BNi-6: The Powerhouse for High-Temperature Brazing
Table of Contents
Brazing, the magical process of joining metals using a molten filler material, takes center stage in countless industries. But what if the heat gets cranked up, and your standard brazing alloys start to wilt? Enter BNi-6, a nickel-based brazing powerhouse that thrives in high-temperature environments.
This article delves into the world of BNi-6, exploring its composition, properties, applications, and even dissecting some of the leading metal powder models available. So, buckle up and get ready to unlock the secrets of brazing with BNi-6!
Understanding BNi-6: A Compositional Breakdown
BNi-6 is a eutectic nickel-based brazing alloy, meaning its elements combine to form a uniform melting point. Here’s a peek at the key players in its composition:
- Nickel (Ni): The dominant force, nickel provides the foundation for BNi-6’s strength and high-temperature resistance.
- Phosphorus (P): This element acts as a flow agent, ensuring the molten BNi-6 wets the base metals effectively, creating a strong bond.
While the exact percentages can vary slightly between manufacturers, BNi-6 typically consists of around 88-92% nickel and 8-12% phosphorus, with trace amounts of other elements like silicon or boron.
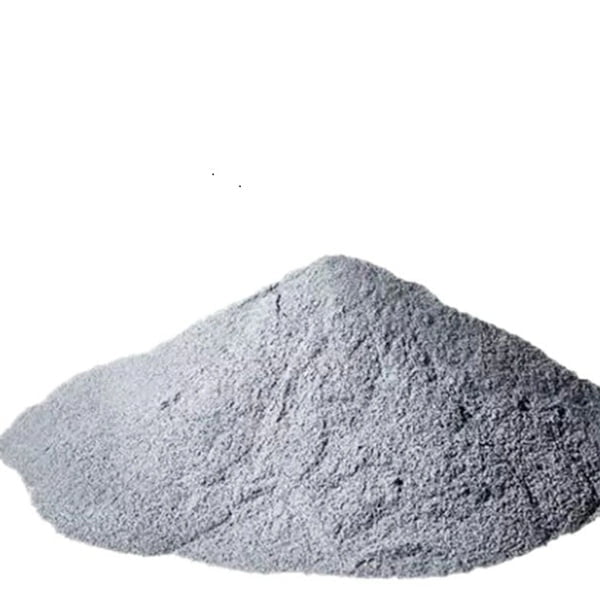
The Powerhouse Properties of BNi-6
Now that you know what’s inside, let’s explore the impressive properties that make BNi-6 a champion in the brazing arena:
- High-Temperature Brazing: BNi-6 boasts a brazing temperature range of 930°C to 1090°C (1700°F to 2000°F). This makes it ideal for applications where traditional silver-based brazing alloys simply can’t handle the heat.
- Exceptional Strength: Even at elevated temperatures, BNi-6 joints maintain excellent mechanical strength. Imagine brazing turbine components that need to withstand intense heat and pressure – BNi-6 is your go-to solution!
- Outstanding Oxidation Resistance: BNi-6 stands strong against the destructive effects of oxidation at high temperatures. This is crucial for applications where components are exposed to hot, oxygen-rich environments.
- Good Corrosion Resistance: Many brazing alloys struggle with corrosion, but BNi-6 offers a decent level of resistance, making it suitable for use in mildly corrosive environments.
- Excellent Flow Characteristics: The presence of phosphorus ensures that BNi-6 flows smoothly during brazing, filling tight gaps and creating strong, capillary action-driven bonds.
Where Does BNi-6 Shine? Unveiling its Applications
BNi-6’s unique properties translate into a diverse range of applications across various industries. Here are some prime examples:
- Aerospace: From jet engine components to rocket assemblies, BNi-6 brazes high-temperature alloys used in the brutal aerospace environment.
- Power Generation: Turbines, heat exchangers, and other power generation equipment rely on BNi-6 for strong, reliable brazing joints that can withstand extreme temperatures.
- Chemical Processing: BNi-6 tackles the challenges of brazing in chemical processing equipment, where corrosion resistance is a must.
- Heat Exchangers: BNi-6 ensures leak-proof, high-performance brazing in heat exchangers operating at elevated temperatures.
- Medical Devices: When it comes to joining components in medical devices that need to function flawlessly, BNi-6’s combination of strength and corrosion resistance makes it a compelling choice.
Beyond these core applications, BNi-6 finds its way into various other industries, including:
- Automotive (exhaust systems)
- Electronics (high-temperature components)
- Oil and Gas (equipment exposed to high temperatures)
the Leading Metal Powder Models of BNi-6
With BNi-6 gaining traction, several manufacturers offer metal powder models for brazing applications. Let’s delve into some of the key players:
1. Höganäs BrazeLet® BNi-6: This spherical nickel-based brazing powder boasts excellent flow characteristics, making it ideal for intricate brazing jobs.
2. Sandvik SAF 518 (BNi-6): Renowned for its high-quality standards, Sandvik’s BNi-6 powder offers consistent performance and reliable results.
3. AMI Metals BNi-6: Providing a cost-effective option, AMI Metals’ BNi-6 powder caters to applications where budget is a major consideration.
4. Carpenter® Pyrobraz® 180 (BNi-6): This BNi-6 powder from Carpenter Brothers is known for its excellent oxidation resistance, making it a strong contender for applications in harsh environments.
5. Materion BrazeCoat® 5500 (BNi-6): Materion’s BNi-6 powder comes in various forms, including paste and preforms, offering brazing flexibility for diverse needs.
6. Bodycote Wall Colmonoy® Colmonoy® 557 (BNi-6): Wall Colmonoy’s BNi-6 powder caters to the brazing requirements of the gas turbine industry, delivering exceptional performance.
7. Special Metals Corporation AtomFlo® 617 (BNi-6): This BNi-6 powder from Special Metals Corporation boasts a tight particle size distribution, ensuring optimal flow and capillary action during brazing.
8. Gusmer™ Ni-P BNi-6: Gusmer’s BNi-6 powder prioritizes affordability while maintaining good overall brazing performance.
9. PlasmaTech BNi-6: PlasmaTech’s BNi-6 powder is specifically designed for plasma brazing applications, offering compatibility with this advanced joining technique.
10. Metco (Sulzer) Metco 180 (BNi-6): Metco, a Sulzer brand, offers a BNi-6 powder known for its consistent quality and suitability for various brazing processes.
Choosing the Right BNi-6 Metal Powder Model
With this diverse array of BNi-6 metal powder models, selecting the right one becomes crucial. Here are some key factors to consider:
- Application Requirements: The specific demands of your brazing project will dictate the most suitable BNi-6 powder. Consider factors like brazing temperature, desired joint strength, and corrosion resistance needs.
- Particle Size and Distribution: The size and distribution of the powder particles significantly impact flow characteristics and brazeability. Choose a powder with a particle size range that aligns with your joint geometry and brazing process.
- Manufacturer Reputation: Opting for a reputable manufacturer ensures consistent quality and reliable brazing performance. Research the manufacturer’s experience and expertise in BNi-6 powder production.
- Cost Considerations: BNi-6 powder can vary in price depending on the manufacturer and specific features. Balance cost with the desired performance level for your application.
Beyond these core factors, additional considerations may include:
- Powder Form (e.g., powder, paste, preforms): Choose the form that best suits your brazing application and equipment.
- Availability: Ensure the BNi-6 powder you choose is readily available from a reliable supplier.
Remember, consulting with a brazing expert can be invaluable when selecting the optimal BNi-6 metal powder model for your specific needs.
The Pros and Cons of BNi-6
Like any material, BNi-6 has its own set of advantages and limitations. Let’s weigh them to understand where it shines and where alternatives might be more suitable.
Advantages of BNi-6 Brazing Powder:
- Exceptional High-Temperature Performance: BNi-6 tackles brazing tasks where other alloys simply can’t handle the heat.
- Superior Strength: Even at elevated temperatures, BNi-6 joints maintain excellent mechanical strength, crucial for demanding applications.
- Outstanding Oxidation Resistance: BNi-6 stands strong against oxidation, making it ideal for hot, oxygen-rich environments.
- Decent Corrosion Resistance: While not its strongest suit, BNi-6 offers sufficient corrosion resistance for mildly corrosive environments.
- Excellent Flow Characteristics: BNi-6 flows smoothly, filling tight gaps and creating strong capillary action-driven bonds.
Limitations of BNi-6 Brazing Powder:
- Higher Cost: Compared to traditional silver-based brazing alloys, BNi-6 can be more expensive.
- Brittleness: At room temperature, BNi-6 joints can exhibit some degree of brittleness. Consider this if your application requires significant post-brazing deformation.
- Health Considerations: During brazing, BNi-6 can generate fumes that require proper ventilation and personal protective equipment (PPE).
By understanding these pros and cons, you can make an informed decision about whether BNi-6 is the ideal brazing solution for your project.
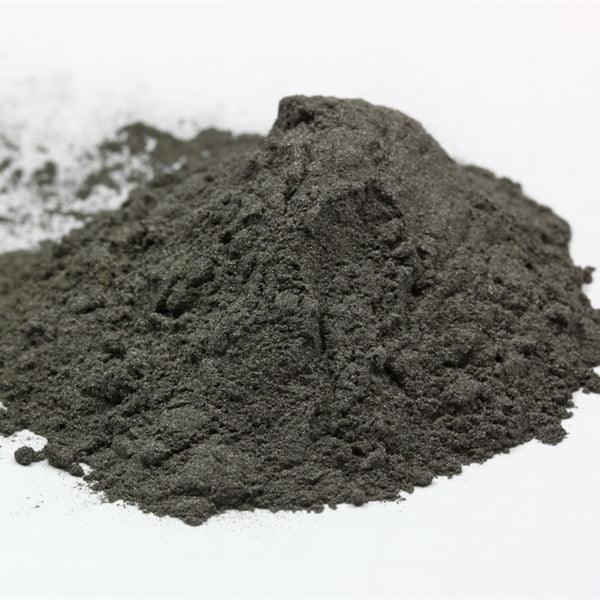
FAQs
The world of BNi-6 brazing powder can spark many questions. Let’s explore some of the most frequently asked ones:
Q: What are some alternatives to BNi-6 brazing powder?
While BNi-6 reigns supreme in high-temperature brazing, alternatives exist depending on your specific needs:
- Silver-based brazing alloys: For lower temperature applications (up to around 800°C/1472°F), silver-based alloys offer a more cost-effective option with good strength and flow characteristics.
- Nickel-chromium brazing alloys: These alloys provide a balance between high-temperature performance (up to around 1200°C/2192°F) and affordability compared to BNi-6. However, their oxidation resistance might be lower.
- Copper-based brazing alloys: If you’re brazing copper or copper alloys at moderate temperatures (up to around 700°C/1292°F), copper-based brazing alloys can be a suitable choice.
Q: What safety precautions should I take when using BNi-6 brazing powder?
BNi-6 brazing, like any brazing process, requires proper safety measures:
- Ventilation: Ensure adequate ventilation to remove fumes generated during brazing. Local exhaust ventilation is highly recommended.
- Personal Protective Equipment (PPE): Wear appropriate PPE, including safety glasses, gloves, and a respirator suitable for brazing fumes.
- Training: Proper training on safe brazing practices, including BNi-6 handling, is crucial.
Q: How do I store BNi-6 brazing powder?
Store BNi-6 brazing powder in a cool, dry place in a sealed container to prevent moisture absorption, which can affect its flow characteristics.
Q: Can BNi-6 brazing powder be used with different brazing techniques?
Yes, BNi-6 brazing powder is compatible with various brazing techniques, including torch brazing, furnace brazing, and induction brazing. The optimal technique depends on your specific application and joint geometry.
Q: Where can I buy BNi-6 brazing powder?
BNi-6 brazing powder is available from a variety of welding and brazing supply companies. Research reputable suppliers in your area or online to find the best pricing and selection.
By understanding these FAQs, you’re well on your way to leveraging the power of BNi-6 brazing powder for your next high-temperature joining project!
In Conclusion
BNi-6 brazing powder emerges as a game-changer for tackling high-temperature joining challenges. Its exceptional performance at elevated temperatures, impressive strength, and decent corrosion resistance make it a compelling choice for various industries. While factors like cost and brittleness require consideration, BNi-6 stands tall as a reliable solution for demanding brazing applications. So, the next time your project demands brazing under scorching conditions, remember BNi-6 – the nickel-based powerhouse ready to take the heat!
Share On
MET3DP Technology Co., LTD is a leading provider of additive manufacturing solutions headquartered in Qingdao, China. Our company specializes in 3D printing equipment and high-performance metal powders for industrial applications.
Inquiry to get best price and customized Solution for your business!
Related Articles
About Met3DP
Recent Update
Our Product
CONTACT US
Any questions? Send us message now! We’ll serve your request with a whole team after receiving your message.
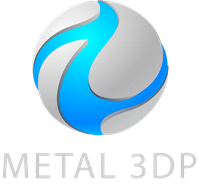
Metal Powders for 3D Printing and Additive Manufacturing