Directed Energy Deposition (DED)
Table of Contents
Directed Energy Deposition (DED) is a sophisticated additive manufacturing technique that’s revolutionizing the world of metal fabrication. Whether you’re a seasoned engineer, a curious tech enthusiast, or someone diving into 3D printing for the first time, this article will walk you through every aspect of DED. From the basics to advanced applications, we’ll cover it all in a friendly, conversational style.
Overview of Directed Energy Deposition (DED)
Directed Energy Deposition is a process that involves melting material, typically metal powder or wire, using a focused energy source such as a laser, electron beam, or plasma arc. This melted material is then deposited precisely where it’s needed, layer by layer, to build up a three-dimensional object. Think of it like a high-tech welding process, but with extreme precision and control.
Types of Directed Energy Deposition (DED) Systems
DED systems can vary significantly based on the energy source and material used. Here’s a breakdown:
Type | Energy Source | Material | Key Characteristics |
---|---|---|---|
Laser-Based DED | Laser | Metal powder/wire | High precision, excellent surface finish, versatile |
Electron Beam DED | Electron beam | Metal powder/wire | High energy efficiency, suitable for high-melting-point metals |
Plasma Arc DED | Plasma arc | Metal powder/wire | Cost-effective, robust, good for large parts |
Each type has its strengths and weaknesses, making them suitable for different applications. For example, laser-based systems are known for their precision, making them ideal for aerospace components, while plasma arc systems are favored for their cost-effectiveness in producing large parts.
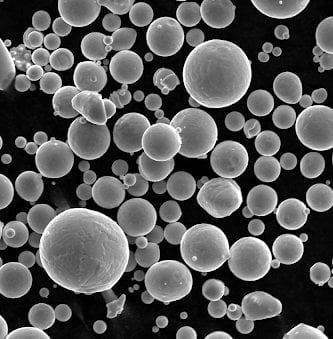
Metal Powder Models for Directed Energy Deposition
Selecting the right metal powder is crucial for the success of DED processes. Here are ten popular metal powders used in DED, along with their descriptions:
- Inconel 718: A nickel-chromium alloy known for its high strength and corrosion resistance, ideal for aerospace and high-temperature applications.
- Ti-6Al-4V (Titanium Grade 5): This titanium alloy is known for its high strength-to-weight ratio and excellent corrosion resistance, commonly used in aerospace and biomedical applications.
- Stainless Steel 316L: An austenitic stainless steel with excellent corrosion resistance and good mechanical properties, often used in marine and medical applications.
- AlSi10Mg: An aluminum alloy with good strength and thermal properties, widely used in automotive and aerospace industries.
- Cobalt-Chrome (CoCr): Known for its high wear resistance and biocompatibility, making it perfect for dental and orthopedic implants.
- Tool Steel H13: A hot-work tool steel with excellent toughness and heat resistance, ideal for die-casting and extrusion applications.
- Copper (Cu): Offers excellent electrical and thermal conductivity, used in electrical components and heat exchangers.
- Nickel Alloy 625: A nickel-based superalloy with high strength and resistance to oxidation and corrosion, suitable for chemical processing and marine applications.
- Maraging Steel: Known for its high strength and toughness, commonly used in aerospace and tooling applications.
- Aluminum 7075: An aluminum alloy with high strength, often used in aerospace and military applications.
Applications of Directed Energy Deposition (DED)
DED technology has a wide range of applications across various industries. Here’s a look at some of the most common uses:
Application | Industry | Examples |
---|---|---|
Aerospace | Aerospace | Turbine blades, structural components |
Medical | Biomedical | Custom implants, prosthetics |
Automotive | Automotive | Engine components, prototype parts |
Tooling | Manufacturing | Molds, dies, tooling fixtures |
Energy | Energy | Turbine components, heat exchangers |
Marine | Marine | Propellers, structural components |
Defense | Defense | Armament components, repair of military equipment |
Specifications and Standards for Metal Powders in DED
When selecting metal powders for DED, it’s essential to consider various specifications and standards to ensure quality and performance. Here are some key details:
Material | Particle Size | Purity | Standards |
---|---|---|---|
Inconel 718 | 15-45 µm | >99.9% | ASTM B637, AMS 5662 |
Ti-6Al-4V | 15-45 µm | >99.5% | ASTM F2924, AMS 4998 |
Stainless Steel 316L | 15-45 µm | >99.5% | ASTM F3184, AMS 5653 |
AlSi10Mg | 20-63 µm | >99.5% | EN 1706, ASTM B85 |
Cobalt-Chrome (CoCr) | 15-45 µm | >99.9% | ASTM F75, ISO 5832-4 |
Tool Steel H13 | 15-45 µm | >99.9% | ASTM A681, AMS 6487 |
Copper (Cu) | 15-45 µm | >99.9% | ASTM B216, ISO 9208 |
Nickel Alloy 625 | 15-45 µm | >99.9% | ASTM B443, AMS 5599 |
Maraging Steel | 15-45 µm | >99.9% | AMS 6514, ASTM A538 |
Aluminum 7075 | 20-63 µm | >99.5% | ASTM B211, AMS 4045 |
Suppliers and Pricing Details for Metal Powders
Understanding the market and pricing details is vital for budgeting and planning. Here’s a comparison of some major suppliers and their pricing details for various metal powders used in DED:
Supplier | Material | Price/kg (USD) | Lead Time | MOQ |
---|---|---|---|---|
Praxair Surface Tech | Inconel 718 | $100 | 2-4 weeks | 10 kg |
Carpenter Technology | Ti-6Al-4V | $120 | 3-5 weeks | 5 kg |
Sandvik | Stainless Steel 316L | $80 | 2-3 weeks | 10 kg |
Höganäs | AlSi10Mg | $70 | 2-4 weeks | 15 kg |
Arcam AB | Cobalt-Chrome (CoCr) | $200 | 4-6 weeks | 5 kg |
GKN Additive | Tool Steel H13 | $90 | 2-3 weeks | 10 kg |
Heraeus | Copper (Cu) | $150 | 3-4 weeks | 10 kg |
VDM Metals | Nickel Alloy 625 | $110 | 3-5 weeks | 5 kg |
Aubert & Duval | Maraging Steel | $130 | 4-6 weeks | 5 kg |
ECKA Granules | Aluminum 7075 | $60 | 2-3 weeks | 20 kg |
Advantages and Limitations of Directed Energy Deposition (DED)
DED technology offers numerous advantages but also comes with certain limitations. Here’s a comparison:
Advantages | Limitations |
---|---|
High precision and accuracy | High initial setup cost |
Ability to repair and add material | Requires skilled operators |
Suitable for a wide range of materials | Limited by part size and complexity |
Reduced material waste | Slower production speeds |
Excellent mechanical properties | Post-processing often required |
Versatility in applications | High energy consumption |
Key Parameters in Directed Energy Deposition (DED)
Understanding the key parameters in DED is essential for optimizing the process. Here are some critical factors:
Parameter | Description |
---|---|
Laser Power | Determines the energy input and affects melting |
Scan Speed | Affects layer quality and build time |
Layer Thickness | Influences surface finish and mechanical properties |
Powder Feed Rate | Controls material deposition rate |
Shielding Gas Flow | Protects the melt pool from oxidation |
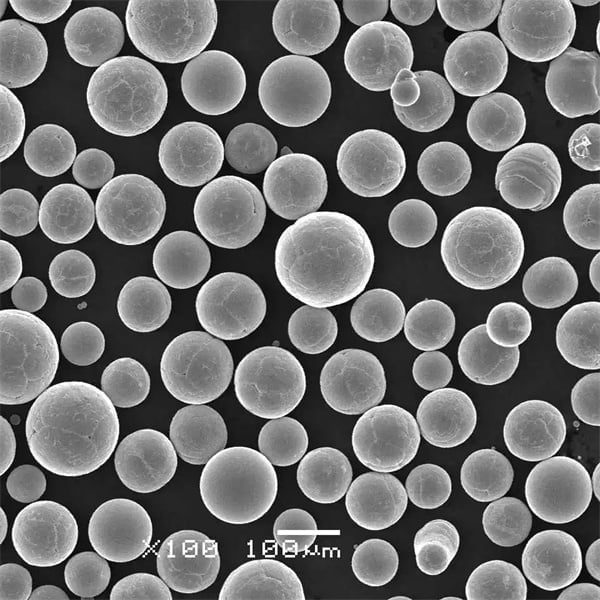
FAQs
1. What is Directed Energy Deposition (DED)?
DED is a 3D printing process that uses focused energy sources, such as lasers, electron beams, or plasma arcs, to melt feedstock material and deposit it onto a substrate. This process allows for the creation of complex geometries, repair of existing components, and additive manufacturing.
2. What are the common types of energy sources used in DED?
Common energy sources for DED include:
- Laser: High-intensity light beams focused to melt the feedstock.
- Electron Beam: High-energy electrons used to melt the feedstock in a vacuum environment.
- Plasma Arc: A high-temperature plasma arc used to melt and deposit material.
3. What types of materials can be used in DED?
DED can use a variety of materials, including:
- Metals: Steel, titanium, aluminum, nickel alloys, etc.
- Metal Matrix Composites: Metals reinforced with ceramic particles or fibers.
- Certain Ceramics: For specialized applications.
4. What are the typical applications of DED?
DED is used in various applications, such as:
- Repair and Maintenance: Restoring worn or damaged parts in industries like aerospace, automotive, and energy.
- Custom Parts Manufacturing: Creating complex, customized components for various industries.
- Prototyping: Developing new designs and products.
- Tooling: Producing or repairing tools and dies.
5. What industries benefit most from DED technology?
Industries that benefit from DED include:
- Aerospace: For component repair and manufacturing.
- Automotive: For parts production and repair.
- Energy: Repairing turbine blades and other critical components.
- Medical: Custom implants and prosthetics.
Share On
MET3DP Technology Co., LTD is a leading provider of additive manufacturing solutions headquartered in Qingdao, China. Our company specializes in 3D printing equipment and high-performance metal powders for industrial applications.
Inquiry to get best price and customized Solution for your business!
Related Articles
About Met3DP
Recent Update
Our Product
CONTACT US
Any questions? Send us message now! We’ll serve your request with a whole team after receiving your message.
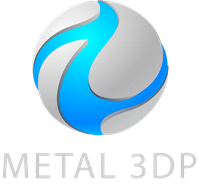
Metal Powders for 3D Printing and Additive Manufacturing