of benefits, it’s essential to consider some factors before diving headfirst:
- Post-Processing Requirements: Binder jetted parts typically require additional post-processing steps like infiltration and sintering to achieve their final properties. These steps can add to the overall production time and cost.
- Part Surface Finish: Binder jetted parts may have a slightly rougher surface finish compared to parts produced by other methods like machining. This might necessitate additional finishing processes depending on the application.
- Material Properties: The properties of binder jetted parts may not always be identical to those of traditionally manufactured parts due to factors like porosity and grain size. It’s crucial to carefully evaluate the material properties to ensure they meet the application requirements.
Binder Jetting vs. Other Metal Additive Manufacturing Methods
Here’s a quick comparison of binder jetting with other popular metal additive manufacturing methods:
Feature | Binder Jetting | Laser Sintering (SLM) | Electron Beam Melting (EBM) |
---|---|---|---|
Speed | Fastest | Moderate | Moderate |
Cost | Low to Moderate | Moderate to High | High |
Material Choice | Wide | Limited (high melting point materials) | Limited (high melting point materials) |
Build Volume | Large | Moderate | Moderate |
Surface Finish | Moderate | Good | Excellent |
Post-Processing | Required | Required | Required |
FAQ
Q: What are the limitations of binder jetting?
A: As discussed earlier, binder jetting involves post-processing steps that can add time and cost. Additionally, surface finish and material properties might require additional considerations depending on the application.
Q: Is binder jetting suitable for mass production?
A: Binder jetting excels in low-volume to medium-volume production runs. Its high speed and ability to print multiple parts simultaneously make it ideal for these scenarios. While true mass production might be better suited for traditional methods, binder jetting is continuously evolving and could potentially play a role in mass production in the future.
Q: What are some of the emerging applications of binder jetting?
A: Binder jetting is constantly pushing boundaries and finding applications in new and exciting areas. Here are a few examples:
- Customized Mass Production: Binder jetting’s ability to create complex geometries at high speeds makes it suitable for producing customized parts within a mass production setting. Imagine personalized sporting equipment, medical implants tailored to individual patients, or consumer electronics with unique features – all produced efficiently with binder jetting.
- Additive Manufacturing for Tooling: Binder jetting can be used to create complex tooling inserts and jigs at a fraction of the time and cost compared to traditional manufacturing methods. This enables rapid prototyping of tools and facilitates on-demand tool production, leading to increased flexibility and reduced lead times in manufacturing processes.
- Space Exploration: The lightweight and high-strength properties achievable with binder jetting make it ideal for creating components for spacecraft and satellites. Additionally, the ability to print complex geometries opens doors for the development of novel space exploration equipment.
- Cultural Heritage Preservation: Binder jetting can be used to reproduce historical artifacts and sculptures with incredible detail. This technology has the potential to revolutionize the way we preserve cultural heritage and make historical artifacts more accessible for study and education.
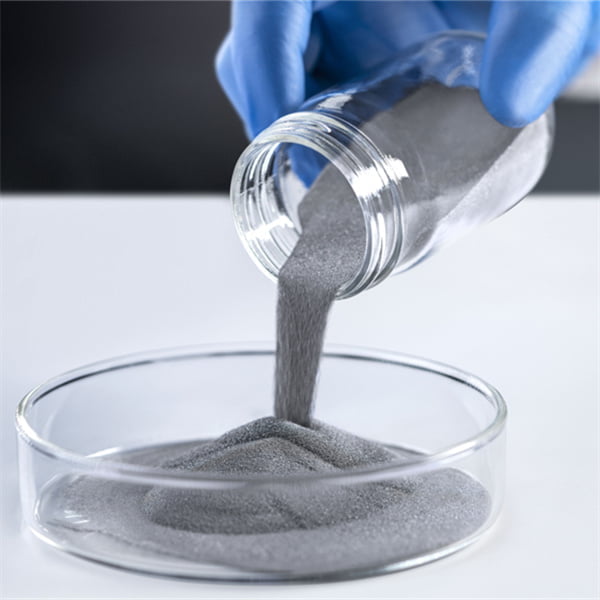
The Future of Binder Jetting: A Collaborative Effort
The future of binder jetting is bright, but it requires a collaborative effort from various stakeholders. Here’s what we can expect:
- Advancements in Material Science: Developing new metal powders specifically optimized for binder jetting will unlock even greater potential in terms of material properties and printability.
- Improved Post-Processing Techniques: Streamlining and potentially automating post-processing steps like infiltration and sintering will further reduce production time and cost, making binder jetting even more competitive.
- Software Enhancements: Advancements in 3D printing software will optimize printing parameters and support structures for binder jetting, leading to improved part quality and consistency.
- Wider Adoption and Integration: As the technology matures and its benefits become more widely recognized, binder jetting is poised for significant growth across various industries. We can expect increased integration of binder jetting into existing manufacturing workflows, leading to a more agile and efficient production landscape.
In Conclusion
Binder jetting is not just a metal additive manufacturing method; it’s a transformative technology poised to reshape the manufacturing landscape. Its unique combination of speed, affordability, and material versatility makes it a compelling choice for a wide range of applications. As the technology continues to evolve and overcome its limitations, binder jetting has the potential to revolutionize how we design, develop, and produce metal parts. So, buckle up and get ready for the exciting ride that binder jetting promises!
Share On
MET3DP Technology Co., LTD is a leading provider of additive manufacturing solutions headquartered in Qingdao, China. Our company specializes in 3D printing equipment and high-performance metal powders for industrial applications.
Inquiry to get best price and customized Solution for your business!
Related Articles
About Met3DP
Recent Update
Our Product
CONTACT US
Any questions? Send us message now! We’ll serve your request with a whole team after receiving your message.
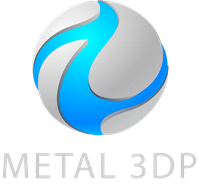
Metal Powders for 3D Printing and Additive Manufacturing