Engine Housing 3D Printing with Aluminum and Titanium
Table of Contents
Introduction: Revolutionizing Engine Housing Manufacturing with Metal 3D Printing
The engine housing, often referred to as the engine block, casing, or crankcase depending on the specific application and industry terminology, stands as a cornerstone component in virtually all internal combustion engines and many other types of power generation and conversion machinery. It serves as the structural foundation, enclosing critical moving parts like pistons, crankshafts, and camshafts, while also providing mounting points for auxiliary systems and managing vital fluids like oil and coolant. Traditionally, manufacturing these complex and robust components has relied heavily on established methods like casting (sand casting, die casting) followed by extensive machining. While effective, these conventional processes often face limitations related to design freedom, weight optimization, lead times for tooling, and the ability to produce highly customized or low-volume batches cost-effectively. The quest for enhanced performance, improved fuel efficiency, reduced emissions, and streamlined supply chains across industries like aerospace, automotive, and industrial manufacturing is driving a paradigm shift towards more advanced production techniques. Enter metal additive manufacturing (AM), commonly known as metal 3D printing. This transformative technology is rapidly moving beyond prototyping into the realm of serial production for demanding applications, offering unprecedented capabilities to reimagine how critical components like engine housings are designed, developed, and manufactured.
Metal 3D printing technologies, such as Selective Laser Melting (SLM), Direct Metal Laser Sintering (DMLS), and Electron Beam Melting (EBM), build parts layer by layer directly from digital CAD models using high-energy sources (lasers or electron beams) to fuse fine metal powders. This additive approach fundamentally differs from subtractive (machining) or formative (casting, forging) methods, unlocking a host of advantages perfectly suited to the challenges of modern engine housing production. Imagine engine housings with intricate internal cooling channels precisely following the contours of heat-generating areas, impossible to achieve through casting or drilling. Picture significantly lighter structures achieved through topology optimization, removing material only where it isn’t structurally necessary, leading to direct fuel savings in vehicles and aircraft. Consider the ability to consolidate multiple components into a single, integrated 3D printed part, reducing assembly time, potential leak paths, and overall system complexity. Furthermore, AM eliminates the need for expensive and time-consuming tooling (molds or dies), making it economically viable for producing customized designs, legacy parts for which tooling no longer exists, or small-to-medium volume production runs. This capability is invaluable for performance tuning, niche vehicle markets, rapid development cycles, and on-demand spare parts management, directly addressing the needs of procurement managers looking for agile and efficient manufacturing solutions.
Companies at the forefront of this technological wave, like Met3dp, are providing the essential building blocks for this manufacturing revolution. Headquartered in Qingdao, China, Met3dp specializes not only in developing and supplying industry-leading metal 3D printing equipment, renowned for print volume, accuracy, and reliability, but also in producing the high-performance metal powders critical for creating dense, high-quality parts. Utilizing advanced powder production techniques like gas atomization and Plasma Rotating Electrode Process (PREP), Met3dp ensures its spherical metal powders exhibit excellent flowability and consistency, leading to superior mechanical properties in the final printed components. Their expertise spans a wide range of materials relevant to engine housings, including aluminum alloys, titanium alloys, and nickel-based superalloys. As engineers and procurement specialists increasingly explore the potential of AM, understanding its application to components like engine housings becomes crucial for maintaining a competitive edge and leveraging the full benefits of next-generation manufacturing. This article delves deep into the world of 3D printed engine housings, exploring their applications, the compelling advantages of using metal AM, recommended materials like AlSi10Mg, Ti-6Al-4V, and IN718, critical design considerations, achievable precision, post-processing needs, potential challenges, supplier selection criteria, cost factors, and frequently asked questions, providing a comprehensive guide for businesses considering this innovative approach.
What are Engine Housings Used For? Key Industries and Functions
The engine housing is far more than just a protective shell; it is a multifunctional, highly stressed component that forms the backbone of an engine or related powertrain/fluid system. Its design and material must meet stringent requirements dictated by the specific application, operating environment, and performance expectations. Understanding the diverse roles and industry applications of engine housings clarifies why optimizing their design and manufacturing process through technologies like metal 3D printing holds such significant potential for B2B suppliers, manufacturers, and end-users.
Core Functions of an Engine Housing:
- Structural Support: Provides the main framework for the engine, supporting the crankshaft, cylinders (or cylinder liners), and often the cylinder head(s). It must withstand significant mechanical loads from combustion pressure, rotating/reciprocating masses, and external vibrations.
- Containment: Encloses the internal moving parts, protecting them from external contaminants (dirt, water) and containing engine fluids (lubricating oil, coolant). Maintaining seal integrity is critical.
- Alignment: Ensures precise alignment of critical components like the crankshaft main bearings and cylinder bores, which is essential for efficient operation, minimizing wear, and ensuring longevity. Tolerances are often very tight.
- Heat Dissipation: Plays a role in managing engine heat, often incorporating water jackets or cooling fins to transfer heat from the combustion chambers and cylinders to the cooling system (liquid or air).
- Fluid Management: Incorporates intricate passages for lubricating oil (galleries, supply lines to bearings) and coolant (water jackets). The design must ensure efficient flow and prevent leaks.
- Mounting Points: Provides secure locations for attaching the engine to the vehicle chassis or equipment frame, as well as mounting points for auxiliary components like the starter motor, alternator, water pump, oil pump, sensors, and transmission/gearbox.
- Noise and Vibration Damping: The mass and stiffness of the housing contribute to damping engine noise and vibration, improving operator comfort and reducing fatigue on surrounding structures.
Key Industries and Specific Applications:
- Automotive:
- Passenger Vehicles: Engine blocks (crankcases) for gasoline and diesel engines, transmission casings, differential housings. The drive for lightweighting to improve fuel economy and performance is paramount. Aluminum alloys (like AlSi10Mg) are common, but AM opens possibilities for optimized designs and potentially higher-performance materials in niche applications. Wholesale supply chains rely on consistent quality and cost-effective production.
- Motorsport: High-performance engine blocks, gearbox housings, dry sump pans. Here, customization, rapid iteration, lightweighting, and maximizing performance through complex internal geometries (oil/coolant passages) are critical. Materials like high-strength aluminum, titanium (Ti-6Al-4V), and sometimes even nickel superalloys (IN718) for turbocharger-adjacent components are considered. AM allows teams to gain a competitive edge through bespoke designs.
- Commercial Vehicles (Trucks, Buses): Larger, robust diesel engine crankcases, transmission housings. Durability, reliability, and cost-effectiveness over long service lives are key. While traditional casting dominates, AM could offer solutions for specialized vehicles or legacy part replacement.
- Aerospace:
- Aircraft Engines (Jet & Turboprop): Gearbox housings, accessory drive housings, bearing housings, structural casings within the engine core. Extreme lightweighting (using Ti-6Al-4V), high operating temperatures (requiring IN718 or similar superalloys), and absolute reliability are non-negotiable. AM enables complex, highly optimized geometries and part consolidation, reducing weight and improving buy-to-fly ratios. Stringent certifications (AS9100) are mandatory for suppliers.
- Space & Launch Vehicles: Rocket engine components, turbopump housings, propellant management system casings. Similar requirements to aircraft engines, but often with even more extreme temperature differentials and pressure demands. AM facilitates rapid development and production of intricate components needed for complex fluid dynamics and structural integrity.
- Industrial Manufacturing & Power Generation:
- Stationary Engines (Generators, Pumps): Crankcases, housings for industrial pumps, compressors, and turbines. Reliability, service life, and often noise reduction are important factors. AM can be used for custom configurations, replacement parts for aging equipment where original tooling is gone, or components with enhanced cooling or durability features.
- Marine Engines: Engine blocks, gearbox housings. Corrosion resistance (especially in saltwater environments) is a major consideration, alongside durability. Specific alloys suited for marine use can be processed via AM.
- Heavy Machinery (Construction, Agriculture): Engine blocks, hydraulic system housings, transmission casings. Robustness and cost-effectiveness are primary drivers. AM might be employed for specialized equipment or optimized replacement parts.
Across these diverse industries, procurement managers and engineers face common challenges: sourcing reliable suppliers, managing inventory for numerous configurations, reducing lead times for both development and production, minimizing weight while maintaining strength, and controlling manufacturing costs. The ability to produce complex engine housings on-demand using metal 3D printing offers a compelling solution to many of these challenges, enabling more agile, efficient, and potentially higher-performing designs tailored to specific industry needs. Met3dp, with its robust printing systems and high-quality powder portfolio including AlSi10Mg, Ti-6Al-4V, and IN718, is well-positioned to partner with businesses across these sectors to realize the benefits of additive manufacturing for critical engine components.
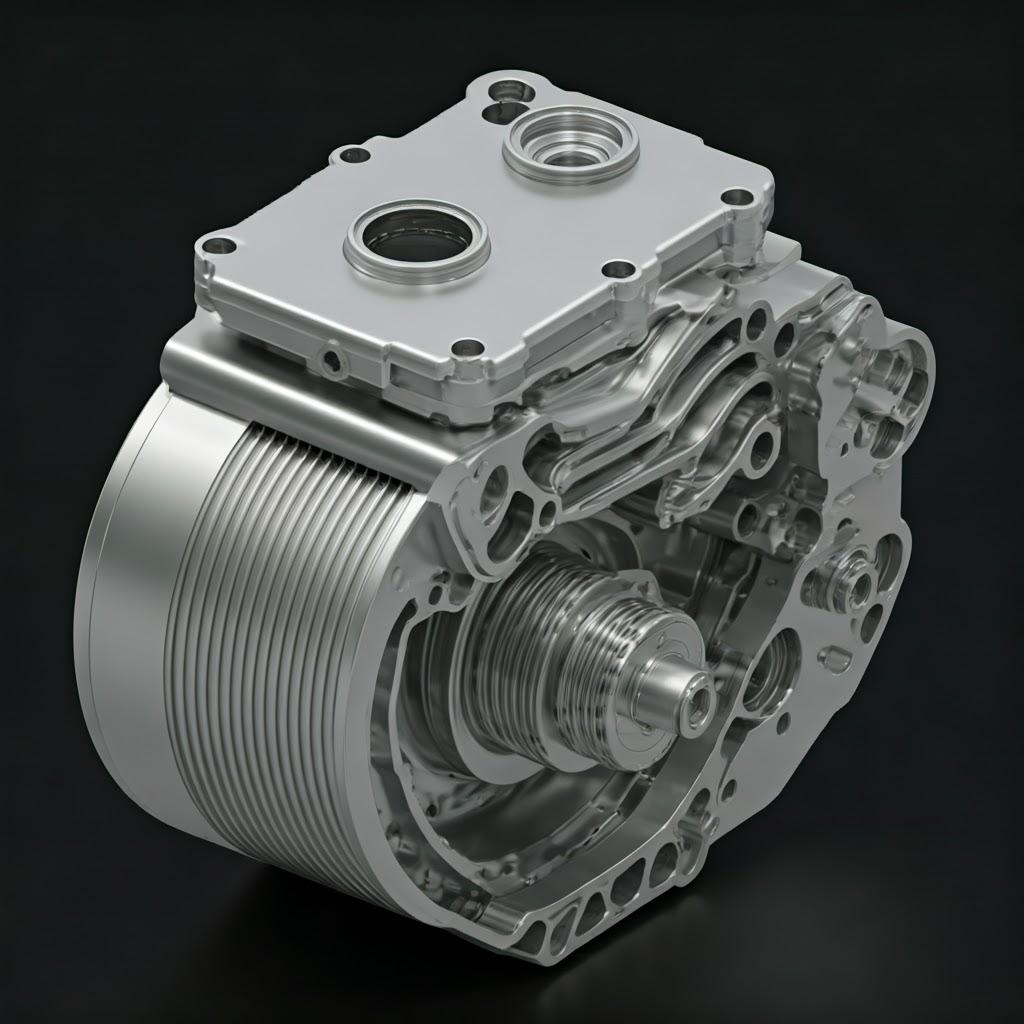
Why Use Metal Additive Manufacturing for Engine Housings? Advantages Over Traditional Methods
While traditional manufacturing methods like casting and machining have served the industry well for decades in producing engine housings, they come with inherent limitations that metal additive manufacturing (AM) can effectively overcome. For engineers striving for innovation and procurement managers focused on efficiency and cost-effectiveness, understanding the distinct advantages of metal AM is key to making informed decisions about future manufacturing strategies. The shift towards AM is not merely about adopting a new technology; it’s about unlocking new levels of performance, design freedom, and supply chain agility that are increasingly critical in competitive global markets.
Limitations of Traditional Manufacturing (Casting & Machining):
- Design Constraints: Casting relies on molds and cores, limiting the complexity of internal features (e.g., undercut channels, intricate lattices). Achieving complex internal geometries often requires multiple cast parts to be assembled or extensive, costly machining.
- Tooling Costs & Lead Times: Creating molds (for casting) or specialized fixtures (for machining) is expensive and time-consuming. This makes low-volume production, prototyping, and design iteration slow and costly. Any design change necessitates tooling modification or replacement.
- Material Waste: Subtractive manufacturing (machining) starts with a larger block of material and removes excess, generating significant scrap (low buy-to-fly ratio), particularly with expensive materials like titanium or superalloys. While casting is more material-efficient initially, subsequent machining still produces waste.
- Weight Optimization Challenges: Achieving optimal lightweighting solely through casting and machining is difficult. Material can only be removed where tools can reach, and casting requires minimum wall thicknesses and draft angles, often leaving non-load-bearing material intact.
- Part Consolidation Difficulty: Complex assemblies often require multiple individual components to be cast, machined, and then joined (welded, bolted), increasing assembly time, weight, potential leak points, and tolerance stack-up issues.
- Supply Chain Complexity: Managing foundries, machine shops, assembly lines, and the associated logistics for traditionally manufactured parts can be complex, especially for global operations or diverse product portfolios. Long lead times associated with tooling and production scheduling can hinder responsiveness.
Advantages of Metal Additive Manufacturing for Engine Housings:
Metal AM addresses many of these limitations head-on, offering compelling benefits for engine housing production:
- Unprecedented Design Freedom:
- Complex Geometries: AM builds parts layer by layer, enabling the creation of highly intricate internal and external features without the constraints of molds or tool access. This allows for:
- Conformal Cooling/Lubrication Channels: Passages can precisely follow complex surfaces or heat-affected zones for vastly improved thermal management or targeted lubrication, impossible to achieve conventionally.
- Internal Lattices & Optimized Structures: Topology optimization software can generate organic, load-path-optimized designs, removing material from non-critical areas and incorporating internal lattice structures for stiffness with minimal weight.
- Benefit: Lighter, more efficient designs, improved performance (better cooling, lubrication), potential for enhanced noise/vibration damping through engineered structures.
- Complex Geometries: AM builds parts layer by layer, enabling the creation of highly intricate internal and external features without the constraints of molds or tool access. This allows for:
- Part Consolidation:
- Reduced Assembly: Multiple components previously manufactured separately and assembled can often be redesigned and printed as a single, monolithic part.
- Benefit: Reduced part count, eliminated assembly steps and costs, fewer potential leak paths or failure points, improved structural integrity, simplified supply chain for procurement managers.
- Significant Lightweighting:
- Topology Optimization: As mentioned, AM allows the practical realization of designs generated by topology optimization, leading to substantial weight reduction (often 20-50% or more) while maintaining or even increasing structural performance.
- Benefit: Improved fuel efficiency (automotive, aerospace), increased payload capacity (aerospace), better handling dynamics (automotive, motorsport), reduced overall system mass.
- Rapid Prototyping & Iteration:
- Tooling-Free Production: Parts are printed directly from CAD data, eliminating the need for molds or dies. Design modifications can be implemented quickly in the digital model and reprinted within days, not weeks or months.
- Benefit: Faster development cycles, reduced R&D costs, ability to test multiple design variants quickly, accelerated time-to-market for new engine designs.
- Customization & Low-Volume Production:
- Economical Small Batches: The absence of tooling costs makes AM economically viable for producing customized engine housings (e.g., for motorsport, specialized equipment) or low-volume runs that wouldn’t justify investment in traditional tooling.
- Benefit: Ability to serve niche markets, offer bespoke solutions, produce legacy parts on demand without maintaining expensive tooling inventory.
- Material Efficiency:
- Near-Net Shape: AM processes typically use only the material needed to build the part and its supports, resulting in significantly less waste compared to subtractive machining, especially important for expensive aerospace-grade alloys like Ti-6Al-4V or IN718. Unfused powder can often be recycled.
- Benefit: Reduced raw material costs, improved sustainability, better buy-to-fly ratios critical for aerospace economics.
- Supply Chain Simplification & Digital Inventory:
- On-Demand Manufacturing: Parts can be produced closer to the point of need when required, reducing reliance on complex global supply chains and large physical inventories. Designs can be stored digitally.
- Benefit: Reduced warehousing costs, minimized inventory obsolescence risk, increased supply chain resilience, faster response to demands for spare parts or custom orders.
Leveraging Met3dp’s Capabilities:
Choosing a partner like Met3dp enhances these advantages. Their focus on both advanced printing systems (like SEBM, known for processing reactive materials and reducing residual stress) and high-quality, spherical metal powders ensures that the theoretical benefits of AM translate into real-world, high-performance engine housings. Met3dp’s industry-leading gas atomization and PREP technologies produce powders with the consistency and purity required for demanding applications in aerospace, automotive, and medical fields, ensuring that the final parts possess the necessary density, mechanical properties, and reliability. Their comprehensive solutions, spanning equipment, materials, and application development services, empower businesses to fully exploit the potential of AM for components like engine housings. While traditional methods remain suitable for high-volume, standardized production, metal AM offers a powerful, complementary, and often superior approach for components demanding high performance, complex designs, lightweighting, and manufacturing agility.
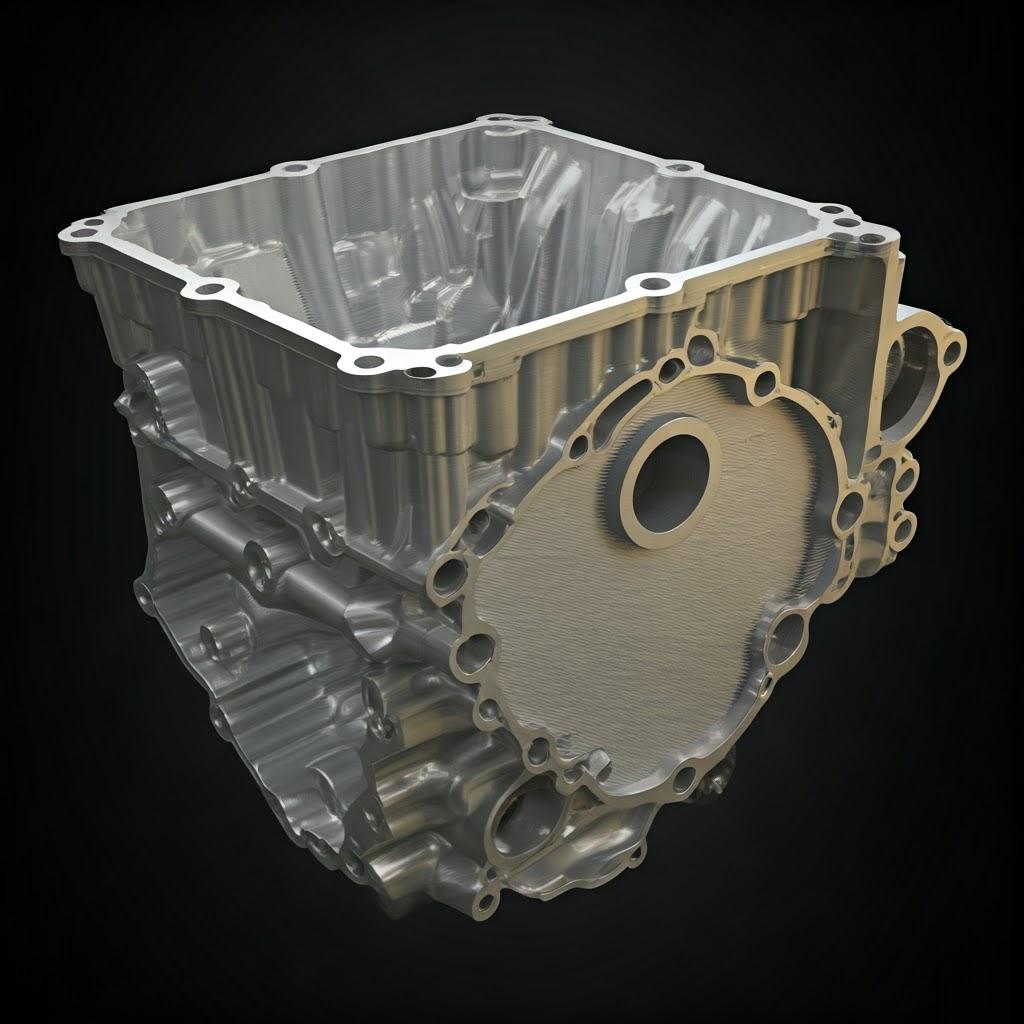
Recommended Materials for 3D Printed Engine Housings: AlSi10Mg, Ti-6Al-4V, IN718
Selecting the right material is fundamental to the success of any engineering component, and 3D printed engine housings are no exception. The choice depends heavily on the specific application requirements, including operating temperature, structural loads, weight targets, environmental conditions (corrosion), and cost constraints. Metal additive manufacturing offers a growing portfolio of materials, but for engine housings, three alloys stand out due to their well-understood properties, processability, and relevance to key industries: Aluminum AlSi10Mg, Titanium Ti-6Al-4V, and Nickel Alloy IN718. Each offers a unique balance of characteristics making them suitable for different types of engine housing applications. Partnering with a knowledgeable metal powder supplier and AM service provider, like Met3dp, who possesses deep expertise in processing these specific materials, is crucial for achieving optimal results. Met3dp not only manufactures these high-quality powders using advanced atomization techniques but also has extensive experience printing them on their advanced SEBM systems, ensuring parts meet stringent quality and performance standards.
1. Aluminum Alloy: AlSi10Mg
- Description: AlSi10Mg is a widely used aluminum alloy in casting and has become one of the most popular choices for metal AM via Laser Powder Bed Fusion (LPBF) processes like SLM/DMLS. It contains silicon (Si) for improved castability (relevant to melt pool behavior in AM) and fluidity, and magnesium (Mg) for precipitation hardening capability through heat treatment.
- Key Properties & Benefits for Engine Housings:
- Lightweight: Aluminum alloys have a low density (approx. 2.68 g/cm³) compared to steels or titanium, making them ideal for automotive and aerospace applications where weight reduction is critical for fuel efficiency and performance.
- Good Strength-to-Weight Ratio: While not as strong as steel or titanium, AlSi10Mg offers a good balance of strength and low weight, sufficient for many engine casing and transmission housing applications, especially after appropriate heat treatment (e.g., T6).
- Excellent Thermal Conductivity: Aluminum alloys dissipate heat effectively, which is advantageous for engine components that need to manage thermal loads.
- Good Corrosion Resistance: Offers adequate resistance to corrosion in typical operating environments.
- Well-Established Processability: It’s one of the most mature alloys for LPBF, with well-defined printing parameters and post-processing protocols (like stress relief and T6 heat treatment).
- Cost-Effective (Relative): Compared to titanium or nickel superalloys, AlSi10Mg powder is significantly less expensive, making it a viable choice for broader automotive and industrial applications.
- Typical Applications: Automotive engine blocks (especially for performance/niche vehicles), transmission casings, oil pans, gearbox housings, covers, brackets, prototyping housings for form/fit/function testing.
- Considerations: Lower high-temperature strength compared to Ti or IN718 (generally suitable up to ~150-200°C depending on load). Requires careful heat treatment to achieve optimal properties. Can be challenging to weld or repair compared to other alloys.
Table: AlSi10Mg Properties Overview (Typical values after T6 Heat Treatment)
Property | Typical Value (LPBF, T6) | Unit | Significance for Engine Housings |
---|---|---|---|
Density | ~2.68 | g/cm³ | Primary driver for lightweighting |
Ultimate Tensile Strength | 430 – 480 | MPa | Indicates resistance to breaking under tension |
Yield Strength | 280 – 350 | MPa | Stress at which permanent deformation begins |
Elongation at Break | 6 – 10 | % | Measure of ductility before fracture |
Modulus of Elasticity | ~70 | GPa | Stiffness, resistance to elastic deformation |
Thermal Conductivity | 120 – 140 | W/(m·K) | Ability to conduct heat away from hot spots |
Max Service Temperature | ~150 – 200 | °C | Approximate limit for maintaining significant strength |
Export to Sheets
2. Titanium Alloy: Ti-6Al-4V (Grade 5)
- Description: Ti-6Al-4V (often called Ti64) is the workhorse of the titanium industry, accounting for over 50% of total titanium usage. It’s an alpha-beta alloy containing aluminum (Al) and vanadium (V), known for its excellent combination of high strength, low density, and outstanding corrosion resistance. It is widely processed using LPBF and Electron Beam Melting (EBM). Met3dp’s expertise with EBM (SEBM – Selective Electron Beam Melting) is particularly relevant, as EBM often produces Ti-6Al-4V parts with lower residual stress compared to LPBF.
- Key Properties & Benefits for Engine Housings:
- Exceptional Strength-to-Weight Ratio: Ti-6Al-4V offers strength comparable to many steels but at roughly 40% lower density (~4.43 g/cm³). This is a major advantage for aerospace engine components and high-performance automotive applications where minimizing mass is paramount.
- High Temperature Capability: Retains good strength at elevated temperatures (up to ~350-400°C), significantly higher than aluminum alloys.
- Excellent Corrosion Resistance: Highly resistant to corrosion from engine fluids, atmospheric conditions, and even saltwater, making it suitable for demanding aerospace and marine environments.
- Biocompatibility: While not typically relevant for engine housings, its biocompatibility highlights its inert nature.
- Good Fatigue Strength: Performs well under cyclic loading conditions common in engines.
- Typical Applications: Aerospace gearbox housings, accessory drive housings, bearing supports, critical engine structural components, high-performance motorsport engine parts (where cost is secondary to performance/weight), components requiring high specific strength.
- Considerations: Significantly higher material cost compared to aluminum or steel. More challenging and costly to machine during post-processing. Reactive nature requires controlled atmosphere (argon) or vacuum (EBM) during printing. Lower thermal conductivity than aluminum.
Table: Ti-6Al-4V Properties Overview (Typical values, Annealed)
Property | Typical Value (LPBF/EBM, Annealed) | Unit | Significance for Engine Housings |
---|---|---|---|
Density | ~4.43 | g/cm³ | Significantly lighter than steel, heavier than aluminum |
Ultimate Tensile Strength | 900 – 1100 | MPa | High strength for demanding structural loads |
Yield Strength | 830 – 1000 | MPa | High resistance to permanent deformation |
Elongation at Break | 10 – 18 | % | Good ductility |
Modulus of Elasticity | ~110 – 115 | GPa | Good stiffness |
Thermal Conductivity | ~6.7 – 7.5 | W/(m·K) | Relatively low, can lead to heat buildup if not managed |
Max Service Temperature | ~350 – 400 | °C | Suitable for moderately high-temperature sections |
Export to Sheets
3. Nickel-Based Superalloy: IN718 (Inconel 718)
- Description: Inconel 718 is a high-strength, corrosion-resistant nickel-chromium superalloy precipitation-hardened with niobium (Nb), molybdenum (Mo), aluminum (Al), and titanium (Ti). It is renowned for its ability to maintain exceptional strength and resist creep rupture at very high temperatures. It’s commonly processed via LPBF and EBM for demanding applications.
- Key Properties & Benefits for Engine Housings:
- Outstanding High-Temperature Strength: Maintains excellent mechanical properties (tensile, creep, rupture strength) at temperatures up to 700°C (1300°F) and usable strength up to ~980°C (1800°F). This is critical for components near combustion zones or exhaust gas paths.
- Excellent Corrosion and Oxidation Resistance: Resists harsh chemical environments and high-temperature oxidation, crucial in aggressive engine operating conditions.
- High Strength: Offers very high tensile, yield, and fatigue strength even at room temperature.
- Good Weldability (Relative to other Superalloys): While still requiring expertise, IN718 is generally considered one of the more weldable nickel superalloys, which can be relevant for post-processing or assembly if needed.
- Typical Applications: Aerospace engine components in hot sections (e.g., turbine casings, exhaust components, heat shields, housings near turbochargers), land-based gas turbine parts, high-temperature industrial applications. Less common for typical automotive engine blocks due to cost and density, but relevant for extreme performance or specific high-heat components.
- Considerations: Highest material cost among the three. Highest density (~8.19 g/cm³), making it heavy unless used strategically where its temperature resistance is essential. Requires careful process control during printing and specific, often complex, multi-stage heat treatments (solution annealing and aging) to achieve optimal properties. Machining is difficult and costly due to its high strength and work-hardening tendency.
Table: IN718 Properties Overview (Typical values, Solution Annealed & Aged)
Property | Typical Value (LPBF/EBM, Aged) | Unit | Significance for Engine Housings |
---|---|---|---|
Density | ~8.19 | g/cm³ | Heaviest of the three; use justified by extreme temperature needs |
Ultimate Tensile Strength | 1250 – 1450 | MPa | Extremely high strength, maintained well at high temperatures |
Yield Strength | 1050 – 1250 | MPa | Very high resistance to yielding, crucial for high-stress parts |
Elongation at Break | 12 – 20 | % | Adequate ductility for a high-strength superalloy |
Modulus of Elasticity | ~200 | GPa | Very stiff material |
Thermal Conductivity | ~11.4 | W/(m·K) | Low thermal conductivity |
Max Service Temperature | ~700 (for high stress) | °C | Excellent performance in very high-temperature engine environments |
Export to Sheets
Choosing the Right Material with Met3dp:
The selection process involves balancing performance requirements against cost and weight.
- For general automotive or industrial housings where weight reduction is important but temperatures are moderate, AlSi10Mg is often the most economical and practical choice.
- For aerospace or high-performance applications demanding significant weight savings and moderate temperature resistance, Ti-6Al-4V is the preferred option despite its higher cost.
- For components exposed to extreme heat, such as those near exhaust systems or within the hot sections of jet engines or turbines, IN718 is indispensable, even with its high density and cost.
Engaging with a partner like Met3dp early in the design process is highly recommended. Their deep knowledge of material science, powder characteristics derived from their advanced manufacturing processes (gas atomization, PREP), and extensive experience with different printing methods (including SEBM optimized for Ti-6Al-4V and potentially IN718) allows them to provide invaluable guidance. They can help engineers and procurement managers evaluate trade-offs, select the optimal powder from their portfolio, and ensure the chosen material is processed correctly to deliver an engine housing that meets or exceeds all performance specifications.
Design for Additive Manufacturing (DfAM): Optimizing Engine Housings for 3D Printing
Simply taking a design intended for casting or machining and directly sending it to a metal 3D printer rarely unlocks the full potential of additive manufacturing. To truly harness the benefits outlined previously – lightweighting, part consolidation, enhanced performance, and cost-efficiency – engineers must embrace Design for Additive Manufacturing (DfAM). DfAM is not just a set of rules; it’s a mindset shift that involves rethinking component design from the ground up, specifically leveraging the unique capabilities and considering the inherent constraints of layer-by-layer fabrication. For complex components like engine housings, applying DfAM principles is crucial for maximizing ROI and achieving superior outcomes compared to traditional methods. Collaborating with experienced AM service providers, such as Met3dp, whose application engineers understand the nuances of DfAM for materials like AlSi10Mg, Ti-6Al-4V, and IN718, can significantly accelerate the learning curve and lead to more successful, optimized designs ready for production.
Key DfAM Principles for Engine Housings:
- Topology Optimization:
- Concept: This is perhaps the most impactful DfAM technique for engine housings. Using specialized software (e.g., Altair Inspire, nTopology, Autodesk Generative Design), engineers define load cases, boundary conditions, design space, and performance targets (e.g., minimize mass, maximize stiffness). The software then iteratively removes material from non-load-bearing areas, generating an organic, highly efficient structure that follows the principal stress paths.
- Application: Dramatically reduce the weight of engine blocks, transmission casings, mounting brackets, and structural supports while maintaining or even increasing stiffness and strength. This directly translates to better fuel economy, improved vehicle dynamics, or increased payload capacity.
- Considerations: Optimized shapes can be highly complex and non-intuitive, often resembling bone structures. They are typically impossible or prohibitively expensive to manufacture traditionally but are well-suited for AM. Requires careful validation through FEA (Finite Element Analysis).
- Lattice Structures & Infill:
- Concept: AM allows for the creation of internal lattice structures – complex networks of interconnected struts or repeating unit cells – within solid volumes. These can be tailored for specific properties like high stiffness-to-weight ratio, energy absorption (vibration damping), or facilitating heat transfer. Different lattice types (e.g., cubic, octet-truss, gyroid) offer different characteristics. Variable density lattices can further optimize material distribution.
- Application: Replace solid sections of the housing with lightweight lattices where high strength is not the primary driver but stiffness or vibration damping is desired. Can also be used to create internal baffling or enhance heat exchange surfaces within fluid passages.
- Considerations: Requires specialized software for generation and simulation. Powder removal from fine lattices can be challenging (discussed later). Structural performance needs thorough validation.
- Part Consolidation:
- Concept: Leverage AM’s ability to create complex geometries to combine multiple, previously separate components into a single, monolithic printed part.
- Application: Integrate brackets, mounting bosses, fluid connectors, or even elements of adjacent systems directly into the main engine housing structure. For example, an oil pan, pump housing, and mounting bracket could potentially be consolidated.
- Benefit: Reduces part count, eliminates fasteners and seals (potential leak points), simplifies assembly, reduces weight, improves structural integrity, and streamlines inventory management for procurement teams.
- Considerations: Requires a holistic view of the system. May increase complexity of the single printed part. Access for inspection or potential repairs needs thought.
- Feature Integration (e.g., Conformal Channels):
- Concept: Design internal channels and passages that precisely follow the contours of surfaces or functional requirements, rather than being restricted to straight lines achievable by drilling or simple cores in casting.
- Application: Create highly efficient conformal cooling channels that closely follow cylinder liners or high-heat zones for superior thermal management. Optimize internal oil galleries for reduced pressure drop and targeted lubrication delivery. Integrate sensor housings or wiring conduits directly within the housing walls.
- Benefit: Improved engine performance, enhanced durability, reduced thermal stress, potential for engine downsizing due to better cooling efficiency.
- Considerations: Internal channel design must consider support requirements and powder removal accessibility. Minimum channel diameter is limited by the AM process resolution and de-powdering capabilities.
- Designing for Minimal Support Structures:
- Concept: Powder bed fusion processes (LPBF, EBM) require support structures for overhanging features (typically below 45 degrees from horizontal) and to anchor the part to the build plate, managing thermal stress. These supports consume extra material, add print time, and require removal in post-processing, which can be labor-intensive and potentially damage the part surface. DfAM aims to minimize the need for supports where possible.
- Application: Orient the part strategically on the build plate. Design gradual transitions and chamfers/fillets instead of sharp overhangs. Utilize self-supporting angles (often >45 degrees). Incorporate sacrificial ribs or features that can be easily machined away if supports are unavoidable in critical areas. Design internal channels with diamond or teardrop cross-sections instead of circular to make them self-supporting.
- Benefit: Reduced print time and cost, less post-processing labor, minimized risk of surface damage during support removal, easier powder removal from internal cavities.
- Considerations: Achieving completely support-free designs is often difficult for complex housings. Requires understanding the specific process limitations (e.g., minimum feature size, achievable overhang angles for the chosen material and machine).
- Wall Thickness and Feature Size:
- Concept: AM processes have limitations on minimum achievable wall thickness and feature resolution (e.g., small holes, thin ribs). Designing below these limits can lead to print failures or parts lacking structural integrity. Conversely, excessively thick sections can increase thermal stress, print time, and material consumption.
- Application: Adhere to recommended minimum wall thicknesses (often 0.4-1.0 mm depending on process and material, but may need to be thicker for structural integrity). Avoid large, solid masses where possible; consider shelling and infill (lattices). Ensure features like small holes or fine details are within the process resolution.
- Considerations: Guidelines vary by machine, material, and specific feature geometry. Consult with the AM provider (like Met3dp) for specific recommendations based on their equipment and experience.
- Considering Post-Processing:
- Concept: Design with downstream processes in mind. If surfaces require high precision or specific finishes, ensure they are accessible for machining or polishing. If internal channels need thorough cleaning, include access ports for powder removal and flushing.
- Application: Add extra stock material (machining allowance) on surfaces that will be CNC machined to final tolerance. Design robust features for clamping during machining. Ensure internal channels have adequate inlet/outlet ports for de-powdering. Avoid overly complex internal geometries that trap powder permanently.
- Benefit: Streamlined post-processing workflow, reduced risk of damage, ensures final part meets all specifications.
By integrating these DfAM principles, engineers can move beyond simply replicating existing designs and start creating truly optimized engine housings that leverage the unique advantages of metal AM. This requires a collaborative approach between the design team and the manufacturing partner to ensure feasibility, efficiency, and quality throughout the entire process, from initial concept to final product.
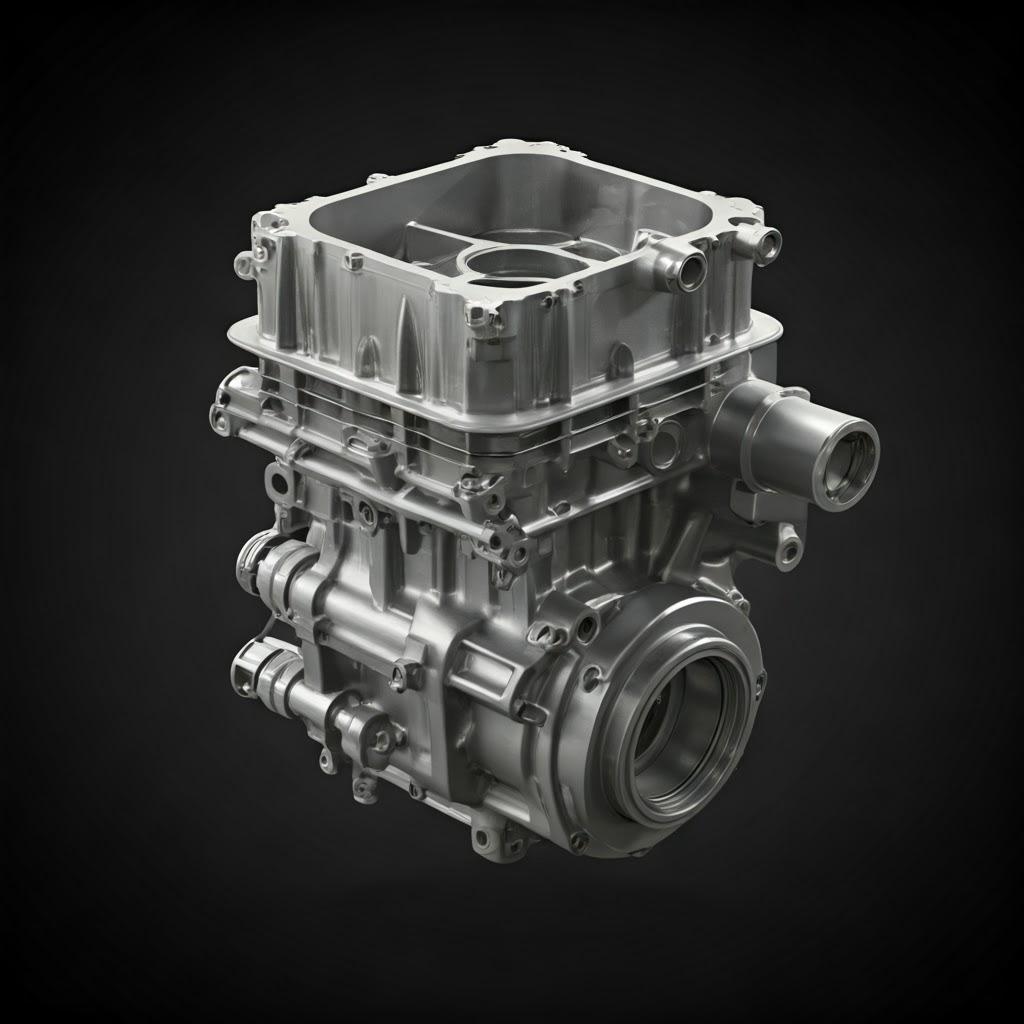
Achievable Precision: Tolerance, Surface Finish, and Dimensional Accuracy in Metal AM
Engine housings often have critical features requiring tight tolerances, specific surface finishes, and high overall dimensional accuracy to ensure proper assembly, sealing, and function. Procurement managers and engineers evaluating metal additive manufacturing need realistic expectations about the precision achievable directly from the printer (“as-built”) and what typically requires post-processing steps like machining. While metal AM technology has advanced significantly, it’s generally not a direct replacement for high-precision machining in terms of achievable tolerances and surface smoothness straight off the build plate. However, it provides an excellent near-net shape starting point, significantly reducing subsequent machining efforts compared to starting from a raw casting or billet. The achievable precision depends on several factors, including the specific AM process (LPBF vs. EBM), the machine quality and calibration, the material being used (AlSi10Mg, Ti-6Al-4V, IN718 behave differently), part size and geometry, and build orientation.
Dimensional Accuracy & Tolerances:
- General Expectations: As a rule of thumb, well-calibrated industrial metal AM systems (LPBF/EBM) can often achieve dimensional accuracies in the range of ±0.1 mm to ±0.3 mm or ±0.1% to ±0.2% of the nominal dimension, whichever is greater, for moderately sized parts. Smaller features might hold tighter tolerances locally.
- LPBF (SLM/DMLS): Generally capable of finer feature resolution and potentially slightly better accuracy on smaller details compared to EBM due to smaller beam spot size and thinner layers.
- EBM (like Met3dp’s SEBM): Operates at higher temperatures in a vacuum, which significantly reduces residual stress build-up during the print. This can lead to better overall dimensional stability and less distortion, especially for larger or complex parts made from crack-sensitive or high-stress materials like Ti-6Al-4V or certain nickel alloys. However, the minimum feature size and as-built surface roughness are typically larger than LPBF.
- Factors Influencing Accuracy:
- Machine Calibration: Regular calibration of the scanner system, laser/electron beam focus, and build platform is crucial. High-quality machine providers ensure robust calibration procedures.
- Thermal Effects: The repeated heating and cooling cycles inherent to AM cause expansion and contraction, leading to potential stress build-up and warping/distortion, especially in large or geometrically complex parts. EBM’s hot process mitigates this significantly. Stress relief heat treatment post-build is critical for LPBF parts.
- Material Properties: Each material (AlSi10Mg, Ti-6Al-4V, IN718) has different thermal conductivity, expansion coefficients, and melt pool behavior, influencing final accuracy.
- Part Geometry & Size: Large, flat surfaces are more prone to warping. Tall, thin features can be less stable. Complex internal structures can introduce localized stresses.
- Support Structures: Properly designed supports help anchor the part and manage thermal stress, improving accuracy. Poor support strategy can lead to deformation.
- Build Orientation: How the part is oriented on the build plate affects support needs, thermal gradients, and potentially the accuracy of specific features due to the anisotropic nature of layer-wise building.
- Achieving Tight Tolerances: For critical features like bearing bores, cylinder liner interfaces, mating surfaces, or threaded holes requiring tolerances tighter than the general AM capability (e.g., sub-±0.05 mm), post-process CNC machining is invariably required. DfAM principles should incorporate adding machining stock (e.g., 0.5 – 1.5 mm) to these specific features in the CAD model.
Surface Finish (Roughness):
- As-Built Surface: The surface finish of as-built metal AM parts is inherently rougher than machined surfaces. It’s influenced by powder particle size, layer thickness, beam parameters, and surface orientation.
- LPBF: Typically produces surface roughness (Ra) values ranging from 6 µm to 20 µm, depending on the angle of the surface relative to the build direction (upward-facing and vertical surfaces are generally smoother than downward-facing surfaces reliant on supports).
- EBM: Due to larger powder particles and higher energy input, EBM generally results in rougher surfaces, often with Ra values ranging from 20 µm to 40 µm or higher.
- Significance for Engine Housings:
- Flow Paths: Rough internal surfaces in coolant or oil passages can increase pressure drop and potentially affect flow efficiency.
- Sealing Surfaces: As-built surfaces are usually unsuitable for critical sealing (e.g., gasket interfaces); they require machining or specialized coatings.
- Fatigue Life: Surface roughness can act as initiation sites for fatigue cracks. For dynamically loaded housings, improving surface finish in critical areas through polishing or machining is often necessary.
- Improving Surface Finish: Various post-processing techniques can significantly improve the as-built surface finish:
- Abrasive Blasting (Bead Blasting, Sand Blasting): Provides a uniform matte finish, removes loose powder, and can slightly improve Ra (e.g., down to 5-10 µm Ra depending on starting point and media).
- Tumbling/Vibratory Finishing: Uses abrasive media in a tumbling barrel or vibratory bowl to smooth surfaces and deburr edges, effective for batches of smaller parts or achieving general smoothness.
- CNC Machining: Provides the best control over surface finish for specific features, easily achieving Ra values below 1.6 µm or even lower (mirror polish).
- Polishing (Manual or Automated): Can achieve very smooth, mirror-like finishes (Ra < 0.1 µm) but is often labor-intensive and typically reserved for specific functional requirements or aesthetics.
- Electrochemical Polishing: Can smooth complex geometries but requires specific electrolytes and setup.
Met3dp’s Role in Precision:
Achieving the required precision consistently demands robust process control. Met3dp, with its focus on high-quality, spherical metal powders produced via advanced atomization, coupled with their industry-leading printing equipment known for accuracy and reliability, provides a strong foundation. Their understanding of material-process interactions for alloys like AlSi10Mg, Ti-6Al-4V, and IN718 allows them to optimize build parameters and recommend appropriate post-processing strategies (including leveraging the unique aspects of different printing methods like SEBM) to meet the specific tolerance and surface finish requirements outlined by engineering blueprints for demanding engine housing applications. Engaging with them early allows for realistic assessment of what can be achieved as-built versus what will necessitate secondary operations, ensuring efficient planning and costing for procurement.
Essential Post-Processing Steps for 3D Printed Engine Housings
Unlike parts produced by net-shape processes like die casting or injection molding, metal additive manufactured components almost always require several post-processing steps to transform them from the raw, as-built state into a functional, finished engine housing ready for assembly. These steps are crucial for achieving the required mechanical properties, dimensional accuracy, surface characteristics, and overall quality and reliability. Understanding this workflow is vital for engineers designing the parts and for procurement managers budgeting for time and cost. The specific sequence and necessity of each step depend on the AM technology used (LPBF vs. EBM), the material (AlSi10Mg, Ti-6Al-4V, IN718 have different needs), the complexity of the part, and the final application requirements. Partnering with a full-service provider or coordinating with specialized subcontractors is often necessary.
Typical Post-Processing Workflow for Metal AM Engine Housings:
- De-Powdering:
- Objective: Remove as much unfused metal powder as possible from the part, especially from internal channels and complex geometries.
- Methods: Manual brushing, compressed air blowing, vacuuming, automated de-powdering stations involving vibration or rotation. For complex internal channels, careful design (access ports, smooth pathways) and dedicated procedures are essential. Sometimes ultrasonic cleaning in a solvent bath is used.
- Importance: Residual powder can compromise functionality (block passages), add weight, and interfere with subsequent steps like heat treatment or HIP. Incomplete powder removal is a significant quality concern.
- Stress Relief Heat Treatment:
- Objective: Reduce the high residual stresses induced during the rapid heating and cooling cycles of the printing process, particularly critical for LPBF parts. These stresses can cause distortion or cracking during printing, after removal from the build plate, or during subsequent machining.
- Methods: Heating the part (often while still attached to the build plate) in a controlled atmosphere furnace (e.g., Argon, vacuum) to a specific temperature below the material’s aging or annealing temperature, holding it for a defined time, and then cooling slowly. Parameters vary significantly by material (e.g., AlSi10Mg ~300°C, Ti-6Al-4V ~650-800°C, IN718 ~980-1065°C for homogenization/stress relief, though specific cycles vary).
- Importance: Essential for dimensional stability, preventing cracking, and enabling safe removal from the build plate and subsequent machining. EBM parts generally have much lower residual stress due to the hot process, but a stress relief cycle may still be beneficial depending on the alloy and geometry.
- Removal from Build Plate:
- Objective: Separate the printed engine housing(s) from the metal build plate they were fused to during printing.
- Methods: Typically done using wire EDM (Electrical Discharge Machining) or a bandsaw. Care must be taken not to damage the parts.
- Importance: A necessary step to liberate the parts for further processing.
- Support Structure Removal:
- Objective: Remove the temporary support structures required during the build process.
- Methods: Can range from simple manual breaking (for easily accessible, light supports) to cutting with hand tools, CNC machining, or sometimes wire EDM for delicate or hard-to-reach supports.
- Importance: Supports are non-functional and must be removed. This step can be labor-intensive and requires skill to avoid damaging the part surface, especially on complex housings with internal supports. DfAM strategies aim to minimize supports.
- Hot Isostatic Pressing (HIP) – Optional but often Recommended:
- Objective: Eliminate internal porosity (small voids) that can sometimes remain after the AM process, improving mechanical properties like fatigue strength, fracture toughness, and ductility.
- Methods: Subjecting the part to high temperature (below melting point) and high inert gas pressure (typically Argon, ~100-200 MPa) simultaneously in a specialized HIP vessel. The pressure collapses internal voids, diffusion bonding the material across the void interfaces.
- Importance: Crucial for critical, fatigue-sensitive components common in aerospace and high-performance automotive engine applications. Significantly improves material consistency and reliability. Often specified for Ti-6Al-4V and IN718 parts in demanding roles. It can also improve the properties of AlSi10Mg.
- Solution Annealing & Aging Heat Treatment (Properties Development):
- Objective: Develop the final desired microstructure and mechanical properties (strength, hardness, ductility) of the alloy. This is distinct from stress relief.
- Methods: Involves specific multi-stage heat treatment cycles tailored to the alloy.
- AlSi10Mg: Typically a T6 cycle (Solution treatment around 500-540°C, quench, then artificial aging around 150-170°C) to achieve precipitation hardening.
- Ti-6Al-4V: Often annealed (e.g., ~700-850°C, cool) for improved ductility and stability, or potentially solution treated and aged (STA) for higher strength. Specific cycles depend on whether LPBF or EBM was used and the desired property balance.
- IN718: Requires a complex cycle, typically solution treatment (~950-980°C) followed by a two-step aging process (~720°C then ~620°C) to precipitate strengthening phases (gamma prime and gamma double-prime).
- Importance: Absolutely essential to achieve the target mechanical specifications listed in material datasheets. Without proper heat treatment, the as-built or stress-relieved material will not have optimal strength or performance.
- CNC Machining:
- Objective: Achieve tight tolerances, precise geometries, and smooth surface finishes on critical features that cannot be met by the as-built AM process.
- Methods: Using standard CNC milling, turning, drilling, tapping, and grinding operations. Requires careful fixture design to hold the complex AM part securely without distortion.
- Importance: Necessary for mating surfaces, bearing bores, cylinder deck flatness, seal grooves, threaded holes, and any feature requiring high precision for assembly and function.
- Surface Finishing & Cleaning:
- Objective: Achieve the final desired surface texture, clean the part thoroughly, and potentially apply protective or functional coatings.
- Methods: As discussed previously (blasting, tumbling, polishing). Followed by thorough cleaning and inspection to ensure no contaminants, machining chips, or residual powder remain, especially in internal passages. Surface coatings (e.g., anodizing for aluminum, specialized wear-resistant or thermal barrier coatings) may be applied depending on the application.
- Importance: Impacts aesthetics, corrosion resistance, wear resistance, fatigue life, and fluid dynamics within passages. Final cleaning is critical for engine internals.
Integrated Approach:
Managing this multi-step workflow requires expertise and coordination. Companies like Met3dp, while specializing in printers and powders, understand this entire value chain and can often advise on or help manage these post-processing steps through partnerships, ensuring that the final engine housing meets all specifications. Procurement managers should factor the cost and lead time associated with these essential steps into their overall project planning when considering metal AM.
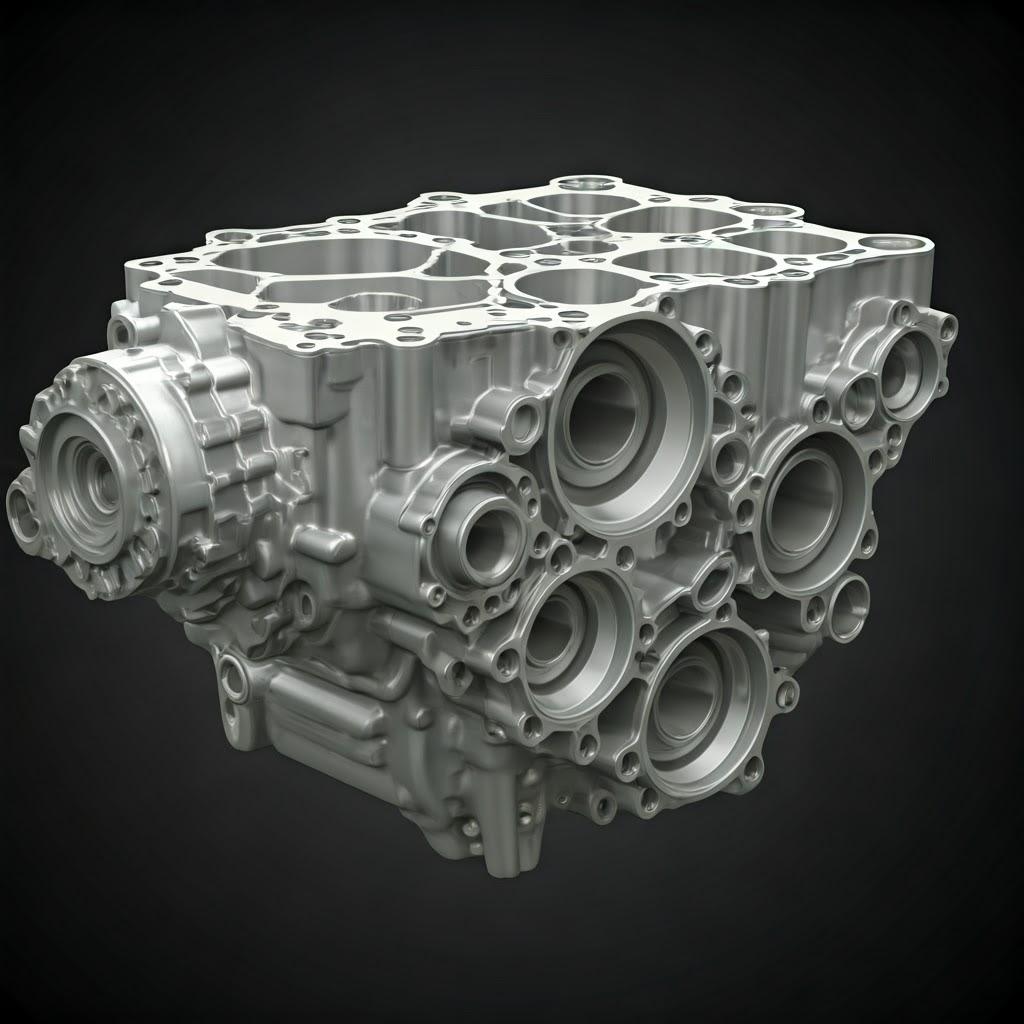
Common Challenges in 3D Printing Engine Housings and Mitigation Strategies
While metal additive manufacturing offers transformative potential for engine housings, it’s not without its challenges. Engineers, operators, and procurement managers should be aware of potential issues that can arise during the printing and post-processing phases. Understanding these challenges allows for proactive mitigation through careful design (DfAM), rigorous process control, appropriate material selection, and leveraging the expertise of experienced AM providers like Met3dp. Successfully navigating these hurdles is key to realizing the quality, performance, and cost benefits of AM technology.
Common Challenges & Mitigation Strategies:
- Residual Stress, Warping, and Cracking:
- Challenge: The intense, localized heating and rapid cooling inherent in powder bed fusion processes (especially LPBF) generate significant thermal gradients, leading to internal stresses within the part. These stresses can cause warping (distortion from the intended geometry), detachment from the build plate, or even cracking, particularly in large parts, complex geometries, or materials prone to hot cracking (like some aluminum alloys or nickel superalloys if not processed correctly).
- Mitigation Strategies:
- Process Selection: Electron Beam Melting (EBM/SEBM), which operates at elevated temperatures within a vacuum (e.g., >600°C for Ti-6Al-4V), significantly reduces thermal gradients and residual stress compared to LPBF, making it advantageous for large titanium or stress-sensitive parts. Met3dp’s focus on SEBM technology directly addresses this challenge for relevant materials.
- Optimized Build Parameters: Fine-tuning laser/electron beam power, scan speed, scan strategy (e.g., island scanning, layer rotation), and layer thickness can minimize stress accumulation.
- Build Plate Heating (LPBF): Pre-heating the build plate (up to 200°C or sometimes higher for specific materials) reduces the temperature difference between the solidified material and the surrounding powder bed/plate, lowering stress.
- Smart Support Strategy: Well-designed support structures act as heat sinks and anchors, helping to manage thermal stresses and prevent warping. Software simulation can help optimize support placement.
- DfAM: Designing parts with gradual transitions, avoiding large solid blocks, and incorporating stress-relieving features can help.
- Immediate Post-Build Stress Relief: Performing a stress relief heat treatment cycle before removing the part from the build plate is crucial for LPBF parts to prevent distortion or cracking upon release.
- Support Structure Removal Difficulties:
- Challenge: While necessary, support structures add cost (material, time) and require removal. Removing supports from internal channels, intricate geometries, or delicate features without damaging the part surface can be very difficult, time-consuming, and costly. Inaccessible internal supports might be impossible to remove completely.
- Mitigation Strategies:
- DfAM for Self-Support: Prioritize designing parts with self-supporting angles (>45° generally, but material/machine specific), using features like chamfers and fillets, and choosing optimal build orientation. Design internal channels with teardrop or diamond shapes.
- Optimized Support Design: Use support generation software to create supports that are strong enough during the build but easier to remove (e.g., smaller contact points, perforated structures). Specialized support types (e.g., tree supports) can improve accessibility.
- Accessibility Planning: Ensure designs allow physical or tool access for support removal. If internal supports are unavoidable, design requires careful consideration of how they will be removed (e.g., chemical etching – rare for these structural metals, machining access).
- Process Choice: Some processes might require fewer supports for certain geometries (e.g., EBM sometimes requires fewer supports than LPBF due to powder sintering).
- Powder Removal from Internal Channels:
- Challenge: Engine housings often contain complex internal passages for coolant or lubricant. Ensuring all unfused metal powder is removed from these channels after printing is critical for functionality but can be extremely challenging, especially for long, narrow, or tortuous paths. Trapped powder can block flow or dislodge during operation, causing catastrophic engine failure.
- Mitigation Strategies:
- DfAM for De-Powdering: Design internal channels with smooth transitions, avoid sharp corners or dead ends where powder can collect. Ensure adequate inlet and outlet ports (potentially larger than functionally required and plugged/machined later) to allow powder evacuation and inspection access. Consider minimum channel diameters based on powder particle size and de-powdering capabilities (often >1-2 mm needed).
- Optimized Orientation: Orient the part on the build plate to facilitate gravity-assisted powder drainage.
- Effective De-Powdering Procedures: Utilize multi-axis rotation/vibration stations, targeted compressed air/inert gas jets, potentially ultrasonic cleaning in appropriate fluids.
- Inspection: Employ non-destructive methods like CT scanning (Computed Tomography) or borescopic inspection to verify complete powder removal in critical passages.
- Porosity and Material Defects:
- Challenge: Incomplete fusion between layers or gas entrapment during melting can lead to microscopic voids (porosity) within the printed material. High porosity degrades mechanical properties, particularly fatigue strength and fracture toughness. Other defects like inclusions (from contaminated powder) or lack-of-fusion zones can also occur.
- Mitigation Strategies:
- High-Quality Powder: Using high-purity, spherical powder with consistent particle size distribution and good flowability is paramount. Met3dp’s advanced gas atomization and PREP processes are designed to produce such powders, minimizing gas porosity inherent in the raw material. Careful powder handling and recycling protocols are also crucial to prevent contamination.
- Optimized Process Parameters: Developing and strictly controlling optimized parameters (beam power, speed, focus, layer thickness, atmosphere control) for each specific material and machine combination is key to achieving dense (>99.5%, often >99.9%) parts.
- Hot Isostatic Pressing (HIP): As mentioned in post-processing, HIP is highly effective at closing internal gas porosity and improving density and mechanical properties. It’s often a standard requirement for critical aerospace and medical AM parts.
- Quality Control & NDT: Implementing rigorous quality control, including powder analysis, melt pool monitoring (where available), and non-destructive testing (NDT) like CT scanning or ultrasonic testing on finished parts, helps detect and prevent defects.
- Cost and Lead Time:
- Challenge: While offering long-term benefits, the initial cost per part for metal AM can be higher than traditional methods, especially for larger components or higher volumes, due to expensive machines, materials, and extensive post-processing. Lead times can also be longer than expected if the entire workflow isn’t efficiently managed.
- Mitigation Strategies:
- Design Optimization (DfAM): Maximizing lightweighting, part consolidation, and designing for minimal supports/post-processing directly reduces material consumption, print time, and labor costs.
- Nesting & Build Optimization: Printing multiple parts simultaneously on a single build plate (nesting) improves machine utilization and reduces cost per part.
- Targeted Application Selection: Focus AM on applications where its unique benefits (complexity, lightweighting, customization, consolidation) provide the highest value proposition, rather than trying to replace cost-effective traditional methods for simple, high-volume parts.
- Partnering with Experienced Providers: Working with efficient, experienced service providers like Met3dp who have optimized workflows and understand cost drivers can help manage expenses and ensure realistic lead time estimates. Open communication with procurement teams regarding cost breakdowns is vital.
By acknowledging these challenges and implementing robust mitigation strategies grounded in sound DfAM principles, meticulous process control, and strong partnerships, manufacturers can confidently leverage metal additive manufacturing to produce high-quality, high-performance engine housings for the demanding requirements of the aerospace, automotive, and industrial sectors.
Choosing Your Metal 3D Printing Partner: Evaluating Service Providers and Suppliers
Successfully implementing metal additive manufacturing for critical components like engine housings requires more than just access to a printer; it demands a strategic partnership with a capable and reliable service provider or supplier. The right partner acts as an extension of your engineering and procurement teams, offering technical expertise, robust processes, consistent quality, and reliable delivery. For B2B buyers, wholesale distributors, and procurement managers navigating the growing landscape of AM providers, evaluating potential partners based on a defined set of criteria is essential to mitigate risks and ensure project success. Choosing wisely means looking beyond just the quoted price to assess the provider’s overall capabilities, quality systems, and suitability for your specific industry and application needs.
Key Criteria for Evaluating Metal AM Partners:
- Technical Expertise & Application Support:
- Assessment: Does the provider possess deep knowledge of the specific AM process (LPBF, EBM/SEBM), materials (AlSi10Mg, Ti-6Al-4V, IN718), and their associated behaviors? Do they offer Design for Additive Manufacturing (DfAM) support to help optimize your engine housing design for printability, performance, and cost-effectiveness? Can they advise on material selection trade-offs? Do they have engineers experienced in your industry (aerospace, automotive, industrial)?
- Why it Matters: Engine housings are complex components. A partner with strong technical depth can help avoid costly design errors, optimize performance, troubleshoot issues, and ensure the part meets functional requirements. Providers like Met3dp, with decades of collective expertise in metal AM spanning materials science, process engineering, and application development, offer significant value here.
- Machine Park & Technology:
- Assessment: What types and brands of metal AM systems do they operate? Do they have the right technology (e.g., LPBF for fine features, EBM/SEBM for low-stress titanium parts) for your specific housing needs? What is their machine capacity (build volume, number of machines) to handle your project size and potential production volumes? Are their machines well-maintained and calibrated?
- Why it Matters: The specific technology impacts achievable features, tolerances, surface finish, and material properties. Sufficient capacity ensures reasonable lead times and scalability. Providers investing in industry-leading equipment, like Met3dp’s focus on systems delivering high print volume, accuracy, and reliability, demonstrate a commitment to quality production.
- Material Portfolio & Powder Quality Control:
- Assessment: Does the provider offer the specific alloys required for your engine housing (e.g., AlSi10Mg, Ti-6Al-4V, IN718)? Crucially, what are their processes for sourcing, handling, storing, and recycling metal powders? Do they have robust quality control for incoming powder (e.g., chemistry analysis, particle size distribution, morphology, flowability)? Can they provide material certifications and traceability?
- Why it Matters: The quality of the final printed part is fundamentally dependent on the quality of the powder feedstock. Inconsistent or contaminated powder leads to defects and poor mechanical properties. Companies like Met3dp, which manufacture their own high-performance metal powders using advanced techniques like gas atomization and PREP, offer superior control over powder quality and consistency, providing greater assurance for critical applications.
- Quality Management System & Certifications:
- Assessment: Does the provider operate under a certified Quality Management System (QMS)? Essential certifications include ISO 9001 (general quality management). For aerospace applications, AS9100 is typically mandatory. For medical, ISO 13485 might be relevant (though less so for engine housings). Are they open to audits? What are their internal quality control procedures during and after the build?
- Why it Matters: Certifications demonstrate a commitment to standardized processes, traceability, and continuous improvement, providing confidence in the reliability and repeatability of their manufacturing operations. This is non-negotiable for safety-critical components and essential for regulated industries.
- Post-Processing Capabilities:
- Assessment: Does the provider offer necessary post-processing steps in-house (e.g., heat treatment, support removal, basic finishing) or manage them through a qualified network of partners (e.g., HIP, CNC machining, NDT, advanced coating)? How seamless is this integration?
- Why it Matters: Engine housings require multiple post-processing steps. A partner who can manage this entire workflow simplifies the supply chain for the procurement team and ensures accountability throughout the process. Understanding which steps are performed in-house versus outsourced is important for assessing control and potential lead time impacts.
- Track Record & Case Studies:
- Assessment: Can the provider demonstrate successful past projects, particularly with components similar in complexity, material, or industry to your engine housing? Are they willing to share case studies or references (within confidentiality limits)?
- Why it Matters: Proven experience reduces risk. Seeing evidence of successful execution on similar projects provides confidence in their ability to deliver on your requirements.
- Communication, Support & Transparency:
- Assessment: How responsive and communicative is the provider during the quoting and project discussion phase? Are they transparent about their processes, capabilities, and potential challenges? Do they provide clear project updates?
- Why it Matters: A strong working relationship relies on clear, open communication. This is especially important for complex AM projects that may require iterative design adjustments or collaborative problem-solving.
- Cost & Lead Time:
- Assessment: Is their pricing competitive and transparent? Do their quoted lead times seem realistic given the scope of work (printing and post-processing)? How do they compare to other qualified suppliers?
- Why it Matters: While cost is always a factor, it should be evaluated in the context of quality, expertise, and reliability. The cheapest quote may not offer the best value or lowest risk. Ensure quotes clearly detail all included steps.
Table: Partner Evaluation Checklist Summary
Criteria | Key Questions | Why It’s Critical for Engine Housings |
---|---|---|
Technical Expertise | DfAM support? Material/process knowledge? Industry experience? | Optimizes complex design, ensures functionality, avoids costly errors. |
Machine Park/Technology | Right process (LPBF/EBM)? Build volume? Capacity? Machine quality? | Determines feasibility, quality, lead time, scalability. |
Material/Powder Quality | Required alloys available? Powder QC? Traceability? Supplier vs. Manufacturer (like Met3dp)? | Foundation of part quality, mechanical properties, defect prevention. |
Quality System/Certs | ISO 9001? AS9100 (if aerospace)? Internal QC procedures? Auditable? | Ensures process control, repeatability, compliance for critical parts. |
Post-Processing | In-house capabilities? Managed network? Workflow integration? | Streamlines complex workflow, ensures end-to-end quality management. |
Track Record/Case Studies | Relevant project experience? References? | Reduces risk, provides confidence in execution capabilities. |
Communication/Support | Responsiveness? Transparency? Collaboration potential? | Facilitates smooth project execution, problem-solving. |
Cost & Lead Time | Competitive & transparent pricing? Realistic lead times? Detailed quotes? | Balances budget with quality, reliability, and time-to-market needs. |
Export to Sheets
Selecting the right metal AM partner is a critical strategic decision. By thoroughly evaluating potential suppliers against these criteria, focusing on providers like Met3dp that demonstrate end-to-end capabilities from advanced powder production to reliable printing systems and application support, businesses can build the strong partnerships needed to successfully leverage additive manufacturing for high-value components like engine housings.
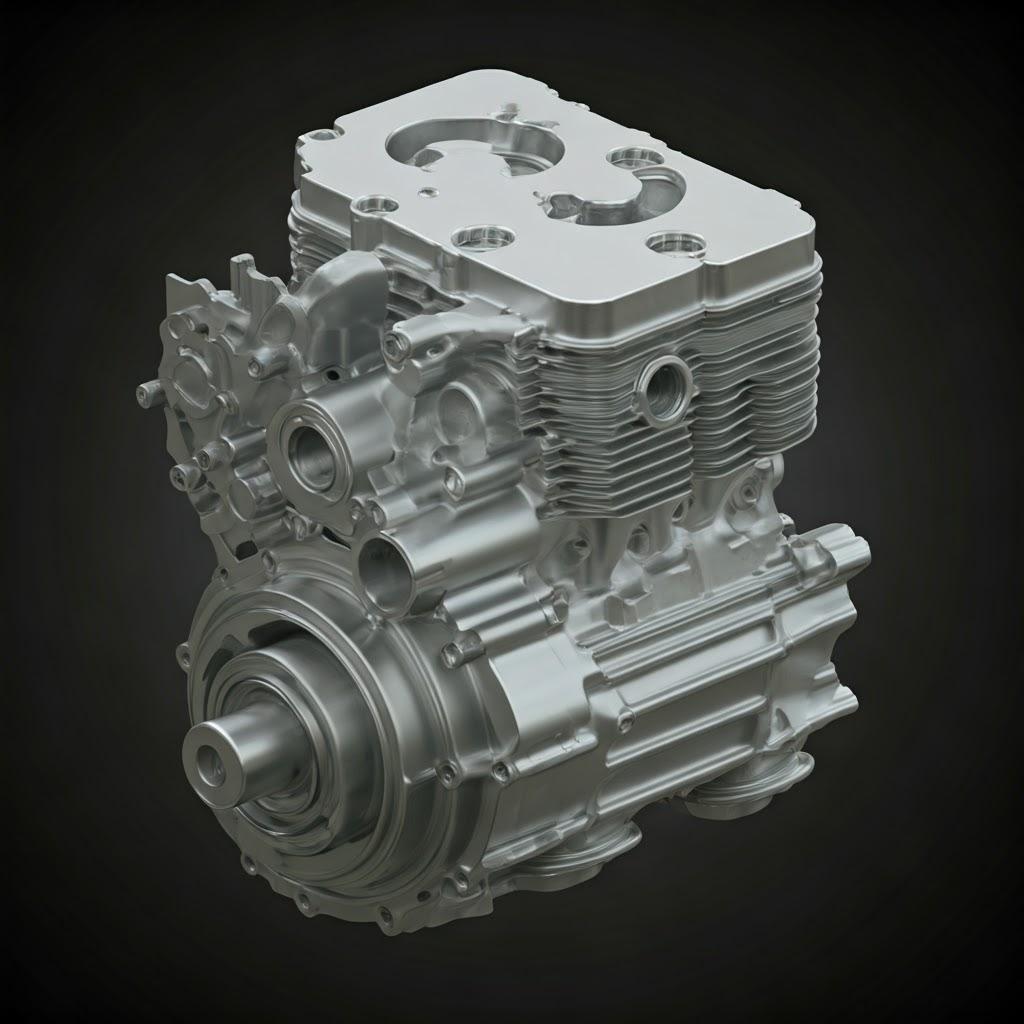
Understanding Cost Factors and Lead Times for 3D Printed Engine Housings
One of the most common questions from engineers and procurement managers considering metal additive manufacturing for engine housings revolves around cost and lead time. While AM offers significant advantages in design freedom and potential long-term value, it’s crucial to understand the factors that drive its pricing structure and production timelines compared to traditional methods. The cost is not simply based on weight; it’s a complex calculation influenced by material choice, machine utilization, part complexity, labor, and extensive post-processing requirements. Similarly, lead times involve more than just the printing duration.
Primary Cost Drivers for Metal AM Engine Housings:
- Material Cost:
- Powder Price: Metal powders vary significantly in price per kilogram. AlSi10Mg is relatively inexpensive, Ti-6Al-4V is considerably more expensive, and IN718 is typically the most costly of the three.
- Material Consumption: This includes the material in the final part plus the material used for support structures. DfAM efforts to minimize supports and optimize design volume directly reduce material consumption.
- Density: Denser materials (like IN718) mean more kilograms are needed for the same volume compared to lighter materials (like AlSi10Mg).
- Powder Recycling: Efficient recycling of unfused powder helps reduce overall material cost, but requires careful quality control to prevent degradation or contamination. Experienced providers have optimized recycling protocols.
- Machine Time:
- Build Preparation: Software setup, build plate preparation, and machine loading/unloading contribute to overall time.
- Printing Time: This is often the largest component of machine time. It depends primarily on the part height (more layers = more time), the volume of material being fused per layer, the chosen layer thickness, and the scan speed/strategy. Complex internal features or extensive support structures increase print time.
- Cooling Time: After printing, the build chamber needs to cool down before parts can be safely removed, especially important for EBM’s high-temperature process.
- Machine Depreciation & Overhead: The high capital cost of industrial metal AM systems is factored into the hourly operating rate charged by service providers.
- Labor Costs:
- Technician Time: Skilled technicians are required for build setup, machine operation, monitoring, de-powdering, part removal, basic support removal, and general handling.
- Engineering Support: DfAM consultation, process planning, and quality assurance engineering add to the labor component.
- Post-Processing Labor: Manual support removal, surface finishing (blasting, polishing), inspection, and coordination of outsourced steps can be significant labor contributors.
- Post-Processing Costs:
- Heat Treatment: Furnace time, energy consumption, and controlled atmospheres (vacuum/inert gas) for stress relief, HIP, and final property treatments add cost. HIP is a particularly specialized and costly step.
- Machining: CNC machining time for critical features depends on the amount of material to be removed, the complexity of the features, the material’s machinability (Ti-6Al-4V and IN718 are much harder to machine than AlSi10Mg), and fixture requirements.
- Surface Finishing: Costs vary depending on the method (blasting is relatively cheap, extensive polishing is expensive).
- Inspection & QA: Non-destructive testing (CT scanning, ultrasonic, dye penetrant), dimensional inspection (CMM), and material testing add to the overall cost but are essential for quality assurance.
- Part Complexity & Size:
- Complexity: While AM excels at complexity, highly intricate designs often require more support structures and significantly more challenging de-powdering and support removal, increasing labor and risk. Complex internal channels may require advanced inspection methods.
- Size: Larger parts consume more material and require longer print times and potentially larger, more expensive machines. They are also more challenging regarding thermal management and post-process handling.
- Production Volume:
- Setup Amortization: Fixed setup costs (build preparation) are amortized over the number of parts in a single build. Printing multiple parts (nesting) or larger batch sizes generally reduces the cost per part.
- Volume Discounts: For ongoing production or larger wholesale orders, suppliers may offer volume discounts on materials and processing.
Table: Cost Factor Summary
Cost Category | Key Influences | Impact on Engine Housing Cost |
---|---|---|
Material | Powder price (Al < Ti < IN718), Part volume, Support volume, Density, Recycling | Significant driver, especially for Ti & IN718. |
Machine Time | Part height, Volume/complexity per layer, Machine rate, Cooling time | Major cost component, directly related to build duration. |
Labor | Setup, Operation, De-powdering, Support removal, Finishing, QA Engineering | Significant, especially for complex parts needing extensive handling. |
Post-Processing | Heat treatment types (HIP is costly), Machining extent & difficulty, Finishing | Can represent 50% or more of the total cost. |
Complexity/Size | Intricacy (supports, cleaning), Overall dimensions | Affects material use, print time, labor, and handling costs. |
Volume | Number of parts per build, Total order quantity | Setup amortization & potential discounts reduce cost per part. |
Export to Sheets
Lead Time Considerations:
The total lead time for a 3D printed engine housing is the sum of several stages:
- Quoting & Design Review (1-5 days): Initial file assessment, DfAM review/feedback, quote generation.
- Order Confirmation & Scheduling (1-3 days): Finalizing order details and scheduling the build into the machine queue.
- Build Preparation & Printing (2 days – 2+ weeks): Depending on part size, complexity, number of parts nested, and machine availability. Printing itself can take many days for large/complex housings.
- Cooling & De-Powdering (1-2 days): Necessary cool-down period followed by powder removal.
- Post-Processing (1 – 4+ weeks): This is often the most variable and potentially longest phase. It includes:
- Stress Relief (1-2 days)
- Build Plate Removal / Support Removal (1-3 days, depending on complexity)
- HIP (if required, often involves sending parts out, adding 1-2 weeks including logistics)
- Final Heat Treatment (2-5 days, depending on cycle complexity)
- CNC Machining (2 days – 2+ weeks, depending on complexity and machine shop scheduling)
- Finishing & Inspection (1-5 days)
- Shipping (1-5 days): Depending on location and method.
Total Estimated Lead Time: For a complex metal AM engine housing requiring full post-processing, typical lead times can range from 4 weeks to 10 weeks or more. Prototyping with minimal post-processing might be faster (2-4 weeks), while aerospace-certified parts requiring extensive QA and specialized processing will likely be at the longer end of the scale.
Working with Met3dp:
Experienced providers like Met3dp understand these cost and lead time drivers. They can provide detailed, transparent quotes outlining all steps and work with clients to optimize designs and processes for efficiency. Their integrated approach, combining high-quality powder production, reliable printing systems, and application expertise, aims to streamline the workflow and deliver high-value components within predictable timeframes. Clear communication with your chosen AM partner about specific requirements and deadlines is crucial for effective project management.
Frequently Asked Questions (FAQ) about 3D Printed Engine Housings
As metal additive manufacturing becomes increasingly adopted for functional components, engineers and procurement managers often have specific questions regarding its application to engine housings. Here are answers to some common inquiries:
1. Is 3D printed metal as strong and reliable as metal parts made by casting or forging?
- Answer: Yes, absolutely. When produced using optimized process parameters, high-quality metal powders (like those manufactured by Met3dp), and appropriate post-processing (especially heat treatments like stress relief, HIP, and solution/aging cycles), metal AM parts can achieve mechanical properties (tensile strength, yield strength, fatigue strength, hardness) that are comparable to, and sometimes even superior to, those of wrought or cast materials. For example, Ti-6Al-4V produced via AM can meet or exceed ASTM standards for cast and wrought equivalents. The key is rigorous process control, appropriate heat treatment tailored to the alloy (e.g., T6 for AlSi10Mg, specific cycles for Ti-6Al-4V and IN718), and quality assurance measures like HIP to minimize porosity for critical applications. It’s crucial to work with experienced providers who understand material science and process optimization to ensure the final part meets or exceeds the required specifications for reliability and durability in demanding engine environments.
2. Can large engine components, like a full V8 engine block, be 3D printed?
- Answer: Technically, yes, it’s becoming increasingly feasible. Metal AM machine manufacturers are continuously developing systems with larger build volumes capable of printing sizeable components. For instance, build envelopes exceeding 500mm x 500mm x 500mm are available, and even larger custom systems exist. Met3dp offers printers with industry-leading print volumes suitable for substantial parts. However, several factors need consideration for very large housings:
- Cost: Printing very large volumes consumes significant amounts of expensive powder and requires extensive machine time, making the cost potentially prohibitive compared to traditional casting for standard production, unless the benefits (e.g., extreme lightweighting, integrated complex features for high performance) justify the expense.
- Print Time: Build times for very large, solid, or complex parts can extend into weeks.
- Thermal Management: Managing residual stress and potential distortion becomes more challenging in larger parts, making processes like EBM/SEBM (with its heated chamber) potentially more advantageous, or requiring very careful LPBF parameter and support strategy design.
- Post-Processing: Handling, heat treating, and machining very large AM parts requires specialized equipment.
- Alternative: For some very large structures, an alternative approach might be to print smaller sections optimally designed for AM and then join them using conventional methods like welding, though this adds assembly steps. The feasibility and cost-effectiveness need careful evaluation on a case-by-case basis.
3. How does the cost of a 3D printed engine housing compare to one made by traditional casting?
- Answer: There’s no single answer, as it depends heavily on several factors:
- Volume: For very high production volumes (thousands or tens of thousands), traditional casting (especially die casting) typically offers a lower cost per part due to economies of scale, despite high initial tooling costs. For low volumes (prototypes, custom parts, small series production up to a few hundred units), metal AM is often significantly more cost-effective because it eliminates the need for expensive tooling (molds/dies).
- Complexity: AM excels at complex geometries. If the design incorporates intricate internal channels, topology optimization, or consolidated features that are difficult or impossible to cast, AM can be more cost-effective even at moderate volumes because it avoids complex core packages, multiple machining setups, or assembly steps required for the cast equivalent.
- Material: For expensive materials like Ti-6Al-4V or IN718, AM’s near-net-shape process can lead to better material utilization (less waste) compared to machining from billet, potentially offering cost savings despite higher initial powder costs.
- Lead Time & Agility: AM offers much shorter lead times for initial parts (no tooling delay) and allows for rapid design iteration, which has significant economic value in R&D phases or time-sensitive projects.
- Total Cost of Ownership: When considering lightweighting benefits (fuel savings over lifetime), performance improvements (better cooling), or supply chain simplification (digital inventory, reduced assembly), the total cost of ownership for an AM part might be lower than a traditionally manufactured one, even if the initial purchase price is higher.
- Break-Even Point: There’s typically a break-even volume below which AM is cheaper and above which casting becomes cheaper (for designs suitable for both). This point varies greatly depending on complexity and material. A detailed cost analysis comparing AM (including all post-processing) with traditional methods (tooling + part cost + machining + assembly) is needed for specific cases.
4. What quality certifications are most important when selecting a supplier for aerospace-grade 3D printed engine housings?
- Answer: For aerospace applications, quality and traceability are paramount. The key certifications to look for in a metal AM supplier include:
- AS9100: This is the standardized Quality Management System requirement for the aerospace industry. It incorporates ISO 9001 requirements and adds specific criteria related to safety, reliability, airworthiness, and traceability crucial for aerospace components. Compliance is generally mandatory for suppliers manufacturing flight-critical or primary structural parts.
- ISO 9001: While AS9100 is preferred for aerospace, ISO 9001 certification demonstrates a fundamental commitment to quality management principles, process control, and documentation, which is essential baseline credibility.
- NADCAP (National Aerospace and Defense Contractors Accreditation Program): While AS9100 covers the overall QMS, NADCAP provides specific accreditation for special processes. Relevant NADCAP accreditations for an AM workflow might include Heat Treating, Non-Destructive Testing (NDT), Materials Testing Laboratories, and potentially Welding (if joining AM parts). Suppliers need accreditation for the specific processes they perform or manage.
- Specific Customer Approvals: Major aerospace OEMs (Original Equipment Manufacturers) often have their own additional supplier qualification requirements and approved vendor lists.
Ensuring your chosen partner holds the necessary certifications provides confidence that they adhere to the stringent quality control, process validation, and traceability standards demanded by the aerospace industry for components like engine housings.
Conclusion: The Future of Engine Housing Production is Additive
The journey through the intricacies of metal additive manufacturing for engine housings reveals a technology that has firmly moved beyond rapid prototyping into the realm of advanced manufacturing for demanding, end-use applications. For engineers and procurement managers in the automotive, aerospace, and industrial sectors, metal AM using materials like AlSi10Mg, Ti-6Al-4V, and IN718 offers a compelling suite of advantages that traditional methods simply cannot match. The ability to achieve unprecedented design freedom – enabling topology optimization for radical lightweighting, intricate conformal cooling channels for superior thermal management, and the consolidation of multiple parts into a single, robust component – represents a paradigm shift in how engine performance, efficiency, and reliability can be approached.
While challenges related to residual stress, support structures, powder removal, and the necessity of comprehensive post-processing exist, they are being effectively addressed through advancements in DfAM principles, sophisticated process control (as seen in technologies like Met3dp’s SEBM systems), high-quality material production, and integrated workflow management. The key lies in understanding both the immense potential and the practical considerations of the technology. Success requires a holistic approach: rethinking design possibilities, carefully selecting the right material for the application, meticulously planning and executing post-processing steps, and, perhaps most importantly, choosing the right manufacturing partner.
A partner like Met3dp, with its deep roots in both the science of high-performance metal powder production and the engineering of industry-leading additive manufacturing equipment, embodies the integrated expertise required. Their commitment to quality, from the atomization of spherical powders to the reliable operation of their printers, provides the foundation needed to produce engine housings that meet the stringent demands of modern industry. By leveraging such partnerships, companies can de-risk the adoption of AM, accelerate development cycles, and unlock performance benefits previously unattainable.
The decision to use metal AM for engine housings is strategic. It may involve higher upfront costs per part compared to high-volume casting in some scenarios, but the value proposition often extends far beyond the initial price tag. Reduced assembly costs, lower lifetime fuel consumption due to lightweighting, extended component life through better thermal management, and unparalleled supply chain agility through on-demand production and digital inventories contribute to a compelling total cost of ownership.
As industries continue to push the boundaries of performance and efficiency, metal additive manufacturing will undoubtedly play an increasingly vital role in the production of next-generation engine housings and other critical components. The future of engine production is not just about making parts; it’s about intelligently manufacturing integrated systems – lighter, stronger, more efficient, and tailored precisely to their function. Metal AM is a cornerstone technology enabling that future.
Ready to explore how metal additive manufacturing can revolutionize your engine housing designs? Visit Met3dp to learn more about our advanced SEBM printers, high-performance metal powders, and comprehensive application development services. Contact our team today to discuss your project requirements and discover how our expertise can power your organization’s additive manufacturing goals.
Share On
MET3DP Technology Co., LTD is a leading provider of additive manufacturing solutions headquartered in Qingdao, China. Our company specializes in 3D printing equipment and high-performance metal powders for industrial applications.
Inquiry to get best price and customized Solution for your business!
Related Articles
About Met3DP
Recent Update
Our Product
CONTACT US
Any questions? Send us message now! We’ll serve your request with a whole team after receiving your message.
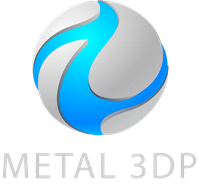
Metal Powders for 3D Printing and Additive Manufacturing