Corrosion-Resistant Pipe Fittings in 316L Stainless Steel
Table of Contents
Introduction: The Critical Role of Corrosion-Resistant Pipe Fittings in Modern Industry
Pipe fittings are the unsung heroes of countless industrial systems. These essential components connect pipes, redirect flow, change pipe size, and control fluid movement within complex networks. From vast chemical processing plants and offshore oil rigs to sterile pharmaceutical manufacturing lines and food processing facilities, the reliability of piping systems hinges directly on the integrity of their fittings. However, in many demanding environments, standard materials fall short. The pervasive threat of corrosion – the gradual degradation of materials due to chemical reactions with their environment – can lead to leaks, system failures, costly downtime, contamination, and significant safety hazards. This is where the specification of corrosion-resistant materials becomes not just beneficial, but absolutely critical for operational success, safety, and longevity.
For decades, materials like stainless steels have been the go-to solution. Among them, 316L stainless steel stands out as a workhorse alloy, prized for its excellent resistance to a wide range of corrosive media, particularly chlorides, making it ideal for marine, chemical, and food-grade applications. Its low carbon content (“L”) further enhances its weldability and resistance to sensitization, a form of intergranular corrosion. When standard 316L isn’t quite enough, advanced alloys like 254SMO offer even greater resilience in highly aggressive environments.
Traditionally, manufacturing these fittings involved processes like casting, forging, and machining. While effective, these methods often come with limitations, including long lead times for tooling, design constraints, material waste, and difficulties in producing complex or customized geometries efficiently, especially for small-to-medium volume orders or replacement parts. This is where a paradigm shift is occurring, driven by advancements in metal additive manufacturing (AM), commonly known as metal 3D printing.
Metal AM enables the direct fabrication of dense, functional metal parts, including intricate pipe fittings, layer by layer from a digital design file using specialized metal powders. This technology unlocks unprecedented design freedom, facilitates rapid prototyping and on-demand production, minimizes material waste, and allows for the creation of optimized, high-performance components that were previously difficult or impossible to manufacture. For engineers designing next-generation fluid systems and procurement managers seeking robust, reliable, and efficiently sourced components, understanding the intersection of corrosion-resistant materials like 316L and the capabilities of metal AM is becoming increasingly vital. Companies like Met3dp, specializing in both advanced metal powders and industrial 3D printing systems, are at the forefront of providing these innovative solutions, offering pathways to enhanced performance and optimized supply chains. This article delves into the specifics of using metal 3D printing, particularly with 316L and related alloys, to produce high-performance, corrosion-resistant pipe fittings for demanding industrial applications.
Applications Unveiled: Where are 316L Corrosion-Resistant Pipe Fittings Essential?
The demand for corrosion-resistant pipe fittings, particularly those made from 316L stainless steel, spans a vast spectrum of industries where fluid handling under challenging conditions is paramount. The inherent properties of 316L – its resistance to pitting and crevice corrosion caused by chlorides, its durability, and its hygienic qualities – make it indispensable in applications where lesser materials would quickly fail. Let’s explore some key sectors and specific use cases:
1. Chemical Processing Industry (CPI):
- Environment: Exposure to a wide array of acids, alkalis, solvents, and intermediate chemicals, often at elevated temperatures and pressures.
- Applications: Connecting reactors, distillation columns, heat exchangers, storage tanks, and transfer lines. Fittings like elbows, tees, reducers, and flanges must reliably contain potentially hazardous materials without degradation.
- Why 316L/254SMO? 316L provides broad resistance suitable for many common chemicals. For highly concentrated chlorides, sulfuric acid, or other aggressive media, the superior resistance of super austenitic stainless steels like 254SMO might be specified by process engineers. Preventing contamination and ensuring long service life are critical for plant safety and economics. Procurement managers in CPI look for reliable suppliers offering bulk supply options and documented material traceability.
2. Marine and Offshore:
- Environment: Constant exposure to saltwater (high chloride concentration), salt spray, and humid, corrosive atmospheres. Biofouling can also exacerbate corrosion.
- Applications: Seawater cooling systems, ballast water management systems, hydraulic lines, desalination plants (especially feed water and brine handling), and general plumbing on ships and offshore platforms.
- Why 316L/254SMO? 316L offers good performance in marine atmospheres and general seawater applications. However, in stagnant seawater, low-flow conditions, or crevices (like under flange gaskets), pitting and crevice corrosion can be concerns. 254SMO, with its higher molybdenum and nitrogen content, provides significantly better resistance to these localized corrosion forms, making it ideal for critical seawater systems and desalination components. Sourcing industrial-grade marine fittings requires adherence to specific maritime standards and certifications.
3. Oil and Gas (Upstream, Midstream, Downstream):
- Environment: Exposure to corrosive elements like hydrogen sulfide (H2S – sour gas), carbon dioxide (CO2), chlorides (in produced water), and various hydrocarbons, often under high pressure and temperature.
- Applications: Flowlines, processing equipment piping, injection lines (water, chemicals), utility systems on platforms and refineries.
- Why 316L/254SMO? 316L is used in less severe service conditions, particularly in utility systems or where chloride and H2S levels are controlled. However, for handling sour gas or high-chloride produced water, more resistant alloys are often required. While duplex stainless steels are common, 254SMO can be a viable alternative in specific high-chloride, moderate-temperature applications where superior pitting resistance is needed. The reliability of every single fitting is paramount due to the extreme pressures and hazardous nature of the fluids.
4. Pharmaceutical and Biotechnology:
- Environment: Stringent requirements for purity, cleanability, sterilizability, and resistance to corrosion from process fluids and cleaning agents (e.g., Clean-in-Place/Sterilize-in-Place systems using caustics, acids, steam).
- Applications: Process piping for bioreactors, fermentation tanks, purification systems (chromatography, filtration), WFI (Water For Injection) distribution loops, transfer panels.
- Why 316L? 316L is the dominant material due to its excellent cleanability, good corrosion resistance to typical pharma process fluids and cleaning chemicals, relatively low cost, and established acceptance (ASME BPE standards). Its smooth surface finish potential minimizes areas for bacterial growth. Preventing product contamination is the absolute priority. Procurement often involves sourcing hygienic fittings (sanitary clamps, Tri-Clamp® style) with specific surface finish requirements (electropolished).
5. Food and Beverage:
- Environment: Similar to pharma, requiring high levels of hygiene, cleanability, and resistance to food acids (citric, acetic), cleaning solutions, and process conditions (temperature fluctuations, steam).
- Applications: Dairy processing lines, brewery piping, juice and sauce production, water bottling plants, ingredient transfer lines.
- Why 316L? Like in pharmaceuticals, 316L is widely used for its hygienic properties, resistance to food product corrosion, and compliance with food contact regulations. Fittings must be easily cleanable and prevent any leaching into the product. The ability to source food-grade fittings quickly, sometimes in custom configurations for specific processing lines, is crucial for manufacturers.
6. Pulp and Paper:
- Environment: Highly corrosive bleaching chemicals (chlorine dioxide, peroxides), acidic process liquors, and high chloride concentrations in whitewater systems.
- Applications: Bleach plant piping, digester circulation lines, stock preparation systems, recovery boiler areas.
- Why 316L/254SMO? While 316L finds use in less aggressive areas, the extremely corrosive conditions in bleach plants often necessitate higher alloys. 254SMO is frequently specified for its outstanding resistance to chloride stress corrosion cracking and pitting/crevice corrosion in these challenging environments.
7. Water and Wastewater Treatment:
- Environment: Exposure to treated and untreated water (varying chemistries, potential for chlorides, sulfates), disinfection chemicals (chlorine, ozone), and sludge.
- Applications: Chemical dosing lines, filtration systems, aeration piping, sludge handling, desalination (as mentioned in Marine).
- Why 316L/254SMO? 316L is suitable for many municipal water applications. However, in brackish water, industrial wastewater with high chloride levels, or specific chemical treatment stages, the enhanced resistance of 254SMO or other super austenitic/duplex steels may be required for long-term reliability.
Across all these sectors, the common thread is the need for reliable, long-lasting pipe fittings that can withstand specific corrosive challenges. Engineers must carefully select materials based on the precise operating conditions, while procurement managers need access to suppliers who can provide high-quality, certified fittings, potentially leveraging advanced manufacturing methods like metal 3D printing to meet specific design needs or demanding lead times.
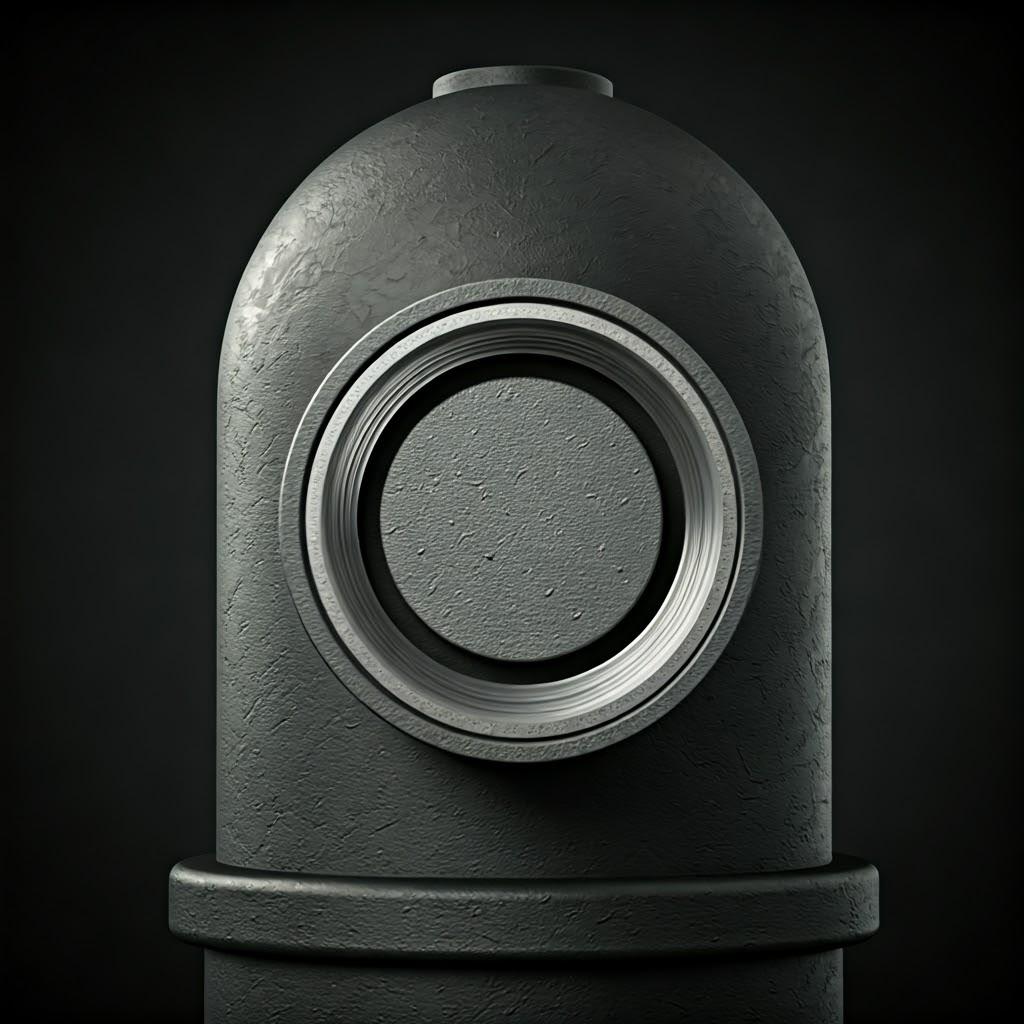
Additive Manufacturing Advantage: Why Choose Metal 3D Printing for Pipe Fittings?
While traditional manufacturing methods like casting, forging, and machining have long served the industry in producing pipe fittings, metal additive manufacturing (AM) presents a compelling suite of advantages, particularly for corrosion-resistant fittings like those made from 316L or 254SMO. These benefits resonate strongly with engineers seeking optimal performance and procurement managers focused on efficiency, cost-effectiveness, and supply chain resilience.
1. Unmatched Design Freedom and Complexity:
- Challenge with Traditional Methods: Casting requires molds, limiting internal complexity and often resulting in bulky designs. Machining starts with solid stock, generating significant waste and struggling with intricate internal channels or blended surfaces. Forging provides strength but is limited to relatively simple shapes.
- AM Advantage: Metal AM builds parts layer-by-layer directly from a CAD model. This allows for:
- Optimized Internal Geometries: Designing fittings with smoother internal flow paths, reducing pressure drop and turbulence. Internal features like flow splitters or mixers can be integrated directly.
- Part Consolidation: Combining multiple components of a fitting assembly into a single printed part, reducing potential leak points, assembly time, and inventory complexity.
- Complex External Shapes: Creating fittings tailored to fit into tight spaces or integrate seamlessly with surrounding equipment, without the constraints of mold draft angles or machining tool access.
- Lightweighting: Incorporating lattice structures or topology optimization (where applicable and structurally sound) to reduce weight without compromising strength – particularly relevant in aerospace or mobile applications.
2. Speed, Agility, and Reduced Lead Times:
- Challenge with Traditional Methods: Creating patterns and molds for casting or setting up complex multi-axis machining routines can take weeks or months, especially for custom designs or low volumes. Minimum order quantities (MOQs) for casting/forging can be prohibitive for prototyping or obtaining just a few replacement parts.
- AM Advantage:
- Rapid Prototyping: Producing functional prototypes in the target material (e.g., 316L) within days allows for rapid design iteration and verification before committing to larger production runs.
- Tooling Elimination: AM is a tool-less process, eliminating the significant time and cost associated with creating, maintaining, and storing molds or specialized fixtures.
- On-Demand Production: Manufacturing fittings as needed reduces inventory holding costs and waste associated with overstocking. This is ideal for spare parts, especially for legacy systems where original suppliers may no longer exist.
- Faster Time-to-Market: For new product developments or system upgrades, AM significantly accelerates the timeline from design conception to functional part deployment. This agility is a major competitive advantage.
3. Material Efficiency and Sustainability:
- Challenge with Traditional Methods: Subtractive manufacturing (machining) can generate substantial material waste (swarf), sometimes exceeding the weight of the final part. Casting can also involve significant material in gates and risers that must be removed.
- AM Advantage: AM, specifically powder bed fusion techniques, is inherently more resource-efficient.
- Near-Net Shape: Parts are built close to their final dimensions, minimizing the material required and reducing subsequent machining needs.
- Powder Reusability: Unfused metal powder within the build chamber can often be recovered, sieved, and reused in subsequent builds (following strict quality control procedures), further improving material utilization. While not 100% waste-free, it’s a significant improvement over traditional subtractive methods.
4. Customization and Small Batch Production:
- Challenge with Traditional Methods: High setup costs make producing small batches or one-off custom fittings economically challenging using casting or forging.
- AM Advantage: Since AM doesn’t require part-specific tooling, the cost per part is less sensitive to batch size. This makes it highly cost-effective for:
- Customized Fittings: Tailoring dimensions, connection types, or internal features to specific application requirements without incurring massive tooling charges.
- Low-Volume Production: Efficiently producing niche fittings or replacement parts in small quantities.
- Bridge Production: Manufacturing initial batches of a new fitting design via AM while traditional tooling is being prepared for mass production.
5. Potential for Enhanced Performance:
- AM Advantage: The rapid solidification inherent in many metal AM processes can lead to fine-grained microstructures, which may offer improved mechanical properties (strength, fatigue resistance) compared to conventionally cast parts, although post-processing like heat treatment is crucial to optimize these properties. Furthermore, the design freedom allows for performance optimization (e.g., flow efficiency) unattainable through other means. Companies with deep materials science expertise, like Met3dp leveraging their advanced powder making systems, can ensure the resulting parts meet stringent performance requirements.
Implications for B2B Buyers and Procurement:
- Supply Chain Resilience: AM offers a digital manufacturing route, reducing reliance on geographically concentrated traditional suppliers and complex tooling supply chains. Parts can potentially be printed closer to the point of need.
- Reduced Inventory Costs: The ability to print on demand minimizes the need for large stocks of spare parts, freeing up capital and warehouse space.
- Total Cost of Ownership: While the per-part cost of AM might sometimes be higher than mass-produced traditional parts, the benefits in reduced lead times, minimized waste, lower tooling costs, reduced inventory, and potential for improved performance can lead to a lower total cost of ownership, especially for complex, custom, or low-volume fittings.
- Streamlined RFQs: Digital design files (CAD models) form the basis for AM production, potentially streamlining the Request for Quotation (RFQ) process with qualified AM service providers.
In summary, metal 3D printing offers a powerful alternative or complement to traditional methods for producing corrosion-resistant pipe fittings. Its ability to handle complexity, speed up delivery, enable customization, and potentially enhance performance makes it an increasingly attractive option for engineers and procurement professionals across demanding industries.
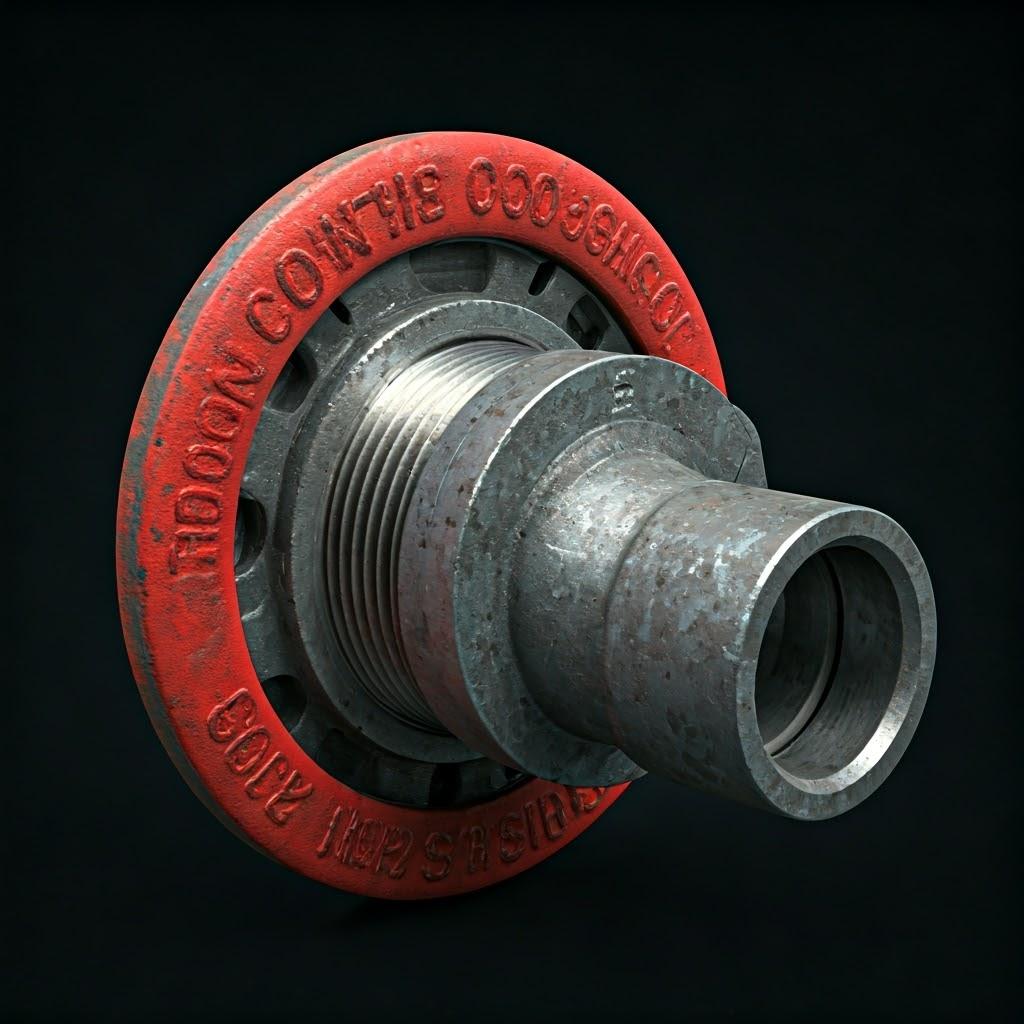
Material Matters: Deep Dive into 316L and 254SMO for Additive Manufacturing
The success of any additively manufactured component hinges critically on the quality and suitability of the material used. For corrosion-resistant pipe fittings, 316L stainless steel and the super austenitic grade 254SMO are primary candidates, each offering distinct advantages depending on the severity of the application environment. Understanding their properties, behavior during AM processing, and the importance of powder quality is essential for engineers and procurement specialists.
316L Stainless Steel (UNS S31603): The Versatile Workhorse
- Composition: An austenitic stainless steel alloy containing primarily Iron (Fe), Chromium (Cr: ~16-18%), Nickel (Ni: ~10-14%), and Molybdenum (Mo: ~2-3%). The “L” designation signifies low carbon content (<0.03%), which is crucial for minimizing sensitization (chromium carbide precipitation at grain boundaries) during welding or thermal cycles inherent in AM, thereby preserving maximum corrosion resistance, especially in the as-built or stress-relieved state.
- Key Properties:
- Excellent General Corrosion Resistance: Resists a wide variety of atmospheric, chemical, and marine environments.
- Good Pitting and Crevice Corrosion Resistance: The molybdenum content provides significantly better resistance to chloride-induced localized corrosion compared to 304/304L stainless steel.
- Good Formability and Weldability: Although less relevant for AM part formation, good weldability is important if post-print welding is required.
- Hygienic Qualities: Can achieve smooth surface finishes, making it suitable for food, beverage, and pharmaceutical applications.
- Biocompatibility: Widely used for medical implants (though specific certifications are needed for implantable use).
- Good Strength and Ductility: Offers a good balance of mechanical properties at room and moderately elevated temperatures.
- Suitability for Additive Manufacturing: 316L is one of the most common and well-characterized stainless steels used in metal AM, particularly Laser Powder Bed Fusion (L-PBF) and Electron Beam Powder Bed Fusion (EB-PBF/SEBM). Print parameters are relatively well-established, allowing for the production of high-density (>99.5%) parts with properties comparable or sometimes superior to wrought counterparts after appropriate post-processing (like stress relief or solution annealing).
- Corrosion Mechanism Resistance: Primarily resists uniform corrosion and offers good defense against chloride pitting and crevice corrosion in moderate environments due to the protective passive chromium oxide layer, enhanced by molybdenum.
- Applications in AM Fittings: Ideal for general chemical processing, food/beverage lines, pharmaceutical systems, marine hardware (above waterline or moderate exposure), architectural elements, and water treatment components where good corrosion resistance and cleanability are required.
254SMO® (UNS S31254): Superior Resistance for Extreme Conditions
- Composition: A high-alloy “super austenitic” stainless steel. Compared to 316L, it contains significantly higher levels of Chromium (~20%), Nickel (~18%), and Molybdenum (~6%), along with an important addition of Nitrogen (~0.2%). (Note: 254SMO is a trademark of Outokumpu).
- Key Properties:
- Exceptional Pitting and Crevice Corrosion Resistance: The high Cr, Mo, and N content results in a very high Pitting Resistance Equivalent Number (PREN = Cr% + 3.3 * Mo% + 16 * N%), typically >42, indicating outstanding resistance in high-chloride environments like seawater, brackish water, and bleach solutions. Significantly superior to 316L (PREN ~24).
- High Resistance to Chloride Stress Corrosion Cracking (SCC): Offers better resistance to SCC than standard 300-series stainless steels, although not immune.
- High Strength: Possesses higher yield and tensile strength compared to 316L.
- Good Weldability: Can be welded, but requires appropriate procedures and filler metals.
- Good Ductility and Toughness: Maintains good toughness even at low temperatures.
- Suitability for Additive Manufacturing: While less common than 316L, 254SMO powder is available and can be processed using AM techniques like L-PBF. Achieving optimal properties and corrosion resistance requires careful parameter development and often specific post-processing heat treatments (typically solution annealing at high temperatures followed by rapid quenching) to ensure the alloying elements are properly dissolved and detrimental phases are avoided. Processing can be more challenging than 316L due to the higher alloy content.
- Corrosion Mechanism Resistance: Specifically designed to combat severe pitting, crevice corrosion, and SCC in aggressive chloride-containing media where 316L would be inadequate. The high alloy content creates a very stable and rapidly repairing passive film.
- Applications in AM Fittings: Targeted for highly demanding applications such as desalination plant components (brine heaters, piping), pulp and paper bleach plants, offshore platform seawater handling systems, chemical processing equipment handling concentrated chlorides or acids, and flue gas desulfurization units.
Why Material Powder Quality Matters in AM
Regardless of the alloy chosen, the quality of the metal powder used in the AM process is paramount for producing reliable, high-performance pipe fittings. This is where specialized powder manufacturers like Met3dp play a crucial role. Key powder characteristics include:
- Sphericity: Highly spherical powder particles ensure good flowability within the AM machine’s recoating system and lead to denser, more uniform packing in the powder bed. This contributes significantly to achieving high part density and minimizing porosity. Met3dp utilizes advanced gas atomization and Plasma Rotating Electrode Process (PREP) technologies designed to produce powders with high sphericity.
- Particle Size Distribution (PSD): A controlled PSD, optimized for the specific AM process (e.g., L-PBF, SEBM), is critical for consistent melting, good surface finish, and predictable part properties. Too many fine particles can hinder flowability and pose safety risks, while too many large particles can lead to incomplete melting and porosity.
- Chemical Composition: The powder chemistry must strictly adhere to the specified alloy standard (e.g., ASTM standards for 316L or S31254). Contamination or deviations can compromise corrosion resistance and mechanical properties. Rigorous quality control during powder production and handling is essential.
- Flowability: As mentioned, good flowability ensures uniform powder layer deposition, which is fundamental for consistent melting and defect-free parts.
- Absence of Satellites and Porosity: High-quality powders should have minimal satellites (smaller particles attached to larger ones) and low internal porosity, both of which can negatively impact packing density and final part quality.
Met3dp’s Role in Material Excellence:
Met3dp’s commitment to utilizing industry-leading atomization technologies and rigorous quality control ensures their high-quality metal powders, including stainless steels like 316L and potentially advanced alloys, meet the demanding requirements for critical applications like corrosion-resistant pipe fittings. Their expertise in powder manufacturing translates directly into enabling the production of dense, reliable, high-performance AM components with superior mechanical properties and corrosion resistance. When sourcing AM fittings, understanding the powder source and the supplier’s commitment to material quality is as important as the printing process itself.
Comparative Overview Table:
Feature | 316L Stainless Steel (UNS S31603) | 254SMO® (UNS S31254) |
---|---|---|
Primary Application | General corrosion resistance, moderate chlorides | Severe chloride environments, high pitting resistance |
Key Alloying Elements | Cr (~17%), Ni (~12%), Mo (~2.5%), Low C (<0.03%) | Cr (~20%), Ni (~18%), Mo (~6%), N (~0.2%) |
PREN (Typical) | ~24 | >42 |
Pitting/Crevice Resist. | Good | Excellent |
Chloride SCC Resistance | Moderate | Good |
Strength | Good | High |
AM Processability | Well-established, relatively easy | More challenging, requires careful parameter control |
Common AM Post-Process | Stress Relief / Solution Anneal | Solution Anneal & Quench |
Relative Cost | Lower | Higher |
Suitable Industries | CPI (general), Food/Bev, Pharma, Marine (mod.) | Desalination, Pulp/Paper (Bleach), Offshore (severe) |
Export to Sheets
Choosing between 316L and 254SMO for an additively manufactured pipe fitting requires a thorough analysis of the service environment, performance requirements, and budget, always ensuring the use of high-quality, process-optimized metal powder.
Designing for Durability: Key Considerations for AM Pipe Fittings
Transitioning the design of a pipe fitting from traditional manufacturing methods to additive manufacturing isn’t just a matter of converting a file format. To fully leverage the benefits of AM and ensure the production of robust, reliable, and cost-effective corrosion-resistant fittings (like those from 316L or 254SMO), engineers must embrace Design for Additive Manufacturing (DfAM) principles. DfAM goes beyond simple geometry replication; it involves optimizing the design to suit the layer-by-layer building process, minimizing potential issues, and maximizing performance. For critical components like pipe fittings, durability under pressure, flow efficiency, and ease of integration are paramount.
Here are key design considerations for AM pipe fittings:
1. Optimize for Flow Efficiency:
- Challenge: Abrupt changes in direction (sharp elbows), sudden contractions/expansions, or internal obstructions can create turbulence, increase pressure drop, and potentially accelerate erosion or localized corrosion. Traditional manufacturing often imposes limitations on creating smooth, optimized internal pathways.
- DfAM Solution: AM allows for the creation of fittings with:
- Sweeping Bends: Replace sharp 90-degree turns with smoother, larger-radius bends to minimize flow separation and pressure loss.
- Gradual Transitions: Design reducers or expanders with gentler taper angles for more efficient flow adaptation.
- Integrated Flow Guides: Incorporate internal vanes or features to direct flow smoothly, especially in complex junctions like tees or manifolds, potentially reducing the need for separate flow conditioning elements downstream.
- Computational Fluid Dynamics (CFD): Use CFD analysis early in the design phase to simulate fluid flow through the AM-designed fitting, identify areas of high turbulence or low pressure, and iteratively refine the geometry for optimal hydraulic performance before printing.
2. Manage Wall Thickness:
- Challenge: Walls that are too thin may not print accurately, could be fragile, or may not meet pressure containment requirements according to relevant piping codes (e.g., ASME B31.3). Walls that are excessively thick increase material consumption, print time, cost, and potentially residual stress.
- DfAM Solution:
- Minimum Printable Thickness: Understand the minimum wall thickness achievable with the chosen AM process (L-PBF, SEBM) and material (e.g., typically 0.4-1.0 mm, but varies). Design walls above this threshold.
- Pressure Calculations: Perform necessary engineering calculations (based on design pressure, temperature, material allowable stress, and fitting geometry) to determine the required minimum wall thickness for pressure containment. Factor in appropriate safety margins and corrosion allowances if applicable.
- Uniformity (where possible): Aim for relatively uniform wall thicknesses throughout the fitting to promote consistent cooling rates during printing, reducing the risk of warping and residual stress buildup. Where thickness changes are necessary, implement gradual transitions.
- Topology Optimization: For non-pressurized structural elements or applications where weight is critical (e.g., aerospace), topology optimization software can help remove material from low-stress areas while maintaining structural integrity, but this must be carefully applied to pressure-retaining components.
3. Strategize Support Structures:
- Challenge: Powder bed fusion processes typically require support structures for overhanging features (usually angles below 45 degrees from the horizontal) and to anchor the part to the build plate, preventing warping. Internal supports within complex fitting geometries can be extremely difficult or impossible to remove after printing.
- DfAM Solution:
- Self-Supporting Angles: Design overhangs with angles greater than 45 degrees wherever possible to minimize the need for supports. Utilize chamfers or tear-drop shapes for holes on horizontal surfaces.
- Build Orientation: Carefully consider the optimal build orientation. Orienting the fitting to minimize downward-facing surfaces and internal overhangs can significantly reduce support requirements. For example, printing a standard elbow on its side might require less internal support than printing it upright. This is a key aspect where collaboration with an experienced AM provider like Met3dp, knowledgeable about various printing methods and their constraints, is invaluable.
- Accessible Internal Supports: If internal supports are unavoidable, design them for accessibility. This might involve incorporating access ports (that can be plugged or welded shut later) or designing supports that are frangible or can be dissolved chemically (less common for 316L/254SMO). Sometimes, a design must be split into multiple pieces to allow internal support removal and then joined post-print (e.g., welding).
- Support Optimization Software: Utilize advanced AM preparation software to generate efficient support structures that use minimal material, are easy to remove, and provide adequate thermal conduction and anchoring.
4. Incorporate Functional Features:
- Challenge: Traditional fittings might require separate components or post-machining for features like wrench flats, mounting brackets, or sensor ports.
- DfAM Solution: AM allows these features to be integrated directly into the printed fitting design:
- Wrench Flats: Design hexagonal or flattened sections for easy gripping during installation and removal.
- Mounting Bosses/Brackets: Integrate mounting points directly into the fitting body, reducing part count and assembly complexity.
- Sensor Ports: Design threaded or flanged ports for pressure gauges, temperature sensors, or sampling points directly into the fitting wall (ensure adequate wall thickness around ports).
- Markings: Embed part numbers, material designations, flow indicators, or logos directly onto the surface during the printing process.
5. Minimize Stress Concentrations:
- Challenge: Sharp internal corners, abrupt changes in cross-section, and areas around connections (threads, flanges) can act as stress risers, potentially leading to fatigue failure or crack initiation under pressure cycling or vibration.
- DfAM Solution:
- Filleting and Radiusing: Apply generous fillets and radii to all internal and external corners to distribute stress more evenly.
- Smooth Transitions: Ensure gradual changes in geometry and wall thickness.
- Reinforcement: Consider adding extra material (local thickening) in high-stress areas identified through Finite Element Analysis (FEA). FEA should be strongly considered for critical fittings, especially those with complex geometries or operating under high pressure/temperature or cyclic loading.
DfAM Considerations Summary Table:
DfAM Principle | Objective | Key Actions | Benefit |
---|---|---|---|
Flow Optimization | Minimize pressure drop, turbulence | Use sweeping bends, gradual transitions, integrated guides; CFD analysis | Improved system efficiency, reduced erosion/corrosion |
Wall Thickness Mgmt | Ensure pressure integrity, printability, cost | Adhere to min. thickness, perform pressure calcs, aim for uniformity, use transitions | Structural integrity, reliable printing, optimized material usage |
Support Strategy | Minimize supports, ensure removability | Design self-supporting angles, optimize orientation, design accessible supports | Reduced post-processing time/cost, improved internal surface quality |
Feature Integration | Reduce part count, simplify assembly | Embed wrench flats, mounts, ports, markings directly into the design | Lower assembly effort, improved functionality, better traceability |
Stress Reduction | Enhance fatigue life, prevent failure | Use fillets/radii, smooth transitions, reinforcement; FEA analysis | Increased durability, higher safety factor, longer service life |
Export to Sheets
By thoughtfully applying these DfAM principles, engineers can design corrosion-resistant pipe fittings in 316L or 254SMO that are not only manufacturable via AM but are also optimized for performance, durability, and cost-effectiveness, meeting the stringent demands of industrial B2B applications.
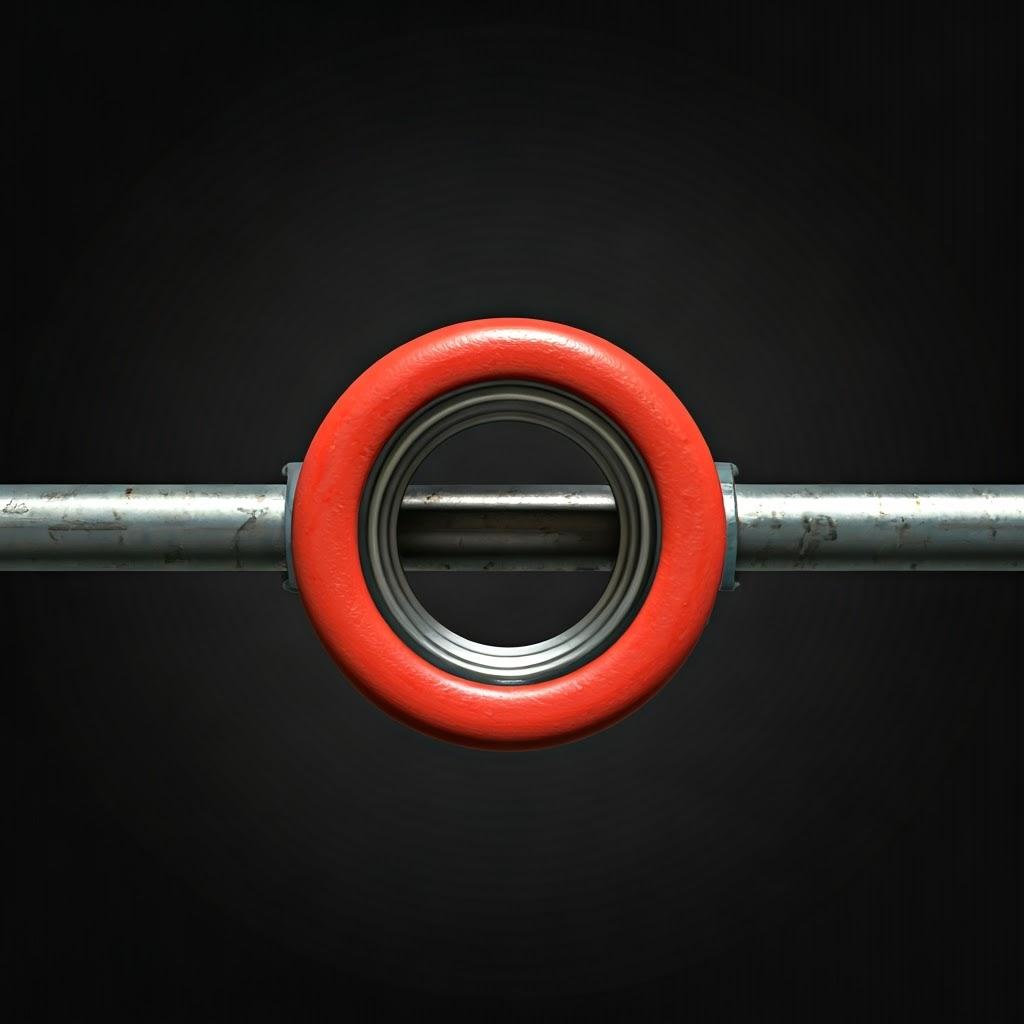
Precision Performance: Achieving Tight Tolerances and Surface Finish
While metal additive manufacturing offers remarkable geometric freedom, achieving the necessary precision for functional pipe fittings – especially at connection points and sealing surfaces – requires careful consideration of tolerances and surface finish. Engineers and procurement managers must understand the typical capabilities of AM processes like L-PBF and SEBM for materials like 316L and 254SMO, and recognize where post-processing becomes essential to meet specifications.
Dimensional Accuracy and Tolerances:
- As-Built Accuracy: The dimensional accuracy of a part directly off the AM machine depends on several factors, including the specific machine, process parameters, material (316L and 254SMO generally behave well), part size and geometry, and build orientation. Typical achievable tolerances for medium-sized parts (e.g., up to 150-200 mm) are often in the range of:
- L-PBF: ±0.1 mm to ±0.2 mm or ±0.1-0.2% of the nominal dimension, whichever is greater.
- SEBM: Often slightly less accurate than L-PBF in the as-built state, perhaps ±0.2 mm to ±0.4 mm or ±0.5-1.0%. However, SEBM produces parts with lower residual stress, potentially reducing distortion during post-processing.
- Factors Influencing Accuracy:
- Thermal Effects: Residual stress buildup during printing and subsequent stress relief heat treatment can cause minor distortion or shrinkage, which must be anticipated and potentially compensated for in the design or build preparation stage.
- Support Structures: The location and removal of support structures can slightly affect the dimensions and surface quality of the supported areas.
- Part Complexity & Size: Larger and more complex parts are generally more prone to deviation.
- Meeting Tight Tolerances: For critical dimensions, such as:
- Flange Bolt Holes: Precise location and diameter for proper alignment and bolt insertion.
- Flange Sealing Faces: Flatness and parallelism specifications are crucial for effective gasket sealing.
- Threaded Connections (Internal/External): Adherence to thread standards (e.g., NPT, BSP, ISO) is vital for leak-tight joints.
- Pipe Schedule Dimensions: Outer diameter (OD) and inner diameter (ID) must match standard pipe sizes for proper connection (e.g., welding, compression fitting).
- Overall Length/Alignment: Critical for fitting into existing pipe runs. It is generally necessary to incorporate post-machining operations for these features. While AM can produce near-net shapes, achieving tolerances tighter than ~±0.1 mm or specific geometric dimensioning and tolerancing (GD&T) callouts (like flatness, perpendicularity, runout) usually requires CNC machining after printing and heat treatment. Designs should include adequate machining allowance (e.g., 0.5-2.0 mm) on surfaces requiring tight tolerances.
Surface Finish (Roughness):
- As-Built Surface Roughness (Ra): The surface finish of AM parts is inherently rougher than machined surfaces due to the layer-wise construction and partially melted powder particles adhering to the surface. Typical as-built Ra values:
- Top Surfaces: Generally smoother, perhaps Ra 5-15 µm.
- Vertical Walls: Moderate roughness, Ra 8-20 µm.
- Overhanging/Supported Surfaces: Typically the roughest, potentially Ra 15-30 µm or higher, depending on support type and removal method.
- Internal Channels: Can be challenging to control and measure; often rougher than external surfaces.
- Impact of Surface Finish:
- Sealing: Rough surfaces on flange faces or threaded connections can create leak paths.
- Flow Resistance: Rough internal surfaces increase friction and pressure drop.
- Corrosion: Rougher surfaces can potentially trap contaminants or create initiation sites for crevice corrosion, although the inherent passivity of 316L/254SMO mitigates this significantly compared to less resistant alloys.
- Cleanability: Critical in hygienic applications (pharma, food); smoother surfaces are easier to clean and less prone to bacterial adhesion.
- Achieving Desired Surface Finish: For most industrial pipe fitting applications, the as-built surface finish is often acceptable for non-critical external surfaces. However:
- Sealing Surfaces: Almost always require post-machining (turning, milling, grinding) to achieve smooth, flat finishes (e.g., Ra 1.6 µm, 0.8 µm, or even smoother depending on gasket type and pressure). Specific lay patterns (e.g., phonographic/serrated finishes for flanges) may be required.
- Hygienic Applications: May require mechanical polishing and/or electropolishing to achieve very low Ra values (e.g., <0.8 µm or <0.4 µm) for optimal cleanability and corrosion resistance.
- Improved Flow: Internal polishing or abrasive flow machining might be considered for high-performance applications, although this can be complex and costly for intricate fittings.
- General Improvement: Surface treatments like bead blasting or tumbling can provide a more uniform, matte finish and remove loose powder particles, slightly improving the Ra value compared to the raw as-built state.
Quality Control and Metrology:
Ensuring fittings meet the required precision involves rigorous quality control:
- Dimensional Inspection: Using calibrated tools like calipers, micrometers, height gauges, and Coordinate Measuring Machines (CMMs) to verify critical dimensions against drawings and specifications. 3D scanning can also be used for comparing the final part to the original CAD model.
- Surface Roughness Measurement: Using profilometers to quantify the Ra value on critical surfaces.
- GD&T Checks: Verifying geometric tolerances like flatness, parallelism, concentricity, etc., using appropriate metrology equipment.
Supplier Capability: When sourcing AM pipe fittings, it’s crucial to partner with a provider like Met3dp, whose industrial printers are known for industry-leading print volume, accuracy and reliability. A capable supplier will understand the achievable tolerances of their machines, provide guidance on necessary post-processing, and have robust quality management systems (e.g., ISO 9001 certification) and metrology capabilities to verify that the final parts meet all engineering specifications. Clear communication of tolerance and surface finish requirements on engineering drawings is essential for successful procurement.
Beyond the Print: Essential Post-Processing for 3D Printed Pipe Fittings
Creating a dimensionally accurate pipe fitting with the desired geometry on a metal 3D printer is only the first step. For materials like 316L and 254SMO, especially when used in demanding industrial applications, a series of crucial post-processing steps are typically required to transform the as-built part into a functional, reliable, and safe component. These steps are essential for achieving the required mechanical properties, dimensional tolerances, surface characteristics, and overall integrity. Procurement managers and engineers must factor these processes into project timelines and cost estimations.
Common Post-Processing Steps for AM Pipe Fittings (316L/254SMO):
- Stress Relief Heat Treatment:
- Purpose: The rapid heating and cooling cycles inherent in powder bed fusion processes (especially L-PBF) generate significant residual stresses within the printed part. These stresses can cause distortion or warping after removal from the build plate, reduce mechanical performance (especially fatigue life), and increase susceptibility to stress corrosion cracking in certain environments. Stress relief aims to reduce these internal stresses without significantly altering the microstructure or hardness.
- Process: Typically involves heating the part (while often still attached to the build plate) in a controlled atmosphere furnace (e.g., argon or vacuum to prevent oxidation) to a specific temperature below the alloy’s annealing temperature (e.g., for 316L, common stress relief cycles might be around 650°C, but optimal cycles depend on specific requirements and can range higher; 254SMO may require different cycles). The part is held at temperature for a defined period, followed by slow, controlled cooling.
- Importance: This is arguably the most critical initial post-processing step for dimensionally sensitive parts and for ensuring optimal performance. It should generally be performed before removing the part from the build plate.
- Part Removal & Cleaning:
- Purpose: Separating the printed fitting(s) from the build plate and removing any loose or semi-sintered powder.
- Process: Parts are typically cut from the build plate using wire EDM (Electrical Discharge Machining) or a bandsaw. Excess powder is removed using brushes, vacuum systems, and compressed air blasting in a controlled environment (powder handling requires safety precautions).
- Support Structure Removal:
- Purpose: Removing the temporary structures used to support overhangs and anchor the part during printing.
- Process: This can be a labor-intensive step, often involving manual breaking or cutting (using pliers, grinders, hand tools) or machining (milling). The ease of removal depends heavily on the DfAM principles applied (see Subheading 5). Careful removal is needed to avoid damaging the part surface. Areas where supports were attached will typically have a rougher surface finish that may require further refinement.
- Hot Isostatic Pressing (HIP) – (Optional but Recommended for Critical Applications):
- Purpose: To eliminate residual internal microporosity that might remain after the AM process. Porosity can act as stress concentrators, reducing fatigue life and potentially creating leak paths in pressure-retaining components. HIP significantly improves material density, ductility, fatigue strength, and impact toughness.
- Process: Involves placing the part in a specialized high-pressure vessel, heating it to an elevated temperature (below melting point, often similar to solution annealing temperatures), and simultaneously applying high inert gas pressure (e.g., Argon) uniformly from all directions (typically 100 MPa or more). This pressure collapses internal voids.
- Consideration: HIP adds cost and lead time but provides a significant boost in material integrity, often making the AM part’s properties equivalent or superior to wrought material. It’s strongly recommended for fittings in high-pressure, fatigue-critical, or extreme-temperature service.
- Solution Annealing (Especially for 254SMO or after HIP/Welding):
- Purpose: To dissolve any detrimental secondary phases (like sigma phase) that may have formed during printing or previous thermal cycles, homogenize the microstructure, and restore maximum corrosion resistance and ductility. Particularly important for high-alloy materials like 254SMO or if significant welding has been performed. For 316L, it might be performed after HIP or if specific properties are required, but simple stress relief is often sufficient.
- Process: Involves heating the part to a higher temperature than stress relief (e.g., ~1050-1150°C for 316L, potentially higher for 254SMO) for a specific duration, followed by rapid cooling (quenching, typically in water) to prevent the re-precipitation of undesirable phases. Must be done in a controlled atmosphere or vacuum.
- CNC Machining:
- Purpose: To achieve tight dimensional tolerances, specific geometric features (GD&T), and required surface finishes on critical areas that cannot be met by the as-built AM process.
- Process: Utilizing milling, turning, drilling, tapping, or grinding operations. As discussed previously, this is essential for:
- Flange faces (flatness, smoothness, serrations)
- Threaded connections (correct profile and size)
- Sealing surfaces (O-ring grooves, gasket seats)
- Precise overall lengths or alignment features
- Pipe end preparation for welding (beveling)
- Requirement: Designs must include sufficient machining stock on relevant surfaces.
- Surface Finishing:
- Purpose: To improve surface roughness, cleanability, aesthetics, or prepare for coating.
- Process: Options include:
- Bead Blasting/Sand Blasting: Creates a uniform matte finish, removes minor surface imperfections and discoloration from heat treatment.
- Tumbling/Vibratory Finishing: Uses abrasive media in a rotating or vibrating drum to deburr edges and provide a smoother, more uniform finish, especially for batches of smaller parts.
- Manual Grinding/Polishing: Targeted removal of support witnesses or achieving specific finishes on accessible surfaces.
- Electropolishing: An electrochemical process that removes a microscopic layer of material, resulting in a very smooth, clean, passive, and often brighter surface. Widely used for hygienic applications (pharma, food) to enhance cleanability and corrosion resistance.
- Passivation:
- Purpose: To enhance the natural corrosion resistance of stainless steels (including 316L and 254SMO) by removing any free iron or other contaminants from the surface and thickening the passive chromium oxide layer. While stainless steels are inherently passive, processes like machining, handling, or even exposure to shop air can introduce contaminants.
- Process: Typically involves immersing the fitting in a mild oxidant solution, such as nitric acid or citric acid solution (specific concentration, temperature, and time depend on the standard, e.g., ASTM A967).
- Importance: Often a standard requirement, especially for chemical, pharmaceutical, and food-grade applications, to ensure maximum corrosion performance from the outset.
- Inspection and Testing:
- Purpose: To verify that the finished fitting meets all specified requirements before shipment or installation.
- Process: Includes:
- Final Dimensional Inspection: Verifying all critical dimensions and GD&T callouts after all machining and finishing steps.
- Visual Inspection: Checking for surface defects, proper finishing, and markings.
- Leak Testing (Pressure Testing): Essential for pressure-retaining components. Hydrostatic testing (using water) or pneumatic testing (using air or nitrogen) is performed at a specified pressure (typically 1.5x design pressure) to ensure no leaks.
- Non-Destructive Testing (NDT): For highly critical applications, methods like Dye Penetrant Testing (PT) to detect surface-breaking cracks, Magnetic Particle Testing (MT – less common for austenitic steels), Radiographic Testing (RT – X-ray) to detect internal voids or inclusions, or Ultrasonic Testing (UT) may be specified.
- Material Certification Review: Ensuring traceability and conformity of the powder used and verification of post-processing steps like heat treatment.
The specific sequence and necessity of these steps depend heavily on the fitting’s design complexity, material, application criticality, and governing industry standards. Collaborating with an experienced AM service provider who offers comprehensive post-processing capabilities is crucial for ensuring the final corrosion-resistant pipe fitting meets all performance and quality expectations.
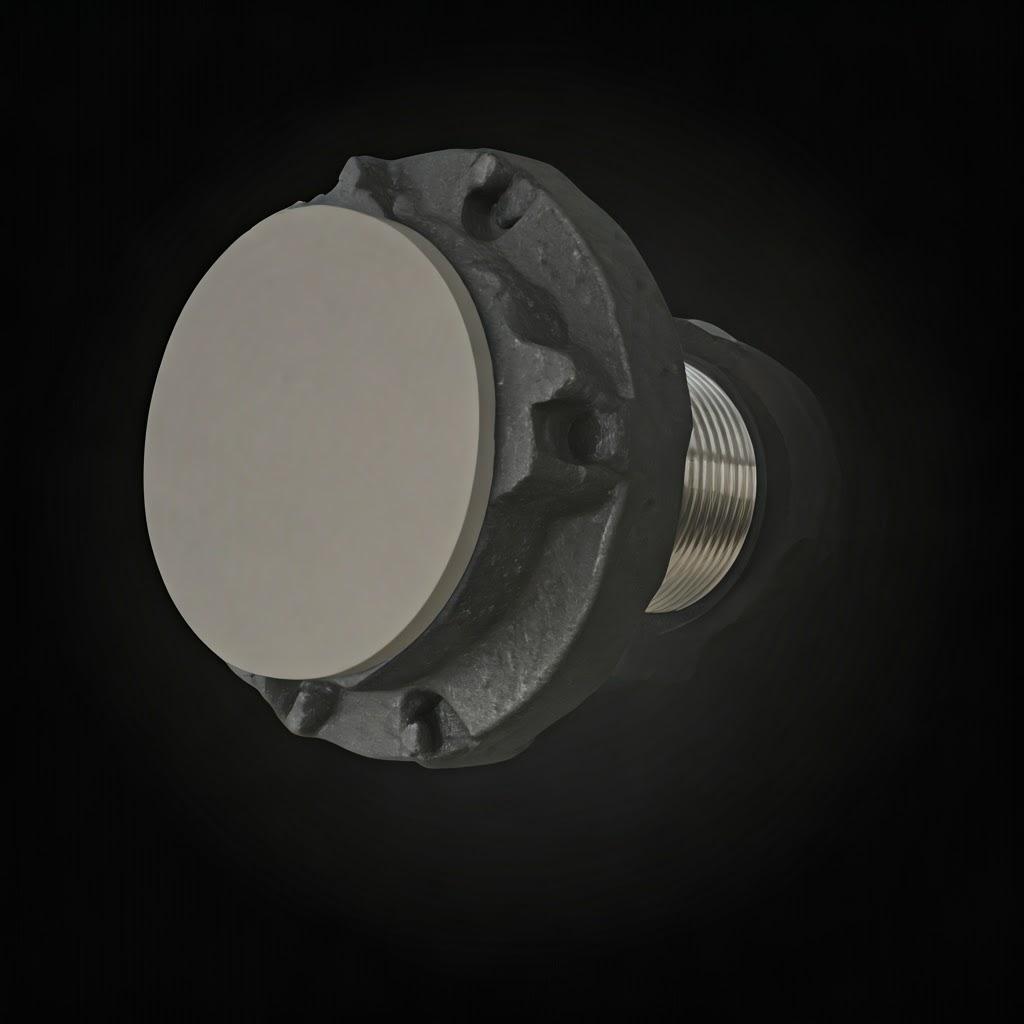
Navigating Challenges: Overcoming Hurdles in Metal AM for Fittings
While metal additive manufacturing offers significant advantages for producing corrosion-resistant pipe fittings, like any advanced manufacturing process, it presents its own set of potential challenges. Recognizing these hurdles and implementing appropriate mitigation strategies – often through a combination of smart design (DfAM), optimized process parameters, meticulous post-processing, and robust quality control – is key to successfully leveraging AM for demanding industrial applications. Partnering with an experienced provider like Met3dp, with decades of collective expertise in metal additive manufacturing, can significantly help navigate these complexities.
Here are some common challenges and how to address them:
1. Warping and Distortion (Residual Stress):
- Challenge: The intense localized heating and rapid cooling during powder bed fusion builds up internal stresses. Upon removal from the build plate or during subsequent heat treatment, these stresses can cause the part to warp, distort, or even crack, compromising dimensional accuracy.
- Mitigation Strategies:
- DfAM: Design parts with gradual thickness transitions and minimize large, flat unsupported sections.
- Build Orientation & Support Strategy: Orient the part to minimize stress accumulation and use robust support structures to anchor the part firmly to the build plate during printing. Well-designed supports also help conduct heat away.
- Optimized Process Parameters: Experienced AM providers fine-tune laser/electron beam power, scan speed, layer thickness, and scan strategies to minimize stress build-up for specific materials like 316L and 254SMO. Met3dp’s focus on printer reliability includes stable process control.
- Appropriate Heat Treatment: Performing stress relief heat treatment before removing the part from the build plate is crucial. Subsequent solution annealing (if required) must also be carefully controlled.
- Simulation: Thermal simulation software can predict stress distribution and potential distortion, allowing for design or process adjustments pre-build.
2. Porosity:
- Challenge: Small voids or pores can remain within the printed material due to incomplete melting, gas entrapment (from powder or shielding gas), or keyholing (vapor depression collapse). Porosity reduces density, degrades mechanical properties (especially fatigue strength), and can potentially create leak paths in pressure fittings.
- Mitigation Strategies:
- High-Quality Powder: Using powder with high sphericity, controlled PSD, low internal gas porosity, and good flowability (like Met3dp’s gas atomized powders) is fundamental. Powder handling and storage are also critical to prevent moisture absorption or contamination.
- Optimized Print Parameters: Careful control over energy density (laser/beam power, speed, hatch spacing) is essential to ensure complete melting and fusion between layers without excessive vaporization.
- Proper Machine Calibration & Maintenance: Ensuring the AM system is correctly calibrated and maintained, including optics and gas flow systems.
- Hot Isostatic Pressing (HIP): As mentioned in post-processing, HIP is highly effective at closing internal pores, significantly improving density and mechanical integrity for critical parts.
- NDT Inspection: Using methods like X-ray computed tomography (CT) or radiography (RT) to detect and quantify internal porosity if required by specifications.
3. Internal Support Removal:
- Challenge: Removing support structures from complex internal channels or cavities within a fitting can be extremely difficult, time-consuming, or sometimes impossible without damaging the part. Residual support material can obstruct flow or act as corrosion initiation sites.
- Mitigation Strategies:
- DfAM is Key: The primary solution is designing internal features to be self-supporting (e.g., using angles >45°, tear-drop or diamond-shaped channels instead of circular horizontal ones).
- Orientation: Choose a build orientation that minimizes internal overhangs needing support.
- Accessible Supports: If internal supports are unavoidable, design them to be reachable through openings or design the fitting in sections that allow access before final joining.
- Alternative AM Processes: For some complex internal channel designs where support removal is impossible, binder jetting followed by sintering might be considered (though properties may differ from powder bed fusion).
- Abrasive Flow Machining/Chemical Polishing: Can sometimes smooth internal surfaces but may not fully remove robust support remnants.
4. Achieving Leak-Proof Seals:
- Challenge: Ensuring reliable, leak-tight seals at connection points (flanges, threads, compression fittings) requires precise dimensions and appropriate surface finishes on sealing surfaces. As-built AM surfaces are typically too rough for direct sealing.
- Mitigation Strategies:
- Design for Sealing: Incorporate standard sealing features (e.g., raised face flanges, O-ring grooves) according to industry standards.
- Post-Machining: Critically important to machine sealing surfaces (flange faces, thread profiles) to the required dimensional tolerances and surface finish specifications (e.g., specific Ra value, flatness, serrated finish). Ensure adequate machining stock is included in the AM design.
- Appropriate Gasketing/Sealants: Select compatible gaskets or thread sealants based on the fluid, temperature, pressure, and the machined surface finish.
- Rigorous Leak Testing: Perform hydrostatic or pneumatic leak testing at specified pressures after final assembly or machining to verify seal integrity.
5. Ensuring Consistent Material Properties and Microstructure:
- Challenge: Achieving uniform mechanical properties and the desired microstructure throughout a complex AM part requires consistent processing conditions and appropriate thermal post-processing. Variations can affect strength, ductility, and corrosion resistance.
- Mitigation Strategies:
- Process Control & Monitoring: Utilizing AM systems with robust monitoring and control features to ensure consistent energy delivery, powder deposition, and atmospheric conditions.
- Standardized Parameters: Developing and adhering to qualified printing parameters specific to the material (316L, 254SMO) and machine.
- Appropriate Heat Treatment: Applying necessary stress relief and/or solution annealing cycles uniformly to the entire part to homogenize the microstructure and optimize properties. HIP also contributes to uniformity.
- Material Testing: Performing tensile tests, hardness tests, and potentially microstructural analysis (metallography) on representative samples or witness coupons printed alongside the parts to verify material properties meet specifications.
Overcoming Challenges – Summary Table:
Challenge | Primary Cause(s) | Key Mitigation Strategies |
---|---|---|
Warping/Distortion | Residual Stress | DfAM, Supports, Optimized Parameters, Stress Relief (Pre-Removal), Simulation |
Porosity | Incomplete Melting, Gas Entrapment | Quality Powder, Optimized Parameters, Machine Calibration, HIP, NDT |
Internal Support Removal | Complex Internal Overhangs | DfAM (Self-Supporting), Orientation, Accessible Supports, Design Segmentation |
Leak-Proof Seals | Dimensional Inaccuracy, Rough Surface Finish | Design for Sealing, Post-Machining (Critical), Correct Gaskets/Sealants, Leak Testing |
Inconsistent Properties | Process Variation, Inadequate Heat Treat | Process Control, Standardized Parameters, Correct Heat Treatment, Material Testing |
Export to Sheets
By proactively addressing these potential challenges through careful design, process optimization, thorough post-processing, and rigorous quality control, manufacturers and end-users can confidently utilize metal additive manufacturing to produce high-quality, reliable, corrosion-resistant pipe fittings in 316L and 254SMO for even the most demanding industrial environments.
Supplier Selection Strategy: Choosing Your Metal 3D Printing Partner
Selecting the right additive manufacturing service provider is as crucial as perfecting the design or choosing the correct material (like 316L or 254SMO) for your corrosion-resistant pipe fittings. The quality, reliability, and performance of the final component depend heavily on the capabilities, expertise, and quality systems of your chosen partner. For engineers and procurement managers navigating the AM landscape, especially those sourcing critical industrial components, a structured evaluation process is essential.
Here are key criteria to consider when selecting a metal 3D printing supplier for pipe fittings:
1. Technical Expertise and DfAM Support:
- What to look for: Does the supplier have metallurgists and engineers experienced specifically with 316L, 254SMO, and other relevant alloys in the context of AM? Can they provide meaningful Design for Additive Manufacturing (DfAM) feedback to optimize your fitting design for printability, performance, cost-effectiveness, and minimized post-processing? Do they understand the nuances of fluid dynamics relevant to pipe fittings?
- Why it matters: Expertise ensures correct parameter selection, appropriate post-processing recommendations, and potential design improvements you might not have considered, leading to a better final product.
2. Equipment Capability and Capacity:
- What to look for: Does the supplier operate well-maintained, industrial-grade AM systems (e.g., L-PBF, SEBM) suitable for producing dense metal parts? What is their build envelope size (can they accommodate your fitting dimensions)? Do they have sufficient machine capacity to meet your required lead times, including potential for bulk manufacturing or recurring orders? What is their track record for reliability and uptime?
- Why it matters: The quality and calibration of the AM machine directly impact part quality. Sufficient capacity ensures timely delivery and scalability for future needs. Providers like Met3dp, offering industry-leading print volume, accuracy and reliability, demonstrate a commitment to robust production capabilities.
3. Material Quality, Handling, and Traceability:
- What to look for: Where does the supplier source their metal powders (e.g., 316L, 254SMO)? Do they use powders from reputable manufacturers with certified chemistries (e.g., adhering to ASTM standards)? What are their procedures for powder handling, storage, testing (e.g., chemistry, PSD, flowability), and recycling (if applicable)? Can they provide full material traceability (e.g., heat/lot number) linking the powder batch to your specific part, often documented via EN 10204 3.1 material certifications?
- Why it matters: Powder quality is fundamental to part integrity. Strict handling prevents contamination and degradation. Full traceability is often a requirement for critical applications in industries like aerospace, medical, and oil & gas, ensuring accountability and quality assurance. Companies like Met3dp, which manufacture their own high-quality metal powders using advanced atomization techniques, often have superior control over material consistency. Explore their range of printers and powders to see their vertically integrated approach.
4. Comprehensive Post-Processing Capabilities:
- What to look for: Does the supplier offer the necessary post-processing steps in-house or through qualified partners? This includes stress relief, HIP (if required), support removal, CNC machining (for critical tolerances and features), surface finishing (blasting, polishing, passivation), and relevant heat treatments (like solution annealing).
- Why it matters: In-house capabilities often streamline the workflow, reduce lead times, and ensure better process control and accountability compared to managing multiple subcontractors. Verify their expertise and equipment for each required step.
5. Quality Management System (QMS) and Certifications:
- What to look for: Does the supplier operate under a robust QMS, ideally certified to standards like ISO 9001? For specific industries, certifications like AS9100 (Aerospace) or ISO 13485 (Medical) may be relevant or required. Do they have documented procedures for process control, inspection, calibration, and non-conformance management?
- Why it matters: A certified QMS demonstrates a commitment to consistent quality, process control, continuous improvement, and customer satisfaction – essential for industrial procurement confidence.
6. Inspection and Testing Capabilities:
- What to look for: What metrology equipment does the supplier possess (CMMs, profilometers, scanners)? Can they perform required NDT (PT, RT, UT) and pressure/leak testing? Do they have procedures for final inspection and documentation?
- Why it matters: Verification is key. The supplier must be able to demonstrate, with objective evidence, that the manufactured fittings meet all drawing specifications and performance requirements.
7. Communication, Collaboration, and Support:
- What to look for: Is the supplier responsive and transparent throughout the RFQ, ordering, and production process? Do they provide clear technical communication and collaborate effectively on design or manufacturing challenges? What level of post-delivery support do they offer?
- Why it matters: A strong working relationship built on clear communication is vital for navigating the complexities of AM and ensuring project success.
Supplier Evaluation Checklist Summary:
Criteria | Key Questions | Importance Level |
---|---|---|
Technical Expertise / DfAM | Experience with alloy/AM? DfAM support offered? Application understanding? | High |
Equipment / Capacity | Industrial machines? Build size adequate? Capacity for volume/lead time? | High |
Material Quality/Traceability | Reputable powder source? Handling procedures? Full traceability provided? | High |
Post-Processing Capability | Required steps available (in-house preferred)? Expertise in each step? | High |
QMS / Certifications | ISO 9001 or relevant industry certs? Documented procedures? | High |
Inspection / Testing | Metrology equipment? NDT capability? Leak testing? Final inspection protocol? | High |
Communication / Support | Responsive? Transparent? Collaborative? Post-delivery support? | Medium-High |
Cost / Lead Time | Competitive pricing? Reliable lead time estimates? | Medium-High |
Export to Sheets
By systematically evaluating potential suppliers against these criteria, companies can identify a metal 3D printing partner capable of delivering high-quality, reliable, corrosion-resistant pipe fittings that meet the demanding requirements of their specific application.
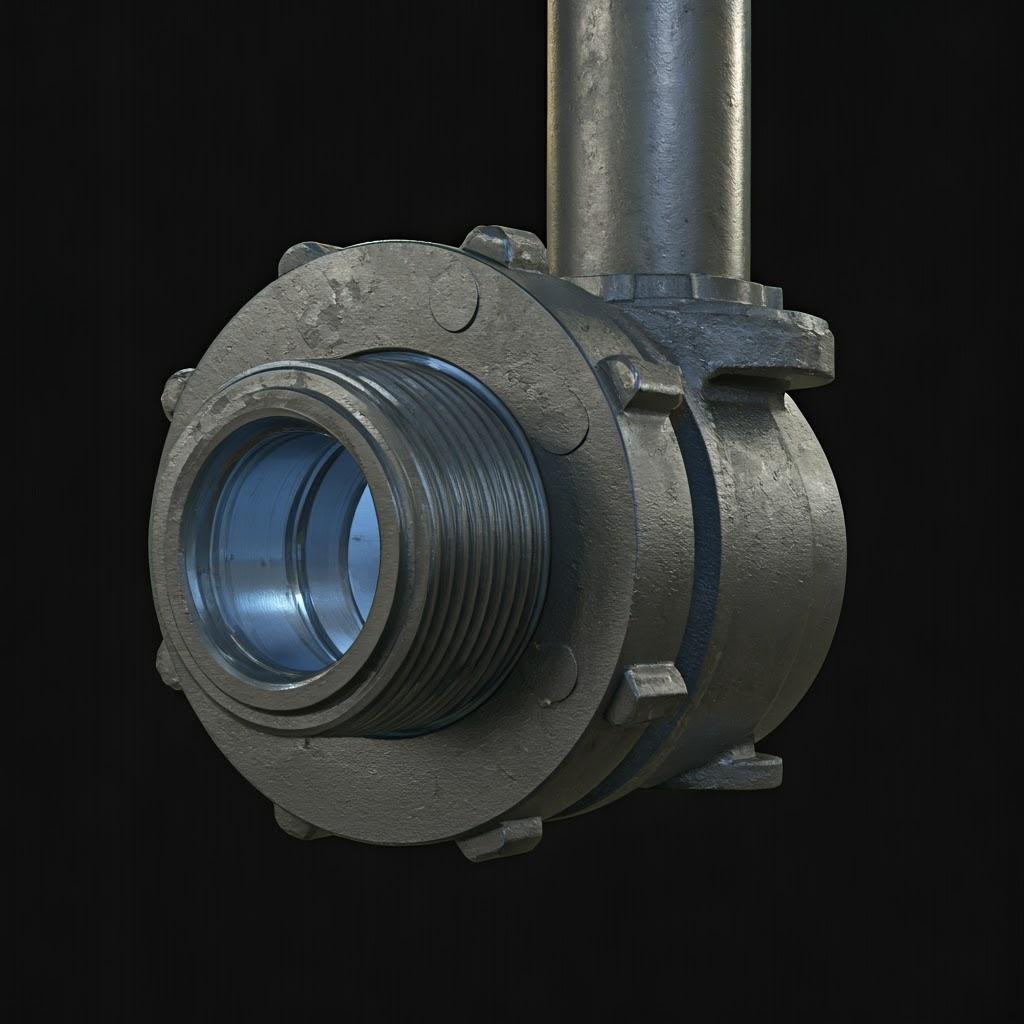
Understanding Investment: Cost Factors and Lead Times for AM Pipe Fittings
While the technical advantages of using metal additive manufacturing for corrosion-resistant pipe fittings are compelling, procurement managers and project engineers must also have a clear understanding of the associated costs and lead times. Unlike traditional mass production where tooling amortization dominates, AM costs are driven by different factors. Understanding these drivers helps in accurate budgeting, evaluating the total cost of ownership (TCO), and managing project timelines.
Key Cost Drivers for AM Pipe Fittings (316L/254SMO):
- Part Volume and Bounding Box:
- Impact: Larger parts consume more material and take longer to print. The overall size (bounding box) also dictates how many parts can fit onto a single build plate (nesting density), affecting machine time efficiency.
- Consideration: Optimize designs to minimize unnecessary bulk while meeting structural requirements. Efficient nesting by the AM provider is crucial for reducing per-part machine time costs.
- Part Complexity:
- Impact: Highly intricate designs with complex internal channels or features requiring extensive support structures increase build preparation time, print time (due to more scanner movements), and significantly increase post-processing effort (support removal).
- Consideration: Leverage DfAM to simplify designs where possible and minimize difficult-to-remove supports. However, AM’s strength lies in handling complexity that’s impossible otherwise, so the value of the complex feature must be weighed against its cost.
- Material Type:
- Impact: The cost of metal powder varies significantly. High-performance alloys like 254SMO are considerably more expensive per kilogram than standard 316L stainless steel due to higher alloying element costs and potentially lower production volumes.
- Consideration: Specify the most cost-effective material that meets the application’s corrosion resistance and mechanical requirements. Don’t over-specify if 316L is sufficient.
- Machine Time:
- Impact: This is often a primary cost driver, calculated based on the hours the AM machine is occupied printing the part(s). It depends on part height (number of layers), part volume, and the specific machine’s build rate.
- Consideration: Optimize build orientation and nesting to maximize the number of parts per build and minimize build height where feasible.
- Post-Processing Intensity:
- Impact: This can contribute significantly to the final cost. Each step – stress relief, support removal, HIP, solution annealing, extensive CNC machining, high-level polishing, passivation, NDT – adds labor, machine time, and potentially specialized equipment costs.
- Consideration: Clearly define the necessary post-processing based on application requirements. Avoid specifying unnecessary steps. For example, HIP is beneficial but adds significant cost; justify its use based on criticality. Discuss options with the supplier to find the most cost-effective finishing route.
- Quantity Ordered:
- Impact: While AM avoids tooling costs, there are still economies of scale. Setup costs (build preparation) are amortized over more parts in larger batches. Material costs may decrease slightly with bulk powder purchases. Dedicated machine runs become more efficient.
- Consideration: While ideal for prototypes and low volumes, per-part costs will generally decrease for medium-volume runs compared to one-off prints. Discuss potential price breaks for higher quantities during the RFQ process.
- Quality Assurance Requirements:
- Impact: Extensive NDT (like CT scanning), detailed CMM reports for every part, or additional material testing add significant cost and time.
- Consideration: Specify QA requirements appropriate to the part’s criticality. Standard material certifications and dimensional checks might suffice for non-critical fittings, while aerospace or nuclear applications will demand far more rigorous (and costly) validation.
Lead Time Components:
The total lead time for receiving finished AM pipe fittings comprises several stages:
- Quotation & Order Processing: (1-5 days) Review of design files, DfAM feedback, quotation generation, order confirmation.
- Build Preparation: (1-2 days) File preparation, build layout planning (nesting), support generation, machine setup.
- Machine Queue Time: (Variable: days to weeks) Waiting for an available machine slot, depending on supplier workload.
- Printing Time: (Hours to days) Depends on part height, volume, nesting density, and machine speed. Can range from ~12 hours for a small build to several days for a tall or densely packed large build.
- Cooling & Depowdering: (Hours to 1 day) Allowing the build chamber to cool, removing the build plate, and initial powder removal.
- Post-Processing: (Variable: days to weeks) This is often the most time-consuming stage, involving:
- Heat Treatment (Stress relief/Annealing/HIP): 1-3 days per cycle (including furnace time).
- Part Removal & Support Removal: Highly variable based on complexity (hours to days).
- Machining: Depends on complexity and number of features (hours to days).
- Finishing/Passivation: 1-2 days.
- Inspection & Quality Control: (1-3 days) Dimensional checks, NDT, documentation review.
- Packing & Shipping: (1-5 days depending on location/method).
Typical Overall Lead Times: Expect lead times ranging from 1-2 weeks for simple, rapidly processed prototypes to 4-8 weeks or more for complex fittings requiring extensive post-processing (especially HIP and machining) and rigorous QA, or for larger batch orders. Clear communication with the supplier is key to getting realistic estimates.
Return on Investment (ROI) Perspective:
While the per-part cost of an AM fitting might sometimes appear higher than a mass-produced traditional fitting, the ROI calculation should consider:
- Elimination of Tooling Costs: Significant savings for prototypes, low volumes, or custom designs.
- Reduced Lead Times: Faster time-to-market for new products or quicker replacement of critical spares, minimizing costly downtime.
- Design Optimization: Potential for improved performance (flow efficiency, weight reduction) leading to better system performance.
- Part Consolidation: Reducing assembly time and potential leak points.
- Inventory Reduction: On-demand production minimizes warehousing costs for spares.
For the right applications – complex geometries, urgent needs, customization, low-to-medium volumes, legacy part replacement – metal AM offers a compelling value proposition and strong ROI despite potentially higher initial per-part costs.
Frequently Asked Questions (FAQ) about 3D Printed 316L Pipe Fittings
Here are answers to some common questions engineers and procurement specialists have about using metal additive manufacturing for 316L corrosion-resistant pipe fittings:
1. Can 3D printed 316L pipe fittings meet standard pressure ratings (e.g., ASME B16.9, B16.5)?
- Answer: Yes, it is possible for AM 316L fittings to meet or even exceed the requirements of standard pressure piping codes, but it’s not automatic. Success depends on:
- Proper Engineering Design: Ensuring wall thicknesses and overall geometry meet the code calculations for the intended pressure and temperature, considering the mechanical properties of AM 316L (which can be slightly different from wrought material).
- High-Quality AM Processing: Achieving fully dense parts (>99.5%) with minimal defects through optimized print parameters and high-quality powder.
- Appropriate Post-Processing: Performing necessary heat treatments (stress relief, potentially solution annealing) to optimize microstructure and mechanical properties. Hot Isostatic Pressing (HIP) is often recommended or required for critical high-pressure applications to ensure maximum density and eliminate potential leak paths.
- Verification Testing: Performing burst tests on prototypes or rigorous NDT and pressure testing (hydrostatic) on production parts as required by the code or application specification. Collaboration with an experienced AM provider knowledgeable about pressure component requirements is crucial.
2. What material certifications and quality documentation can I expect with AM 316L fittings?
- Answer: Reputable AM service providers should be able to provide comprehensive documentation. Common deliverables include:
- Material Certification: Typically an EN 10204 Type 3.1 certificate for the specific batch of 316L powder used, confirming its chemical composition conforms to standards (e.g., ASTM A276/A479 chemical requirements).
- Certificate of Conformance (CoC): A statement from the AM provider confirming that the parts were manufactured according to the specified processes, drawings, and quality procedures.
- Heat Treatment Reports: Records detailing the parameters (temperature, time, atmosphere) used for stress relief, annealing, or HIP cycles.
- Dimensional Inspection Report: Measurement data verifying that critical dimensions are within tolerance (e.g., CMM report).
- NDT Reports: Results from any specified non-destructive testing (PT, RT, UT, etc.).
- Pressure Test Certificate: Documentation confirming successful completion of required leak or pressure tests.
- QMS Certification: Evidence of the provider’s quality system certification (e.g., ISO 9001).
3. How does the corrosion resistance of additively manufactured 316L compare to traditional wrought or cast 316L?
- Answer: When produced correctly (high density, proper chemistry) and appropriately post-processed (stress relieved/annealed, passivated), the corrosion resistance of AM 316L is generally considered comparable or potentially even slightly better than conventional 316L in many environments.
- Density: Achieving near-full density (>99.5%) is critical; residual porosity can act as initiation sites for localized corrosion. HIP can effectively eliminate this.
- Microstructure: The fine-grained microstructure often achieved in AM can sometimes enhance passivity, although this depends heavily on thermal history. Proper heat treatment is key to ensure homogeneity and prevent detrimental phase precipitation.
- Surface Finish: As-built AM surfaces are rougher than machined surfaces. While passivation helps, very rough surfaces might be slightly more susceptible to crevice effects or biofilm attachment initially. For critical applications, post-machining or polishing of key surfaces enhances corrosion performance alongside ensuring sealability.
- Chemistry: Ensuring the powder meets the 316L chemical specification is fundamental.
4. Are there Minimum Order Quantities (MOQs) for 3D printed pipe fittings?
- Answer: One of the significant advantages of AM is its flexibility regarding batch size. Generally, there are no strict MOQs. AM is highly suitable for:
- Prototypes: Producing single pieces or very small numbers for testing and design validation.
- Low-Volume Production: Manufacturing niche or custom fittings in small quantities (e.g., 1-100 pieces) where tooling for traditional methods would be cost-prohibitive.
- Spare Parts: Printing one-off replacements for obsolete or hard-to-source components.
- While there’s no technical MOQ, the per-part price tends to decrease with larger quantities due to the amortization of setup costs and more efficient machine utilization. Discuss volume pricing with your supplier.
5. Can you print custom thread types or flange standards directly?
- Answer: AM can print the shape of threads and flange features directly. However, achieving the necessary precision, surface finish, and strict adherence to standards (e.g., NPT taper accuracy, ASME B16.5 flange face finish and dimensions) directly via printing is very challenging and often not reliable for leak-tight sealing.
- Best Practice: The standard approach is to print the fitting with machining stock added to the threaded or flange areas. These critical features are then CNC machined after printing and heat treatment to meet the exact specifications and required surface finish. This ensures dimensional accuracy, proper sealing, and interchangeability with standard components. So, while the overall custom geometry is enabled by AM, precision threads and flanges rely on post-machining.
Conclusion: Future-Proofing Fluid Systems with Additively Manufactured Corrosion-Resistant Fittings
The landscape of industrial fluid handling is continuously evolving, demanding components that offer higher performance, greater reliability, and more agile supply chains. Metal additive manufacturing has emerged as a transformative technology capable of meeting these demands, particularly for critical components like corrosion-resistant pipe fittings fabricated from proven materials such as 316L and advanced alloys like 254SMO.
As we’ve explored, the advantages are clear:
- Unprecedented Design Freedom: Enabling complex geometries for optimized flow, part consolidation, and tailored solutions.
- Accelerated Timelines: Facilitating rapid prototyping and significantly reducing lead times for custom or low-volume production compared to tooling-based methods.
- Enhanced Efficiency: Minimizing material waste through near-net-shape production and enabling on-demand manufacturing to reduce inventory costs.
- Material Versatility: Effectively processing robust, corrosion-resistant alloys essential for demanding chemical, marine, energy, and pharmaceutical applications.
However, successfully implementing AM for fittings requires a holistic approach. It necessitates embracing Design for Additive Manufacturing (DfAM) principles, understanding the critical role of meticulous post-processing (including heat treatment, machining, and finishing), and navigating potential challenges like residual stress and porosity through careful process control.
Crucially, partnering with the right AM supplier – one with deep technical expertise, robust equipment, stringent material quality control, comprehensive post-processing capabilities, and certified quality systems – is paramount to realizing the full potential of this technology.
Met3dp stands ready to be that partner. With our foundation in advanced powder manufacturing, utilizing industry-leading gas atomization and PREP technologies to produce high-sphericity, high-quality metal powders, and our portfolio of industrial SEBM printers delivering exceptional accuracy and reliability, we offer a comprehensive solution. Our decades of collective expertise in metal additive manufacturing allow us to collaborate effectively with engineers and procurement managers, providing DfAM support, process optimization, and end-to-end manufacturing services.
Whether you are developing next-generation systems requiring complex custom fittings, seeking rapid prototypes for validation, or needing reliable on-demand production of critical spare parts in 316L, 254SMO, or other high-performance alloys, metal AM offers a powerful pathway.
Ready to explore how additive manufacturing can enhance your fluid systems? Contact the experts at Met3dp today to discuss your application requirements and discover how our cutting-edge equipment, premium metal powders, and extensive know-how can help you manufacture stronger, more efficient, and more reliable corrosion-resistant pipe fittings.
Share On
MET3DP Technology Co., LTD is a leading provider of additive manufacturing solutions headquartered in Qingdao, China. Our company specializes in 3D printing equipment and high-performance metal powders for industrial applications.
Inquiry to get best price and customized Solution for your business!
Related Articles
About Met3DP
Recent Update
Our Product
CONTACT US
Any questions? Send us message now! We’ll serve your request with a whole team after receiving your message.
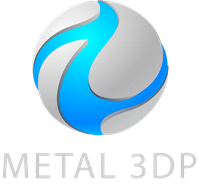
Metal Powders for 3D Printing and Additive Manufacturing