Aerospace-Grade Cooling Shrouds
Table of Contents
Introduction – The Critical Role of Custom Cooling Shrouds in Aerospace Applications
In the demanding realm of aerospace engineering, where precision, reliability, and performance are paramount, even seemingly minor components can play a crucial role in the overall functionality and safety of aircraft and spacecraft. Among these vital elements are cooling shrouds – custom-engineered structures designed to manage and dissipate heat generated by critical systems. From protecting sensitive electronics in the avionics bay to ensuring the optimal operating temperature of engine components, cooling shrouds are indispensable for maintaining the integrity and efficiency of aerospace vehicles. Traditional manufacturing methods often struggle to meet the complex geometric requirements and stringent material specifications demanded by these applications, leading to increased lead times and higher costs. This is where the transformative power of metal 3D printing, also known as metal additive manufacturing, comes into play, offering unprecedented design freedom, material versatility, and the potential for significant performance enhancements. At Metal3DP, we understand the critical nature of aerospace components and are dedicated to providing cutting-edge metal 3D printing solutions that meet the exacting standards of this industry. Our advanced printing technology, coupled with a comprehensive range of high-performance metal powders, empowers aerospace engineers and procurement managers to create custom cooling shrouds with optimized thermal management properties, reduced weight, and enhanced durability. Explore our metal 3D printing services to discover how we can support your aerospace manufacturing needs.
What are Aerospace Cooling Shrouds Used For? – Diverse Applications in Aircraft and Spacecraft
Aerospace cooling shrouds serve a multitude of critical functions across various subsystems within aircraft and spacecraft. Their primary purpose is to regulate the temperature of sensitive components, preventing overheating that could lead to performance degradation, malfunction, or even catastrophic failure. The applications of these custom-designed shrouds are diverse and essential, including:
- Electronics Cooling: Protecting sensitive avionics, control systems, and communication equipment from the heat generated during operation. This ensures the reliability and longevity of these critical systems.
- Engine Component Thermal Management: Dissipating heat from engine parts such as turbines, combustion chambers, and exhaust nozzles, maintaining optimal operating temperatures and preventing material fatigue.
- Hydraulic System Cooling: Regulating the temperature of hydraulic fluids and components to ensure consistent performance and prevent viscosity breakdown.
- Sensor Protection: Shielding delicate sensors and instrumentation from extreme temperatures, ensuring accurate data acquisition and reliable operation.
- Laser System Thermal Control: Managing the heat generated by high-powered lasers used in various aerospace applications, maintaining beam quality and system efficiency.
- Spacecraft Thermal Regulation: In the harsh environment of space, cooling shrouds play a vital role in managing the extreme temperature fluctuations, protecting sensitive instruments and ensuring the functionality of spacecraft systems.
The specific design and material requirements for each application vary significantly, underscoring the need for custom solutions. Metal 3D printing offers the flexibility to create intricate geometries and optimize designs for specific thermal management needs, making it an ideal manufacturing method for these diverse applications.
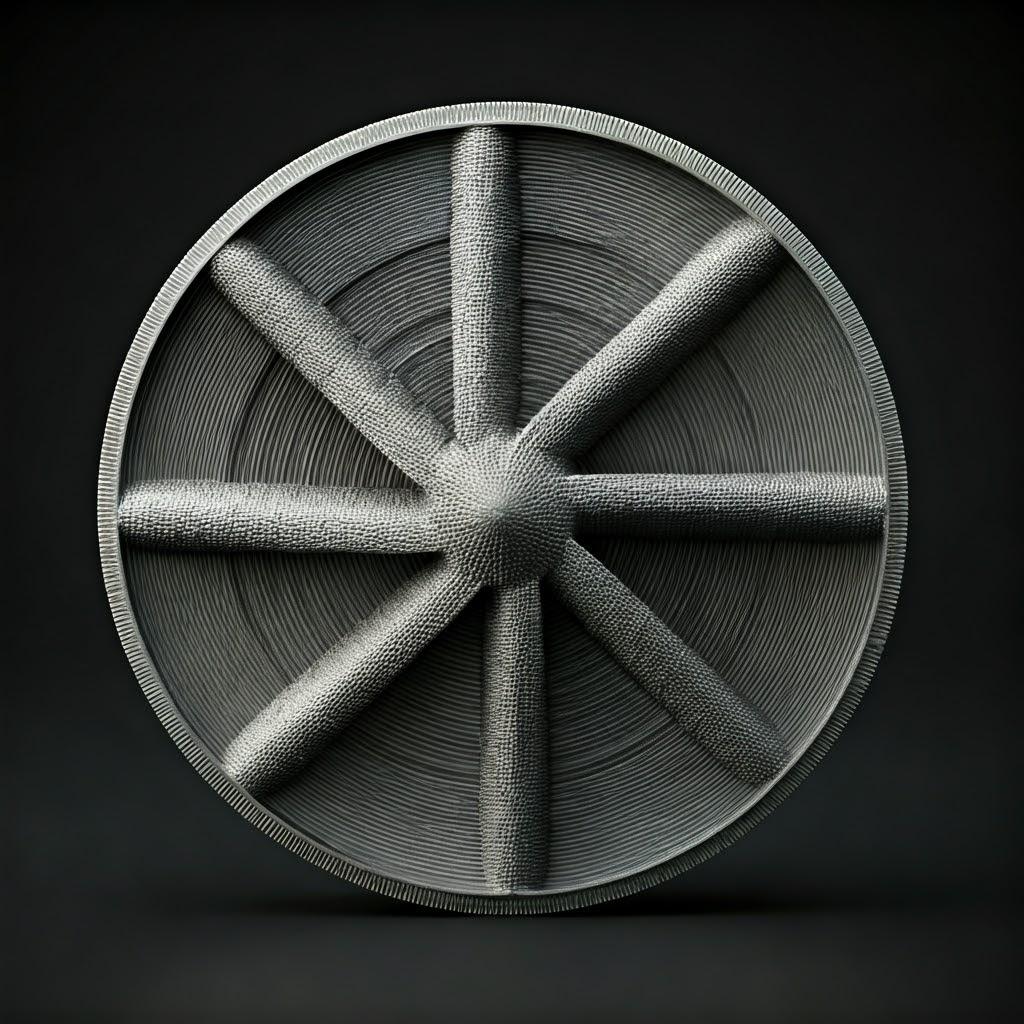
Why Use Metal 3D Printing for Aerospace Cooling Shrouds? – Advantages of Additive Manufacturing
The adoption of metal 3D printing for the fabrication of aerospace cooling shrouds offers a compelling array of advantages over traditional manufacturing techniques such as machining, casting, or forging. These benefits are particularly significant in the demanding aerospace sector, where performance, weight, and lead time are critical considerations:
- Design Freedom and Complexity: Metal 3D printing allows for the creation of highly complex geometries that are often impossible or cost-prohibitive to achieve with traditional methods. This enables the optimization of cooling shroud designs for enhanced thermal efficiency, incorporating intricate internal channels, thin walls, and complex external features to maximize heat dissipation while minimizing weight.
- Material Efficiency and Waste Reduction: Additive manufacturing processes build parts layer by layer, using only the material needed for the final component. This significantly reduces material waste compared to subtractive methods like machining, where a substantial portion of the raw material is removed. This is particularly important when working with expensive aerospace-grade alloys.
- Lightweighting Potential: The ability to create optimized geometries and use advanced lightweight materials through metal 3D printing directly contributes to weight reduction in aerospace vehicles. Lighter components lead to improved fuel efficiency, increased payload capacity, and enhanced performance.
- Rapid Prototyping and Reduced Lead Times: Metal 3D printing accelerates the design and development cycle by enabling the rapid creation of prototypes for testing and validation. This significantly reduces lead times compared to traditional tooling-dependent methods, allowing for faster iteration and quicker time-to-market. At Metal3DP, our advanced printing capabilities ensure efficient production timelines for even complex cooling shroud designs.
- Customization and On-Demand Manufacturing: Each aerospace application may have unique cooling requirements. Metal 3D printing facilitates the production of highly customized cooling shrouds tailored to specific needs, without the added cost and time associated with creating custom tooling for each variation. This also enables on-demand manufacturing, reducing the need for large inventories.
- Enhanced Performance and Functionality: By leveraging the design freedom offered by metal 3D printing, engineers can create cooling shrouds with optimized thermal transfer characteristics, improved structural integrity, and integrated features, leading to enhanced overall performance and functionality. Metal3DP’s expertise in material selection and process optimization ensures that your 3D printed cooling shrouds meet the highest performance standards.
Recommended Materials and Why They Matter – High-Performance Metal Powders for Extreme Environments
The selection of the appropriate metal powder is paramount in achieving the desired performance characteristics for aerospace cooling shrouds. These components often operate in extreme environments, requiring materials that exhibit exceptional thermal conductivity, high strength-to-weight ratio, corrosion resistance, and high-temperature performance. At Metal3DP, we offer a range of high-quality metal powders specifically suited for aerospace applications, including:
- IN625 (Nickel Alloy 625): This nickel-chromium-molybdenum alloy is renowned for its exceptional high-temperature strength, excellent corrosion and oxidation resistance, and good fatigue properties. Its ability to withstand extreme thermal cycling and corrosive environments makes it an ideal choice for cooling shrouds in demanding aerospace applications, such as engine components and exhaust systems. | Property | Value | Significance for Cooling Shrouds | | :—————————- | :————————————- | :—————————————————————————————————————————– | | Tensile Strength | ~827 MPa | Ensures structural integrity under high thermal and mechanical loads. | | Operating Temperature | Up to 980 °C (1800 °F) | Suitable for high-temperature environments typical in aerospace applications. | | Corrosion Resistance | Excellent | Withstands harsh environmental conditions and prevents degradation of the shroud. | | Thermal Conductivity | ~9.8 W/m·K | Facilitates efficient heat transfer away from critical components. | | Density | ~8.44 g/cm³ | Provides a good balance of strength and weight. | | Recommended by Metal3DP | For high-temperature, high-stress applications requiring exceptional corrosion resistance. | Our advanced powder processing ensures optimal flowability and density for superior part quality. |
- AlSi10Mg (Aluminum Silicon Magnesium): This aluminum alloy offers a high strength-to-weight ratio, excellent thermal conductivity, and good corrosion resistance. Its lightweight properties make it particularly attractive for aerospace applications where weight reduction is a critical factor, such as cooling shrouds for electronics and hydraulic systems. | Property | Value | Significance for Cooling Shrouds | | :—————————- | :————————————- | :————————————————————————————————————————— | | Tensile Strength | ~370 MPa | Provides sufficient strength for many aerospace cooling shroud applications. | | Operating Temperature | Up to 200 °C (intermittent) | Suitable for applications where temperatures are moderately high. | | Corrosion Resistance | Good | Offers adequate protection against environmental degradation. | | Thermal Conductivity | ~160 W/m·K | Excellent for efficient heat dissipation, crucial for cooling electronic components. | ~2.67 g/cm³ | Significantly lighter than steel or nickel alloys, contributing to fuel efficiency. | | Recommended by Metal3DP | For applications prioritizing lightweighting and high thermal conductivity. | Our AlSi10Mg powder is optimized for consistent printability and high-density parts. |
At Metal3DP, our advanced powder making system ensures the production of high-quality metal powders with excellent sphericity and flowability, critical for achieving dense and high-performance 3D printed parts. We can help you select the optimal material for your specific aerospace cooling shroud application, considering factors such as operating temperature, mechanical loads, environmental conditions, and weight requirements. Contact us to discuss your material needs and explore our comprehensive range of high-performance metal powders. Sources and related content
Design Considerations for Additive Manufacturing of Cooling Shrouds – Optimizing for Performance and Efficiency
Designing aerospace cooling shrouds for metal 3D printing requires a different mindset compared to traditional manufacturing methods. To fully leverage the capabilities of additive manufacturing and achieve optimal performance and efficiency, several key design considerations must be taken into account:
- Topology Optimization: This advanced design technique uses algorithms to determine the most efficient material distribution for a given set of loads and constraints. By removing unnecessary material while maintaining structural integrity and thermal performance, topology optimization can lead to significant weight reduction and improved efficiency in cooling shroud designs. Metal3DP’s expertise can help you apply these advanced techniques to your designs.
- Lattice Structures: Incorporating lattice structures within the cooling shroud design can provide a high strength-to-weight ratio and enhance heat transfer. These intricate, repeating patterns can be tailored to specific load requirements and thermal management needs, offering a lightweight yet robust solution. Our printing technology excels at producing complex lattice geometries with high accuracy.
- Conformal Cooling Channels: Metal 3D printing enables the creation of complex, internal cooling channels that closely follow the contours of the heat-generating components. This conformal cooling approach maximizes heat transfer efficiency compared to traditional straight channels, leading to better temperature regulation and improved component lifespan.
- Wall Thickness and Feature Size: Careful consideration of minimum wall thicknesses and feature sizes is crucial for successful 3D printing. These parameters are influenced by the chosen material, printing technology, and desired structural integrity. Designing with manufacturability in mind ensures that the cooling shroud can be produced with high quality and minimal defects.
- Support Structures: Support structures are often necessary in metal 3D printing to prevent part deformation during the build process and to support overhanging features. The design of these supports should minimize material usage and be easy to remove during post-processing without damaging the final part. Our engineers at Metal3DP have extensive experience in optimizing support structures for various geometries.
- Surface Finish Considerations: The as-printed surface finish of a metal 3D printed part may not always meet the requirements for certain aerospace applications. Designing with the intended surface finish in mind can influence build orientation and the need for post-processing steps like machining or polishing.
By carefully considering these design aspects and working with an experienced metal 3D printing service provider like Metal3DP, engineers can create innovative and highly effective cooling shroud solutions for aerospace applications.
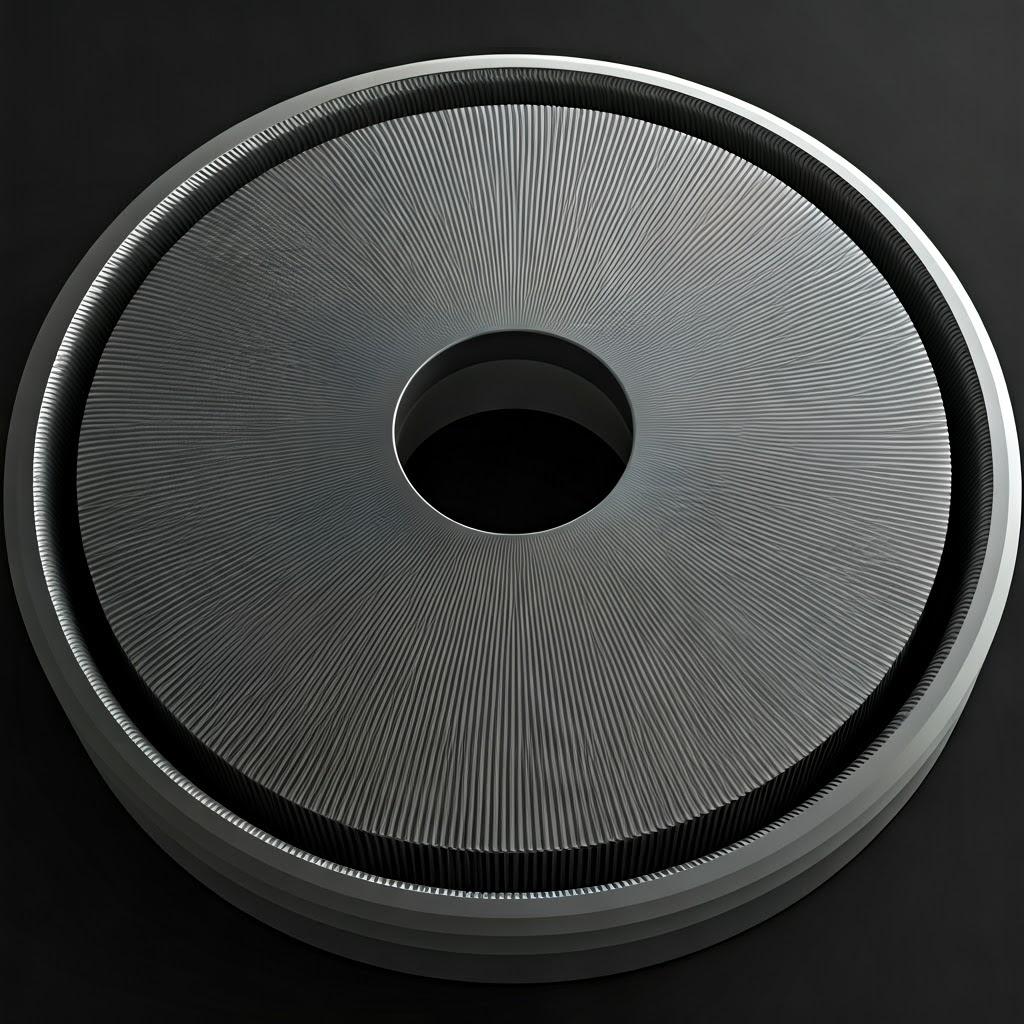
Tolerance, Surface Finish, and Dimensional Accuracy of 3D Printed Cooling Shrouds – Meeting Stringent Aerospace Standards
In the aerospace industry, dimensional accuracy and surface finish are critical for ensuring the proper fit, function, and performance of components. Metal 3D printing has advanced significantly in its ability to achieve tight tolerances and good surface finishes, making it a viable manufacturing method for demanding applications like cooling shrouds.
- Dimensional Accuracy: The dimensional accuracy achievable with metal 3D printing depends on several factors, including the printing technology (e.g., Selective Laser Melting (SLM), Electron Beam Melting (EBM)), the material used, part geometry, and build parameters. With optimized processes and high-quality equipment, tolerances of ±0.1 mm or even tighter can be achieved for critical dimensions. Metal3DP’s state-of-the-art SEBM printers are known for their high accuracy and reliability.
- Surface Finish: The as-printed surface finish in metal 3D printing typically has a higher roughness compared to machined surfaces. The surface roughness (Ra) can range from 5 to 20 µm depending on the printing parameters and material. For aerospace cooling shrouds requiring smoother surfaces for improved airflow or reduced friction, post-processing techniques such as polishing, abrasive blasting, or machining can be employed.
- Factors Affecting Accuracy and Finish:
- Layer Thickness: Thinner layers generally result in smoother surface finishes and higher accuracy but increase build time.
- Powder Particle Size and Distribution: Consistent and fine powder particles contribute to better surface finish and detail resolution. Metal3DP’s advanced powder making system ensures high-quality powders with optimal characteristics.
- Build Orientation: The orientation of the part during printing can significantly impact dimensional accuracy and surface finish on different surfaces.
- Support Structures: The placement and removal of support structures can affect the surface finish of the supported areas.
- Calibration and Maintenance: Properly calibrated and maintained 3D printing equipment is essential for achieving consistent and accurate results.
- Achieving Aerospace Standards: To meet the stringent requirements of the aerospace industry, it’s crucial to work with a metal 3D printing service provider that has robust quality control processes, experience with aerospace materials, and the capability to perform necessary post-processing to achieve the required tolerances and surface finishes. Metal3DP is committed to delivering high-quality, accurate parts that meet the demanding standards of the aerospace sector.
Post-Processing Requirements for Aerospace-Grade Cooling Shrouds – Ensuring Optimal Performance and Durability
While metal 3D printing offers significant advantages in creating complex geometries, post-processing steps are often necessary to achieve the final desired properties, surface finish, and dimensional accuracy for aerospace-grade cooling shrouds. Common post-processing requirements include:
- Support Removal: After the printing process is complete, support structures that were used to stabilize the part during the build must be carefully removed. The method of removal depends on the support material and geometry and may involve manual breaking, cutting, or machining.
- Heat Treatment: Heat treatment is often required to relieve internal stresses that may have built up during the rapid solidification of the metal layers in the 3D printing process. It can also be used to enhance the mechanical properties, such as strength and hardness, of the material to meet specific aerospace requirements.
- Surface Finishing: As mentioned earlier, the as-printed surface finish may not be suitable for all aerospace applications. Techniques like polishing, grinding, abrasive blasting, or chemical etching can be used to achieve smoother surfaces, which can be important for airflow, reducing friction, or meeting aesthetic requirements.
- CNC Machining: For critical features requiring very tight tolerances or specific surface finishes that are difficult to achieve directly with 3D printing, CNC machining may be employed as a secondary process. This can ensure precise dimensions and smooth surfaces for interfaces or mounting points.
- Inspection and Quality Control: Rigorous inspection processes are essential in the aerospace industry to ensure that the manufactured parts meet the required specifications. This may involve dimensional measurements using coordinate measuring machines (CMMs), non-destructive testing (NDT) methods like X-ray or ultrasonic inspection to detect internal defects, and material analysis to verify the composition and properties of the alloy.
- Coating and Surface Treatments: Depending on the application and environmental conditions, cooling shrouds may require coatings to enhance corrosion resistance, improve wear properties, or provide thermal barrier functions. Common aerospace coatings include anodizing, chromate conversion coating, and thermal spray coatings.
Choosing a metal 3D printing service provider like Metal3DP that offers comprehensive post-processing capabilities and has experience with aerospace standards is crucial for obtaining готовые to-use components that meet the stringent requirements of the industry. We have the expertise and equipment to handle all necessary post-processing steps to ensure the optimal performance and durability of your 3D printed aerospace cooling shrouds.
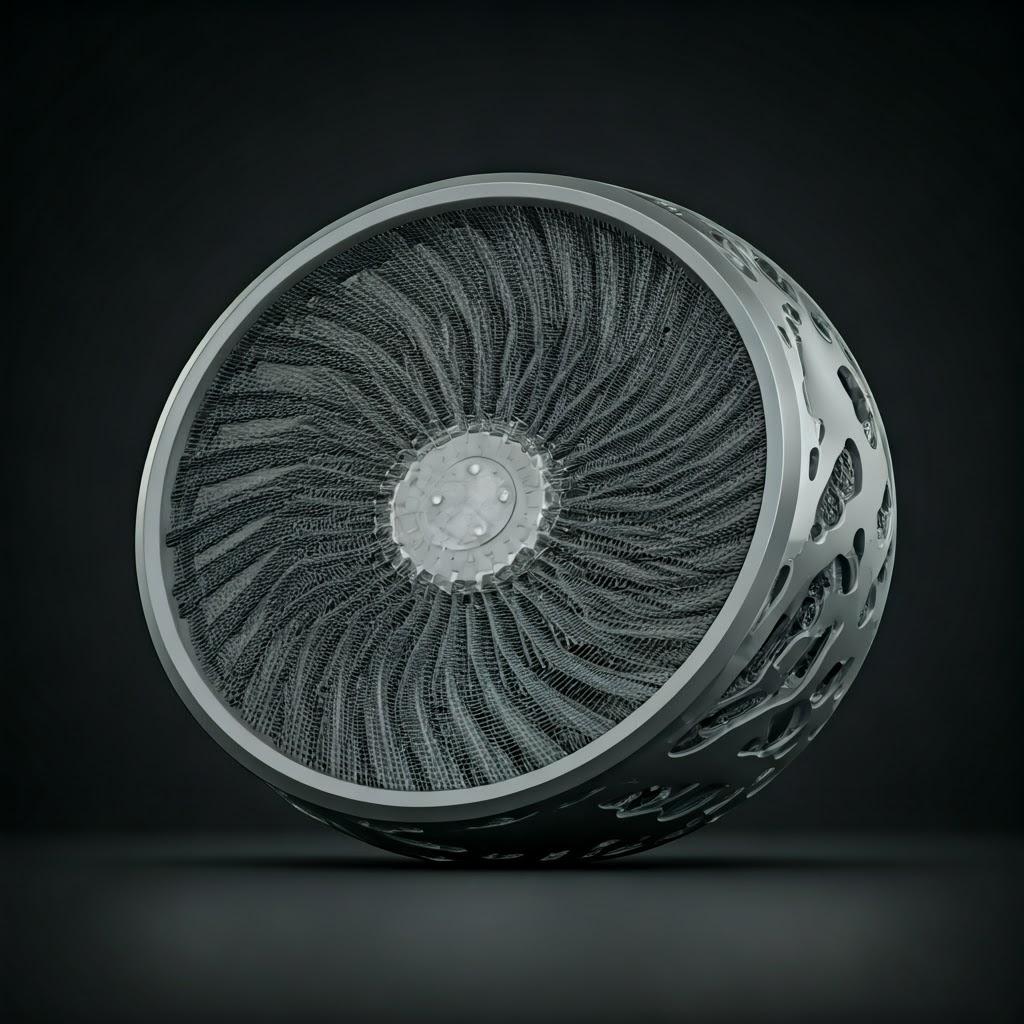
Common Challenges and How to Avoid Them in 3D Printing Aerospace Cooling Shrouds
While metal 3D printing offers numerous advantages, there are also potential challenges that need to be addressed to ensure the successful fabrication of high-quality aerospace cooling shrouds. Understanding these challenges and implementing appropriate strategies can help avoid costly errors and delays:
- Warping and Distortion: Thermal stresses during the printing process can lead to warping or distortion of the part, especially for complex geometries or thin-walled structures.
- How to Avoid: Optimize part orientation, use appropriate support structures, control build chamber temperature, and consider stress-relieving heat treatments after printing. Metal3DP’s expertise in process optimization minimizes the risk of warping.
- Porosity and Internal Defects: Incomplete melting or solidification of the metal powder can result in porosity or internal defects within the printed part, which can compromise its mechanical properties.
- How to Avoid: Optimize printing parameters such as laser power, scan speed, and powder bed temperature. Ensure the use of high-quality metal powders with good flowability and packing density, such as those produced by Metal3DP’s advanced powder making system.
- Support Structure Removal Damage: Improper removal of support structures can damage the surface of the part, especially for delicate features.
- How to Avoid: Design support structures that are easy to remove, use appropriate removal techniques, and consider using dissolvable support materials where applicable. Our engineers are skilled in designing and removing support structures without causing damage.
- Surface Roughness: The as-printed surface roughness may not meet the requirements for certain aerospace applications, potentially affecting airflow or requiring additional post-processing.
- How to Avoid: Optimize printing parameters, consider build orientation, and plan for necessary surface finishing steps like polishing or machining.
- Material Property Variability: Achieving consistent and predictable material properties throughout the printed part is crucial for aerospace applications. Variations in density, microstructure, or chemical composition can affect performance.
- How to Avoid: Work with a reputable metal 3D printing service provider like Metal3DP that has strict quality control processes, uses well-characterized materials, and optimizes printing parameters for consistent results.
- Cost Considerations: While metal 3D printing can be cost-effective for complex, low-volume production, the initial investment in equipment and materials can be significant.
- How to Avoid: Carefully evaluate the total cost of ownership, including material usage, build time, post-processing, and quality control. Partnering with an experienced service provider like Metal3DP can provide cost-effective solutions and access to advanced technologies without the need for large upfront investments.
By being aware of these potential challenges and implementing appropriate mitigation strategies, aerospace engineers and procurement managers can effectively leverage metal 3D printing to create high-performance cooling shroud solutions.
How to Choose the Right Metal 3D Printing Service Provider for Aerospace Components
Selecting the right metal 3D printing service provider is a critical decision for aerospace companies looking to leverage the benefits of additive manufacturing. Given the stringent requirements and high stakes involved in aerospace applications, it’s essential to partner with a provider that possesses the necessary expertise, capabilities, and quality standards. Here are key factors to consider when making this choice:
- Aerospace Experience and Certifications: Look for a provider with a proven track record of working with aerospace clients and a deep understanding of the industry’s specific requirements. Relevant certifications such as AS9100D demonstrate a commitment to quality management systems for the aerospace, space, and defense organizations. Metal3DP is dedicated to meeting the rigorous standards of the aerospace industry.
- Material Capabilities: Ensure the service provider offers a range of aerospace-grade metal powders that meet your application needs. This includes materials like IN625 and AlSi10Mg, as well as other high-performance alloys. Verify that they have experience processing these materials and can provide material data sheets and testing reports. Metal3DP manufactures a wide range of high-quality metal powders optimized for demanding applications.
- Printing Technology and Equipment: The type of metal 3D printing technology and the quality of the equipment used by the service provider directly impact the accuracy, surface finish, and mechanical properties of the printed parts. Technologies like Selective Laser Melting (SLM) and Electron Beam Melting (EBM) are commonly used for aerospace applications. Metal3DP utilizes industry-leading SEBM printers known for their accuracy and reliability.
- Design and Engineering Support: A good service provider should offer design and engineering support to help optimize your cooling shroud designs for additive manufacturing. This includes expertise in topology optimization, lattice structures, and design for manufacturability. Metal3DP’s team has decades of collective expertise in metal additive manufacturing and can provide comprehensive application development services.
- Post-Processing Capabilities: As discussed earlier, post-processing is often crucial for aerospace components. Ensure the provider has in-house or access to reliable partners for necessary steps like support removal, heat treatment, surface finishing, CNC machining, and coating.
- Quality Control and Inspection: Robust quality control processes and inspection capabilities are non-negotiable for aerospace parts. The provider should have established procedures for dimensional inspection, non-destructive testing, and material verification.
- Lead Times and Production Capacity: Evaluate the service provider’s lead times and production capacity to ensure they can meet your project timelines and volume requirements.
- Communication and Customer Support: Clear communication, responsiveness, and strong customer support are essential for a successful partnership. Choose a provider that is proactive, collaborative, and committed to understanding your specific needs.
- Transparency and Traceability: The ability to provide full transparency and traceability of materials and processes is critical in the aerospace industry for quality assurance and regulatory compliance.
By carefully evaluating these factors, you can select a metal 3D printing service provider like Metal3DP that can reliably produce high-quality, aerospace-grade cooling shrouds that meet your performance and regulatory requirements. Contact Metal3DP to explore how our capabilities can power your organization’s additive manufacturing goals.
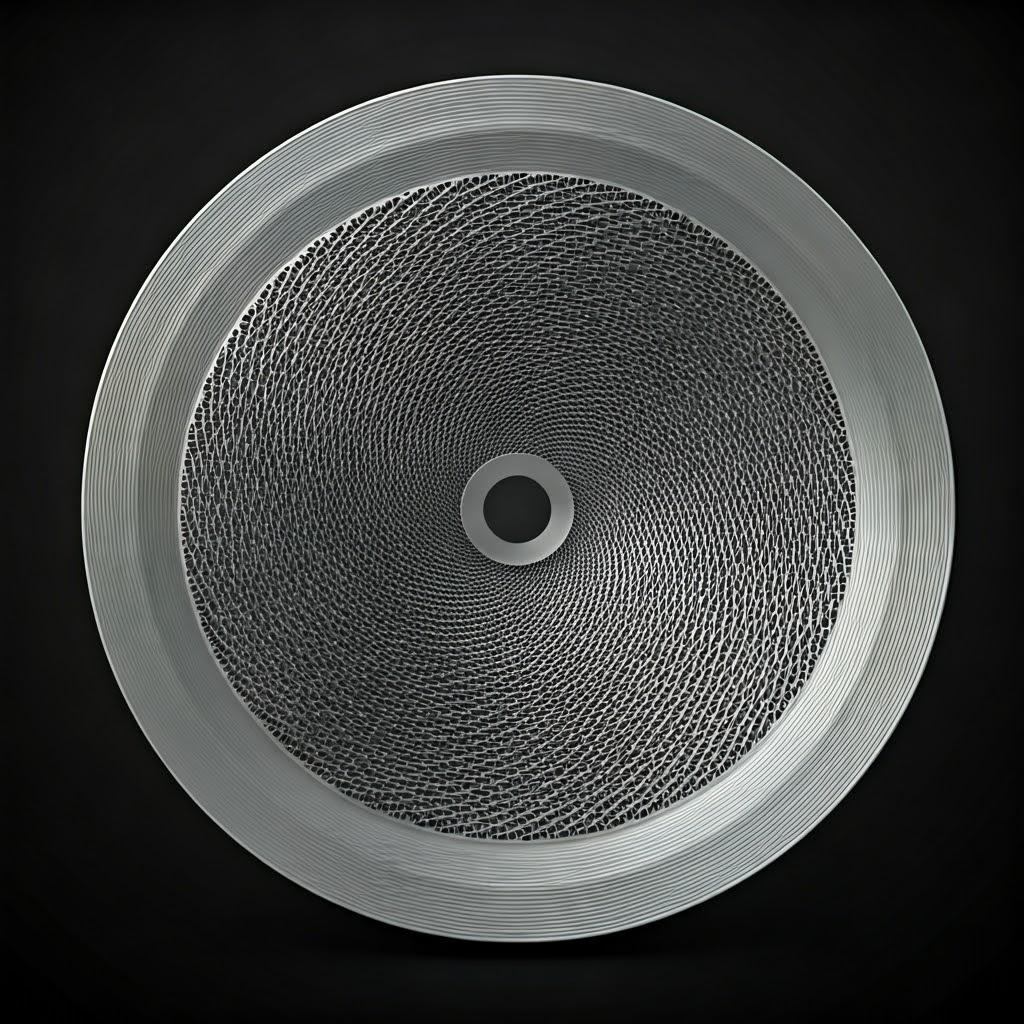
Cost Factors and Lead Time for 3D Printed Aerospace Cooling Shrouds
Understanding the cost factors and lead times associated with metal 3D printing is essential for effective project planning and budgeting. While these can vary depending on several parameters, here’s a general overview for aerospace cooling shrouds:
- Cost Factors:
- Material Costs: Aerospace-grade metal powders like IN625 and AlSi10Mg can be expensive. The quantity of material used for the part and support structures significantly impacts the overall cost. Metal3DP offers a range of high-quality metal powders at competitive prices.
- Build Time: The time it takes to print a cooling shroud depends on its size, complexity, and the chosen printing parameters (e.g., layer thickness, scan speed). Longer build times translate to higher machine operating costs.
- Post-Processing Costs: The extent of post-processing required (support removal, heat treatment, surface finishing, machining, coating) will add to the overall cost. Complex post-processing can significantly increase the final price.
- Design and Engineering Costs: If design optimization or engineering support is needed, these services will also factor into the cost. Metal3DP provides comprehensive application development services.
- Quality Control and Inspection Costs: Rigorous quality control procedures, including dimensional inspection and non-destructive testing, are necessary for aerospace parts and contribute to the overall cost.
- Tooling Costs (Minimized): One of the key advantages of 3D printing is the minimal need for traditional tooling, which can lead to significant cost savings, especially for low-volume or complex parts.
- Lead Time:
- Design and Optimization: The initial design and optimization phase can take anywhere from a few days to several weeks, depending on the complexity of the cooling shroud and the need for simulations or iterations.
- Printing Time: The actual printing time can range from several hours to several days, depending on the part size and complexity.
- Post-Processing Time: Post-processing steps can add significant time to the overall lead time, ranging from a few days to several weeks, depending on the required processes.
- Quality Control and Inspection: Thorough inspection processes also contribute to the lead time.
- Shipping: The time required for shipping the final parts to the customer needs to be considered.
While the initial cost per part for metal 3D printing might be higher than for high-volume traditional manufacturing, it often becomes more cost-effective for complex geometries, low to medium production volumes, and customized parts, especially when considering the reduced tooling costs and faster time-to-market. Metal3DP is committed to providing cost-effective metal 3D printing solutions with efficient lead times for aerospace applications. Contact us to discuss your specific requirements and obtain a detailed quotation.
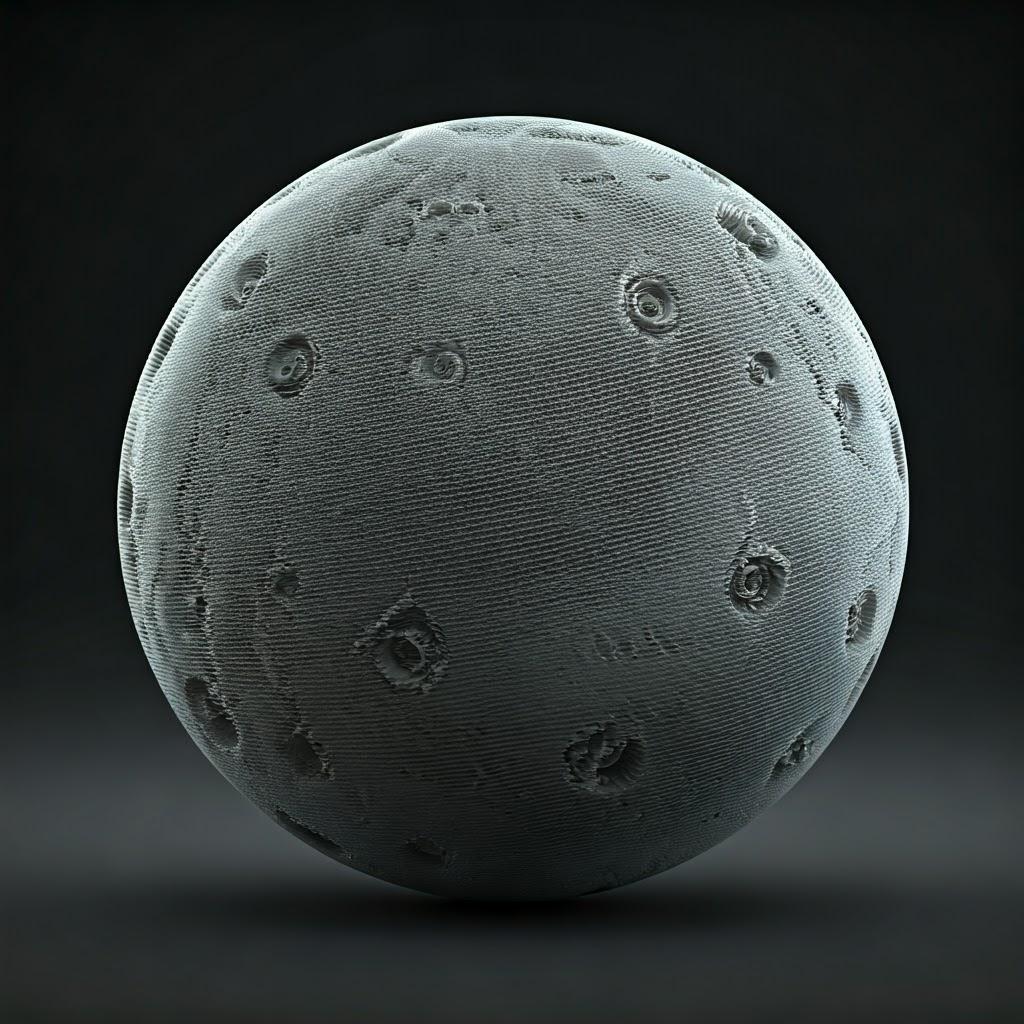
Frequently Asked Questions (FAQ) – Addressing Common Inquiries About Aerospace Cooling Shrouds
Here are some frequently asked questions regarding the use of metal 3D printing for aerospace cooling shrouds:
- Q: Can metal 3D printed cooling shrouds meet the stringent material property requirements of the aerospace industry?
- A: Yes, when using aerospace-grade metal powders and optimized printing parameters, metal 3D printed parts can achieve mechanical properties comparable to or even exceeding those of traditionally manufactured components. Rigorous testing and quality control are essential to verify these properties. Metal3DP utilizes advanced printing technologies and high-quality powders to ensure the required material properties are met.
- Q: What is the typical lifespan of a metal 3D printed cooling shroud in an aerospace application?
- A: The lifespan depends on factors such as the material used, the operating environment (temperature, pressure, corrosive agents), and the specific application. When the appropriate material is selected and the part is properly designed and post-processed, metal 3D printed cooling shrouds can offer excellent durability and a long service life in aerospace applications.
- Q: Is metal 3D printing cost-effective for producing aerospace cooling shrouds?
- A: Metal 3D printing can be highly cost-effective for complex, low to medium volume production of customized cooling shrouds, especially when considering the reduced tooling costs and design flexibility. For very high production volumes of simple geometries, traditional methods might still be more economical. Metal3DP offers competitive pricing and can help you assess the cost-effectiveness of 3D printing for your specific needs.
- Q: What kind of design support does Metal3DP offer for aerospace cooling shrouds?
- A: Metal3DP provides comprehensive design and engineering support, including topology optimization, design for additive manufacturing (DFAM) guidance, material selection advice, and simulation services to ensure your cooling shroud designs are optimized for performance and manufacturability. Our experienced team can help you leverage the full potential of metal 3D printing.
Conclusion – Embracing Metal 3D Printing for Next-Generation Aerospace Cooling Solutions
The aerospace industry is constantly pushing the boundaries of innovation, demanding lighter, more efficient, and higher-performing components. Metal 3D printing stands at the forefront of this evolution, offering unparalleled design freedom, material versatility, and the potential for significant advancements in the development and manufacturing of critical parts like cooling shrouds.
By embracing metal additive manufacturing, aerospace engineers and procurement managers can unlock new possibilities in thermal management, achieving complex geometries, optimizing for weight reduction, and accelerating development cycles. The ability to use high-performance materials like IN625 and AlSi10Mg, tailored to specific application requirements, further enhances the value proposition of this technology.
At Metal3DP, we are committed to empowering the aerospace industry with cutting-edge metal 3D printing solutions. Our industry-leading SEBM printers, advanced metal powders, and comprehensive application development services enable our partners to create next-generation cooling shrouds with superior performance and reliability. We understand the critical nature of aerospace components and are dedicated to meeting the highest standards of quality and precision.
Contact Metal3DP today to explore how our metal 3D printing capabilities can transform your aerospace manufacturing processes and drive innovation in your organization. Let us be your trusted partner in realizing the full potential of additive manufacturing for your cooling shroud needs and beyond.
Share On
MET3DP Technology Co., LTD is a leading provider of additive manufacturing solutions headquartered in Qingdao, China. Our company specializes in 3D printing equipment and high-performance metal powders for industrial applications.
Inquiry to get best price and customized Solution for your business!
Related Articles
About Met3DP
Recent Update
Our Product
CONTACT US
Any questions? Send us message now! We’ll serve your request with a whole team after receiving your message.
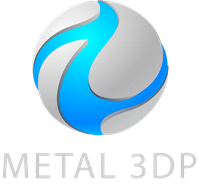
Metal Powders for 3D Printing and Additive Manufacturing