Inconel 718 Powder: Price,Specifications
Table of Contents
Inconel 718 is a high-performance nickel-chromium-based superalloy exhibiting excellent strength and corrosion resistance at elevated temperatures up to 700°C. This guide provides a detailed overview of Inconel 718 powder covering its characteristics, applications, manufacturing process, specifications, pricing, pros and cons, and frequently asked questions.
Overview of Inconel 718 Powder
Inconel 718 powder contains nickel, chromium, niobium, molybdenum, titanium and aluminum as its major alloying elements. Key properties:
- High yield, tensile and creep rupture strength at temperatures up to 700°C
- Good fatigue and corrosion resistance
- Age hardenable microstructure
- Excellent cryogenic properties
- Higher strength compared to Inconel 625
Inconel 718 powder is used in aerospace components like gas turbine disks, rocket motor casings, cylinders, pumps and valves requiring high temperature capability.
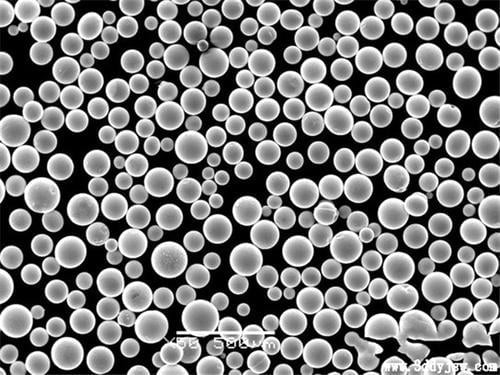
Applications of Inconel 718 Powder
Inconel 718 powder finds usage in demanding applications across industries:
Industry | Applications |
---|---|
Aerospace | Engine components, rocket motors, actuators, hovercraft parts |
Oil and gas | Wellhead equipment, downhole tools, valves, pumps |
Nuclear | Reactor vessels, transfer tube assemblies |
Automotive | Turbocharger rotors, valves, exhaust manifolds |
Chemical | Heat exchangers, pressure vessels, process piping |
Benefits offered by Inconel 718:
- High temperature strength for improved efficiency
- Corrosion resistance in harsh environments
- Excellent fatigue properties for rotating components
- Good cryogenic properties down to -253°C
- Oxidation resistance up to 700°C
Manufacturing Process for Inconel 718 Powder
Inconel 718 powder can be produced via processes like:
- Gas Atomization – Most common method where molten alloy is disintegrated by nitrogen/argon gas jets into fine droplets that solidify into powder particles. Provides spherical powder preferred for AM applications.
- Rotating Electrode Process – Electrode of alloy is spun at high speeds in an inert gas atmosphere and melted by an electric arc to generate fine droplets that solidify into powder.
- Plasma Rotating Electrode Process – Arc melting is done using ionized plasma jet instead of electric arc. It yields highly spherical powder ideal for AM.
- Vacuum Induction Melting – Alloy is induction melted under vacuum and the melt is then converted into powder using gas or water atomization process.
Gas atomization and PREP methods allow close control over powder characteristics like particle size distribution, morphology, oxide levels and microstructure.
Specifications of Inconel 718 Powder
Inconel 718 powder is available with the following specifications:
Parameter | Specification |
---|---|
Alloy chemistry | 50-55% Ni, 17-21% Cr, 4.75-5.5% Nb+Ta, 2.8-3.3% Mo |
Particle size | 10 to 150 microns |
Particle shape | Spherical, irregular |
Size distribution | Customizable based on application |
Purity | Up to 99.9% |
Oxygen level | <300 ppm |
Apparent density | 2 – 4.5 g/cc |
Flow rate | Up to 25 s/50g |
The specifications can be customized as per requirements for composition, particle characteristics, purity levels, density, and flow properties.
Suppliers and Pricing of Inconel 718 Powder
Some of the major suppliers and pricing for Inconel 718 powder include:
Supplier | Location | Price Range |
---|---|---|
Sandvik | Germany | $90 – $220 per kg |
Praxair | USA | $100 – $250 per kg |
AP&C | Canada | $110 – $200 per kg |
Met3DP | China | $70 – $150 per kg |
Tekna | Canada | $140 – $280 per kg |
The price varies based on:
- Purity levels
- Particle size and distribution
- Sphericity and flowability
- Production method used
- Order quantity
- Additional analysis or treatment
Prices are higher for spherical and controlled particle size distribution powder.
Pros and Cons of Inconel 718 Powder
Pros | Cons |
---|---|
High strength at elevated temperatures | Expensive compared to steel and titanium alloys |
Excellent corrosion resistance | Lower thermal conductivity than copper alloys |
Good fatigue strength and cryogenic toughness | Challenging to machine and grind |
Age hardening capability | Subject to strain-age cracking |
Oxidation resistance up to 700°C | Requires heat treatment for optimal properties |
Non-magnetic property | Limited availability for larger sections |
Ideal for critical applications despite higher cost. Limitations include lower thermal conductivity, machinability issues, propensity for cracking during forming.
FAQs
Q: What is the typical composition range of Inconel 718 alloy?
A: Typical composition is 50-55% Ni, 17-21% Cr, 4.75-5.5% Nb, 2.8-3.3% Mo, 0.65-1% Ti, 0.2-0.8% Al and trace elements like Co, Cu, Mn, Si, P, S.
Q: What particle size is recommended for Inconel 718 powder for AM?
A: For powder bed fusion AM, Inconel 718 powder with particle size range of 15-45 microns is typically used. Finer powder below 100 microns improves density and properties.
Q: What affects the pricing of Inconel 718 powder?
A: Pricing is affected by purity levels, particle characteristics like size range and sphericity, production method, order volume, additional analysis or treatment, and supplier profit margins.
Q: What is the role of niobium in Inconel 718 alloy?
A: Niobium is the key strengthening element in Inconel 718. It causes precipitation of intermetallic phases gamma double prime and gamma prime for high temperature strength and corrosion resistance.
Q: What are the typical applications of Inconel 718 alloy?
A: Inconel 718 is widely used in aircraft engines, rockets, pumps, nuclear reactors, and cryogenic tankage due to its high strength at elevated temperatures and good corrosion resistance.
Q: What are the alternatives to Inconel 718 for high temperature applications?
A: Alternatives include stainless steels like 310 and 330, iron-nickel alloys, cobalt alloys MP159 and FSX-414, and titanium alloys Ti-6242 and IMI 834. However, Inconel 718 remains superior.
Q: How does Inconel 718 compare with Inconel 625 in terms of properties?
A: Inconel 718 has higher tensile and creep rupture strength compared to Inconel 625 but lower oxidation and corrosion resistance. Inconel 625 is easier to weld and fabricate.
Q: What are the latest developments in Inconel 718 alloy?
A: New variants like Allvac 718Plus offer higher strength through composition modification. Research is ongoing to improve processing methods and properties using powder metallurgy and additive manufacturing.
Q: What makes Inconel 718 suitable for 3D printing applications?
A: Fine Inconel 718 powder with controlled particle size enables printing complex shapes with high density and superior mechanical properties compared to cast alloy components.
Conclusion
Inconel 718 nickel-based superalloy powder provides an exceptional combination of high temperature strength, corrosion resistance, fatigue properties and cryogenic toughness for critical applications where performance requirements are paramount. This guide summarizes Inconel 718 powder characteristics, manufacturing methods, pricing, pros and cons, and FAQs to support engineers, designers and technical teams in adopting this advanced material. With its unique properties, Inconel 718 powder will continue seeing high demand across aerospace, gas turbines, chemical and nuclear sectors.
Share On
MET3DP Technology Co., LTD is a leading provider of additive manufacturing solutions headquartered in Qingdao, China. Our company specializes in 3D printing equipment and high-performance metal powders for industrial applications.
Inquiry to get best price and customized Solution for your business!
Related Articles
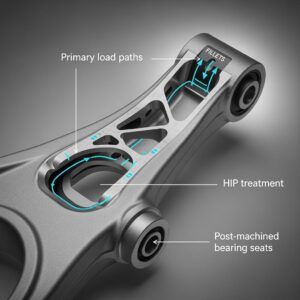
Metal 3D Printing for U.S. Automotive Lightweight Structural Brackets and Suspension Components
Read More »About Met3DP
Recent Update
Our Product
CONTACT US
Any questions? Send us message now! We’ll serve your request with a whole team after receiving your message.