Electronics Bays for Spacecraft
Table of Contents
Introduction – The Critical Role of Electronics Bays in Spacecraft and the Metal 3D Printing Advantage
In the unforgiving vacuum of space, the reliability and performance of every component are paramount. At the heart of any spacecraft lies its electronics bay – a meticulously designed and engineered structure that houses and protects the mission-critical electronic systems. These bays serve as the central nervous system of the spacecraft, orchestrating vital functions such as communication, navigation, power distribution, data processing, and scientific instrumentation control. The integrity and functionality of the electronics bay directly impact the overall success of space missions, making its design and manufacturing process a critical area of focus for aerospace engineers and procurement managers.
Traditional manufacturing methods for spacecraft electronics bays often involve complex machining, welding, and assembly processes. These methods can be time-consuming, generate significant material waste, and impose limitations on design complexity. However, the advent of metal 3D printing, also known as metal additive manufacturing (AM), is revolutionizing the way these critical components are being conceived and produced. Metal 3D printing offers unprecedented design freedom, enabling the creation of intricate geometries and optimized structures that were previously unattainable. This technology allows for the integration of features like internal cooling channels, lightweight lattice structures, and consolidated parts, leading to significant improvements in performance, weight reduction, and time-to-market.
Metal3DP, headquartered in Qingdao, China, stands at the forefront of this technological shift. As a leading provider of additive manufacturing solutions, we specialize in high-performance metal powders and cutting-edge 3D printing equipment tailored for demanding industrial applications, including aerospace. Our commitment to industry-leading print volume, accuracy, and reliability ensures that mission-critical parts, like spacecraft electronics bays, meet the stringent requirements of the space industry. By leveraging our advanced powder making systems and a comprehensive portfolio of high-quality metal powders, including those ideal for spacecraft applications, Metal3DP empowers organizations to embrace the benefits of metal AM and accelerate their digital manufacturing transformations. Discover more about Metal3DP and our expertise in metal 3D printing.
What are Spacecraft Electronics Bays Used For? – Core Functions, Housing Sensitive Components, and Ensuring Mission Success
Spacecraft electronics bays are more than just enclosures; they are sophisticated, multi-functional systems vital for the operation and success of any space mission. Their primary purpose is to provide a secure and controlled environment for the spacecraft’s sensitive electronic components, protecting them from the harsh conditions of space, including extreme temperature variations, radiation, and mechanical stresses during launch and operation.
Here’s a breakdown of the core functions of spacecraft electronics bays:
- Protection: Shielding delicate electronics from the external environment, including thermal fluctuations, vacuum, microgravity, and radiation.
- Structural Support: Providing a robust framework to mount and secure various electronic units, ensuring they remain in place during the intense vibrations and accelerations experienced during launch and orbital maneuvers.
- Thermal Management: Facilitating the dissipation of heat generated by electronic components to prevent overheating and ensure optimal performance. This often involves integrated heat sinks, cooling channels, and thermal interfaces.
- Electromagnetic Interference (EMI) Shielding: Minimizing the interference between different electronic systems and protecting them from external electromagnetic radiation.
- Cable Management: Organizing and routing electrical wiring and data cables efficiently to prevent entanglement, reduce weight, and simplify maintenance.
- Modularity and Accessibility: Designing the bay to allow for easy access to components for assembly, testing, and potential in-flight maintenance or upgrades (where applicable).
The types of critical electronic components housed within these bays can include:
- Command and Data Handling (C&DH) Systems: Responsible for processing commands, collecting telemetry data, and managing the overall operation of the spacecraft.
- Communication Systems: Transceivers and antennas used for communicating with ground stations and other spacecraft.
- Navigation and Guidance Systems: Inertial measurement units (IMUs), star trackers, and GPS receivers that determine the spacecraft’s position and orientation.
- Power Distribution Units (PDUs): Manage and distribute electrical power generated by solar panels or batteries to various subsystems.
- Scientific Instruments: Control units and data acquisition systems for onboard scientific payloads.
- Actuation and Control Electronics: Drivers for motors, valves, and other mechanical systems responsible for attitude control and deployment mechanisms.
The reliable operation of these electronic systems, housed within a well-designed and manufactured electronics bay, is fundamental to achieving mission objectives, whether it’s capturing high-resolution images of Earth, exploring distant planets, or deploying critical satellite constellations. The integrity of the electronics bay directly translates to the mission’s success or failure.
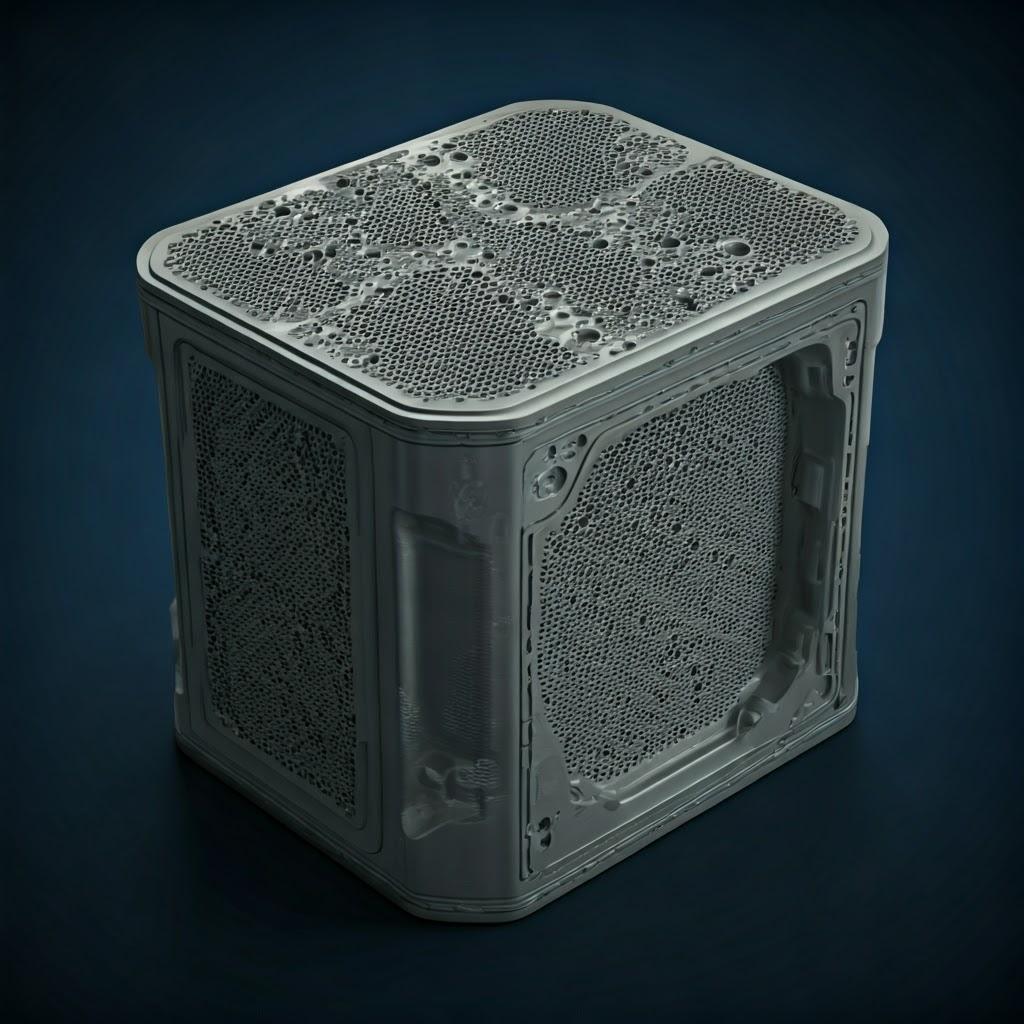
Why Use Metal 3D Printing for Spacecraft Electronics Bays? – Design Freedom, Lightweighting, Rapid Prototyping, and Enhanced Performance
Metal 3D printing offers a paradigm shift in the design and manufacturing of spacecraft electronics bays, providing significant advantages over traditional methods. These benefits are particularly crucial in the aerospace industry, where performance, weight, and reliability are paramount.
- Unprecedented Design Freedom: Additive manufacturing allows for the creation of complex geometries that are difficult or impossible to achieve with conventional techniques. This includes:
- Optimized Topologies: Designing structures with material concentrated only where it’s needed for strength and support, leading to significant weight reduction.
- Integrated Features: Incorporating features like internal cooling channels, cable routing pathways, and mounting interfaces directly into the design, reducing the need for multiple parts and assembly steps.
- Customization: Tailoring the design precisely to the specific electronic components and spatial constraints of the spacecraft, maximizing space utilization.
- Significant Lightweighting: Reducing the mass of spacecraft components is critical for lowering launch costs and improving fuel efficiency. Metal 3D printing enables the creation of lightweight structures through:
- Lattice Structures: Implementing intricate, internal lattice designs that provide high strength-to-weight ratios.
- Topology Optimization: Using software algorithms to optimize the material distribution based on applied loads, removing unnecessary mass while maintaining structural integrity.
- Rapid Prototyping and Iteration: Metal 3D printing accelerates the design and development cycle by allowing for the quick production of prototypes. This enables engineers to:
- Test and Validate Designs Rapidly: Identifying and resolving design flaws early in the process.
- Iterate Quickly on Design Modifications: Implementing changes based on testing and simulation results with minimal lead time.
- Reduce Time-to-Market: Accelerating the overall development and deployment of spacecraft.
- Enhanced Performance and Functionality: Additive manufacturing can lead to improved performance through:
- Optimized Thermal Management: Designing internal cooling channels that precisely follow heat-generating components, improving heat dissipation and preventing overheating.
- Part Consolidation: Combining multiple parts into a single 3D-printed component, reducing the number of joints and fasteners, which are potential points of failure. This enhances structural integrity and reliability.
- Improved Material Properties: Advanced metal powders, processed through controlled 3D printing parameters, can exhibit superior mechanical properties compared to conventionally manufactured materials.
Metal3DP‘s advanced Selective Electron Beam Melting (SEBM) printers and high-quality metal powders are ideally suited for producing complex, lightweight, and high-performance spacecraft electronics bays. Our industry-leading print volume allows for the creation of larger, consolidated parts, while our focus on accuracy and reliability ensures that these critical components meet the demanding standards of the aerospace industry. Explore our range of metal 3D printing solutions.
Recommended Materials and Why They Matter – Exploring AlSi10Mg and Scalmalloy® for Optimal Performance in Space Environments
The choice of material is paramount when manufacturing spacecraft electronics bays, as these components must withstand the extreme conditions of space while providing structural integrity and functional reliability. Metal3DP offers a range of high-performance metal powders specifically designed for demanding applications. For spacecraft electronics bays, two particularly compelling materials are AlSi10Mg and Scalmalloy®.
AlSi10Mg:
- Description: AlSi10Mg is a widely used aluminum alloy in additive manufacturing, known for its excellent strength-to-weight ratio, good thermal conductivity, and corrosion resistance. It is a powder typically used in Laser Powder Bed Fusion (LPBF) processes.
- Why it Matters for Spacecraft Electronics Bays:
- Lightweighting: Aluminum alloys are inherently lightweight, which is crucial for reducing the overall mass of the spacecraft and minimizing launch costs.
- Thermal Management: The good thermal conductivity of AlSi10Mg allows for efficient heat dissipation from electronic components, helping to maintain optimal operating temperatures in the vacuum of space where convective cooling is absent.
- Good Mechanical Properties: This alloy offers a good balance of strength and ductility, providing the necessary structural integrity to withstand launch stresses and operational loads.
- Processability: AlSi10Mg is well-established for additive manufacturing, offering consistent and reliable printing results.
Scalmalloy®:
- Description: Scalmalloy® is a high-performance aluminum-magnesium-scandium alloy specifically developed for additive manufacturing applications requiring exceptional strength and lightweighting. It exhibits significantly higher strength than conventional aluminum alloys.
- Why it Matters for Spacecraft Electronics Bays:
- Ultra-Lightweighting with High Strength: Scalmalloy® offers an even higher strength-to-weight ratio than AlSi10Mg, enabling the creation of even lighter electronics bays without compromising structural integrity. This is particularly beneficial for demanding space missions where every gram counts.
- Excellent Mechanical Properties: The superior strength and stiffness of Scalmalloy® make it ideal for components that need to withstand significant mechanical loads and vibrations.
- Good Corrosion Resistance: While aluminum alloys generally offer good corrosion resistance, Scalmalloy®’s specific composition enhances this property, which is important for long-duration space missions.
- Potential for Complex Geometries: Like other aluminum alloys used in AM, Scalmalloy® can be used to create intricate designs that optimize space utilization and functionality.
Metal3DP provides high-quality AlSi10Mg powder that is optimized for laser powder bed fusion, ensuring the production of dense, high-performance parts with excellent mechanical properties. Furthermore, our expertise in material science allows us to work with advanced alloys like Scalmalloy®, enabling our customers in the aerospace industry to push the boundaries of lightweight design and performance for critical components like spacecraft electronics bays. Our advanced powder making system ensures the high sphericity and flowability of our metal powders, which are crucial for achieving consistent and reliable 3D printing outcomes. Learn more about our high-quality metal powders.
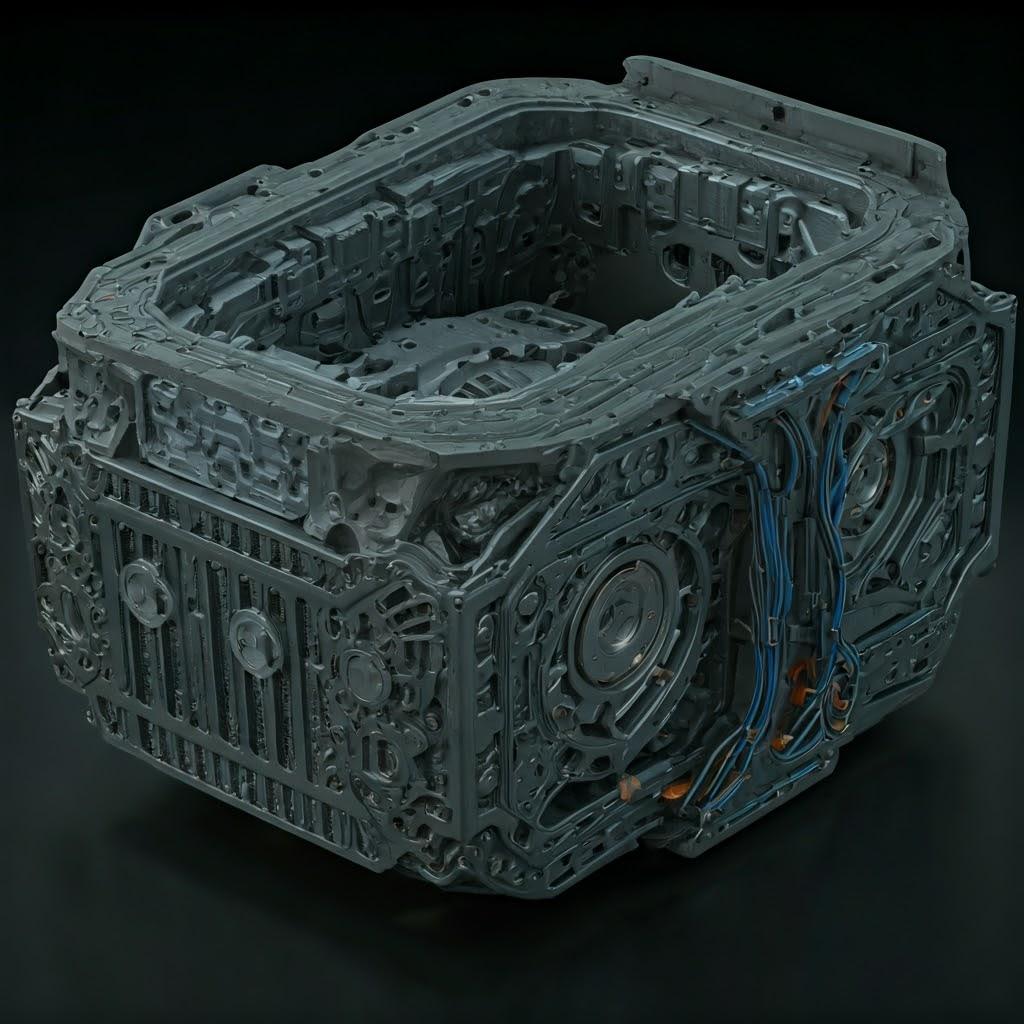
Design Considerations for Additive Manufacturing of Electronics Bays – Optimizing Geometry, Thermal Management Features, and Integration Capabilities
Designing spacecraft electronics bays for metal 3D printing requires a different mindset compared to traditional manufacturing. To fully leverage the capabilities of additive manufacturing, engineers must consider several key factors:
- Topology Optimization: Employing specialized software to analyze the structural requirements and material distribution, allowing for the creation of lightweight yet strong designs. This involves removing material from low-stress areas and concentrating it where it’s needed most. The resulting organic-looking shapes are often impossible to produce with conventional methods.
- Lattice Structures: Integrating internal lattice structures can significantly reduce weight while maintaining or even enhancing stiffness and strength. Different lattice patterns (e.g., gyroid, cubic, octet) can be chosen based on specific load-bearing requirements and weight targets.
- Thermal Management Integration: Designing internal cooling channels directly into the electronics bay structure allows for efficient heat dissipation. These channels can be tailored to follow the contours of heat-generating components, optimizing thermal transfer to a cooling fluid or heat sink. Conformal cooling designs, achievable through 3D printing, are far more effective than straight drilled channels.
- Part Consolidation: Identifying opportunities to combine multiple components into a single 3D-printed part reduces the need for fasteners, assembly time, and potential points of failure. This can lead to lighter, more reliable, and easier-to-integrate electronics bays.
- Interface Design: Carefully designing the interfaces for mounting electronic components, connecting cables, and integrating with the spacecraft structure is crucial. Additive manufacturing allows for the creation of complex mounting features, snap-fits, and integrated cable routing pathways.
- Minimizing Support Structures: While support structures are often necessary in metal 3D printing, designing parts to minimize their use reduces material waste, post-processing time, and potential surface finish issues. Orienting the part strategically on the build platform and incorporating self-supporting angles can help achieve this.
- Outgassing Considerations: For space applications, the materials used must have low outgassing properties to prevent contamination of sensitive instruments and degradation of performance in the vacuum of space. Material selection and post-processing (e.g., vacuum baking) are critical to address this.
- Design for Assembly and Disassembly: While part consolidation is beneficial, consider potential maintenance or upgrades. Designing modular sections that can be easily assembled and disassembled might be necessary for certain applications.
By thoughtfully considering these design principles, engineers can harness the full potential of metal 3D printing to create spacecraft electronics bays that are lighter, stronger, more functional, and faster to produce than those made with traditional methods. Metal3DP‘s expertise in additive manufacturing processes and materials enables us to guide our clients in optimizing their designs for successful 3D printing outcomes. Our advanced printing methods can accommodate intricate geometries and integrated features, leading to superior performance. You can learn more about our printing methods here.
Tolerance, Surface Finish, and Dimensional Accuracy of 3D Printed Electronics Bays – Achieving Precision for Sensitive Electronic Components
In the realm of spacecraft electronics, precision is paramount. The electronics bay must provide accurate mounting surfaces and interfaces for sensitive components to ensure proper functionality and reliable operation in the harsh space environment. Metal 3D printing technologies have made significant strides in achieving tight tolerances, good surface finishes, and high dimensional accuracy.
- Achievable Tolerances: The achievable tolerances in metal 3D printing depend on the specific printing technology (e.g., LPBF, DED, Binder Jetting), the material used, and the part geometry. Typically, tolerances in the range of ±0.1 mm to ±0.05 mm can be achieved for critical dimensions in powder bed fusion processes like those offered by Metal3DP. For features requiring even tighter tolerances, post-processing steps like CNC machining can be employed.
- Surface Finish: The as-printed surface finish in metal 3D printing is generally rougher than that achieved by machining. The surface roughness (Ra) can range from 5 to 20 µm depending on the process parameters and powder size. For applications requiring smoother surfaces, post-processing techniques such as polishing, grinding, or shot peening can be used to achieve the desired finish. For electronics bays, a consistent and controlled surface finish might be necessary for proper thermal contact with cooling elements or for minimizing particle generation in the vacuum of space.
- Dimensional Accuracy: Dimensional accuracy refers to how closely the printed part matches the intended design dimensions. Factors affecting accuracy include material shrinkage during solidification, thermal gradients during printing, and the calibration of the 3D printer. High-quality metal 3D printers, like those offered by Metal3DP, along with optimized process parameters and build orientation, contribute to achieving high dimensional accuracy. Furthermore, design compensation techniques can be used to account for predictable shrinkage.
- Importance for Electronics Bays: Precise tolerances and dimensional accuracy are crucial for:
- Accurate Mounting of Components: Ensuring that electronic units fit correctly and are securely fastened within the bay.
- Proper Thermal Contact: Achieving good contact between heat-generating components and thermal management features like heat sinks or cooling channels.
- Reliable Electrical Connections: Ensuring that connectors and wiring harnesses can be properly integrated.
- Structural Integrity: Maintaining the overall shape and dimensions of the bay under load and thermal stress.
Metal3DP‘s commitment to industry-leading accuracy ensures that our printed parts meet the stringent dimensional requirements of aerospace applications. We understand the critical nature of precision in spacecraft components and employ rigorous quality control measures to deliver parts with the required tolerances and surface finishes. For projects demanding exceptionally tight tolerances or specific surface finish requirements, we can also facilitate post-processing services through our network of trusted partners.
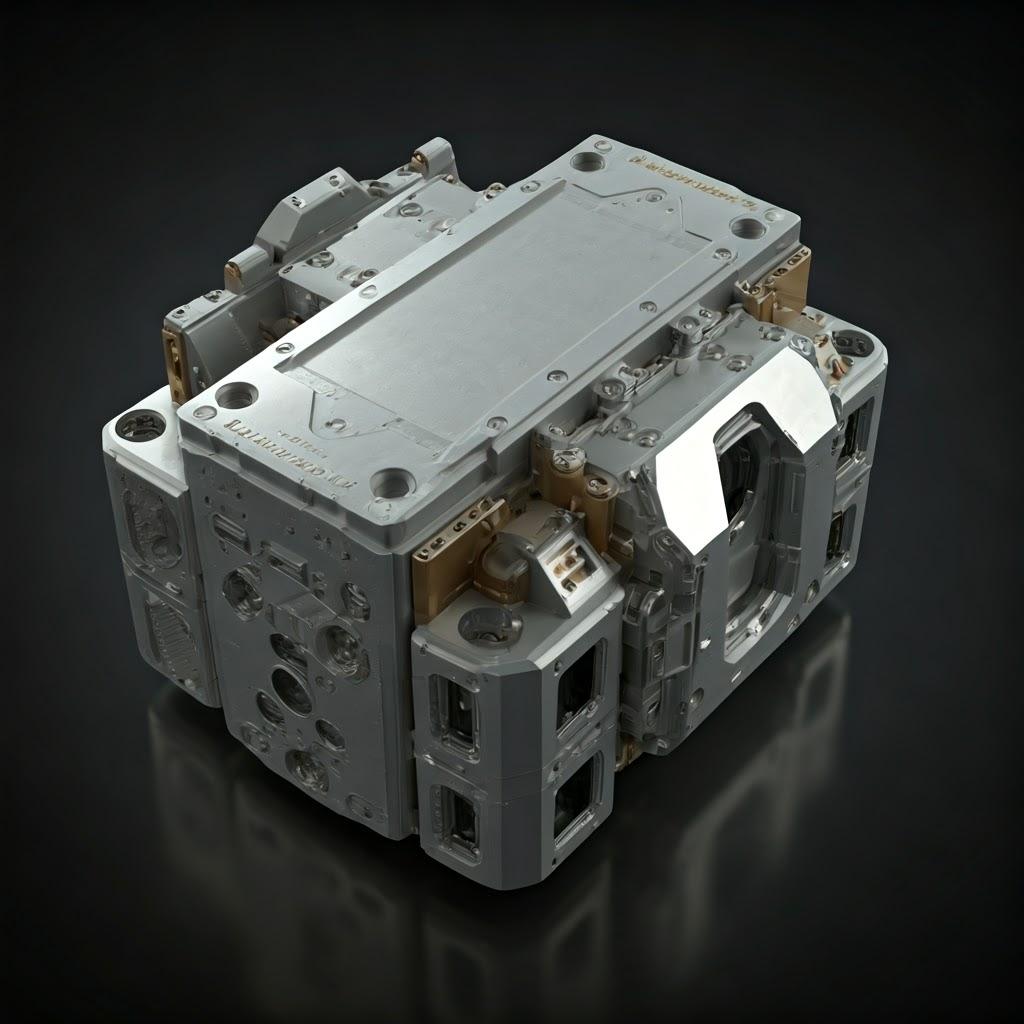
Post-Processing Requirements for Space-Grade Electronics Bays – Ensuring Cleanliness, Surface Integrity, and Protective Coatings
While metal 3D printing offers significant advantages, post-processing is often a necessary step to achieve the final desired properties and surface condition for space-grade electronics bays. The specific requirements depend on the application and the material used.
- Support Structure Removal: Metal 3D printed parts often require support structures to prevent collapse or distortion during the build process. These supports need to be carefully removed without damaging the part’s surface. Techniques include manual removal, machining, or chemical dissolution, depending on the material and support geometry.
- Stress Relief Heat Treatment: To alleviate residual stresses that can build up during the rapid heating and cooling cycles of the 3D printing process, a stress relief heat treatment is often performed. This improves the dimensional stability and mechanical properties of the part.
- Surface Cleaning: Ensuring the cleanliness of components for space applications is critical to prevent outgassing and contamination. This may involve ultrasonic cleaning, vacuum baking, or other specialized cleaning processes to remove any residual powder or contaminants.
- Surface Finishing: As mentioned earlier, post-processing techniques like polishing, grinding, or machining can be used to achieve smoother surface finishes if required for thermal contact, sealing, or other functional reasons.
- Protective Coatings: Depending on the material and the mission environment, protective coatings may be applied to enhance corrosion resistance, provide thermal control (e.g., reflective or emissive coatings), or offer radiation shielding.
- Non-Destructive Testing (NDT): For critical aerospace components, NDT methods like dye penetrant inspection, ultrasonic testing, or X-ray radiography may be employed to ensure the internal integrity and absence of defects in the 3D-printed part.
- Dimensional Inspection: Precise dimensional inspection using coordinate measuring machines (CMMs) or other metrology equipment is essential to verify that the printed part meets the required tolerances.
Metal3DP understands the critical post-processing requirements for space-grade components. We have established processes and partnerships to ensure that parts produced using our metal 3D printing technology can undergo the necessary post-processing steps to meet the stringent demands of the aerospace industry. Our focus on high-quality printing minimizes the need for extensive rework, and we can guide our customers through the appropriate post-processing options for their specific applications.
Common Challenges and How to Avoid Them in 3D Printing Spacecraft Components – Addressing Warping, Outgassing, and Material Integrity
While metal 3D printing offers numerous advantages, there are also potential challenges that need to be addressed to ensure the successful fabrication of high-quality spacecraft components like electronics bays.
- Warping and Distortion: Thermal stresses during the printing process can lead to warping or distortion of the part, especially for complex geometries or large parts.
- How to Avoid: Optimizing part orientation on the build platform, using appropriate support structures, controlling the build chamber temperature, and employing stress relief heat treatments post-printing can mitigate warping. Metal3DP‘s expertise in process parameter optimization helps minimize these issues.
- Porosity and Defects: Inconsistent powder fusion or gas entrapment can lead to porosity or internal defects, which can compromise the mechanical strength and integrity of the part.
- How to Avoid: Using high-quality metal powders with good flowability (like those produced by Metal3DP‘s advanced powder making system), optimizing laser or electron beam parameters, and ensuring a controlled printing environment are crucial for minimizing porosity.
- Outgassing: As mentioned earlier, materials used in space must have low outgassing properties. Residual gases trapped within the printed part or volatile organic compounds on the surface can outgas in the vacuum of space, contaminating sensitive instruments.
- How to Avoid: Selecting materials with inherently low outgassing properties, optimizing printing parameters to minimize porosity, and employing vacuum baking post-printing to remove any trapped gases or surface contaminants are essential.
- Surface Finish Issues: Achieving a smooth surface finish directly from the 3D printing process can be challenging. Rough surfaces can affect thermal contact, sealing, or lead to particle generation.
- How to Avoid: Optimizing printing parameters, using finer powder sizes, and employing appropriate post-processing techniques like polishing or machining can improve surface finish.
- Material Property Consistency: Ensuring consistent material properties throughout the printed part and from one build to another is crucial for reliability.
- How to Avoid: Using high-quality, well-characterized metal powders, maintaining consistent printing parameters, and implementing rigorous quality control measures are essential. Metal3DP‘s focus on advanced powder technology and precise printing processes ensures material property consistency.
- Support Structure Removal Damage: Improper removal of support structures can damage the surface of the printed part.
- How to Avoid: Designing parts with minimal support requirements, using appropriate support removal techniques, and carefully planning the support structure placement can prevent damage.
By understanding these potential challenges and implementing appropriate design strategies, process controls, and post-processing techniques, the aerospace industry can effectively leverage metal 3D printing to produce high-performance and reliable spacecraft electronics bays. Metal3DP is committed to providing the expertise and technology to help our customers overcome these challenges and achieve their additive manufacturing goals.
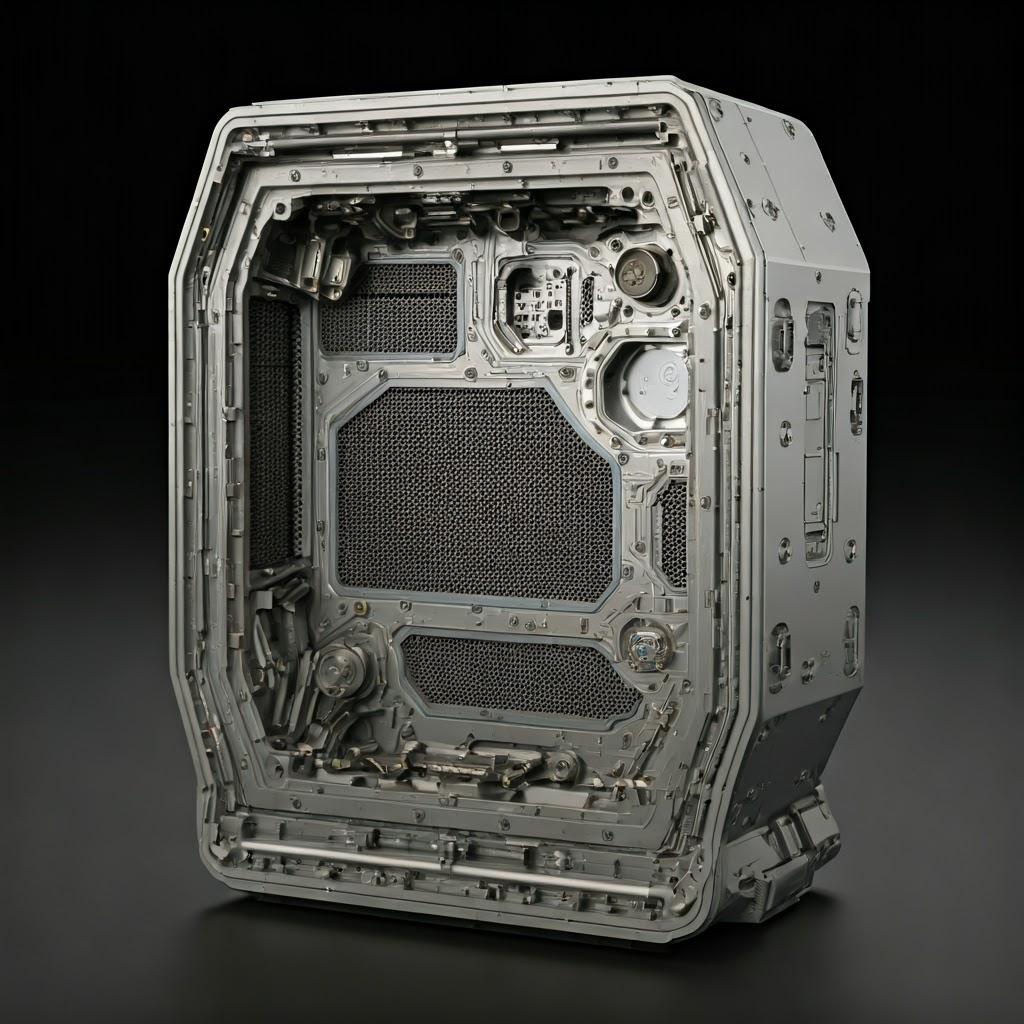
How to Choose the Right Metal 3D Printing Service Provider for Aerospace Applications – Evaluating Expertise, Certifications, and Material Capabilities
Selecting the appropriate metal 3D printing service provider is a critical decision, especially for demanding aerospace applications like spacecraft electronics bays. The chosen partner should possess the expertise, certifications, and capabilities necessary to deliver high-quality, reliable parts that meet stringent industry standards. Here are key factors to consider:
- Aerospace Experience and Certifications: Look for a provider with a proven track record in serving the aerospace industry. Relevant certifications such as AS9100D (Quality Management Systems – Requirements for Aviation, Space, and Defense Organizations) are crucial indicators of their commitment to quality and process control.
- Material Capabilities: Ensure the service provider offers the specific metal powders required for your application, such as AlSi10Mg and Scalmalloy®, and has experience processing these materials for aerospace-grade components. Inquire about their material characterization data and traceability. Metal3DP specializes in a wide range of high-performance metal powders optimized for demanding applications. You can explore our product offerings here.
- Technology and Equipment: Understand the types of metal 3D printing technologies they employ (e.g., LPBF, DED, SEBM). The choice of technology can impact achievable tolerances, surface finish, and build volume. Metal3DP utilizes advanced SEBM printers known for their accuracy and reliability.
- Design and Engineering Support: A strong service provider should offer design consultation and engineering support to optimize your part for additive manufacturing. This includes guidance on topology optimization, lightweighting strategies, and design for assembly. Metal3DP provides comprehensive solutions spanning equipment, materials, and application development services.
- Post-Processing Capabilities: Inquire about their in-house or partnered post-processing services, including support removal, heat treatment, surface finishing, and NDT. Ensure they can meet the specific post-processing requirements for your application.
- Quality Control and Inspection: A robust quality management system with thorough inspection processes is essential. Ask about their dimensional inspection capabilities, material testing procedures, and reporting protocols.
- Build Volume and Capacity: Ensure the provider has the capacity to handle the size and volume of your production needs, both for prototyping and serial manufacturing. Metal3DP‘s printers deliver industry-leading print volume.
- Lead Times and Scalability: Discuss their typical lead times for projects similar to yours and their ability to scale up production if needed.
- Communication and Project Management: Effective communication and transparent project management are crucial for a successful partnership. Assess their responsiveness and their approach to managing complex projects.
By carefully evaluating these factors, you can select a metal 3D printing service provider that aligns with your aerospace application requirements and ensures the delivery of high-quality, reliable spacecraft electronics bays.
Cost Factors and Lead Time for 3D Printed Spacecraft Electronics Bays – Understanding Pricing Structures and Production Timelines
Understanding the cost drivers and typical lead times for 3D printed spacecraft electronics bays is essential for budgeting and project planning. These factors can vary depending on the complexity of the part, the material used, the production volume, and the chosen service provider.
Cost Factors:
- Material Costs: The cost of the metal powder is a significant factor. Specialized aerospace-grade alloys like Scalmalloy® can be more expensive than standard aluminum alloys like AlSi10Mg. The quantity of material used for the part and support structures also contributes to the overall cost. Metal3DP offers a range of high-quality metal powders at competitive prices.
- Build Time: The time it takes to print a part depends on its size, complexity, and the chosen printing technology. Longer build times translate to higher machine operating costs.
- Post-Processing Costs: The extent of post-processing required (e.g., support removal, heat treatment, surface finishing, NDT) will impact the overall cost. Complex post-processing can add significantly to the final price.
- Design and Engineering Costs: If you require design optimization or engineering support from the service provider, these services will be factored into the cost.
- Tooling Costs (vs. Traditional Manufacturing): While metal 3D printing typically eliminates the need for expensive hard tooling, there might be costs associated with build plate preparation or specialized fixtures. However, these are generally lower than traditional tooling costs for complex parts.
- Quantity and Economy of Scale: The cost per part generally decreases as the production volume increases, but metal 3D printing can still be cost-effective for low to medium volumes and highly customized parts where traditional tooling would be prohibitive.
Lead Time:
- Prototyping: Metal 3D printing offers significantly faster lead times for prototypes compared to traditional methods. Complex designs can often be produced in a matter of days or weeks.
- Low-Volume Production: For small production runs or highly customized parts, lead times can be relatively short, depending on the printer availability and the complexity of post-processing.
- High-Volume Production: Scaling up production with metal 3D printing requires careful planning and may involve longer lead times depending on the number of printers available and the efficiency of the overall workflow.
It’s crucial to discuss cost and lead time expectations with your chosen metal 3D printing service provider early in the project. Obtaining detailed quotes that break down the costs for material, printing, and post-processing will help in making informed decisions. Metal3DP is committed to providing transparent and competitive pricing for our metal 3D printing services and high-quality powders. Contact us to explore how our capabilities can power your organization’s additive manufacturing goals.
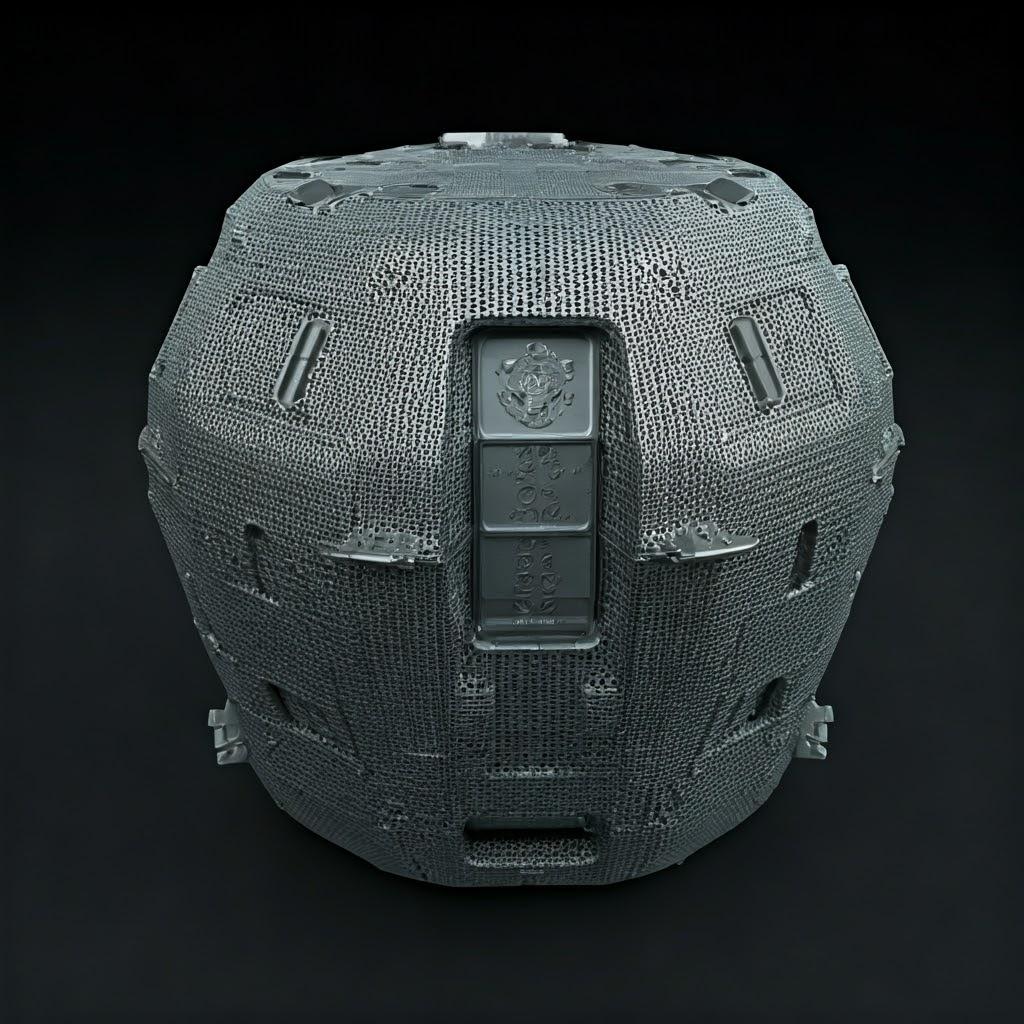
Frequently Asked Questions (FAQ) – Addressing Common Inquiries about 3D Printing Electronics Bays for Space
Here are some frequently asked questions about using metal 3D printing for spacecraft electronics bays:
- Q: Is metal 3D printing strong enough for aerospace applications?
- A: Yes, when the right materials and printing parameters are used, metal 3D printed parts can meet or exceed the strength and durability requirements of aerospace applications. Alloys like AlSi10Mg and Scalmalloy®, processed under controlled conditions, offer excellent mechanical properties.
- Q: What about the reliability of 3D printed electronics bays in the harsh space environment?
- A: Reliability is paramount. By selecting appropriate materials with low outgassing properties, optimizing designs for stress and thermal management, and implementing rigorous quality control and post-processing, 3D printed electronics bays can be highly reliable in space.
- Q: Can metal 3D printing handle the complex geometries required for electronics bays?
- A: Absolutely. One of the key advantages of metal 3D printing is its ability to create intricate geometries, including internal channels, lattice structures, and consolidated parts, which can be challenging or impossible with traditional manufacturing methods.
- Q: What is the typical turnaround time for a 3D printed electronics bay prototype?
- A: Turnaround times for prototypes can vary depending on the size and complexity of the part, but typically range from a few days to a couple of weeks. This is significantly faster than traditional prototyping methods for complex metal parts.
- Q: Is metal 3D printing cost-effective for producing spacecraft electronics bays?
- A: For low to medium volumes, highly customized designs, and parts with complex geometries, metal 3D printing can be very cost-effective by eliminating tooling costs and reducing material waste. As production volumes increase, the cost-effectiveness depends on the specific application and the chosen manufacturing method.
Conclusion – Embracing Metal 3D Printing for Next-Generation Spacecraft Electronics Bay Manufacturing
Metal 3D printing is rapidly transforming the landscape of spacecraft manufacturing, offering unprecedented opportunities for designing and producing high-performance, lightweight, and complex components like electronics bays. The ability to use advanced materials like AlSi10Mg and Scalmalloy®, coupled with the design freedom and rapid prototyping capabilities of additive manufacturing, enables the creation of next-generation spacecraft that are more efficient, reliable, and cost-effective.
Metal3DP is proud to be at the forefront of this revolution, providing cutting-edge metal 3D printing equipment and high-quality metal powders tailored for the demanding needs of the aerospace industry. Our commitment to accuracy, reliability, and innovation empowers organizations to embrace the benefits of metal AM and accelerate their journey towards digital manufacturing. By partnering with Metal3DP, aerospace engineers and procurement managers can unlock new possibilities in spacecraft design and manufacturing, paving the way for future advancements in space exploration and technology. Contact Metal3DP today to explore how our capabilities can power your organization’s additive manufacturing goals and visit our website to learn more about our metal 3D printing solutions.
Share On
MET3DP Technology Co., LTD is a leading provider of additive manufacturing solutions headquartered in Qingdao, China. Our company specializes in 3D printing equipment and high-performance metal powders for industrial applications.
Inquiry to get best price and customized Solution for your business!
Related Articles
About Met3DP
Recent Update
Our Product
CONTACT US
Any questions? Send us message now! We’ll serve your request with a whole team after receiving your message.
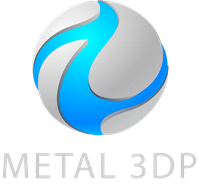
Metal Powders for 3D Printing and Additive Manufacturing