Precision Instrument Waveguides 3D Printed in Invar
Table of Contents
Introduction to 3D Printed Radar Waveguides
In today’s rapidly evolving technological landscape, the demand for high-performance, intricate components is ever-increasing. Among these critical elements are radar waveguides, essential conduits for transmitting electromagnetic waves in radar systems. Traditionally manufactured through subtractive methods, these crucial parts are now being revolutionized by metal additive manufacturing, also known as metal 3D printing. This innovative approach offers unparalleled design freedom, reduced lead times, and the ability to optimize performance characteristics. For industries like aerospace, defense, telecommunications, and meteorology, where precision and reliability are paramount, metal 3D printing of radar waveguides presents a transformative solution. At Metal3DP, we are at the forefront of this revolution, providing advanced metal 3D printing equipment and high-performance metal powders to meet the demanding needs of these sectors. Our commitment to industry-leading print volume, accuracy, and reliability ensures that mission-critical parts, like precision instrument waveguides, are manufactured to the highest standards.
What are Precision Instrument Waveguides Used For?
Precision instrument waveguides serve as the backbone for transmitting high-frequency electromagnetic waves with minimal signal loss and distortion. Their primary function is to guide these waves between different components of a radar system, such as the transmitter, receiver, and antenna. The specific applications of these waveguides are diverse and span numerous critical industries:
- Aerospace and Defense: In radar systems for air traffic control, weather monitoring, and military applications, waveguides ensure accurate signal transmission for detection, tracking, and communication. Their precision is crucial for the reliability of navigation systems and surveillance equipment.
- Telecommunications: With the advent of 5G and beyond, high-frequency signal transmission is vital. Waveguides are used in base stations and satellite communication systems to maintain signal integrity over short distances.
- Medical Imaging: Advanced medical imaging techniques like MRI and specialized X-ray systems utilize waveguides to generate and direct electromagnetic waves for precise diagnostics.
- Scientific Instrumentation: Research facilities and laboratories employ waveguides in various scientific instruments, including spectrometers and particle accelerators, where controlled transmission of electromagnetic energy is essential for experimentation and data acquisition.
- Automotive Industry: With the increasing integration of radar technology in advanced driver-assistance systems (ADAS) for features like adaptive cruise control and blind-spot detection, precision waveguides are becoming integral components in vehicles.
- Industrial Manufacturing: Certain industrial sensors and measurement devices rely on waveguides for non-destructive testing and process control.
The intricate designs and tight tolerances required for these applications often make traditional manufacturing methods complex and costly. Metal 3D printing, particularly using materials like Invar and Ti-6Al-4V, offers a flexible and efficient alternative for producing these critical components. Metal3DP’s metal 3D printing services provide the precision and material properties necessary for these demanding applications.

Why Use Metal 3D Printing for Precision Instrument Waveguides?
Opting for metal 3D printing over conventional manufacturing techniques for precision instrument waveguides offers a multitude of compelling advantages:
- Design Freedom and Complexity: Additive manufacturing allows for the creation of complex geometries that are difficult or impossible to achieve with traditional methods like machining or casting. This includes intricate internal channels, optimized tapers, and integrated features, leading to improved performance and reduced assembly requirements.
- Material Optimization: Metal 3D printing enables the use of specialized materials like Invar (FeNi36) and Ti-6Al-4V, which offer specific properties crucial for waveguide performance, such as low thermal expansion (in the case of Invar) and high strength-to-weight ratio (in the case of Ti-6Al-4V). Metal3DP’s range of high-quality metal powders is specifically optimized for these demanding applications.
- Weight Reduction: In industries like aerospace and automotive, weight is a critical factor. 3D printing allows for the creation of lightweight designs with optimized material distribution, without compromising structural integrity or performance.
- Reduced Lead Times: Traditional manufacturing processes often involve lengthy tooling and setup times. Metal 3D printing significantly reduces these lead times, allowing for faster prototyping and production of custom waveguides, especially beneficial for low-volume or highly specialized applications.
- Customization and Rapid Prototyping: The ability to quickly iterate on designs and produce customized waveguides without the need for new tooling makes metal 3D printing ideal for rapid prototyping and the development of tailored solutions for specific radar system requirements.
- Reduced Material Waste: Unlike subtractive manufacturing, which generates significant material waste, additive manufacturing builds parts layer by layer, using only the necessary material. This leads to more efficient material utilization and cost savings, particularly with expensive alloys.
- Enhanced Performance: The design flexibility offered by 3D printing allows for the optimization of waveguide geometry to minimize signal loss, improve bandwidth, and enhance overall electromagnetic performance.
By leveraging metal 3D printing, businesses can achieve higher performance, lighter weight, faster turnaround times, and greater design flexibility for their precision instrument waveguides. Metal3DP’s advanced Selective Electron Beam Melting (SEBM) printers are well-suited for producing these intricate components with high accuracy and material integrity.
Recommended Materials and Why They Matter
The choice of material is paramount in determining the performance characteristics of precision instrument waveguides. For demanding applications, two exceptional materials stand out: Invar (FeNi36) and Ti-6Al-4V. Metal3DP offers high-quality powders of both these alloys, manufactured using advanced gas atomization and PREP technologies to ensure high sphericity and flowability, essential for consistent 3D printing.
Invar (FeNi36)
- Composition: Invar is a nickel-iron alloy containing approximately 36% nickel.
- Key Properties and Why They Matter for Waveguides:
- Ultra-Low Coefficient of Thermal Expansion (CTE): This is the most significant property of Invar. Its exceptionally low CTE means that the dimensions of a waveguide made from Invar will remain remarkably stable over a wide range of temperatures. This is crucial for maintaining precise signal transmission and preventing frequency shifts in sensitive radar systems operating in fluctuating thermal environments, such as aerospace or outdoor installations.
- Dimensional Stability: The minimal thermal expansion also contributes to excellent dimensional stability, ensuring consistent performance and preventing mechanical stress on the waveguide and connected components.
- Good Weldability and Machinability: While 3D printing eliminates some of the need for these processes, these properties can be beneficial for post-processing or integration with other system parts.
Ti-6Al-4V
- Composition: Ti-6Al-4V is an alpha-beta titanium alloy composed of approximately 6% aluminum, 4% vanadium, and the balance titanium.
- Key Properties and Why They Matter for Waveguides:
- High Strength-to-Weight Ratio: This alloy offers exceptional strength while being significantly lighter than many other metals. This is a critical advantage in aerospace and automotive applications where weight reduction is paramount for fuel efficiency and performance.
- Excellent Corrosion Resistance: Ti-6Al-4V exhibits superior resistance to corrosion in a wide range of environments, ensuring the long-term reliability and performance of waveguides exposed to harsh conditions.
- Good Fatigue Resistance: Radar systems often operate under cyclic loading conditions. The high fatigue resistance of Ti-6Al-4V ensures the structural integrity and longevity of the waveguide.
- Biocompatibility: In medical imaging applications, the biocompatibility of Ti-6Al-4V can be an important factor.
The selection between Invar and Ti-6Al-4V depends on the specific requirements of the radar waveguide application. If thermal stability is the primary concern, Invar is the ideal choice. If a high strength-to-weight ratio and corrosion resistance are more critical, Ti-6Al-4V offers superior performance. Metal3DP’s expertise in metal additive manufacturing allows us to guide customers in selecting the optimal material for their specific waveguide needs. Sources and related content
Design Considerations for Additive Manufacturing of Waveguides
Designing waveguides for metal 3D printing requires a shift in mindset compared to traditional manufacturing. The layer-by-layer build process offers unique opportunities and imposes specific constraints that engineers must consider to optimize performance, reduce costs, and ensure successful fabrication.
- Topology Optimization: One of the significant advantages of metal 3D printing is the ability to employ topology optimization techniques. This involves using specialized software to mathematically determine the optimal material distribution for a given set of loads and constraints. For waveguides, this can lead to designs with reduced weight and material usage while maintaining or even improving structural integrity and electromagnetic performance. Consider incorporating internal lattices or honeycombs within non-critical areas to minimize weight without sacrificing stiffness.
- Wall Thickness: Maintaining a consistent and appropriate wall thickness is crucial for waveguide performance and printability. Walls that are too thin may be difficult to print and could exhibit insufficient strength or allow for signal leakage. Conversely, overly thick walls can increase weight and material cost. The optimal wall thickness will depend on the material, the printing technology used (e.g., SEBM), and the operating frequency of the waveguide.
- Surface Finish Considerations: The surface finish of the internal walls of a waveguide significantly impacts its electrical performance, particularly at higher frequencies. Rough surfaces can cause scattering and signal loss. When designing for additive manufacturing, consider the inherent surface roughness achievable with the chosen printing process and material. Design orientations that minimize the number of support structures on critical internal surfaces can improve the final finish. Post-processing techniques like polishing or chemical etching may be necessary to achieve the required surface smoothness.
- Support Structure Design: Support structures are often required in metal 3D printing to prevent warping, sagging, and collapse of overhanging features during the build process. For intricate waveguide geometries, careful planning of support placement and removal is essential. Design parts with self-supporting angles where possible to minimize the need for supports, especially within internal channels. When supports are necessary, design them for easy and clean removal to avoid damaging the delicate internal surfaces of the waveguide.
- Feature Integration: Additive manufacturing allows for the integration of multiple features into a single part, reducing the need for assembly. Consider incorporating flanges, mounting features, or cooling channels directly into the waveguide design. This can simplify the overall system, reduce weight, and improve reliability.
- Orientation Optimization: The orientation in which the waveguide is printed can significantly affect its dimensional accuracy, surface finish, and the need for support structures. Careful consideration of the build orientation can optimize these factors and lead to a more efficient and cost-effective manufacturing process. For example, orienting long, thin features vertically might require more support but could improve straightness.
- Internal Channels and Complex Geometries: Metal 3D printing excels at creating complex internal geometries. For waveguides, this opens up possibilities for novel designs that optimize electromagnetic performance, such as complex bends, twists, or integrated filtering structures that would be challenging or impossible to manufacture using traditional methods.
By carefully considering these design principles tailored for additive manufacturing, engineers can unlock the full potential of metal 3D printing to create high-performance, efficient, and cost-effective precision instrument waveguides. Metal3DP’s application development services can provide valuable expertise in optimizing designs for our advanced metal 3D printing processes.
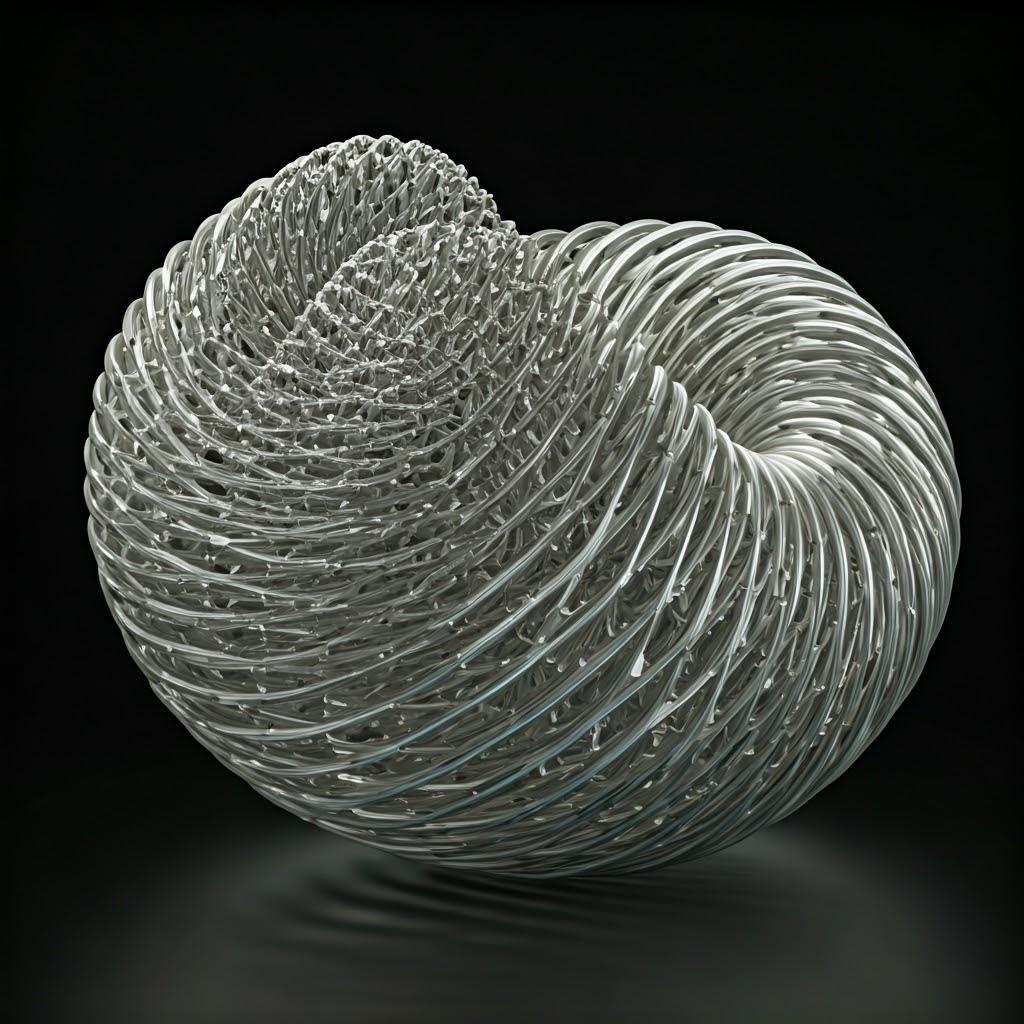
Tolerance, Surface Finish, and Dimensional Accuracy of 3D Printed Waveguides
Achieving the required tolerance, surface finish, and dimensional accuracy is paramount for the functional performance of precision instrument waveguides. Metal 3D printing, particularly Selective Electron Beam Melting (SEBM) technology employed by Metal3DP, offers significant advantages in producing parts with tight specifications. However, understanding the achievable levels and the factors influencing them is crucial.
Tolerance and Dimensional Accuracy:
- Achievable Tolerances: With advanced metal 3D printing processes like SEBM, tolerances of ±0.1 to ±0.2 mm (or even tighter in specific cases with optimized parameters and post-processing) can be achieved for critical dimensions of waveguides. The actual tolerance will depend on factors such as part size, geometry complexity, material, and build orientation.
- Factors Influencing Accuracy:
- Printer Calibration and Accuracy: The inherent accuracy and repeatability of the 3D printer are fundamental. Metal3DP’s printers are engineered for industry-leading accuracy and reliability.
- Material Shrinkage: During the solidification and cooling process, metal powders undergo shrinkage. Accurate prediction and compensation for this shrinkage in the design and process parameters are essential for achieving dimensional accuracy.
- Build Orientation: The orientation of the part on the build platform can influence dimensional accuracy, particularly for overhanging features and complex geometries.
- Support Structures: The placement and removal of support structures can sometimes affect the surface finish and dimensional accuracy of the supported areas.
- Post-Processing: Techniques like CNC machining can be employed for critical surfaces requiring very tight tolerances that might exceed the as-printed capabilities.
Surface Finish:
- Typical Surface Roughness: The as-printed surface finish in metal 3D printing is generally rougher compared to machined surfaces. For SEBM, the typical surface roughness (Ra) can range from 5 to 20 μm, depending on the material, layer thickness, and build parameters.
- Impact on Waveguide Performance: The internal surface finish of a waveguide is critical as it affects signal transmission. Rougher surfaces can lead to increased scattering losses and reduced efficiency, especially at higher frequencies.
- Post-Processing for Improved Surface Finish: Several post-processing techniques can be used to improve the surface finish of 3D printed waveguides:
- Media Blasting: Used to remove partially sintered powder and achieve a more uniform surface texture.
- Polishing (Mechanical or Electrochemical): Can significantly reduce surface roughness to the levels required for high-frequency applications.
- Chemical Etching: A controlled material removal process that can smooth surfaces and reduce roughness.
- Coating: Applying a conductive and smooth coating can improve the electrical performance of the waveguide.
Achieving Desired Specifications:
A combination of careful design for additive manufacturing, optimized printing parameters on high-accuracy machines like those offered by Metal3DP, and appropriate post-processing techniques are essential to achieve the required tolerance, surface finish, and dimensional accuracy for precision instrument waveguides. Collaboration with an experienced metal 3D printing service provider is crucial to ensure these critical specifications are met.
Post-Processing Requirements for 3D Printed Waveguides
While metal 3D printing offers near-net-shape manufacturing capabilities, post-processing steps are often necessary to achieve the final desired properties, dimensions, and surface finish for precision instrument waveguides. The specific requirements will depend on the application, material, and the as-printed characteristics.
- Powder Removal: After the printing process, unbound or partially sintered powder remains on the surface and within any internal channels of the waveguide. This powder must be carefully removed using techniques such as brushing, air blasting, or vacuuming. For complex internal geometries, specialized cleaning methods may be required.
- Support Structure Removal: If support structures were used during printing, they need to be removed. The method of removal depends on the support material and geometry. It can involve manual breaking, cutting, machining, or dissolving in a chemical solution. Careful removal is essential to avoid damaging the delicate features of the waveguide.
- Stress Relief Heat Treatment: Metal 3D printed parts often contain residual stresses due to the rapid heating and cooling cycles during the build process. Stress relief heat treatment, performed at specific temperatures for a определенное time, helps to reduce these internal stresses, improving the mechanical properties and dimensional stability of the waveguide.
- Hot Isostatic Pressing (HIP): For high-performance applications, especially in demanding industries like aerospace, Hot Isostatic Pressing (HIP) may be employed. This process involves subjecting the printed part to high pressure and temperature simultaneously, which helps to eliminate internal porosity, increase density, and improve the overall mechanical properties of the material. Metal3DP’s advanced powder making system ensures high-density powders, which can further enhance the effectiveness of HIP.
- Surface Finishing: As discussed earlier, the as-printed surface finish may not be suitable for all waveguide applications, particularly those involving high frequencies. Post-processing techniques to improve surface finish include:
- Media Blasting: To achieve a uniform and cleaner surface.
- Machining (CNC): For critical surfaces requiring very tight tolerances and smooth finishes, precision CNC machining can be employed.
- Polishing (Mechanical or Electrochemical): To reduce surface roughness for improved electrical performance.
- Chemical Etching: To smooth surfaces and remove minor imperfections.
- Coating: In some cases, coatings may be applied to the waveguide to enhance its electrical conductivity, corrosion resistance, or surface properties. Common coatings include conductive metals like silver or gold.
- Dimensional Inspection and Quality Control: After post-processing, thorough dimensional inspection using coordinate measuring machines (CMMs) or other precision measurement tools is crucial to ensure the waveguide meets the required specifications and tolerances. Non-destructive testing methods like dye penetrant inspection or ultrasonic testing may also be used to detect any internal flaws.
The specific post-processing steps required for a 3D printed precision instrument waveguide will depend on the design, material, application, and the desired final properties. Collaborating with an experienced metal 3D printing service provider like Metal3DP ensures that the appropriate post-processing techniques are applied to achieve the highest quality and performance.
Common Challenges and How to Avoid Them in 3D Printing Waveguides
While metal 3D printing offers numerous advantages for manufacturing precision instrument waveguides, certain challenges can arise during the process. Understanding these potential issues and implementing appropriate strategies can help mitigate risks and ensure successful outcomes.
- Warping and Distortion: Thermal stresses during the rapid heating and cooling cycles of the printing process can lead to warping or distortion of the waveguide geometry, particularly for large or complex parts with thin walls.
- How to Avoid: Optimize part orientation on the build platform to minimize stress concentration. Employ appropriate support structures to anchor critical features. Utilize stress relief heat treatment post-printing. Consider design modifications to reduce large flat areas or incorporate stiffening ribs. Metal3DP’s expertise in SEBM technology helps minimize thermal stresses due to its high build temperature.
- Support Structure Removal Damage: Aggressive removal of support structures can damage the delicate surfaces or thin walls of waveguides, especially internal channels.
- How to Avoid: Design self-supporting geometries where possible. Optimize support structure design for easy and clean removal. Use dissolvable support materials if compatible with the chosen metal powder. Employ skilled technicians for support removal with appropriate tools and techniques.
- Porosity and Density Issues: Insufficient melting and fusion of the metal powder can lead to internal porosity, which can negatively impact the mechanical strength and electrical conductivity of the waveguide.
- How to Avoid: Utilize high-quality metal powders with good flowability, such as those offered by Metal3DP. Optimize printing parameters, including laser or electron beam power and scan strategies. Consider Hot Isostatic Pressing (HIP) post-processing to eliminate internal voids and increase density.
- Surface Roughness Affecting Performance: As discussed earlier, a rough internal surface can increase signal loss in waveguides, especially at high frequencies.
- How to Avoid: Design orientations that minimize support structures on critical internal surfaces. Employ post-processing techniques like polishing, chemical etching, or coating to achieve the required surface smoothness.
- Dimensional Inaccuracies and Tolerance Issues: Deviations from the intended dimensions and exceeding tolerance limits can compromise the performance and integration of the waveguide within the radar system.
- How to Avoid: Calibrate and maintain the 3D printer regularly. Optimize build parameters for the specific material and geometry. Account for material shrinkage during the design phase. Employ precision measurement techniques for quality control and consider CNC machining for critical features requiring very tight tolerances.
- Material Contamination: Introducing impurities into the metal powder or during the printing process can affect the material properties and performance of the waveguide.
- How to Avoid: Use high-purity, certified metal powders from reputable suppliers like Metal3DP. Maintain a clean printing environment and follow proper material handling procedures.
- Bridging and Overhang Issues: Printing unsupported horizontal spans or overhangs can lead to sagging or collapse if the printing parameters are not optimized.
- How to Avoid: Design parts with self-supporting angles (typically 45 degrees or less). Use appropriate support structures for larger overhangs. Optimize printing parameters such as layer height and scan speed.
By understanding these common challenges and implementing the recommended avoidance strategies, manufacturers can leverage the benefits of metal 3D printing to produce high-quality, precision instrument waveguides with consistent performance and reliability. Partnering with an experienced metal 3D printing service provider like Metal3DP can provide valuable insights and expertise to navigate these challenges effectively.

How to Choose the Right Metal 3D Printing Service Provider for Waveguides
Selecting the right metal 3D printing service provider is crucial for ensuring the successful manufacturing of precision instrument waveguides that meet stringent performance and quality requirements. Here are key factors to consider when evaluating potential suppliers:
- Technology and Material Capabilities: Ensure the provider has experience with metal 3D printing technologies suitable for producing waveguides with the required precision and material properties. For Invar and Ti-6Al-4V waveguides, Selective Electron Beam Melting (SEBM) and Direct Metal Laser Sintering (DMLS) are common and effective technologies. Verify that they offer the specific metal powders needed for your application, such as the high-quality powders available from Metal3DP.
- Industry Experience and Expertise: Look for a provider with a proven track record of manufacturing parts for demanding industries like aerospace, defense, medical, or telecommunications. Experience with RF components or waveguides specifically is a significant advantage. Inquire about their engineering expertise and their ability to provide design optimization and material selection guidance.
- Quality Assurance and Certifications: Verify that the provider has robust quality management systems in place and holds relevant certifications (e.g., ISO 9001, AS9100 for aerospace). Inquire about their inspection processes, dimensional accuracy capabilities, and material testing procedures.
- Post-Processing Services: Determine if the provider offers the necessary post-processing services to meet your requirements, including powder removal, support removal, stress relief heat treatment, HIP, surface finishing (polishing, coating), and dimensional inspection. A comprehensive suite of in-house services can streamline the production process and ensure quality control.
- Equipment and Facility: Assess the provider’s equipment and facilities. Do they have a modern and well-maintained fleet of metal 3D printers? What is their production capacity and lead time? Metal3DP boasts industry-leading print volume, accuracy, and reliability.
- Communication and Customer Support: Evaluate the provider’s responsiveness, communication clarity, and willingness to collaborate. A strong partner will work closely with you throughout the design, manufacturing, and post-processing stages.
- Cost and Lead Time: While cost should not be the sole determining factor, it is an important consideration. Obtain detailed quotes that outline all costs, including printing, materials, and post-processing. Inquire about typical lead times for similar projects.
- References and Case Studies: Request references from previous clients, particularly those in similar industries or with comparable projects. Review case studies or testimonials that highlight the provider’s capabilities and successful outcomes.
- Confidentiality and Intellectual Property Protection: Ensure the provider has strong confidentiality agreements and measures in place to protect your intellectual property.
By carefully evaluating potential metal 3D printing service providers based on these criteria, you can select a partner that aligns with your specific needs and ensures the successful production of high-quality precision instrument waveguides. Consider contacting Metal3DP to explore how our comprehensive solutions can power your organization’s additive manufacturing goals.
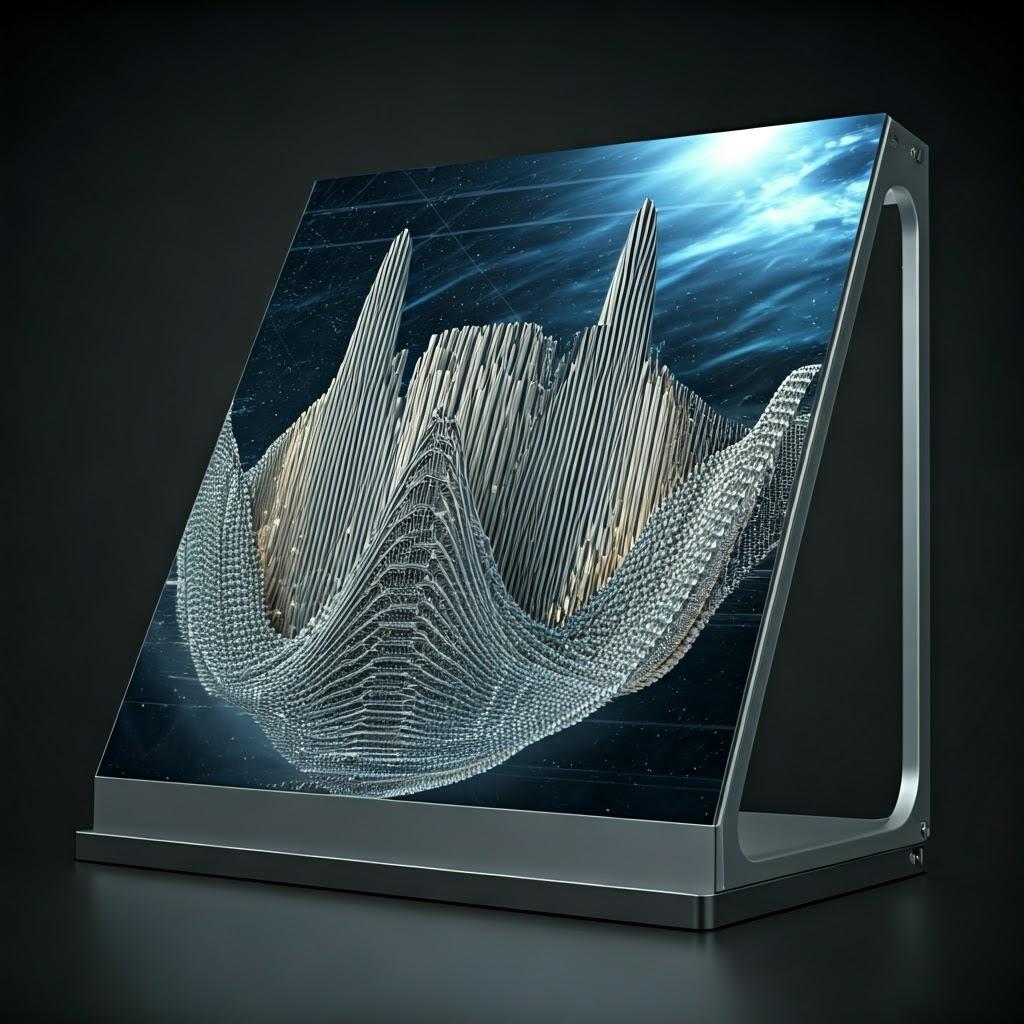
Cost Factors and Lead Time for 3D Printed Waveguides
Understanding the factors that influence the cost and lead time for 3D printed precision instrument waveguides is essential for effective project planning and budgeting.
Cost Factors:
- Material Costs: The cost of the metal powder is a significant factor. Alloys like Invar and Ti-6Al-4V can be relatively expensive compared to standard metals. The quantity of material required for the part and support structures will directly impact the overall material cost. Metal3DP’s advanced powder making system focuses on producing high-quality powders cost-effectively.
- Build Time: The duration of the printing process on the 3D printer is a key cost driver. Build time is influenced by factors such as part volume, complexity, layer height, and the number of parts being printed simultaneously on the build platform. Longer build times translate to higher machine operating costs (energy consumption, maintenance) and labor costs.
- Pre-Processing Costs: This includes the time and effort involved in design optimization for additive manufacturing, build preparation, and generating support structures. Complex geometries may require more extensive pre-processing.
- Post-Processing Costs: The cost of post-processing steps such as powder removal, support removal, heat treatment, HIP (if required), surface finishing, and quality inspection can be substantial. The complexity and number of post-processing steps will affect the overall cost.
- Equipment and Overhead Costs: The service provider’s investment in equipment, facility, and operational overhead is factored into their pricing. Providers with advanced equipment and comprehensive services may have higher rates.
- Quantity and Volume: Similar to traditional manufacturing, economies of scale can apply to 3D printing. Larger production volumes may result in lower per-part costs.
Lead Time Factors:
- Pre-Processing Time: The time required for design optimization, file preparation, and build planning.
- Printing Time: The actual duration of the 3D printing process.
- Post-Processing Time: The time needed for each of the required post-processing steps. Some processes, like heat treatment or HIP, can have significant lead times.
- Quality Control and Inspection Time: Thorough inspection processes can add to the overall lead time.
- Shipping and Handling: The time required for packaging and transportation of the finished parts.
- Service Provider Backlog: The current workload and capacity of the chosen service provider can impact lead times.
Strategies for Managing Cost and Lead Time:
- Design Optimization for AM: Designing parts specifically for additive manufacturing can minimize material usage, build time, and the need for extensive support structures.
- Material Selection: Choosing the most appropriate material based on performance requirements and cost considerations is crucial.
- Build Planning and Nesting: Optimizing part orientation and nesting multiple parts on the build platform can improve efficiency and reduce per-part costs and lead times.
- Minimizing Post-Processing: Designing parts to minimize the need for complex post-processing steps can save both time and money.
- Choosing the Right Service Provider: Selecting a provider with efficient processes, appropriate technology, and a track record of timely delivery is essential. Metal3DP’s commitment to efficiency and reliability aims to provide competitive lead times.
By carefully considering these cost and lead time factors and working closely with an experienced metal 3D printing service provider, businesses can effectively manage the production of their precision instrument waveguides.
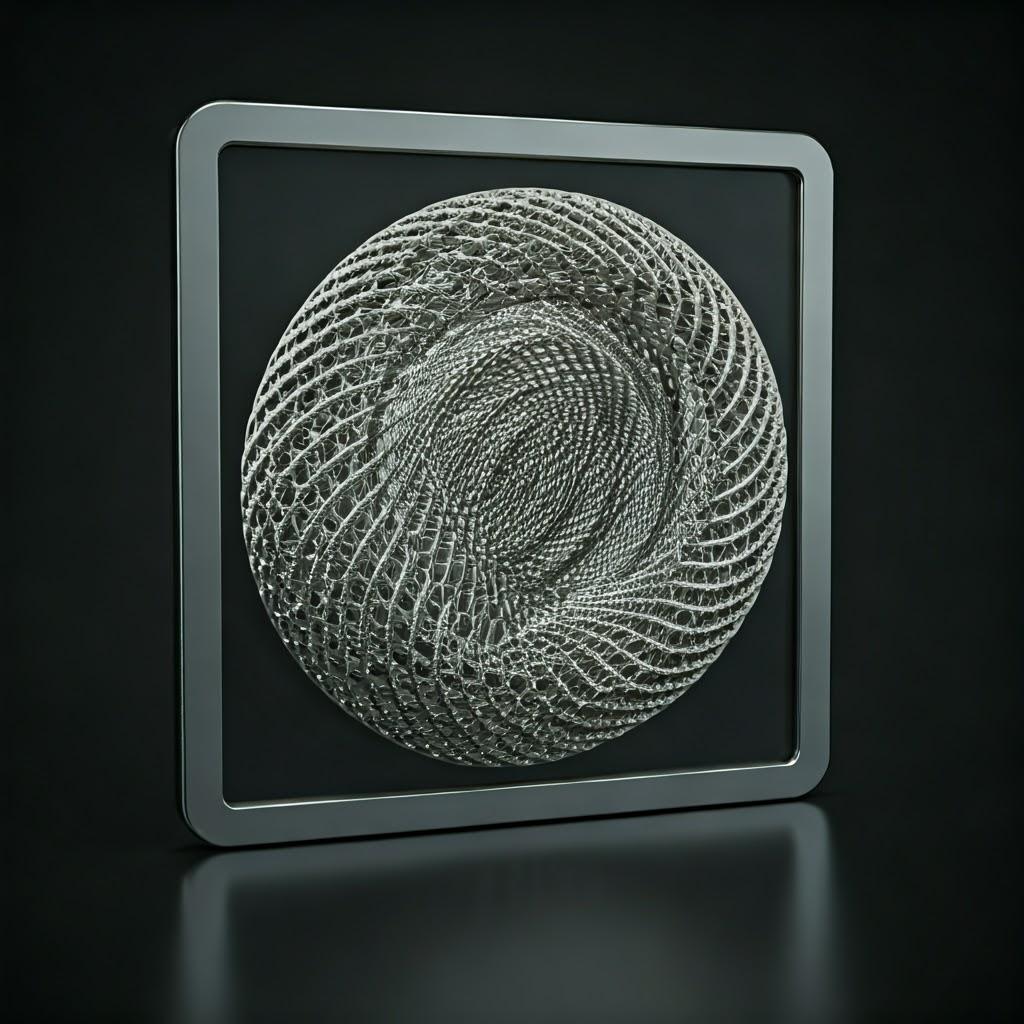
Frequently Asked Questions (FAQ)
- What is the typical dimensional accuracy achievable for 3D printed waveguides? With advanced metal 3D printing technologies like SEBM, dimensional accuracies of ±0.1 to ±0.2 mm are achievable. However, this can vary based on part size, geometry, material, and build orientation. For critical features, post-processing like CNC machining can further improve accuracy.
- What surface finish can be expected from a 3D printed Invar waveguide? The as-printed surface roughness (Ra) typically ranges from 5 to 20 μm depending on the printing parameters. For high-frequency applications, post-processing techniques like polishing or chemical etching are often employed to achieve smoother surface finishes and minimize signal loss.
- Is heat treatment always necessary for 3D printed waveguides? Stress relief heat treatment is often recommended to reduce residual stresses and improve the mechanical properties and dimensional stability of 3D printed metal parts, including waveguides. Hot Isostatic Pressing (HIP) may be required for demanding applications to eliminate porosity and enhance density. The specific requirements depend on the material and application.
Conclusion: The Future of Precision Waveguides is Additive
Metal 3D printing is revolutionizing the manufacturing of precision instrument waveguides, offering unprecedented design freedom, material optimization, and the potential for enhanced performance. By leveraging advanced technologies like Selective Electron Beam Melting (SEBM) and high-performance materials such as Invar and Ti-6Al-4V, industries like aerospace, defense, and telecommunications can achieve lighter, more efficient, and highly customized waveguide solutions.
Metal3DP, with its industry-leading printing equipment and expertise in advanced metal powders, is at the forefront of this transformative technology. Our commitment to accuracy, reliability, and comprehensive services empowers businesses to unlock the full potential of metal additive manufacturing for their critical waveguide applications. From intricate designs and rapid prototyping to optimized performance and reduced lead times, metal 3D printing offers a compelling alternative to traditional manufacturing methods. As technology continues to advance, the role of metal 3D printing in the production of precision instrument waveguides will only become more significant, driving innovation and enabling the next generation of radar and communication systems. Contact Metal3DP today to explore how our capabilities can support your organization’s additive manufacturing journey.
Share On
MET3DP Technology Co., LTD is a leading provider of additive manufacturing solutions headquartered in Qingdao, China. Our company specializes in 3D printing equipment and high-performance metal powders for industrial applications.
Inquiry to get best price and customized Solution for your business!
Related Articles
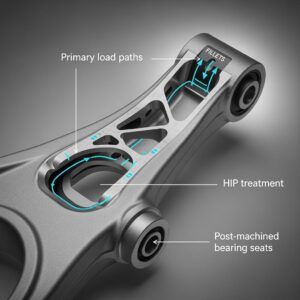
Metal 3D Printing for U.S. Automotive Lightweight Structural Brackets and Suspension Components
Read More »About Met3DP
Recent Update
Our Product
CONTACT US
Any questions? Send us message now! We’ll serve your request with a whole team after receiving your message.