verview of Inconel Powder 3D Printers
Table of Contents
Inconel powder 3D printers are specialized additive manufacturing systems designed to work with Inconel, a family of austenitic nickel-chromium-based super alloys. These alloys are known for their exceptional strength, oxidation resistance, and ability to withstand extreme temperatures, making them ideal for applications in the aerospace, automotive, and energy industries.
Inconel 3D printing allows for the creation of complex geometries and intricate designs that would be difficult or impossible to achieve through traditional manufacturing methods. By fusing thin layers of Inconel powder together, these printers can produce highly intricate and durable components with excellent dimensional accuracy and minimal material waste.
Inconel Powder 3D Printer Guide
Inconel powder 3D printers are typically industrial-grade machines that employ either powder bed fusion (PBF) or directed energy deposition (DED) technologies. PBF processes, like selective laser melting (SLM) and electron beam melting (EBM), involve selectively melting and fusing thin layers of Inconel powder according to a computer-aided design (CAD) model. DED processes, on the other hand, involve depositing and fusing Inconel powder directly onto a substrate using a focused energy source, such as a laser or electron beam.
Inconel Powder 3D Printer Types
Printer Type | Technology | Advantages | Limitations |
---|---|---|---|
Selective Laser Melting (SLM) | Powder Bed Fusion (PBF) | High precision, excellent surface finish, suitable for complex geometries | Limited build volume, relatively slow build rate |
Electron Beam Melting (EBM) | Powder Bed Fusion (PBF) | Fast build rate, ideal for high-temperature applications, stress-relieved parts | Requires a vacuum environment, rougher surface finish |
Direct Energy Deposition (DED) | Directed Energy Deposition | Large build volumes, multi-material capabilities, good for repair and coating applications | Lower resolution and surface finish compared to PBF |
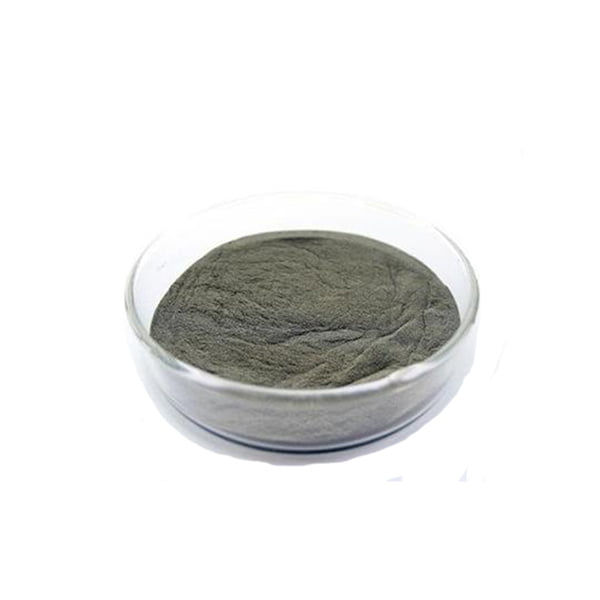
Inconel 3D Printing Process
The Inconel 3D printing process typically involves the following steps:
- CAD Modeling: A 3D model of the desired component is created using computer-aided design (CAD) software.
- File Preparation: The CAD model is then converted into a compatible file format (e.g., STL, AMF) and sliced into thin layers for the printer to interpret.
- Powder Preparation: Inconel powder is carefully prepared and loaded into the printer’s powder delivery system.
- Build Setup: The build platform is prepared, and the printer is calibrated for the specific Inconel alloy and build parameters.
- Layer-by-Layer Fabrication: The printer selectively melts and fuses layers of Inconel powder according to the digital model, creating the desired component.
- Post-Processing: After the build is complete, the component may undergo various post-processing steps, such as heat treatment, surface finishing, or machining, depending on the application requirements.
Inconel Powder 3D Printer Capabilities
Capability | Details |
---|---|
Build Volume | Ranges from desktop-sized build chambers to large-scale industrial systems |
Materials | Capable of printing with various Inconel alloys, including Inconel 625, 718, and others |
Precision | Typical layer thicknesses range from 20 to 100 microns, providing excellent dimensional accuracy |
Feature Resolution | Capable of producing intricate geometries and internal features down to sub-millimeter levels |
Surface Finish | As-built surface finishes can vary from rough to near-mirror depending on the process and post-processing |
Customization | Some systems offer customizable build parameters, materials, and post-processing options |
Inconel Powder 3D Printer Suppliers and Price Range
Supplier | Printer Model | Price Range (USD) |
---|---|---|
EOS | EOS M 290 (EBM) | $800,000 – $1,200,000 |
SLM Solutions | SLM 500 (SLM) | $600,000 – $900,000 |
Concept Laser | Concept Laser M2 (SLM) | $500,000 – $800,000 |
Optomec | LENS 850-R (DED) | $400,000 – $700,000 |
3D Systems | DMP Flex 350 (DED) | $300,000 – $600,000 |
Note: Prices can vary based on configuration, accessories, and regional pricing.
Installation, Operation, and Maintenance of Inconel Powder 3D Printers
Aspect | Details |
---|---|
Installation | Typically requires a dedicated facility with appropriate power, ventilation, and safety systems |
Operator Training | Extensive training is necessary for safe and effective operation of these complex systems |
Material Handling | Proper handling and storage of Inconel powders is crucial to ensure consistent print quality |
Maintenance | Regular maintenance, including cleaning, calibration, and component replacements, is essential |
Safety Considerations | Appropriate personal protective equipment (PPE) and safety protocols must be followed |
Choosing an Inconel Powder 3D Printer Supplier
When selecting an Inconel powder 3D printer supplier, it’s essential to consider the following factors:
Factor | Considerations |
---|---|
Application Requirements | Evaluate the printer’s capabilities in terms of build volume, materials, precision, and feature resolution |
Production Volume | Assess the printer’s throughput and scalability to meet your production needs |
Service and Support | Consider the supplier’s technical support, training, and maintenance services |
Certifications | Ensure the supplier meets relevant industry certifications and standards |
Total Cost of Ownership | Factor in the initial investment, operating costs, consumables, and maintenance expenses |
Pros and Cons of Inconel Powder 3D Printing
Pros | Cons |
---|---|
Ability to produce complex geometries | High initial investment and operating costs |
Excellent material properties (strength, temperature resistance) | Limited build volumes in some systems |
Minimal material waste compared to subtractive manufacturing | Potential for residual stresses and defects |
Customization and design flexibility | Strict material handling and safety requirements |
Potential for lightweighting and performance optimization | Post-processing may be required for certain applications |
Advantages and Limitations of Inconel Powder 3D Printers
Advantages | Limitations |
---|---|
Ability to create intricate internal features and complex geometries | Build volumes are typically smaller compared to traditional manufacturing methods |
Excellent mechanical properties and high-temperature performance | Strict material handling and safety protocols are required |
Design flexibility and customization potential | Potential for residual stresses and defects in printed components |
Minimal material waste compared to subtractive manufacturing | High initial investment and operating costs |
Potential for lightweighting and performance optimization | Limited choice of materials (restricted to Inconel alloys) |
Note: The advantages and limitations may vary depending on the specific printer model, application, and user requirements.
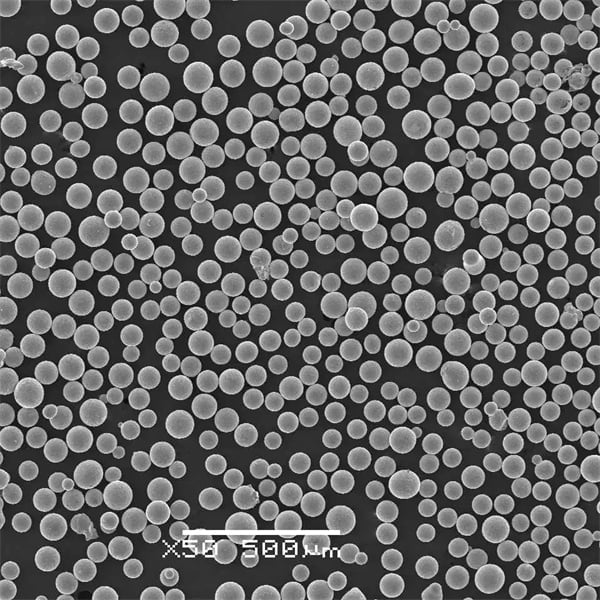
FAQ
Question | Answer |
---|---|
What industries commonly use Inconel powder 3D printers? | Aerospace, automotive, energy, and other sectors that require high-performance components with exceptional strength and temperature resistance. |
How does Inconel 3D printing compare to traditional manufacturing methods? | Inconel 3D printing allows for the creation of complex geometries and internal features that would be difficult or impossible to achieve through conventional methods like casting or machining. However, build volumes are typically smaller, and the process requires stricter material handling and safety protocols. |
What are the typical layer thicknesses and feature resolutions achievable with Inconel 3D printers? | Layer thicknesses typically range from 20 to 100 microns, and feature resolutions can reach sub-millimeter levels, allowing for the production of intricate geometries and internal features. |
Can Inconel 3D printers work with other materials besides Inconel alloys? | Most Inconel 3D printers are designed specifically for Inconel alloys, though some systems may offer limited compatibility with other nickel-based superalloys or high-temperature materials. |
How does the surface finish of 3D-printed Inconel components compare to traditionally manufactured parts? | As-built surface finishes can vary from rough to near-mirror, depending on the specific printing process and parameters used. Post-processing steps, such as machining or surface finishing, may be required to achieve desired surface qualities. |
What are the typical maintenance requirements for Inconel 3D printers? | Regular maintenance, including cleaning, calibration, and component replacements, is essential to ensure consistent print quality and system performance. Proper handling and storage of Inconel powders are also crucial. |
How do I choose the right Inconel 3D printer supplier? | Consider factors such as application requirements, production volume, service and support, certifications, and total cost of ownership when selecting a supplier. Additionally, evaluate the printer’s capabilities in terms of build volume, materials, precision, and feature resolution. |
Share On
MET3DP Technology Co., LTD is a leading provider of additive manufacturing solutions headquartered in Qingdao, China. Our company specializes in 3D printing equipment and high-performance metal powders for industrial applications.
Inquiry to get best price and customized Solution for your business!
Related Articles
About Met3DP
Recent Update
Our Product
CONTACT US
Any questions? Send us message now! We’ll serve your request with a whole team after receiving your message.
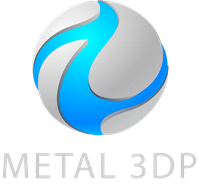
Metal Powders for 3D Printing and Additive Manufacturing