the Application of Binder jetting in Medical Devices
Table of Contents
Imagine a world where surgeons can hold a patient’s custom-made implant in their hands, perfectly designed to fit their unique anatomy. This isn’t science fiction; it’s the reality of binder jetting in medical devices. This innovative 3D printing technology is transforming the medical landscape, offering unprecedented possibilities for personalization, complexity, and affordability.
But before we dive into the exciting applications of binder jetting, let’s take a step back and understand how it works. Binder jetting utilizes a powder bed printing process. A print head selectively deposits a liquid binder onto thin layers of metal powder, gradually building the desired 3D object layer by layer. After printing, the part undergoes a debinding process to remove the binder, followed by sintering to fuse the metal particles, resulting in a strong and functional medical device.
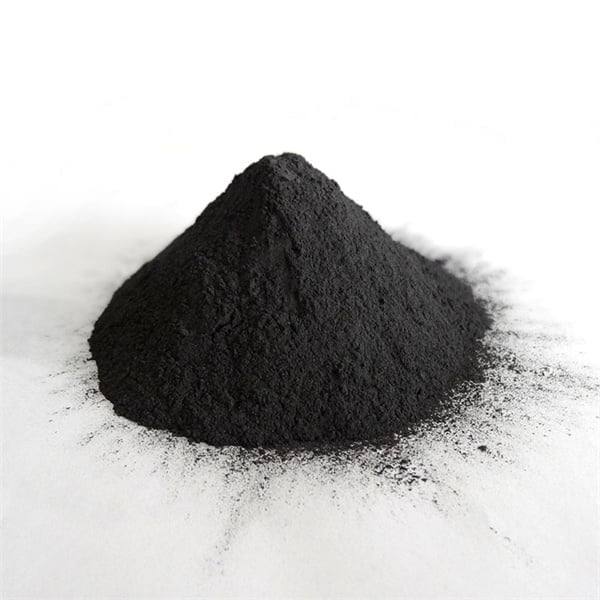
Metal Powders for Binder Jetting
The magic of binder jetting lies in the diverse metal powders it can utilize. Each powder offers unique properties, catering to specific medical device requirements. Here’s a closer look at 10 prominent metal powders used in binder jetting:
Metal Powder | Composition | Properties | Applications in Medical Devices |
---|---|---|---|
Stainless Steel 316L | 66-70% Iron, 16-18% Chromium, 2-3% Molybdenum, Nickel, Manganese, Silicon | Excellent corrosion resistance, biocompatible, high strength | Hip and knee implants, dental restorations, surgical instruments |
Titanium Grade 2 | 99% Titanium | High strength-to-weight ratio, excellent biocompatibility, osseointegration (bone bonding) | Cranioplasty implants, spinal implants, dental implants |
Cobalt Chrome (CoCr) | 60-65% Cobalt, 20-25% Chromium, 7-15% Molybdenum | High strength, wear resistance, good biocompatibility | Knee and hip joint replacements, dental prosthetics |
Nickel Chrome (NiCr) | 80% Nickel, 20% Chromium | High thermal stability, good corrosion resistance | Dental crowns and bridges, orthodontic appliances |
Inconel 625 | 61% Nickel, 21% Chromium, 9% Molybdenum, Iron, Manganese, Silicon | Exceptional high-temperature performance, corrosion resistance | Implants for extreme environments (e.g., bone near heat-generating devices) |
Tantalum | 100% Tantalum | Excellent biocompatibility, radiopaque (shows up on X-rays), good corrosion resistance | Cranial and facial implants, dental implants |
Molybdenum | 100% Molybdenum | High melting point, good electrical conductivity | Radiation shielding components in medical devices (e. g., X-ray machines) |
Tungsten | 100% Tungsten | Extremely high melting point, high density | Radiation shielding components in medical devices (e.g., cancer treatment equipment) |
Copper | 100% Copper | Excellent thermal conductivity, good electrical conductivity, antimicrobial properties | Heat sinks in medical devices, antimicrobial coatings for implants |
Maraging Steel | Iron, Nickel, Molybdenum, Titanium, Aluminum | High strength-to-weight ratio, good corrosion resistance, excellent toughness | Trauma fixation devices (e.g., plates and screws for bone fractures)
This table provides a glimpse into the vast potential of metal powders in binder jetting. From the workhorse stainless steel 316L to the exotic Inconel 625, each powder offers unique advantages for specific medical device applications.
Why Binder Jetting is Making Waves in Medical Devices
Binder jetting isn’t just another 3D printing technology; it’s a game-changer for medical device manufacturing. Here’s why:
- Unmatched Personalization: Imagine a surgeon holding a patient-specific knee implant, perfectly mirroring their unique anatomy. Binder jetting allows for the creation of highly customized medical devices, leading to improved implant fit, reduced surgery time, and potentially faster patient recovery.
- Complex Geometries Made Easy: Binder jetting excels at producing intricate geometries that traditional manufacturing methods might struggle with. This opens doors for the development of innovative medical devices with complex internal structures, potentially leading to improved functionality and performance.
- Cost-Effective Production: Compared to traditional techniques like machining or casting, binder jetting can be more cost-effective, especially for low-volume, complex medical devices. This translates to potentially lower costs for healthcare providers and patients.
Applications of Binder Jetting
The potential of binder jetting in medical devices isn’t just theoretical; it’s a reality shaping the future of healthcare. Let’s explore some of the most exciting applications:
Binder Jetting Can be Used to Manufacture Personalized Orthopedic Implants
Imagine a world where a patient walks into surgery with a custom-made hip implant, perfectly designed to fit their unique bone structure. This dream is becoming a reality with binder jetting. Unlike traditional “off-the-shelf” implants, binder jetting allows for the creation of highly customized implants that:
- Improve Implant Fit: Traditional implants often require surgeons to adapt the patient’s anatomy to fit the implant. Personalized implants, created using patient CT scans, offer a more precise fit, potentially reducing complications and improving long-term outcomes.
- Reduce Surgery Time: A perfect fit often translates to a shorter surgery time. With less bone modification needed, surgeons can potentially perform implant procedures faster, benefiting both patients and healthcare systems.
- Enhance Patient Recovery: A well-fitting implant can lead to a faster and more comfortable recovery for patients. Reduced pain and improved mobility can translate into a quicker return to daily activities.
Beyond hips, binder jetting holds immense promise for creating personalized implants for knees, shoulders, and other joints. This technology can revolutionize orthopedic surgery, leading to improved patient outcomes and a higher quality of life.
Binder Jetting Can be Used to Manufacture Personalized Surgical Instruments
Surgeons are the artists of the operating room, and their tools play a crucial role in the success of a procedure. Binder jetting is making waves by enabling the creation of:
- Custom Surgical Guides: Imagine a drill guide that perfectly aligns with a patient’s specific anatomy, ensuring precise implant placement during surgery. Binder jetting allows for the creation of such custom guides, potentially leading to improved surgical accuracy and reduced risk of complications.
- Patient-Specific Instrumentation: Complex surgeries often require specialized instruments. Binder jetting can be used to manufacture these instruments based on patient data, potentially improving surgical efficiency and minimizing tissue damage.
- Lightweight and Ergonomic Instruments: Binder jetting allows for the creation of lightweight instruments with complex internal structures. This can lead to improved ergonomics for surgeons, reducing fatigue and potentially enhancing surgical precision.
The ability to create personalized surgical instruments opens doors for a new era of minimally invasive surgery, benefiting both patients and surgeons.
Binder Jetting Can be Used to Manufacture Personalized Dental Restorations
A beautiful smile shouldn’t be a luxury. Binder jetting is transforming dentistry by enabling the creation of:
- Custom Dental Implants: Similar to orthopedic implants, binder jetting allows for the creation of personalized dental implants that perfectly match a patient’s jawbone anatomy. This can lead to improved implant stability and long-term success.
- Crown and Bridge Fabrication: Gone are the days of ill-fitting crowns. Binder jetting allows for the creation of highly customized crowns and bridges that offer a perfect fit and a natural look.
- Complex Orthodontic Appliances: Binder jetting can be used to manufacture intricate orthodontic appliances with precise geometries, potentially leading to faster and more effective orthodontic treatment.
The ability to create personalized dental restorations with binder jetting can revolutionize the field of dentistry, offering patients improved aesthetics, functionality, and comfort.
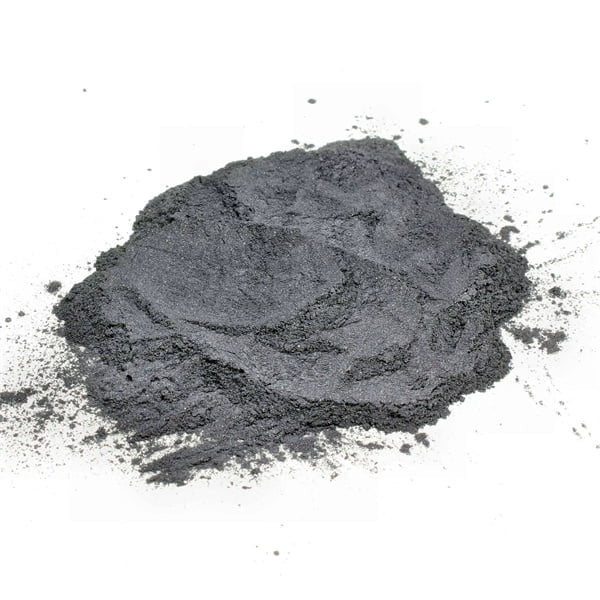
the Advantages and Limitations of Binder Jetting
Binder jetting offers a compelling case for medical device manufacturing, but like any technology, it has its own set of advantages and limitations:
Advantages:
- Unmatched Personalization: As discussed earlier, binder jetting excels at creating customized medical devices, leading to improved patient outcomes.
- Design Freedom: Binder jetting allows for the production of complex geometries, opening doors for innovative medical device designs.
- Cost-Effectiveness: For low-volume, complex medical devices, binder jetting can be a more cost-effective manufacturing option compared to traditional methods.
- Faster Time to Market: The rapid prototyping capabilities of binder jetting can significantly reduce the development time for new medical devices.
Limitations:
- Surface Roughness: Binder jetting can sometimes produce parts with a slightly rougher surface finish compared to other 3D printing techniques. However, post-processing techniques can mitigate this limitation.
- Material Availability: While the range of metal powders for binder jetting is expanding, it may not yet encompass all the materials used in traditional medical device manufacturing.
- Part Strength: The strength of parts produced by binder jetting can be slightly lower compared to some traditional manufacturing methods. However, advancements in technology are continuously improving the strength of binder-jetted parts.
Binder Jetting’s Impact on Medical Devices
The potential of binder jetting in medical devices stretches far beyond current applications. Here’s a glimpse into the exciting future this technology holds:
- Bioprinting with Binder Jetting: Imagine printing human tissues and organs for transplants! While still in its early stages, binder jetting is being explored for bioprinting applications. By combining metal powders with biocompatible materials like hydrogels and bioinks, scientists are working towards creating functional tissues and organs that could revolutionize transplant medicine.
- Microfluidics and Advanced Drug Delivery: Binder jetting’s ability to produce intricate geometries makes it ideal for creating microfluidic devices. These tiny channels can be used for controlled drug delivery, potentially leading to more targeted and effective treatment options.
- Medical Device Customization on Demand: Imagine a future where hospitals can print custom medical devices on-site based on a patient’s specific needs. Binder jetting’s potential for rapid prototyping and small-scale production opens doors for this possibility, leading to a more personalized approach to healthcare.
These are just a few examples of how binder jetting is poised to disrupt and redefine the medical device landscape. As research and development continue, we can expect even more innovative applications to emerge, pushing the boundaries of what’s possible in healthcare.
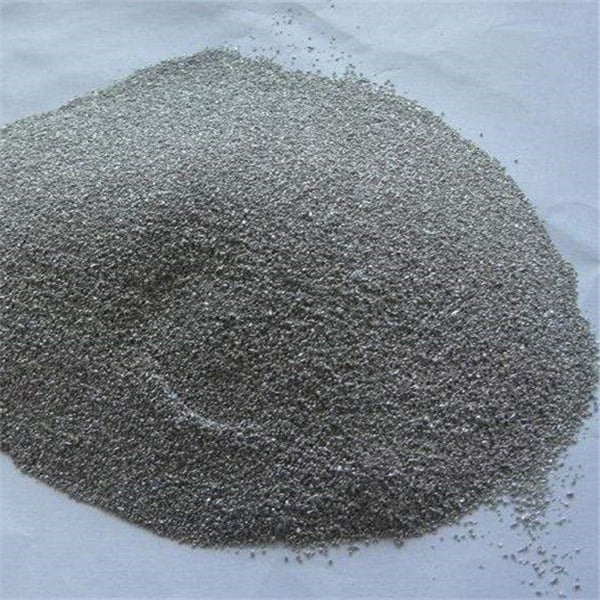
FAQ
Here are some of the most common questions regarding binder jetting in medical devices, answered in a clear and concise format:
Q: Is binder jetting safe for medical devices?
A: The safety of binder jetting for medical devices depends on the specific metal powder used and the post-processing techniques employed. However, many metal powders used in binder jetting are biocompatible, meaning they are well-tolerated by the human body. Additionally, stringent regulations govern medical device manufacturing, ensuring that all materials and processes meet safety standards.
Q: How strong are medical devices made with binder jetting?
A: The strength of binder-jetted medical devices depends on the chosen metal powder and the sintering process. While some may have slightly lower strength compared to traditionally manufactured counterparts, advancements in technology are continuously improving the strength of these parts. Additionally, for many medical device applications, the strength offered by binder jetting is more than sufficient.
Q: Is binder jetting cost-effective for medical devices?
A: For low-volume, complex medical devices, binder jetting can be a more cost-effective option compared to traditional manufacturing methods like machining or casting. This is because binder jetting eliminates the need for expensive tooling and allows for on-demand production. However, for high-volume, simpler devices, traditional methods might still be more cost-effective.
Q: What are the environmental benefits of binder jetting for medical devices?
A: Binder jetting offers some potential environmental benefits compared to traditional manufacturing techniques. It can minimize material waste by allowing for near-net-shape production and reducing the need for subtractive processes like machining. Additionally, binder jetting can potentially lead to more localized manufacturing, reducing transportation emissions.
Q: What is the future of binder jetting in medical devices?
A: The future of binder jetting in medical devices is bright. As the technology matures, we can expect to see wider adoption, development of new metal powders with tailored properties, and potentially even bioprinting applications. Binder jetting has the potential to revolutionize medical device manufacturing, leading to a new era of personalized, efficient, and cost-effective healthcare solutions.
Share On
MET3DP Technology Co., LTD is a leading provider of additive manufacturing solutions headquartered in Qingdao, China. Our company specializes in 3D printing equipment and high-performance metal powders for industrial applications.
Inquiry to get best price and customized Solution for your business!
Related Articles
About Met3DP
Recent Update
Our Product
CONTACT US
Any questions? Send us message now! We’ll serve your request with a whole team after receiving your message.
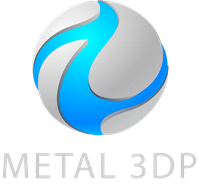
Metal Powders for 3D Printing and Additive Manufacturing