High-Stress Engine Materials
Table of Contents
Imagine a material that can withstand the scorching inferno of a jet engine, where temperatures routinely exceed 1,500 degrees Celsius (2,732 degrees Fahrenheit). Imagine something strong enough to resist the immense pressure and constant stress of a turbine blade spinning at supersonic speeds. That’s the remarkable world of nickel-based superalloys, a class of high-performance materials that defy the limitations of ordinary metals.
Characteristics of High-Stress Engine Materials
Think about the engine of a car. It gets hot, sure, but nowhere near the white-hot fury of a jet engine. So, what makes jet engines and other high-stress applications require such exotic materials? The answer lies in a deadly combination of factors:
- Extreme Temperatures: Ordinary metals soften and lose their strength as temperatures rise. At jet engine operating temperatures, most metals would simply turn to mush.
- High Pressures: The forces exerted within a jet engine are immense. Turbine blades, for example, experience tremendous centrifugal forces as they spin at high speeds. The material needs to be strong enough to resist deformation or even shattering under such pressure.
- Oxidation and Creep: Hot environments don’t just weaken metals; they also accelerate oxidation, the process where metals react with oxygen and form brittle oxides. Additionally, creep, the slow and continuous deformation of a material under stress, becomes a major concern at high temperatures.
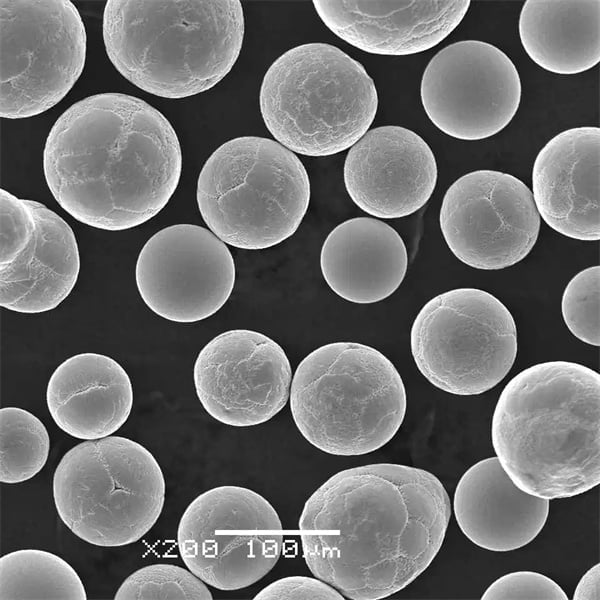
Common High-Stress Engine Materials
Several classes of materials can handle these extreme conditions, but nickel-based superalloys reign supreme. Here’s why:
- The Power of Nickel: Nickel itself possesses a unique crystal structure that makes it inherently strong and resistant to high temperatures. This inherent strength forms the foundation for the superalloy’s remarkable properties.
- The Magic of Alloying: Nickel-based superalloys are not just pure nickel. They are meticulously crafted by adding other elements like chromium, cobalt, aluminum, and titanium. These alloying elements play a crucial role in:
- Solid Solution Strengthening: Certain elements dissolve within the nickel matrix, strengthening the overall structure like tiny reinforcements.
- Precipitation Strengthening: Microscopic particles of specific compounds, rich in elements like aluminum and titanium, form within the nickel matrix. These act like tiny roadblocks, hindering the movement of dislocations (defects) within the material and preventing creep deformation.
The Result: A Material Like No Other
Through careful composition and processing techniques, engineers create nickel-based superalloys with a potent combination of properties:
- Exceptional High-Temperature Strength: These alloys retain their strength at temperatures where other metals fail, making them ideal for jet engine turbine blades, vanes, and combustor liners.
- Superior Oxidation Resistance: The carefully chosen alloying elements form a protective oxide layer that shields the underlying metal from further oxidation, ensuring component longevity.
- Good Creep Resistance: The combination of solid solution and precipitation strengthening significantly hinders creep, allowing the material to maintain its shape under prolonged high-temperature stress.
Application of High-Stress Engine Materials
Nickel-based superalloys aren’t just for jet engines. Their unique properties make them the go-to material for a wide range of demanding applications, including:
- Gas Turbines: From power plants to industrial generators, nickel-based superalloys ensure efficient and reliable operation in high-temperature gas turbine environments.
- Rocket Engine Components: The scorching heat and immense pressure within rocket engines necessitate the use of these high-performance alloys for critical components like combustion chambers and turbine blades.
- Nuclear Reactors: In the harsh environment of a nuclear reactor, nickel-based superalloys find use in fuel cladding materials and other structural components that need to withstand radiation and high temperatures.
The Trade-Off: Strength Meets Challenges
While nickel-based superalloys are undeniably impressive, they do come with some challenges:
- High Cost: The complex manufacturing processes and the use of expensive raw materials make these alloys significantly more costly than conventional metals.
- Fabrication Difficulties: These alloys are challenging to weld, machine, and shape due to their inherent strength and high melting points. Specialized techniques and equipment are required for their fabrication.
- Environmental Concerns: Some of the elements used in these alloys, like cobalt, can pose environmental challenges during the manufacturing process and disposal. Research is ongoing to develop more environmentally friendly alternatives.
The Future of Nickel-Based Superalloys
Despite these challenges, the future of nickel-based superalloys remains bright. Here’s why:
- Continuous Development: Material scientists are constantly pushing the boundaries, developing new alloys with even better high-temperature performance and improved oxidation resistance.
- Additive Manufacturing: The emergence of additive manufacturing techniques like 3D printing holds immense promise for the future of nickel-based superalloys. Here’s how:
- Complex Designs: Additive manufacturing allows for the creation of intricate and lightweight components with internal channels for cooling, something that’s difficult or impossible with traditional manufacturing techniques. This can lead to more efficient and powerful engines.
- Reduced Waste: Traditional manufacturing often involves significant material waste during machining and shaping. Additive manufacturing allows for a more precise use of materials, minimizing waste and potentially reducing overall costs.
- Customization: The ability to create complex geometries with 3D printing opens doors for customization of components for specific applications, potentially leading to even more optimized performance.
The Search for Alternatives: Pushing the Boundaries
While nickel-based superalloys are dominant, the relentless pursuit of even higher performance engines and the ever-present cost pressure drive the search for alternatives. Here are some promising contenders:
- Ceramic Matrix Composites (CMCs): These composites combine the high-temperature strength of ceramic fibers with a metallic matrix, offering excellent heat resistance and potential weight reduction compared to nickel alloys. However, CMCs can be brittle and require further development for wider application.
- Intermetallic Alloys: These alloys are formed from two or more metals, offering unique properties like exceptional high-temperature strength and oxidation resistance. However, their brittleness and difficulty in processing present challenges that need to be addressed.
Balancing Performance, Cost, and Sustainability
The future of high-performance materials for extreme environments will likely involve a multi-pronged approach:
- Further Development of Nickel Alloys: Nickel-based superalloys will likely remain a mainstay for many applications. Continued research will focus on improving their performance, reducing costs, and developing more environmentally friendly manufacturing processes.
- The Rise of Alternatives: As CMCs, intermetallic alloys, and other novel materials mature, they may find their niche in specific applications where their unique properties offer significant advantages.
The Impact: A Symphony of Innovation
The development of high-performance materials like nickel-based superalloys plays a crucial role in various technological advancements. Here’s how:
- More Efficient Engines: Stronger and more reliable engine components lead to more efficient jet engines, reducing fuel consumption and emissions. This translates to a more sustainable future for air travel.
- Pushing the Boundaries of Power Generation: Advanced materials enable the development of more efficient and powerful gas turbines for power plants, leading to increased energy output and potentially lower costs.
- Space Exploration: Nickel-based superalloys are vital for the success of rockets and spacecraft, allowing them to withstand the extreme heat and pressure encountered during launch and re-entry.
Looking Forward: A Material for the Future
Nickel-based superalloys are a testament to human ingenuity. They are a perfect example of how pushing the boundaries of material science can lead to groundbreaking innovations. As we strive for cleaner, more efficient, and powerful technologies, these remarkable materials will continue to play a vital role in shaping the future.
the benefits of using nickel-based superalloys
Despite the machining difficulties and higher cost, nickel-based superalloys offer several compelling benefits that make them the preferred choice for many demanding applications:
- Unmatched High-Temperature Performance: Their exceptional strength and resistance to creep and oxidation at high temperatures are unmatched by most other materials. This allows for the development of more powerful and efficient engines that can operate in extreme environments.
- Durability and Reliability: In critical applications like jet engines and power plants, component failure can have catastrophic consequences. Nickel-based superalloys offer the necessary durability and reliability to ensure safe and long-lasting operation.
- Material Stability: These alloys exhibit excellent dimensional stability at high temperatures, meaning they retain their shape and size even under prolonged exposure to extreme heat. This is crucial for maintaining precise tolerances in critical components.
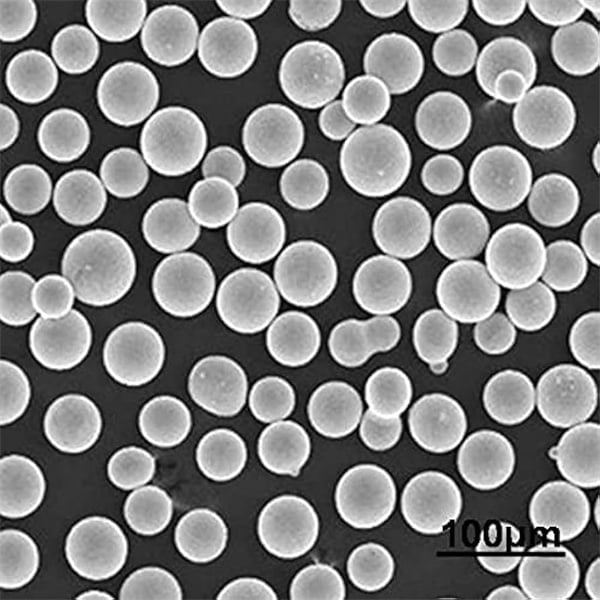
FAQs
What are the different types of nickel-based superalloys?
There are numerous types of nickel-based superalloys, each with a unique composition optimized for specific properties and applications. Some common classifications include:
- Iron-nickel-chromium based alloys (Incoloy®) – known for their good oxidation resistance and high-temperature strength.
- Nickel-chromium based alloys (Inconel®) – offer excellent creep resistance and high strength at elevated temperatures.
- Nickel-cobalt based alloys (Rene®) – developed for exceptional high-temperature strength and resistance to creep and oxidation.
Property | Description |
---|---|
Alloy Classification | Examples: Incoloy®, Inconel®, Rene® |
Composition | Varies depending on the specific alloy, but typically includes nickel, chromium, cobalt, aluminum, titanium, and other elements. |
Key Properties | High-temperature strength, oxidation resistance, creep resistance |
Applications | Jet engine components, gas turbines, rocket engines, nuclear reactors |
environmental concerns associated with nickel-based superalloys?
The mining and processing of some of the elements used in these alloys, like cobalt, can have environmental impacts. Additionally, disposal of these alloys at the end of their lifespan needs to be done responsibly to minimize environmental impact. Research is ongoing to develop more environmentally friendly alternatives and responsible recycling methods.
How much do nickel-based superalloys cost?
Nickel-based superalloys are significantly more expensive than conventional metals due to the complex manufacturing processes and the use of expensive raw materials. The cost can vary depending on the specific alloy composition, but they can be several times more expensive than steel or aluminum.
Are there any alternatives to nickel-based superalloys?
Yes, there are some promising alternatives being explored, each with its own advantages and limitations:
- Ceramic Matrix Composites (CMCs):
- Advantages: Exceptional high-temperature resistance, potential for weight reduction compared to nickel alloys.
- Limitations: Brittle and require further development for wider application. May not be suitable for all high-stress environments due to their brittleness.
- Intermetallic Alloys:
- Advantages: Offer unique properties like exceptional high-temperature strength and oxidation resistance.
- Limitations: Can be brittle and difficult to process, posing challenges for manufacturing complex shapes.
What are some of the challenges associated with machining nickel-based superalloys?
The inherent strength and high melting points of nickel-based superalloys make them challenging to machine. Here’s why:
- Work Hardening: These alloys tend to harden as they are machined, requiring specialized cutting tools and techniques to avoid tool wear and breakage.
- High Cutting Forces: The strength of the material necessitates high cutting forces during machining, which can put a strain on machine tools and require more powerful equipment.
- Heat Generation: Friction during machining generates significant heat, which can further harden the material and reduce tool life. Special coolants and machining techniques are needed to minimize heat generation.
Conclusion
Nickel-based superalloys are a remarkable class of materials that have revolutionized various industries. Their unique combination of properties makes them irreplaceable for many high-stress applications. As we continue to push the boundaries of technology, the development of new alloys, improved manufacturing processes, and advanced machining techniques will ensure that nickel-based superalloys remain the material of choice for the most demanding environments for years to come.
Share On
MET3DP Technology Co., LTD is a leading provider of additive manufacturing solutions headquartered in Qingdao, China. Our company specializes in 3D printing equipment and high-performance metal powders for industrial applications.
Inquiry to get best price and customized Solution for your business!
Related Articles
About Met3DP
Recent Update
Our Product
CONTACT US
Any questions? Send us message now! We’ll serve your request with a whole team after receiving your message.
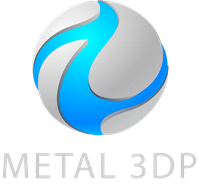
Metal Powders for 3D Printing and Additive Manufacturing