dual-phase alloy powder
Table of Contents
Imagine a material that’s both incredibly strong and surprisingly flexible. That’s the magic of dual-phase alloy powders! These finely-ground metal particles hold the key to producing components that can withstand heavy loads while still being shaped into intricate designs. In this comprehensive guide, we’ll delve deep into the world of dual-phase alloy powders, exploring their composition, properties, applications, and the specific models that reign supreme in the industry. Buckle up, engineers and makers, because we’re about to unlock the potential of these remarkable materials!
Unveiling the Composition: A Tale of Two Phases
Dual-phase alloy powders, as the name suggests, are a unique blend of two distinct metallic phases. Typically, these phases consist of a soft, ductile ferrite matrix and a dispersion of hard, high-strength martensite islands. This combination creates a synergistic effect, where the ferrite phase grants excellent formability for shaping the material, while the martensite islands act as reinforcements, boosting overall strength and wear resistance.
Here’s an analogy: Think of the ferrite matrix as a bed of fluffy pillows, offering a comfortable base for shaping. The martensite islands, on the other hand, are like strategically placed steel rods within the pillows, providing support and preventing excessive deformation.
The specific composition of these powders varies depending on the desired final properties. Here’s a table outlining some common elements and their influence:
Element | Influence on Properties |
---|---|
Iron (Fe) | Base element, determines overall weight and magnetic properties |
Manganese (Mn) | Improves hardenability and strength |
Carbon (C) | Crucial for the formation of martensite, affects strength and hardness |
Silicon (Si) | Improves deoxidization and flowability of the powder |
Chromium (Cr) | Enhances corrosion resistance and high-temperature strength |
Nickel (Ni) | Improves toughness and ductility |
Chemical Composition of Dual-Phase Alloy Powders
Alloy | Typical Composition (wt%) |
---|---|
Fe-1.5Mo | Fe-1.5Mo, (C, Mn, Si) |
Fe-2Cr-0.5Mo | Fe-2Cr-0.5Mo, (C, Mn, Si) |
Fe-3Cr-Mo | Fe-3Cr-Mo, (C, Mn, Si) |
17-4PH | 16.5-18.5 Ni, 4.5-5.5 Cr, <0.05 C, (Cu, Nb, Si, Mn) |
Please note: This table provides a general overview, and the specific composition can vary depending on the manufacturer and desired properties.
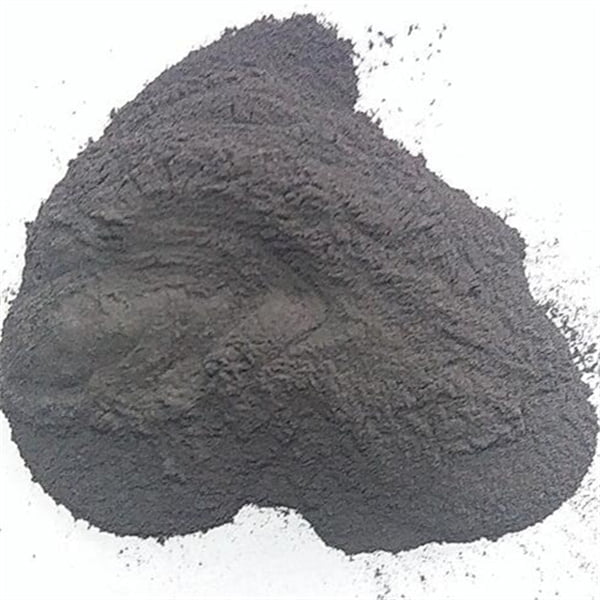
A Spectrum of Properties: Strength Meets Formability
The beauty of dual-phase alloy powders lies in their ability to combine seemingly opposing characteristics:
- High Strength: The presence of martensite islands significantly enhances the tensile strength and yield strength of the final component compared to single-phase steels. Imagine building a bridge – dual-phase alloy powders would ensure it can withstand immense weight without buckling.
- Good Ductility: The ferrite matrix allows the material to be shaped and formed into complex geometries without cracking. Think of intricate car parts – dual-phase powders enable the creation of these shapes while maintaining structural integrity.
- Improved Workability: Compared to high-strength steels, dual-phase alloy powders offer better cold-workability, allowing for easier shaping and forming processes. Imagine shaping a sheet metal component – these powders make the process less prone to tearing or breaking.
- Tailorable Properties: By adjusting the composition and processing parameters, manufacturers can fine-tune the strength, ductility, and workability of the final component to meet specific application needs. Imagine building a lightweight yet robust bicycle frame – these powders offer the flexibility to achieve that balance.
The Advantages of Dual-Phase Alloy Powders
Advantage | Benefit |
---|---|
High Strength | Enables the creation of lightweight yet strong components |
Good Ductility | Allows for efficient shaping and forming of complex geometries |
Improved Workability | Facilitates easier cold-working processes |
Tailorable Properties | Offers flexibility to achieve desired strength-ductility balance |
Unleashing Potential: Applications Galore
Dual-phase alloy powders are finding their way into a diverse range of applications due to their unique properties:
- Automotive Industry: From lightweight car body components to high-strength suspension parts, dual-phase alloy powders are revolutionizing the automotive industry. Their ability to offer both strength and formability makes them ideal for creating lighter vehicles with improved fuel efficiency and crashworthiness.
- Aerospace Industry: The aerospace industry demands materials that are strong, lightweight, and resistant to harsh environments. Dual-phase alloy powders are increasingly being used to manufacture components like aircraft landing gear, structural elements, and engine parts. Their ability to withstand high stresses and maintain integrity at extreme temperatures makes them a valuable asset in aerospace applications.
- Consumer Goods: From durable sporting equipment like bicycle frames and golf clubs to intricate components in electronics and appliances, dual-phase alloy powders are making their mark in the consumer goods sector. Their combination of strength, formability, and corrosion resistance allows for the creation of high-performance and long-lasting products.
- Medical Devices: The medical field is constantly seeking materials that are biocompatible, strong, and lightweight for implants and surgical instruments. Dual-phase alloy powders are being explored for the development of orthopedic implants, surgical tools, and even dental prosthetics. Their potential to offer a balance between strength and workability makes them a promising option for these critical applications.
Applications of Dual-Phase Alloy Powders
Application | Benefit | Example |
---|---|---|
Automotive Industry | Lightweight, strong components for improved fuel efficiency and crashworthiness | Car body panels, suspension parts |
Aerospace Industry | Strong, lightweight materials for harsh environments | Aircraft landing gear, structural elements, engine parts |
Consumer Goods | Durable, formability for high-performance products | Bicycle frames, golf clubs, electronics components |
Medical Devices | Biocompatible, strong, lightweight for implants and instruments | Orthopedic implants, surgical tools, dental prosthetics |
A Multitude of Models: Unveiling the Top contenders
Now that we’ve explored the wonders of dual-phase alloy powders, let’s delve into the specific models that dominate the market. Here are 10 prominent contenders, each boasting unique characteristics:
- Fe-1.5Mo: This workhorse material offers a good balance of strength and ductility, making it a popular choice for automotive applications like car body panels and structural components. Compared to its peers, Fe-1.5Mo is known for its excellent cold-workability, allowing for easier shaping during manufacturing.
- Fe-2Cr-0.5Mo: This chromium-infused variant boasts enhanced corrosion resistance compared to Fe-1.5Mo. It’s particularly well-suited for applications where exposure to harsh environments is a concern, such as in some automotive underbody components or industrial equipment.
- Fe-3Cr-Mo: Taking the chromium content a step further, Fe-3Cr-Mo offers superior corrosion resistance, making it ideal for applications in marine environments or those involving exposure to chemicals. While its strength is comparable to Fe-1.5Mo, the higher chromium content can slightly reduce its formability.
- 17-4PH: This precipitation-hardening stainless steel powder stands out for its exceptional strength and good ductility. It’s often used in high-performance applications like aerospace components, demanding medical devices, and even sporting goods that require a combination of strength and formability. Here’s an interesting comparison: 17-4PH offers superior strength to Fe-based powders but might require more specific heat treatment processes to achieve its full potential.
- AM301: This alloy powder is a favorite in the laser additive manufacturing (LAM) space, known for its excellent printability and good mechanical properties. Compared to other options, AM301 offers a good balance between strength and ductility, making it suitable for a wide range of LAM applications, from automotive parts to medical implants.
- DX40: Another LAM-friendly option, DX40 boasts high strength and good toughness. It’s often used for applications where both high loads and impact resistance are crucial, such as in tooling components or parts for heavy machinery. While strong, DX40 might have slightly lower formability compared to Fe-based options.
- CM24: This chromium-molybdenum alloy powder is known for its exceptional creep resistance, making it ideal for high-temperature applications like heat exchangers or turbine components. Compared to other options, CM24 can withstand prolonged exposure to elevated temperatures without compromising its structural integrity.
- HDH: Designed specifically for high-density applications, HDH offers exceptional strength and wear resistance. It’s often used in components like gears, bearings, and wear plates that experience significant friction and stress. Here’s a key point to consider: HDH might have lower ductility compared to other options, making it less suitable for applications requiring extensive shaping.
- Custody® 420: This unique offering by Carpenter Additive powder program boasts high strength and excellent fatigue resistance. It’s particularly well-suited for applications like aerospace components and high-performance motorsports parts that experience repeated stress and strain cycles. Compared to traditional 420 stainless steel powders, Custody® 420 offers improved printability and performance through its optimized composition.
- AMSteel 290: This offering from ArcelorMittal stands out for its combination of high strength, good ductility, and excellent corrosion resistance. It’s designed for additive manufacturing applications in the automotive and industrial sectors, where components require a balance of these properties. Here’s an interesting fact: AMSteel 290 is relatively new to the market but has garnered attention for its potential to replace traditional manufacturing methods for complex, high-performance parts.
Key Considerations When Choosing Dual-Phase Alloy Powders
When selecting the ideal dual-phase alloy powder for your application, several key factors need consideration:
- Desired Properties: The most crucial step is identifying the essential properties for your application. Do you prioritize strength, ductility, corrosion resistance, or a specific combination?
- Formability Requirements: Consider the level of shaping and forming your component will undergo during manufacturing. Some powders offer better cold-workability compared to others.
- Processing Method: The chosen powder should be compatible with your intended processing method, such as laser additive manufacturing or traditional powder metallurgy techniques.
- Cost Considerations: Dual-phase alloy powders can vary in price depending on the specific composition and desired properties.
Specifications, Sizes, Grades, and Standards of Dual-Phase Alloy Powders
Property | Description | Example |
---|---|---|
Chemical Composition | The specific weight percentages of elements like iron, chromium, manganese, etc. | Fe-1.5Mo: Fe-1.5Mo, (C, Mn, Si) |
Particle Size Distribution | The range of particle sizes within the powder | D50 (median particle size) of 15-45 microns |
Apparent Density | The bulk density of the powder | 4.0 – 5.0 g/cm³ |
Flowability | The ease with which the powder flows | Measured by standardized tests like Hall flowmeter |
Grade | Can indicate specific properties or certifications | AM301 (for additive manufacturing) |
Standards | Compliance with industry standards like ASTM or ISO | ASTM F3049 (Standard Specification for Additive Manufacturing Powders) |
Pricing of Dual-Phase Alloy Powders
Pricing for dual-phase alloy powders can vary depending on several factors, including:
- Specific powder composition: More complex alloys with higher alloying elements might command a premium.
- Particle size and distribution: Powders with tighter particle size control might be more expensive.
- Quantity: Bulk purchases often come with discounted pricing compared to smaller quantities.
- Manufacturer and distributor: Prices can vary between different suppliers.
It’s important to note that specific pricing information is typically not publicly available and is often obtained through direct quotes from manufacturers or distributors.
Pros and Cons: Weighing the Benefits and Limitations
Dual-phase alloy powders offer a compelling combination of advantages, but it’s crucial to acknowledge their limitations as well.
Advantages of Dual-Phase Alloy Powders
- High Strength and Ductility: This unique combination allows for the creation of lightweight yet robust components.
- Improved Workability: Compared to high-strength steels, these powders offer better cold-workability, facilitating shaping processes.
- Tailorable Properties: By adjusting composition and processing, manufacturers can fine-tune the final properties for specific applications.
- Design Flexibility: Additive manufacturing allows for the creation of complex geometries with these powders.
Disadvantages of Dual-Phase Alloy Powders
- Cost: Dual-phase alloy powders can be more expensive compared to some traditional steels.
- Processing Requirements: These powders might require specific processing techniques or equipment, adding complexity to manufacturing.
- Limited Availability: Compared to some widely used metal powders, certain dual-phase alloy variants might have lower availability.
Comparison of Dual-Phase Alloy Powders
Feature | Fe-1.5Mo | Fe-2Cr-0.5Mo | Fe-3Cr-Mo | 17-4PH | AM301 | DX40 | CM24 | HDH | Custody® 420 | AMSteel 290 |
---|---|---|---|---|---|---|---|---|---|---|
Primary Benefit | Balance of strength & ductility | Enhanced corrosion resistance | Superior corrosion resistance | Exceptional strength & ductility | Excellent printability & good mechanical properties | High strength & good toughness | Exceptional creep resistance | High strength & wear resistance | High strength & fatigue resistance | High strength, good ductility & corrosion resistance |
Strength | High | High | High | Very High | High | Very High | High | Very High | Very High | High |
Ductility | Good | Good | Fair | Good | Good | Fair | Low | Low | Good | Good |
Formability | Excellent | Excellent | Good | Fair | Excellent | Fair | N/A | N/A | Good | Good |
Corrosion Resistance | Moderate | Good | Excellent | Moderate | Moderate | Moderate | Low | Low | Moderate | Good |
Processing Method | LAM, PM | LAM, PM | LAM, PM | LAM, PM | LAM | LAM | LAM | LAM | LAM | LAM |
Typical Applications | Car body panels, structural components | Underbody components, industrial equipment | Marine components, chemical processing equipment | Aerospace parts, medical devices, sporting goods | Automotive parts, medical implants | Tooling components, heavy machinery parts | Heat exchangers, turbine components | Gears, bearings, wear plates | Aerospace components, motorsports parts | Automotive, industrial components |
Please note: This table provides a general comparison, and specific properties can vary depending on the manufacturer and processing parameters.
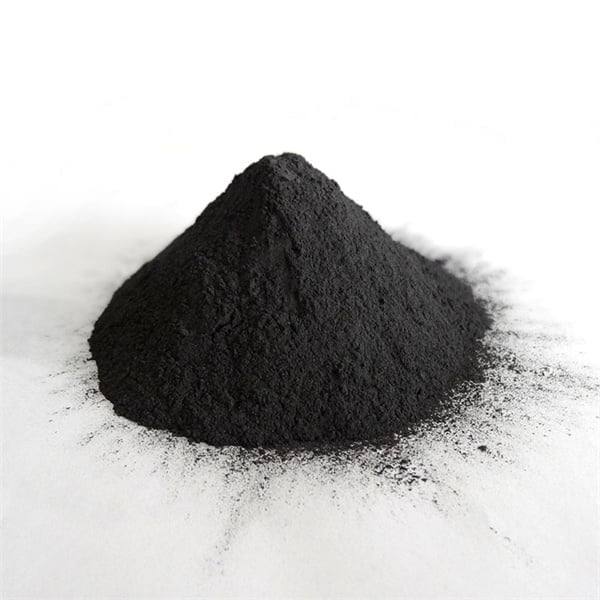
FAQ
Here are some commonly asked questions regarding dual-phase alloy powders, answered in an informative and engaging way:
Q: Are dual-phase alloy powders environmentally friendly?
While the environmental impact depends on the specific manufacturing processes involved, dual-phase alloy powders offer some potential benefits. Compared to traditional metal production methods that might generate more waste or require higher energy consumption, these powders can potentially lead to more efficient material utilization. Additionally, the ability to create lightweight components with dual-phase alloys can contribute to reduced fuel consumption in applications like the automotive industry.
Q: How does the surface finish of dual-phase alloy powders impact the final product?
The surface finish of the powder particles can influence several aspects of the final product. Powders with a smoother surface finish can generally flow more easily during processing, leading to improved printability or consistency in powder metallurgy techniques. Additionally, a smoother surface might minimize internal defects within the final component. However, a slightly rougher surface finish can sometimes enhance bonding between particles, potentially leading to increased strength in the final product. Manufacturers typically choose powders with a surface finish optimized for their specific processing method and desired final properties.
Q: What are the future trends for dual-phase alloy powders?
The future of dual-phase alloy powders appears bright! Ongoing research and development efforts are focused on creating new compositions with even better combinations of strength, ductility, and other desired properties. Additionally, advancements in additive manufacturing technology are expected to unlock the full potential of these powders for creating complex, high-performance components in various industries. Expect to see wider adoption of dual-phase alloy powders in sectors like aerospace, automotive, and even medical device manufacturing as the technology matures and production costs become more competitive.
Q: Where can I find more information about specific dual-phase alloy powders?
Several resources can provide you with detailed information about specific dual-phase alloy powders. Here are a few suggestions:
- Metal powder manufacturers’ websites: Leading manufacturers like Carpenter Additive, ArcelorMittal, and Höganäs often offer comprehensive information about their dual-phase alloy powder offerings, including product specifications, technical data sheets, and application case studies.
- Industry publications and research papers: Technical journals and publications focused on additive manufacturing or powder metallurgy might feature articles discussing the latest advancements and research findings related to dual-phase alloy powders.
- Professional societies and organizations: Organizations like the American Society for Materials Testing (ASTM) or the Additive Manufacturing Users Group (AMUG) can provide valuable resources and insights into the world of dual-phase alloy powders.
By delving into these resources, you can gain a deeper understanding of the specific properties, processing requirements, and potential applications of various dual-phase alloy powder options.
Share On
MET3DP Technology Co., LTD is a leading provider of additive manufacturing solutions headquartered in Qingdao, China. Our company specializes in 3D printing equipment and high-performance metal powders for industrial applications.
Inquiry to get best price and customized Solution for your business!
Related Articles
About Met3DP
Recent Update
Our Product
CONTACT US
Any questions? Send us message now! We’ll serve your request with a whole team after receiving your message.
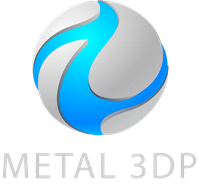
Metal Powders for 3D Printing and Additive Manufacturing