The Application of EBM Technology in Medical Devices
Table of Contents
Imagine a world where medical devices are no longer one-size-fits-all, but meticulously crafted to perfectly match the unique needs of each patient. This vision is rapidly becoming reality thanks to Electron Beam Melting (EBM) technology, a revolutionary additive manufacturing process shaking the foundations of the medical device industry.
EBM utilizes a highly focused electron beam to meticulously melt layers of metal powder, building complex three-dimensional objects layer by layer. This high-precision technique allows for the creation of intricate medical devices with superior mechanical properties, biocompatibility, and unmatched customization possibilities.
The Building Blocks of EBM Medical Devices
The foundation of any EBM-produced medical device lies in the metallic powder used. Just like artists wielding different paints create distinct masterpieces, the specific metal powder employed in EBM significantly influences the final device’s characteristics. Here’s a closer look at ten prominent metal powders shaping the future of medical devices:
Metal Powder | Composition | Properties | Applications in Medical Devices |
---|---|---|---|
Ti6Al4V ELI | 90% Titanium, 6% Aluminum, 4% Vanadium | Excellent strength-to-weight ratio, biocompatible, corrosion resistant | Artificial joints, knee and hip replacements, dental implants, cranial implants |
CoCrMo Alloy | 60% Cobalt, 20% Chromium, 10% Molybdenum | High wear resistance, good biocompatibility | Hip and knee replacements, dental implants |
Tantalum | 100% Tantalum | Excellent biocompatibility, radiolucent (invisible on X-rays), corrosion resistant | Cranial implants, facial reconstruction plates, dental implants |
Stainless Steel 316L | 66% Iron, 16-18% Chromium, 10-13% Nickel, 2% Molybdenum | Affordable, good corrosion resistance | Surgical instruments, bone screws, dental implants (limited use due to lower biocompatibility compared to other options) |
Nickel-Titanium (NiTi) | 55% Nickel, 45% Titanium | Shape memory effect, superelasticity | Orthodontic wires, stents (expandable tubes used to open blocked vessels) |
Inconel 625 | 61% Nickel, 21% Chromium, 9% Iron | High strength, excellent corrosion resistance | Surgical instruments, implants for harsh environments |
Molybdenum | 100% Molybdenum | Biocompatible, high melting point | Radiation shielding for medical devices used in cancer treatment |
Copper | 100% Copper | Antimicrobial properties, good thermal conductivity | Antibacterial coatings for medical devices, heat sinks for implantable electronics |
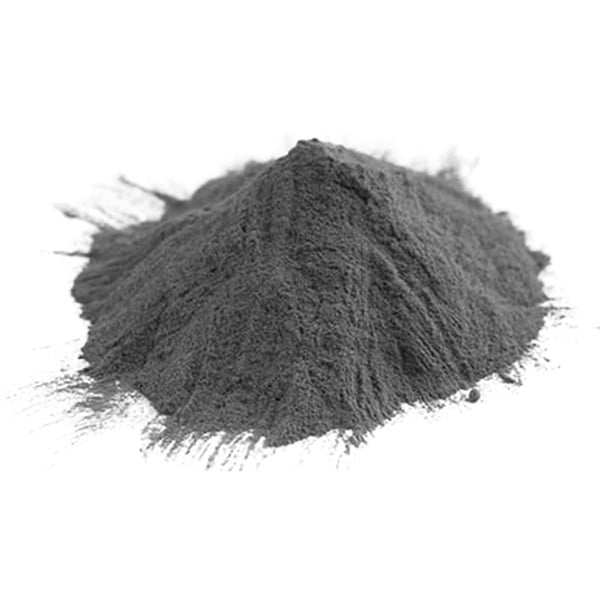
Beyond the Basics: Unveiling Additional Considerations
This table provides a snapshot of some popular metal powders, but the selection process goes beyond just composition. Particle size, surface area, and flowability all play a crucial role in achieving optimal EBM printing results. For instance, finer powders with a larger surface area can lead to improved inter-layer bonding, resulting in stronger and more durable medical devices.
The choice of metal powder ultimately hinges on the specific application and desired properties of the final device. For instance, when creating artificial joints requiring exceptional strength and biocompatibility, Ti6Al4V ELI shines. Alternatively, for implants exposed to harsh bodily fluids, tantalum’s superior corrosion resistance makes it an ideal candidate.
Why EBM Reigns Supreme in Medical Device Manufacturing
The transformative power of EBM in medical device manufacturing extends far beyond the versatility offered by a diverse range of metal powders. Here’s a deeper dive into the key advantages propelling EBM to the forefront of the industry:
Unmatched Customization: EBM’s digital nature allows for the creation of highly complex geometries, enabling the production of patient-specific implants that perfectly match individual anatomies. This level of customization can significantly improve implant fit, leading to faster healing times, reduced pain, and improved long-term patient outcomes.
Superior Mechanical Properties: The high-energy electron beam in EBM creates a near-net-shape manufacturing process, resulting in parts with excellent mechanical properties like strength, fatigue resistance, and osseointegration (the ability to bond with bone). This translates to more durable and longer-lasting medical devices.
Enhanced Porous Structures: EBM allows for the creation of intricate lattice structures within implants. These porous designs mimic the natural structure of bone, promoting bone ingrowth and osseointegration, ultimately leading to better implant stability and fixation.
Biocompatible Marvels: Many of the metal powders used in EBM are biocompatible, meaning they are well-tolerated by the human body and minimize the risk of rejection. This While the advantages of EBM are undeniable, navigating the diverse landscape of metal powders can be a complex task. Let’s delve deeper into a comparative analysis of some key metal powders, highlighting their strengths, weaknesses, and ideal applications:
Head-to-Head: Ti6Al4V ELI vs. CoCrMo Alloy
Ti6Al4V ELI: This workhorse material reigns supreme in EBM due to its exceptional:
- Strength-to-weight ratio: Ideal for weight-bearing applications like artificial joints.
- Biocompatibility: Minimizes the risk of rejection by the body.
- Corrosion resistance: Ensures long-term implant performance.
However, Ti6Al4V ELI comes at a premium compared to some alternatives. Additionally, its slightly lower wear resistance necessitates careful consideration for applications like high-friction areas in knee replacements.
CoCrMo Alloy: A strong contender, CoCrMo offers:
- High wear resistance: Excellent for applications experiencing significant friction.
- Cost-effectiveness: A more affordable option compared to Ti6Al4V ELI.
However, concerns linger regarding potential long-term health effects associated with trace metal ions released from the alloy. Additionally, CoCrMo exhibits lower biocompatibility compared to Ti6Al4V ELI.
The Verdict: For applications demanding exceptional strength, biocompatibility, and weight reduction, Ti6Al4V ELI remains the gold standard. However, CoCrMo emerges as a viable alternative in cost-sensitive scenarios or for applications where wear resistance is paramount.
Tantalum vs. Stainless Steel 316L
Tantalum: This precious metal boasts:
- Unparalleled biocompatibility: Minimizes the risk of rejection, making it ideal for sensitive applications like cranial implants.
- Radiolucency: Invisible on X-rays, facilitating post-operative imaging.
However, tantalum’s high cost can be a limiting factor.
Stainless Steel 316L: An affordable option offering:
- Good corrosion resistance: Suitable for various medical devices.
The major drawback of Stainless Steel 316L lies in its lower biocompatibility compared to tantalum and Ti6Al4V ELI. This characteristic makes it less suitable for long-term implants or applications in close contact with bone.
The Verdict: For applications requiring exceptional biocompatibility and radiolucency, tantalum reigns supreme. However, for cost-conscious scenarios or applications where biocompatibility is less critical, Stainless Steel 316L presents a viable alternative.
Exploring the Potential of NiTi and Inconel 625
NiTi (Nickel-Titanium): This unique material exhibits:
- Shape memory effect: Allows implants to return to their original shape after deformation.
- Superelasticity: Enables implants to absorb significant stress without permanent deformation.
These properties make NiTi ideal for applications like self-expanding stents. However, NiTi poses challenges in EBM processing due to its high reactivity.
Inconel 625: This high-performance alloy offers:
- Exceptional strength and corrosion resistance: Suitable for demanding applications or harsh environments.
However, Inconel 625’s biocompatibility is lower compared to Ti6Al4V ELI, limiting its use in some medical devices.
The Verdict: NiTi holds immense potential for innovative medical devices with unique functionalities. Inconel 625 is a compelling option for instruments requiring superior strength and corrosion resistance in non-implant applications.
A Guide to Selecting the Right Metal Powder
The selection of the optimal metal powder for EBM hinges on a careful consideration of several factors:
- Application requirements: Consider the specific properties needed for the device, such as strength, wear resistance, biocompatibility, and weight.
- Patient anatomy: For customized implants, the metal powder should be compatible with the patient’s specific needs.
- Regulatory considerations: Ensure the chosen metal powder meets relevant medical device standards and regulations.
- Cost-effectiveness: Balance the desired properties with budgetary constraints.
By carefully evaluating these factors, medical device manufacturers can leverage EBM technology to create innovative and personalized solutions that revolutionize patient care.
Applications of EBM Technology in Medical Devices
EBM’s ability to create intricate, biocompatible, and high-performance devices has opened a new chapter in medical device manufacturing. Let’s explore some of the most promising applications of EBM technology across various medical specialties:
EBM Revolutionizing Orthopedics:
- Artificial Joints: EBM-produced knee and hip replacements made from Ti6Al4V ELI offer exceptional strength, durability, and biocompatibility, leading to improved patient outcomes and longer implant lifespans. The ability to create porous structures further enhances osseointegration, promoting bone ingrowth and implant stability.
- Custom Implants: EBM excels at producing patient-specific implants that perfectly match individual bone anatomy. This customization can significantly improve implant fit and function, reducing pain, and accelerating recovery times. For instance, EBM-made cranial implants can be meticulously designed to match a patient’s skull defect, leading to superior cosmetic outcomes.
- Spinal Implants: EBM technology enables the creation of complex spinal implants with intricate lattice structures that promote bone fusion and provide optimal support for the spine.
EBM Shaping the Future of Dentistry:
- Dental Implants: EBM-produced dental implants made from Ti6Al4V ELI offer superior biocompatibility and osseointegration, creating a strong foundation for dental crowns and bridges. The ability to customize implant dimensions ensures a perfect fit within the patient’s jawbone.
- Orthodontic Devices: EBM allows for the creation of customized orthodontic wires and brackets with intricate features, potentially leading to more efficient and comfortable orthodontic treatments.
Beyond Bones and Teeth: EBM’s Expanding Horizons
- Maxillofacial Reconstruction: EBM’s ability to create patient-specific implants with complex geometries makes it ideal for reconstructing facial bones following injury or surgery. This technology can restore both functionality and aesthetics, significantly improving patient quality of life.
- Medical Instrumentation: EBM-produced surgical instruments can be crafted from high-strength and corrosion-resistant materials like Inconel 625, ensuring exceptional durability and performance in demanding surgical environments.
- Radiotherapy Devices: EBM’s ability to create intricate shapes with minimal internal stress makes it suitable for manufacturing components used in radiotherapy equipment for cancer treatment.
Embracing the Future: The Potential of EBM in Medical Devices
EBM technology is rapidly transforming the medical device landscape, paving the way for a future of:
- Personalized Medicine: The ability to create patient-specific devices based on individual needs will revolutionize patient care.
- Enhanced Functionality: EBM-produced devices with intricate features and biocompatible materials will offer improved performance and long-term durability.
- Reduced Healthcare Costs: The potential for EBM to create longer-lasting implants and minimize revision surgeries can lead to significant cost savings in the healthcare system.
As EBM technology continues to evolve and become more cost-effective, its applications in medical devices are poised to expand exponentially. This innovative technology holds immense promise for shaping a future of improved patient outcomes and a transformed healthcare landscape.
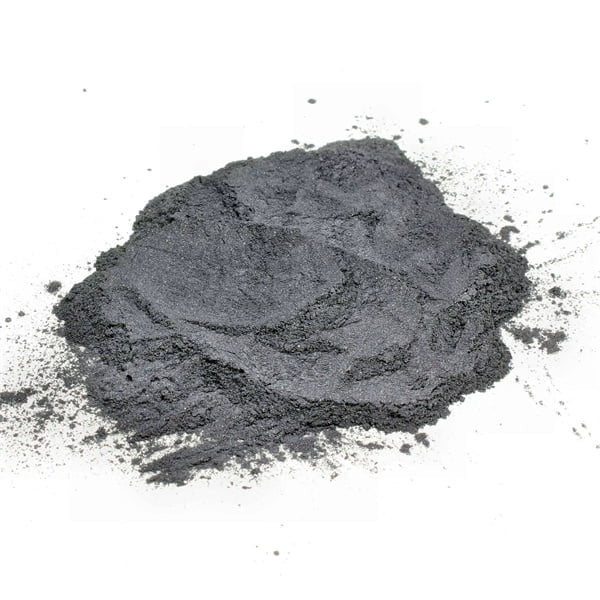
FAQ
Q: Is EBM technology safe for use in medical devices?
A: Yes, many of the metal powders used in EBM are biocompatible and well-tolerated by the human body. However, the biocompatibility of the final device depends on the specific metal powder chosen.
Q: What are the limitations of EBM technology in medical devices?
A: Current limitations include the high cost of some metal powders and EBM equipment. Additionally, certain metal powders can be challenging to process using EBM.
Q: How does EBM compare to traditional manufacturing methods for medical devices?
A: EBM offers several advantages, including the ability to create complex geometries, unmatched customization possibilities, and the production of devices with superior mechanical properties and biocompatibility. However, traditional methods may be more cost-effective for simpler devices.
Q: What is the future outlook for EBM technology in medical devices?
A: The future of EBM in medical devices is bright. As the technology becomes more affordable and accessible, we can expect to see a wider range of innovative and personalized medical devices created using EBM.
Share On
MET3DP Technology Co., LTD is a leading provider of additive manufacturing solutions headquartered in Qingdao, China. Our company specializes in 3D printing equipment and high-performance metal powders for industrial applications.
Inquiry to get best price and customized Solution for your business!
Related Articles
About Met3DP
Recent Update
Our Product
CONTACT US
Any questions? Send us message now! We’ll serve your request with a whole team after receiving your message.
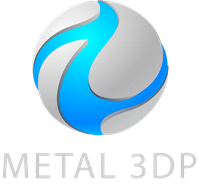
Metal Powders for 3D Printing and Additive Manufacturing