3D Printing Fuel Manifolds for Aerospace Engines
Table of Contents
Introduction – The Ascent of Additive Manufacturing in Aerospace Fuel Systems
The aerospace industry constantly demands innovation, pushing the boundaries of engineering to achieve greater efficiency, performance, and safety. Within this dynamic landscape, the manufacturing of critical engine components, such as fuel manifolds, is undergoing a significant transformation. Traditional manufacturing methods often present limitations in terms of design complexity, material utilization, and production timelines. However, the advent of metal 3D printing, also known as metal additive manufacturing (AM), is providing groundbreaking solutions. This technology empowers aerospace engineers and procurement managers to reimagine the design and production of intricate parts like fuel manifolds, unlocking unprecedented possibilities in performance optimization and supply chain efficiency. At the forefront of this revolution is Metal3DP Technology Co., LTD, a leading provider of additive manufacturing solutions, headquartered in Qingdao, China. With their industry-leading print volume, accuracy, and reliability, as highlighted on their Metal 3D Printing service page, Metal3DP is enabling the next generation of aerospace manufacturing.
What Role Do Fuel Manifolds Play in Aerospace Applications?
Fuel manifolds are integral components within aerospace engines, serving as the central distribution systems for fuel delivery to the combustion chambers. These complex networks of channels and nozzles must ensure a precise and consistent flow of fuel under extreme operating conditions, including high pressures, varying temperatures, and intense vibrations. The efficiency and reliability of fuel manifolds directly impact engine performance, fuel consumption, and overall aircraft safety. Their intricate designs are often tailored to specific engine architectures, necessitating complex manufacturing processes when using conventional techniques. The demand for lighter, more efficient, and geometrically optimized fuel manifolds is constantly increasing as the aerospace industry strives for greater sustainability and performance.
Why Metal 3D Printing is Revolutionizing Aerospace Fuel Manifold Production
Metal 3D printing offers a compelling alternative to traditional manufacturing methods for aerospace fuel manifolds, providing numerous advantages:
- Design Freedom: Additive manufacturing allows for the creation of complex internal geometries and intricate flow channels that are virtually impossible to achieve with conventional methods like casting or machining. This design freedom enables engineers to optimize fuel flow, improve combustion efficiency, and reduce weight by eliminating unnecessary material.
- Material Efficiency: Unlike subtractive manufacturing processes that involve material removal, 3D printing builds parts layer by layer, significantly reducing material waste. This is particularly crucial when working with expensive, high-performance alloys commonly used in aerospace applications.
- Rapid Prototyping and Iteration: Metal 3D printing accelerates the design and development cycle. Engineers can quickly produce prototypes of fuel manifolds, test their performance, and iterate on designs in a fraction of the time compared to traditional methods. This agility is invaluable in the fast-paced aerospace industry.
- Part Consolidation: Complex assemblies of multiple components can be consolidated into a single 3D-printed part. This reduces the number of joints and fasteners, leading to improved structural integrity, reduced assembly time, and lower overall costs.
- Customization and On-Demand Manufacturing: Metal 3D printing enables the production of highly customized fuel manifolds tailored to specific engine requirements. It also facilitates on-demand manufacturing, reducing the need for large inventories and enabling the production of spare parts as needed.
Metal3DP‘s commitment to providing cutting-edge systems, as showcased on their product page, directly addresses these needs, empowering aerospace companies to leverage the benefits of metal 3D printing for their fuel manifold production.
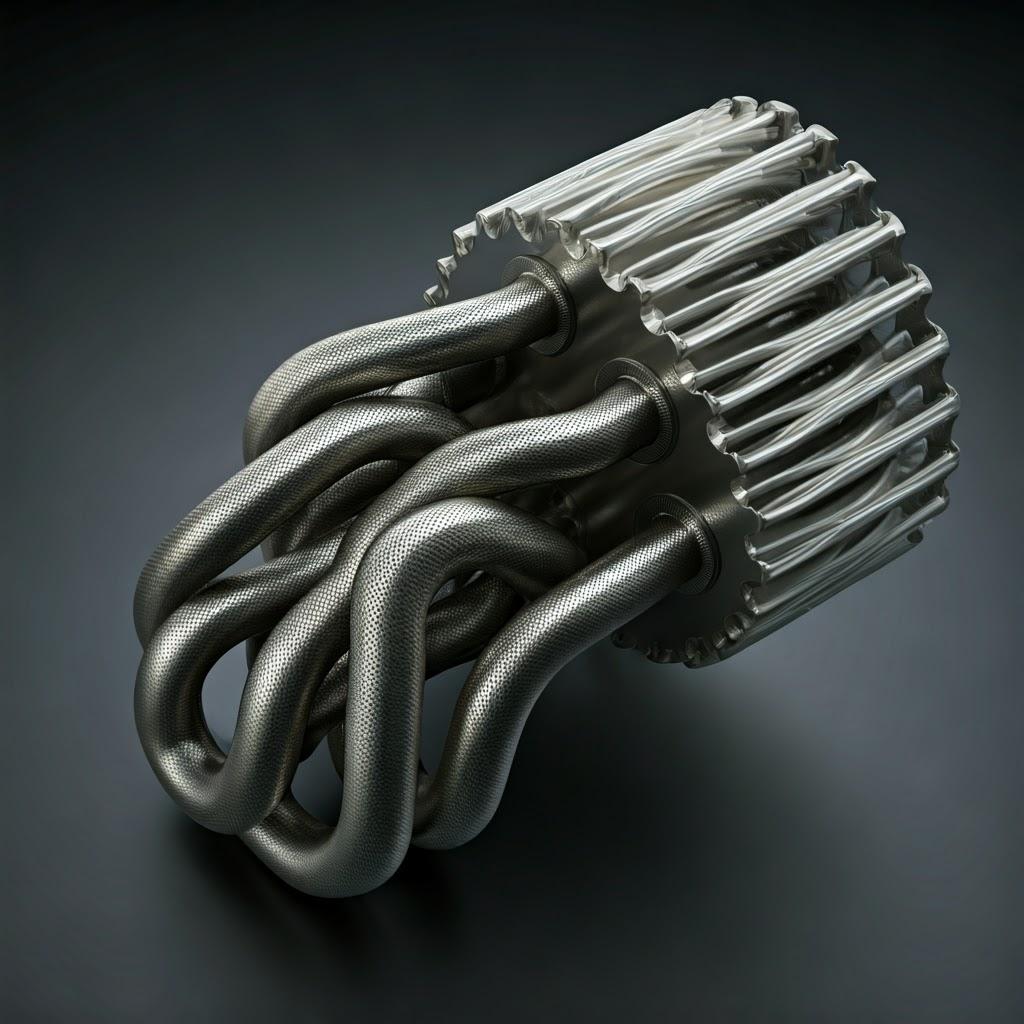
Unlocking Superior Performance with Recommended Metal Powders
The choice of metal powder is paramount in determining the final properties and performance of a 3D-printed aerospace fuel manifold. Metal3DP manufactures a wide range of high-quality metal powders optimized for laser and electron beam powder bed fusion, ensuring superior mechanical properties and reliability. For aerospace fuel manifolds, two high-performance nickel-based superalloys stand out:
- IN718: This nickel-chromium alloy exhibits exceptional high-temperature strength, creep resistance, and corrosion resistance up to approximately 700°C (1300°F). Its excellent weldability and fabricability make it a popular choice for demanding aerospace applications, including turbine blades, combustion chambers, and, importantly, fuel manifolds. The chemical composition of IN718 typically includes nickel, chromium, molybdenum, niobium, and tantalum.
- IN625: Another high-strength nickel-chromium-molybdenum alloy, IN625, offers excellent corrosion and oxidation resistance, even in harsh environments. It maintains its strength at elevated temperatures and is known for its good fatigue resistance. These properties make it well-suited for aerospace fuel manifolds that are exposed to corrosive fuels and extreme operating conditions. The typical composition of IN625 includes nickel, chromium, molybdenum, and niobium.
Metal3DP‘s advanced powder making system, utilizing industry-leading gas atomization and PREP technologies, ensures that their IN718 and IN625 powders possess high sphericity and good flowability, crucial for achieving dense, high-quality 3D-printed parts. You can learn more about their commitment to high-quality metal powders on their about us page.
Property | IN718 | IN625 | Importance for Fuel Manifolds |
---|---|---|---|
High-Temperature Strength | Excellent up to 700°C (1300°F) | Good at elevated temperatures | Crucial for maintaining structural integrity under engine operating temperatures. |
Corrosion Resistance | Good resistance to various corrosive environments | Excellent resistance to oxidation and a wide range of corrosive media | Essential for withstanding exposure to aviation fuels and potential environmental factors. |
Creep Resistance | High resistance to deformation under sustained high temperatures | Good creep resistance | Prevents long-term deformation and ensures the dimensional stability of the manifold. |
Fatigue Resistance | Good fatigue strength | Good fatigue resistance | Important for withstanding the cyclic stresses and vibrations experienced during flight. |
Weldability | Excellent | Good | Facilitates potential repairs or joining with other components. |
Density | ~8.2 g/cm³ | ~8.4 g/cm³ | Impacts the overall weight of the component, a critical factor in aerospace applications. |
Yield Strength (annealed) | ~1030 MPa | ~414 MPa | Indicates the material’s resistance to permanent deformation. |
Tensile Strength (annealed) | ~1275 MPa | ~827 MPa | Represents the maximum stress the material can withstand before breaking. |
Export to Sheets
By selecting the appropriate metal powder from a trusted supplier like Metal3DP, aerospace manufacturers can ensure that their 3D-printed fuel manifolds meet the stringent performance requirements of the industry.
Design Optimization for 3D-Printed Aerospace Fuel Manifolds
Designing for metal additive manufacturing requires a different mindset compared to traditional methods. To fully leverage the capabilities of 3D printing for aerospace fuel manifolds, engineers must consider several key design principles:
- Topology Optimization: This computational technique can identify and remove material from low-stress areas, resulting in lightweight yet structurally sound designs. For fuel manifolds, topology optimization can be used to create organic, free-form structures that minimize weight while maintaining the necessary strength and stiffness to withstand operational pressures and vibrations.
- Lattice Structures: Incorporating lattice structures within the fuel manifold design can further reduce weight without compromising structural integrity. These intricate, repeating cellular structures offer high strength-to-weight ratios and can be tailored to specific load-bearing requirements.
- Conformal Cooling Channels: Metal 3D printing enables the integration of complex, conformal cooling channels directly into the fuel manifold design. These channels can follow the exact contours of the part, providing more efficient heat dissipation and preventing overheating, which is crucial in high-temperature aerospace engine environments.
- Internal Channels and Features: Additive manufacturing allows for the creation of intricate internal channels and features that would be impossible or very costly to produce using traditional methods. For fuel manifolds, this can lead to optimized fuel flow paths, improved mixing, and enhanced combustion efficiency.
- Self-Supporting Geometries: Designing parts with self-supporting geometries minimizes the need for support structures during the printing process. This reduces material waste, post-processing time, and potential surface finish issues. However, some support structures may still be necessary for complex overhangs and internal features.
- Wall Thickness and Feature Size: Careful consideration of minimum wall thicknesses and feature sizes is essential for successful metal 3D printing. These parameters are influenced by the chosen material, printing process, and desired mechanical properties. Metal3DP‘s expertise in printing methods can provide valuable guidance on these design considerations.
By embracing these design principles, aerospace engineers can unlock the full potential of metal 3D printing to create high-performance, lightweight, and efficient fuel manifolds.
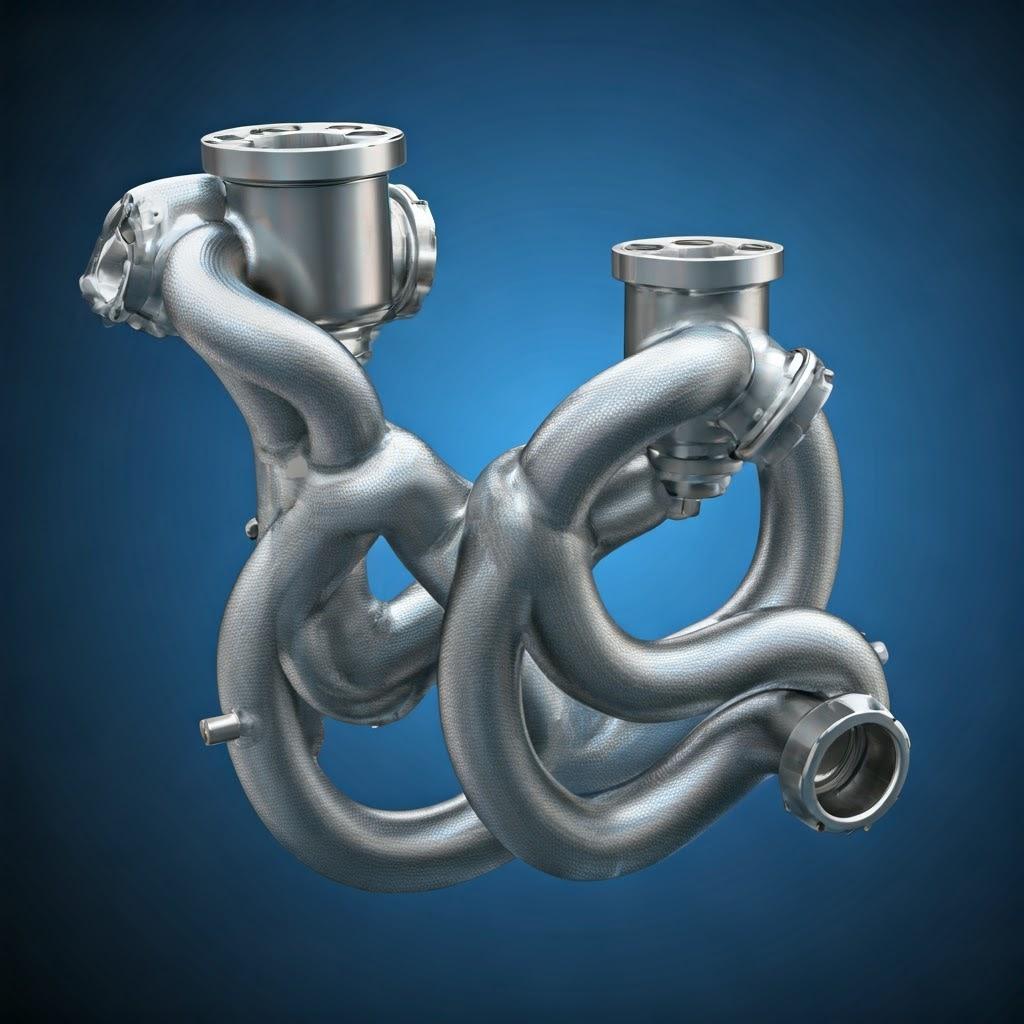
Achieving Critical Tolerances and Surface Finish in 3D-Printed Fuel Manifolds
Aerospace components, including fuel manifolds, often have stringent requirements for dimensional accuracy, tolerances, and surface finish. Metal 3D printing technologies have advanced significantly in their ability to meet these demands.
- Dimensional Accuracy: Powder bed fusion processes, such as Selective Laser Melting (SLM) and Electron Beam Melting (EBM), offered by companies like Metal3DP, can achieve high levels of dimensional accuracy, typically within tens of microns. The accuracy depends on factors such as the machine calibration, material properties, and part geometry.
- Tolerances: Depending on the design and post-processing, tolerances of ±0.1 mm or even tighter can be achieved with metal 3D printing. Critical functional surfaces may require post-machining to achieve tighter tolerances.
- Surface Finish: The as-printed surface finish in metal 3D printing is typically rougher compared to machined surfaces. The surface roughness is influenced by the powder particle size, layer thickness, and build orientation. For fuel manifolds, smooth internal channels are crucial for optimal fuel flow. Post-processing techniques like polishing, abrasive flow machining, or chemical etching can be employed to achieve the desired surface finish.
Metal3DP‘s commitment to industry-leading accuracy ensures that their 3D printing services can meet the demanding specifications of the aerospace industry. Understanding the achievable tolerances and surface finishes early in the design process is crucial for minimizing post-processing requirements and ensuring the functionality of the fuel manifold.
Essential Post-Processing for Aerospace-Grade Fuel Manifolds
While metal 3D printing offers significant advantages, post-processing is often necessary to achieve the final desired properties and surface finish for aerospace fuel manifolds. Common post-processing steps include:
- Support Removal: Support structures, which are often required during the printing process to prevent collapse or distortion, need to be carefully removed. This can be done manually, mechanically, or through chemical dissolution, depending on the support material and part geometry.
- Heat Treatment: Heat treatment is crucial for relieving internal stresses, optimizing the microstructure, and achieving the desired mechanical properties of the 3D-printed material. The specific heat treatment cycle depends on the alloy used (e.g., annealing, solution treatment, aging for IN718 and IN625).
- Hot Isostatic Pressing (HIP): HIP involves subjecting the 3D-printed part to high pressure and temperature simultaneously. This process helps to eliminate internal porosity, increase density, and improve the overall mechanical properties, which is particularly important for critical aerospace components.
- CNC Machining: For surfaces requiring very tight tolerances or specific features that are difficult to achieve directly with 3D printing, CNC machining may be employed as a secondary process. This can include machining of mounting surfaces, threads, or critical sealing areas.
- Surface Finishing: As mentioned earlier, various surface finishing techniques, such as polishing, abrasive flow machining, shot peening, or chemical etching, can be used to improve the surface roughness of the fuel manifold’s internal and external surfaces. This is important for ensuring proper fuel flow and preventing corrosion.
- Non-Destructive Testing (NDT): To ensure the integrity and quality of the 3D-printed fuel manifolds, NDT methods like dye penetrant inspection, ultrasonic testing, or radiographic testing may be performed to detect any internal flaws or surface defects.
Metal3DP‘s comprehensive solutions likely include guidance and partnerships for these essential post-processing steps, ensuring that the final parts meet the stringent quality standards of the aerospace industry.
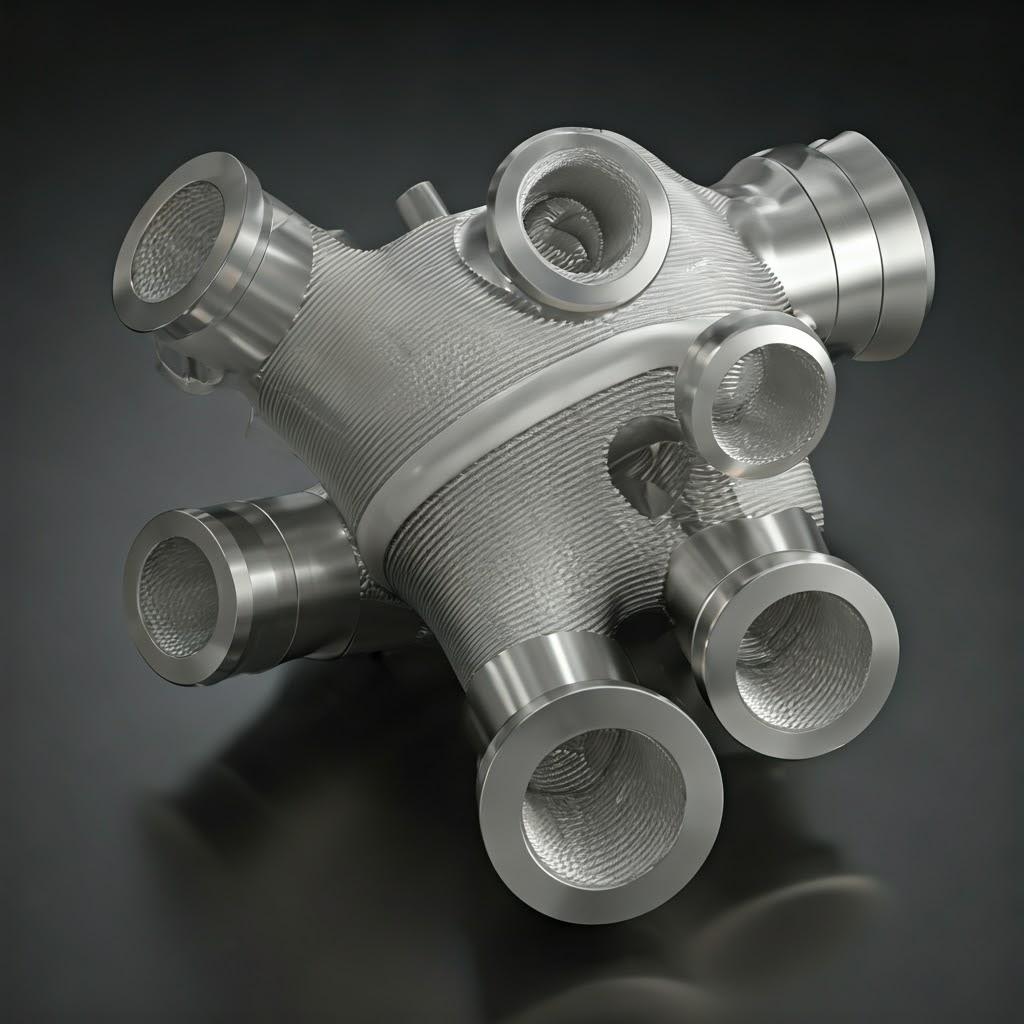
Navigating Challenges in Metal 3D Printing of Fuel Manifolds
While metal 3D printing offers numerous benefits, there are also potential challenges that need to be addressed to ensure successful production of aerospace fuel manifolds:
- Warping and Distortion: Thermal stresses during the printing process can lead to warping or distortion of the part, especially for complex geometries or large parts. Careful design optimization, process parameter control, and the use of appropriate support structures can mitigate these issues.
- Porosity: Internal porosity can compromise the mechanical properties and fatigue life of the 3D-printed part. Optimizing printing parameters, material selection, and employing post-processing techniques like HIP can minimize porosity. Metal3DP‘s high-quality metal powders are designed to minimize this risk.
- Support Removal Damage: Improper removal of support structures can damage the surface of the part. Careful design of support structures and the use of appropriate removal techniques are essential.
- Surface Roughness: As mentioned earlier, the as-printed surface roughness may not meet the requirements for certain applications. Additional post-processing steps are often necessary.
- Material Property Variability: Achieving consistent and predictable material properties throughout the 3D-printed part can be challenging. Strict process control, high-quality metal powders from reputable suppliers like Metal3DP, and thorough testing are crucial.
- Cost and Scalability: While 3D printing can be cost-effective for low-volume production and complex geometries, the cost per part may be higher for large-scale production compared to traditional methods. However, advancements in technology and increasing production volumes are making metal 3D printing more scalable.
By understanding these potential challenges and implementing appropriate design strategies, process controls, and post-processing techniques, aerospace manufacturers can successfully leverage metal 3D printing for the production of high-quality fuel manifolds.
Selecting a Trusted Metal 3D Printing Service Provider for Aerospace Components
Choosing the right metal 3D printing service provider is crucial for the successful production of aerospace fuel manifolds. Given the critical nature of these components and the stringent quality requirements of the aerospace industry, several factors should be carefully considered:
- Industry Experience and Certifications: Look for a provider with a proven track record in serving the aerospace industry and relevant certifications such as AS9100. Metal3DP‘s decades of collective expertise in metal additive manufacturing positions them as a knowledgeable partner.
- Material Capabilities: Ensure the provider has experience processing the required metal powders, such as IN718 and IN625, and can provide material data sheets and testing reports to verify the properties of the printed parts. Metal3DP manufactures a wide range of high-quality metal powders optimized for various applications.
- Printing Technology and Equipment: Understand the types of metal 3D printing technologies the provider utilizes (e.g., SLM, EBM). The choice of technology can impact the achievable accuracy, surface finish, and material properties. Metal3DP offers industry-leading print volume, accuracy, and reliability with their printing equipment.
- Quality Control Processes: Inquire about the provider’s quality control procedures, including in-process monitoring, post-printing inspection, and non-destructive testing capabilities. Robust quality control is essential for ensuring the integrity of aerospace components.
- Post-Processing Services: Determine if the provider offers the necessary post-processing services, such as heat treatment, HIP, CNC machining, and surface finishing, or if they have partnerships with qualified vendors.
- Design Support and Expertise: A good service provider should offer design consultation and support to optimize the fuel manifold design for additive manufacturing. Metal3DP provides comprehensive solutions spanning equipment, powders, and application development services.
- Lead Times and Scalability: Discuss the provider’s typical lead times for production and their ability to scale up production volumes if needed.
- Communication and Customer Support: Effective communication and responsive customer support are essential for a smooth and successful project.
By carefully evaluating potential metal 3D printing service providers based on these criteria, aerospace companies can establish reliable partnerships for the production of high-quality fuel manifolds.
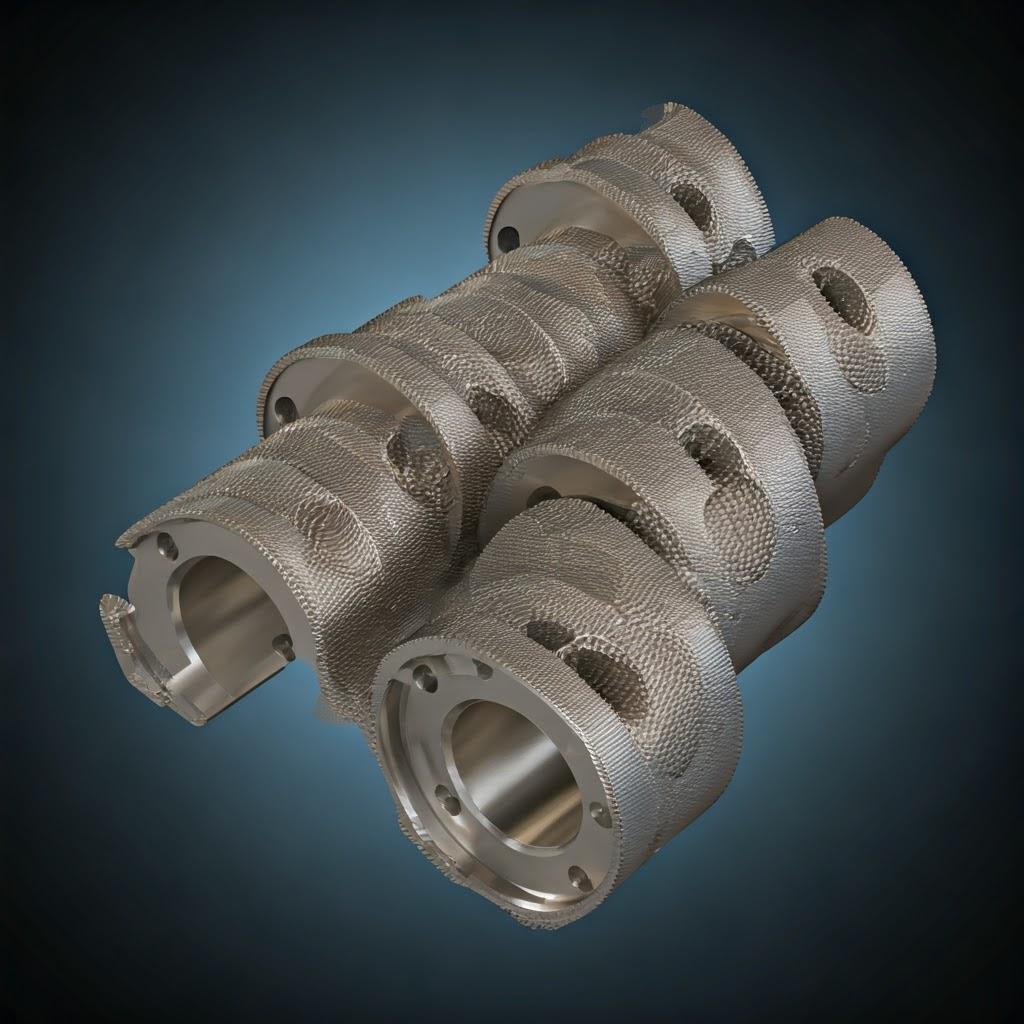
Understanding the Economics and Lead Times for 3D-Printed Fuel Manifolds
The cost and lead time for producing aerospace fuel manifolds using metal 3D printing are influenced by several factors:
- Material Costs: The cost of the metal powder (e.g., IN718, IN625) is a significant factor. High-performance aerospace alloys tend to be more expensive. Material waste is generally lower in 3D printing compared to subtractive methods, which can offset some of the initial material cost.
- Printing Time: The build time depends on the complexity and volume of the part, as well as the layer thickness and scanning speed of the 3D printer. Longer build times translate to higher machine costs.
- Post-Processing Costs: The cost of post-processing steps such as support removal, heat treatment, HIP, machining, and surface finishing needs to be factored in. Complex post-processing requirements will increase the overall cost.
- Design Optimization Costs: Investing in design optimization for additive manufacturing can lead to more efficient designs and reduced material usage, potentially lowering overall costs in the long run.
- Production Volume: The cost per part in 3D printing generally decreases with increasing production volume, especially when considering factors like setup costs and economies of scale. However, for very high volumes, traditional manufacturing methods may still be more cost-effective.
- Lead Times: Metal 3D printing can significantly reduce lead times compared to traditional manufacturing, especially for complex geometries that require multiple steps and tooling. Prototyping can be done much faster, and on-demand manufacturing eliminates the need for long lead times associated with tooling and setup. However, the actual printing time and post-processing duration will influence the overall lead time.
Metal3DP can provide detailed cost analyses and lead time estimates based on specific fuel manifold designs and production requirements. Understanding these economic and timeline considerations is crucial for making informed decisions about adopting metal 3D printing for aerospace applications.
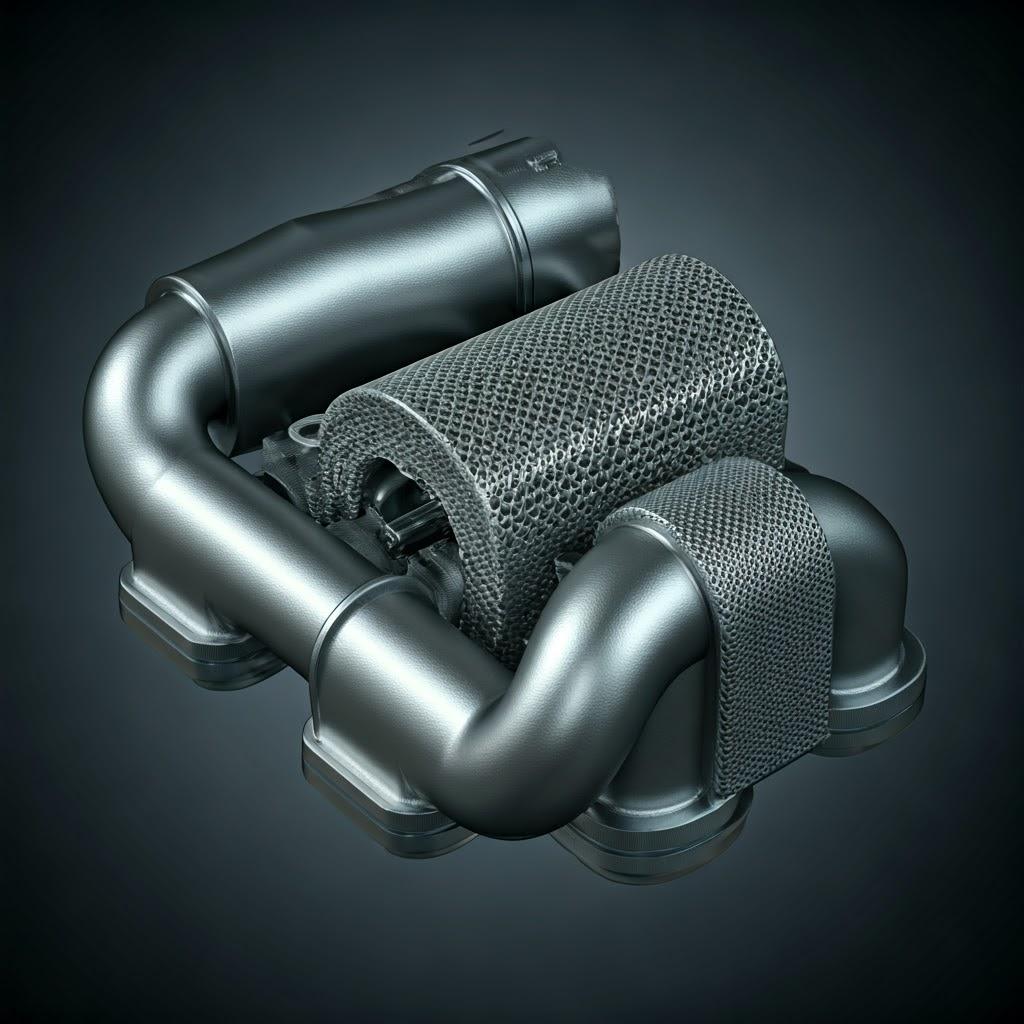
Frequently Asked Questions (FAQ)
Q: Is metal 3D printing strong enough for aerospace fuel manifolds? A: Yes, when the appropriate high-performance metal powders like IN718 or IN625 are used, and the printing process is carefully controlled with proper post-processing (including heat treatment and potentially HIP), 3D-printed metal parts can achieve mechanical properties comparable to or even better than those produced by traditional methods. Metal3DP‘s high-quality powders are designed for demanding applications.
Q: What are the typical tolerances achievable with metal 3D printing for fuel manifolds? A: Depending on the printing technology and part geometry, tolerances of ±0.1 mm or better can be achieved. For critical functional surfaces, post-machining may be required to achieve tighter tolerances.
Q: Can metal 3D printing help reduce the weight of aerospace fuel manifolds? A: Absolutely. The design freedom offered by metal 3D printing allows for topology optimization and the incorporation of lattice structures, which can significantly reduce the weight of fuel manifolds without compromising structural integrity.
Conclusion – The Future of Aerospace Fuel Manifolds Lies in Metal 3D Printing
Metal 3D printing is rapidly transforming the manufacturing landscape for aerospace components, offering unprecedented opportunities for innovation in the design and production of fuel manifolds. The ability to create complex geometries, optimize for weight and performance, and utilize high-performance materials like IN718 and IN625 makes additive manufacturing an increasingly attractive alternative to traditional methods. Companies like Metal3DP Technology Co., LTD, with their advanced metal powders, reliable printing equipment, and comprehensive expertise, are at the forefront of this revolution, empowering aerospace engineers and procurement managers to realize the full potential of metal 3D printing. By embracing this technology, the aerospace industry can achieve lighter, more efficient, and more reliable fuel systems, paving the way for the next generation of aircraft. Contact Metal3DP today via their website to explore how their capabilities can power your organization’s additive manufacturing goals.
Share On
MET3DP Technology Co., LTD is a leading provider of additive manufacturing solutions headquartered in Qingdao, China. Our company specializes in 3D printing equipment and high-performance metal powders for industrial applications.
Inquiry to get best price and customized Solution for your business!
Related Articles
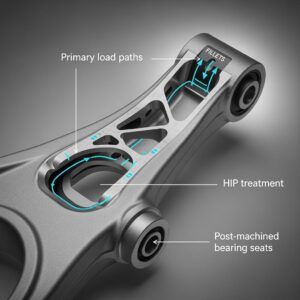
Metal 3D Printing for U.S. Automotive Lightweight Structural Brackets and Suspension Components
Read More »About Met3DP
Recent Update
Our Product
CONTACT US
Any questions? Send us message now! We’ll serve your request with a whole team after receiving your message.