Dual-Phase Alloy Powder
Table of Contents
Overview of Dual-Phase Alloy Powder
Dual-phase alloy powders are revolutionizing the materials engineering and manufacturing sectors. These powders are composed of two distinct phases, usually a soft and a hard phase, which combine to offer unique mechanical properties. They are employed in various applications, from automotive parts to aerospace components, due to their superior strength, ductility, and wear resistance.
What is Dual-Phase Alloy Powder?
At its core, dual-phase alloy powder is a blend of two different metal phases, typically in a finely powdered form. This combination allows manufacturers to harness the best properties of each metal, resulting in a material that is both strong and malleable. Imagine having a tool that is as tough as a diamond yet flexible enough to withstand bending – that’s the essence of dual-phase alloy powder.
Why Dual-Phase Alloy Powders Matter
In a world where the demand for high-performance materials is ever-increasing, dual-phase alloy powders stand out. They provide a balanced mix of hardness and ductility, making them ideal for high-stress applications. Think of them as the superheroes of the materials world, combining the best traits of their components to achieve feats that single-phase materials can’t.
Key Characteristics of Dual-Phase Alloy Powders
- High Strength: The hard phase imparts significant strength to the alloy.
- Excellent Ductility: The soft phase allows the material to bend and stretch without breaking.
- Wear Resistance: They withstand wear and tear better than many single-phase materials.
- Versatility: Suitable for various manufacturing processes, including additive manufacturing.
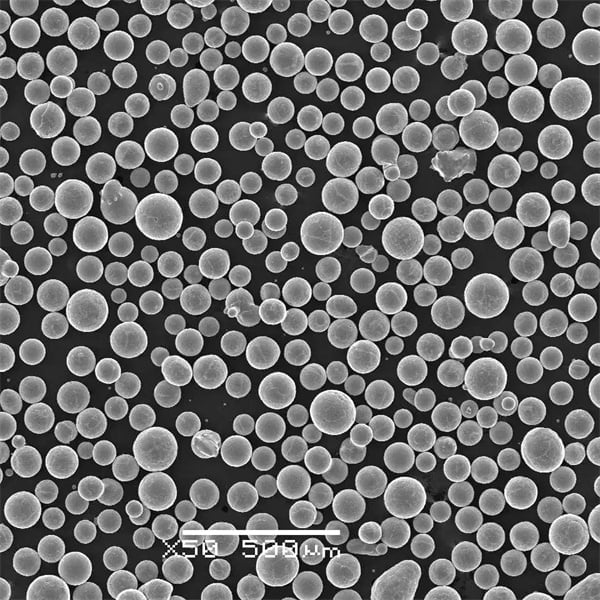
Types and Models of Dual-Phase Alloy Powders
When diving into the world of dual-phase alloy powders, it’s essential to understand the different types and models available. Here are ten specific models that showcase the diversity and capabilities of these materials.
1. DP600
Composition: 60% Ferrite, 40% Martensite
Properties: High tensile strength, good formability
Applications: Automotive panels, structural components
2. DP800
Composition: 50% Ferrite, 50% Martensite
Properties: Balanced strength and ductility
Applications: Crash-relevant automotive parts, lightweight structures
3. DP980
Composition: 40% Ferrite, 60% Martensite
Properties: Higher strength, moderate ductility
Applications: Reinforced automotive frames, safety components
4. DP1000
Composition: 35% Ferrite, 65% Martensite
Properties: Excellent strength, reduced weight
Applications: High-strength automotive parts, aerospace fittings
5. DP1200
Composition: 30% Ferrite, 70% Martensite
Properties: Extreme strength, lower formability
Applications: Structural reinforcements, heavy-duty machinery
6. DP1400
Composition: 25% Ferrite, 75% Martensite
Properties: Superior strength, limited ductility
Applications: High-stress components, advanced aerospace structures
7. DP1600
Composition: 20% Ferrite, 80% Martensite
Properties: Maximum strength, minimal ductility
Applications: Ultra-high-strength applications, critical structural parts
8. DP1800
Composition: 15% Ferrite, 85% Martensite
Properties: Extreme tensile strength, very low ductility
Applications: Specialized defense components, extreme load-bearing parts
9. DP2000
Composition: 10% Ferrite, 90% Martensite
Properties: Ultimate strength, almost no ductility
Applications: High-performance sports equipment, specialized industrial tools
10. DP2200
Composition: 5% Ferrite, 95% Martensite
Properties: Peak strength, negligible formability
Applications: Advanced engineering projects, cutting-edge aerospace designs
Composition and Properties of Dual-Phase Alloy Powders
To fully grasp the potential of dual-phase alloy powders, understanding their composition and properties is crucial. The composition directly affects their characteristics and suitability for various applications.
Type | Composition | Strength | Ductility | Applications |
---|---|---|---|---|
DP600 | 60% Ferrite, 40% Martensite | High | Good | Automotive panels, structural components |
DP800 | 50% Ferrite, 50% Martensite | Balanced | Moderate | Crash-relevant parts, lightweight structures |
DP980 | 40% Ferrite, 60% Martensite | Higher | Moderate | Reinforced frames, safety components |
DP1000 | 35% Ferrite, 65% Martensite | Excellent | Reduced | High-strength parts, aerospace fittings |
DP1200 | 30% Ferrite, 70% Martensite | Extreme | Low | Structural reinforcements, heavy machinery |
DP1400 | 25% Ferrite, 75% Martensite | Superior | Limited | High-stress components, advanced structures |
DP1600 | 20% Ferrite, 80% Martensite | Maximum | Minimal | Ultra-high-strength applications, critical parts |
DP1800 | 15% Ferrite, 85% Martensite | Extreme | Very Low | Defense components, load-bearing parts |
DP2000 | 10% Ferrite, 90% Martensite | Ultimate | Negligible | High-performance sports equipment, industrial tools |
DP2200 | 5% Ferrite, 95% Martensite | Peak | None | Advanced engineering, aerospace designs |
Applications of Dual-Phase Alloy Powder
Dual-phase alloy powders are incredibly versatile, finding applications in a wide range of industries. Here’s a closer look at how these powders are utilized.
Automotive Industry
The automotive industry is a primary user of dual-phase alloy powders, thanks to their superior strength-to-weight ratio. These materials are used in:
- Crash-Resistant Components: DP800 and DP980 are popular choices for manufacturing parts that need to absorb impact during collisions.
- Lightweight Structural Parts: DP1000 and DP1200 are used in creating lightweight yet strong frames, enhancing fuel efficiency and performance.
Aerospace Industry
In aerospace, every gram counts. Dual-phase alloy powders help create:
- Aircraft Fuselages: DP1400 and DP1600 are used for crafting durable and lightweight fuselages.
- Engine Components: DP1800 and DP2000 are employed in high-stress areas of engines where both strength and heat resistance are critical.
Defense Sector
For defense applications, the need for materials that can withstand extreme conditions is paramount. Dual-phase alloys are used in:
- Armor Plating: DP2000 and DP2200 provide the necessary toughness for protective armor.
- Advanced Weaponry: These materials ensure that weapons are both durable and reliable under harsh conditions.
Industrial Manufacturing
In industrial manufacturing, dual-phase alloy powders are used for making:
- Heavy Machinery: DP1200 and DP1400 are ideal for components that need to withstand significant wear and tear.
- Specialized Tools: DP1600 and DP1800 are used in tools that require both durability and precision.
Industry | Applications | Powder Models |
---|---|---|
Automotive | Crash-resistant components, lightweight parts | DP600, DP800, DP980, DP1000 |
Aerospace | Aircraft fuselages, engine components | DP1400, DP1600, DP1800, DP2000 |
Defense | Armor plating, advanced weaponry | DP2000, DP2200 |
Industrial | Heavy machinery, specialized tools | DP1200, DP1400, DP1600, DP1800 |
Specifications, Sizes, Grades, and Standards
Understanding the specifications, sizes, grades, and standards of dual-phase alloy powders is crucial for selecting the right material for your application.
Specifications
- Particle Size: Typically ranges from 10 to 100 micrometers, depending on the application.
- Purity: High-purity powders ensure consistent properties and performance.
- Density: Varies based on composition, typically between 7.8 to 8.5 g/cm³.
Sizes
Dual-phase alloy powders are available in various sizes to suit different manufacturing processes:
- Fine Powder: (< 20 micrometers) for precision applications like additive manufacturing.
- Medium Powder: (20-50 micrometers) for general manufacturing needs.
- Coarse Powder: (> 50 micrometers) for heavy-duty applications.
Grades and Standards
- ASTM Standards: Various ASTM standards apply, ensuring consistency and reliability in material properties.
- ISO Standards: International standards provide guidelines for composition, quality, and performance.
Specification | Range |
---|---|
Particle Size | 10 to 100 micrometers |
Purity | High-purity |
Density | 7.8 to 8.5 g/cm³ |
Fine Powder Size | < 20 micrometers |
Medium Powder Size | 20-50 micrometers |
Coarse Powder Size | > 50 micrometers |
Standards | ASTM, ISO |
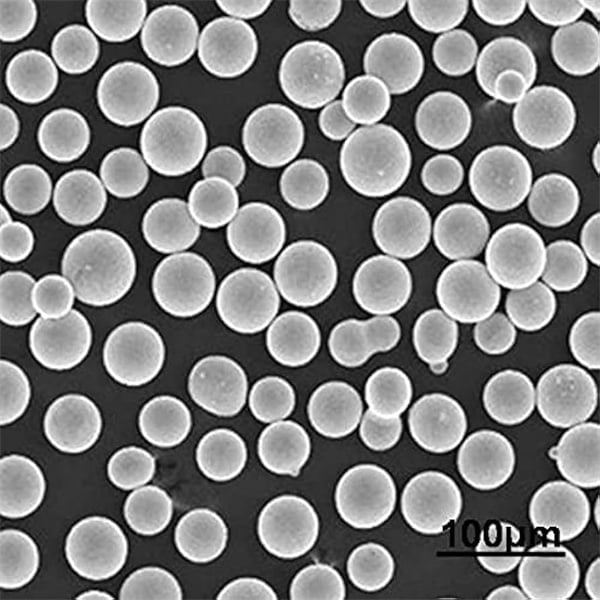
Suppliers and Pricing Details
Finding reliable suppliers and understanding pricing details are essential for procurement. Here’s a list of prominent suppliers and an overview of their offerings.
Top Suppliers
- Sandvik Materials Technology
- Products: DP600, DP800, DP1000
- Pricing: $50-$100/kg
- Höganäs AB
- Products: DP980, DP1200, DP1400
- Pricing: $80-$120/kg
- Carpenter Technology
- Products: DP1600, DP1800, DP2000
- Pricing: $100-$150/kg
- Rio Tinto Metal Powders
- Products: DP2200, custom grades
- Pricing: $120-$180/kg
Pricing Overview
The price of dual-phase alloy powders can vary based on composition, purity, and supplier. Generally, prices range from $50 to $180 per kilogram, reflecting the complexity and quality of the materials.
Supplier | Products | Pricing |
---|---|---|
Sandvik Materials Technology | DP600, DP800, DP1000 | $50-$100/kg |
Höganäs AB | DP980, DP1200, DP1400 | $80-$120/kg |
Carpenter Technology | DP1600, DP1800, DP2000 | $100-$150/kg |
Rio Tinto Metal Powders | DP2200, custom grades | $120-$180/kg |
Advantages and Disadvantages of Dual-Phase Alloy Powder
Understanding the pros and cons of dual-phase alloy powders helps in making informed decisions for specific applications.
Advantages
- Superior Strength and Ductility: Combining hard and soft phases provides an optimal balance of strength and flexibility.
- Enhanced Wear Resistance: These materials can endure high wear and tear, extending the life of components.
- Versatility: Suitable for a wide range of applications across various industries.
- Customization: Compositions can be tailored to meet specific needs.
Disadvantages
- Cost: Higher production costs compared to single-phase alloys.
- Complex Manufacturing Process: Requires sophisticated technology and expertise.
- Limited Availability: Not as widely available as traditional alloys, leading to potential supply chain issues.
Advantages | Disadvantages |
---|---|
Superior strength and ductility | Higher production costs |
Enhanced wear resistance | Complex manufacturing process |
Versatility | Limited availability |
Customization |
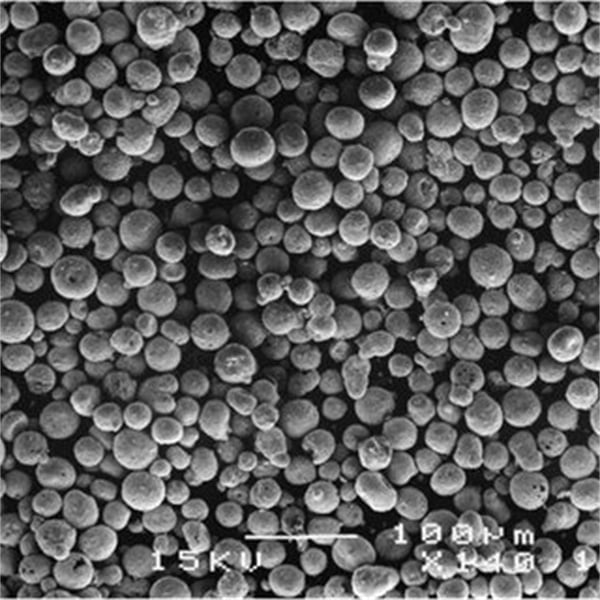
Comparing Dual-Phase Alloy Powder Models
When selecting a dual-phase alloy powder, comparing different models helps identify the best fit for your application.
DP600 vs. DP800
- Strength: DP800 offers higher strength than DP600.
- Ductility: DP600 provides better ductility, making it easier to form.
- Applications: DP600 is ideal for general structural parts, while DP800 is better suited for crash-resistant components.
DP1000 vs. DP1200
- Strength: DP1200 has higher strength but lower ductility compared to DP1000.
- Weight: Both provide weight savings, but DP1200 offers greater structural integrity.
- Applications: DP1000 is used in automotive parts, whereas DP1200 finds applications in heavy machinery.
DP1400 vs. DP1600
- Strength: DP1600 boasts superior strength over DP1400.
- Formability: DP1400 is easier to form and process.
- Applications: DP1400 is common in aerospace structures, while DP1600 is used in ultra-high-strength applications.
DP1800 vs. DP2000
- Strength: DP2000 is stronger but less ductile than DP1800.
- Heat Resistance: DP2000 offers better performance in high-temperature environments.
- Applications: DP1800 is used in defense components, whereas DP2000 is preferred for high-performance sports equipment.
Comparison | DP600 | DP800 | DP1000 | DP1200 | DP1400 | DP1600 | DP1800 | DP2000 |
---|---|---|---|---|---|---|---|---|
Strength | High | Higher | Excellent | Extreme | Superior | Maximum | Extreme | Ultimate |
Ductility | Better | Good | Reduced | Low | Limited | Minimal | Very Low | Negligible |
Applications | Structural parts | Crash-resistant components | Automotive parts | Heavy machinery | Aerospace structures | Ultra-high-strength applications | Defense components | High-performance sports equipment |
Weight Savings | Moderate | Higher | High | Greater | Significant | Substantial | Significant | Critical |
FAQ
Question | Answer |
---|---|
What is dual-phase alloy powder? | A blend of two different metal phases, typically a hard and a soft phase, combined to offer unique mechanical properties such as high strength and excellent ductility. |
Why is dual-phase alloy powder important? | It provides a balanced mix of hardness and ductility, making it ideal for high-stress applications in industries like automotive, aerospace, and defense. |
What are the key properties of dual-phase alloy powder? | High strength, excellent ductility, wear resistance, and versatility in manufacturing processes. |
How is dual-phase alloy powder used in the automotive industry? | Used in crash-resistant components, lightweight structural parts, and reinforced automotive frames. |
What are the advantages of dual-phase alloy powders? | Superior strength and ductility, enhanced wear resistance, versatility, and customization options. |
What are the disadvantages of dual-phase alloy powders? | Higher production costs, complex manufacturing processes, and limited availability. |
How do DP600 and DP800 differ? | DP800 offers higher strength than DP600, while DP600 provides better ductility, making it easier to form and process. |
What specifications are important for dual-phase alloy powders? | Particle size, purity, density, and compliance with standards like ASTM and ISO. |
Who are the top suppliers of dual-phase alloy powders? | Sandvik Materials Technology, Höganäs AB, Carpenter Technology, and Rio Tinto Metal Powders. |
What are the typical applications of dual-phase alloy powders? | Automotive parts, aerospace components, defense applications, heavy machinery, and specialized tools. |
In conclusion, dual-phase alloy powders offer a remarkable combination of strength and ductility, making them indispensable in various high-performance applications. Whether you are in the automotive, aerospace, defense, or industrial manufacturing sectors, understanding the nuances of these materials can help you make informed decisions and leverage their full potential.
Share On
MET3DP Technology Co., LTD is a leading provider of additive manufacturing solutions headquartered in Qingdao, China. Our company specializes in 3D printing equipment and high-performance metal powders for industrial applications.
Inquiry to get best price and customized Solution for your business!
Related Articles
About Met3DP
Recent Update
Our Product
CONTACT US
Any questions? Send us message now! We’ll serve your request with a whole team after receiving your message.
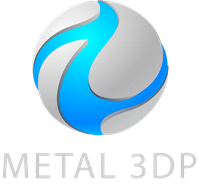
Metal Powders for 3D Printing and Additive Manufacturing
COMPANY
PRODUCT
cONTACT INFO
- Qingdao City, Shandong, China
- [email protected]
- [email protected]
- +86 19116340731