Hot Isostatic Pressing (HIP)
Table of Contents
Hot Isostatic Pressing (HIP) is a fascinating technology that’s playing a crucial role in the manufacturing world. If you’ve ever wondered about how certain metal components achieve their exceptional strength and integrity, HIP might just be the answer. Let’s dive deep into the world of Hot Isostatic Pressing, exploring everything from its basic principles to its wide array of applications.
Overview of Hot Isostatic Pressing (HIP)
Hot Isostatic Pressing (HIP) is a manufacturing process that uses high pressure and temperature to improve the properties of materials. It’s commonly applied to metals and ceramics to eliminate internal porosity, increasing density and enhancing mechanical properties. By subjecting materials to isostatic pressure in a high-temperature environment, HIP can produce components with superior structural integrity.
How Does Hot Isostatic Pressing (HIP) Work?
Imagine you’re baking a cake, but instead of just heat, you add pressure from all sides. The cake turns out denser and more uniform. That’s essentially what HIP does to metals and ceramics. The process involves placing the material in a pressure vessel, heating it to the desired temperature, and then applying gas pressure (usually argon) uniformly. This high-pressure environment helps close any voids and reduce porosity, resulting in a material with enhanced properties.
Key Steps in the HIP Process:
- Loading: The material or component is loaded into a pressure vessel.
- Heating: The vessel is heated to the material’s optimal temperature.
- Pressurizing: Argon gas is introduced to create uniform pressure.
- Cooling: The material is slowly cooled while maintaining pressure to avoid thermal stress.
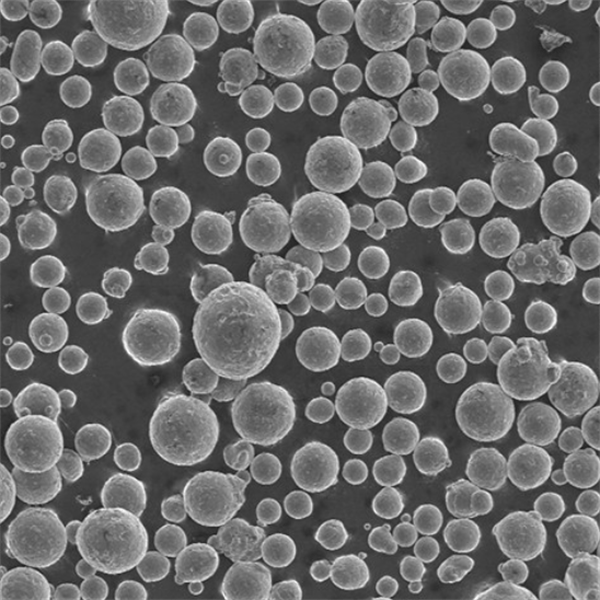
Types of Materials for HIP
Various metal powders are used in HIP to create high-performance components. Here’s a closer look at some specific models:
Metal Powder Model | Description |
---|---|
316L Stainless Steel | Known for its excellent corrosion resistance and high strength. Used in aerospace and medical implants. |
Inconel 718 | A nickel-chromium alloy with high temperature and corrosion resistance, often used in gas turbines and aerospace applications. |
Ti-6Al-4V | A titanium alloy known for its high strength-to-weight ratio and excellent corrosion resistance, widely used in the medical and aerospace industries. |
H13 Tool Steel | Highly resistant to thermal fatigue and wear, commonly used for die casting and plastic molding. |
CuCrZr | A copper alloy with high thermal and electrical conductivity, used in electrical components and welding electrodes. |
AlSi10Mg | An aluminum alloy known for its lightweight and good mechanical properties, used in automotive and aerospace parts. |
CoCrMo | A cobalt-chrome-molybdenum alloy with high wear resistance, used in medical implants like hip and knee replacements. |
Molybdenum TZM | An alloy with high melting point and strength at high temperatures, used in aerospace and nuclear applications. |
Maraging Steel | Known for its superior strength and toughness, often used in tooling and high-stress applications. |
Stellite 6 | A cobalt-based alloy with excellent wear and corrosion resistance, used in cutting tools and aerospace components. |
Applications of Hot Isostatic Pressing (HIP)
HIP is incredibly versatile, finding applications across numerous industries. Here’s a detailed look at how different sectors leverage HIP technology:
Industry | Application |
---|---|
Aerospace | Production of turbine blades, structural components, and high-temperature alloys. HIP ensures these components have the strength and reliability required for flight. |
Medical | Manufacturing of orthopedic implants, dental prosthetics, and surgical instruments. The process ensures high biocompatibility and mechanical strength. |
Automotive | Fabrication of high-performance engine parts, transmission components, and lightweight structures. HIP helps in producing parts that can withstand extreme conditions and stresses. |
Energy | Production of components for nuclear reactors, wind turbines, and oil and gas equipment. HIP enhances the durability and performance of these critical parts. |
Tool and Die Making | Manufacturing of molds, dies, and cutting tools. HIP ensures these tools have high wear resistance and longevity. |
Electronics | Fabrication of heat sinks, electrical connectors, and semiconductor components. HIP improves thermal and electrical conductivity, ensuring reliable performance in electronic devices. |
Defense | Production of armor, weapon components, and specialized alloys for military applications. HIP ensures these materials have the required strength and durability for defense use. |
Aerospace and Defense | Manufacturing of rocket engine parts and satellite components. HIP provides the high-strength and lightweight characteristics needed for space applications. |
Oil and Gas | Production of drill bits, valves, and other high-stress components used in exploration and extraction. HIP enhances the wear resistance and toughness of these parts. |
Jewelry | Fabrication of intricate designs and durable pieces. HIP allows for the creation of unique and high-quality jewelry items. |
Advantages of Hot Isostatic Pressing (HIP)
HIP offers numerous benefits, making it a preferred method in various industries. Here’s why HIP stands out:
- Enhanced Material Properties: By eliminating internal porosity, HIP improves the mechanical properties of materials, resulting in stronger and more durable components.
- Uniform Density: The process ensures uniform density throughout the material, which is crucial for high-stress applications.
- Versatility: HIP can be used with a wide range of materials, including metals, ceramics, and composites.
- Reduced Defects: HIP significantly reduces the occurrence of defects like voids and cracks, enhancing the overall quality of the material.
- Cost-Effective: While the initial setup can be expensive, HIP reduces the need for additional processing and rework, ultimately saving costs.
Disadvantages of Hot Isostatic Pressing (HIP)
Despite its advantages, HIP is not without its drawbacks. Here are some considerations:
- High Initial Costs: The equipment and setup costs for HIP can be high, making it less accessible for smaller operations.
- Energy-Intensive: The process requires significant energy to maintain the high temperatures and pressures, leading to high operational costs.
- Complexity: HIP requires precise control and monitoring, adding to the complexity of the manufacturing process.
- Size Limitations: The size of the pressure vessel limits the size of the components that can be processed.
Detailed Characteristics of Metal Powders for HIP
316L Stainless Steel
- Composition: Chromium, Nickel, Molybdenum
- Properties: Corrosion-resistant, high strength
- Applications: Medical implants, aerospace components
- Advantages: Excellent durability and biocompatibility
- Limitations: Expensive compared to other steels
Inconel 718
- Composition: Nickel, Chromium, Iron
- Properties: High temperature and corrosion resistance
- Applications: Gas turbines, aerospace parts
- Advantages: Maintains strength at high temperatures
- Limitations: High cost, difficult to machine
Ti-6Al-4V
- Composition: Titanium, Aluminum, Vanadium
- Properties: High strength-to-weight ratio, corrosion-resistant
- Applications: Aerospace, medical implants
- Advantages: Lightweight, excellent biocompatibility
- Limitations: Expensive, challenging to work with
H13 Tool Steel
- Composition: Chromium, Molybdenum, Vanadium
- Properties: High thermal fatigue and wear resistance
- Applications: Die casting, plastic molding
- Advantages: Durable and long-lasting
- Limitations: Can be brittle under certain conditions
CuCrZr
- Composition: Copper, Chromium, Zirconium
- Properties: High thermal and electrical conductivity
- Applications: Electrical components, welding electrodes
- Advantages: Excellent conductivity
- Limitations: Limited mechanical strength
AlSi10Mg
- Composition: Aluminum, Silicon, Magnesium
- Properties: Lightweight, good mechanical properties
- Applications: Automotive, aerospace
- Advantages: Low density, good castability
- Limitations: Moderate strength
CoCrMo
- Composition: Cobalt, Chromium, Molybdenum
- Properties: High wear resistance, corrosion-resistant
- Applications: Medical implants
- Advantages: Excellent biocompatibility and durability
- Limitations: Expensive, difficult to machine
Molybdenum TZM
- Composition: Titanium, Zirconium, Molybdenum
- Properties: High melting point, strength at high temperatures
- Applications: Aerospace, nuclear
- Advantages: High-temperature stability
- Limitations: Difficult to fabricate
Maraging Steel
- Composition: Nickel, Cobalt, Molybdenum
- Properties: Superior strength, toughness
- Applications: Tooling, high-stress applications
- Advantages: High strength and durability
- Limitations: Expensive, requires aging process
Stellite 6
- Composition: Cobalt, Chromium, Tungsten
- Properties: Wear and corrosion-resistant
Comparing Metal Powders for HIP
Metal Powder | Advantages | Disadvantages |
---|---|---|
316L Stainless | Corrosion-resistant, high strength | Expensive |
Inconel 718 | High temperature and corrosion resistance | High cost, difficult to machine |
Ti-6Al-4V | High strength-to-weight ratio, corrosion-resistant | Expensive, challenging to work with |
H13 Tool Steel | High thermal fatigue and wear resistance | Can be brittle |
CuCrZr | High thermal and electrical conductivity | Limited mechanical strength |
AlSi10Mg | Lightweight, good mechanical properties | Moderate strength |
CoCrMo | High wear resistance, corrosion-resistant | Expensive, difficult to machine |
Molybdenum TZM | High melting point, strength at high temperatures | Difficult to fabricate |
Maraging Steel | Superior strength, toughness | Expensive, requires aging process |
Stellite 6 | Wear and corrosion-resistant | Expensive, difficult to machine |
Suppliers and Pricing of Metal Powders for HIP
Supplier | Metal Powder | Price Range (per kg) | Notes |
---|---|---|---|
Carpenter Technology | 316L Stainless | $30 – $50 | High-quality, suitable for medical applications |
ATI Metals | Inconel 718 | $100 – $200 | Premium aerospace-grade powder |
Arcam AB | Ti-6Al-4V | $200 – $400 | High-performance titanium powder |
Uddeholm | H13 Tool Steel | $40 – $60 | Durable tool steel powder |
Höganäs AB | CuCrZr | $20 – $40 | Excellent conductivity, suitable for electrical components |
ECKART | AlSi10Mg | $30 – $50 | Lightweight aluminum alloy |
HC Starck | CoCrMo | $150 – $300 | Premium cobalt-chrome alloy |
Plansee | Molybdenum TZM | $200 – $350 | High-temperature alloy |
Sandvik | Maraging Steel | $100 – $200 | High-strength tool steel |
Kennametal | Stellite 6 | $150 – $300 | Wear-resistant cobalt-based alloy |
Applications and Use Cases of HIP Process
The versatility of HIP makes it suitable for a wide range of applications. Let’s explore some specific use cases across different industries:
Industry | Use Case | Benefits |
---|---|---|
Aerospace | Manufacturing turbine blades and structural components | Enhanced strength, high-temperature resistance |
Medical | Producing orthopedic implants and dental prosthetics | Superior biocompatibility, high mechanical strength |
Automotive | Fabricating high-performance engine parts and lightweight structures | Improved durability, reduced weight |
Energy | Making components for nuclear reactors and wind turbines | Increased durability, enhanced performance |
Tool and Die Making | Creating molds and cutting tools | High wear resistance, extended tool life |
Electronics | Fabricating heat sinks and electrical connectors | Improved thermal and electrical conductivity |
Defense | Producing armor and weapon components | High strength, enhanced durability |
Oil and Gas | Manufacturing drill bits and valves | Enhanced wear resistance, increased toughness |
Jewelry | Creating intricate and durable jewelry pieces | Unique designs, high-quality craftsmanship |
Space Exploration | Making rocket engine parts and satellite components | High strength, lightweight characteristics |
Specifications, Sizes, and Standards for HIP Metal Powders
Metal Powder | Specifications | Sizes Available | Standards |
---|---|---|---|
316L Stainless | ASTM A276, UNS S31603 | 5-45 µm, 45-150 µm | ASTM F138, ASTM F139 |
Inconel 718 | AMS 5662, UNS N07718 | 15-53 µm, 53-150 µm | AMS 5662, ASTM B637 |
Ti-6Al-4V | ASTM B348, UNS R56400 | 15-45 µm, 45-100 µm | ASTM F1472, AMS 4928 |
H13 Tool Steel | ASTM A681, UNS T20813 | 10-53 µm, 53-150 µm | ASTM A681 |
CuCrZr | ASTM B224, UNS C18150 | 20-63 µm, 63-150 µm | ASTM B224 |
AlSi10Mg | ASTM B209, UNS A96061 | 20-63 µm, 63-150 µm | ISO 3522 |
CoCrMo | ASTM F75, UNS R31537 | 10-45 µm, 45-150 µm | ASTM F75 |
Molybdenum TZM | ASTM B386, UNS R05252 | 10-45 µm, 45-150 µm | ASTM B386 |
Maraging Steel | ASTM A538, UNS K92890 | 15-45 µm, 45-150 µm | AMS 6514, ASTM A538 |
Stellite 6 | ASTM F75, UNS R31537 | 10-45 µm, 45-150 µm | AMS 5387 |
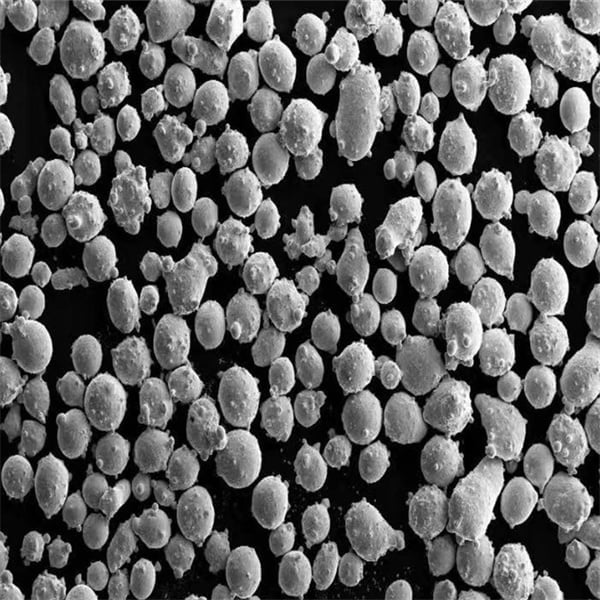
Pros and Cons of HIP Metal Powders
When choosing the right metal powder for HIP, it’s essential to consider the specific advantages and disadvantages of each type:
Metal Powder | Pros | Cons |
---|---|---|
316L Stainless | Excellent corrosion resistance, high strength | Expensive, limited by temperature constraints |
Inconel 718 | High temperature and corrosion resistance, excellent mechanical properties | High cost, difficult to machine |
Ti-6Al-4V | High strength-to-weight ratio, biocompatible | Expensive, challenging to process |
H13 Tool Steel | High wear resistance, good thermal properties | Can be brittle |
CuCrZr | Excellent thermal and electrical conductivity | Limited mechanical strength |
AlSi10Mg | Lightweight, good castability | Moderate strength |
CoCrMo | High wear resistance, biocompatible | Expensive, difficult to machine |
Molybdenum TZM | High melting point, maintains strength at high temperatures | Difficult to fabricate |
Maraging Steel | Superior strength, toughness, good machinability after aging | Expensive, requires aging process |
Stellite 6 | Excellent wear and corrosion resistance, maintains properties at high temperatures | Expensive, difficult to machine |
FAQ
Question | Answer |
---|---|
What is Hot Isostatic Pressing (HIP)? | HIP is a manufacturing process that uses high pressure and temperature to improve the properties of materials, eliminating porosity and enhancing density and mechanical strength. |
What materials can be used in HIP? | Metals, ceramics, and composites are commonly used in HIP. Specific metal powders include 316L Stainless Steel, Inconel 718, Ti-6Al-4V, and more. |
What are the benefits of HIP? | HIP offers enhanced material properties, uniform density, reduced defects, and versatility. |
What are the limitations of HIP? | High initial costs, energy-intensive process, complexity, and size limitations are some drawbacks. |
How does HIP improve material properties? | By applying uniform pressure and high temperature, HIP closes voids and reduces porosity, resulting in stronger and more durable materials. |
What industries use HIP? | Aerospace, medical, automotive, energy, tool and die making, electronics, defense, oil and gas, jewelry, and space exploration industries utilize HIP. |
What is the cost range for HIP metal powders? | Prices vary by material, ranging from $20 to $400 per kilogram, depending on the type and quality of the metal powder. |
Share On
MET3DP Technology Co., LTD is a leading provider of additive manufacturing solutions headquartered in Qingdao, China. Our company specializes in 3D printing equipment and high-performance metal powders for industrial applications.
Inquiry to get best price and customized Solution for your business!
Related Articles
About Met3DP
Recent Update
Our Product
CONTACT US
Any questions? Send us message now! We’ll serve your request with a whole team after receiving your message.