Cobalt-Chromium Powders
Table of Contents
Cobalt-chromium (Co-Cr) powders have revolutionized various industries with their exceptional properties and versatile applications. These powders are crucial in manufacturing components that require high strength, wear resistance, and biocompatibility. Whether you’re a materials scientist, an engineer, or simply curious about advanced materials, this guide will provide a comprehensive overview of cobalt-chromium powders, including their types, compositions, properties, applications, specifications, suppliers, pricing, and much more.
Overview of Cobalt-Chromium Powders
Cobalt-chromium powders are widely used in sectors like aerospace, medical, dental, and industrial manufacturing. The unique combination of cobalt and chromium offers several advantages, such as excellent corrosion resistance, high-temperature stability, and superior mechanical properties. This makes Co-Cr alloys ideal for producing parts that endure harsh environments and demanding conditions.
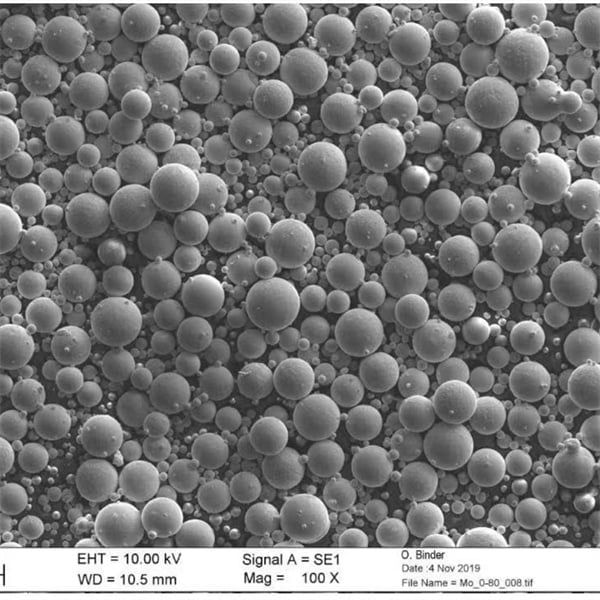
Types, Composition, and Properties of Cobalt-Chromium Powders
Understanding the different types of cobalt-chromium powders and their specific compositions is crucial for selecting the right material for your application. Here’s a detailed table summarizing the various types of Co-Cr powders, their compositions, properties, and characteristics.
Type | Composition | Properties | Characteristics |
---|---|---|---|
Co-Cr-Mo Alloy | Co: 60-65%, Cr: 27-30%, Mo: 5-7% | High wear resistance, excellent biocompatibility | Commonly used in medical implants |
Co-Cr-W Alloy | Co: 50-55%, Cr: 25-30%, W: 10-15% | High temperature stability, exceptional strength | Ideal for aerospace components |
Co-Cr-Fe Alloy | Co: 60-65%, Cr: 25-30%, Fe: 5-10% | Good corrosion resistance, high tensile strength | Used in industrial applications |
Co-Cr-Ni Alloy | Co: 50-55%, Cr: 20-25%, Ni: 15-20% | Excellent mechanical properties, good wear resistance | Suitable for dental prosthetics |
Co-Cr-Si Alloy | Co: 60-65%, Cr: 25-30%, Si: 5-7% | High hardness, good oxidation resistance | Used in cutting tools and wear-resistant coatings |
Co-Cr-Al Alloy | Co: 50-55%, Cr: 20-25%, Al: 15-20% | Lightweight, high strength | Used in aerospace and automotive applications |
Co-Cr-Nb Alloy | Co: 55-60%, Cr: 20-25%, Nb: 5-10% | Good ductility, excellent fatigue resistance | Ideal for structural components |
Co-Cr-Ta Alloy | Co: 55-60%, Cr: 25-30%, Ta: 5-10% | High melting point, good thermal stability | Used in high-temperature applications |
Co-Cr-Ti Alloy | Co: 50-55%, Cr: 20-25%, Ti: 15-20% | Good corrosion resistance, high strength-to-weight ratio | Suitable for biomedical implants |
Co-Cr-C Alloy | Co: 60-65%, Cr: 25-30%, C: 5-7% | Excellent hardness, good wear resistance | Used in wear-resistant coatings and hard-facing applications |
Applications of Cobalt-Chromium Powders
Cobalt-chromium powders are utilized in a wide range of applications due to their remarkable properties. Let’s dive into the specific uses of these powders across various industries.
Application | Industry | Description |
---|---|---|
Medical Implants | Healthcare | Co-Cr-Mo alloys are commonly used for hip and knee replacements due to their biocompatibility and wear resistance. |
Dental Prosthetics | Dental | Co-Cr-Ni alloys are used to manufacture dental crowns, bridges, and partial dentures. |
Aerospace Components | Aerospace | Co-Cr-W and Co-Cr-Al alloys are used in turbine blades and other high-temperature components. |
Industrial Tools | Manufacturing | Co-Cr-Si and Co-Cr-C alloys are utilized in cutting tools, wear-resistant coatings, and hard-facing applications. |
Automotive Parts | Automotive | Co-Cr-Al alloys are used in lightweight, high-strength components for engines and exhaust systems. |
Structural Components | Construction | Co-Cr-Nb and Co-Cr-Ta alloys are ideal for structural components that require excellent fatigue resistance. |
High-Temperature Applications | Energy | Co-Cr-Ta alloys are used in components that operate in extreme heat conditions, such as gas turbines. |
Wear-Resistant Coatings | Surface Engineering | Co-Cr-C alloys are applied as coatings to protect surfaces from wear and abrasion. |
Specifications, Sizes, Grades, and Standards of Cobalt-Chromium Powders
When selecting cobalt-chromium powders, it’s essential to consider their specifications, sizes, grades, and standards to ensure they meet the requirements of your application. The following table provides an overview of these parameters.
Parameter | Description |
---|---|
Particle Size | Typically ranges from 10 to 100 microns, depending on the application. |
Purity | High-purity powders (>99.5%) are preferred for medical and aerospace applications. |
Density | Ranges from 8.4 to 9.2 g/cm³, depending on the alloy composition. |
Hardness | Typically ranges from 350 to 500 HV, providing excellent wear resistance. |
Tensile Strength | Varies from 700 to 1200 MPa, depending on the specific alloy. |
Standards | Complies with ASTM F75, ISO 5832-4, and other relevant standards. |
Grades | Available in various grades, including medical, aerospace, and industrial grades. |
Suppliers and Pricing of Cobalt-Chromium Powders
Selecting the right supplier is crucial for obtaining high-quality cobalt-chromium powders. Here’s a table listing some of the top suppliers along with their pricing details.
Supplier | Location | Product Range | Pricing (per kg) |
---|---|---|---|
Sandvik | Sweden | Medical and industrial grades | $200 – $300 |
H.C. Starck | Germany | High-purity powders | $250 – $350 |
Carpenter Technology | USA | Aerospace and medical grades | $220 – $320 |
GKN Hoeganaes | USA | Industrial and automotive grades | $180 – $280 |
Oerlikon Metco | Switzerland | High-performance powders | $240 – $340 |
AP&C (GE Additive) | Canada | Additive manufacturing powders | $260 – $360 |
Praxair Surface Technologies | USA | Coatings and industrial powders | $200 – $300 |
Kennametal | USA | Wear-resistant powders | $210 – $310 |
Ametek | USA | Specialty metal powders | $230 – $330 |
Heraeus | Germany | Medical and dental powders | $250 – $350 |
Comparing Pros and Cons of Cobalt-Chromium Powders
Every material has its strengths and weaknesses. Let’s compare the pros and cons of cobalt-chromium powders to understand their advantages and limitations.
Pros | Cons |
---|---|
High Strength: Co-Cr alloys offer superior mechanical properties, making them ideal for demanding applications. | Cost: Cobalt-chromium powders can be expensive compared to other materials. |
Wear Resistance: Excellent wear resistance ensures longevity and durability of components. | Density: High density can be a drawback in applications where weight is a concern. |
Corrosion Resistance: Exceptional resistance to corrosion and oxidation, even at high temperatures. | Machinability: Co-Cr alloys can be challenging to machine, requiring specialized equipment. |
Biocompatibility: Highly biocompatible, making them suitable for medical implants. | Availability: Limited availability of high-purity powders in some regions. |
Thermal Stability: Maintain their properties at elevated temperatures, ideal for aerospace and energy applications. | Processing: Processing Co-Cr powders requires advanced techniques like additive manufacturing or high-temperature sintering. |
Key Applications and Case Studies
Let’s explore some real-world examples and case studies that highlight the versatility and effectiveness of cobalt-chromium powders in various applications.
Medical Implants
Cobalt-chromium-molybdenum (Co-Cr-Mo) alloys are widely used in orthopedic implants, including hip and knee replacements. Their excellent wear resistance and biocompatibility ensure the longevity of implants, reducing the need for revision surgeries. For instance, a study on Co-Cr-Mo hip implants showed a 95% success rate over a 10-year period, highlighting the material’s reliability and effectiveness.
Dental Prosthetics
In the dental industry, cobalt-chromium-nickel (Co-Cr-Ni) alloys are used to manufacture crowns, bridges, and partial dentures. These alloys offer excellent mechanical properties and corrosion resistance, ensuring the durability of dental prosthetics. A case study on Co-Cr-Ni dental crowns revealed a high success rate in terms of patient satisfaction and longevity, with minimal instances of corrosion or mechanical failure over a span of several years.
Aerospace Components
In the aerospace sector, cobalt-chromium-tungsten (Co-Cr-W) and cobalt-chromium-aluminum (Co-Cr-Al) alloys are utilized for high-temperature components such as turbine blades and jet engine parts. These alloys maintain their mechanical properties under extreme heat and stress, ensuring the safety and efficiency of aerospace machinery. A notable case study from a leading aerospace manufacturer demonstrated that turbine blades made from Co-Cr-W alloys exhibited significantly improved performance and longer service life compared to traditional materials.
Industrial Tools and Coatings
Cobalt-chromium-silicon (Co-Cr-Si) and cobalt-chromium-carbon (Co-Cr-C) alloys are used in industrial tools and wear-resistant coatings. These alloys provide excellent hardness and durability, making them ideal for cutting tools and surfaces exposed to high wear and tear. A case study on Co-Cr-Si coated cutting tools showed a marked improvement in tool life and cutting performance, reducing operational costs and downtime in manufacturing processes.
Advantages of Cobalt-Chromium Powders
High Mechanical Strength
One of the primary advantages of cobalt-chromium powders is their high mechanical strength. This property makes them suitable for applications that require robust and durable materials, such as aerospace components, industrial tools, and medical implants.
Wear and Corrosion Resistance
Cobalt-chromium alloys are renowned for their exceptional wear and corrosion resistance. This makes them ideal for environments where materials are exposed to harsh conditions, such as in the aerospace and medical industries. The alloys can withstand prolonged exposure to corrosive substances and abrasive wear without significant degradation.
Biocompatibility
The biocompatibility of cobalt-chromium alloys is a significant advantage for medical applications. These materials do not elicit adverse reactions when implanted in the human body, making them suitable for medical implants like hip and knee replacements, dental prosthetics, and heart valves.
Thermal Stability
Cobalt-chromium alloys maintain their properties at elevated temperatures, which is essential for applications in high-temperature environments. This thermal stability ensures that components made from these materials can perform reliably under extreme heat, as seen in aerospace and energy applications.
Disadvantages of Cobalt-Chromium Powders
High Cost
One of the main drawbacks of cobalt-chromium powders is their high cost. These materials are more expensive than other metal powders, which can be a limiting factor for some applications. The high cost is primarily due to the complex processing and the use of high-purity raw materials.
High Density
Cobalt-chromium alloys have a high density, which can be a disadvantage in applications where weight is a critical factor. For instance, in aerospace applications, the high density of Co-Cr alloys can add to the overall weight of the components, potentially affecting fuel efficiency and performance.
Difficult Machinability
Cobalt-chromium alloys can be challenging to machine due to their hardness and strength. Specialized equipment and techniques are often required to process these materials, which can increase manufacturing costs and complexity.
Limited Availability
High-purity cobalt-chromium powders may not be readily available in all regions, which can pose a challenge for manufacturers. This limited availability can lead to supply chain issues and increased lead times for obtaining the materials.
Specifications and Standards for Cobalt-Chromium Powders
When selecting cobalt-chromium powders, it is essential to ensure they meet the required specifications and standards for your application. Here’s a detailed table of the specifications, sizes, grades, and standards:
Specification | Description |
---|---|
ASTM F75 | Standard specification for cobalt-28 chromium-6 molybdenum alloy castings and casting alloy for surgical implants. |
ISO 5832-4 | International standard for wrought cobalt-chromium-molybdenum alloy for surgical implants. |
Particle Size Distribution | Typically 10-100 microns, suitable for various additive manufacturing techniques. |
Purity Levels | ≥99.5% purity to ensure high performance and reliability. |
Density | Ranges between 8.4 – 9.2 g/cm³ depending on the alloy composition. |
Mechanical Properties | Tensile strength of 700-1200 MPa, hardness of 350-500 HV. |
Compliance | Must comply with industry-specific standards such as ASTM, ISO, and AMS. |
Suppliers and Pricing Information
Finding reliable suppliers for cobalt-chromium powders is crucial for ensuring material quality and consistency. Here’s a detailed table of prominent suppliers, their locations, product ranges, and pricing:
Supplier | Location | Product Range | Pricing (per kg) |
---|---|---|---|
Sandvik | Sweden | Medical and industrial grades | $200 – $300 |
H.C. Starck | Germany | High-purity powders | $250 – $350 |
Carpenter Technology | USA | Aerospace and medical grades | $220 – $320 |
GKN Hoeganaes | USA | Industrial and automotive grades | $180 – $280 |
Oerlikon Metco | Switzerland | High-performance powders | $240 – $340 |
AP&C (GE Additive) | Canada | Additive manufacturing powders | $260 – $360 |
Praxair Surface Technologies | USA | Coatings and industrial powders | $200 – $300 |
Kennametal | USA | Wear-resistant powders | $210 – $310 |
Ametek | USA | Specialty metal powders | $230 – $330 |
Heraeus | Germany | Medical and dental powders | $250 – $350 |
Comparing Cobalt-Chromium Powders: Advantages and Limitations
To make an informed decision when selecting cobalt-chromium powders, it is essential to weigh their advantages and limitations. Here’s a comparison table highlighting these aspects:
Aspect | Advantages | Limitations |
---|---|---|
Mechanical Strength | High strength, suitable for demanding applications | High density, which can be a drawback in weight-sensitive applications |
Wear Resistance | Excellent wear resistance, ensuring longevity | Difficult machinability, requiring specialized equipment |
Corrosion Resistance | Superior corrosion resistance, even at high temperatures | High cost compared to other materials |
Biocompatibility | Highly biocompatible, ideal for medical implants | Limited availability in some regions |
Thermal Stability | Maintains properties at elevated temperatures | Processing challenges due to high hardness |
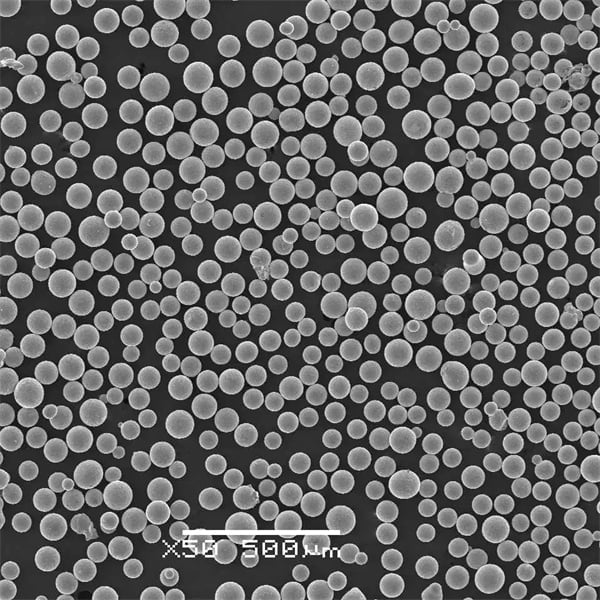
FAQ
Q: What are the primary uses of cobalt-chromium powders?
A: Cobalt-chromium powders are primarily used in medical implants, dental prosthetics, aerospace components, industrial tools, and wear-resistant coatings. Their high strength, wear resistance, and biocompatibility make them ideal for these applications.
Q: Why are cobalt-chromium alloys preferred for medical implants?
A: Cobalt-chromium alloys are preferred for medical implants due to their excellent biocompatibility, high mechanical strength, and superior wear resistance. These properties ensure the longevity and reliability of implants, reducing the need for revision surgeries.
Q: What are the challenges associated with machining cobalt-chromium alloys?
A: Machining cobalt-chromium alloys can be challenging due to their high hardness and strength. Specialized equipment and techniques are required to process these materials, which can increase manufacturing costs and complexity.
Q: How do cobalt-chromium alloys compare to titanium alloys in medical applications?
A: While both cobalt-chromium and titanium alloys are used in medical applications, Co-Cr alloys offer higher wear resistance and mechanical strength. However, titanium alloys are lighter and more corrosion-resistant, making them suitable for different types of implants.
Q: Are cobalt-chromium powders suitable for additive manufacturing?
A: Yes, cobalt-chromium powders are suitable for additive manufacturing, particularly for producing complex geometries and custom components. They offer high strength and excellent surface finish, making them ideal for aerospace, medical, and industrial applications.
Conclusion
Cobalt-chromium powders are an indispensable material in various high-performance applications due to their exceptional properties. From medical implants to aerospace components, their high strength, wear resistance, and biocompatibility make them a preferred choice across multiple industries. While they come with challenges such as high cost and difficult machinability, the advantages they offer often outweigh these limitations. By understanding the different types, compositions, applications, and suppliers of cobalt-chromium powders, you can make informed decisions that best meet your specific needs.
With advancements in material science and manufacturing technologies, the use of cobalt-chromium powders is expected to grow, opening new possibilities and enhancing the performance of critical components in demanding environments. Whether you’re developing cutting-edge medical devices, high-performance aerospace parts, or durable industrial tools, cobalt-chromium powders provide a reliable and robust solution for your material needs.
Share On
MET3DP Technology Co., LTD is a leading provider of additive manufacturing solutions headquartered in Qingdao, China. Our company specializes in 3D printing equipment and high-performance metal powders for industrial applications.
Inquiry to get best price and customized Solution for your business!
Related Articles
About Met3DP
Recent Update
Our Product
CONTACT US
Any questions? Send us message now! We’ll serve your request with a whole team after receiving your message.
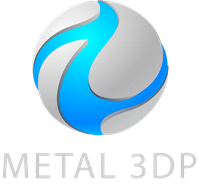
Metal Powders for 3D Printing and Additive Manufacturing