Electrode Inert Gas Atomisers
Table of Contents
Ever wondered how high-quality metal powders are made? Well, you’ve come to the right place! Today, we’re diving into the fascinating world of electrode inert gas atomisers. Buckle up, because this journey is going to be both informative and engaging!
Overview of Electrode Inert Gas Atomisers
Electrode inert gas atomisers are cutting-edge devices used to produce fine metal powders. These powders are crucial in various industries, from aerospace to pharmaceuticals. But what makes these atomisers so special? Let’s break it down:
- Process: Electrode inert gas atomisation involves melting a metal using an electrode and then dispersing it into fine droplets using an inert gas. These droplets cool and solidify into powder.
- Precision: The process allows for precise control over particle size and distribution.
- Purity: The use of inert gas prevents oxidation, ensuring high-purity metal powders.
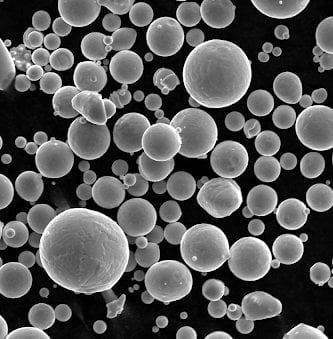
Types and Characteristics of Metal Powders
When it comes to metal powders produced by electrode inert gas atomisers, there are several models, each with unique properties. Here’s a rundown of some notable ones:
Metal Powder Model | Composition | Properties | Characteristics |
---|---|---|---|
AlSi10Mg | Al, Si, Mg | Lightweight, high strength | Ideal for aerospace components |
Ti-6Al-4V | Ti, Al, V | Excellent biocompatibility | Widely used in medical implants |
Inconel 718 | Ni, Cr, Fe | High temperature resistance | Used in jet engine components |
SS316L | Fe, Cr, Mo, Ni | Corrosion resistance | Preferred in marine applications |
Copper | Pure Cu | High electrical conductivity | Essential for electrical parts |
Maraging Steel | Fe, Ni, Mo, Co | Ultra-high strength | Used in tooling and machinery |
CoCrMo | Co, Cr, Mo | Wear resistance | Dental and orthopedic implants |
NiCrFe | Ni, Cr, Fe | Oxidation resistance | Chemical processing equipment |
Al6061 | Al, Mg, Si | Good machinability | General engineering applications |
Tungsten | Pure W | High density and melting point | Radiation shielding, filaments |
Each of these powders serves distinct purposes and showcases how versatile electrode inert gas atomisers can be.
Applications of Electrode Inert Gas Atomisers
These atomisers have revolutionized many industries. Here’s a closer look at their applications:
Industry | Application | Examples |
---|---|---|
Aerospace | Lightweight, strong components | Turbine blades, structural parts |
Medical | Biocompatible implants | Hip joints, dental crowns |
Automotive | High-performance parts | Engine components, gear systems |
Electronics | Conductive elements | Circuit boards, connectors |
Tooling | Durable tools and dies | Cutting tools, molds |
Energy | High-temperature resistance | Turbine engines, nuclear reactor components |
Defense | High-strength materials | Armor, weaponry |
Additive Manufacturing | Metal 3D printing materials | Prototyping, custom parts |
Specifications, Sizes, Grades, and Standards
When selecting metal powders, specifications matter. Here’s a breakdown of some key specs:
Metal Powder Model | Size Range (µm) | Grades | Standards |
---|---|---|---|
AlSi10Mg | 20-63 | A1, A2 | ISO 9001, ASTM B933 |
Ti-6Al-4V | 15-45 | Grade 5 | ASTM F2924, ISO 5832-3 |
Inconel 718 | 15-53 | 718-01 | AMS 5662, ASTM B637 |
SS316L | 10-45 | 316L-A | ASTM F138, ISO 5832-1 |
Copper | 15-63 | C11000 | ASTM B170, ISO 4288 |
Maraging Steel | 20-53 | 18Ni300 | AMS 6514, ASTM A538 |
CoCrMo | 15-45 | F75, F1537 | ASTM F75, ISO 5832-4 |
NiCrFe | 20-60 | Inconel X | ASTM B168, ISO 6208 |
Al6061 | 15-53 | 6061-T6 | ASTM B209, ISO 3522 |
Tungsten | 20-63 | W-1 | ASTM B777, ISO 3878 |
Suppliers and Pricing Details
Choosing the right supplier can make a significant difference in quality and cost. Here’s a snapshot of some leading suppliers:
Supplier | Metal Powders Available | Price Range (per kg) | Special Notes |
---|---|---|---|
Advanced Metal Powders | AlSi10Mg, Ti-6Al-4V, Inconel 718 | $100 – $300 | Bulk discounts available |
PowderTech Solutions | SS316L, Copper, Maraging Steel | $80 – $250 | Custom particle size distribution |
Metalurgy Experts | CoCrMo, NiCrFe, Al6061 | $120 – $400 | High purity options |
Innovative Metals Inc. | Tungsten, Ti-6Al-4V, Inconel 718 | $200 – $500 | Specialized in aerospace-grade powders |
Quality Metal Powders | AlSi10Mg, SS316L, Copper | $90 – $270 | Fast delivery and excellent customer service |
Advantages of Electrode Inert Gas Atomisers
Why should you consider using electrode inert gas atomisers? Here are some compelling reasons:
- High Purity: The use of inert gas prevents contamination and oxidation, ensuring high-purity powders.
- Controlled Particle Size: Achieving specific particle sizes and distributions is straightforward, providing versatility for different applications.
- Efficiency: The process is efficient, producing minimal waste and maximizing yield.
- Flexibility: Suitable for a wide range of metals and alloys, making it adaptable to various industries.
Imagine having a toolbox that can adapt to almost any job you throw at it. That’s what electrode inert gas atomisers offer in the world of metal powders.
Disadvantages of Electrode Inert Gas Atomisers
Of course, no technology is without its downsides. Here are a few to consider:
- Cost: The equipment and operation can be expensive, especially for small-scale production.
- Complexity: The process requires precise control and expertise, which can be a barrier for some users.
- Maintenance: Regular maintenance is essential to ensure consistent performance and avoid downtime.
It’s like having a high-performance sports car; the performance is unmatched, but it comes with higher costs and maintenance needs.
Comparing Electrode Inert Gas Atomisers with Other Methods
How do electrode inert gas atomisers stack up against other methods like water atomisation or plasma atomisation? Let’s compare:
Method | Pros | Cons |
---|---|---|
Electrode Inert Gas | High purity, controlled particle size, efficient | Expensive, complex, high maintenance |
Water Atomisation | Cost-effective, simple | Lower purity, risk of oxidation, limited to certain metals |
Plasma Atomisation | Extremely high purity, suitable for reactive metals | Very expensive, complex, limited throughput |
Centrifugal Atomisation | High yield, uniform particles | High initial cost, limited to spherical powders |
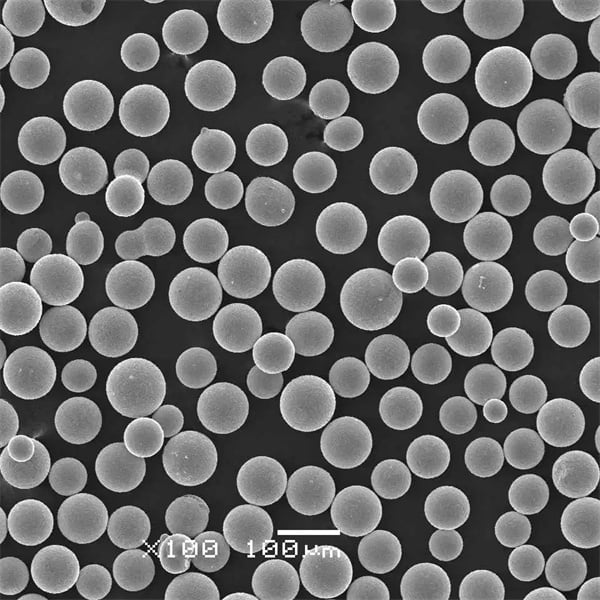
FAQs
Let’s tackle some common questions:
Question | Answer |
---|---|
What metals can be atomised using this method? | Almost all metals, including aluminum, titanium, and nickel alloys. |
Is the process environmentally friendly? | Yes, it produces minimal waste and the inert gas can be recycled. |
How does inert gas prevent oxidation? | Inert gases like argon do not react with the metal, preventing oxidation. |
What industries benefit the most from these powders? | Aerospace, medical, automotive, electronics, and more. |
Can small businesses afford this technology? | While initially costly, it’s a long-term investment for high-quality output. |
How do I choose the right powder for my application? | Consult with suppliers and consider your specific application needs. |
Share On
MET3DP Technology Co., LTD is a leading provider of additive manufacturing solutions headquartered in Qingdao, China. Our company specializes in 3D printing equipment and high-performance metal powders for industrial applications.
Inquiry to get best price and customized Solution for your business!
Related Articles
About Met3DP
Recent Update
Our Product
CONTACT US
Any questions? Send us message now! We’ll serve your request with a whole team after receiving your message.
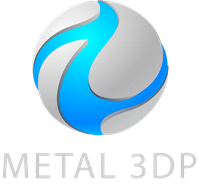
Metal Powders for 3D Printing and Additive Manufacturing
COMPANY
PRODUCT
cONTACT INFO
- Qingdao City, Shandong, China
- [email protected]
- [email protected]
- +86 19116340731