Jaké kovové prášky lze vyrábět pomocí HIP
Obsah
Představte si, že byste z plátna drobných kovových částic vyráběli složité komponenty. To není sci-fi, ale realita lisování za tepla (Hot Isostatic Pressing).HIP), což je revoluční technika, která přeměňuje kovové prášky na vysoce výkonné díly. Jaké kovové prášky jsou však s tímto procesem kompatibilní? Připoutejte se, protože se chystáme na cestu za poznáním fascinujícího světa kovových prášků připravených pro HIP!
Co je HIP a proč je důležitý?
Lisování za tepla (HIP) je kombinace dvou lisů pro kovové prášky. Vystavuje je intenzivnímu teplu a rovnoměrnému tlaku současně. Teplo částice změkčí, což jim umožní deformovat se a propojit se se sousedními částicemi. Tlak mezitím zajistí úplné zhutnění, čímž se odstraní vnitřní dutiny a vytvoří se součástka téměř síťového tvaru s výjimečnými mechanickými vlastnostmi.
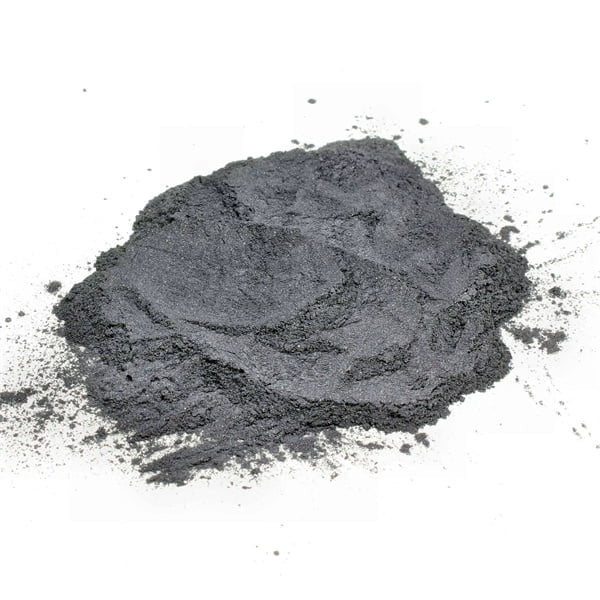
Kovové prášky ideální pro HIP
Ne všechny kovové prášky jsou stejné. Pro úspěšnou operaci HIP musí mít prášek specifické vlastnosti. Zde je deset významných kovových prášků, kterým se pod magickým dotekem HIP daří:
- Nerezové oceli (316L, 17-4PH): Tyto třídy nerezové oceli, které jsou pracovními koňmi ve světě kovových prášků, se vyznačují vynikající odolností proti korozi, vysokou pevností a biokompatibilitou. Díky HIP jsou ještě pevnější a hustší, což je ideální pro použití v letectví, lékařských implantátech a zařízeních pro chemické zpracování.
- Nástrojové oceli (M2, AISI H13): Představte si, že byste z malých kovových částeček vyrobili řezné nástroje ostré jako břitva. To je síla nástrojových ocelí HIP. Tyto jakosti se vyznačují výjimečnou odolností proti opotřebení a tvrdostí, což je ideální pro razníky, zápustky a formy, které musí odolávat neustálému namáhání.
- Superslitiny na bázi niklu (Inconel 625, Haynes 282): V aplikacích, kde jde doslova o hodně, jsou nesporným šampionem superslitiny na bázi niklu. Zachovávají si výjimečnou pevnost a odolnost proti tečení při spalujících teplotách, takže jsou ideální pro součásti proudových motorů, plynových turbín a výměníků tepla. HIP ještě více zvyšuje jejich výkonnost tím, že zajišťuje minimální vnitřní vady.
- Titan a slitiny titanu (Ti-6Al-4V, Gr2): Lehké a zároveň neuvěřitelně pevné titanové slitiny jsou miláčky leteckého průmyslu. HIP umožňuje vytvářet složité titanové díly téměř síťového tvaru s vynikající únavovou pevností a schopností snižovat hmotnost.
- Slitiny kobaltu a chromu (CoCrMo): Slitiny kobaltu a chromu, které jsou biokompatibilní a odolné proti opotřebení, jsou oblíbeným materiálem pro ortopedické implantáty, jako jsou náhrady kyčelních a kolenních kloubů. HIP zajišťuje bezchybnou vnitřní strukturu, která má zásadní význam pro dlouhodobý výkon implantátu a pohodu pacienta.
- Karbid wolframu (WC): Karbid wolframu, král tvrdosti, se používá k výrobě řezných nástrojů a opotřebitelných dílů, které si poradí i s nejabrazivnějším prostředím. HIP zhušťuje práškový karbid wolframu, čímž maximalizuje jeho tvrdost a odolnost proti odlamování.
- Slitiny hliníku (AlSi10Mg, AA2024): Slitiny hliníku, které nabízejí přesvědčivou kombinaci lehkých vlastností a dobré pevnosti, nacházejí stále větší uplatnění v automobilovém a leteckém průmyslu. HIP může zlepšit jejich mechanické vlastnosti, čímž se stávají ještě atraktivnějšími pro aplikace citlivé na hmotnost.
- Slitiny mědi (Cu-Sn, Cu-Ni): Měď je díky své vynikající elektrické vodivosti důležitým materiálem pro výrobu elektrických součástek. HIP může zvýšit vodivost měděných slitin a zároveň zlepšit jejich mechanickou pevnost, což je ideální pro aplikace, jako jsou přípojnice a chladiče.
- Žáruvzdorné kovy (molybden, tantal): Tyto kovy s vysokým bodem tání vynikají v extrémních teplotách. HIP zajišťuje jejich strukturální integritu a minimalizuje vnitřní dutiny, takže jsou ideální pro součásti pecí, raketové trysky a tepelné štíty.
- Amorfní kovy (Vitreloy): Díky jedinečné sklovité struktuře mají amorfní kovy výjimečnou odolnost proti opotřebení a pružné vlastnosti. HIP lze použít ke konsolidaci těchto prášků do téměř síťovitých součástí pro aplikace vyžadující vysokou odolnost proti opotřebení a nízké tření.
Klíčové aspekty výběru HIP-Kompatibilní kovový prášek
Těchto deset kovových prášků je vynikajícími kandidáty pro HIP, ale výběr nakonec závisí na konkrétní aplikaci. Zde je několik klíčových faktorů, které je třeba zvážit:
- Požadované vlastnosti: Jaké jsou kritické mechanické vlastnosti (pevnost, tažnost, vodivost), které potřebujete pro svou finální součást?
- Geometrie dílu: HIP je ideální pro složité geometrie, ale je třeba vzít v úvahu omezení toku prášku a hustoty balení.
- Dostupnost materiálu: Ne všechny prášky jsou snadno dostupné ve všech tvarech a velikostech. Zohledněte náklady a dobu dodání.
- Environmentální předpisy: U některých materiálů mohou platit omezení jejich použití z důvodu ochrany životního prostředí.
Srovnávací analýza kovových prášků pro HIP
V předchozí části bylo uvedeno deset významných kovových prášků kompatibilních s HIP. Jak si ale při tak rozmanité nabídce vybrat ten správný pro váš projekt? Zde je tabulka srovnávací analýzy, která vám to trochu osvětlí:
Vlastnosti | Nerezové oceli (316L, 17-4PH) | Nástrojové oceli (M2, AISI H13) | Superslitiny na bázi niklu (Inconel 625, Haynes 282) | Titan a slitiny titanu (Ti-6Al-4V, Gr2) |
---|---|---|---|---|
Klíčové vlastnosti | Vynikající odolnost proti korozi, vysoká pevnost, biokompatibilní | Výjimečná odolnost proti opotřebení, tvrdost | Pevnost při vysokých teplotách, odolnost proti tečení | Lehká konstrukce, vysoká pevnost, dobrá odolnost proti únavě |
Aplikace | letectví, lékařské implantáty, chemické zpracování | Děrovačky, raznice, formy | Součásti proudových motorů, plynové turbíny, výměníky tepla | Letecké a kosmické komponenty, protetika |
Výhody pro HIP | Lepší pevnost, hustota | Minimalizace vnitřních vad, zvýšená odolnost proti opotřebení | Bezchybná vnitřní struktura, výkon při vysokých teplotách | Vynikající únavová pevnost, snížení hmotnosti |
Nevýhody | Může být během zpracování ztvrdlý | Může vyžadovat vyšší teploty HIP | Vyšší náklady ve srovnání s některými možnostmi | Větší náchylnost ke kontaminaci |
Náklady | Mírný | Vysoký | Vysoký | Vysoký |
Vlastnosti | Slitiny kobaltu a chromu (CoCrMo) | Karbid wolframu (WC) | Slitiny hliníku (AlSi10Mg, AA2024) | Slitiny mědi (Cu-Sn, Cu-Ni) | Žáruvzdorné kovy (molybden, tantal) |
---|---|---|---|---|---|
Klíčové vlastnosti | Biokompatibilní, odolný proti opotřebení | Vysoká tvrdost, odolnost proti oděru | Lehké, s dobrou pevností | Vynikající elektrická vodivost | Vysoký bod tání, pevnost při vysokých teplotách |
Aplikace | Ortopedické implantáty | Řezné nástroje, opotřebitelné díly | Automobilový průmysl, letecké a kosmické komponenty | Sběrnice, chladiče | součásti pecí, raketové trysky, tepelné štíty |
Výhody pro HIP | Zajišťuje bezchybnou vnitřní strukturu | Maximální tvrdost, minimalizace odštípnutí | Zlepšené mechanické vlastnosti | Zvýšená vodivost a pevnost | Minimalizace vnitřních dutin, výkon při vysokých teplotách |
Nevýhody | Omezená tisknutelnost složitých tvarů | Křehké ve srovnání s některými možnostmi | Nižší pevnost ve srovnání s některými ocelemi | Nižší bod tání ve srovnání s některými možnostmi | Omezená dostupnost některých tříd |
Náklady | Vysoký | Vysoký | Mírný | Mírný | Vysoký |
Za stolem: Další úvahy
Tato tabulka je výchozím bodem pro váš výběr. Zde jsou uvedeny některé další faktory, které je třeba zvážit:
- Vlastnosti prášku: Velikost částic, morfologie (tvar) a tekutost mohou ovlivnit hustotu balení a vlastnosti výsledné složky.
- Požadavky na povrchovou úpravu: HIP může zlepšit kvalitu povrchu, ale některé aplikace mohou vyžadovat další následné zpracování.
- Zásah do životního prostředí: Zvažte dopad těžby, zpracování a likvidace materiálu na životní prostředí.
potenciál kovových prášků s HIP
Synergie mezi HIP a kompatibilními kovovými prášky otevírá svět možností. Tato výkonná kombinace posouvá hranice výroby - od lehkých leteckých součástí až po řezné nástroje odolné proti opotřebení. Pochopením jedinečných vlastností jednotlivých kovových prášků a pečlivým zvážením požadavků vašeho projektu můžete využít sílu HIP vytvářet vysoce výkonné díly, které nově definují možnosti.
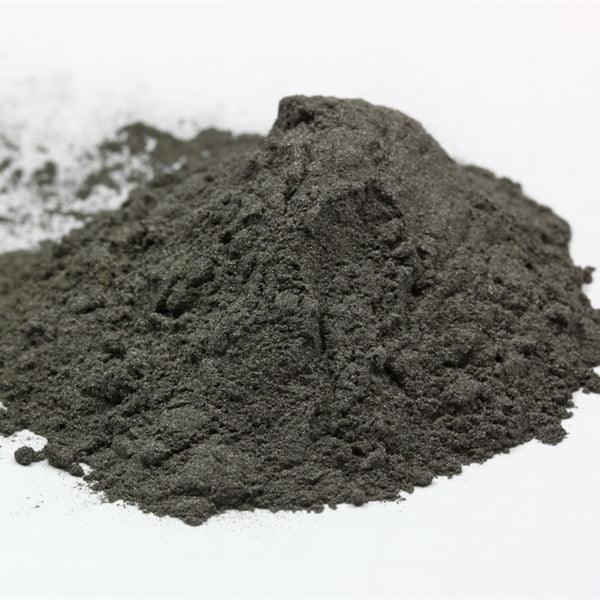
FAQ
Otázka: Jaké jsou výhody použití HIP s kovovými prášky?
Odpověď: HIP nabízí několik výhod, včetně:
- Lepší hustota a odstranění vnitřních dutin
- Vylepšené mechanické vlastnosti, jako je pevnost, odolnost proti únavě a opotřebení.
- Výroba složitých komponentů ve tvaru blížícím se tvaru sítě
- Minimalizace zbytkových napětí
Otázka: Existují nějaká omezení při použití HIP s kovovými prášky?
Odpověď: Mezi omezení, která je třeba vzít v úvahu, patří:
- Vyšší náklady na zpracování ve srovnání s tradičními technikami
- Omezení velikosti některých součástí
- Možnost degradace materiálu při vysokých teplotách zpracování
Otázka: Jak vybrat správný kovový prášek pro HIP?
Odpověď: Výběr závisí na konkrétní aplikaci. Zvažte požadované vlastnosti, geometrii dílu, dostupnost materiálu a předpisy týkající se životního prostředí.
Otázka: Co je izostatické lisování za tepla (HIP)?
Odpověď: Izostatické lisování za tepla (HIP) je technika následného zpracování kovových prášků. Prášek je při něm vystaven vysokým teplotám a současně rovnoměrnému tlaku. Teplo změkčuje částice a umožňuje jim deformovat se a vzájemně se spojovat. Tlak zajišťuje úplné zhutnění, čímž se eliminují vnitřní dutiny a vzniká součástka téměř síťového tvaru s výjimečnými mechanickými vlastnostmi.
Otázka: Jaké jsou výhody použití HIP s kovovými prášky?
Odpověď: HIP nabízí několik výhod, včetně:
- Lepší hustota a odstranění vnitřních dutin: To vede k pevnějším a předvídatelnějším mechanickým vlastnostem.
- Vylepšené mechanické vlastnosti: HIP může zlepšit vlastnosti, jako je pevnost, únavová odolnost, odolnost proti opotřebení a celková strukturální integrita.
- Výroba složitých komponentů ve tvaru blížícím se tvaru sítě: HIP umožňuje vytvářet složité tvary s minimálními požadavky na následné zpracování.
- Minimalizace zbytkových napětí: Vysoký tlak při HIP pomáhá zmírnit zbytková napětí vzniklá při výrobě prášku nebo při tvarování.
Otázka: Existují nějaká omezení při použití HIP s kovovými prášky?
Odpověď: Mezi omezení, která je třeba vzít v úvahu, patří:
- Vyšší náklady na zpracování: V porovnání s tradičními technikami, jako je obrábění nebo odlévání, může být HIP dražší kvůli specializovanému vybavení a potřebným parametrům zpracování.
- Omezení velikosti některých součástí: Velikost komponent, které lze zpracovávat pomocí HIP, je omezena kapacitou nádoby HIP.
- Možnost degradace materiálu při vysokých teplotách zpracování: U některých kovových prášků může při vysokých teplotách používaných při HIP dojít k nežádoucím změnám mikrostruktury nebo vlastností.
Sdílet na
MET3DP Technology Co., LTD je předním poskytovatelem řešení aditivní výroby se sídlem v Qingdao v Číně. Naše společnost se specializuje na zařízení pro 3D tisk a vysoce výkonné kovové prášky pro průmyslové aplikace.
Dotaz k získání nejlepší ceny a přizpůsobeného řešení pro vaše podnikání!
Související články
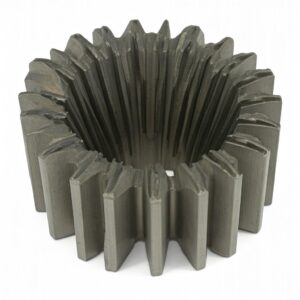
Vysoce výkonné segmenty lopatek trysek: Revoluce v účinnosti turbín díky 3D tisku z kovu
Přečtěte si více "O Met3DP
Nedávná aktualizace
Náš produkt
KONTAKTUJTE NÁS
Nějaké otázky? Pošlete nám zprávu hned teď! Po obdržení vaší zprávy obsloužíme vaši žádost s celým týmem.
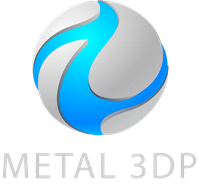
Kovové prášky pro 3D tisk a aditivní výrobu