3D Printed Aluminum Electrical Enclosures
Table of Contents
Introduction: The Critical Role of Advanced Electrical Enclosures in Modern Industry
In today’s technologically advanced world, sensitive electronic components are the lifeblood of countless operations, from critical aerospace systems and complex automotive controls to life-saving medical devices and sophisticated industrial automation. Protecting these vital components from environmental hazards, electromagnetic interference (EMI), physical impact, and thermal stress is paramount. This is the fundamental role of an electrical enclosure: to provide a secure, controlled environment ensuring the reliability, longevity, and safety of the electronics within.
Traditionally, manufacturing these enclosures involved methods like sheet metal fabrication, CNC machining from billet, or die casting. While effective, these processes often come with significant limitations, particularly when dealing with demands for:
- Complex Geometries: Integrating unique mounting points, intricate cooling features, or form-fitting shapes can be difficult or expensive.
- Rapid Prototyping & Iteration: Creating custom tooling for prototypes or making design changes incurs substantial costs and lead times.
- Low-to-Medium Volume Production: Tooling amortization makes small batch production economically challenging.
- Weight Optimization: Traditional methods may struggle to efficiently remove material only where it’s not needed, crucial for weight-sensitive applications.
Enter Metal Additive Manufacturing (AM), commonly known as metal 3D printing. This transformative technology builds parts layer by layer directly from digital designs, offering unprecedented freedom and efficiency. For electrical enclosures, metal AM, particularly using advanced aluminum alloys like AlSi10Mg and A6061, presents a paradigm shift. It allows engineers and procurement managers to overcome the limitations of traditional methods, enabling the creation of highly customized, performance-optimized, and lightweight custom electrical enclosure solutions faster and often more cost-effectively, especially for complex or low-volume requirements.
Aluminum alloys are particularly well-suited due to their inherent properties: excellent strength-to-weight ratio, superior thermal conductivity for heat dissipation, and natural corrosion resistance. By leveraging metal 3D printing, these benefits can be harnessed to create enclosures with features previously unattainable.
At Metal3DP, we stand at the forefront of this manufacturing revolution. As a leading provider of additive manufacturing solutions headquartered in Qingdao, China, we specialize in both state-of-the-art metal 3D printing equipment and the high-performance metal powders essential for producing robust, industrial-grade components. Our expertise empowers businesses across aerospace, automotive, medical, and industrial sectors to leverage AM for demanding applications like electrical enclosures, ensuring optimal protection and performance. For B2B clients seeking reliable industrial enclosure solutions or B2B enclosure supply partners, understanding the capabilities of AM is the first step towards unlocking significant competitive advantages.

What Are 3D Printed Aluminum Electrical Enclosures Used For? Applications Across Demanding Sectors
The versatility and performance benefits of 3D printed aluminum electrical enclosures make them ideal for a wide array of demanding applications where standard off-the-shelf solutions fall short. The ability to customize size, shape, mounting features, and integrate thermal management elements allows engineers to design enclosures perfectly tailored to specific requirements. Key sectors benefiting from this technology include:
- Aerospace & Defense:
- Applications: Housings for avionics, control system modules, communication equipment, sensor arrays, power distribution units.
- Why AM Aluminum? Extreme weight sensitivity makes aluminum’s low density crucial. AM enables topology optimization for further weight reduction without compromising structural integrity. Complex, space-saving geometries are often required to fit within tight aircraft or satellite constraints. Need for high reliability in harsh environments (vibration, temperature fluctuations).
- Keywords: Aerospace electronics housing, custom avionics enclosure, lightweight satellite components, defense system casing, Mil-spec enclosure solutions. Procurement managers in this sector often seek specialized aerospace enclosure suppliers capable of meeting stringent quality and material certifications.
- Automotive:
- Applications: Housings for Electronic Control Units (ECUs), Battery Management Systems (BMS), inverter casings, sensor clusters, custom connector housings, prototype enclosures for testing.
- Why AM Aluminum? Need for good thermal conductivity to dissipate heat from power electronics. Weight reduction contributes to fuel efficiency and vehicle dynamics. Ability to rapidly prototype and iterate designs for new vehicle platforms. Potential for part consolidation, integrating mounting brackets or cooling channels directly into the automotive ECU enclosure.
- Keywords: Automotive enclosure manufacturer, custom ECU housing, EV battery enclosure, thermal management automotive, rapid prototyping automotive parts.
- Medical:
- Applications: Casings for diagnostic equipment (ultrasound, imaging systems), housings for surgical tools and robotics, enclosures for monitoring devices, customized housings for implantable device programmers or controllers.
- Why AM Aluminum? Biocompatibility potential (depending on alloy and finish), need for high precision and complex internal features. Ability to create ergonomic and patient-specific designs. Good EMI shielding properties for sensitive diagnostic equipment. Requirement for sterilization compatibility (achievable with appropriate post-processing like anodizing).
- Keywords: Medical device casing supplier, custom diagnostic equipment housing, surgical robot components, biocompatible enclosure materials, ISO 13485 manufacturing. Sourcing medical device enclosure solutions often requires partners with specific industry expertise and quality systems.
- Industrial Manufacturing & Automation:
- Applications: Custom control panel boxes, junction boxes in harsh environments, housings for robotic arm controllers, protective casings for sensors and actuators on production lines, specialized NEMA or IP-rated enclosures.
- Why AM Aluminum? Need for robust protection against dust, moisture, vibration, and impact (achieving specific IP rated enclosure standards). Customization to fit specific machinery or integration needs. Good thermal management for densely packed control panels. Corrosion resistance for challenging factory environments.
- Keywords: Industrial control panel box, custom junction box manufacturer, automation equipment housing, harsh environment enclosure, custom NEMA enclosure, wholesale enclosure supplier for industrial applications.
Key Functions Enabled by 3D Printed Aluminum Enclosures:
Function | Benefit of 3D Printed Aluminum | Target Keywords |
---|---|---|
EMI/RFI Shielding | Aluminum’s inherent conductivity provides good shielding. AM allows optimizing wall thickness and geometry for specific frequency ranges. Gasket grooves can be integrated. | EMI shielding enclosure, RFI protected housing |
Environmental Protection | Design freedom enables integrated seals, overlapping joints, and specific features to meet NEMA or IP ratings (e.g., IP65, IP67). | IP67 enclosure manufacturer, NEMA 4X enclosure |
Thermal Management | High thermal conductivity of aluminum combined with AM allows for integrated heat sinks, cooling fins, liquid cooling channels, or optimized airflow paths directly into the enclosure body. | Thermal management enclosure, integrated heat sink |
Structural Support & Impact Resistance | Aluminum alloys offer good strength-to-weight. AM enables topology optimization and internal lattice structures for enhanced rigidity and impact absorption where needed. | High-strength enclosure, impact resistant casing |
Component Mounting & Integration | Custom bosses, standoffs, snap-fits, cable routing channels, and connector integration features can be designed directly into the part, simplifying assembly. | Custom mounting enclosure, integrated features |
Export to Sheets
Procurement managers and engineers looking for wholesale enclosure suppliers or manufacturers capable of delivering highly customized solutions find that metal AM providers like Metal3DP offer capabilities far beyond traditional off-the-shelf distributors.
Why Use Metal 3D Printing for Electrical Enclosures? Unlocking Design Freedom and Performance Advantages
While traditional manufacturing methods have served well, metal additive manufacturing offers compelling advantages, particularly when performance, customization, or speed are critical. Comparing AM to conventional processes highlights why metal 3D printing is becoming the preferred choice for many advanced electrical enclosure applications.
Comparison: Metal AM vs. Traditional Methods for Electrical Enclosures
Feature | Metal Additive Manufacturing (e.g., PBF) | Traditional Methods (CNC Machining, Sheet Metal, Casting) | Key B2B Advantage |
---|---|---|---|
Design Freedom | Extremely high; complex geometries, internal channels, organic shapes, topology optimization, integrated features easily achievable. | Limited by tooling constraints, machining access, sheet bend radii, draft angles (casting). | Enables highly optimized, application-specific custom enclosure design. |
Tooling Costs | None; direct digital manufacturing. | High for casting molds, stamping dies; moderate for CNC fixtures. | Significant cost savings for low volume production enclosure & prototypes. |
Lead Time (Proto/Low Vol) | Very fast (days); enables rapid iteration. | Moderate to long (weeks/months) due to tooling creation or complex CNC programming. | Faster time-to-market, quicker design validation via rapid prototyping enclosure. |
Material Waste | Low; uses only necessary material (plus supports). | High for subtractive (CNC); moderate for casting/sheet metal (offcuts). | More sustainable manufacturing, potential material cost savings on expensive alloys. |
Part Consolidation | High potential; multiple components can be printed as a single unit. | Limited; often requires assembly of multiple parts (brackets, heat sinks, etc.). | Reduced assembly time/cost, fewer potential failure points, simplified supply chain. |
Customization | High; economical for unique parts or small batches with variations. | Costly; requires tooling modification or significant reprogramming for variations. | Efficient production of bespoke or highly varied custom enclosure manufacturing. |
Weight Reduction | Excellent; topology optimization and lattice structures readily implemented. | Possible but often less efficient or more complex to achieve compared to AM. | Critical for lightweight enclosure solutions in aerospace, automotive, portable devices. |
Export to Sheets
Key Advantages Summarized:
- Unmatched Design Complexity: Create enclosures with integrated cooling channels, conformal shielding, organically shaped mounts, and intricate internal structures impossible or prohibitively expensive with other methods. Leverage topology optimization enclosure techniques to place material only where structurally necessary.
- Accelerated Development Cycles: Go from digital design to physical prototype in days, not weeks or months. This allows engineering teams to test, refine, and validate rapid prototyping enclosure designs much faster, reducing overall project timelines and costs.
- Economical Customization & Low Volumes: Produce unique or small batches of enclosures without the financial burden of tooling. This is ideal for specialized equipment, replacement parts for legacy systems, or niche market products. AM provides significant procurement advantages for non-standard requirements.
- Enhanced Performance: Integrate features like high-surface-area heat sinks directly into the enclosure wall for superior thermal management. Optimize for structural rigidity or impact resistance using advanced design techniques like lattice structures.
- Supply Chain Flexibility & On-Demand Production: Manufacture enclosures when and where needed, reducing inventory holding costs and mitigating risks associated with traditional supply chains. Embrace digital manufacturing principles with a digital inventory of enclosure designs.
Choosing metal AM benefits procurement managers and engineers by offering a powerful tool to overcome design constraints, accelerate innovation, and create superior industrial enclosure solutions. Companies like Metal3DP provide the expertise and capacity to realize these advantages effectively.
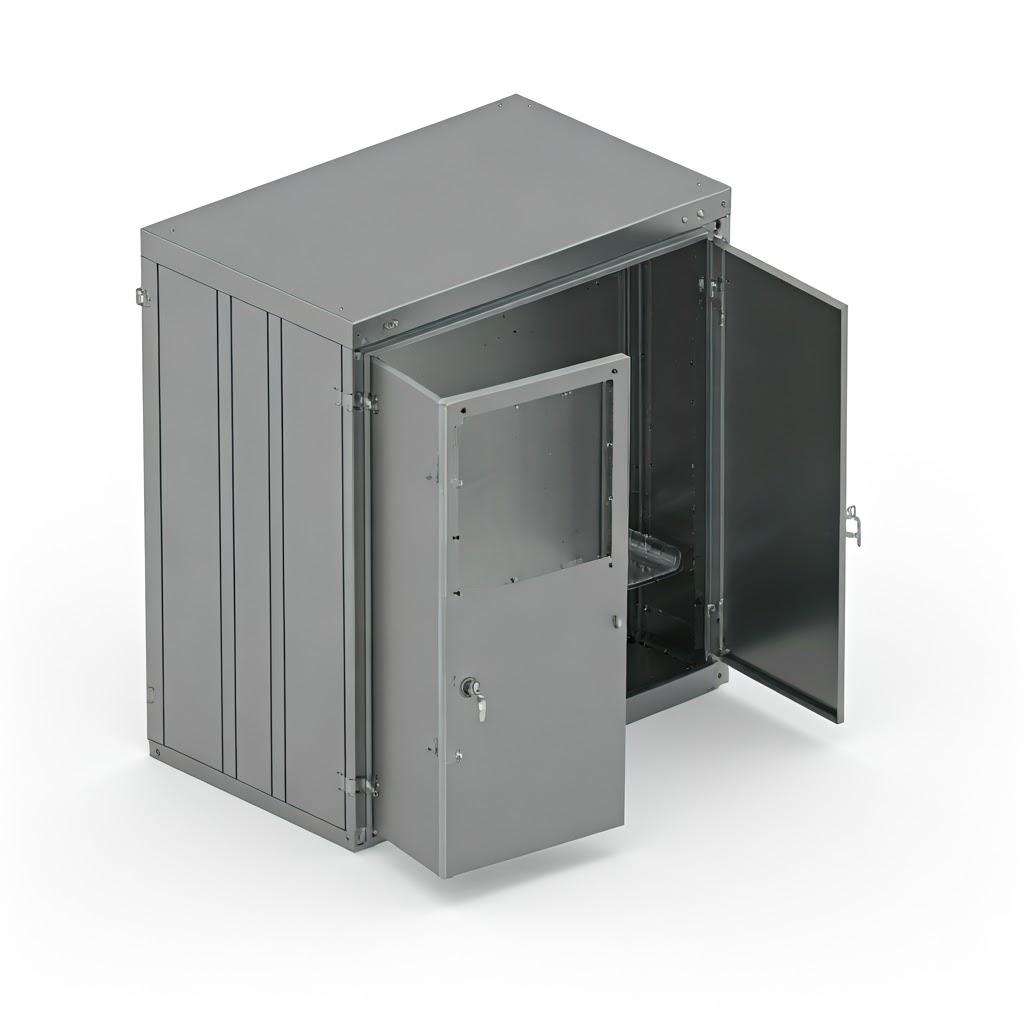
Recommended Aluminum Alloys (AlSi10Mg & A6061) and Why They Excel: Material Properties for Optimal Enclosure Performance
Selecting the right material is crucial for the success of any 3D printed electrical enclosure. Aluminum alloys are often favored for their balance of properties. Two of the most common and effective aluminum alloys used in Powder Bed Fusion (PBF) processes like Selective Laser Melting (SLM) or Direct Metal Laser Sintering (DMLS) are AlSi10Mg and A6061. Understanding their characteristics helps in choosing the best fit for a specific application.
AlSi10Mg:
This is arguably the most common aluminum alloy used in metal AM. It’s essentially a casting alloy adapted for additive manufacturing, known for its excellent printability and good all-around mechanical properties.
- Key Characteristics:
- Excellent Printability: Relatively easy to process with good dimensional accuracy and surface finish achievable. Less prone to cracking during printing compared to some other high-strength aluminum alloys.
- Good Strength & Hardness: Offers mechanical properties suitable for many structural enclosure applications after appropriate heat treatment.
- Good Thermal Conductivity: Facilitates heat dissipation from enclosed electronic components.
- Good Corrosion Resistance: Suitable for various operating environments.
- Ideal for Complex Geometries: Its fluidity during melting allows for intricate details and thin walls.
A6061:
A well-known wrought alloy widely used in traditional manufacturing, A6061 has been adapted for AM processes. It typically offers better ductility and fracture toughness compared to AlSi10Mg but can be more challenging to print reliably without cracking.
- Key Characteristics:
- Excellent Corrosion Resistance: Superior to AlSi10Mg in certain environments.
- Good Mechanical Properties: Offers a good balance of strength, ductility, and toughness, particularly after T6 heat treatment.
- Good Weldability: Relevant if post-print welding operations are required.
- Requires Careful Parameter Control: More susceptible to issues like solidification cracking during printing; requires optimized process parameters and potentially specific build strategies.
- Better Ductility/Toughness: May be preferred for applications experiencing higher impacts or requiring more deformation before fracture.
Material Property Comparison (Typical values after heat treatment):
Property | AlSi10Mg (Heat Treated) | A6061 (T6 Heat Treated) | Importance for Enclosures |
---|---|---|---|
Ultimate Tensile Strength (UTS) | ~330 – 430 MPa | ~290 – 310 MPa | Overall strength to resist deformation and protect contents. |
Yield Strength (YS) | ~230 – 300 MPa | ~240 – 275 MPa | Point at which permanent deformation begins; indicates load-bearing capacity. |
Elongation at Break | ~3 – 10% | ~8 – 15% | Ductility; ability to deform before fracturing. Higher value beneficial for impact resistance. |
Hardness | ~100 – 120 HB | ~90 – 100 HB | Resistance to scratching and surface indentation. |
Density | ~2.67 g/cm³ | ~2.70 g/cm³ | Low density contributes to lightweight designs (critical for aerospace/automotive). |
Thermal Conductivity | ~130 – 150 W/(m·K) | ~150 – 170 W/(m·K) | Ability to dissipate heat; crucial for thermal conductivity aluminum enclosures. |
Corrosion Resistance | Good | Excellent | Durability in various operating environments; essential for corrosion resistance enclosure. |
Printability | Excellent | Good (Requires more optimization) | Ease of manufacturing complex shapes reliably. |
Export to Sheets
Why These Properties Matter for Enclosures:
- Strength & Hardness: Ensure the enclosure can withstand potential impacts, vibrations, and the weight of internal components without deformation.
- Low Density: Critical for applications where weight is a primary concern (aerospace, automotive, portable devices), contributing to high-strength lightweight alloy solutions.
- Thermal Conductivity: Allows the enclosure itself to act as a heat sink, drawing heat away from sensitive electronics, vital for thermal management enclosure designs.
- Corrosion Resistance: Ensures longevity and reliability, especially in humid, industrial, or outdoor environments.
- Printability: Directly impacts the feasibility of producing complex designs, the achievable tolerances, and the overall cost and speed of manufacturing.
As a metal powder supplier, Metal3DP recognizes the critical importance of powder quality for successful additive manufacturing. We employ industry-leading gas atomization and Plasma Rotating Electrode Process (PREP) technologies to produce high-quality, spherical aluminum 3D printing powder, including alloys like AlSi10Mg. Our advanced powder-making systems ensure high sphericity, good flowability, controlled particle size distribution, and low oxygen content – all essential factors for achieving dense, reliable, high-performance 3D printed parts. Procurement managers sourcing materials or services should always verify the metal powder supplier specification and quality control processes. You can explore our range of advanced metal powders here. Choosing the right alloy, coupled with high-quality powder and optimized printing processes, is key to unlocking the full potential of AM for electrical enclosures.
Design Considerations for Additively Manufactured Electrical Enclosures: Optimizing for Printability, Functionality, and Cost
One of the most significant advantages of metal additive manufacturing is the vast design freedom it offers. However, to fully leverage this potential and ensure successful, cost-effective production of electrical enclosures, designers must adopt Design for Additive Manufacturing (DfAM) principles. This involves considering the layer-by-layer build process, material properties, and post-processing requirements right from the initial design stage. Optimizing your enclosure design for AM can significantly impact printability, performance, lead time, and final cost. For businesses submitting an RFQ enclosure design, providing a DfAM-optimized model accelerates quoting and production.
Here are key DfAM considerations for 3D printed aluminum electrical enclosures using Powder Bed Fusion (PBF):
- Wall Thickness:
- Minimum Thickness: While PBF can produce very thin walls (down to ~0.4-0.5 mm), practical minimums for robust enclosures are typically higher (e.g., 1.0 – 1.5 mm) to ensure structural integrity, handleability, and proper sealing.
- Consistency: Aim for relatively uniform wall thicknesses to minimize thermal stress gradients during printing, reducing the risk of warping.
- Avoid Overly Thick Sections: Large solid volumes can accumulate thermal stress, increase print time/cost, and may require careful parameter adjustment to avoid internal defects. Consider hollowing thick sections or using internal lattice structures if high stiffness is needed without the mass.
- Keyword Focus: Wall thickness optimization, minimum feature size AM.
- Holes and Channels:
- Orientation: Vertically oriented holes generally achieve better roundness than horizontally printed holes, which can be slightly elliptical due to the layer-wise approximation. Small horizontal holes may not require support depending on their diameter and the printer’s capabilities.
- Self-Supporting Angles: Small horizontal holes or channels might be self-supporting up to a certain diameter (e.g., 6-8 mm). Larger horizontal openings will require support structures internally.
- Internal Channels: AM excels at creating complex internal cooling channels or cable routing paths. Ensure these channels are designed for powder removal (escape holes) and support removal if necessary.
- Keyword Focus: Designing holes for AM, internal cooling channels, self-supporting features.
- Overhangs and Support Structures:
- Critical Angle: Surfaces angled below a certain threshold relative to the build plate (typically around 45 degrees for aluminum PBF) will require support structures to prevent collapse during printing.
- Minimize Supports: Design strategically to reduce the need for supports. Orient the part effectively on the build plate. Use chamfers or fillets instead of sharp 90-degree overhangs where possible. Design self-supporting angles (>45 degrees).
- Support Accessibility: If supports are unavoidable, ensure they are accessible for easy removal during post-processing without damaging the part. Inaccessible internal supports can be impossible to remove.
- Impact on Surface: Support structures leave contact marks (“witness marks”) on the surface, resulting in higher roughness in those areas. Consider critical surfaces and orient the part to avoid supports on them if possible.
- Keyword Focus: Support structure reduction, self-supporting design AM, overhang angle metal printing.
- Integrated Features:
- Mounting Bosses & Standoffs: Design these directly into the enclosure body, eliminating the need for separate components and assembly steps. Ensure adequate thickness and consider adding fillets at the base for strength.
- Snap-Fits & Clips: Possible to design integrated fastening features, but requires careful consideration of aluminum’s flexibility and layer orientation for strength. Prototyping is key.
- Heat Sinks: AM allows for highly optimized heat sink design AM, including complex fin geometries (pin fins, wavy fins, lattice structures) with high surface area, integrated directly into the enclosure walls for superior thermal performance.
- Sealing Grooves: Design grooves for O-rings or EMI gaskets directly into mating surfaces for reliable sealing.
- Cable Routing & Connectors: Integrate channels, pass-throughs, and mounting features for specific connectors.
- Keyword Focus: Integrated features enclosure, part consolidation AM, custom mounting enclosure.
- Topology Optimization & Lightweighting:
- Utilize specialized software to perform topology optimization, removing material from non-critical areas while maintaining structural requirements. This is invaluable for creating lightweight enclosure solutions, especially in aerospace and automotive sectors where every gram counts. The result is often an organic-looking structure that is highly efficient.
- Keyword Focus: Topology optimization lightweighting, generative design AM.
- Assembly & Tolerances:
- Consider tolerances required for mating parts (lids, covers, internal components). Design clearances appropriately, knowing the typical tolerances of the AM process (see next section).
- Factor in potential warping or distortion, especially for large, flat surfaces. Adding reinforcing ribs can help maintain flatness.
- Design features that aid assembly, such as alignment pins or guides.
Metal3DP’s engineering team possesses deep expertise in DfAM and works closely with clients to optimize their enclosure designs for successful additive manufacturing, ensuring functionality, printability, and cost-effectiveness.
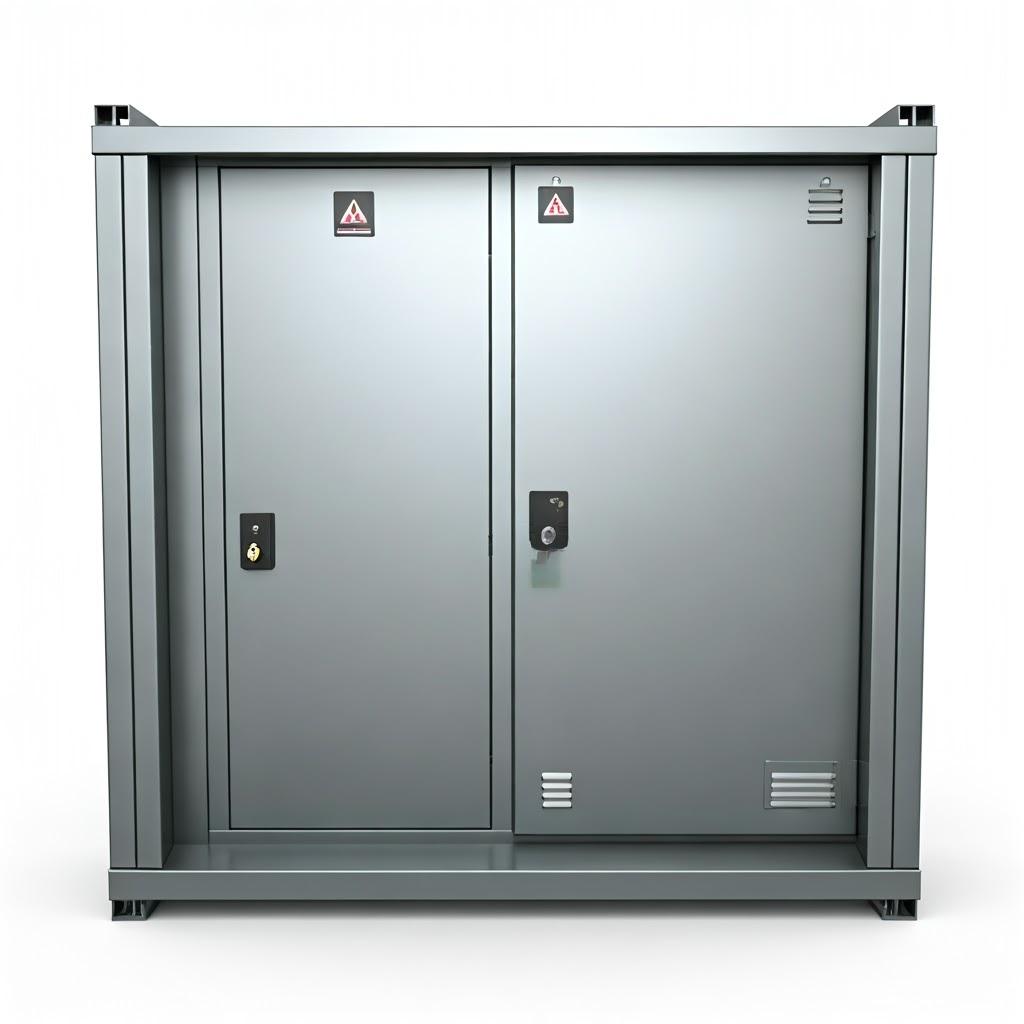
Achieving Precision: Tolerance, Surface Finish, and Dimensional Accuracy in 3D Printed Enclosures
While metal 3D printing offers incredible design freedom, it’s essential to understand the levels of precision achievable directly from the process. Factors like the specific PBF machine (SLM, DMLS), material (AlSi10Mg, A6061), part geometry, size, orientation, and support strategy all influence the final dimensional accuracy and surface finish. Managing expectations and designing accordingly, potentially incorporating post-machining steps, is key for successful precision enclosure manufacturing.
Typical Tolerances:
- General Tolerances: For aluminum PBF processes, typical achievable tolerances are often in the range of ±0.1 mm to ±0.2 mm for smaller features (e.g., up to 20-50 mm).
- Larger Dimensions: For larger dimensions, tolerances are often expressed as a percentage of the length, for example, ±0.1% to ±0.2% of the dimension. So, a 200 mm feature might have a tolerance of ±0.2 mm to ±0.4 mm.
- Factors Influencing Tolerance:
- Machine Calibration: Regular calibration is crucial for accuracy.
- Thermal Effects: Shrinkage and potential warping during the build and cool-down phases.
- Part Geometry & Orientation: Large flat surfaces may warp more easily; feature resolution depends on orientation relative to layers.
- Support Strategy: Supports can slightly affect the dimensions of the surfaces they touch.
Surface Finish (Roughness):
- As-Built Roughness: The surface finish of as-printed metal parts is generally rougher than machined surfaces. Typical values for Ra (average roughness) can range significantly:
- Vertical Walls: Often achieve the best finish, perhaps Ra 6-12 µm.
- Up-Facing Surfaces: Generally good finish, slightly rougher than vertical, maybe Ra 8-15 µm.
- Down-Facing (Supported) Surfaces: Typically the roughest due to support contact points, potentially Ra 15-25 µm or more.
- Curved/Angled Surfaces: Roughness varies depending on the angle and layer stepping effect.
- Improving Surface Finish: If a smoother finish is required for sealing, aesthetics, or function, post-processing steps like bead blasting, tumbling, or CNC machining are necessary.
Achieving Higher Precision:
- Post-Machining: For critical features requiring tight tolerances (e.g., sealing faces for IP ratings, bearing bores, precise mounting points, connector interfaces), post-machining enclosure features via CNC is standard practice. Key surfaces are designed with extra stock material (“machining allowance”) that is removed during machining to achieve the final required dimensions and surface finish (e.g., Ra 1.6 µm or better).
- Design for Machining: If post-machining is planned, ensure the design allows clear access for machining tools to reach the critical features.
Understanding Process Capabilities:
Different additive manufacturing technologies yield varying results. While this post focuses on PBF (like SLM/DMLS) common for aluminum enclosures, exploring various printing methods can provide broader context on achievable precision across the AM landscape. Metal3DP utilizes industry-leading PBF equipment designed for accuracy and reliability, but understanding the inherent capabilities and limitations is crucial for project planning.
Tolerance & Surface Finish Summary Table (Typical Aluminum PBF):
Parameter | Typical As-Built Value Range | Achievable with Post-Machining | Importance for Enclosures |
---|---|---|---|
Tolerance (Small Features) | ±0.1 mm to ±0.2 mm | ±0.01 mm to ±0.05 mm (or better) | Fit of components, lid alignment, connector positioning. |
Tolerance (Large Features) | ±0.1% to ±0.2% of dimension | As above (locally) | Overall enclosure dimensions, mating with other structures. |
Surface Roughness (Ra) | 6 µm (Vertical) – 25+ µm (Down-facing) | Ra 0.8 µm – 3.2 µm (or better) | Sealing effectiveness (IP/NEMA), aesthetics, friction. |
Export to Sheets
Effective quality control metal printing involves verifying these aspects through measurement (CMM, scanners) and surface profilometry, ensuring the final enclosure meets all specifications.
Essential Post-Processing for 3D Printed Aluminum Enclosures: Finishing Touches for Peak Performance
A metal 3D printed part, straight off the build plate, is rarely ready for its end-use application. This is especially true for functional components like electrical enclosures. A series of post-processing steps are typically required to remove supports, relieve stress, achieve the desired tolerances and surface finish, and enhance properties like corrosion resistance. Planning for these steps is crucial for budgeting and determining realistic lead times.
Common post-processing steps for 3D printed aluminum (AlSi10Mg, A6061) enclosures include:
- Stress Relief / Heat Treatment:
- Purpose: The rapid heating and cooling cycles inherent in PBF create internal stresses within the printed part. Heat treatment (annealing or specific aging cycles like T6 for A6061) relieves these stresses, preventing potential distortion later and stabilizing the material’s microstructure to achieve the desired final mechanical properties (strength, hardness, ductility).
- Process: Involves heating the part in a controlled furnace atmosphere to specific temperatures for a set duration, followed by controlled cooling.
- Necessity: Generally considered essential for functional aluminum AM parts to ensure dimensional stability and optimal performance.
- Keyword Focus: Heat treatment aluminum AM, residual stress relief.
- Part Removal & Cleaning:
- Purpose: Separating the printed enclosure(s) from the build plate (often done via wire EDM or sawing) and removing excess metal powder.
- Process: Manual brushing, compressed air blow-off, or automated powder handling systems. Important to remove powder from internal channels or complex features.
- Support Structure Removal:
- Purpose: Removing the temporary support structures required during printing.
- Process: Can involve manual breaking/cutting (for easily accessible supports) or CNC machining for more integrated or robust supports. Care must be taken to avoid damaging the part surface. Accessibility designed during DfAM is critical here.
- Keyword Focus: Support removal AM, post-processing challenges.
- Surface Finishing:
- Purpose: Improving surface texture, removing layer lines, deburring edges, preparing for coating, or achieving specific aesthetic/functional requirements.
- Methods:
- Bead Blasting / Sand Blasting: Creates a uniform, non-directional matte finish. Effective for cleaning and improving aesthetics. Different media (glass beads, aluminum oxide) yield different textures.
- Tumbling / Vibratory Finishing: Parts are placed in a machine with media that vibrates or tumbles, smoothing surfaces and rounding edges. Good for batch processing but less precise than machining.
- CNC Machining: Used to achieve tight tolerances on specific features (e.g., mating surfaces, sealing grooves, mounting holes) and create very smooth finishes (Ra < 1.6 µm). Essential for precision enclosure manufacturing.
- Manual Grinding/Polishing: For specific localized smoothing or achieving mirror finishes, though often labor-intensive.
- Keyword Focus: Surface finishing enclosure, bead blasting aluminum, CNC machining 3D prints.
- Coating & Surface Treatments:
- Purpose: Enhancing corrosion resistance, wear resistance, electrical properties, or aesthetics. Aluminum benefits greatly from surface treatments.
- Methods:
- Anodizing (Type II / Type III Hardcoat): An electrochemical process that creates a durable, corrosion-resistant, electrically insulating oxide layer on the aluminum surface. Type III (Hardcoat) offers superior wear resistance. Can also be dyed various colors (Type II). Excellent choice for anodizing aluminum enclosure.
- Powder Coating: Applying a thermosetting powder electrostatically, then curing it with heat to form a tough, durable, and aesthetic colored finish. Wide range of colors and textures available. Good option for powder coating aluminum.
- Chromate Conversion Coating (e.g., Alodine, Iridite): A chemical treatment providing good corrosion resistance and an excellent primer base for paint or adhesives. Often has a characteristic gold or clear finish.
- Electroless Nickel Plating: Provides excellent wear resistance, corrosion protection, and can enhance EMI shielding.
- Keyword Focus: Corrosion protection enclosure, surface treatment aluminum.
- Assembly:
- Purpose: Installing gaskets, fasteners (e.g., Heli-Coils in tapped holes), connectors, or other components into the finished enclosure.
- Consideration: Design features (alignment pins, indexed shapes) can simplify assembly. Access for tools should be considered in DfAM.
- Keyword Focus: Enclosure assembly services.
Choosing the right combination of post-processing steps depends entirely on the enclosure’s specific requirements. Discussing these needs early with your manufacturing partner, like Metal3DP, ensures they are factored into the overall production plan and quote.
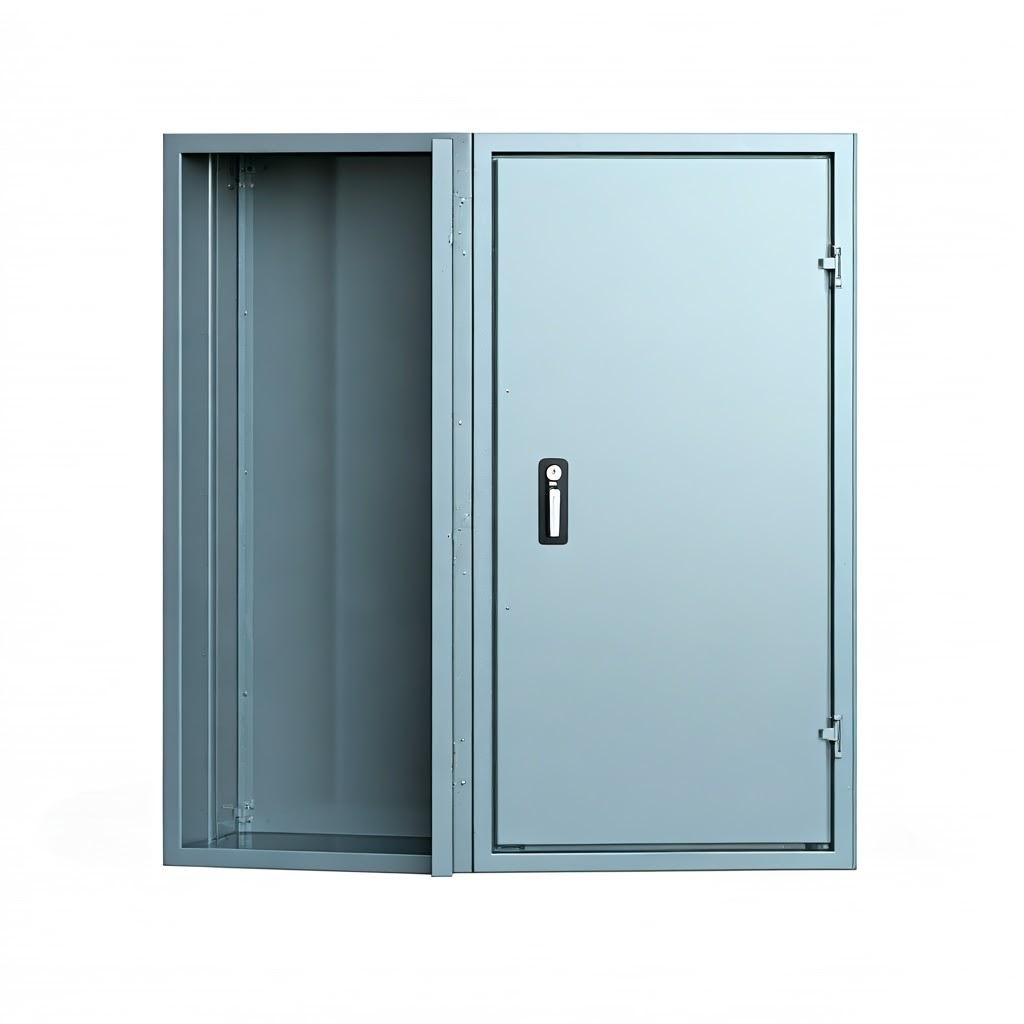
Common Challenges in 3D Printing Enclosures and Mitigation Strategies: Ensuring Quality and Reliability
While metal AM is a powerful technology, producing high-quality, reliable 3D printed aluminum enclosures requires expertise and careful process control to overcome potential challenges. Understanding these common issues and their mitigation strategies is crucial for both designers and procurement managers selecting a manufacturing partner.
- Warping and Distortion:
- Cause: Uneven heating and cooling leads to residual stress management issues, causing parts (especially large, flat ones like enclosure walls or lids) to deform or lift from the build plate.
- Mitigation:
- Optimized Orientation: Orienting the part to minimize large flat areas parallel to the build plate or reduce thermal gradients.
- Robust Support Structures: Using well-designed supports to anchor the part firmly to the build plate and counteract shrinkage forces.
- Process Parameter Optimization: Fine-tuning laser power, scan speed, and scan strategy.
- Stress Relief Heat Treatment: Essential post-processing step to relax internal stresses.
- Design Modifications: Adding temporary stiffening ribs (removed later) or slight design alterations to improve thermal stability.
- Keyword Focus: Warping metal 3D printing, residual stress control.
- Porosity:
- Cause: Small gas bubbles trapped during melting or incomplete fusion between powder particles, creating voids within the material. Porosity can reduce strength, fatigue life, and compromise sealing integrity.
- Mitigation:
- High-Quality Powder: Using powder with high sphericity, good flowability, controlled particle size distribution, and low trapped gas/moisture content. Metal3DP’s advanced atomization processes (Gas Atomization, PREP) are crucial for porosity control aluminum AM.
- Optimized Print Parameters: Ensuring sufficient energy density for complete melting and fusion without overheating (which can trap gas).
- Controlled Atmosphere: Maintaining a high-purity inert gas environment (Argon or Nitrogen) in the build chamber to minimize oxidation.
- Hot Isostatic Pressing (HIP): A post-processing step (high temperature and pressure) that can close internal pores (adds cost/time, usually reserved for highly critical parts).
- Keyword Focus: Porosity control aluminum AM, powder quality metal AM.
- Support Removal Difficulty & Surface Damage:
- Cause: Supports designed too densely, placed in inaccessible locations, or bonded too strongly to the part. Removal efforts can scratch, break, or deform the enclosure surface.
- Mitigation:
- DfAM Focus: Designing parts to minimize the need for supports and ensuring remaining supports are easily accessible.
- Optimized Support Parameters: Using appropriate support types (e.g., cone, block, lattice) and adjusting contact points/density for easier removal without sacrificing stability.
- Skilled Post-Processing: Careful manual removal or precise CNC machining of support structures.
- Keyword Focus: Support removal challenges, DfAM for support reduction.
- Cracking (Solidification/Liquation):
- Cause: Some alloys, particularly certain high-strength aluminum alloys like A6061 if not processed correctly, are susceptible to cracking along grain boundaries during the rapid solidification or re-melting of adjacent tracks.
- Mitigation:
- Optimized Process Parameters: Precise control over laser power, scan speed, hatch spacing, and potentially pre-heating the build plate.
- Specific Scan Strategies: Using techniques like island scanning or checkerboard patterns to manage thermal gradients.
- Alloy Selection: AlSi10Mg is generally less prone to cracking than A6061 during printing.
- Keyword Focus: Cracking aluminum AM, solidification cracking PBF.
- Surface Roughness & Dimensional Inaccuracy:
- Cause: Layer stepping effect, support contact marks, thermal variations, machine calibration drift.
- Mitigation:
- Orientation Strategy: Choosing the best orientation for critical surfaces and features.
- Post-Processing: Utilizing bead blasting, tumbling, or CNC machining as needed (discussed previously).
- Regular Machine Calibration & Maintenance: Ensuring the AM system performs accurately.
- Quality Assurance: Implementing rigorous quality assurance metal AM protocols, including dimensional inspection (CMM, scanning) and potentially non-destructive testing (NDT) if required.
- Keyword Focus: AM surface roughness, dimensional accuracy AM, quality control metal printing.
Partnering with an experienced additive manufacturing provider like Metal3DP is crucial for mitigating these challenges. Our company leverages deep process knowledge, state-of-the-art equipment, high-quality materials, and robust quality systems – all detailed further on our About Us page – to deliver reliable, high-performance 3D printed aluminum electrical enclosures that meet stringent industry requirements. Effective troubleshooting 3D printed enclosures relies on this combination of technology and expertise.
How to Choose the Right Metal 3D Printing Service Provider for Enclosures: Evaluating Suppliers for Your Needs
Selecting the right manufacturing partner is as critical as the design and material choices for your 3D printed aluminum enclosure project. The quality, reliability, cost-effectiveness, and overall success hinge on the capabilities and expertise of your chosen metal AM service bureau. For procurement managers and engineers tasked with sourcing these components, a thorough enclosure supplier evaluation process is essential.
Here are key criteria to consider when selecting a provider for your aluminum enclosure needs:
- Technical Expertise & Application Experience:
- Material Specialization: Do they have proven experience specifically with aluminum alloys like AlSi10Mg and A6061 using PBF processes? Ask for case studies or examples relevant to enclosures or similar components.
- DfAM Knowledge: Can they provide expert advice on optimizing your design for printability, functionality, and cost reduction? Do they offer engineering support services? (Metal3DP prides itself on decades of collective expertise in metal AM application development).
- Industry Experience: Familiarity with the specific requirements and standards of your industry (aerospace, medical, automotive, industrial) is a significant advantage.
- Equipment & Technology:
- Machine Fleet: What specific PBF machines (SLM, DMLS) do they operate? Are they modern, well-maintained, and properly calibrated for consistent results?
- Build Volume: Can their machines accommodate the size of your enclosure?
- Process Control: What measures do they take to monitor and control the printing environment (oxygen levels, temperature)? (Metal3DP utilizes industry-leading printers known for accuracy and reliability).
- Material Capabilities & Quality Control:
- Alloy Availability: Do they stock or source the specific aluminum alloy you require?
- Powder Quality: How do they guarantee the quality of their metal powder supplier specification? Ask about powder sourcing, testing (chemistry, particle size distribution, morphology, flowability), handling, storage, and traceability procedures. (Metal3DP manufactures its own high-quality spherical powders using advanced atomization, ensuring material consistency).
- Material Certifications: Can they provide material test certificates confirming compliance with required standards?
- Comprehensive Post-Processing Capabilities:
- In-House vs. Outsourced: Do they perform critical post-processing steps like heat treatment, CNC machining, and surface finishing in-house, or do they rely on external partners? In-house capabilities often lead to better control and shorter lead times.
- Range of Services: Can they provide all the necessary steps – from support removal and heat treatment to precision machining, anodizing, powder coating, and even enclosure assembly services?
- Quality Management System (QMS) & Certifications:
- Certifications: Do they hold relevant certifications like ISO 9001 (general quality management)? If required for your application, do they have AS9100 (aerospace) or ISO 13485 (medical devices)?
- Inspection Capabilities: What methods do they use for quality assurance (visual inspection, CMM dimensional checks, surface roughness testing, NDT if needed)?
- Capacity, Lead Time & Communication:
- Production Capacity: Can they handle your required production volume, whether it’s prototypes or low-to-medium series production?
- Lead Time: What are their typical lead time metal printing estimates for parts similar to your enclosure, including post-processing? Are they reliable in meeting deadlines?
- Quoting Process: How efficiently and clearly do they handle a request for quote (RFQ) metal AM?
- Communication: Are they responsive, transparent, and easy to communicate with throughout the project lifecycle?
- Location & Logistics:
- Consider shipping costs and transit times from the provider’s location (e.g., Metal3DP is headquartered in Qingdao, China) to your facility.
Supplier Evaluation Checklist:
Criteria | Key Questions | Notes / Rating |
---|---|---|
Technical Expertise | Aluminum AM experience? DfAM support? Industry knowledge? | |
Equipment & Technology | Machine type/quality? Build volume? Process control? | |
Material Quality | Alloy availability? Powder QA/traceability? Certifications? | |
Post-Processing | In-house capabilities? Range of services (Heat Treat, CNC, Finishing, Coating, Assembly)? | |
Quality System | Relevant certifications (ISO 9001, AS9100, ISO 13485)? Inspection methods? | |
Capacity & Lead Time | Volume capability? Quoted vs. actual lead times? RFQ efficiency? | |
Communication & Service | Responsiveness? Clarity? Project management? | |
Cost & Value | Competitive pricing? Overall value proposition (quality, speed, service)? | |
Location & Logistics | Shipping cost/time considerations? |
Export to Sheets
Choosing a partner like Metal3DP, with comprehensive Metal3DP capabilities spanning advanced equipment, high-quality materials manufacturing, and deep application expertise, significantly de-risks your project and ensures you receive high-quality aluminum enclosures optimized for your needs.
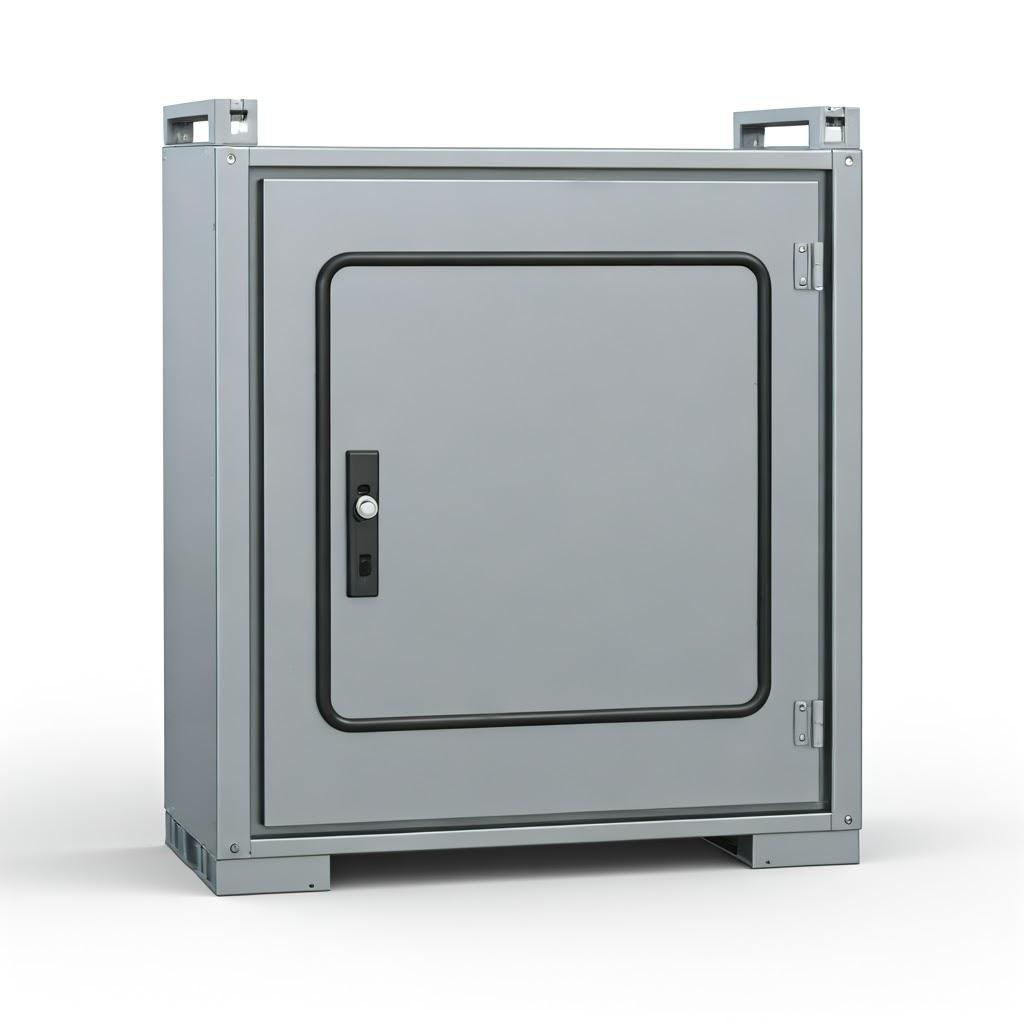
Understanding Cost Factors and Lead Times for 3D Printed Enclosures: Budgeting and Planning Your Project
A common question regarding metal additive manufacturing is about its cost-effectiveness. While AM eliminates tooling costs, making it highly competitive for prototypes and low volumes, the pricing structure differs from traditional methods. Understanding the key drivers behind metal 3D printing cost analysis and lead times is essential for accurate budgeting and project planning.
Key Cost Drivers for 3D Printed Aluminum Enclosures:
- Machine Time (Primary Driver):
- Build Height (Z-Height): The taller the part, the more layers need to be printed, directly increasing machine time. This is often the most significant single factor. Orienting parts to minimize height can reduce cost.
- Part Volume/Density: Larger, denser parts require more material to be scanned per layer, increasing the laser-on time.
- Scanning Complexity: Intricate features require more complex laser scanning paths per layer compared to simple geometries.
- Material Consumption:
- Part Volume: The actual amount of material cost aluminum AM powder fused to create the part.
- Support Structure Volume: Material used for supports is necessary for the print but is ultimately waste material, adding to the cost. Efficient DfAM minimizes support needs.
- Post-Processing:
- This can be a substantial portion of the total cost. Each step adds time and labor:
- Heat Treatment: Furnace time and energy costs.
- Support Removal: Labor-intensive, especially for complex parts.
- CNC Machining: Machine time (hourly rates), setup complexity, and programming time.
- Surface Finishing: Blasting, tumbling, polishing – each has associated labor and consumables costs.
- Coating/Anodizing: Process costs based on surface area, masking requirements, and batch size.
- Assembly: Labor costs for installing components.
- Keyword Focus: Post-processing costs impact overall enclosure manufacturing pricing.
- This can be a substantial portion of the total cost. Each step adds time and labor:
- Labor:
- Includes machine setup, part removal, powder handling, manual post-processing steps, quality inspection, and project management.
- Quality Assurance:
- The level of inspection required (visual, basic dimensional checks, CMM reports, NDT) impacts labor time and cost.
- Order Quantity:
- While setup costs are lower than traditional tooling, there are still per-batch setup tasks (machine preparation, powder loading). Bulk order enclosure pricing may offer slight per-part cost reductions due to amortization of these setup efforts over more units, but the primary cost drivers (machine time, material, post-processing) scale more linearly with quantity compared to injection molding or casting.
Factors Influencing Lead Times:
- Print Time: As discussed, primarily driven by build height (Z-height) and volume/complexity. Can range from several hours to multiple days for large or complex enclosures.
- Machine Queue: The service provider’s current workload and machine availability. Urgent orders may incur expedite fees.
- Post-Processing Time: This often dictates the overall lead time. Heat treatment cycles take hours, CNC machining depends on complexity, and coating processes have specific turnaround times. Complex multi-step post-processing can add days or weeks.
- Quality Assurance & Inspection: Time required for necessary checks and documentation.
- Shipping & Logistics: Transit time from the provider to your location.
Typical Lead Times:
- Simple Prototypes (Minimal Post-Processing): ~5-10 business days.
- Functional Parts (Heat Treat, Basic Finish): ~10-15 business days.
- Complex Parts (Extensive Machining/Coating): ~15-25+ business days.
It’s crucial to get a detailed quote that breaks down costs and provides a realistic AM lead time estimation based on your specific design and requirements. Early consultation with your AM provider can help optimize the design for cost and speed.
Frequently Asked Questions (FAQ) about 3D Printed Aluminum Enclosures
Here are answers to some common questions regarding 3D printed aluminum electrical enclosures:
Q1: How strong are 3D printed aluminum enclosures compared to machined or cast ones?
A: The mechanical properties of 3D printed aluminum alloys like AlSi10Mg or A6061 (after proper heat treatment) are generally comparable to their cast counterparts and can approach the strength of wrought alloys like A6061-T6, although ductility and fatigue properties might differ slightly depending on print orientation and process parameters. For most enclosure applications requiring structural integrity and protection, 3D printed enclosure strength is more than adequate and often superior to plastic alternatives. Proper design (DfAM) and material selection are key.
Q2: Is 3D printing aluminum enclosures more expensive than CNC machining?
A: It depends heavily on several factors.
- For Prototypes, Complex Geometries, and Low Volumes (e.g., 1-100 units): Metal 3D printing is often more cost-effective because it avoids high upfront tooling costs (casting molds) or extensive programming and setup time (complex multi-axis CNC).
- For Simple Geometries in High Volumes (e.g., 1000+ units): Traditional methods like CNC machining from stock or die casting typically become more economical due to lower per-part cycle times and material costs, once tooling is amortized. The cost comparison AM vs CNC enclosure should also factor in design freedom advantages and potentially faster lead times for AM in the initial stages.
Q3: Can 3D printed aluminum enclosures achieve high IP (Ingress Protection) or NEMA ratings?
A: Yes, absolutely. Achieving a high IP rating 3D printed enclosure (like IP65, IP67, or IP68) or NEMA rating depends on:
- Design: Incorporating features like well-designed sealing grooves for gaskets or O-rings, overlapping joints between enclosure parts (lid/base), and appropriate cable gland integration.
- Material Integrity: Ensuring the printed part is dense and free from critical porosity.
- Post-Processing: Often requires CNC machining of sealing surfaces to achieve the necessary flatness and surface finish for effective sealing.
- Assembly: Correct installation of appropriate seals/gaskets.
Q4: What is the best aluminum alloy for 3D printing electrical enclosures?
A: There isn’t one single “best” alloy; it depends on the specific requirements:
- AlSi10Mg: Often preferred for its excellent printability, suitability for complex geometries, and good all-around strength and thermal properties. It’s a reliable choice for many general-purpose enclosures.
- A6061: Chosen when higher ductility, fracture toughness, or superior corrosion resistance is needed. However, it requires more careful process control during printing to avoid defects like cracking. Discuss your application’s mechanical, thermal, and environmental requirements with your AM service provider to select the best aluminum for 3D printing enclosure needs.
Q5: How do I get a quote for a custom 3D printed aluminum enclosure?
A: The typical custom enclosure order process involves:
- Prepare Your Data: Have a 3D CAD model ready, preferably in STEP format.
- Define Requirements: Specify the aluminum alloy (e.g., AlSi10Mg), required quantity, desired tolerances (highlight critical dimensions), necessary post-processing (heat treatment, machining specifics, finishing, coating), and any specific testing or certification needs. Describe the application environment.
- Submit RFQ: Contact your chosen metal AM service provider, like Metal3DP. You can typically upload your files and specifications through their website or contact form. Visithttps://met3dp.com/to initiate the process.
- Review Quote: The provider will analyze your request and provide a detailed quote outlining costs and estimated lead times.
Conclusion: Embracing the Future of Enclosure Manufacturing with Metal 3D Printing and Reliable Partners
The landscape of electrical enclosure manufacturing is evolving, driven by the capabilities of metal additive manufacturing. As we’ve explored, using 3D printing with advanced aluminum alloys like AlSi10Mg and A6061 offers unparalleled advantages:
- Unmatched Design Freedom: Creating complex, optimized, and integrated enclosure solutions previously impossible.
- Rapid Prototyping & Customization: Accelerating development cycles and enabling cost-effective low-volume production without tooling.
- Enhanced Performance: Achieving superior thermal management, lightweighting, and tailored structural integrity.
- Supply Chain Optimization: Enabling on-demand production and digital inventory strategies.
These digital manufacturing benefits are transforming how engineers and procurement managers approach enclosure design and sourcing in demanding industries like aerospace, automotive, medical, and industrial automation. The future of enclosure manufacturing undoubtedly involves leveraging AM to meet increasing demands for performance, customization, and speed.
However, realizing the full potential of this technology requires more than just access to a printer. It demands expertise in DfAM, meticulous process control, high-quality materials, comprehensive post-processing capabilities, and robust quality assurance. Choosing the right manufacturing partner is paramount.
Metal3DP stands as a leader in this field, offering comprehensive advanced enclosure solutions. As a vertically integrated company headquartered in Qingdao, China, we not only provide cutting-edge Selective Electron Beam Melting (SEBM) and PBF printers but also manufacture our own high-performance metal powders, including specialized alloys. Our decades of collective expertise ensure we understand the nuances of metal AM, from initial design consultation to final finished part. We partner with organizations worldwide to implement 3D printing effectively and accelerate their digital manufacturing transformations.
If you are looking to leverage the power of metal 3D printing for your next electrical enclosure project, or seeking a reliable partner for partnering with Metal3DP for your additive manufacturing needs, we invite you to reach out.
Contact Metal3DP today to discuss your requirements and discover how our capabilities can power your organization’s additive manufacturing goals and deliver next-generation enclosure solutions.
Share On
MET3DP Technology Co., LTD is a leading provider of additive manufacturing solutions headquartered in Qingdao, China. Our company specializes in 3D printing equipment and high-performance metal powders for industrial applications.
Inquiry to get best price and customized Solution for your business!
Related Articles
About Met3DP
Recent Update
Our Product
CONTACT US
Any questions? Send us message now! We’ll serve your request with a whole team after receiving your message.
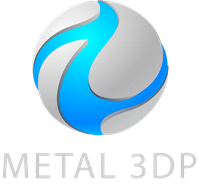
Metal Powders for 3D Printing and Additive Manufacturing