The Application of Binder Jetting in Automotive
Table of Contents
The automotive industry is in a constant state of flux, driven by a relentless pursuit of efficiency, performance, and lightweighting. Enter binder jetting, a revolutionary 3D printing technology poised to disrupt traditional manufacturing methods and redefine what’s possible under the hood. But what exactly is binder jetting, and how is it transforming the way we build cars? Buckle up, gearheads, because we’re about to take a deep dive into this fascinating technology.
Binder Jetting: Printing Parts, Not Just Ink
Imagine a 3D printer that doesn’t rely on melted plastic filament, but instead uses a fine powder as its building material. Binder jetting works precisely like this. A layer of metal powder, for example, is spread across a platform. Then, a print head selectively jets a binding agent onto the powder, adhering particles together according to a digital design. This process repeats layer by layer, gradually building up the desired 3D object. Finally, the unbound powder is removed, leaving behind a green part that undergoes a sintering process to achieve its final strength and density.
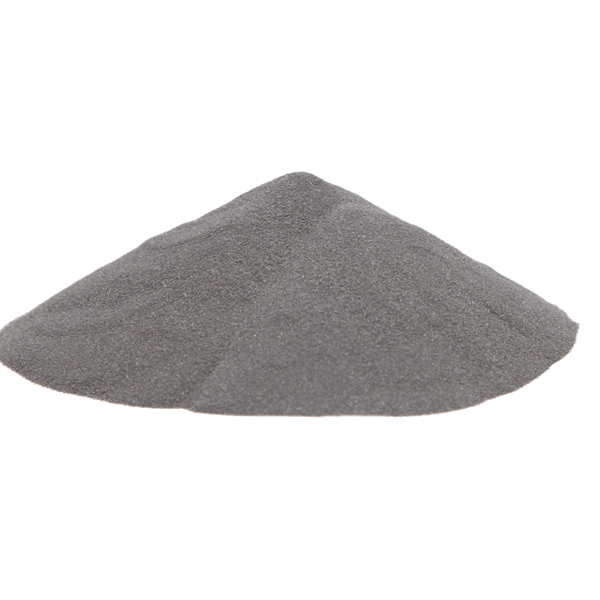
Binder Jetting Advantages for Automotive Applications
Binder jetting offers a compelling value proposition for automotive manufacturers seeking to streamline production and create innovative designs. Here are some key benefits:
- Mass Production Potential: Unlike traditional 3D printing technologies often limited to small batch runs, binder jetting can achieve production rates comparable to conventional methods. This paves the way for the high-volume manufacturing of complex automotive parts.
- Cost-Effectiveness: Compared to traditional casting or machining techniques, binder jetting can be more cost-effective, especially for intricate components. This is because it eliminates the need for expensive tooling and reduces material waste significantly.
- Design Freedom: Binder jetting shines in its ability to produce parts with intricate geometries and internal features. This opens doors for lightweight structures, improved cooling systems, and components with optimized performance characteristics.
- Material Versatility: Binder jetting isn’t limited to just a few materials. A wide range of metal powders can be used, tailored to specific performance requirements. Think of it as having a virtual toolbox of materials at your disposal.
10 Metal Powders for Binder Jetting
Now, let’s delve into the fascinating world of metal powders specifically formulated for binder jetting in automotive applications.
Metal Powder | Composition | Properties | Applications |
---|---|---|---|
Stainless Steel 316L | 16-18% chromium, 10-14% nickel, 2-3% molybdenum | Excellent corrosion resistance, high strength, biocompatible | Engine components, exhaust manifolds, body panels (luxury cars) |
Inconel 625 | Nickel-chromium superalloy with additions of molybdenum and niobium | High-temperature strength, oxidation resistance | Turbine blades, heat exchangers, exhaust manifolds (high-performance cars) |
Aluminum 6061 | Widely used aluminum alloy with magnesium and silicon | Lightweight, good strength-to-weight ratio, excellent machinability | Structural components, engine brackets, lightweight body panels |
Titanium Grade 2 | Pure titanium with excellent biocompatibility | High strength-to-weight ratio, excellent corrosion resistance | Prosthetic implants (racing seats), high-performance suspension components |
Maraging Steel | Nickel-steel alloy with high strength and low ductility after initial heat treatment | High strength-to-weight ratio, good dimensional stability | Critical suspension components, high-performance brake calipers |
Copper | Pure copper with excellent thermal conductivity | High electrical conductivity, good thermal conductivity | Heat exchangers, radiators, busbars (electric vehicles) |
Tool Steel (H13) | Chromium-molybdenum alloy steel | High wear resistance, good hot work tool steel | Dies, molds, tooling inserts for metal forming processes |
Nickel Alloy 718 | High-performance nickel-chromium alloy | Excellent strength at elevated temperatures, good corrosion resistance | Aerospace components (think lightweight, high-strength parts) |
Cobalt Chrome (CoCr) | Cobalt-chromium alloy with high strength and biocompatibility | Wear resistance, good corrosion resistance | Prosthetic implants (racing seats), gears (high-performance applications) |
Grey Cast Iron | Iron-carbon alloy with high silicon content | Good wear resistance, machinability | Engine blocks (low-volume, classic car restoration) |
the Technical Specifications Binder Jetting
While the concept of binder jetting might seem straightforward, the technical details behind achieving high-quality automotive parts involve a delicate interplay of various factors. Let’s explore some key aspects to consider:
- Powder Particle Size and Distribution: The size and distribution of the metal powder particles significantly impact the final properties of the printed part. Finer powders generally produce smoother surface finishes and potentially higher densities after sintering. However, finer powders can also lead to challenges in powder flow and potential issues with achieving uniform packing density. Conversely, larger particles can improve flow characteristics but might result in a rougher surface finish and potentially lower mechanical strength. Finding the optimal balance between particle size and distribution is crucial for achieving the desired outcome.
- Binder Selection and Jetting Process: The binder plays a critical role in holding the powder particles together during the printing process and influencing the final microstructure after sintering. Different types of binders exist, each with its own advantages and limitations. For instance, some binders might offer excellent adhesion but require a complex debinding process before sintering. Conversely, other binders might be easier to remove but might not provide sufficient strength during the printing stage. The jetting process itself, including factors like droplet size and jetting pattern, also influences the quality of the printed part. Optimizing both binder selection and the jetting process is essential for achieving consistent and reliable results.
- Sintering Parameters: Sintering is the final stage where the printed part is subjected to high temperatures, typically close to the melting point of the metal powder. This process allows the particles to bond together, densifying the part and achieving its final mechanical properties. Sintering parameters like temperature, time, and atmosphere significantly impact the final product. For instance, higher sintering temperatures generally lead to higher density and improved mechanical strength. However, excessively high temperatures can lead to grain growth and potential distortion of the part. Finding the optimal sintering parameters is crucial for achieving the desired balance between strength, density, and dimensional accuracy.
Applications of Binder Jetting in Automotive Manufacturing
Binder jetting isn’t just about revolutionizing engine components. Its potential extends far beyond the traditional realm of automotive manufacturing. Here are some exciting applications currently being explored:
- Lightweighting: The ability to create complex, near-net-shape components with metal powders opens doors for significant weight reduction in vehicles. This translates to improved fuel efficiency and potentially longer driving ranges for electric vehicles.
- Customization and On-Demand Manufacturing: Imagine a future where spare parts can be printed on-demand at dealerships or repair shops. Binder jetting’s potential for rapid prototyping and low-volume production makes this a distinct possibility.
- Performance Parts: The design freedom offered by binder jetting allows for the creation of intricate cooling channels and internal structures within components. This paves the way for the development of high-performance parts with optimized heat dissipation and improved efficiency.
- Classic Car Restoration: Binder jetting can be a game-changer for restoring classic cars. It allows for the replication of discontinued parts, ensuring the longevity of these automotive icons.
the Pros and Cons of Binder Jetting
While binder jetting offers a compelling array of benefits for automotive manufacturing, it’s important to acknowledge the technology’s current limitations:
- Post-Processing Requirements: Binder jetted parts often require additional post-processing steps, such as debinding and sintering, which can add to the overall production time and cost.
- Surface Finish: While advancements are being made, achieving a surface finish comparable to traditional machining techniques can still be a challenge with binder jetting.
- Material Availability: The availability of certain metal powders specifically formulated for binder jetting is still evolving. This can limit the range of applications for the technology in the short term.
The Future of Binder Jetting in Automotive Manufacturing
Despite these limitations, binder jetting is rapidly maturing and poised to play a transformative role in the automotive industry. Here’s a glimpse into what the future might hold:
- Advancements in Material Science: The development of new metal powders specifically optimized for binder jetting will expand the range of applications and improve the mechanical properties of printed parts.
- Integration with Automation: Binder jetting systems will become increasingly integrated with automation technologies like robotics, streamlining the production process and reducing reliance on manual labor.
- Hybrid Manufacturing Techniques: The potential for combining binder jetting with other additive manufacturing technologies, such as selective laser melting, could lead to the creation of parts with unique combinations of properties.
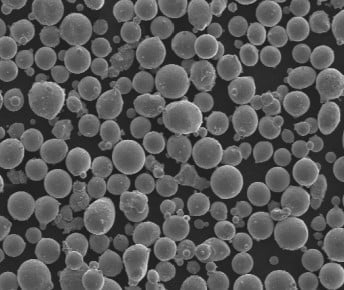
FAQs
In conclusion, binder jetting presents a revolutionary approach to automotive manufacturing, offering the potential for mass production, design freedom, and material versatility. As the technology continues to evolve, we can expect to see even more innovative applications emerge, shaping the future of vehicles and the way they are built. Here, we answer some frequently asked questions (FAQs) to shed further light on binder jetting in the automotive industry:
Q: Is binder jetting suitable for all automotive parts?
A: Not all automotive parts are ideal candidates for binder jetting at this stage. While the technology is rapidly advancing, some limitations still exist. Parts requiring extremely high surface finishes or those exposed to immense pressure might be better suited for traditional manufacturing methods for now. However, binder jetting excels at producing complex, lightweight components, making it a valuable tool for many applications.
Q: How does the cost of binder jetting compare to traditional manufacturing?
A: The cost equation for binder jetting is multifaceted. For complex, low-volume parts, binder jetting can be more cost-effective compared to traditional methods that require expensive tooling. Additionally, binder jetting often minimizes material waste, leading to cost savings. However, the post-processing requirements and potential limitations in surface finish can add to the overall cost. As the technology matures and production volumes increase, binder jetting is expected to become even more cost-competitive.
Q: How strong are parts made with binder jetting?
A: The strength of binder-jetted parts depends on several factors, including the chosen metal powder, sintering parameters, and post-processing techniques. Generally, binder-jetted parts can achieve mechanical properties comparable to their traditionally manufactured counterparts. Advancements in material science and sintering processes are continuously pushing the boundaries of achievable strength with binder jetting.
Q: Is binder jetting an environmentally friendly manufacturing process?
A: Binder jetting offers several environmental benefits. The technology significantly reduces material waste compared to traditional subtractive manufacturing methods. Additionally, binder jetting allows for the consolidation of multiple parts into a single, lighter component, which can improve fuel efficiency in vehicles.
Q: What are the safety considerations for using binder jetting in automotive applications?
A: As with any manufacturing process, safety is paramount. Similar to traditional metalworking techniques, binder jetting can involve hazards like dust inhalation and exposure to high temperatures during sintering. Implementing proper ventilation systems, using personal protective equipment, and adhering to safety protocols are crucial for ensuring a safe working environment.
Q: Where can I learn more about binder jetting for automotive applications?
A: Numerous resources are available to delve deeper into binder jetting. Reputable industry publications, research papers from universities and institutes, and websites of leading binder jetting equipment manufacturers are excellent starting points. Additionally, attending industry trade shows and conferences can provide valuable insights into the latest advancements and applications of this transformative technology.
By understanding the capabilities and limitations of binder jetting, automotive manufacturers can leverage this technology to create lighter, more efficient, and innovative vehicles. As the technology matures and production costs decrease, we can expect to see binder jetting play an increasingly significant role in shaping the future of the automotive landscape.
Share On
MET3DP Technology Co., LTD is a leading provider of additive manufacturing solutions headquartered in Qingdao, China. Our company specializes in 3D printing equipment and high-performance metal powders for industrial applications.
Inquiry to get best price and customized Solution for your business!
Related Articles
About Met3DP
Recent Update
Our Product
CONTACT US
Any questions? Send us message now! We’ll serve your request with a whole team after receiving your message.
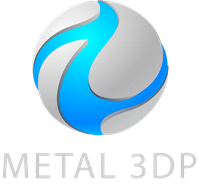
Metal Powders for 3D Printing and Additive Manufacturing