High Sphericity Powder
Table of Contents
High sphericity powder is a revolutionary material finding applications across various industries. From metal additive manufacturing to electronics, the unique properties of these powders enhance performance, reliability, and efficiency. In this guide, we’ll dive deep into the world of high sphericity powders, discussing specific metal powder models, their compositions, properties, and applications. We’ll also compare various models, explore their pros and cons, and provide detailed tables for specifications, suppliers, and more. Let’s get started!
Overview of High Sphericity Powder
High sphericity powder refers to metal powders characterized by their highly spherical shape. This geometric uniformity offers numerous advantages, including better flowability, packing density, and more predictable behavior in manufacturing processes. Industries such as aerospace, automotive, and medical rely on these powders for critical applications where precision and performance are paramount.
Key Properties
- Flowability: High sphericity powders flow more easily compared to irregularly shaped powders.
- Packing Density: These powders pack more efficiently, reducing voids and improving the mechanical properties of the final product.
- Surface Area: Lower surface area compared to irregular powders, leading to better oxidation resistance and lower contamination.
- Consistency: More uniform particle size distribution enhances repeatability and reliability in manufacturing.
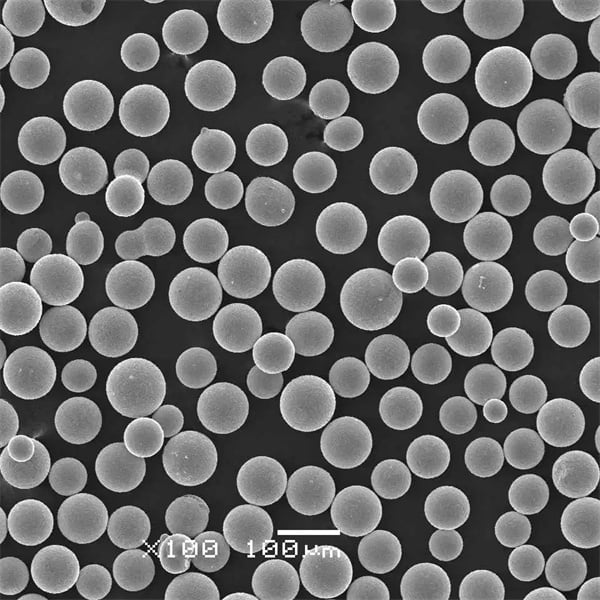
Types of High Sphericity Metal Powders
1. Titanium Alloy (Ti-6Al-4V)
Composition: Titanium, Aluminum, Vanadium
Properties: High strength, lightweight, corrosion resistance
Applications: Aerospace, medical implants, automotive
2. Stainless Steel 316L
Composition: Iron, Chromium, Nickel, Molybdenum
Properties: Excellent corrosion resistance, high strength, good ductility
Applications: Medical devices, food processing equipment, chemical industry
3. Inconel 718
Composition: Nickel, Chromium, Iron, Niobium, Molybdenum
Properties: High temperature resistance, excellent mechanical properties
Applications: Aerospace engines, gas turbines, nuclear reactors
4. Aluminum Alloy (AlSi10Mg)
Composition: Aluminum, Silicon, Magnesium
Properties: Lightweight, good thermal conductivity, decent strength
Applications: Automotive, aerospace, electronics
5. Copper Powder
Composition: Copper
Properties: Excellent electrical conductivity, thermal conductivity
Applications: Electrical components, heat exchangers, electronics
6. Cobalt-Chrome Alloy (CoCr)
Composition: Cobalt, Chromium, Molybdenum
Properties: High wear resistance, biocompatibility
Applications: Dental implants, orthopedic implants, aerospace
7. Tungsten Carbide (WC)
Composition: Tungsten, Carbon
Properties: Extremely hard, wear-resistant
Applications: Cutting tools, mining equipment, wear-resistant coatings
8. Maraging Steel
Composition: Iron, Nickel, Cobalt, Molybdenum, Titanium
Properties: High strength, toughness, good machinability
Applications: Aerospace, tooling, high-performance motorsport components
9. Nickel Superalloy (Hastelloy X)
Composition: Nickel, Chromium, Iron, Molybdenum, Tungsten
Properties: Excellent high-temperature strength, oxidation resistance
Applications: Jet engines, chemical processing, industrial furnaces
10. Magnesium Alloy (AZ91D)
Composition: Magnesium, Aluminum, Zinc
Properties: Lightweight, good strength-to-weight ratio, corrosion resistance
Applications: Automotive, aerospace, electronics casings
Detailed Properties and Characteristics
Here’s a table summarizing the key properties and characteristics of each high sphericity metal powder:
Metal Powder | Composition | Properties | Applications |
---|---|---|---|
Titanium Alloy (Ti-6Al-4V) | Titanium, Aluminum, Vanadium | High strength, lightweight, corrosion resistance | Aerospace, medical implants, automotive |
Stainless Steel 316L | Iron, Chromium, Nickel, Molybdenum | Excellent corrosion resistance, high strength, good ductility | Medical devices, food processing, chemical industry |
Inconel 718 | Nickel, Chromium, Iron, Niobium, Molybdenum | High temperature resistance, excellent mechanical properties | Aerospace engines, gas turbines, nuclear reactors |
Aluminum Alloy (AlSi10Mg) | Aluminum, Silicon, Magnesium | Lightweight, good thermal conductivity, decent strength | Automotive, aerospace, electronics |
Copper Powder | Copper | Excellent electrical conductivity, thermal conductivity | Electrical components, heat exchangers, electronics |
Cobalt-Chrome Alloy (CoCr) | Cobalt, Chromium, Molybdenum | High wear resistance, biocompatibility | Dental implants, orthopedic implants, aerospace |
Tungsten Carbide (WC) | Tungsten, Carbon | Extremely hard, wear-resistant | Cutting tools, mining equipment, wear-resistant coatings |
Maraging Steel | Iron, Nickel, Cobalt, Molybdenum, Titanium | High strength, toughness, good machinability | Aerospace, tooling, high-performance motorsport components |
Nickel Superalloy (Hastelloy X) | Nickel, Chromium, Iron, Molybdenum, Tungsten | Excellent high-temperature strength, oxidation resistance | Jet engines, chemical processing, industrial furnaces |
Magnesium Alloy (AZ91D) | Magnesium, Aluminum, Zinc | Lightweight, good strength-to-weight ratio, corrosion resistance | Automotive, aerospace, electronics casings |
Applications of High Sphericity Powder
High sphericity powders are indispensable in various advanced manufacturing processes. Their unique properties make them suitable for a wide range of applications:
Industry | Applications | Benefits |
---|---|---|
Aerospace | Jet engine components, structural parts | High strength-to-weight ratio, reliability |
Medical | Implants, prosthetics, surgical tools | Biocompatibility, corrosion resistance |
Automotive | Engine parts, structural components | Lightweight, high strength |
Electronics | Conductive inks, heat sinks, electronic components | Excellent electrical and thermal conductivity |
Tooling | Cutting tools, molds | Wear resistance, high hardness |
Energy | Turbine blades, fuel cells | High temperature resistance, efficiency |
Dental | Crowns, bridges, implants | Biocompatibility, durability |
Specifications, Sizes, Grades, and Standards
Each type of high sphericity powder comes with specific standards and specifications to ensure optimal performance:
Metal Powder | Sizes | Grades | Standards |
---|---|---|---|
Titanium Alloy (Ti-6Al-4V) | 15-45 µm, 45-105 µm | Grade 5, Grade 23 | ASTM F1472, ASTM F2924 |
Stainless Steel 316L | 15-45 µm, 45-105 µm | AISI 316L | ASTM F138, ISO 5832-1 |
Inconel 718 | 15-45 µm, 45-105 µm | – | AMS 5662, ASTM B637 |
Aluminum Alloy (AlSi10Mg) | 20-63 µm, 63-100 µm | – | DIN EN 1706, ASTM B211 |
Copper Powder | 10-50 µm, 50-150 µm | – | ASTM B170, ASTM B216 |
Cobalt-Chrome Alloy (CoCr) | 15-45 µm, 45-105 µm | – | ISO 5832-4, ASTM F75 |
Tungsten Carbide (WC) | 1-10 µm, 10-45 µm | – | ISO 4499-2, ASTM B777 |
Maraging Steel | 15-45 µm, 45-105 µm | Grade 250, Grade 350 | ASTM A538 |
Nickel Superalloy (Hastelloy X) | 15-45 µm, 45-105 µm | – | AMS 5754, ASTM B435 |
Magnesium Alloy (AZ91D) | 15-45 µm, 45-105 µm | – | ASTM B94, ASTM B108 |
Suppliers and Pricing Details
Finding reliable suppliers is crucial for ensuring the quality and consistency of high sphericity powders. Here’s a list of some suppliers along with pricing details:
Supplier | Metal Powder | Price (per kg) | Contact Information |
---|---|---|---|
Höganäs | Titanium Alloy (Ti-6Al-4V) | $300 | www.hoganas.com |
Carpenter Technology | Stainless Steel 316L | $150 | www.carpentertechnology.com |
Sandvik | Inconel 718 | $350 | www.home.sandvik |
EOS | Aluminum Alloy (AlSi10Mg) | $100 | www.eos.info |
GKN Additive | Copper Powder | $200 | www.gknpm.com |
Arcam | Cobalt-Chrome Alloy (CoCr) | $250 | www.arcam.com |
HC Starck | Tungsten Carbide (WC) | $400 | www.hcstarck.com |
QuesTek Innovations | Maraging Steel | $275 | www.questek.com |
Kennametal | Nickel Superalloy (Hastelloy X) | $375 | www.kennametal.com |
Luxfer | Magnesium Alloy (AZ91D) | $180 | www.luxfer.com |
Advantages and Disadvantages of High Sphericity Powder
Advantages
- Improved Flowability: High sphericity powders flow better, ensuring more consistent layering in additive manufacturing processes.
- Better Packing Density: These powders pack more densely, reducing porosity and improving the mechanical properties of finished parts.
- Enhanced Oxidation Resistance: With a lower surface area, these powders are less prone to oxidation, enhancing the longevity of components.
- Uniform Properties: The consistent shape and size distribution result in more predictable and reliable properties, essential for high-precision applications.
Disadvantages
- Higher Cost: The advanced manufacturing processes needed to produce high sphericity powders can result in higher costs compared to traditional powders.
- Limited Availability: Not all materials are readily available in high sphericity forms, limiting the range of applications.
- Processing Challenges: Some manufacturing processes may require specific adjustments to accommodate the unique flow and packing characteristics of high sphericity powders.
Comparing High Sphericity Powders
When choosing the right high sphericity powder, it’s essential to compare the options based on specific parameters:
Parameter | Titanium Alloy | Stainless Steel | Inconel | Aluminum Alloy | Copper |
---|---|---|---|---|---|
Cost | High | Medium | High | Low | Medium |
Strength | Very High | High | Very High | Medium | Low |
Corrosion Resistance | High | Very High | High | Medium | High |
Temperature Resistance | Medium | Medium | Very High | Low | Low |
Electrical Conductivity | Low | Low | Low | Medium | Very High |
Thermal Conductivity | Medium | Medium | Low | High | Very High |
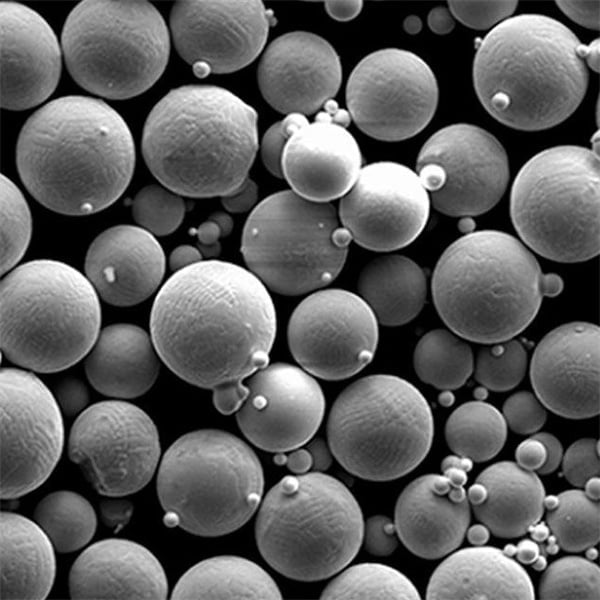
FAQs
What are high sphericity powders?
High sphericity powders are metal powders characterized by their spherical shape, which improves their flowability, packing density, and consistency in various manufacturing processes.
Why are high sphericity powders important in additive manufacturing?
Their improved flowability and packing density lead to more consistent layering and reduced porosity, resulting in better mechanical properties and precision in additive manufacturing.
Which industries benefit the most from high sphericity powders?
Industries such as aerospace, medical, automotive, and electronics benefit significantly due to the powders’ enhanced performance characteristics.
Are high sphericity powders more expensive than traditional powders?
Yes, the advanced manufacturing processes required to produce high sphericity powders typically result in higher costs compared to traditional powders.
Can all metal powders be made with high sphericity?
Not all materials are readily available in high sphericity forms, which can limit their applications. However, many common metals and alloys are available as high sphericity powders.
What is the main advantage of high sphericity powders in the medical industry?
Their biocompatibility and uniform properties make them ideal for implants and prosthetics, ensuring better integration with the human body and longer-lasting performance.
How do high sphericity powders improve the quality of finished products?
By reducing porosity and ensuring more uniform layering in additive manufacturing, high sphericity powders result in finished products with superior mechanical properties and reliability.
Conclusion
High sphericity powders are transforming industries with their unique properties and capabilities. From aerospace to medical applications, these powders enhance performance, reliability, and efficiency. By understanding the specific characteristics and benefits of each type of high sphericity powder, manufacturers can make informed decisions to optimize their processes and products. Whether it’s the exceptional strength of titanium alloys or the biocompatibility of cobalt-chrome, high sphericity powders are paving the way for innovation and excellence in advanced manufacturing.
Share On
MET3DP Technology Co., LTD is a leading provider of additive manufacturing solutions headquartered in Qingdao, China. Our company specializes in 3D printing equipment and high-performance metal powders for industrial applications.
Inquiry to get best price and customized Solution for your business!
Related Articles
About Met3DP
Recent Update
Our Product
CONTACT US
Any questions? Send us message now! We’ll serve your request with a whole team after receiving your message.
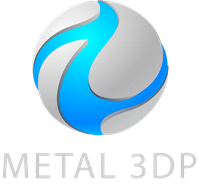
Metal Powders for 3D Printing and Additive Manufacturing