Gas Turbine Atomizing Air Systems
Table of Contents
Imagine a fire-breathing dragon, its immense power fueled by a precise mixture of air and fuel. In the world of gas turbines, achieving optimal combustion efficiency relies on a similar principle, but with a much more meticulous approach. Enter the gas turbine atomizing air system, the unsung hero ensuring a smooth and powerful performance.
What is a Gas Turbine Atomizing Air System?
A gas turbine atomizing air system plays a critical role in gas turbines that utilize liquid fuels like diesel or heavy fuel oil. Unlike natural gas, which readily mixes with air, these liquid fuels need a helping hand to achieve proper combustion. This is where the atomizing air system comes in.
Here’s the breakdown:
- Compressed Air Source: The system taps into the compressed air generated by the gas turbine’s compressor section. This high-pressure air serves as the lifeblood of the system.
- Dedicated Compressor (Optional): In some cases, an additional dedicated compressor might be employed to further increase the air pressure specifically for atomization purposes.
- Air Cooler: Often, the compressed air needs to be cooled down before entering the atomizing nozzles. This is because excessively hot air can negatively impact fuel atomization quality.
- Atomizing Nozzles: These nozzles are strategically positioned within the combustor. They convert the high-pressure, cool air into a forceful, finely dispersed mist.
- Fuel Injection: The atomized air then gets to work, breaking up the liquid fuel into a fine spray. This vastly increases the fuel’s surface area, allowing for more efficient mixing with air and ultimately, a more complete combustion process.
Think of it this way: Imagine pouring gasoline onto a campfire. The large pool of fuel will take a long time to burn and release its energy inefficiently. Now, picture the gasoline being transformed into a fine mist – it ignites much faster and burns more completely, just like what the atomizing air system achieves with liquid fuels in gas turbines.
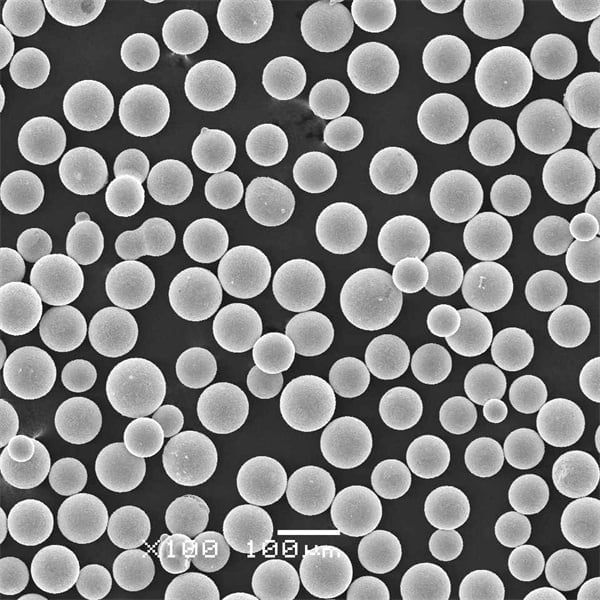
Applications of Gas Turbine Atomizing Air Systems
Gas turbine atomizing air systems aren’t just about keeping the fire burning; they play a crucial role in a fascinating industrial process – additive manufacturing (AM), also known as 3D printing. Here’s how:
- Metal Powder Production: AM relies on metal powders with specific characteristics like particle size, shape, and flowability. Gas turbines equipped with atomizing air systems can be used to create these metal powders. The high-pressure, cool air effectively breaks down molten metal into a fine, uniform powder ideal for AM applications.
- Benefits for AM: The use of atomizing air systems in metal powder production offers several advantages:
- Tight Control: The system allows for precise control over the size and distribution of the metal particles, crucial for achieving the desired properties in the final 3D printed product.
- Improved Flowability: The atomized powder exhibits superior flowability, making it easier to handle and use in 3D printing equipment.
- Diverse Materials: This technology can be used with a wide range of metals, from common ones like aluminum and titanium to more exotic materials like nickel superalloys and even precious metals.
A Glimpse into the Future: As AM technology continues to evolve, the demand for high-quality metal powders is expected to rise. Gas turbine atomizing air systems are poised to play a significant role in meeting this demand, enabling the creation of complex and high-performance 3D printed parts across various industries.
Metal Powder Examples for Additive Manufacturing:
Metal Powder | Description |
---|---|
Gas-atomized Aluminum (AlSi10Mg): | A popular choice for AM due to its excellent combination of strength, machinability, and weldability. Commonly used in aerospace, automotive, and consumer goods applications. |
Gas-atomized Titanium (Ti-6Al-4V): | A high-strength, lightweight metal ideal for applications demanding a good balance of strength and weight reduction. Used in aerospace, medical implants, and high-performance components. |
Inconel 625: | A nickel superalloy known for its exceptional resistance to high temperatures, corrosion, and oxidation. Used in jet engines, gas turbines, and other applications requiring high-performance materials. |
Stainless Steel 316L: | A versatile stainless steel grade offering good corrosion resistance and biocompatibility. Used in medical implants, chemical processing equipment, and food service applications. |
Copper: | Offers excellent thermal and electrical conductivity, making it suitable for heat sinks, electrical components, and applications requiring efficient heat dissipation. |
A Look at Popular Metal Powders for Additive Manufacturing
The previous section highlighted some of the key benefits of using gas turbine atomizing air systems for metal powder production in AM. Now, let’s delve deeper and explore a wider range of metal powders commonly utilized in this revolutionary technology:
Metal Powder Spotlight:
Metal Powder | Description | Advantages | Disadvantages |
---|---|---|---|
Nickel (Ni): | Pure nickel offers good corrosion resistance and electrical conductivity. | High electrical conductivity, good ductility, magnetic properties | Relatively high cost compared to some other metals |
Cobalt (Co): | A key ingredient in many superalloys, offering high-temperature strength and wear resistance. | Excellent high-temperature strength, wear resistance, magnetic properties | High cost, potential health hazards during handling |
Molybdenum (Mo): | Primarily used in alloying due to its high melting point and good strength at elevated temperatures. | High melting point, contributes to strength and creep resistance in alloys | Brittleness in pure form, potential health hazards during handling |
Tungsten (W): | Known for its incredibly high melting point and excellent wear resistance. | Exceptional high-temperature strength, wear resistance | High cost, extreme difficulty in machining, potential health hazards during handling |
Niobium (Nb): | A valuable alloying element that enhances strength and high-temperature performance. | Strengthens alloys, improves high-temperature performance | Relatively high cost, limited availability compared to some other metals |
Tantalum (Ta): | A rare earth metal known for its exceptional corrosion resistance and high melting point. | Excellent corrosion resistance, high melting point, good biocompatibility | Very high cost, limited availability |
Beyond the Basics: Specialty Metal Powders
The world of metal powders for AM extends far beyond these commonly used options. Here’s a glimpse into some specialty powders pushing the boundaries of what’s possible:
- Biocompatible Alloys: Metal powders like titanium and cobalt-chromium alloys are finding increasing use in the medical field for creating implants like hip replacements and dental prosthetics. These powders offer excellent biocompatibility, meaning they can coexist peacefully with the human body without causing adverse reactions.
- Tool Steels: Gas turbine atomized tool steel powders enable the creation of custom-designed cutting tools with superior wear resistance and strength. This translates to longer tool life and improved productivity in various machining applications.
- Amorphous Metals: These unique metallic materials possess a glassy structure, leading to exceptional strength, elasticity, and corrosion resistance. While still under development for AM, gas turbine atomization offers a promising route for producing high-quality amorphous metal powders.
Advantages and Disadvantages of Gas Turbine Atomizing Air Systems
Like any technology, gas turbine atomizing air systems come with their own set of pros and cons. Let’s weigh the advantages and disadvantages to understand where this technology stands:
Advantages:
- Precise Control: The system allows for fine-tuned control over the atomization process, resulting in metal powders with consistent particle size and distribution – crucial for achieving optimal properties in the final 3D printed part.
- High-Quality Powders: The use of compressed air ensures good flowability and minimizes the risk of oxide formation in the powder, leading to high-quality metal powders suitable for demanding AM applications.
- Scalability: Gas turbine atomizing systems can be scaled up or down depending on the desired production volume, making them adaptable to various production needs.
- Wide Material Compatibility: The technology can be used with a broad spectrum of metals, from common ones to exotic materials, offering greater flexibility in AM processes.
Disadvantages:
- High Energy Consumption: Operating gas turbines requires significant energy input, which can translate to higher production costs.
- Complex System: The system itself involves several components, requiring expertise for proper maintenance and operation.
- Environmental Considerations: Gas turbine operation can contribute to greenhouse gas emissions, which necessitates exploring ways to minimize the environmental footprint of this technology.
The Future of Gas Turbine Atomizing Air Systems
The future of gas turbine atomizing air systems in AM appears promising. Here are some key trends to watch:
- Focus on Efficiency: One potential avenue for improvement lies in exploring alternative energy sources for powering the gas turbines. Renewable energy sources like solar or wind power could potentially be integrated into the system, reducing reliance on fossil fuels.
- Advanced Materials: As AM technology ventures into more exotic and high-performance materials, gas turbine atomization systems will need to adapt to handle these challenging materials effectively. This might involve advancements in nozzle design, control systems, and even the selection of compressed air properties to ensure optimal atomization for these unique materials.
- Integration with AM Processes: Greater integration between gas turbine atomization systems and AM equipment could lead to a more streamlined and efficient production workflow. Imagine a scenario where the metal powder is produced and directly fed into the 3D printer in a continuous process, minimizing handling and potential contamination risks.
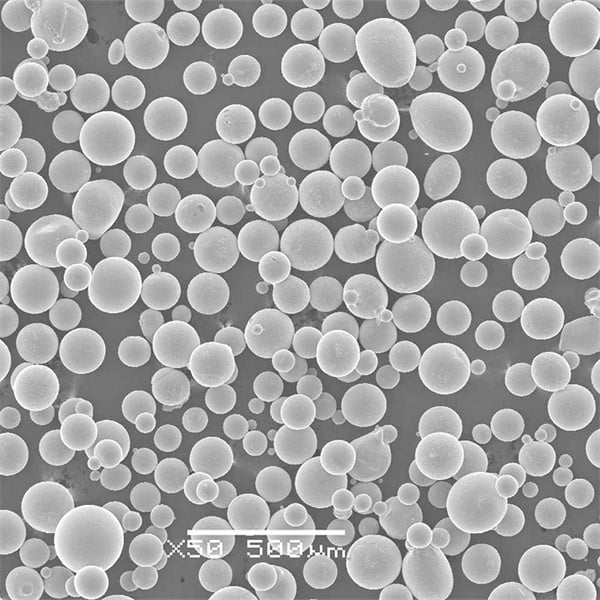
FAQ
Here are some frequently asked questions (FAQs) regarding gas turbine atomizing air systems:
Q: Can other technologies be used for metal powder production in AM?
A: Yes, several alternative methods exist, including water atomization and inert gas atomization. Each method has its own advantages and disadvantages. Water atomization can be a cost-effective option but may introduce unwanted oxygen into the powder. Inert gas atomization offers a cleaner process but can be more expensive. The choice of technology ultimately depends on the desired powder characteristics and production requirements.
Q: What are the safety considerations involved in using gas turbine atomizing air systems?
A: Safety is paramount when working with high-pressure systems and molten metals. Proper training and adherence to safety protocols are essential. This includes wearing appropriate personal protective equipment (PPE) and following established procedures for system operation and maintenance.
Q: How does the cost of gas turbine atomized metal powders compare to other production methods?
A: The cost of gas turbine atomized powders can vary depending on the specific metal, particle size, and production volume. Generally, it falls within the mid-range compared to other methods. However, the high-quality and consistent properties of the powders often justify the cost for demanding AM applications.
Conclusion
Gas turbine atomizing air systems play a critical role in the production of high-quality metal powders for additive manufacturing. Their ability to deliver precise control, high-quality powders, and scalability makes them a valuable tool for this rapidly evolving technology. As AM continues to push boundaries and explore new materials, gas turbine atomization systems will likely adapt and evolve alongside it, paving the way for a future filled with innovative and high-performance 3D printed creations.
Share On
MET3DP Technology Co., LTD is a leading provider of additive manufacturing solutions headquartered in Qingdao, China. Our company specializes in 3D printing equipment and high-performance metal powders for industrial applications.
Inquiry to get best price and customized Solution for your business!
Related Articles
About Met3DP
Recent Update
Our Product
CONTACT US
Any questions? Send us message now! We’ll serve your request with a whole team after receiving your message.
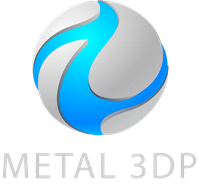
Metal Powders for 3D Printing and Additive Manufacturing