Electron Beam Melting Materials EBM Materials
Table of Contents
Imagine a 3D printer that uses a focused beam of electrons, rather than a laser, to meticulously craft intricate metal parts layer by layer. This is the magic of Electron Beam Melting (EBM), a revolutionary additive manufacturing (AM) process that unlocks a world of possibilities for creating complex, high-performance metal components. But what fuels this process? The answer lies in the very heart of EBM – the electron beam melting materials.These specialized metal powders are the building blocks that EBM utilizes to bring your digital designs to life. Unlike your run-of-the-mill metal dust, EBM materials are meticulously engineered to possess specific characteristics that ensure smooth melting, strong bonding, and exceptional final part properties.Delving deeper, let’s explore the fascinating world of electron beam melting materials and unlock the secrets that lie beneath the surface.
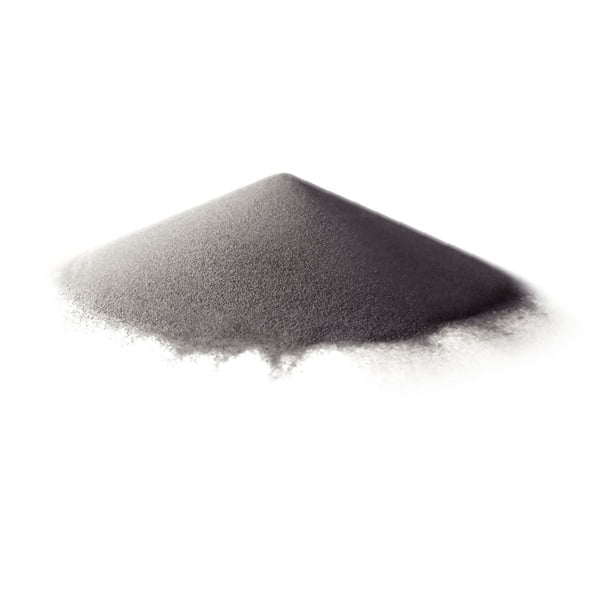
A Look at Common EBM Materials
EBM, due to the nature of the melting process, thrives on electrically conductive materials. This translates to a focus on metals and certain alloys. Here, we’ll delve into some of the most popular and versatile metal powders used in EBM:
Material | Composition | Properties | Applications |
---|---|---|---|
Titanium (Ti) | Pure titanium | Excellent biocompatibility, high strength-to-weight ratio, good corrosion resistance | Biomedical implants, aerospace components, sporting goods |
Titanium-6 Aluminum-4 Vanadium (Ti-6Al-4V) | Titanium alloy with 6% aluminum and 4% vanadium | High strength, good ductility, excellent fatigue resistance | Aerospace components, automotive parts, medical devices |
Cobalt-Chrome (CoCr) | Alloy of cobalt and chromium | High wear resistance, biocompatible, good corrosion resistance | Biomedical implants, dental prosthetics, cutting tools |
Inconel 718 | Nickel-chromium-based superalloy | Exceptional strength at high temperatures, good oxidation resistance | Aerospace components, gas turbine engines, heat exchangers |
Inconel 625 | Nickel-chromium-based superalloy with molybdenum | Excellent corrosion resistance, good high-temperature strength | Chemical processing equipment, marine applications, heat exchangers |
Stainless Steel 316L | Austenitic stainless steel with molybdenum | Excellent corrosion resistance, biocompatible | Biomedical implants, chemical processing equipment, food and beverage equipment |
Stainless Steel 17-4PH | Precipitation-hardening stainless steel | High strength, good corrosion resistance, good ductility | Aerospace components, automotive parts, marine applications |
Tool Steel | Various compositions with high carbon content | Exceptional wear resistance, high hardness | Cutting tools, dies, molds |
Tantalum (Ta) | Pure tantalum | Biocompatible, high melting point, excellent corrosion resistance | Biomedical implants, capacitor components, chemical processing equipment |
Titanium-Tantalum Alloy (TiTa) | Alloy of titanium and tantalum | High strength-to-weight ratio, good biocompatibility, excellent corrosion resistance | Biomedical implants, aerospace components, chemical processing equipment |
A Deeper Dive into Specific Metal Powders
While the table above provides a general overview, let’s take a closer look at some of these metal powders to understand their unique strengths:
- Titanium (Ti): The king of biocompatibility, pure titanium is a popular choice for medical implants due to its ability to seamlessly integrate with the human body. Its lightweight nature and impressive strength-to-weight ratio further solidify its place in aerospace applications and sporting goods.
- Titanium-6 Aluminum-4 Vanadium (Ti-6Al-4V): This workhorse alloy is the go-to material for demanding applications in the aerospace industry. Its superior strength, good ductility, and excellent fatigue resistance make it ideal for withstanding the harsh conditions encountered in flight. Think of it as the muscle behind rockets and jet engines.
- Cobalt-Chrome (CoCr): Renowned for its exceptional wear resistance, CoCr finds its calling in applications where friction is a constant battle. From biomedical implants like hip replacements to dental prosthetics, CoCr ensures smooth operation and longevity.
- Inconel 718 & Inconel 625: These superalloys are the ultimate champions when it comes to high-temperature performance. Imagine the scorching heat inside a gas turbine engine – that’s where Inconel thrives. Inconel 625 adds an extra layer of protection against corrosion, making it a valuable asset in harsh chemical environments.
Selecting the Right EBM Material
- Mechanical Properties: Strength, ductility, fatigue resistance – these properties dictate how a material will behave under stress. For a lightweight aircraft component, high strength-to-weight ratio might be paramount. Conversely, a tool steel used for cutting through tough materials needs exceptional wear resistance and hardness.
- Thermal Properties: How a material handles heat plays a crucial role in EBM. Inconel alloys excel in high-temperature environments, while some tool steels might lose their strength at elevated temperatures. Understanding the thermal profile of your application is vital for choosing the right material.
- Corrosion Resistance: Will your component be exposed to harsh chemicals or saltwater? Stainless steel and tantalum offer excellent corrosion resistance, making them ideal for applications like chemical processing equipment and marine components.
- Biocompatibility: For medical implants, the material needs to seamlessly integrate with the body without causing adverse reactions. Titanium and CoCr are popular choices due to their biocompatible nature.
- Printability: Not all metal powders are created equal when it comes to EBM. Factors like particle size, flowability, and melting point can influence the printability of the material. Working closely with your EBM service provider to choose a material with good printability ensures smooth operation and high-quality parts.
Exploring Advanced EBM Materials
The world of EBM materials is constantly evolving. Researchers are pushing the boundaries by developing innovative alloys with unique properties:
- Nickel-based superalloys: Going beyond Inconel, new nickel alloys are being developed with even higher temperature capabilities, targeting applications like next-generation jet engines.
- High-strength aluminum alloys: Imagine aluminum parts with strength approaching that of steel. This is the promise of new aluminum alloys being explored for EBM, offering a lightweight alternative for demanding applications.
- Functionally graded materials (FGMs): These fascinating materials possess a gradient in composition, transitioning from one material to another within a single component. This allows for tailoring properties across different regions of the part, a potential game-changer for complex applications.
Resources for EBM Material Selection
Selecting the right EBM material requires careful consideration. Here are some valuable resources to guide you:
- Metal powder suppliers: Reputable suppliers like Met3DP offer a wide range of EBM materials and can provide expert advice on material selection based on your specific needs.
- EBM service providers: Experienced EBM service providers have extensive knowledge of material properties and printability characteristics. Partnering with a reliable service provider can ensure optimal material selection for your project.
- Online databases: Several online databases offer comprehensive information on EBM materials, including their properties, certifications, and compatibility with specific EBM machines.
EBM Material Specifications: A Deep Dive into Data
While understanding general properties is crucial, specific data plays a vital role in material selection. Here’s a breakdown of some key specifications for popular EBM materials:
Material | Particle Size (µm) | Density (g/cm³) | Melting Point (°C) | Standards |
---|---|---|---|---|
Titanium (Ti) | 45-150 | 4.5 | 1668 | ASTM B294, AMS 4921 |
Titanium-6 Aluminum-4 Vanadium (Ti-6Al-4V) | 45-150 | 4.43 | 1640 | ASTM F136, AMS 4928 |
Cobalt-Chrome (CoCr) | 20-100 | 8.3 | 1495 | ASTM F645, ISO 5832-4 |
Inconel 718 | 45-150 | 8.19 | 1484 | ASTM B904, AMS 5662 |
Inconel 625 | 20-100 | 8.4 | 1350 | ASTM B168, UNS N06625 |
Price Considerations: How Much Does EBM Material Cost?
The cost of EBM materials can vary depending on the specific material, its grade, and the market demand. Here’s a general range to provide some perspective:
EBM Material Cost
Material | Price Range (USD/kg) |
---|---|
Inconel 718 | $200 – $300 |
Inconel 625 | $250 – $350 |
Stainless Steel 316L | $80 – $120 |
Stainless Steel 17-4PH | $90 – $130 |
Tool Steel | $150 – $250 |
Tantalum (Ta) | $400 – $600 |
Titanium-Tantalum Alloy (TiTa) | $250 – $350 |
It’s important to remember that these are just ballpark figures. The actual cost can be influenced by factors like:
- Order quantity: Larger orders typically qualify for bulk discounts.
- Supplier: Different suppliers may have varying pricing structures.
- Material grade: Higher purity or specific certifications can increase the cost.
Weighing the Pros and Cons: A Balanced Look at EBM Materials
EBM materials offer a compelling set of advantages, but it’s essential to consider the limitations as well. Here’s a breakdown of the pros and cons:
Pros
- Exceptional mechanical properties: EBM materials can achieve outstanding strength, ductility, and fatigue resistance, making them ideal for demanding applications.
- High-quality surface finishes: The EBM process produces parts with excellent surface finishes, reducing the need for post-processing.
- Design freedom: EBM enables the creation of complex geometries that are difficult or impossible to achieve with traditional manufacturing methods.
- Lightweighting: Several EBM materials offer a high strength-to-weight ratio, making them ideal for applications where weight reduction is critical.
Cons
- Limited material selection: Compared to traditional manufacturing techniques, EBM has a somewhat narrower range of readily available materials.
- High cost: Both the EBM materials and the EBM process itself can be more expensive than some traditional methods.
- Residual stress: The EBM process can introduce residual stress into parts, which may need to be addressed through post-processing techniques.
- Surface roughness: While generally good, EBM surfaces might require additional finishing depending on the specific application requirements.
EBM Material FAQs
Here are some frequently asked questions regarding EBM materials:
Q: What is the strongest EBM material?
A: The strength of an EBM material depends on its composition. Inconel 718 and some tool steels are known for their exceptional strength.
Q: What is the most biocompatible EBM material?
A: Titanium and Cobalt-Chrome are popular choices for medical implants due to their biocompatibility.
Q: Can I use recycled metal powder for EBM?
A: While some research is ongoing, using recycled metal powder in EBM is currently not a widespread practice due to concerns about contamination and maintaining consistent material properties.
Q: How long does it take to get EBM materials?
A: Lead times for EBM materials can vary depending on the specific material, its grade, and the supplier’s inventory. It’s always best to check with your chosen supplier for current lead times.
The Future of EBM Materials: A Glimpse into Innovation
The future of EBM materials is brimming with promise. Here are some exciting trends to watch out for:
- Development of new materials: Researchers are continuously exploring new alloys and material compositions to expand the capabilities of EBM.
- Standardization of materials: Greater standardization of EBM materials will improve quality control and streamline the selection process.
- Sustainability efforts: There’s a growing focus on developing sustainable practices for the production and recycling of EBM materials.
Conclusion: EBM Materials
EBM materials are the building blocks of a revolutionary additive manufacturing process. Understanding their properties, limitations, and selection considerations empowers you to leverage the true potential of EBM. From crafting high-performance aerospace components to creating biocompatible medical implants, EBM materials are poised to shape the future of manufacturing across diverse industries. As technology continues to evolve, the possibilities with EBM materials are truly limitless.
Share On
MET3DP Technology Co., LTD is a leading provider of additive manufacturing solutions headquartered in Qingdao, China. Our company specializes in 3D printing equipment and high-performance metal powders for industrial applications.
Inquiry to get best price and customized Solution for your business!
Related Articles
About Met3DP
Recent Update
Our Product
CONTACT US
Any questions? Send us message now! We’ll serve your request with a whole team after receiving your message.
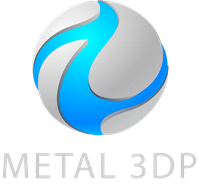
Metal Powders for 3D Printing and Additive Manufacturing