3D Metal Powders Produced by Chemical vapor deposition
Table of Contents
Imagine crafting intricate structures layer by layer, atom by atom, using the power of chemistry. This is the essence of Chemical Vapor Deposition (CVD), a technology transforming the world of materials science, particularly in the realm of metal powders.
What is Chemical Vapor Deposition (CVD)?
Think of CVD as a sophisticated painting technique, but instead of pigments, it utilizes gaseous precursors that decompose and deposit metal atoms onto a substrate, building a three-dimensional structure. This controlled deposition allows for the creation of highly pure, fine-grained, and precisely shaped metal powders with unique properties.
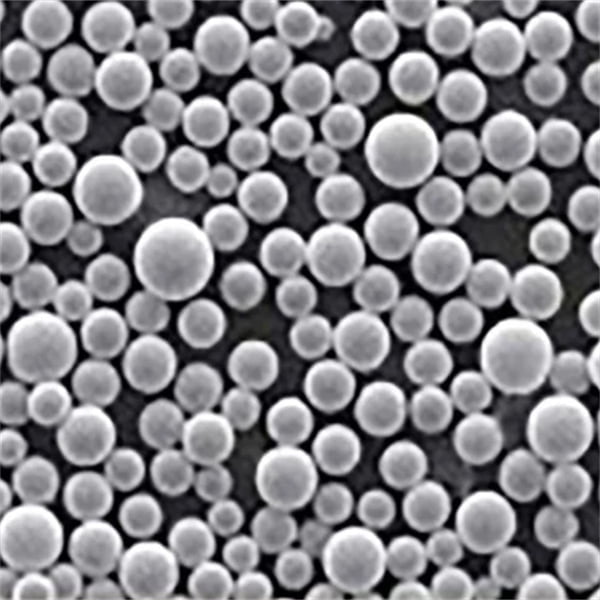
The Type of Metal Powders Produced by Chemical Vapor Deposition
CVD boasts the ability to produce a diverse spectrum of metal powders, each with its own set of characteristics and applications. Let’s delve into the fascinating world of some prominent examples:
- Tungsten (W): Renowned for its exceptional high melting point, strength, and resistance to corrosion, tungsten powder is a champion in various industries. It finds applications in incandescent light bulb filaments, welding electrodes, and armor-piercing projectiles. Additionally, its intricate structures like nanowires and nanotubes have opened doors in fields like electronics and catalysis.
- Molybdenum (Mo): Sharing similarities with tungsten, molybdenum powder offers excellent high-temperature strength and corrosion resistance. It plays a crucial role in aerospace components, heat sinks, and electrical contacts.
- Rhenium (Re): Often used in conjunction with tungsten due to its similar properties, rhenium powder further enhances strength and high-temperature performance. It finds applications in jet engine components, turbine blades, and filaments for high-performance lighting.
- Tantalum (Ta): A champion of corrosion resistance and biocompatibility, tantalum powder is widely used in medical implants, capacitors, and chemical processing equipment. Its ability to withstand harsh environments makes it irreplaceable in specific applications.
- Nickel (Ni): A versatile metal, nickel powder finds applications in a diverse range of fields. Its excellent magnetic properties make it valuable in electromagnets, batteries, and catalysts. Furthermore, its corrosion resistance makes it suitable for marine and chemical engineering applications.
- Cobalt (Co): Known for its magnetic properties and high-temperature strength, cobalt powder plays a vital role in permanent magnets, cutting tools, and wear-resistant coatings. Its ability to retain magnetism at high temperatures makes it crucial for various technological advancements.
- Iron (Fe): The most abundant metal on Earth, iron powder has transformed various industries. It is widely used in powder metallurgy, for creating magnetic cores in transformers, and in friction materials for brakes. Its affordability and versatility make it a cornerstone of various applications.
- Copper (Cu): Renowned for its excellent electrical conductivity and thermal conductivity, copper powder has diverse applications in electronics, heat sinks, and conductive coatings. Its ability to efficiently transfer heat and electricity makes it a key player in various technological advancements.
- Titanium (Ti): Valued for its exceptional strength-to-weight ratio, corrosion resistance, and biocompatibility, titanium powder is extensively used in aerospace components, medical implants, and sporting goods. Its unique combination of properties makes it a highly sought-after material in demanding environments.
- Niobium (Nb): Often used in alloys with other metals, niobium powder offers high strength and superconductivity at low temperatures. It finds applications in jet engines, superconducting magnets, and nuclear reactors. Its ability to withstand extreme conditions makes it valuable for advanced technological applications.
A Glimpse into the Applications of CVD Metal Powders
The unique properties of CVD metal powders translate into a vast array of applications across various industries:
Industry | Applications |
---|---|
Electronics | Capacitors, electrical contacts, heat sinks |
Aerospace | Jet engine components, turbine blades, rocket nozzles |
Medical | Implants, surgical instruments, dental fillings |
Automotive | Catalytic converters, fuel injectors, engine components |
Chemical Processing | Reactors, pumps, valves |
Construction | Building materials, coatings, fasteners |
Energy | Solar cells, fuel cells, batteries |
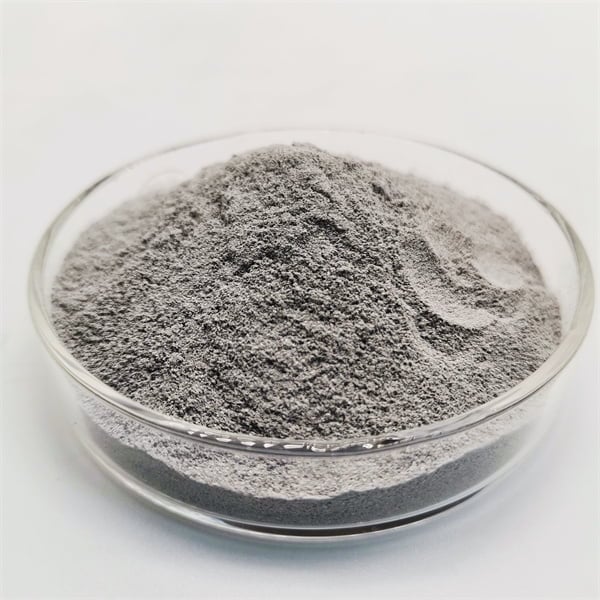
Specifications, Sizes, and Grades of CVD Metal Powders
CVD metal powders come in a variety of specifications, catering to diverse application needs.
Parameter | Description |
---|---|
Particle size | Typically ranges from nanometers to micrometers, offering precise control over material properties. |
Purity | Can reach up to 99.99% for specific applications |
Grades vary depending on the metal and desired properties, often including:
- Standard grade: General-purpose applications requiring good overall quality.
- High-purity grade: Demanding applications where purity is critical, like electronics and medical implants.
- Spherical grade: Offers superior flowability and packing density, valuable in powder metallurgy applications.
Pricing and Suppliers of CVD Metal Powders
The cost of CVD metal powders varies significantly depending on the specific metal, purity, quantity, and desired specifications. Generally, higher purity and finer particle sizes lead to higher prices.
Here’s a table outlining the estimated price range for some commonly available CVD metal powders:
Metal Powder | Estimated Price Range (USD/kg) |
---|---|
Tungsten | $100 – $500 |
Molybdenum | $50 – $200 |
Rhenium | $1,000 – $10,000 |
Tantalum | $200 – $1,000 |
Nickel | $10 – $50 |
Cobalt | $20 – $100 |
Iron | $2 – $10 |
Copper | $10 – $30 |
Titanium | $50 – $200 |
Niobium | $100 – $500 |
Suppliers of CVD metal powders can be found globally, with various companies specializing in specific metals and applications. Some prominent names include:
- American Elements
- Alfa Aesar
- Carpenter Technology Corporation
- Höganäs AB
- Praxair Surface Technologies
Advantages and Limitations of CVD Metal Powders
CVD metal powders offer several advantages over traditional production methods:
- High purity: Achieves significantly higher purity levels compared to other techniques like powder metallurgy.
- Fine-grained structure: Enables the creation of powders with precise control over particle size and morphology, leading to unique properties.
- Tailored properties: Allows for precise control over the composition and structure of the powder, resulting in customized material properties.
- Complex shapes: Can produce powders with intricate shapes, opening doors for advanced applications.
However, CVD also has some limitations:
- Cost: The process can be expensive compared to traditional methods, especially for large-scale production.
- Slow deposition rates: Producing large quantities of powder can be time-consuming due to the layer-by-layer nature of the process.
- Limited material selection: Not all metals can be effectively produced using CVD due to factors like precursor availability and process compatibility.
Choosing the Right CVD Metal Powder
Selecting the optimal CVD metal powder requires careful consideration of several factors:
- Application requirements: Identify the specific properties needed for your intended use, such as strength, conductivity, or corrosion resistance.
- Cost constraints: Evaluate the budget and compare prices of different powders with varying specifications.
- Availability: Ensure the chosen powder is readily available from reliable suppliers in the required quantities.
- Processing compatibility: Consider the compatibility of the powder with your existing production processes and equipment.
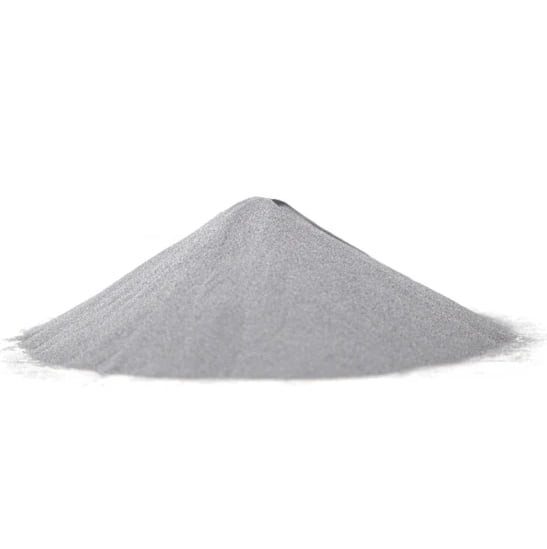
FAQ
Q: What are the environmental impacts of CVD metal powder production?
A: CVD can involve the use of hazardous chemicals, and proper disposal procedures are crucial to minimize environmental impact. Additionally, the energy consumption of the process needs to be considered.
Q: How does CVD compare to other methods of metal powder production?
A: Each method has its own advantages and disadvantages. Compared to traditional methods like atomization, CVD offers higher purity and finer control over powder characteristics but is generally slower and more expensive.
Q: What are the future trends for CVD metal powders?
A: The future of CVD metal powders looks promising, with advancements in technology leading to faster deposition rates, wider material selection, and potentially lower costs. Additionally, research is ongoing to explore novel applications in various fields, further expanding the potential of this versatile technology.
Conclusion
CVD metal powders represent a revolutionary advancement in material science, offering unique properties and enabling the creation of advanced components across various industries. With its ability to produce high-purity, fine-grained, and precisely tailored powders, CVD continues to push the boundaries of what’s possible in the world of materials and engineering. As research and development progress, we can expect even more exciting applications and advancements in this transformative technology.
Share On
MET3DP Technology Co., LTD is a leading provider of additive manufacturing solutions headquartered in Qingdao, China. Our company specializes in 3D printing equipment and high-performance metal powders for industrial applications.
Inquiry to get best price and customized Solution for your business!
Related Articles
About Met3DP
Recent Update
Our Product
CONTACT US
Any questions? Send us message now! We’ll serve your request with a whole team after receiving your message.
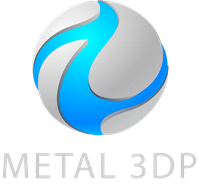
Metal Powders for 3D Printing and Additive Manufacturing