Inconel 625 Powder buyer’s guide:Suppliers, Price, applications
Table of Contents
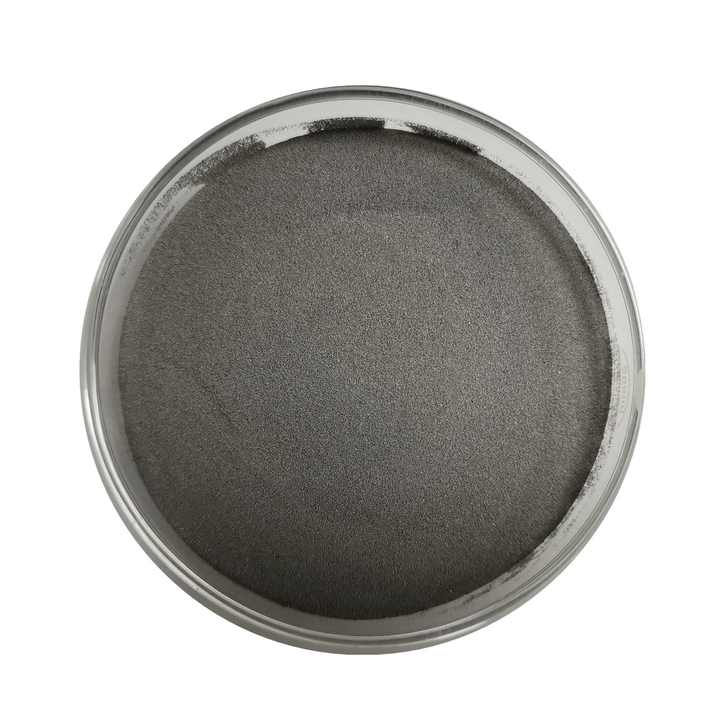
Overview of Inconel 625 Powder
Inconel 625 powder is a nickel-chromium-molybdenum alloy powder used for additive manufacturing and metal 3D printing applications. It is highly corrosion and oxidation resistant while also maintaining high strength and toughness at extreme temperatures. Inconel 625 has excellent fabrication characteristics making it suitable for complex components with intricate shapes and features.
Some key properties and characteristics of Inconel 625 powder include:
- Excellent corrosion resistance especially in reducing, oxidizing and neutral aqueous environments
- High tensile, creep and rupture strength at temperatures up to 1000°C
- Good fatigue strength and outstanding fatigue crack growth resistance
- Retains strength and toughness down to cryogenic temperatures
- Can be thermally treated to further enhance certain properties
- Requires age hardening treatment to achieve optimal mechanical properties
- Resists a wide range of organic and inorganic compounds
- Easy to machine, form and weld by conventional methods
Inconel 625 is used in applications that demand strength, toughness, fatigue resistance and corrosion resistance at extreme temperatures ranging from cryogenic to 1100°C. It is extensively used in the aerospace, chemical processing, pollution control, oil and gas, and marine industries.
Some of the major applications of Inconel 625 include:
- Aerospace components like engine exhaust systems, thrust reversers and turbine blades
- Chemical and food processing equipment like valves, pumps, fasteners, heat exchangers
- Marine components like propeller shafts, marine fasteners and piping systems
- Pollution control equipment and catalyst tubes
- Nuclear fuel element spacers and breeder reactor components
- Wellhead equipment, downhole tubing and subsea components for oil & gas
This article provides a detailed overview of Inconel 625 powder including its composition, properties, applications, specifications, pricing, suppliers and more. It also compares Inconel 625 to other nickel alloys and highlights the advantages and limitations of this versatile superalloy powder.
Composition of Inconel 625 Powder
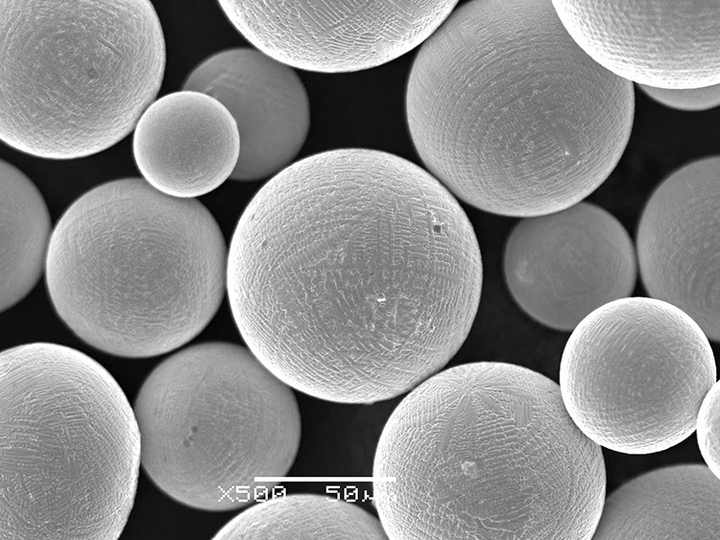
Inconel 625 is a nickel-chromium-molybdenum alloy with additions of iron, niobium and titanium. The chemical composition of Inconel 625 powder is given below:
Element | Composition Range |
---|---|
Nickel (Ni) | 58.0 – 63.0% |
Chromium (Cr) | 20.0 – 23.0% |
Molybdenum (Mo) | 8.0 – 10.0% |
Iron (Fe) | Maximum 5.0% |
Niobium (Nb) + Tantalum (Ta) | 3.15 – 4.15% |
Titanium (Ti) | Maximum 0.40% |
Carbon (C) | Maximum 0.10% |
Manganese (Mn) | Maximum 0.50% |
Silicon (Si) | Maximum 0.50% |
Aluminum (Al) | Maximum 0.40% |
Cobalt (Co) | Maximum 1.0% |
Sulfur (S) | Maximum 0.015% |
Phosphorus (P) | Maximum 0.015% |
Boron (B) | Maximum 0.006% |
The high nickel and chromium content gives Inconel 625 excellent resistance to corrosion, oxidation and other chemical attacks. Molybdenum enhances strength at high temperatures. Niobium provides solid solution strengthening and forms carbides for precipitation hardening. Iron improves high temperature strength. Titanium and aluminum combine with niobium to form hardening precipitates.
Precise control over the composition, powder characteristics and processing parameters allows Inconel 625 powder to deliver consistent, reliable high-performance properties and performance.
Properties of Inconel 625 Powder
Inconel 625 exhibits an excellent combination of high strength, good workability and outstanding corrosion resistance. Its properties make it suitable for critical applications under extreme conditions.
Mechanical Properties
- Excellent tensile strength ranging from 760 – 1380 MPa
- 0.2% Yield strength from 450 – 1210 MPa
- Elongation ranging between 30 – 55%
- Reduction in area up to 75%
- Impact strength up to 300 J at room temperature
- Hardness of 25 – 33 HRc
Physical Properties
- Melting range of 1290 – 1350°C
- Density of 8.44 g/cm3
- Electrical resistivity of 1.25 microhm-cm at 20°C
- Thermal conductivity of 9.8 W/m-K at 20°C
- Modulus of elasticity 205 GPa
- Coefficient of thermal expansion 13 μm/m-°C
Thermal Properties
- Excellent high temperature strength up to 1000°C
- Rupture strength above 250 MPa at 800°C
- Continuous service up to 980°C
- Oxidation resistance in intermittent service to 1150°C
Corrosion Resistance
- Resists pitting and crevice corrosion in oxidizing, neutral and reducing environments
- Excellent resistance to stress corrosion cracking
- Highly resistant to acids like hydrochloric, sulfuric, acetic and phosphoric
- Resistant to alkaline solutions, organic acids and halogen salts
Fatigue Strength
- Excellent fatigue strength and crack growth resistance
- Very high cycles to failure especially in aged tempers
- Used for dynamic, cyclically loaded components
Cryogenic Properties
- Retains high ductility and toughness at cryogenic temperatures
- Impressive strength at -196°C
- Suitable for liquefied gas storage and transportation
Magnetic Permeability
- Displays low magnetic permeability
- Relative permeability ≤1.002 up to saturation
- Used for special applications requiring non-magnetic behavior
Other Characteristics
- Good fabrication characteristics – easily welded, formed, machined
- Excellent finishing and polishing characteristics
- Low neutron absorption cross-section
- Non-magnetic up to the Curie point of -35°C
Applications and Uses of Inconel 625 Powder
The combination of strength, ductility, fatigue resistance and outstanding corrosion resistance makes Inconel 625 suitable for a wide range of critical applications in extreme environments.
Aerospace Applications
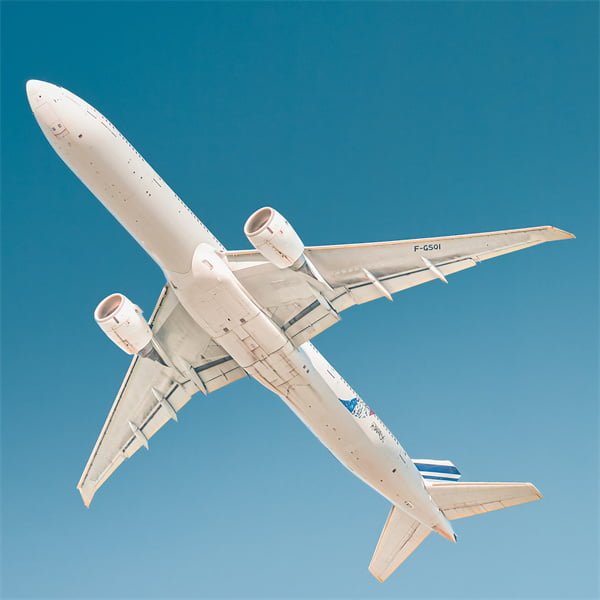
- Exhaust cones and ducts for jet engines
- Thrust reverser components and interior ducts
- Turbine engine hot section parts like seals, cases, blades, disks
- Fasteners like bolts, screws and nuts
- Sections of aircraft ducting systems
- Welded fabricated structures and assemblies
Chemical Processing Industry
- Heat exchanger tubing for corrosive chemicals
- Valves, pumps, fasteners and piping systems
- Linings for chemical reaction vessels and tanks
- Autoclave and pressure vessel components
Marine Engineering
- Shafts, propellers, fasteners for marine engines and structures
- Piping systems, pump housings, valves for desalination plants
- Components exposed to seawater corrosion like tubes, pipes, tanks
Oil and Gas Production
- Downhole tubing, wellhead components and fasteners
- Valves, pumps and piping systems for extraction and refining
- Subsea oilfield equipment like connectors, wellhead parts
Pollution Control Equipment
- Scrubber tubes, stacks, ducts and exhaust components
- Thermowells, fasteners and hangers for catalytic converters
- Components for handling hot corrosive gases
Food Processing Industry
- Tanks, valves, pumps, pipe fittings and fasteners
- Heat exchangers, evaporators and sterilizing equipment
- Components for handling acids, alkalis and salts
Nuclear Applications
- Cladding material for nuclear fuel elements
- Spacer grids and springs in nuclear fuel assemblies
- Reactor internals and breeder reactor components
Cryogenic Applications
- Storage tanks and transportation vessels for liquefied gases
- Cryogenic pipework and piping components
- Structural parts exposed to low cryogenic temperatures
Inconel 625 Powder Suppliers
Inconel 625 powder is widely manufactured and distributed globally. Reputable suppliers with high quality materials and extensive technical expertise include:
Supplier | Description |
---|---|
Sandvik | Leading supplier of metal powders for AM. Gas atomized Inconel 625 powder as per ASTM F3056. |
Met3DP | Metal3DP Technology Co., LTD is a leading provider of additive manufacturing solutions headquartered in Qingdao, China. |
Praxair | Produces high purity metal powders for additive manufacturing. |
AP&C | Specializes in gas atomization of nickel superalloys like Inconel 625. |
H.C. Starck Solutions | Range of cobalt, nickel and iron based alloy powders. |
Höganäs | Swedish company specializing in metal powders for industry. |
LPW Technology | UK based supplier of metal powders and wire for AM. |
SLM Solutions | Provides optimized parameters and powder for SLM equipment. |
Specify the powder size, composition, production method (gas atomized, plasma rotating electrode process or vacuum induction melting), and quality certification required from suppliers. Perform full traceability and quality checks before use.
Inconel 625 Powder Pricing
Inconel 625 powder prices depend on factors like quantity, powder characteristics, supplier margins and geographical location. Indicative pricing for gas atomized Inconel 625 powders suitable for laser or electron beam melting:
Powder Quantity | Price Range |
---|---|
1 kg | $120 – $180 per kg |
10 kg | $100 – $160 per kg |
100 kg | $90 – $150 per kg |
1,000 kg | $80 – $140 per kg |
Larger Inconel 625 powder orders in excess of 1,000 kg typically receive discounted rates from leading manufacturers. Prices also vary based on additional requirements like particle size distribution, flowability, quality checks and special packing.
Metal3DP provides high quality in-stock Inconel 625 powder with low minimum order quantities and fast delivery times. We offer customized solutions for research institutions and companies across various industries.
Metal3DP’s Inconel 625 powder is manufactured using an inert gas atomization process to achieve spherical morphology and tight particle size distribution. Our in-house sieving ensures powders meet your specific requirements, with particle sizes ranging from 15-45 microns for additive manufacturing or up to 150 microns for MIM feedstock production.
Metal3DP can offer small trial sizes of Inconel 625 from 1kg up to bulk quantities of 1000kg. Our inventory allows rapid shipment within 3-5 days after order confirmation. We take pride in our responsive customer service and technical assistance.
For more details on our Inconel 625 powder offerings or custom requirements, please contact our sales team. We look forward to helping with your nickel alloy powder needs.
How to Select Inconel 625 Powder?
Consider the following factors when selecting Inconel 625 powder for AM applications:
- Chemical composition – Confirm powder composition conforms to specified standards for Inconel 625 like ASTM F3056.
- Particle size – Select powder based on AM process and desired resolution. Laser processes use 5 – 45 microns. Electron beam uses 45 – 150 microns.
- Particle shape – Spherical powder morphology ensures good flowability and packing density.
- Particle size distribution – Tight distributions allow high packing density and repeatable performance.
- Flowability – Measure flow rates through Hall flowmeter or Freeman Technology tester.
- Apparent density and tap density – Higher density improves performance. Tap density should exceed 60% of theoretical max density.
- Surface oxide content – Lower oxygen content results in higher density. Aim for less than 0.4% oxygen.
- Microstructure – Powder should have fine, uniform grain structure without porosity or impurities.
- Shape complexity – Spherical powders perform better for complex geometries, thin walls and lattice structures.
- Quality certification – Confirm compliance to specifications like ASTM F3056. Review test reports.
- Process optimization – Match powder characteristics to printer, parameters and requirements.
- Technical expertise – Select suppliers with extensive application experience and data.
Thoroughly evaluate powder samples before purchasing large quantities. Perform test builds to dial in parameters and validate performance.
How to Store Inconel 625 Powder?
Inconel 625 powder requires proper storage and handling to maintain powder quality and prevent contamination:
- Store containers in a cool, dry location away from sunlight and moisture.
- Ideal storage temperatures are below 25°C at 35-60% relative humidity.
- Avoid temperature fluctuations which can cause moisture condensation.
- Use inert gas purging if storing opened containers for extended periods.
- Ensure containers are properly sealed after taking test samples to avoid oxidation.
- Restrict access to powder storage areas to prevent unauthorized handling.
- Avoid plastic containers which may interact with powders. Use original manufacturer’s packing.
- Prevent cross-contamination when storing multiple powders in same location.
- Follow safety precautions – use gloves, masks and minimize dust.
- Refer to manufacturer guidelines and SDS for additional safety and storage instructions.
Proper storage maximizes shelf life, prevents powder degradation and delivers consistent, high quality results.
How to Inspect and Test Inconel 625 Powder?
Incoming powder lots should be thoroughly inspected and tested to ensure they meet all chemical, physical and microstructural requirements.
Typical quality tests performed include:
Test | Description | Equipment Used |
---|---|---|
Chemical analysis | Confirms elemental composition via XRF, ICP-OES or LECO analysis | X-ray fluorescence analyzer, optical emission spectrometer |
Particle size distribution | Measures size range and distribution of powder particles | Laser diffraction particle size analyzer |
Powder morphology | Checks particle shape and surface structure with SEM | Scanning electron microscope |
Flow rate | Determines powder flowability through a standardized funnel | Hall flowmeter, powder rheometer |
Apparent density | Measures the density of a fixed mass of powder | Scott volumeter test |
Tap density | Assesses packing density under vibration/tapping | Tap density measurement apparatus |
Moisture analysis | Quantifies moisture pickup during storage/transit | Infrared moisture analyzers |
Oxygen and nitrogen | Oxygen content impacts powder performance | Inert gas fusion analyzer |
Microstructure | Internal structure inspected for defects | Optical and electron microscopy |
Retain samples from each lot for periodic re-testing and comparison after powder is put into use. Analyze used powder from reactors to confirm it has not degraded during processing.
How to Process Inconel 625 Powder?
Inconel 625 powder can be processed via laser powder bed fusion (LPBF), electron beam melting (EBM) and directed energy deposition (DED) additive manufacturing techniques. Here are some guidelines for processing parameters:
Laser Powder Bed Fusion
- Use powders in 10-45 micron size range
- Laser power: 100-500W
- Scan speed: 300-1000 mm/s
- Hatch spacing: 50-200 μm
- Layer thickness: 20-100 μm
- Preheat at 90-120°C to prevent residual stresses
- Use support structures for overhangs and complex geometries
- Perform stress relieving heat treatment after printing
Electron Beam Melting
- Powder size range of 45-150 microns recommended
- Beam power: 3-10 kW
- Beam speed: 1000-10,000 mm/s
- Beam focus: 2-15 mA/0.1-0.5 mm diameter
- Layer thickness: 50-200 μm
- Preheat at 650-950°C to prevent charging
- Minimize support use; easy removal of trapped powder
- Hot isostatic pressing gives tighter densities
Directed Energy Deposition
- Powder feed rate: 3-15 g/min
- Laser power: 500-2000 W
- Travel speed: 5-25 mm/s
- Powder carrier gas: Argon at 10-25 slpm
- Multiple passes to build height
- Interpass temperature: 150-260°C
Pros and Cons of Inconel 625 Powder
Advantages
- Excellent corrosion resistance in wide range of aggressive environments
- Retains high strength and toughness at both cryogenic and elevated temperatures
- Outstanding fatigue and thermal fatigue resistance
- Resists oxidation and carcinogenic effects at high temperatures
- Better weldability than other nickel superalloys
- More fabricable than stainless steels – easily formed and machined
- Lower costs compared to other nickel and cobalt alloys
- Readily produced in a range of product forms including powder
Limitations
- Less strong than iron, cobalt or nickel-based superalloys at extreme temperatures
- Not recommended for high stress applications above 550°C
- Susceptible to stress corrosion cracking above 260°C
- Lower hardness than high carbon/boron steels
- Not suitable for highly reducing acids like hydrofluoric acid
- Limited high temperature capability up to 705°C compared to superalloys
- Higher costs than nickel-chromium alloys like Hastelloy C276
- Powder can be more expensive than wire for directed energy deposition
How Inconel 625 Compares to Other Nickel Alloys
- Higher tensile and fatigue strength but lower rupture strength
- Superior corrosion resistance in oxidizing media
- Greater fabricability – easier to form and weld
- Higher oxidation resistance at extreme temperatures
- Lower cost powder and wire forms
- Much better fabricability and weldability
- Higher ductility and toughness
- Greater strength in annealed state
- Superior low temperature tensile and impact properties
- Better corrosion resistance in oxidizing environments
Vs Monel 400 Powder
- Much higher strength across all temperatures
- Significantly better corrosion resistance
- Retains strength after prolonged exposure at high temperatures
- More resistant to pitting and crevice corrosion
- Higher hardness and wear resistance
Vs Incoloy 800 Powder
- Far superior high temperature tensile and rupture strength
- Significantly greater corrosion resistance
- Does not require stabilization treatment
- Higher creep resistance and microstructural stability
- Less susceptible to sensitization and intergranular attack
Vs Iconel 600 Powder
- Much higher strength at both room and elevated temperatures
- Significantly better corrosion resistance across all mediums
- Superior oxidation resistance at high temperatures
- Resists pitting, crevice corrosion and intergranular attack
- Does not require annealing or stabilization treatment
Frequently Asked Questions about Inconel 625 Powder
Q: What types of Inconel 625 powder can be used for AM?
A: Gas atomized powder with spherical particle morphology delivers the best performance for AM processes like DED, EBAM and LPBF.
Q: What are the effects of chemical composition on Inconel 625 properties?
A: Nickel provides corrosion resistance. Chromium supplies oxidation resistance. Molybdenum contributes high temperature strength and creep resistance. Iron improves workability. Niobium, titanium and aluminum form strengthening precipitates.
Q: What heat treatment is used for Inconel 625?
A: Solution annealing at 1065-1205°C is performed, followed by rapid air cooling and aging at 760-870°C for 10-20 hours to precipitation harden the alloy.
Q: What is the Curie temperature of Inconel 625?
A: Inconel 625 has a Curie temperature of approximately -35°C. Below this temperature it displays ferromagnetic properties.
Q: What welding processes can be used to join Inconel 625 parts?
A: GTAW and GMAW welding can be used. Proper preheat, interpass temperature control, and post weld heat treatment are critical. EB and laser welding processes are also possible.
Q: What is the typical surface finish achievable with Inconel 625 AM parts?
A: With processes like DED and LPBF, surface roughness Ra values under 25 μm are possible. Additional finishing like CNC machining, grinding or EDM can further improve surface finish.
Q: Are Inconel 625 parts heat treatable after additive manufacturing?
A: Yes, stress relieving, full solution annealing and aging heat treatments can be performed to enhance properties as per specifications like AMS 5666.
Q: What powder bed temperatures are used in LPBF of Inconel 625?
A: Preheating the powder bed to 90-150°C before laser exposure helps reduce residual stresses in printed Inconel 625 parts.
Q: Is Inconel 625 stronger than stainless steel?
A: Yes, Inconel 625 has much higher tensile and yield strength compared to 300 series stainless steels, along with far superior corrosion resistance.
Conclusion
In summary, Inconel 625 is an exceptional nickel-chromium-molybdenum superalloy capable of maintaining high strength, toughness and corrosion resistance at extreme temperatures up to 1000°C. Its well-balanced composition enables outstanding fabricability and weldability compared to other nickel alloys.
In powder form, Inconel 625 is widely used across aerospace, chemical, oil & gas, pollution control, food processing and nuclear industries where resistance to thermal fatigue, oxidation and aggressive chemical environments are critical.
With additive manufacturing, complex and high performance Inconel 625 components can be fabricated by laser, electron beam and directed energy deposition processes. By selecting the optimal powder characteristics, adapting process parameters, and applying post-treatment, producers can leverage the benefits of this alloy for critical applications.
Share On
MET3DP Technology Co., LTD is a leading provider of additive manufacturing solutions headquartered in Qingdao, China. Our company specializes in 3D printing equipment and high-performance metal powders for industrial applications.
Inquiry to get best price and customized Solution for your business!
Related Articles
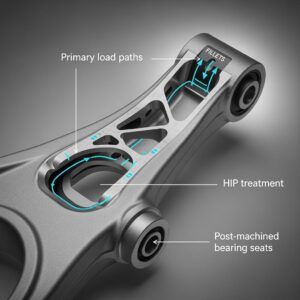
Metal 3D Printing for U.S. Automotive Lightweight Structural Brackets and Suspension Components
Read More »About Met3DP
Recent Update
Our Product
CONTACT US
Any questions? Send us message now! We’ll serve your request with a whole team after receiving your message.