The Centrifugal Atomization Process
Table of Contents
Centrifugal atomization is a fascinating and complex process that plays a pivotal role in creating high-quality metal powders. These powders are essential in various industries, from aerospace to medical devices, due to their unique properties and applications. Let’s delve into the intricacies of the centrifugal atomization process, explore its applications, and review specific metal powder models.
Overview of the Centrifugal Atomization Process
Centrifugal atomization is a method used to produce metal powders by melting a metal and then dispersing it into fine droplets through centrifugal force. This technique is known for its efficiency in creating uniformly sized particles with desirable properties for industrial applications.
How Does Centrifugal Atomization Work?
The process begins with the metal being heated until it reaches a molten state. The molten metal is then introduced to a rapidly rotating disc or cup, which flings the metal outward due to centrifugal force. As the metal is ejected, it breaks up into tiny droplets that solidify into fine powders. The size and shape of these particles can be controlled by adjusting various parameters, such as the rotation speed and the temperature of the metal.
Key Benefits of Centrifugal Atomization
- Uniform Particle Size: Produces powders with consistent particle sizes, which is critical for applications requiring precise measurements.
- High Purity: Reduces contamination and produces high-purity metal powders.
- Versatility: Can be used with a wide range of metals and alloys.
- Efficiency: Capable of producing large quantities of powder in a relatively short time.
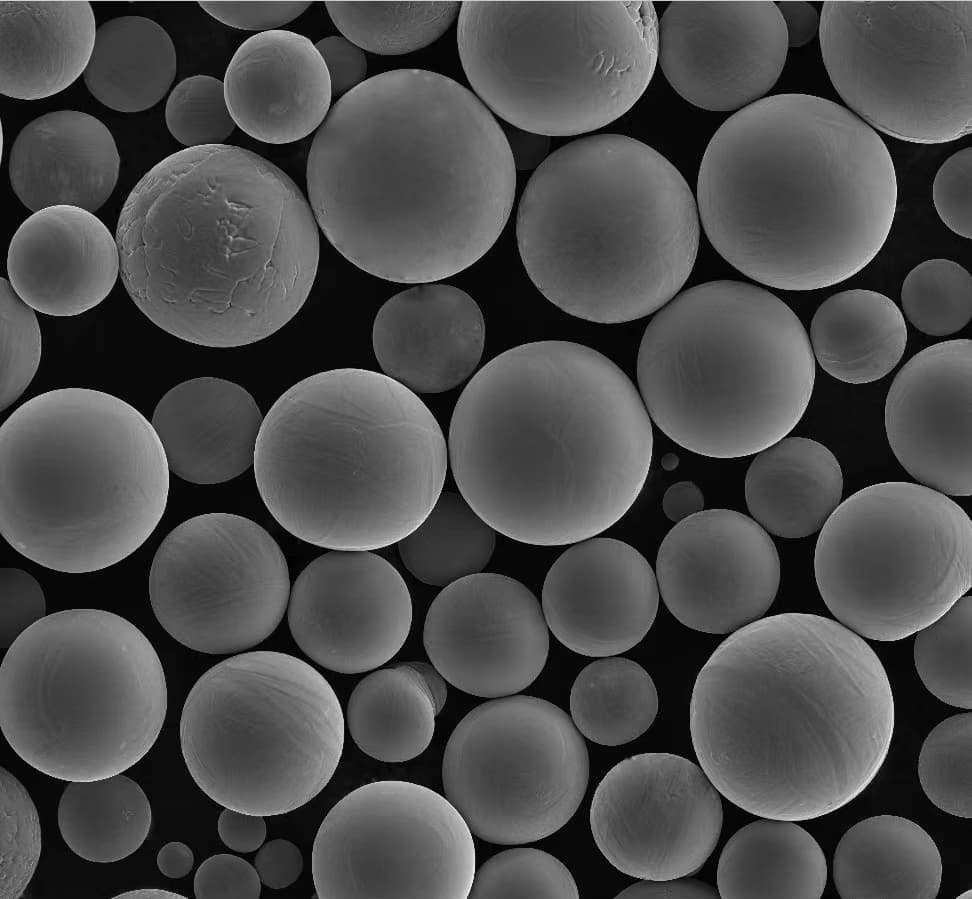
Detailed Breakdown of Centrifugal Atomization Process Parameters
Parameter | Description |
---|---|
Rotation Speed | Higher speeds produce finer particles. |
Temperature | Optimal temperatures ensure proper melting and solidification. |
Metal Type | Different metals require specific conditions for optimal atomization. |
Atomization Environment | Controlled atmosphere (e.g., inert gas) to prevent oxidation and contamination. |
Disc/Cup Design | Specific designs influence particle size and distribution. |
Feed Rate | The rate at which molten metal is fed onto the rotating disc affects particle formation. |
Applications of Centrifugal Atomization Process
Centrifugal atomization is employed in various industries due to its ability to produce high-quality metal powders with tailored properties. Here are some key applications:
Industry | Application |
---|---|
Aerospace | Production of lightweight, high-strength components for aircraft and spacecraft. |
Medical Devices | Creation of biocompatible materials for implants and prosthetics. |
Automotive | Manufacturing of durable and efficient parts for engines and transmissions. |
Additive Manufacturing | Supply of powders for 3D printing and other advanced manufacturing techniques. |
Electronics | Production of conductive materials for electronic components. |
Specifications, Sizes, Grades, and Standards of Metal Powders
The specifications of metal powders produced through centrifugal atomization vary depending on the intended application and the metal used. Here is a detailed table outlining common specifications:
Metal Powder | Particle Size (µm) | Purity (%) | Density (g/cm³) | Standard |
---|---|---|---|---|
Aluminum (Al) | 10-100 | 99.9 | 2.70 | ASTM B 928 |
Titanium (Ti) | 15-150 | 99.5 | 4.50 | ASTM F 1580 |
Nickel (Ni) | 20-200 | 99.7 | 8.90 | ISO 4506 |
Copper (Cu) | 10-90 | 99.9 | 8.96 | ASTM B 964 |
Stainless Steel | 25-250 | 99.8 | 7.80 | ASTM B 212 |
Cobalt (Co) | 20-150 | 99.6 | 8.90 | ISO 8492 |
Iron (Fe) | 5-100 | 99.5 | 7.86 | ASTM A 809 |
Magnesium (Mg) | 20-180 | 99.9 | 1.74 | ASTM B 403 |
Zinc (Zn) | 10-120 | 99.7 | 7.14 | ASTM B 875 |
Gold (Au) | 1-50 | 99.99 | 19.32 | ASTM B 558 |
Suppliers and Pricing Details of Metal Powders
The market for metal powders is vast, with numerous suppliers offering various products at different price points. Below is a table highlighting some of the key suppliers and their pricing details:
Supplier | Metal Powder | Price (USD/kg) | Minimum Order Quantity (kg) | Location |
---|---|---|---|---|
Advanced Powders | Aluminum | 50 | 10 | USA |
Metalco Industries | Titanium | 200 | 5 | Germany |
NiTech Metals | Nickel | 100 | 20 | Canada |
CuPower Inc. | Copper | 75 | 15 | China |
SteelForm Ltd. | Stainless Steel | 80 | 25 | UK |
CoMetals | Cobalt | 150 | 10 | South Korea |
IronTech | Iron | 40 | 50 | India |
MagPower | Magnesium | 60 | 30 | USA |
ZnProducers | Zinc | 45 | 20 | Mexico |
Golden Metals | Gold | 6000 | 1 | Switzerland |
Comparing Pros and Cons of Centrifugal Atomization
When considering the centrifugal atomization process for metal powder production, it’s essential to weigh its advantages against its limitations.
Advantages | Disadvantages |
---|---|
High Purity: Minimal contamination risks. | Cost: High initial setup and equipment costs. |
Uniform Particle Size: Consistent product quality. | Complexity: Requires precise control of parameters. |
Versatility: Applicable to a wide range of metals. | Maintenance: Regular maintenance of equipment is necessary. |
Efficiency: Rapid production rates. | Energy Consumption: High energy usage during the process. |
Specific Metal Powder Models and Descriptions
To provide a clearer picture, let’s explore ten specific metal powder models produced through centrifugal atomization:
- Aluminum Alloy 6061 Powder
- Description: Ideal for lightweight structural components with good mechanical properties.
- Applications: Aerospace parts, automotive frames, and bicycle components.
- Titanium Grade 5 Powder
- Description: Known for its high strength, low density, and excellent corrosion resistance.
- Applications: Medical implants, aerospace fasteners, and sporting goods.
- Nickel Alloy 625 Powder
- Description: Offers outstanding resistance to oxidation and corrosion at high temperatures.
- Applications: Marine applications, chemical processing, and aerospace engines.
- Copper Powder
- Description: High electrical and thermal conductivity make it perfect for electronic applications.
- Applications: Electrical contacts, heat exchangers, and 3D printing.
- Stainless Steel 316L Powder
- Description: Provides excellent corrosion resistance and mechanical properties.
- Applications: Medical devices, food processing equipment, and marine components.
- Cobalt-Chromium Alloy Powder
- Description: Superior wear resistance and biocompatibility.
- Applications: Dental implants, orthopedic implants, and high-performance engine parts.
- Iron Powder
- Description: Used in various industrial applications for its magnetic properties and reactivity.
- Applications: Powder metallurgy, magnetic materials, and chemical catalysts.
- Magnesium Alloy AZ31 Powder
- Description: Combines lightweight properties with good strength and corrosion resistance.
- Applications: Aerospace components, automotive parts, and portable electronic devices.
- Zinc Powder
- Description: Essential for galvanizing steel and producing zinc-rich paints.
- Applications: Corrosion protection coatings, batteries, and pharmaceuticals.
- Gold Powder
- Description: High purity gold powder for specialized applications requiring superior conductivity and resistance.
- Applications: Electronics, jewelry manufacturing, and dental restorations.
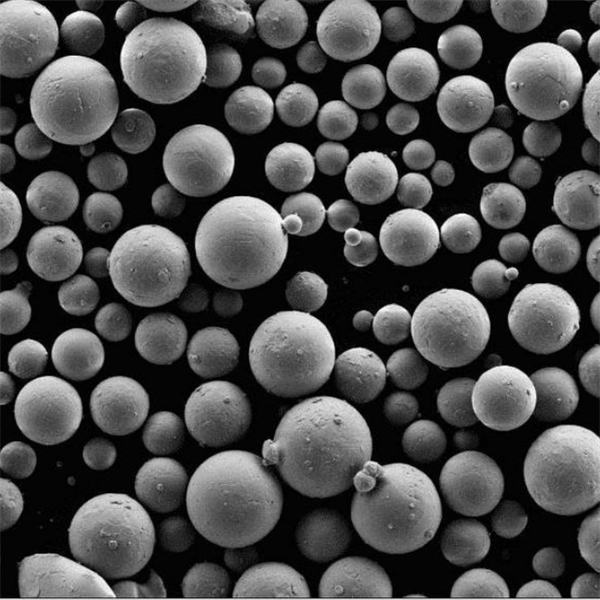
FAQ
To address common questions and concerns, here is a comprehensive FAQ section:
What is centrifugal atomization?
Centrifugal atomization is a process for turning molten metal into a fine powder. Molten metal is poured onto a rapidly spinning disc. The centrifugal force throws the metal off the disc in tiny droplets that solidify into metal powder particles.
What are the advantages of centrifugal atomization?
- Production rate: Centrifugal atomization can produce metal powder at a faster rate than other methods like gas atomization.
What are the disadvantages of centrifugal atomization?
- Particle size and shape control: Centrifugal atomization offers less control over the final size and shape of the powder particles compared to other methods.
What are some applications of centrifugally atomized powders?
Centrifugally atomized powders are used in many applications including:
- 3D printing
- Metal injection molding
- Brazing
- Welding
- Thermal spraying
How does centrifugal atomization compare to other atomization processes?
There are several other methods for atomizing metal. Here’s a brief comparison of centrifugal atomization to a common alternative:
- Gas atomization: Inert gas is used to break up a stream of molten metal into droplets. This method offers greater control over particle size and shape, but has slower production rates.
Share On
MET3DP Technology Co., LTD is a leading provider of additive manufacturing solutions headquartered in Qingdao, China. Our company specializes in 3D printing equipment and high-performance metal powders for industrial applications.
Inquiry to get best price and customized Solution for your business!
Related Articles
About Met3DP
Recent Update
Our Product
CONTACT US
Any questions? Send us message now! We’ll serve your request with a whole team after receiving your message.
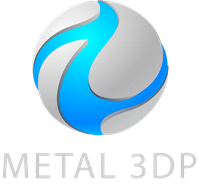
Metal Powders for 3D Printing and Additive Manufacturing