Inconel Powder: A Complete Guide
Table of Contents
Overview of Inconel Powder
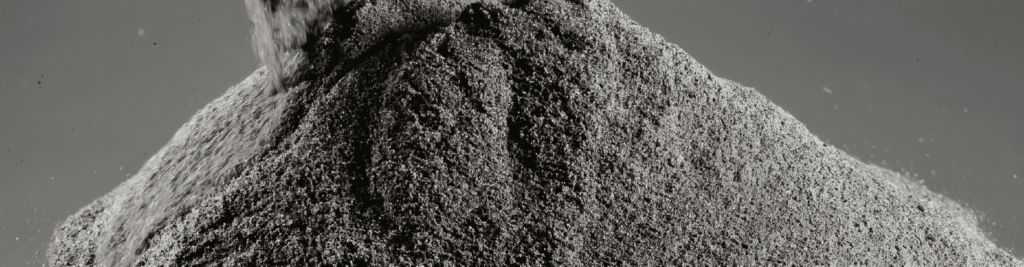
Inconel powder refers to powder metallurgy forms of nickel-chromium-based superalloys trademarked under the Inconel name. Inconel powders are used for additive manufacturing, metal injection molding, and other powder metallurgy applications.
Some key properties of Inconel powder include:
- High strength and hardness at elevated temperatures
- Excellent corrosion and oxidation resistance
- Good weldability and machinability
- High creep rupture strength
- Retains strength and toughness at cryogenic temperatures
Inconel powders are available in different alloy grades such as Inconel 625, 718, and 939 with varying composition and characteristics. They can be used to fabricate components for applications in aerospace, chemical processing, oil & gas, automotive, and power generation industries.
The main product forms are gas atomized spherical powders and agglomerated & sintered powders. Specifications include particle size distribution, flow rate, apparent density, and composition.
Types of Inconel Powder
Inconel 625 Powder
Inconel 625 is a nickel-chromium-molybdenum alloy with excellent corrosion resistance and high strength properties.
Typical Composition (% weight)
Nickel | Chromium | Molybdenum | Niobium | Iron | Other |
---|---|---|---|---|---|
58 min | 20-23 | 8-10 | 3.15-4.15 | 5 max | 1 max |
Key Properties:
- Retains tensile and creep strength at high temperatures up to 980°C
- Resistant to pitting and crevice corrosion in chloride and other aggressive environments
- Oxidation resistance up to 980°C
Applications:
- Aerospace components like engine cowlings, thrust reversers
- Marine components such as shafts, fasteners
- Chemical processing equipment
- Oil & gas extraction and refining
Inconel 718 Powder
Inconel 718 is a precipitation hardening nickel-chromium alloy with outstanding tensile, fatigue and creep properties at temperatures up to 700°C.
Typical Composition (% weight):
Nickel | Chromium | Iron | Niobium | Molybdenum | Titanium | Aluminum | Other |
---|---|---|---|---|---|---|---|
50-55 | 17-21 | Bal. | 4.75-5.5 | 2.8-3.3 | 0.65-1.15 | 0.2-0.8 | 1 max |
Key Properties:
- Retains strength at temperatures up to 700°C
- Excellent corrosion resistance
- Good weldability
- High fatigue strength and toughness
Applications:
- Aerospace components like turbine disks, spacers, shafts
- Rocket motor casings, frames, fasteners
- Nuclear reactors
- Cryogenic storage tanks
Inconel 939 Powder
Inconel 939 is a precipitation hardenable, nickel-based superalloy designed for improved creep rupture strength at high temperatures.
Typical Composition (% weight):
Nickel | Cobalt | Chromium | Tungsten | Titanium | Aluminum | Other |
---|---|---|---|---|---|---|
Bal. | 19-23 | 14.7-17 | 3.8-4.9 | 0.9-1.5 | 1.3-1.7 | 1.5 max |
Key Properties:
- Excellent creep strength up to 1095°C
- Oxidation resistance in continuous service to 980°C
- Corrosion resistance in hot gases
- Retains tensile strength at elevated temperatures
Applications:
- Gas turbine components like combustor cans, transitions
- Steam turbine bolting, casing
- Heat treatment equipment
- Aircraft engine parts
Properties of Inconel Powder
Physical Properties
Property | Description |
---|---|
Density | Ranges from 8.1-8.4 g/cc |
Melting Point | 1315-1370°C |
Thermal Conductivity | 11-12.4 W/mK at 24°C |
Thermal Expansion | 12.5-13.5 x 10<sup>-6</sup>/°C at 20-100°C |
Specific Heat | 0.435 J/g/°C at 20°C |
Electrical Resistivity | 1.24-1.4 μΩ.m at 20°C |
Mechanical Properties
Property | Description |
---|---|
Tensile Strength | 760-1275 MPa |
Yield Strength | 550-1100 MPa |
Elongation | 15-35% |
Hardness | 25-50 HRC |
Modulus of Elasticity | 205-210 GPa |
Poisson’s Ratio | 0.29-0.31 |
Fatigue Strength | 310-690 MPa |
Chemical Properties
- Excellent corrosion resistance in various acids, alkalis, seawater
- Good resistance to oxidation and carburization up to 1095°C
- Resists sulfuric, phosphoric, organic acids
Applications and Uses of Inconel Powder
Industry | Components |
---|---|
Aerospace | Engine components, airframe parts, fasteners, bushings |
Oil & Gas | Downhole tubing, valves, wellhead parts, pumps |
Chemical | Reactor vessels, heat exchangers, condensers, piping |
Automotive | Valves, exhaust components, turbocharger parts |
Power | Gas turbine parts, coal/ash handling parts |
Medical | Surgical implants, prosthetics |
Specifications of Inconel Powder
Size Distribution
Mesh | Micrometers |
---|---|
-140 | less than 106 |
-100 | 150-106 |
-325 | less than 45 |
-500 | less than 32 |
Apparent Density
- Typical range is 2.5-4.5 g/cc
Flow Rate
- Measurement of how freely powder flows
- Expressed in s/50g
- Values of 25-35 s/50g are free flowing
Composition
- Conforms to AMS specification for grade of alloy
- Analysis includes Ni, Cr, Fe, Nb, Mo, Ti, Al
Contamination
- Oxygen content below 0.1%
- Low levels of sulfur, selenium, lead
Suppliers and Pricing
Supplier | Grades Available | Average Price Range |
---|---|---|
Sandvik | 625, 718, 939 | $50-$150/kg |
Met3dp | in625, in718, in939, in738 | $75-$200/kg |
Carpenter Powder | 625, 718, 939 | $60-$180/kg |
Hoganas | 625, 718 | $70-$250/kg |
- Prices vary based on alloy grade, quality, lot size
- Economies of scale for large production volumes
- Extra processing like hot isostatic pressing, degas adds cost
How to Choose Inconel Powder
Factors to Consider
Alloy Grade
- Match alloy to operating temperature and properties needed
- 625 for corrosion resistance, 718 for strength at 700°C, 939 for 1095°C creep strength
Powder Size
- Finer powder for better resolution and surface finish
- Larger powder for higher deposition rates
Production Method
- Gas atomized, plasma rotated electrode process (PREP), or other
Quality Standards
- Chemical analysis, particle shape, contamination levels
- ISO 9001 or AS9100 certified
Lot Size and Lead Time
- Price breaks on large volumes
- Plan ahead for custom orders
Application Method
- Select powder compatible with specific AM or MIM process
Post Processing
- Additional heat treatment, HIP may alter properties
Recommendations
- For additive manufacturing, powder less than 45 microns
- For MIM, go with larger particle size distributions
- Get samples and test prints before purchasing large quantities
- Work closely with your powder supplier to match product to part requirements
- Carefully control handling and storage to avoid contamination or alteration of powder
Pros and Cons of Inconel Powder
Advantages
- High strength at elevated temperatures
- Excellent corrosion and oxidation resistance
- Good weldability and machinability
- Retains toughness at cryogenic temperatures
- Can be used to fabricate complex geometries with AM
- Powder metallurgy processing creates consistent fine microstructures
Disadvantages
- More expensive than steels and aluminum alloys
- Challenging to work with and process
- Susceptible to cracking from thermal stresses
- Difficult to cast without special techniques
- Limited number of suppliers for high quality powder
FAQs
What is Inconel powder used for?
Inconel powder is used to fabricate components with exceptional high temperature mechanical properties and corrosion resistance utilizing additive manufacturing or metal injection molding. Common applications are in aerospace, chemical processing, power generation, oil and gas, and automotive industries.
What is the difference between Inconel 625, 718 and 939 powders?
The main differences relate to composition resulting in varying temperature capabilities:
- Inconel 625 has excellent corrosion resistance to 980°C
- Inconel 718 offers the highest strength up to 700°C
- Inconel 939 is designed for creep strength at extreme temperatures up to 1095°C
What particle size is best for AM?
A particle size range of 15-45 microns is recommended for powder bed fusion additive manufacturing with Inconel powders. Finer particles below 15 microns can cause challenges with flow and spreading. Particles above 45 microns may reduce resolution and surface finish.
Does Inconel powder require special storage or handling?
Yes, Inconel powders readily oxidize and absorb moisture which can alter their properties and flow characteristics. They require storage in sealed containers with either an inert gas or a vacuum. Handling techniques should minimize contact with air.
What post processing is required after AM with Inconel?
Post processes like hot isostatic pressing (HIP), heat treatment, and machining are usually required after additive manufacturing with Inconel powders. These help improve the microstructure and material properties to meet application requirements.
Is Inconel powder reusable after AM?
Yes, Inconel powder can be recovered after additive manufacturing and reused. However, the reused powder needs to be blended with fresh virgin powder at a ratio of 30% reused or less to maintain consistent quality.
Share On
MET3DP Technology Co., LTD is a leading provider of additive manufacturing solutions headquartered in Qingdao, China. Our company specializes in 3D printing equipment and high-performance metal powders for industrial applications.
Inquiry to get best price and customized Solution for your business!
Related Articles
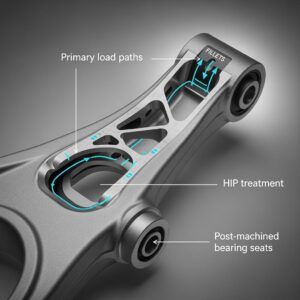
Metal 3D Printing for U.S. Automotive Lightweight Structural Brackets and Suspension Components
Read More »About Met3DP
Recent Update
Our Product
CONTACT US
Any questions? Send us message now! We’ll serve your request with a whole team after receiving your message.