CVD metal Powder: Production of Conductors and Solders
Table of Contents
Imagine crafting minuscule, intricate structures, like the delicate veins of an electronic circuit, with unparalleled precision and control. This is the realm of Chemical Vapor Deposition (CVD) metal powders, a revolutionary approach to creating high-performance conductors and solders.
But what exactly are CVD metal powders, and how do they revolutionize the production of these crucial electronic components? Buckle up, because we’re about to delve into the fascinating world of these microscopic marvels, exploring their properties, applications, and the exciting possibilities they hold for the future.
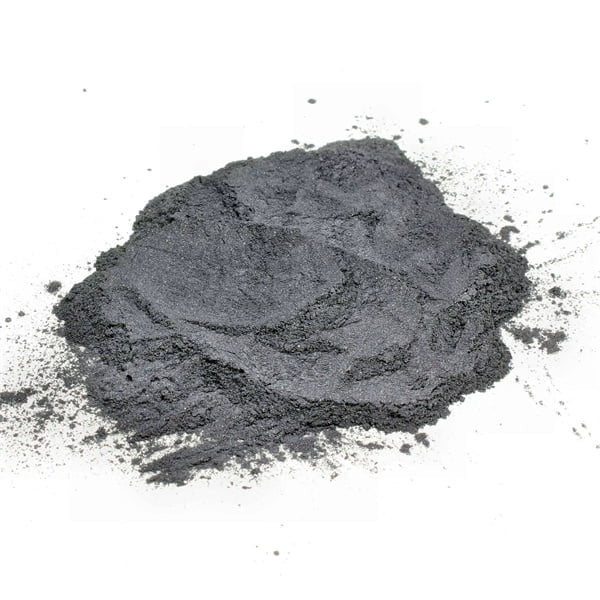
Why CVD Metal Powders Can Produce Conductive Wires
Think of traditional methods for creating electrical wires, like drawing them from bulk metal. While effective, these methods often face limitations in terms of precision and the ability to create complex structures. Enter CVD metal powders.
CVD is a technique where gaseous precursors like metal carbonyls are decomposed on a heated substrate, leaving behind a pure, thin film of the desired metal. This process allows for exceptional control over the thickness, uniformity, and purity of the deposited metal, making it ideal for crafting microscopic wires crucial for modern electronics.
Here’s a breakdown of the magic behind CVD:
- Gaseous precursors: Imagine tiny, gas-phase building blocks containing the desired metal atom. These are pumped into the reaction chamber.
- Heated substrate: This is the foundation on which the metal will be built. It can be a silicon wafer, a polymer film, or even another metal layer.
- Decomposition: As the precursors encounter the heated substrate, they break down, releasing the metal atom and other byproducts.
- Deposition: The liberated metal atom condenses and adheres to the substrate, forming a thin film of the desired metal.
By precisely controlling the temperature, pressure, and precursor flow, engineers can meticulously tailor the thickness, composition, and even the morphology (shape and structure) of the deposited metal layer. This level of control translates to superior conductivity, as the meticulously crafted metal film minimizes scattering of electrons, the current carriers.
Why CVD Metal Powder Can producr Solder
Soldering, the process of joining two metal components using a low-melting-point alloy, is another crucial aspect of electronics manufacturing. While traditional solders often contain lead, raising environmental concerns, CVD metal powders offer a lead-free and environmentally friendly alternative.
Here’s how CVD metal powders excel in soldering:
- Tailored composition: Unlike traditional solders with fixed compositions, CVD allows for the creation of custom alloys with specific melting points and mechanical properties. This enables them to perfectly match the requirements of different electronics components.
- Low-temperature processing: CVD processes typically operate at lower temperatures compared to traditional soldering methods. This reduces thermal stress on delicate electronic components, improving reliability and preventing damage.
- Precise control: Just like creating conductors, CVD allows for precise control over the amount and location of the deposited solder material. This translates to cleaner, more reliable solder joints with minimal waste.
CVD Metal Powder:Manufacture Various Electronic Devices
The versatility and superior properties of CVD metal powders make them invaluable in a wide array of electronic devices:
- Integrated circuits (ICs): These tiny marvels power everything from smartphones to computers. CVD metal powders are used to create the intricate network of conductive pathways within these chips, enabling efficient signal transmission.
- Printed circuit boards (PCBs): PCBs are the backbone of electronic devices, providing physical support and electrical connections. CVD metal powders are used to deposit conductive tracks on these boards, ensuring seamless transmission of electrical signals.
- High-frequency (RF) components: These components are crucial for wireless communication and radar systems. The precise control offered by CVD allows for the creation of highly conductive and low-loss metal structures needed for optimal performance.
- Microelectromechanical systems (MEMS): These tiny devices combine electrical and mechanical elements. CVD metal powders are used to create miniature conductive features within these devices, enabling them to perform various functions like sensing and actuation.
The applications of CVD metal powders extend beyond these examples, with their potential continuously being explored for next-generation electronic devices like flexible electronics and organic light-emitting diodes (OLEDs).
CVD Metal Powder:a New Type of Material
The advantages of CVD metal powders go beyond their ability to create conventional conductors and solders. They pave the way for the development of entirely new types of electronic devices with groundbreaking capabilities:
- 3D printed electronics: The precise control offered by CVD allows for the creation of three-dimensional conductive structures. This opens the door for the development of 3D printed electronics with functionalities not possible with traditional
Specific Metal Powder Models and Their Applications
Now that we’ve explored the magic of CVD metal powders and their diverse applications, let’s delve into specific commercially available models and their unique characteristics:
Model: Copper (Cu)
- Description: The most widely used CVD metal powder due to its excellent electrical conductivity, high ductility, and good thermal conductivity.
- Applications: Primarily used for creating conductive pathways in integrated circuits, printed circuit boards, and high-frequency components.
Model: Silver (Ag)
- Description: Boasts the highest electrical conductivity among all metals, making it ideal for applications requiring exceptional signal transmission. Additionally, silver possesses antimicrobial properties, making it valuable for electronics used in healthcare settings.
- Applications: Found in high-performance RF components, microwave circuits, and medical device connectors.
Model: Gold (Au)
- Description: Renowned for its excellent corrosion resistance, high conductivity, and superior solderability. Gold is often used for plating electrical contacts and connectors, ensuring reliable signal transmission and long-lasting performance.
- Applications: Widely used in connectors, switches, and relays in various electronic devices.
Model: Aluminum (Al)
- Description: Offers a cost-effective alternative to copper with good conductivity and low weight. However, aluminum can form an oxide layer on its surface, hindering conductivity.
- Applications: Primarily used in integrated circuits as metallization layers and for creating heat sinks due to its good thermal conductivity.
Model: Tungsten (W)
- Description: Known for its exceptional high-temperature strength, making it ideal for applications requiring heat resistance. Additionally, tungsten possesses good electrical conductivity and low thermal expansion coefficient.
- Applications: Used in high-temperature electronics, vacuum devices, and as diffusion barriers in integrated circuits.
Model: Nickel (Ni)
- Description: Offers good corrosion resistance, magnetic properties, and can be alloyed with other metals to create various material properties.
- Applications: Used in electromagnetic shielding, magnetic recording media, and as a barrier layer in diffusion processes.
Model: Tantalum (Ta)
- Description: Possesses excellent corrosion resistance and a high dielectric constant, making it valuable for capacitors. Additionally, tantalum offers good biocompatibility, making it suitable for medical implants.
- Applications: Primarily used in tantalum capacitors, and find applications in medical implants and corrosion-resistant coatings.
Model: Platinum (Pt)
- Description: Highly resistant to corrosion and oxidation even at high temperatures. Platinum also possesses good catalytic properties and finds application in fuel cells.
- Applications: Used in high-temperature electronics, chemical sensors, and fuel cells.
Model: Palladium (Pd)
- Description: Similar to platinum, palladium offers good corrosion resistance and catalytic properties. Additionally, it finds application in hydrogen purification.
- Applications: Used in catalytic converters, hydrogen purification membranes, and fuel cells.
These are just a few examples, and the list of available CVD metal powders is continuously expanding as research and development efforts progress. Each model offers unique properties and caters to specific applications within the vast and ever-evolving world of electronics.
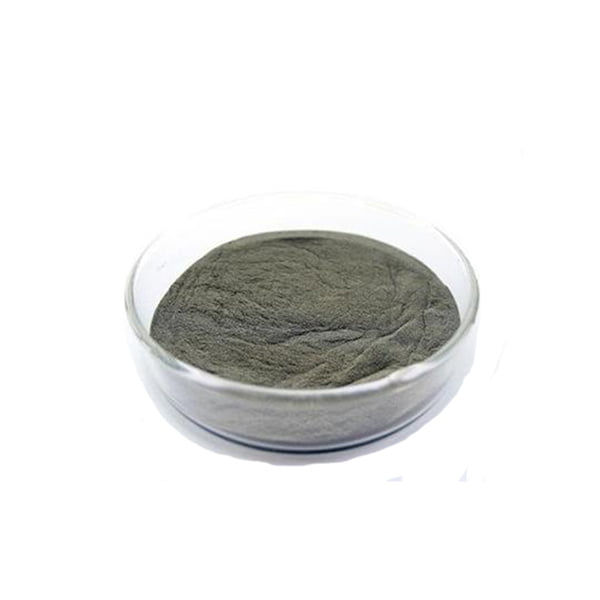
Comparing Metal Powder Models:
Choosing the right CVD metal powder requires careful consideration of various factors, including:
- Required properties: Electrical conductivity, thermal conductivity, corrosion resistance, and mechanical properties are key aspects to consider.
- Application: Different applications demand specific characteristics. For instance, high-frequency components prioritize high conductivity, while medical implants require biocompatibility.
- Cost: Different models vary in price, with precious metals like gold and platinum commanding a premium.
It’s crucial to weigh these factors and consult with material scientists and engineers to select the most suitable CVD metal powder for your specific needs.
By understanding the capabilities and limitations of each model, engineers and manufacturers can harness the power of CVD metal powders to create innovative and high-performance electronic devices, shaping the future of technology.
Advantages and Limitations of CVD Metal Powders
While CVD metal powders offer numerous advantages, it’s essential to acknowledge their limitations to make informed decisions in their application:
Advantages:
- Exceptional control: CVD offers unparalleled control over the thickness, composition, and morphology of deposited metal films, enabling the creation of intricate and precise structures.
- High purity: The controlled environment of the CVD process minimizes contamination, resulting in high-purity metal films with superior electrical and mechanical properties.
- Versatility: A wide variety of metal powders can be produced using CVD, catering to diverse application needs.
- Conformal coating: CVD allows for the deposition of metal films on conformal surfaces, enabling the creation of intricate and three-dimensional structures.
- Environmentally friendly: Compared to traditional soldering methods, CVD can be more environmentally friendly by using lead-free solders and minimizing waste.
Limitations:
- Cost: The CVD process can be relatively expensive compared to traditional metallization techniques, especially for large-scale production.
- Processing time: Depending on the desired thickness and complexity of the film, the CVD process can be time-consuming.
- Limited deposition rates: Compared to some other deposition techniques like electroplating, CVD typically has slower deposition rates.
- Safety considerations: Some CVD precursors can be hazardous and require careful handling and proper safety protocols.
- Substrate limitations: Not all materials are suitable for CVD processes due to limitations in temperature tolerance and other factors.
Future Outlook and Applications of CVD Metal Powders
The future of CVD metal powders is brimming with exciting possibilities:
- Next-generation electronics: As electronic devices continue to miniaturize and require higher performance, CVD metal powders will play a crucial role in creating smaller, faster, and more efficient components.
- 3D printing: The precise control offered by CVD opens doors for the 3D printing of electronics, enabling the creation of complex and functional devices with unique functionalities.
- Flexible electronics: CVD metal powders can be used to create flexible and stretchable conductive pathways, paving the way for wearable electronics and other innovative applications.
- Nanoporous materials: By precisely controlling the deposition process, CVD can be used to create nanoporous materials with unique properties for applications in energy storage, catalysis, and sensors.
The continuous development of new CVD techniques and materials combined with ongoing research in various fields promises to unlock the full potential of CVD metal powders, shaping the future of electronics and beyond.
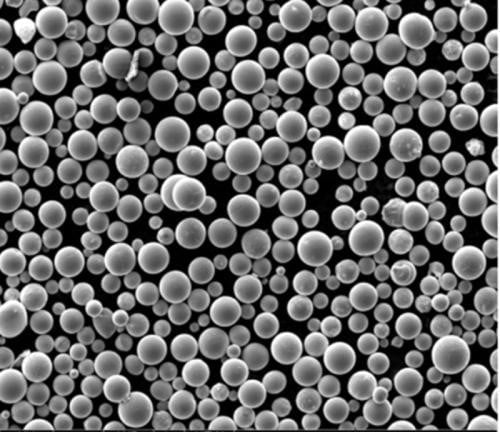
FAQ
Q: What are the different types of CVD processes used for metal powder deposition?
A: Several CVD processes are used, including:
- Thermal CVD: Precursors are decomposed using high temperatures.
- Plasma-enhanced CVD (PECVD): A plasma introduces energy to the process, enabling lower processing temperatures and faster deposition rates.
- Metal-organic CVD (MOCVD): Organometallic precursors are used, offering good control over film composition and purity.
Q: How does the size and morphology of the metal powder particles affect their properties?
A: Particle size and morphology significantly impact the electrical conductivity, mechanical strength, and sintering behavior of the metal powder. For instance, smaller particles tend to have higher surface area and lower conductivity, while larger particles offer better mechanical strength.
Q: Are there any alternatives to CVD for producing metal powders?
A: Yes, several alternative techniques exist, including:
- Electroplating: A cost-effective method for large-scale production, but offers limited control over film properties.
- Sputtering: A physical vapor deposition technique, but can be slow and may not be suitable for all materials.
- Chemical reduction: A method for producing metal powders from solutions, but may not offer the same level of purity as CVD.
Q: Where can I find more information about CVD metal powders and their suppliers?
A: Numerous resources are available online and through scientific publications. Additionally, several companies specialize in the production and supply of CVD metal powders. Consulting with these companies can provide valuable insights and specific product information.
By understanding the advantages, limitations, and future potential of CVD metal powders, you can leverage their unique capabilities to create innovative and high-performing electronic devices, pushing the boundaries of technology and shaping the future of electronics.
Share On
MET3DP Technology Co., LTD is a leading provider of additive manufacturing solutions headquartered in Qingdao, China. Our company specializes in 3D printing equipment and high-performance metal powders for industrial applications.
Inquiry to get best price and customized Solution for your business!
Related Articles
About Met3DP
Recent Update
Our Product
CONTACT US
Any questions? Send us message now! We’ll serve your request with a whole team after receiving your message.
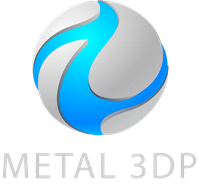
Metal Powders for 3D Printing and Additive Manufacturing
COMPANY
PRODUCT
cONTACT INFO
- Qingdao City, Shandong, China
- [email protected]
- [email protected]
- +86 19116340731