Prášky s menšími póry zachycujícími plyn
Obsah
Obdivovali jste někdy čerstvě obroušený dřevěný povrch, jehož struktura je hladká a bezchybná? Této žádoucí hladkosti lze dosáhnout i u kovových součástí pomocí menší pórové prášky se zachycenými plyny. Ale co přesně tyto prášky jsou a jak fungují?
Porozumění práškům s póry se zachycenými menšími plyny
Představte si kovový komponent posetý drobnými nedokonalostmi – póry. Tyto póry mohou být způsobeny různými faktory během výrobního procesu, jako je tuhnutí nebo bublinky plynu zachycené v kovu. Na pomoc přicházejí drobné prášky z pórů zachycených v plynu. Jedná se o jemně rozmělněné kovové prášky obsahující mikroskopické plynové póry záměrně zavedené při jejich výrobě.
Typy, složení a vlastnosti
Zatímco různé kovové prášky spadají do kategorie menší pórové prášky se zachycenými plyny, mezi ty nejběžnější patří:
- Atomizované železné prášky: Tyto prášky, vyrobené rychlou atomizací roztaveného železa pomocí proudu plynu, nabízejí vynikající stlačitelnost a tekutost, díky čemuž jsou ideální pro aplikace, jako jsou díly práškové metalurgie (PM).
- Prášky z karbonylového železa: Tyto prášky, známé pro svou vysokou čistotu a kulovitý tvar, se vyrábějí rozkladem plynu pentakarbonylu železa. Jejich kulovitý tvar zvyšuje hustotu náplně a usnadňuje rovnoměrné slinování během procesů PM.
- Prášky se sníženým obsahem železa: Tyto prášky, získané redukcí oxidu železa plynným vodíkem, se mohou pochlubit vynikající pevností v surovém stavu (pevností před slinováním) ve srovnání s atomizovanými železnými prášky. To se promítá do lepší kontroly rozměrů u PM dílů.
- Měděné prášky: K dispozici v elektrolytické a atomizované formě, měděné prášky s menšími plynovými póry nacházejí použití v aplikacích vyžadujících vysokou elektrickou vodivost a tepelnou vodivost.
- Niklové prášky: Podobně jako měděné prášky mohou být niklové prášky elektrolytické nebo atomizované. Přítomnost plynových pórů může ovlivnit jejich tekutost a vlastnosti balení, což má dopad na aplikace, jako jsou elektrody.
- Prášky z nerezové oceli: Tyto prášky, vyrobené různými technikami, jako je atomizace nebo atomizace vody, mohou být přizpůsobeny specifickým charakteristikám plynových pórů, aby ovlivnily vlastnosti, jako je hustota a slinovací chování v částech PM.
- Hliníkové prášky: Hliníkové prášky s menšími plynovými póry se typicky používají v pyrotechnických aplikacích nebo jako reaktivní materiály v energetických směsích kvůli jejich velkému povrchu a zvýšené reaktivitě.
- Titanové prášky: Titanové prášky, které se používají v součástech PM pro letectví a lékařství, lze zkonstruovat s plynovými póry pro řízení faktorů, jako je hustota a snížení hmotnosti.
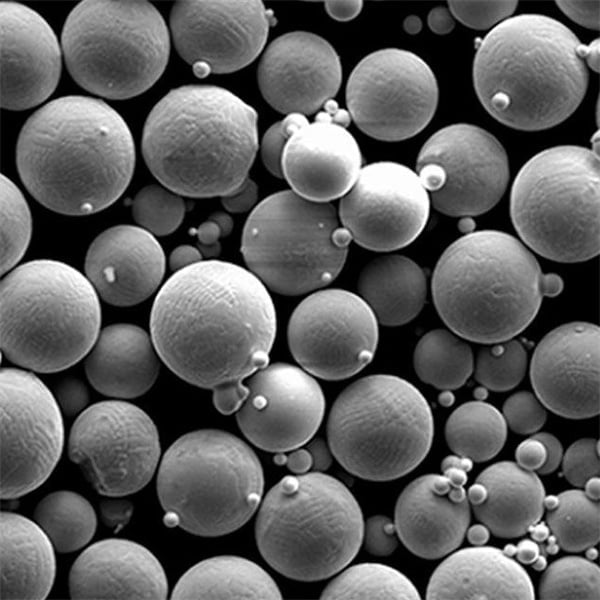
Aplikace z Prášky s menšími póry zachycujícími plyn
Strategické začlenění menších plynových pórů do kovových prášků odemyká řadu výhod:
- Vylepšená stlačitelnost: Plynové póry působí jako drobné rozpěrky v částicích prášku, což jim umožňuje efektivněji se sbalit během lisovacích operací v PM. To znamená hustší součásti se zlepšenými mechanickými vlastnostmi.
- Řízená hustota: Manipulací s velikostí a distribucí plynových pórů mohou výrobci dosáhnout specifických hustot v částech PM. Tato flexibilita je klíčová pro aplikace, kde je prioritou snížení hmotnosti, jako jsou součásti leteckého průmyslu.
- Vylepšené spékání: Plynové póry mohou usnadnit difúzi atomů během procesu slinování, kde se částice prášku spojují a vytvářejí pevnou strukturu. To může vést ke zlepšení mechanické pevnosti a celkové integritě součásti.
Aplikace napříč odvětvími
- Prášková metalurgie (PM): Drobné prášky s póry se zachycenými plyny jsou páteří PM, což umožňuje výrobu složitých kovových dílů s přesnými tvary a téměř čistými tvary (vyžadujícími minimální obrábění). Používají se v různých průmyslových odvětvích, včetně automobilového (ozubená kola, ozubená kola), spotřebičů (holicí strojky, sekačky na trávu) a lékařství (zubní implantáty, chirurgické nástroje).
- Aditivní výroba: Tyto prášky nacházejí stále větší uplatnění v technikách aditivní výroby (AM), jako je selektivní laserové slinování (SLS). Plynové póry mohou ovlivnit tekutost prášku během AM procesu a ovlivnit konečné vlastnosti tištěných dílů.
- Filtrace: Kovové prášky s řízenou charakteristikou plynových pórů lze použít jako filtrační médium v různých aplikacích. Velikost a distribuce pórů určuje účinnost filtrace pro částice různých velikostí.
Výhody a omezení
výhody:
- Vylepšená stlačitelnost a hustota balení
- Přesná kontrola hustoty v PM částech
- Vylepšené chování při slinování u pevnějších dílů
- Potenciální výhody v procesech aditivní výroby
Omezení:
- Plynové póry mohou mírně snížit mechanickou pevnost finálního komponentu ve srovnání s neporézními prášky.
- Pečlivá kontrola velikosti pórů a distribuce je zásadní pro dosažení požadovaných vlastností.
- Nemusí být vhodný pro všechny aplikace PM v závislosti na požadovaném poměru pevnosti k hmotnosti.
Úvahy při výběru Prášky s menšími póry zachycujícími plyn
Zde jsou některé klíčové faktory, které je třeba vzít v úvahu při výběru optimálního prášku s menšími póry se zachycenými plyny, vyžaduje pečlivé zvážení několika faktorů:
- Použití: Zamýšlené použití konečné složky silně ovlivňuje výběr prášku. Pro aplikace s vysokou pevností, jako jsou ozubená kola, mohou být preferovány prášky s minimálními plynovými póry. Naopak součásti upřednostňující snížení hmotnosti v letectví by mohly těžit z prášků s řízenou porézností.
- Vlastnosti prášku: Kromě charakteristik plynových pórů hrají klíčovou roli další vlastnosti prášku, jako je distribuce velikosti částic, tekutost a zdánlivá hustota. Přizpůsobení těchto vlastností konkrétnímu procesu PM nebo AM je nezbytné pro optimální výkon.
- Výběr materiálu: Různé kovové prášky nabízejí jedinečné výhody. Například měděné prášky s plynovými póry vynikají v aplikacích vyžadujících vysokou elektrickou vodivost, zatímco hliníkové prášky s porézností mohou být ideální pro pyrotechniku díky své zvýšené reaktivitě.
- Pověst dodavatele: Výběr renomovaného dodavatele s důslednou kontrolou kvality a osvědčenými výsledky v oblasti prášků s póry se zachycenými plyny zajišťuje konzistentní výkon a minimalizuje problémy s výrobou.
Pohled na specifické kovové prášky
Zatímco předchozí část poskytla obecný přehled, pojďme se hlouběji ponořit do některých specifických kovových prášků s menšími plynovými póry:
- Atomizované železné prášky vs. prášky se sníženým obsahem železa: Oba nabízejí dobrou stlačitelnost, ale redukované železné prášky se mohou pochlubit vynikající pevností v surovém stavu, díky čemuž jsou ideální pro složité díly PM vyžadující rozměrovou přesnost. Rozprášené železné prášky však mohou být nákladově efektivnější pro jednodušší součásti.
- Elektrolytické vs. atomizované měděné prášky: Elektrolytické měděné prášky mají obvykle nepravidelnější tvar ve srovnání s atomizovanými prášky. I když to může mírně ovlivnit hustotu balení, může to být výhodné pro aplikace, jako jsou elektrody, kde povrchová plocha hraje klíčovou roli.
- Prášky z nerezové oceli: Různorodá škála složení nerezové oceli umožňuje přizpůsobení charakteristik plynových pórů. Například prášky s vyšším obsahem chrómu mohou vyžadovat jinou úroveň poréznosti ve srovnání s prášky s nižším obsahem chrómu, aby se dosáhlo optimálního chování při slinování.
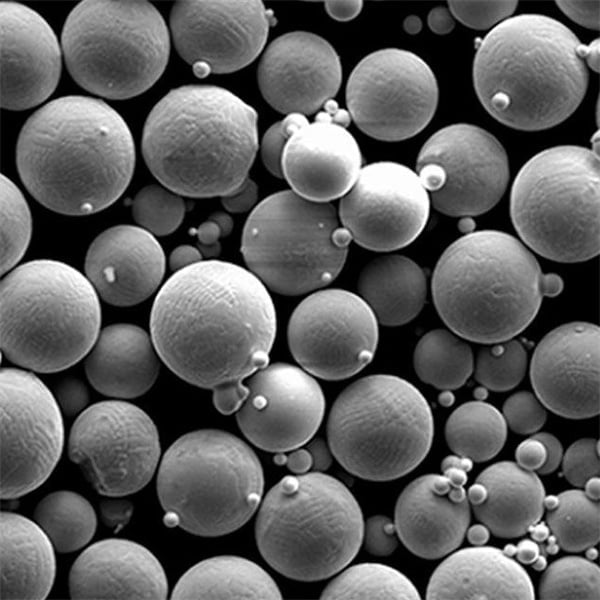
S ohledem na estetiku a udržitelnost
Zatímco technické specifikace jsou prvořadé, vaše rozhodnutí mohou ovlivnit i další faktory:
- Estetika: V aplikacích, kde je viditelná konečná součást, může být problémem povrchová úprava. Prášky s minimálními plynovými póry mohou poskytnout hladší povrchovou úpravu ve srovnání s prášky s vyšší porézností.
- Udržitelnost: Zvažte dopad procesu výroby prášku na životní prostředí. Někteří výrobci zkoumají udržitelné metody výroby prášků s póry se zachycenými plyny, čímž minimalizují svou ekologickou stopu.
FAQ
Otázka | Odpovědět |
---|---|
Jaké jsou výhody používání prášků s póry s menšími plyny? | Tyto prášky nabízejí zlepšenou stlačitelnost, řízenou hustotu v PM částech a potenciálně vylepšené slinování pro pevnější součásti. |
Existují nějaké nevýhody používání prášků s póry se zachycenými plyny? | Mohou mírně snížit mechanickou pevnost ve srovnání s neporézními prášky a vyžadují přesnou kontrolu vlastností pórů. |
Jaké jsou některé typické aplikace prášků s menšími póry se zachycenými plyny? | Mezi běžné aplikace patří prášková metalurgie (PM), aditivní výroba (AM) a filtrace. |
Jak si mohu vybrat správný prášek z pórů s menším plynem? | Zvažte použití, požadované vlastnosti, výběr materiálu, pověst dodavatele a dokonce i estetiku a udržitelnost. |
Sdílet na
MET3DP Technology Co., LTD je předním poskytovatelem řešení aditivní výroby se sídlem v Qingdao v Číně. Naše společnost se specializuje na zařízení pro 3D tisk a vysoce výkonné kovové prášky pro průmyslové aplikace.
Dotaz k získání nejlepší ceny a přizpůsobeného řešení pro vaše podnikání!
Související články
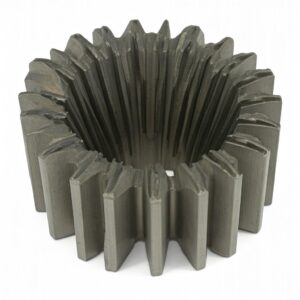
Vysoce výkonné segmenty lopatek trysek: Revoluce v účinnosti turbín díky 3D tisku z kovu
Přečtěte si více "O Met3DP
Nedávná aktualizace
Náš produkt
KONTAKTUJTE NÁS
Nějaké otázky? Pošlete nám zprávu hned teď! Po obdržení vaší zprávy obsloužíme vaši žádost s celým týmem.
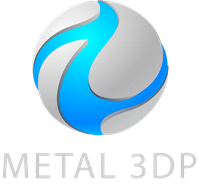
Kovové prášky pro 3D tisk a aditivní výrobu
SPOLEČNOST
PRODUKT
kontaktní informace
- Město Qingdao, Shandong, Čína
- [email protected]
- [email protected]
- +86 19116340731