Minor Gas-Trapped Pore Powders
Table of Contents
Have you ever admired a freshly sanded wooden surface, its texture smooth and flawless? That desirable smoothness can also be achieved in metal components using minor gas-trapped pore powders. But what exactly are these powders, and how do they work their magic?
Understanding Minor Gas-Trapped Pore Powders
Imagine a metal component riddled with tiny imperfections – pores. These pores can be caused by various factors during the manufacturing process, like solidification or gas bubbles trapped within the metal. Minor gas-trapped pore powders come to the rescue. These are finely divided metallic powders containing microscopic gas pores deliberately introduced during their production.
Types, Composition, and Properties
While various metal powders fall under the category of minor gas-trapped pore powders, some of the most common ones include:
- Atomized Iron Powders: Produced by rapidly atomizing molten iron using a gas stream, these powders offer excellent compressibility and flowability, making them ideal for applications like Powder Metallurgy (PM) parts.
- Carbonyl Iron Powders: Known for their high purity and spherical shape, these powders are manufactured by decomposing iron pentacarbonyl gas. Their spherical form enhances packing density and facilitates even sintering during PM processes.
- Reduced Iron Powders: Obtained by reducing iron oxide with hydrogen gas, these powders boast superior green strength (strength before sintering) compared to atomized iron powders. This translates to better dimensional control in PM parts.
- Copper Powders: Available in electrolytic and atomized forms, copper powders with minor gas pores find use in applications requiring high electrical conductivity and thermal conductivity.
- Nickel Powders: Similar to copper powders, nickel powders can be electrolytic or atomized. The presence of gas pores can influence their flowability and packing characteristics, impacting applications like electrodes.
- Stainless Steel Powders: These powders, produced through various techniques like atomization or water atomization, can be tailored with specific gas pore characteristics to influence properties like density and sintering behavior in PM parts.
- Aluminum Powders: Aluminum powders with minor gas pores are typically used in pyrotechnic applications or as reactive materials in energetic mixtures due to their high surface area and enhanced reactivity.
- Titanium Powders: Used in PM parts for aerospace and medical applications, titanium powders can be engineered with gas pores to control factors like density and weight reduction.
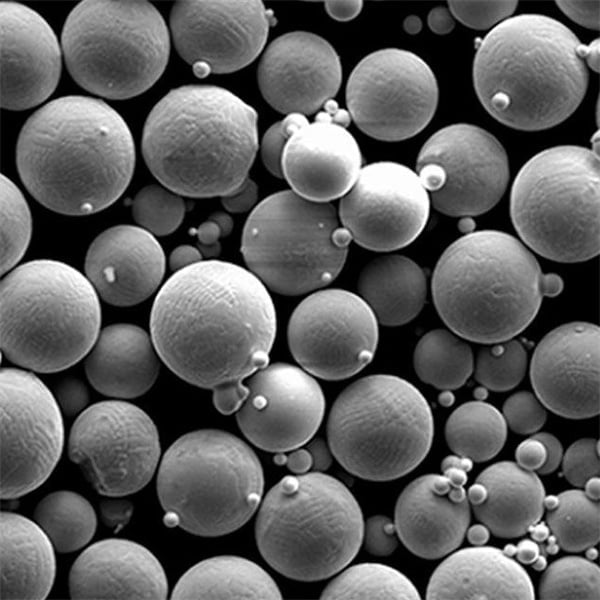
Applications of Minor Gas-Trapped Pore Powders
The strategic incorporation of minor gas pores in metal powders unlocks a range of benefits:
- Improved Compressibility: Gas pores act like tiny spacers within the powder particles, allowing them to pack more efficiently during pressing operations in PM. This translates to denser components with enhanced mechanical properties.
- Controlled Density: By manipulating the size and distribution of gas pores, manufacturers can achieve specific densities in PM parts. This flexibility is crucial for applications where weight reduction is a priority, such as in aerospace components.
- Enhanced Sintering: Gas pores can facilitate the diffusion of atoms during the sintering process, where powder particles bond together to form a solid structure. This can lead to improved mechanical strength and overall part integrity.
Applications across Industries
- Powder Metallurgy (PM): Minor gas-trapped pore powders are the backbone of PM, enabling the production of complex metal parts with precise shapes and near-net shapes (requiring minimal machining). They are used in various industries, including automotive (gears, sprockets), appliance (shavers, lawnmowers), and medical (dental implants, surgical instruments).
- Additive Manufacturing: These powders are finding increasing use in Additive Manufacturing (AM) techniques like Selective Laser Sintering (SLS). The gas pores can influence the flowability of the powder during the AM process and impact the final properties of the printed parts.
- Filtration: Metal powders with controlled gas pore characteristics can be used as filter media in various applications. The size and distribution of the pores determine the filtration efficiency for particles of different sizes.
Advantages and Limitations
Advantages:
- Enhanced compressibility and packing density
- Precise control over density in PM parts
- Improved sintering behavior for stronger parts
- Potential benefits in Additive Manufacturing processes
Limitations:
- Gas pores can slightly reduce the mechanical strength of the final component compared to non-porous powders.
- Careful control of pore size and distribution is crucial to achieve desired properties.
- May not be suitable for all PM applications depending on the required strength-to-weight ratio.
Considerations When Selecting Minor Gas-Trapped Pore Powders
Here are some key factors to consider when choosing the optimal minor gas-trapped pore powder requires careful consideration of several factors:
- Application: The intended use of the final component heavily influences the powder selection. For high-strength applications like gears, powders with minimal gas pores might be preferred. Conversely, components prioritizing weight reduction in aerospace might benefit from powders with controlled porosity.
- Powder Properties: Beyond gas pore characteristics, other powder properties like particle size distribution, flowability, and apparent density play a crucial role. Matching these properties to the specific PM or AM process is essential for optimal performance.
- Material Selection: Different metal powders offer unique advantages. For instance, copper powders with gas pores excel in applications requiring high electrical conductivity, while aluminum powders with porosity might be ideal for pyrotechnics due to their enhanced reactivity.
- Supplier Reputation: Selecting a reputable supplier with consistent quality control and a proven track record in gas-trapped pore powders ensures consistent performance and minimizes production issues.
A Look at Specific Metal Powders
While the previous section provided a general overview, let’s delve deeper into some specific metal powders with minor gas pores:
- Atomized Iron Powders vs. Reduced Iron Powders: Both offer good compressibility, but reduced iron powders boast superior green strength, making them ideal for complex PM parts requiring dimensional accuracy. However, atomized iron powders might be more cost-effective for simpler components.
- Electrolytic vs. Atomized Copper Powders: Electrolytic copper powders typically have a more irregular shape compared to atomized powders. While this can impact packing density slightly, it might be beneficial for applications like electrodes where surface area plays a crucial role.
- Stainless Steel Powders: The diverse range of stainless steel compositions allows for tailored gas pore characteristics. For instance, powders with higher chromium content might require a different level of porosity compared to those with lower chromium content to achieve optimal sintering behavior.
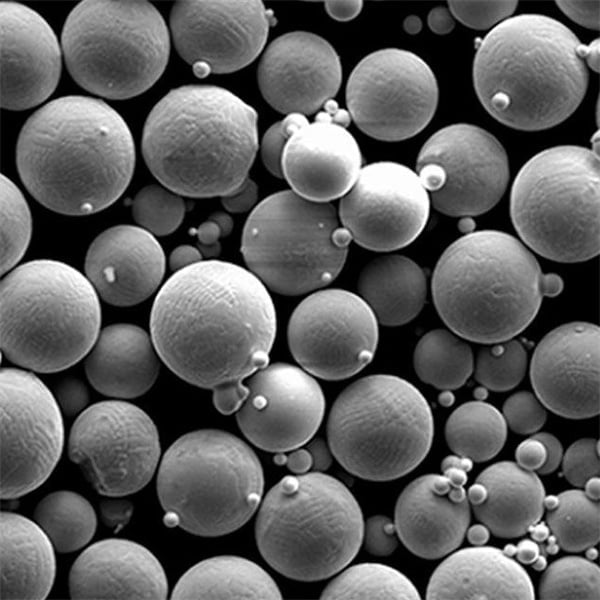
Considering Aesthetics and Sustainability
While technical specifications are paramount, other factors can influence your decision:
- Aesthetics: In applications where the final component is visible, the surface finish can be a concern. Powders with minimal gas pores might yield a smoother surface finish compared to those with higher porosity.
- Sustainability: Consider the environmental impact of the powder production process. Some manufacturers are exploring sustainable methods for producing gas-trapped pore powders, minimizing their environmental footprint.
FAQ
Question | Answer |
---|---|
What are the benefits of using minor gas-trapped pore powders? | These powders offer improved compressibility, controlled density in PM parts, and potentially enhanced sintering for stronger components. |
Are there any drawbacks to using gas-trapped pore powders? | They can slightly reduce the mechanical strength compared to non-porous powders, and require precise control of pore characteristics. |
What are some typical applications of minor gas-trapped pore powders? | Powder Metallurgy (PM), Additive Manufacturing (AM), and filtration are some common applications. |
How do I choose the right minor gas-trapped pore powder? | Consider the application, desired properties, material selection, supplier reputation, and even aesthetics and sustainability. |
Share On
MET3DP Technology Co., LTD is a leading provider of additive manufacturing solutions headquartered in Qingdao, China. Our company specializes in 3D printing equipment and high-performance metal powders for industrial applications.
Inquiry to get best price and customized Solution for your business!
Related Articles
About Met3DP
Recent Update
Our Product
CONTACT US
Any questions? Send us message now! We’ll serve your request with a whole team after receiving your message.
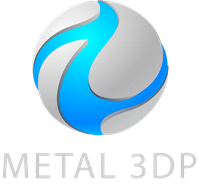
Metal Powders for 3D Printing and Additive Manufacturing
COMPANY
PRODUCT
cONTACT INFO
- Qingdao City, Shandong, China
- [email protected]
- [email protected]
- +86 19116340731