3D Printed Interior Brackets for Lightweight Automotive Design
Table of Contents
Introduction: Revolutionizing Automotive Interiors with 3D Printed Brackets
The automotive industry is in a perpetual state of evolution, driven by relentless demands for improved fuel efficiency, enhanced performance, superior safety, and innovative passenger experiences. Central to achieving these goals is the concept of lightweighting – the strategic reduction of vehicle mass without compromising structural integrity or functionality. While powertrains, chassis, and body panels often dominate lightweighting discussions, the vehicle’s interior presents significant opportunities for optimization. Components often overlooked, such as automotive interior brackets, play a crucial role in both function and overall weight. Traditionally manufactured through methods like stamping, casting, or injection molding (for polymer versions), these brackets, responsible for mounting everything from center consoles and dashboard elements to seats and trim pieces, are increasingly becoming prime candidates for innovation through metal additive manufacturing (AM), commonly known as metal 3D printing.
An interior bracket, in its essence, is a structural connector. It secures one component to another within the complex assembly of a vehicle’s cabin. Its functions can range from simple positioning and alignment to critical load-bearing tasks, vibration damping, and routing pathways for wiring or ducting. The cumulative weight of dozens, sometimes hundreds, of these brackets can be substantial. Furthermore, traditional manufacturing methods often impose design constraints, limiting the potential for part consolidation, complex geometries tailored for specific load paths (topology optimization), and rapid iteration during the vehicle development cycle.
This is where the paradigm shift offered by metal 3D printing becomes compelling. Technologies like Laser Powder Bed Fusion (LPBF) and Electron Beam Melting (EBM) enable the layer-by-layer construction of complex metal parts directly from digital models. For automotive interior brackets, this translates to several transformative possibilities:
- Unprecedented Lightweighting: AM allows for the creation of intricate, topology-optimized designs that place material precisely where it’s needed for strength and stiffness, removing unnecessary mass elsewhere. Lattice structures and hollowed-out sections, impossible or prohibitively expensive to produce traditionally, become feasible, leading to significant weight savings per part.
- Design Freedom & Consolidation: Engineers are no longer bound by the limitations of molds, dies, or machining tools. Complex curves, internal channels, and integrated features (e.g., snap-fits, cable guides) can be designed directly into the bracket. This often allows multiple traditionally separate components to be consolidated into a single, multifunctional 3D printed part, reducing assembly time, complexity, and potential points of failure.
- Rapid Prototyping & Iteration: During the vehicle design phase, AM enables the quick production of functional metal prototypes for fit checks, performance testing, and design validation. This accelerates development cycles, allowing engineers to iterate and optimize designs much faster than with traditional tooling-based methods.
- Customization & Low-Volume Production: Metal 3D printing is economically viable for low-to-medium volume production runs, ideal for specialized vehicle models, aftermarket parts, or service components where investing in expensive tooling is impractical. It also opens doors for customized interior solutions.
- Material Possibilities: AM processes work effectively with high-performance, lightweight alloys like aluminum (such as AlSi10Mg and A6061), titanium, and advanced steels, providing material options perfectly suited for the demanding automotive environment.
Companies at the forefront of additive manufacturing automotive solutions, like Met3dp, are pioneering the equipment and materials necessary to realize these benefits. With advanced powder manufacturing techniques like gas atomization ensuring high-quality, spherical metal powders, and robust printing systems designed for accuracy and reliability, the path is clear for AM to become a standard tool in the automotive engineer’s arsenal. This blog post will delve into the specifics of using metal 3D printing for automotive interior brackets, exploring their applications, the advantages over traditional methods, recommended materials like AlSi10Mg and A6061, crucial design considerations, achievable quality standards, and the practicalities of sourcing these innovative components. We aim to provide engineers and procurement managers in the automotive sector with the insights needed to leverage this technology for next-generation vehicle interior design.
Core Functions & Applications of Automotive Interior Brackets
Automotive interior brackets are the unsung heroes of the cabin environment. While often hidden behind aesthetically pleasing trim panels or integrated seamlessly into larger assemblies, their role is fundamental to the structural integrity, functionality, and perceived quality of the vehicle’s interior. They are essential automotive interior components, acting as the skeletal framework that supports and positions a vast array of parts passengers interact with directly or indirectly. Understanding their diverse functions and widespread applications highlights the potential impact of optimizing their design and manufacturing through technologies like metal 3D printing.
Primary Functions:
- Mounting & Securing: This is the most fundamental role. Brackets provide secure attachment points for various interior modules to the vehicle’s body structure (Body-in-White or BIW) or to other interior sub-assemblies. This includes:
- Instrument Panel (IP) / Dashboard: Supporting the weight of the IP cluster, infotainment screens, HVAC controls, airbags, and associated wiring harnesses.
- Center Console: Anchoring the console structure, which houses gear shifters, storage compartments, armrests, and control interfaces.
- Seats: Providing structural mounting points to the vehicle floor, critical for passenger safety during impacts. Seat track mechanisms often incorporate specialized brackets.
- Interior Trim Panels: Securing door panels, pillar trims, headliners, and cargo area liners.
- Overhead Consoles: Mounting lighting modules, sunroof controls, and storage bins.
- Electronics Modules: Holding ECUs (Electronic Control Units), audio amplifiers, and other electronic components securely in place, often in hidden locations.
- HVAC Ducting: Supporting and routing air ducts behind the dashboard and throughout the cabin.
- Load Bearing & Structural Reinforcement: Many interior brackets are subjected to significant static and dynamic loads. Examples include brackets supporting grab handles, seat anchorages subjected to crash loads, or console structures bearing the weight of occupants leaning on them. They must provide sufficient strength and stiffness to prevent deformation, failure, or unwanted movement.
- Vibration Damping & Noise Reduction (NVH): Brackets can influence the Noise, Vibration, and Harshness (NVH) characteristics of the interior. Poorly designed brackets can transmit vibrations from the powertrain or road surface into the cabin, or they can rattle or buzz. Optimized bracket design, sometimes incorporating specific geometries or being made from materials with inherent damping properties, can help mitigate these issues. Metal AM allows for complex shapes that can be tuned for better NVH performance.
- Positioning & Alignment: Brackets ensure precise positioning and alignment of interior components relative to each other and the vehicle structure. This is crucial for achieving consistent panel gaps, proper sealing, and correct functionality of mating parts (e.g., glove box latches, console lids).
- Space Optimization & Packaging: In the tightly packed environment of a modern vehicle interior, brackets must often conform to complex shapes and fit into restricted spaces. Their design directly impacts packaging efficiency, influencing passenger room, storage capacity, and the ability to integrate new features. AM’s ability to create organic, space-conforming shapes is a distinct advantage here.
- Routing & Management: Some brackets incorporate features like channels, clips, or tie-down points to guide and secure wiring harnesses, fluid lines (e.g., for rear HVAC), or fiber optic cables, preventing them from chafing or interfering with other components.
Key Application Areas & Industries:
- Automotive OEMs (Original Equipment Manufacturers): Directly involved in vehicle design and assembly, specifying and integrating brackets into new models. They are primary drivers for lightweighting and innovation.
- Tier 1 & Tier 2 Suppliers: Companies that design and manufacture complete interior modules (e.g., dashboards, seating systems, consoles) or sub-components for OEMs. They rely on efficient and reliable automotive bracket suppliers.
- Aftermarket & Customization: The market for replacement parts or custom interior modifications often requires specialized or low-volume brackets. AM is particularly well-suited for producing aftermarket brackets or unique designs for custom builds.
- Specialty Vehicles: Manufacturers of buses, trucks, RVs, emergency vehicles, and motorsport vehicles often require robust and sometimes custom-designed interior brackets for specialized equipment and lower production volumes.
- Electric Vehicles (EVs): EVs often feature unique interior layouts (“skateboard” platforms, large central screens) and a heightened focus on lightweighting to maximize range, creating new opportunities and requirements for innovative bracket designs.
The sheer variety of shapes, sizes, and functional requirements for these interior mounting solutions means that a one-size-fits-all manufacturing approach is often inefficient. Traditional methods like stamping excel at high volumes of simple geometries, while casting is suited for complex shapes but can be heavy and require significant post-machining. Machining from billet offers precision but is material-intensive and slow for complex parts. Metal 3D printing emerges as a versatile alternative, particularly advantageous when lightweighting, complex geometry, part consolidation, or speed during development are key drivers for vehicle component manufacturing. It allows engineers to rethink bracket design from the ground up, focusing purely on function and optimal material usage rather than being constrained by traditional manufacturing limitations.
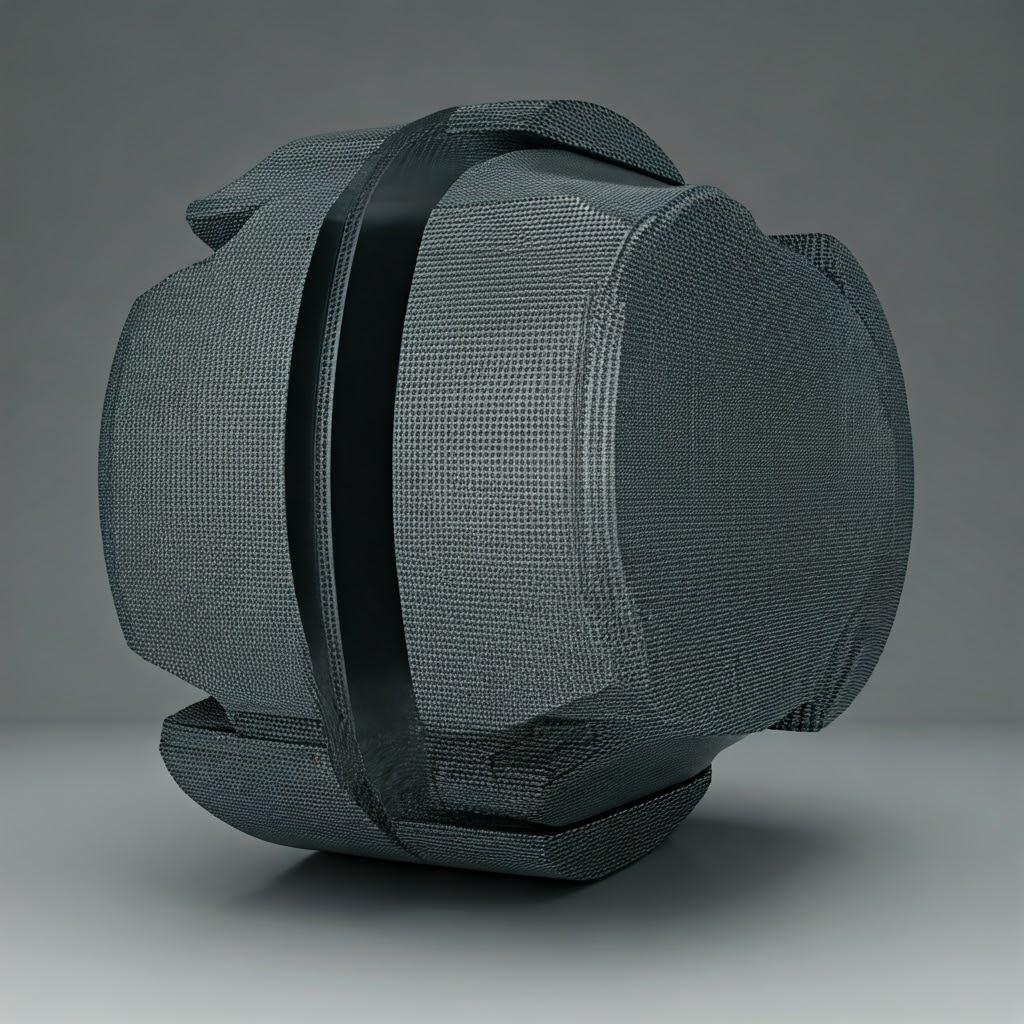
Why Metal Additive Manufacturing for Interior Bracket Production?
The decision to adopt a new manufacturing technology hinges on demonstrable advantages over established methods. For automotive interior brackets, traditionally produced via stamping, casting, injection molding (for polymer versions), or CNC machining, metal additive manufacturing (AM) offers a compelling suite of benefits that directly address the core challenges and goals of modern automotive design: lightweighting, speed, design flexibility, and cost-effectiveness in specific scenarios. Comparing AM against traditional techniques illuminates why it’s becoming an increasingly viable and attractive option for OEM automotive parts and supplier components.
Comparison: Metal AM vs. Traditional Manufacturing for Brackets
Feature | Metal AM (e.g., LPBF) | Stamping (Metal) | Casting (Metal) | CNC Machining (Metal) | Injection Molding (Polymer) |
---|---|---|---|---|---|
Design Freedom | Very High (Complex geometries, lattices) | Low (Limited by tooling, formability) | Moderate (Requires draft angles) | High (Subtractive limitations) | High (Requires mold design) |
Lightweighting | Excellent (Topology optimization) | Moderate (Material choice limited) | Fair (Can be heavy, porosity issues) | Good (Material removal possible) | Excellent (Material density) |
Part Consolidation | High Potential | Low | Moderate | Low | Moderate |
Tooling Cost | None (Tool-less manufacturing) | High (Dies required) | High (Molds required) | Low (Fixturing) | Very High (Molds required) |
Lead Time (Proto) | Very Fast (Days) | Slow (Weeks/Months for tooling) | Slow (Weeks/Months for tooling) | Moderate (Days/Weeks) | Slow (Weeks/Months for tooling) |
Unit Cost (Low Vol) | Moderate to High | Very High (Tooling amortization) | Very High (Tooling amortization) | High | Very High (Tooling amortization) |
Unit Cost (High Vol) | High | Very Low | Low | Moderate | Very Low |
Material Waste | Low (Powder recycling) | Moderate (Sheet offcuts) | Moderate (Gates, runners) | High (Chips) | Low (Runner recycling possible) |
Material Options | Growing Range (Al, Ti, Steel, Ni alloys) | Specific Sheet Metals | Castable Alloys | Wide Range | Wide Range of Thermoplastics |
Complexity Cost | Relatively Low Impact | High Impact | High Impact | High Impact | High Impact (Mold complexity) |
Export to Sheets
Key Advantages of Metal AM for Interior Brackets:
- Revolutionary Lightweighting through Topology Optimization: This is arguably the most significant benefit. AM enables topology optimization, an algorithmic approach where software determines the most efficient material distribution within a defined design space, subject to specific load cases and constraints. This results in organic, often lattice-like structures that maintain or even increase strength and stiffness while drastically reducing mass compared to solid parts designed for traditional manufacturing. For automotive interiors, where cumulative weight savings are critical for fuel efficiency (ICE vehicles) or range (EVs), shaving grams or kilograms through optimized brackets is highly valuable.
- Design Freedom Unleashed: AM liberates engineers from the constraints of traditional manufacturing.
- Complex Geometries: Undercuts, internal channels (for wiring or cooling), freeform surfaces, and variable wall thicknesses are easily achievable without complex tooling or multi-stage machining processes.
- Part Consolidation: Multiple simple brackets, fasteners, and spacers can often be redesigned and printed as a single, complex, multifunctional component. This reduces part count, simplifies assembly, lowers inventory management costs, and eliminates potential failure points at joints.
- Integrated Features: Mounting bosses, snap-fits, cable clips, and alignment features can be built directly into the bracket design, further reducing assembly complexity.
- Accelerated Development via Rapid Prototyping: Creating rapid prototyping automotive parts is a core strength of AM. Engineers can design a bracket, print a functional metal prototype (often in AlSi10Mg or A6061) within days, perform fit checks, conduct load tests, and validate the design in a real-world assembly. If modifications are needed, the digital model is updated, and a new iteration is printed quickly. This drastically shortens the design-test-refine cycle compared to waiting weeks or months for traditional tooling to be produced or modified. This speed is crucial in the fast-paced automotive development environment.
- Economical Low-Volume Production & On-Demand Manufacturing: Traditional methods like stamping and casting involve high upfront tooling costs, making them economically unviable for small production runs. Metal AM is a tool-less process, meaning the cost per part is less dependent on volume. This makes it ideal for:
- Niche vehicle models: Cars with limited production numbers.
- Aftermarket parts: Replacing obsolete or customized components.
- Service parts: Providing spare parts on demand without maintaining large physical inventories.
- Bridge production: Manufacturing parts while waiting for high-volume tooling to be completed. This capability supports more agile and flexible low-volume automotive production strategies.
- Material Efficiency and Sustainability: While the energy consumption of AM machines is a factor, the process itself can be highly material-efficient. Powder bed fusion processes allow unused metal powder to be collected, sieved, and reused in subsequent builds, minimizing raw material waste compared to subtractive machining, which generates significant chip waste. The lightweighting potential also contributes to sustainability during the vehicle’s use phase through improved fuel economy or range.
- Customization Potential: AM allows for easy design variations without tooling changes. This could enable customized interior mounting solutions for specific trim levels, optional equipment, or even personalized vehicle builds in the future.
While metal AM may not replace stamping for simple, high-volume brackets where cost per part is paramount, its advantages in tackling complexity, enabling lightweighting, and accelerating development make it a powerful tool for specific and increasingly numerous applications within the automotive interior. The benefits of additive manufacturing are particularly pronounced for brackets with complex geometries, high structural requirements relative to their weight targets, or those needed in low-to-medium volumes or during rapid development phases. Leading providers like Met3dp, specializing in both advanced printing systems and high-quality metal 3D printing powders, are key enablers in unlocking this potential for the automotive industry.
Material Spotlight: AlSi10Mg and A6061 for Optimal Performance
Selecting the right material is paramount to the success of any engineering application, and 3D printed automotive interior brackets are no exception. The material must meet stringent requirements for strength, weight, durability, corrosion resistance, and manufacturability within the chosen additive manufacturing process. For many automotive bracket applications where lightweighting is a primary goal, aluminum alloys are often the preferred choice. Among the most commonly used and well-characterized aluminum alloys in metal AM, particularly Laser Powder Bed Fusion (LPBF), are AlSi10Mg and A6061. Understanding their properties and why they are suitable for interior brackets is crucial for designers and procurement specialists.
Aluminum Alloys in Automotive:
Aluminum offers an excellent combination of low density (approximately one-third that of steel) and good mechanical properties, making it a cornerstone of automotive lightweighting strategies. Its inherent corrosion resistance is also beneficial for components exposed to varying environmental conditions, even within the vehicle cabin.
AlSi10Mg: The Workhorse of Aluminum AM
AlSi10Mg is a hypoeutectic aluminum-silicon alloy containing magnesium. It’s essentially a casting alloy composition adapted for additive manufacturing and is arguably the most widely used aluminum alloy in LPBF today.
- Key Properties & Characteristics:
- Excellent Processability: AlSi10Mg behaves very well during the LPBF process, exhibiting good melt pool stability and relatively low susceptibility to cracking compared to other high-strength aluminum alloys. This leads to more reliable and consistent printing results.
- Good Strength-to-Weight Ratio: In the as-built or stress-relieved state, it offers moderate strength. However, its properties can be significantly enhanced through appropriate heat treatments (typically T6 Solution Annealing and Artificial Aging). A T6 heat treatment can substantially increase yield strength and ultimate tensile strength, making it suitable for load-bearing applications.
- Good Corrosion Resistance: Like most aluminum alloys, it forms a passive oxide layer, providing good protection against atmospheric corrosion.
- Fine Microstructure: The rapid solidification inherent in LPBF results in a very fine microstructure in AlSi10Mg parts, contributing to its good mechanical properties compared to traditional cast equivalents.
- Weldability: Can be welded, although specific procedures are recommended.
- Availability: Widely available from numerous metal 3D printing powder suppliers, including specialized manufacturers focused on powder quality for AM.
- Why it Matters for Interior Brackets:
- Its excellent printability makes it reliable for producing complex bracket geometries often generated through topology optimization.
- The ability to achieve good mechanical properties after heat treatment allows it to be used for brackets requiring structural integrity and load-bearing capacity, while still benefiting from aluminum’s low density.
- Its widespread use means processing parameters are well-understood, and data on its performance is readily available.
A6061: Strength and Versatility
A6061 (also commonly referred to as 6061) is a precipitation-hardenable aluminum alloy containing magnesium and silicon as its major alloying elements. It’s a very common wrought alloy known for its good mechanical properties, weldability, and corrosion resistance, traditionally used in extrusions and forgings. Adapting it for AM presented challenges, but significant progress has been made, making it a viable and attractive option.
- Key Properties & Characteristics:
- Higher Strength Potential (Post-Treatment): Compared to AlSi10Mg, A6061 can achieve higher strength and toughness after a suitable T6 heat treatment. This makes it attractive for brackets under higher stress or requiring greater durability.
- Good Ductility & Toughness: Generally exhibits better ductility and fracture toughness than AlSi10Mg, which can be important for components subjected to dynamic loads or impacts.
- Excellent Corrosion Resistance: Offers very good resistance to atmospheric corrosion.
- Good Machinability & Finish: Responds well to post-process machining and surface finishing techniques like anodizing.
- Processability Challenges: Historically, A6061 was more challenging to print reliably via LPBF than AlSi10Mg due to issues like cracking and keyholing porosity. However, advancements in machine parameters, process control, and specialized powder chemistries (sometimes designated with suffixes like ‘RAM1’ or ‘RAM2’ indicating AM optimization) have significantly improved its processability.
- Why it Matters for Interior Brackets:
- Its potential for higher strength and toughness makes it suitable for more demanding structural brackets, such as those related to seat mountings or significant IP support structures.
- Its familiarity as a traditional engineering alloy means designers may already have extensive data and comfort working with its property profile.
- Its excellent finishing characteristics allow for high-quality aesthetic finishes if the bracket is partially visible or requires specific surface treatments.
The Importance of Powder Quality:
The final properties and reliability of 3D printed metal parts are heavily dependent on the quality of the metal 3D printing powders used. For alloys like AlSi10Mg and A6061, key powder characteristics include:
- Sphericity: Highly spherical powder particles ensure good flowability, which is critical for uniform powder bed spreading during the LPBF process. Poor flowability can lead to defects like porosity.
- Particle Size Distribution (PSD): A controlled PSD ensures good packing density in the powder bed and consistent melting behavior. Fines can affect flowability and pose safety hazards, while oversized particles may not melt completely.
- Chemical Purity & Composition: Strict adherence to the specified alloy composition is essential for achieving the desired mechanical properties and processability. Impurities can lead to defects and unpredictable performance.
- Low Porosity: Internal gas porosity within the powder particles themselves can transfer to the final part, acting as crack initiation sites.
- Low Oxygen Content: Especially crucial for reactive materials like aluminum, high oxygen content can degrade mechanical properties.
Companies like Met3dp leverage advanced powder production techniques, such as industry-leading gas atomization and Plasma Rotating Electrode Process (PREP) technologies. Their focus on creating high-quality metal powders with high sphericity, controlled PSD, and precise chemical composition is fundamental to enabling the reliable production of dense, high-performance automotive grade aluminum parts, including complex interior brackets made from AlSi10Mg and A6061. Utilizing powders from a reputable high-quality metal powder supplier ensures that the starting material meets the stringent requirements for demanding automotive applications.
Material Selection Summary Table:
Feature | AlSi10Mg | A6061 (AM Optimized) | Recommendation for Interior Brackets |
---|---|---|---|
Printability | Excellent | Good to Very Good | AlSi10Mg often preferred for utmost complexity/reliability |
Strength (T6) | Good | Very Good to Excellent | A6061 for higher load applications; AlSi10Mg sufficient for many |
Ductility/Toughness | Moderate | Good | A6061 potentially better for dynamic loads |
Corrosion Resist. | Good | Excellent | Both generally suitable for interior environments |
Heat Treatment | Required (T6) for optimal properties | Required (T6) for optimal properties | Factor heat treatment into process chain for both |
Cost/Availability | Generally Lower/Wider | Potentially Higher/More Specialized | AlSi10Mg often more cost-effective and readily available |
Best For | Complex geometry, general purpose | High strength/toughness needs | Choose based on specific load case, complexity, and cost sensitivity |
Export to Sheets
Ultimately, the choice between AlSi10Mg and A6061 for a specific interior bracket will depend on a detailed analysis of the performance requirements, design complexity, production volume, and cost targets. Both materials, when processed correctly using high-quality powders and optimized AM parameters, offer significant advantages for creating lightweight, functional, and innovative lightweight metal alloy brackets for the next generation of vehicle interiors. Consulting with an experienced metal 3D printing service provider like Met3dp, who possesses deep knowledge of both materials and processes, is highly recommended during the material selection phase. Sources and related content
Design for Additive Manufacturing (DfAM) Principles for Brackets
Simply replicating a design intended for traditional manufacturing using additive manufacturing (AM) rarely unlocks the full potential of the technology. To truly leverage the benefits of metal 3D printing for automotive interior brackets – particularly achieving maximum lightweighting, performance, and cost-effectiveness – engineers must embrace Design for Additive Manufacturing (DfAM) principles. DfAM is not merely a set of rules but a fundamental shift in design thinking, considering the unique capabilities and constraints of the layer-by-layer building process right from the conceptual stage. Applying robust DfAM guidelines is crucial for creating optimized, functional, and efficiently printable automotive brackets using materials like AlSi10Mg and A6061.
Moving Beyond Traditional Constraints:
Traditional bracket design is often heavily influenced by the limitations of subtractive (machining) or formative (stamping, casting) methods. Engineers might design thicker sections than necessary simply to ensure machinability or accommodate draft angles for mold release. DfAM encourages breaking free from these inherited constraints and focusing on functional requirements first. Key DfAM strategies applicable to interior brackets include:
- Topology Optimization for Lightweighting:
- Concept: This is a cornerstone of DfAM for structural parts like brackets. Software algorithms analyze a defined design space, load cases (forces, pressures, fixture points), constraints (keep-out zones, manufacturing limits), and performance targets (stiffness, stress limits) to determine the most efficient distribution of material.
- Workflow:
- Define the maximum allowable design volume (the space the bracket can occupy).
- Specify connection points (bolt holes, interfaces with other components).
- Apply realistic load scenarios (static weight, vibration loads, potential impact forces).
- Set optimization goals (e.g., minimize mass while respecting stress/deflection limits).
- Run the optimization algorithm, which iteratively removes material from low-stress areas.
- Interpret and refine the resulting organic geometry, smoothing sharp corners and ensuring manufacturability via AM.
- Benefit for Brackets: Creates highly optimized, often skeletal or bio-inspired bracket designs that meet or exceed the strength of traditional solid designs but with significantly reduced weight (often 30-70% lighter). This directly contributes to vehicle lightweighting goals. Specialized software tools are often employed for this topology optimization workflow.
- Support Structure Strategy & Minimization:
- Concept: Most powder bed fusion processes, like LPBF used for AlSi10Mg and A6061, require support structures to anchor overhangs and steep angles to the build plate, prevent warping, and dissipate heat. However, supports consume extra material, add print time, and require removal in post-processing (which adds cost and labor). Effective DfAM aims to minimize the need for supports or make them easier to remove.
- Techniques:
- Self-Supporting Angles: Design features with angles typically greater than 45 degrees relative to the build plate. Below this threshold (which varies slightly based on material and parameters), overhangs generally require support. Understanding and designing within these self-supporting angles for metal AM is critical.
- Orientation Optimization: Orienting the bracket on the build plate strategically can minimize the total area requiring support. Software can often assist in finding the optimal orientation.
- Incorporate Chamfers/Fillets: Replacing sharp horizontal overhangs with chamfered or filleted edges can often make them self-supporting.
- Design for Support Removal: If supports are unavoidable, design them to be accessible for manual or machined removal. Avoid complex internal supports where possible. Consider sacrificial features or specific break-off points.
- Benefit for Brackets: Reduced print time, lower material consumption, and significantly simplified post-processing, leading to lower overall costs.
- Part Consolidation:
- Concept: Leveraging AM’s ability to create complex geometries to combine multiple individual components (e.g., a bracket, several fasteners, a spacer, a clip) into a single, integrated 3D printed part.
- Process: Analyze existing assemblies or functional requirements. Identify adjacent components that could potentially be merged into one AM part. Redesign the consolidated component using DfAM principles (including topology optimization if applicable).
- Benefit for Brackets: Reduces part count, simplifies vehicle assembly, lowers inventory management overhead, eliminates potential tolerance stack-up issues between parts, and potentially reduces weight and failure points associated with joints and fasteners. This is a key advantage for complex automotive interior components.
- Lattice Structures and Infill:
- Concept: Replacing solid material sections with internal lattice structures (repeating geometric unit cells like cubic, octet-truss, etc.) or optimized infill patterns.
- Application: Can be used to further reduce weight while maintaining structural integrity, absorb energy (useful for crash-related components or vibration damping), or facilitate heat dissipation if needed. Lattice structure design software is often integrated into CAD or AM preparation tools.
- Benefit for Brackets: Significant weight reduction beyond just external topology optimization, potential for enhanced vibration damping properties, and creation of multifunctional brackets.
- Minimum Feature Sizes and Wall Thickness:
- Concept: AM processes have limitations on the smallest features they can reliably produce due to laser beam spot size, powder particle size, and melt pool dynamics.
- Guidelines (Typical for LPBF Aluminum):
- Minimum Wall Thickness: Often around 0.4mm – 1.0mm (thicker may be needed for structural robustness or depending on height).
- Minimum Hole Diameter: Typically around 0.5mm – 1.0mm (smaller holes may seal over or require post-drilling).
- Minimum Pin/Feature Size: Around 0.5mm – 1.0mm.
- Benefit for Brackets: Ensures the designed features are actually manufacturable and robust, avoiding print failures or fragile elements. Designing slightly above the absolute minimum is often prudent for interior components that might experience handling or assembly stresses.
- Designing for Load Paths:
- Concept: Ensure the geometry directly supports the primary load paths the bracket will experience. Material should be concentrated along lines of stress, aligning structural elements with the forces they need to resist. Topology optimization inherently does this, but even with manual design, consciously tracing load paths is crucial.
- Benefit for Brackets: Maximizes structural efficiency, ensuring the bracket performs its load-bearing function effectively with minimal material usage.
- Incorporating Functionality:
- Concept: Building features directly into the bracket design that traditionally might require separate components or post-processing steps.
- Examples: Integrated snap-fits, cable routing channels or clips, alignment pins/sockets, textured surfaces for grip or aesthetics, embedded channels for fluids or air (less common for interior brackets but possible).
- Benefit for Brackets: Reduces assembly complexity, enhances functionality, and further leverages the geometric freedom of AM.
DfAM Rules of Thumb for Aluminum Brackets (LPBF):
Parameter | Guideline | Notes |
---|---|---|
Self-Supporting Angle | > 45° from horizontal | Can vary; lower angles possible with specific parameters/shapes |
Min. Wall Thickness | 0.5mm – 1.0mm | Check structural needs; thin, tall walls prone to warping |
Min. Hole Diameter | 0.8mm – 1.0mm | Smaller may require post-drilling; consider orientation |
Min. Pin Diameter | 0.8mm – 1.0mm | Consider robustness for handling/assembly |
Min. Gap/Channel Width | ~0.5mm | For powder removal access |
Recommended Fillets | > 0.5mm radius | Reduces stress concentrations, improves printability |
Overhangs (Unsupported) | < 1.0mm | Longer may droop or require support |
Export to Sheets
Note: These are general guidelines; specific values depend on the machine, material batch, parameters, and part geometry. Consulting with your AM service provider, such as Met3dp, is recommended.
Implementing DfAM requires a collaborative approach between design engineers and AM specialists. Utilizing the capabilities of modern CAD software, simulation tools (for topology optimization and performance validation), and AM preparation software is essential. By thinking additively from the start, engineers can design interior brackets that are not just replacements for traditionally manufactured parts but are superior in performance, lighter in weight, and potentially faster and more cost-effective to produce in relevant scenarios. The journey towards truly optimized components starts with embracing these Design for Additive Manufacturing automotive principles.
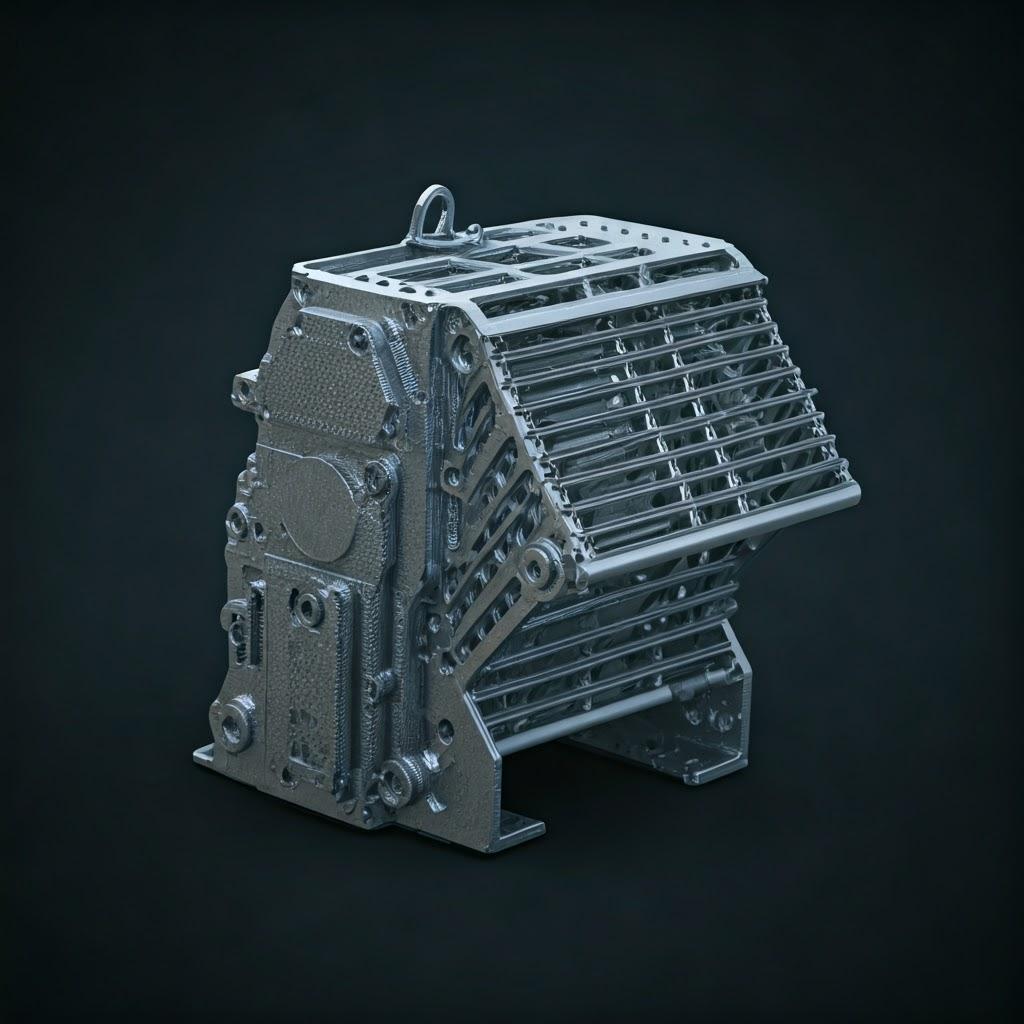
Achievable Tolerances, Surface Finish, and Dimensional Accuracy
When specifying components for automotive applications, engineers and procurement managers operate within defined standards for precision and quality. Understanding the achievable tolerances, surface finish, and dimensional accuracy of metal additive manufacturing processes like Laser Powder Bed Fusion (LPBF) for AlSi10Mg and A6061 is critical for setting realistic expectations and determining necessary post-processing steps for interior brackets. While AM offers incredible geometric freedom, it inherently produces parts with different characteristics than traditional machining or casting.
Dimensional Accuracy:
Dimensional accuracy refers to how closely the dimensions of the printed part match the nominal dimensions specified in the CAD model. Several factors influence this in LPBF:
- Machine Calibration: Regular calibration of the laser scanning system, build platform leveling, and gas flow is crucial.
- Process Parameters: Laser power, scan speed, layer thickness, and hatch spacing affect melt pool size and stability, influencing shrinkage and final dimensions. Optimized parameters are key.
- Thermal Effects: Residual stresses built up during the heating and cooling cycles can cause warping or distortion, affecting overall accuracy, especially on large or complex parts. Stress relief heat treatment is often necessary to stabilize dimensions.
- Part Size and Geometry: Larger parts or those with significant changes in cross-section are generally more prone to distortion.
- Powder Quality: Consistent particle size distribution and morphology contribute to predictable melting and solidification.
- Orientation: The orientation of the part on the build plate can affect accuracy due to anisotropic shrinkage and support structure influence.
Typical Achievable Tolerances (LPBF Aluminum):
- General Tolerances: For as-built parts (after stress relief but before machining), typical achievable tolerances often fall within ISO 2768-m (medium) or sometimes ISO 2768-f (fine) for smaller, less complex features.
- Specific Values: A common rule of thumb cited by many service providers is approximately ±0.1mm to ±0.2mm for the first 25mm, and an additional ±0.05mm to ±0.1mm for each subsequent 25mm.
- Critical Dimensions: For features requiring tighter tolerances (e.g., bearing bores, precise mating surfaces, critical hole locations), post-process CNC machining is almost always necessary. Machining can achieve tolerances comparable to traditional methods (e.g., ±0.01mm to ±0.05mm, depending on the operation).
It’s crucial to specify required tolerances clearly on engineering drawings and discuss capabilities with the metal 3D printing service provider early in the design process. Attempting to achieve extremely tight tolerances across the entire part solely through printing can significantly increase cost and complexity. Applying tight tolerances only to functionally critical features that will be post-machined is often the most practical approach.
Surface Finish (Roughness):
The as-built surface finish of LPBF parts is inherently rougher than machined surfaces due to the layer-by-layer fusion of powder particles.
- As-Built Surface Roughness (Ra):
- Top Surfaces: Generally smoother, often in the range of Ra 5 µm to 15 µm.
- Vertical Walls: Typically rougher due to the layer lines, often Ra 10 µm to 25 µm.
- Down-Facing/Supported Surfaces: Usually the roughest, as they are influenced by the support structures or partially sintered powder. Ra values can range from 15 µm to 30 µm or higher.
- Internal Channels: Can be difficult to finish and may retain partially sintered powder, resulting in high roughness.
- Factors Influencing As-Built Finish:
- Layer thickness (thinner layers generally yield better finish).
- Powder particle size distribution.
- Laser parameters (affect melt pool surface).
- Part orientation relative to the recoater blade and build direction.
- Achievable Finish After Post-Processing:
- Bead Blasting/Shot Peening: Common for achieving a uniform matte finish and removing semi-sintered particles. Typical Ra values after blasting are often Ra 3 µm to 10 µm.
- Tumbling/Vibratory Finishing: Can improve surface finish and deburr edges, especially for smaller parts. Achievable Ra depends on media and time.
- CNC Machining: Produces smooth surfaces comparable to traditional machining (Ra < 1.6 µm or better is possible).
- Polishing: Manual or automated polishing can achieve very smooth, mirror-like finishes (Ra < 0.8 µm) but is labor-intensive and typically reserved for specific aesthetic or functional requirements.
- Anodizing (for Aluminum): While primarily for corrosion/wear resistance and color, anodizing usually requires a reasonably smooth starting surface (often achieved by blasting or light machining) for a uniform appearance.
Surface Finish Considerations for Interior Brackets:
For most hidden interior brackets, the as-built surface finish after bead blasting is often perfectly acceptable. The primary concerns are typically dimensional accuracy at mounting points and structural integrity. If a bracket is partially visible or has specific contact requirements (e.g., sliding surfaces), then further post-processing like machining or polishing might be necessary for those specific areas. The required surface finish additive manufacturing standard should be clearly defined based on functional needs to avoid unnecessary finishing costs.
Ensuring Quality and Accuracy:
Reputable AM service providers employ various quality control measures:
- In-Process Monitoring: Some advanced machines monitor melt pool characteristics, temperature, and layer consistency during the build.
- Powder Analysis: Regular testing of powder chemistry, PSD, and flowability.
- Dimensional Inspection: Using Coordinate Measuring Machines (CMMs), 3D scanners, or traditional metrology tools to verify critical dimensions against the CAD model and drawing specifications.
- Material Testing: Performing tensile tests, density measurements, and microstructural analysis on sample coupons printed alongside the parts to verify material properties.
Achieving the desired dimensional accuracy metal AM and surface finish for automotive interior brackets requires a combination of careful design (DfAM), optimized printing processes (like those offered by providers using reliable equipment and quality materials from sources like Met3dp), and appropriate post-processing. Open communication between the designer and the manufacturer regarding requirements and capabilities is essential for successful outcomes.
Essential Post-Processing Steps for 3D Printed Brackets
Additive manufacturing, particularly metal powder bed fusion, is often mistakenly perceived as a process that yields ready-to-use parts directly from the machine. In reality, post-processing metal 3D prints is an integral and often multi-stage part of the workflow, especially for demanding applications like automotive interior brackets made from AlSi10Mg or A6061. These steps are necessary to achieve the required dimensional accuracy, mechanical properties, surface finish, and overall part integrity. Skipping or improperly executing these steps can compromise the performance and safety of the final component.
Here’s a breakdown of common and essential post-processing operations:
- Depowdering / Powder Removal:
- Purpose: To remove loose and semi-sintered powder trapped within the part’s geometry (e.g., internal channels, complex features) and from the build chamber after the printing process is complete.
- Methods: Typically involves compressed air blow-off, brushing, vacuuming, and sometimes ultrasonic cleaning baths within controlled environments to safely handle reactive metal powders like aluminum. Automated depowdering stations are also used.
- Importance: Ensures clear passageways, prevents powder interference in subsequent steps (like heat treatment or machining), and allows for maximum powder recovery and recycling. Incomplete powder removal can lead to issues later on.
- Stress Relief Heat Treatment:
- Purpose: To alleviate the significant internal stresses built up during the rapid heating and cooling cycles inherent in the LPBF process. These stresses can cause distortion or cracking, especially when the part is removed from the build plate or during subsequent machining.
- Method: Parts are typically heat-treated while still attached to the build plate in an inert atmosphere furnace (e.g., Argon) at a specific temperature below the aging temperature for a set duration (e.g., for AlSi10Mg, ~300°C for ~2 hours).
- Importance: Absolutely critical for dimensional stability. Residual stress metal AM is a significant factor, and stress relief minimizes the risk of warping during support removal or machining and improves the overall predictability of the part’s behavior.
- Part Removal from Build Plate:
- Purpose: To separate the printed brackets (and their support structures) from the metal build plate they were fused to during printing.
- Methods: Commonly done using wire EDM (Electrical Discharge Machining) or a bandsaw. Careful planning of the part’s base layer and support interface can facilitate easier removal.
- Importance: A necessary step to handle individual parts for further processing. Care must be taken to avoid damaging the parts during cutting.
- Support Structure Removal:
- Purpose: To remove the temporary support structures required during the build process.
- Methods: Can range from manual breaking and pliers for easily accessible, lightly connected supports, to CNC machining, grinding, or wire EDM for more robust or intricate supports. DfAM plays a crucial role here – designing supports for easy removal saves significant time and cost. Effective support removal metal AM strategies are key to efficient production.
- Importance: Supports are non-functional and must be removed for the part to meet its final geometric and functional requirements. This can be one of the most labor-intensive post-processing steps if not planned carefully during the design phase.
- Heat Treatment for Mechanical Properties (e.g., T6 Temper):
- Purpose: To achieve the desired final mechanical properties (strength, hardness, ductility) for precipitation-hardenable alloys like AlSi10Mg and A6061. The as-built or stress-relieved properties are often insufficient for demanding applications.
- Method (Typical T6 for Aluminum): Involves two main steps:
- Solution Annealing: Heating the part to a high temperature (e.g., ~520-540°C for Al alloys) to dissolve alloying elements into a solid solution, followed by rapid quenching (usually in water) to lock them in.
- Artificial Aging: Reheating the part to a lower temperature (e.g., ~160-180°C) for several hours to allow controlled precipitation of strengthening phases within the aluminum matrix.
- Importance: Tailors the material properties to meet engineering specifications. The specific heat treatment AlSi10Mg T6 cycle (or A6061 cycle) parameters (temperatures, times, quench rates) are critical and must be carefully controlled to achieve consistent results. This step significantly enhances the suitability of these alloys for structural brackets.
- CNC Machining:
- Purpose: To achieve tight tolerances on critical features, create smooth mating surfaces, drill/tap precise holes, or remove support structure remnants cleanly.
- Method: Using standard CNC milling, turning, or drilling operations. Fixturing strategies need to accommodate potentially complex AM part geometries.
- Importance: Often essential for ensuring precise fit and function within the final automotive assembly. CNC machining 3D printed aluminum is common for interfaces, mounting points, and bearing surfaces.
- Surface Finishing:
- Purpose: To improve surface roughness, achieve a desired aesthetic appearance, prepare for coating/plating, or deburr sharp edges.
- Methods:
- Bead Blasting/Shot Peening: Provides a uniform matte finish, removes loose particles, and can introduce beneficial compressive residual stresses (shot peening).
- Tumbling/Vibratory Finishing: Smooths surfaces and edges, cost-effective for batches of smaller parts.
- Grinding/Polishing: For achieving very smooth surfaces on specific areas.
- Anodizing (Aluminum): Improves corrosion and wear resistance, provides electrical insulation, and allows for coloring. Anodizing 3D printed aluminum requires careful surface preparation for uniformity.
- Painting/Powder Coating: For specific colors or enhanced environmental protection.
- Importance: Addresses functional surface requirements (e.g., low friction) or aesthetic considerations for visible brackets, and enhances durability through protective layers.
- Inspection and Quality Control (QC):
- Purpose: To verify that the final bracket meets all dimensional, material, and functional specifications.
- Methods: Dimensional inspection (CMM, 3D scanning), material testing (hardness, tensile tests on coupons), surface roughness measurements, visual inspection, Non-Destructive Testing (NDT) like CT scanning (X-ray) or dye penetrant testing if internal defect control is critical (less common for typical interior brackets but possible for high-stress applications).
- Importance: Ensures part quality, reliability, and compliance with automotive standards. Forms the final gate before shipping to the customer.
Integrated Post-Processing Workflow:
It’s important to view these steps not in isolation but as an integrated workflow. The order matters (e.g., stress relief before cutting from the plate, machining often after final heat treatment). The requirements for each step should be considered during the initial DfAM phase. Partnering with a knowledgeable AM service provider who understands the nuances of various printing methods and the associated post-processing chains for materials like AlSi10Mg and A6061 is crucial for producing high-quality, reliable automotive interior brackets. Ignoring or underestimating post-processing requirements is a common pitfall that can lead to project delays and unexpected costs.
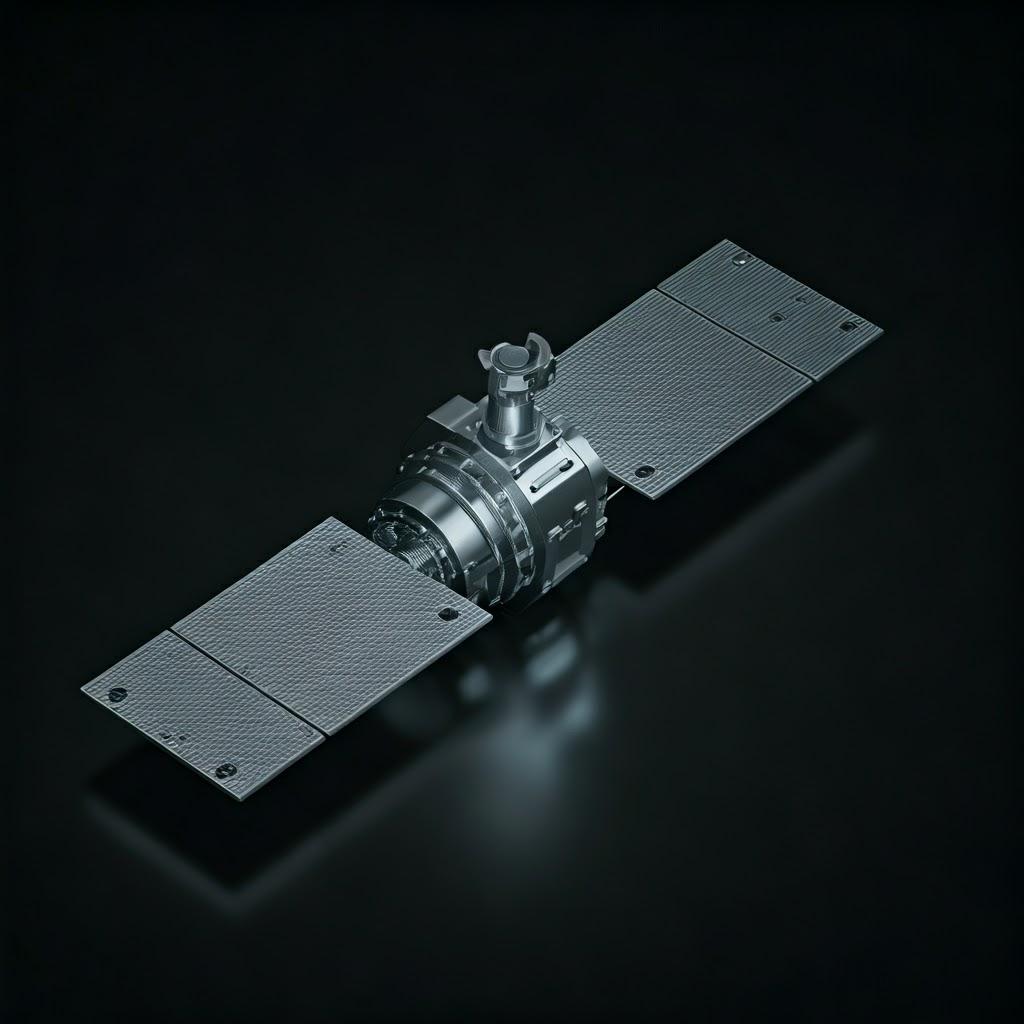
Navigating Common Challenges in Metal AM for Brackets (and Solutions)
While metal additive manufacturing offers tremendous advantages for producing automotive interior brackets, it’s not without its technical hurdles. Understanding the common challenges associated with processes like LPBF for aluminum alloys (AlSi10Mg, A6061) and knowing how to mitigate them is key to achieving consistent, high-quality results. Proactive design choices (DfAM), optimized process parameters, and robust post-processing are essential for overcoming these potential issues.
1. Warping and Distortion:
- Challenge: Parts lifting from the build plate, curling at edges, or distorting from their intended geometry during or after the printing process. This is a primary concern due to the high thermal gradients involved.
- Cause: Rapid, localized heating by the laser followed by rapid cooling creates steep temperature differences between the newly solidified layer and underlying material/build plate. This leads to differential expansion and contraction, generating significant internal residual stress metal AM. If these stresses exceed the material’s yield strength at elevated temperatures or the anchoring force of supports, deformation occurs.
- Solutions:
- Optimized Orientation: Orienting the part to minimize large flat surfaces parallel to the build plate and reduce the height of tall, thin features can lessen stress accumulation.
- Effective Support Structures: Robust supports anchor the part securely to the build plate, resist shrinkage forces, and help conduct heat away. Strategic placement is key.
- Build Plate Heating: Pre-heating the build plate (common in many LPBF machines) reduces the temperature gradient between the melt pool and the surrounding environment, lowering stress buildup.
- Optimized Scan Strategies: Using specific scan patterns (e.g., island scanning, varying hatch vectors) can help distribute heat more evenly and reduce localized stress peaks.
- Stress Relief Heat Treatment: Performing this crucial step before removing the part from the build plate allows stresses to relax while the part is still constrained, minimizing distortion upon release.
- Design Modifications (DfAM): Adding sacrificial ribs or ties, increasing thickness in prone areas, or using topology optimization to eliminate large solid blocks can help. Providing warping additive manufacturing solutions often starts at the design stage.
2. Support Structure Removal Difficulties:
- Challenge: Supports proving difficult, time-consuming, or impossible to remove without damaging the part, especially internal or intricate supports. Residual support material (“witness marks”) can affect fit or aesthetics.
- Cause: Poor DfAM choices (e.g., designing features requiring extensive, inaccessible supports), support parameters creating overly strong bonds, complex internal geometries.
- Solutions:
- DfAM Prioritization: Design for minimal support needs using self-supporting angles, chamfers, and optimal orientation.
- Accessible Supports: Ensure supports are placed where they can be reached with removal tools (manual or automated).
- Optimized Support Parameters: Tuning support density, connection points (teeth vs. solid block), and perforation can make them strong enough during the build but easier to break off later. Software often allows customization.
- Specialized Removal Techniques: Utilizing wire EDM, multi-axis CNC machining, or sometimes chemical etching (less common for aluminum) for challenging supports.
- Consider Alternative Orientations: Sometimes a slightly less optimal orientation for build time might dramatically simplify support removal.
3. Residual Stress Management:
- Challenge: Even if significant warping doesn’t occur, high levels of residual stress can remain within the part after printing. This can lead to premature failure under load, distortion during machining, or reduced fatigue life.
- Cause: Same as warping – the inherent thermal cycles of layer-wise fusion.
- Solutions:
- Mandatory Stress Relief: As mentioned, this is the primary method for significantly reducing bulk residual stress.
- Optimized Parameters & Scan Strategies: Careful control over laser power, speed, and scan patterns influences the thermal history and resulting stress state.
- Build Plate Heating: Helps reduce the overall stress level.
- Post-Build Treatments (Less Common for Brackets): Processes like shot peening can introduce beneficial compressive residual stresses on the surface, improving fatigue life, but don’t eliminate internal tensile stresses. Hot Isostatic Pressing (HIP) can also reduce stress but is more often used for porosity elimination.
- Design Considerations: Avoiding sharp internal corners, large rapid changes in cross-section, and incorporating fillets can help mitigate stress concentrations. Effective residual stress management AM is crucial for part performance.
4. Porosity:
- Challenge: The presence of small voids or pores within the printed material, which can compromise mechanical properties (especially fatigue strength and ductility) and act as crack initiation sites.
- Cause:
- Gas Porosity: Trapped shielding gas (Argon) within the melt pool due to instability or turbulence. Can also come from gas dissolved in the powder itself if powder quality is poor.
- Keyhole Porosity: Occurs when laser energy density is too high, causing deep vaporization of the metal which can collapse and trap gas.
- Lack-of-Fusion Porosity: Insufficient energy input leads to incomplete melting and bonding between layers or adjacent scan tracks, leaving voids.
- Solutions:
- Optimized Process Parameters: Dialing in the correct laser power, scan speed, hatch spacing, and layer thickness for the specific material (AlSi10Mg/A6061) and machine is paramount. This is a core expertise area for service providers like Met3dp.
- High-Quality Powder: Using powder with high sphericity, controlled PSD, low internal gas content, and low moisture/oxygen pickup minimizes gas and flowability-related porosity. Sourcing from reputable suppliers is essential for porosity control LPBF.
- Proper Gas Flow: Ensuring stable, laminar flow of inert shielding gas (Argon) across the build area prevents oxidation and helps remove metal vapor/spatter, promoting melt pool stability.
- Hot Isostatic Pressing (HIP): For critical applications requiring near-zero porosity, HIP (applying high temperature and isostatic gas pressure) can effectively close internal voids (but not surface-connected pores). This adds significant cost and is usually reserved for aerospace or medical applications, not typically standard interior brackets.
5. Material Consistency and Anisotropy:
- Challenge: Mechanical properties (e.g., strength, ductility) may differ slightly depending on the orientation the part was built in (X, Y vs. Z direction). This anisotropy is due to the layer-wise build process and the columnar grain growth common in AM microstructures. Ensuring consistent properties batch-to-batch can also be a concern.
- Cause: Layered fusion, directional solidification, and thermal history differences create microstructural variations. Variations in powder batches or machine calibration can affect consistency.
- Solutions:
- Process Control: Strict adherence to qualified printing parameters and regular machine calibration.
- Material Characterization: Understanding and documenting the anisotropic properties of the chosen material (AlSi10Mg/A6061) as produced by a specific machine/parameter set. Design engineers should account for potential directional property differences.
- Appropriate Heat Treatments: Post-build heat treatments (stress relief, T6) can homogenize the microstructure to some extent and reduce anisotropy, though some level may remain.
- Testing: Performing tensile testing on witness coupons built in different orientations (X, Y, Z) alongside production parts provides data on actual properties and consistency.
- Quality Powder Management: Ensuring consistent powder quality from batch to batch through rigorous supplier qualification and incoming inspection.
Navigating these metal 3D printing defects and challenges requires expertise, process control, and a collaborative approach. Working with an experienced additive manufacturing partner who understands the intricacies of printing automotive-grade materials like AlSi10Mg and A6061, possesses well-maintained equipment, utilizes high-quality materials, and implements robust quality management systems is the most effective way to mitigate risks and successfully produce reliable, high-performance interior brackets.
Selecting the Right Metal 3D Printing Partner for Automotive Components
Choosing the right manufacturing partner is a critical decision for any automotive project, and this holds especially true when venturing into the advanced realm of metal additive manufacturing. The unique complexities of AM processes like Laser Powder Bed Fusion (LPBF), combined with the stringent quality and performance demands of the automotive industry, mean that not all metal 3D printing service providers are created equal. Selecting a partner with the right expertise, technology, quality systems, and understanding of automotive requirements is paramount to successfully implementing 3D printed interior brackets, whether for prototyping or low-volume production. Procurement managers and engineers should evaluate potential automotive additive manufacturing suppliers based on a comprehensive set of criteria.
Key Evaluation Criteria for an AM Partner:
- Technical Expertise & Engineering Support:
- Material Knowledge: Deep understanding of the specific alloys being considered (e.g., AlSi10Mg, A6061), including their behavior during printing, required heat treatments (like T6 cycles), and resulting mechanical properties (including anisotropy).
- Process Optimization: Proven ability to develop and lock down robust process parameters for consistent, high-quality builds, minimizing defects like porosity or cracking.
- DfAM Capability: Offering Design for Additive Manufacturing consultation and support. Can they help optimize your bracket design for lightweighting, reduced support needs, and improved printability? Do they have experience with topology optimization workflows?
- Post-Processing Know-How: In-house or tightly managed external capabilities for all necessary post-processing steps (stress relief, support removal, heat treatment, machining, finishing) tailored for the specific material and application.
- Problem Solving: Experience in troubleshooting common AM challenges (warping, stress, porosity) and implementing effective solutions.
- Equipment, Technology & Capacity:
- Appropriate Technology: Possessing well-maintained industrial-grade LPBF machines suitable for processing aluminum alloys reliably. Enquire about machine brands, models, and maintenance schedules.
- Build Volume: Ensuring their machines have a large enough build envelope to accommodate the size of your brackets.
- Capacity: Sufficient machine availability to meet your project’s lead time requirements, whether for rapid prototypes or scheduled low-volume production runs. Understand their current workload and scheduling flexibility.
- Atmosphere Control: Robust inert gas management (Argon for aluminum) is critical for preventing oxidation and ensuring material quality during printing.
- Quality Management System (QMS) & Certifications:
- Relevant Certifications: Look for certifications demonstrating a commitment to quality and process control. ISO 9001 is a baseline requirement. For automotive components, IATF 16949 certification (or demonstrable compliance with its principles) is highly desirable, though still less common among AM-exclusive providers compared to traditional manufacturers. Ask about their roadmap for automotive certifications.
- Process Control: Evidence of documented procedures, parameter control, machine calibration routines, and operator training.
- Traceability: Ability to trace materials (powder batches), process data (build logs), and post-processing steps back to specific parts or batches. This is crucial for automotive accountability.
- Inspection Capabilities: In-house metrology equipment (CMM, 3D scanners, surface profilometers) and potentially NDT capabilities (though NDT for interior brackets might be overkill unless specified).
- Experience & Track Record:
- Automotive Experience: Have they successfully completed projects for other automotive OEMs or Tier suppliers? Do they understand the pace, documentation requirements (like PPAP elements, if needed), and quality expectations of the industry? Request case studies or references (respecting confidentiality).
- Application Experience: Specific experience producing similar components (brackets, structural parts) in the chosen materials is a significant advantage.
- Material Sourcing, Handling & Quality:
- Reputable Powder Suppliers: Sourcing high-quality metal powders from qualified suppliers known for consistency (like those employing advanced atomization techniques). Companies like Met3dp, who not only provide printing services but also specialize in manufacturing high-performance metal powders, inherently understand the critical link between powder quality and final part integrity. Learn more about Met3dp’s approach on their About Us page.
- Powder Management: Strict procedures for powder handling, storage (preventing moisture/oxygen pickup), sieving, recycling (tracking usage history), and batch control to ensure consistency and prevent cross-contamination.
- Lead Time, Communication & Responsiveness:
- Quoting Speed: How quickly can they provide detailed quotes based on your CAD data and specifications?
- Realistic Lead Times: Transparent communication about actual production lead times, considering machine availability and post-processing steps.
- Communication: Clear points of contact, regular updates on project status, and responsiveness to queries or concerns.
- Cost Competitiveness:
- While cost is always a factor, it shouldn’t be the only driver when selecting an AM partner for critical components. Compare quotes, but weigh them against the provider’s expertise, quality systems, and reliability. Understand what is included in the quote (e.g., specific post-processing steps, inspection reports).
Evaluation Summary Table:
Criterion | Key Questions to Ask Potential Partners | Desired Response/Evidence |
---|---|---|
Technical Expertise | Describe your experience with AlSi10Mg/A6061. How do you optimize parameters? Offer DfAM support? | Detailed material knowledge, documented processes, examples of DfAM improvements. |
Equipment & Capacity | What LPBF machines do you use for aluminum? What’s the build size? What’s your current capacity? | Well-maintained industrial machines, suitable build volume, transparent capacity info. |
Quality (QMS) | Are you ISO 9001 certified? IATF 16949? How do you ensure traceability & process control? | Relevant certifications (IATF ideal), documented QMS, clear traceability procedures. |
Experience | Can you share examples of automotive projects or similar bracket applications? | Relevant case studies/references (respecting NDA), understanding of automotive needs. |
Material Quality | Where do you source your powders? What are your powder handling & testing procedures? | Qualified suppliers, stringent handling protocols (storage, sieving, testing). |
Post-Processing | What post-processing do you perform in-house vs. outsource? Describe your heat treatment capabilities. | Comprehensive capabilities (in-house preferred), validated processes (esp. heat treat). |
Lead Time & Communication | What’s your typical quote turnaround? What are realistic lead times? Who is my point of contact? | Fast quoting, realistic timelines, clear communication channels & responsiveness. |
Cost | Provide a detailed cost breakdown. What’s included? Are there volume discounts? | Transparent pricing, clear inclusions/exclusions, understanding of cost drivers. |
Export to Sheets
Choosing the right additive manufacturing automotive supplier is an investment in quality and reliability. Thoroughly vetting potential partners against these criteria will significantly increase the likelihood of successfully leveraging metal AM for innovative and effective automotive interior brackets.
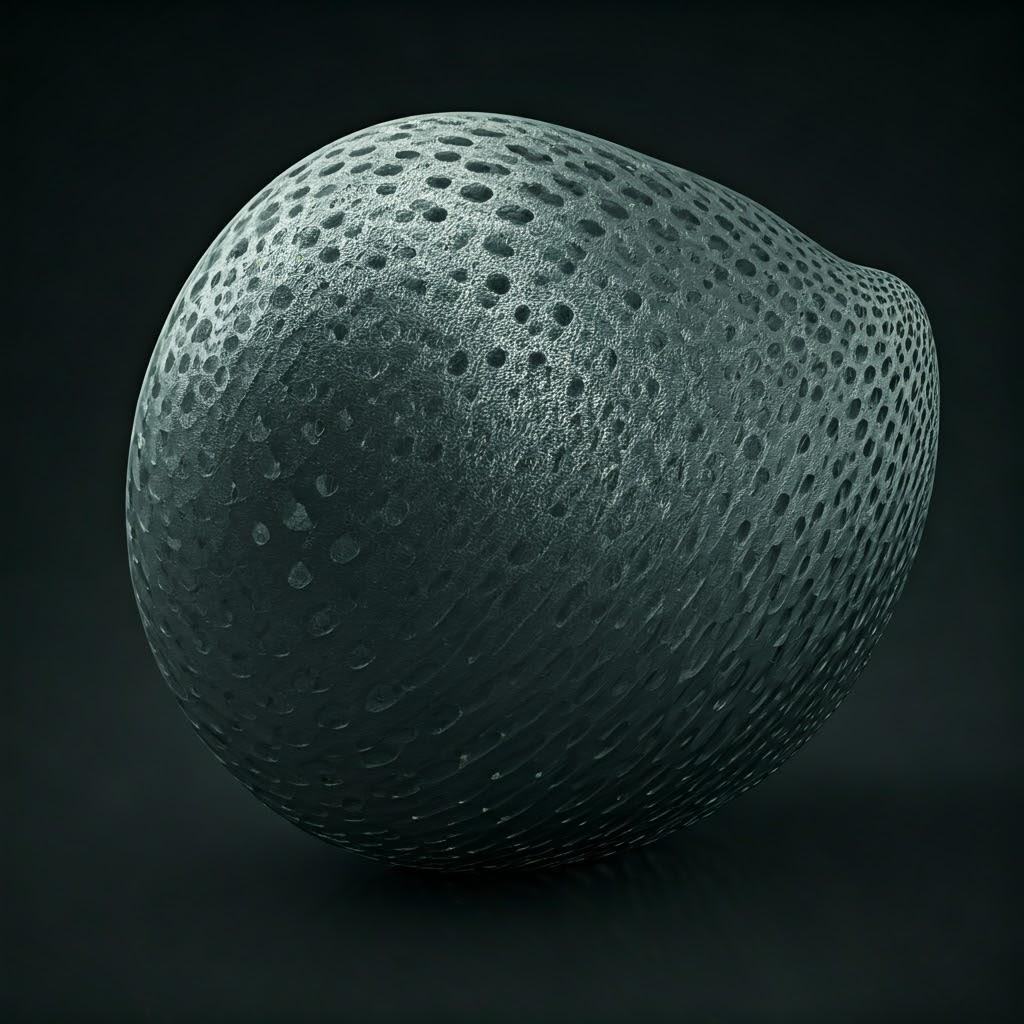
Understanding Cost Drivers and Lead Times for Printed Brackets
One of the most frequent questions regarding metal additive manufacturing concerns its cost and production speed compared to traditional methods. While AM offers compelling technical advantages, understanding the economic and logistical factors is crucial for project planning and budget allocation. The metal 3D printing cost and lead time additive manufacturing automotive components depend on a complex interplay of factors, often different from those governing conventional manufacturing.
Major Cost Drivers for 3D Printed Metal Brackets:
Unlike high-volume traditional processes dominated by tooling amortization, AM costs are more closely tied to direct resource consumption per part or build.
- Material Consumption:
- Part Volume: The actual volume of metal powder fused to create the bracket itself. This is often the most intuitive cost factor. DfAM techniques like topology optimization directly aim to minimize this.
- Support Structure Volume: The material used for supports also contributes significantly to cost. Minimizing supports through DfAM is key.
- Powder Cost: The price per kilogram of the chosen alloy (AlSi10Mg or A6061) impacts the overall cost. Powder quality and supplier also play a role.
- Powder Refresh Rate: Some powder degrades slightly with reuse (e.g., oxygen pickup, morphology changes). Service providers must factor in the cost of periodically refreshing the powder stock with virgin material.
- Machine Time:
- Build Height (Z-Height): Since printing is layer-by-layer, the height of the part (and its supports) in the build orientation is a primary driver of print time. Taller parts take longer.
- Part Volume & Density: Larger or denser parts require more laser scanning time per layer.
- Number of Parts per Build (Nesting): Printing multiple brackets simultaneously in one build (nesting) utilizes the machine more efficiently, reducing the per-part machine time cost. Effective nesting depends on part geometry and build volume.
- Machine Depreciation & Operating Costs: The high capital cost of industrial metal AM systems and their operational expenses (power, inert gas, maintenance) are factored into hourly machine rates.
- Labor:
- File Preparation: Setting up the build file, designing support structures (can be time-consuming if complex), and slicing the model.
- Machine Setup & Teardown: Preparing the machine, loading powder, unloading the build, initial cleaning.
- Depowdering: Manual or semi-automated removal of loose powder.
- Support Removal: Can be highly labor-intensive, depending on complexity and accessibility. Often requires skilled technicians.
- Manual Finishing: Any required hand finishing, deburring, or polishing.
- Quality Inspection: Labor associated with dimensional checks, visual inspection, documentation.
- Post-Processing:
- Heat Treatments: Costs associated with running furnace cycles (energy, gas, labor) for stress relief and/or final property attainment (e.g., T6).
- Machining: Costs of CNC machine time and labor for achieving tight tolerances or specific features.
- Surface Finishing: Costs of bead blasting, tumbling, anodizing, painting, etc.
- Quality Assurance & Complexity:
- Inspection Requirements: More stringent inspection protocols (e.g., CMM reports for multiple features, NDT) add cost.
- Part Complexity: While AM handles geometric complexity well during printing, highly intricate designs might increase labor costs for support removal or finishing.
Cost Factor Summary Table:
Cost Driver | Primary Influences | How to Mitigate/Optimize |
---|---|---|
Material Consumption | Part Volume, Support Volume, Powder Price | DfAM (Topology Opt.), Minimize Supports, Optimize Orientation |
Machine Time | Build Height, Part Volume/Density, Nesting Efficiency | Optimize Orientation (minimize Z), Effective Nesting |
Labor | File Prep Time, Support Complexity, Finishing Needs | DfAM (simplify supports), Automate Post-Processing where able |
Post-Processing | Heat Treat Cycles, Machining Needs, Surface Finish Spec | Specify only necessary steps/tolerances/finishes |
Quality Assurance | Inspection Level, Documentation Requirements | Define clear, appropriate QA requirements |
Export to Sheets
Typical Lead Times for Metal AM Brackets:
Lead times are sequential and depend heavily on the specific part, quantity, provider’s backlog, and required post-processing.
- Quoting & Order Confirmation: 1-3 business days (assuming clear data/requirements provided).
- File Preparation & Scheduling: 1-2 business days (can be longer if DfAM consultation is needed).
- Print Queue: Highly variable, from 1 day to 2+ weeks depending on machine availability. This is often the biggest variable.
- Printing: Hours to several days (e.g., a full build plate of nested brackets might take 24-72 hours or more).
- Cooling & Depowdering: ~1 day (cooling within the machine, then careful powder removal).
- Stress Relief: ~1 day (including furnace cycle and cooling).
- Cutting & Support Removal: 1-3 days (highly dependent on complexity and quantity).
- Heat Treatment (T6): 1-2 days (including furnace cycles and cooling).
- Machining: 1-5 days (depends on complexity, number of features, quantity).
- Finishing: 1-3 days (depends on process and quantity).
- Final Inspection & Shipping: 1-2 days.
Estimated Total Lead Times:
- Rapid Prototypes (1-5 parts): Typically 1 to 3 weeks, depending heavily on queue, complexity, and post-processing needs. Some providers offer expedited services for faster turnaround at a premium cost.
- Low-Volume Production (10-100+ parts): Typically 3 to 6 weeks or longer, depending on batch sizes, nesting efficiency, dedicated machine time, and the full extent of post-processing and QA involved.
It’s crucial to communicate lead time requirements clearly with the service provider early on and understand that additive manufacturing pricing and speed are influenced by factors distinct from traditional manufacturing. While AM excels at rapid initial part generation (no tooling delay), the overall process chain, especially comprehensive post-processing, must be factored in for realistic project timelines.
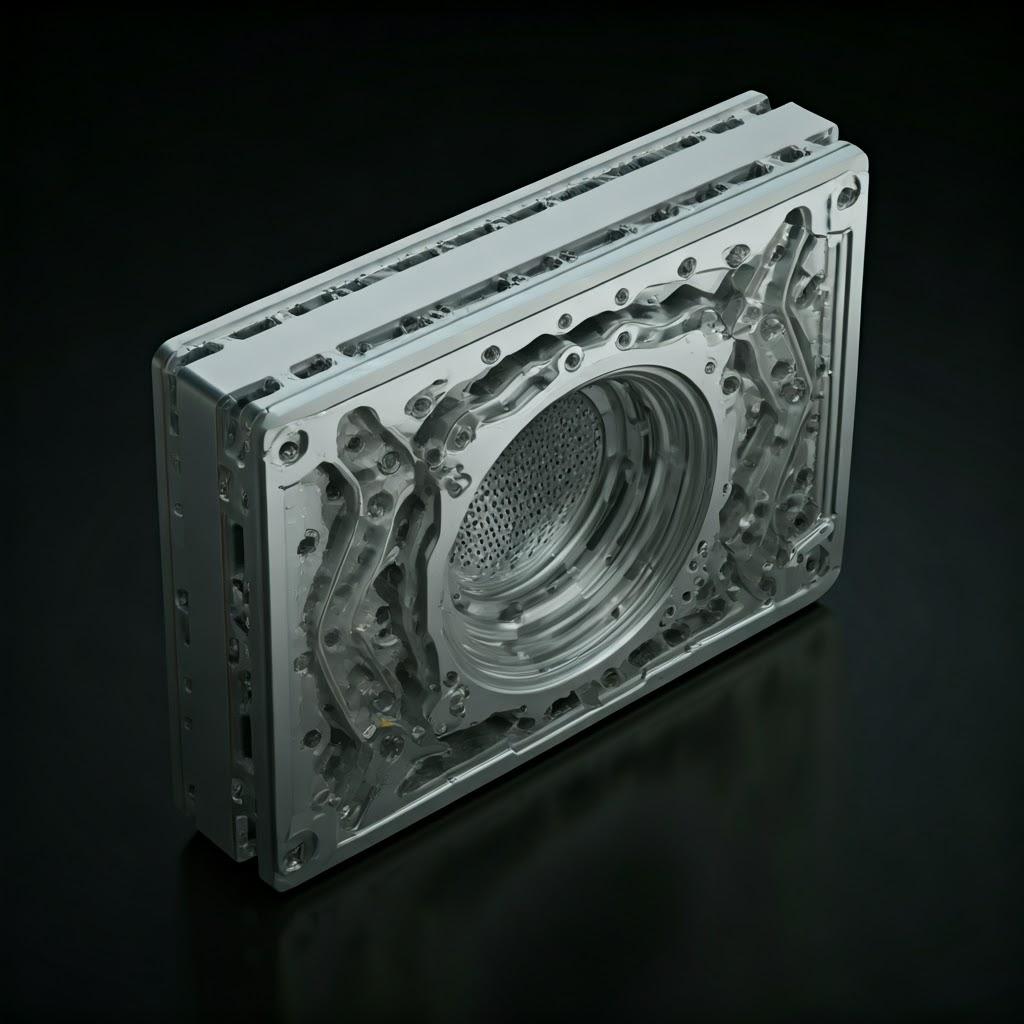
Frequently Asked Questions (FAQ) about 3D Printed Automotive Brackets
As metal additive manufacturing becomes more prevalent in the automotive sector, engineers and designers often have specific questions about its capabilities and limitations, particularly concerning components like interior brackets made from aluminum alloys. Here are answers to some common queries:
1. How does the strength of 3D printed AlSi10Mg/A6061 brackets compare to traditionally manufactured aluminum brackets (e.g., cast or machined)?
- The comparison depends heavily on the specific traditional process, the quality of the AM part, and the heat treatment applied.
- vs. Casting: High-quality LPBF parts made from AlSi10Mg or A6061, especially after appropriate heat treatment (e.g., T6), often exhibit superior mechanical properties (tensile strength, yield strength, fatigue life) compared to traditional castings of similar alloys. This is primarily due to the very fine microstructure achieved through AM’s rapid solidification rates, which minimizes defects common in casting like large grain sizes or porosity.
- vs. Machining (from Wrought Billet): Wrought alloys (like standard 6061-T6) typically represent the benchmark for strength and ductility. Well-produced and T6 heat-treated AM A6061 can achieve properties that are very close to, but sometimes slightly lower than, standard wrought 6061-T6, particularly regarding ductility or fatigue strength in certain build orientations. AM AlSi10Mg-T6 generally has lower strength and ductility compared to wrought 6061-T6 but is significantly stronger than cast aluminum.
- Anisotropy: It’s important to remember that AM parts can exhibit some degree of anisotropy, meaning properties might vary slightly depending on the build direction (X, Y vs. Z). This needs to be considered during design and validation, especially for fatigue-critical applications.
- Conclusion: Properly designed, printed (with high density >99.7%), and heat-treated AM aluminum brackets can offer mechanical performance comparable or superior to castings and approaching that of wrought materials, making them suitable for many structural interior applications. Performance relies heavily on process control and post-treatment. Get data sheets from your AM provider for the specific material/process/heat treatment state.
2. What is the maximum size automotive bracket that can realistically be 3D printed?
- The maximum size is primarily limited by the build volume of the available industrial metal AM machines.
- Common Industrial LPBF Systems: Many systems used for aluminum have build envelopes roughly in the range of 250 x 250 x 300 mm up to 400 x 400 x 400 mm. This is sufficient for a vast majority of typical automotive interior brackets.
- Large Format Systems: There are large format metal 3D printing systems available with significantly larger build volumes, reaching 600 mm or even 800 mm in X and Y, and up to 500mm or more in Z. However, these machines are less common and represent a higher cost tier.
- Practical Considerations: Printing very large monolithic parts via LPBF can present challenges:
- Cost: Machine time and material consumption increase significantly.
- Residual Stress & Warping: Managing thermal stresses becomes more critical in very large parts.
- Post-Processing: Handling, heat treating, and potentially machining very large AM parts requires specialized equipment.
- Alternatives: For extremely large structures, sometimes designing them as several smaller AM sections that are later joined (e.g., by welding or bolting) can be a more practical and cost-effective approach than printing a single massive piece.
- Conclusion: While technology exists for very large prints, most automotive interior brackets fall well within the capabilities of standard industrial LPBF machines. Discuss your specific size requirements with potential service providers to understand their machine capabilities.
3. Can 3D printed aluminum brackets be certified for use in critical automotive applications (e.g., safety-related)?
- Yes, it is possible, but it requires a rigorous and comprehensive qualification process. Simply printing a part does not automatically qualify it for critical use.
- Process Validation: The entire manufacturing workflow – from powder batch acceptance to printing parameters, post-processing steps (especially heat treatment), and inspection methods – must be rigorously validated and proven to be stable and repeatable.
- Material Characterization: Extensive testing is required to fully characterize the mechanical properties (static, dynamic, fatigue), microstructure, density, and chemical composition of the AM material as produced by the specific validated process. This includes understanding anisotropy.
- Adherence to Standards: The manufacturing process and quality management system must align with automotive standards, ideally IATF 16949. Full traceability is essential.
- Non-Destructive Testing (NDT): For safety-critical parts, NDT methods like industrial CT scanning (X-ray) might be required to ensure internal integrity and absence of critical flaws (though this adds significant cost and complexity).
- Performance Testing: The final bracket design must pass all functional and safety-related performance tests as required by the OEM or regulations (e.g., crash testing, durability testing).
- OEM Collaboration & Approval: Ultimately, the automotive OEM must approve the use of AM parts in critical applications based on the demonstrated process control, material data, and component performance.
- Conclusion: Achieving automotive certification 3D printing for critical components is a significant undertaking involving close collaboration between the AM provider and the automotive customer. While technically feasible and increasingly being explored, it demands a higher level of process maturity, control, and validation than typically required for non-critical interior brackets.
Conclusion: Driving the Future of Automotive Interiors with AM Brackets
The journey through the world of 3D printed automotive interior brackets reveals a technology poised to make significant contributions to the future automotive manufacturing landscape. Metal additive manufacturing, particularly Laser Powder Bed Fusion utilizing high-performance aluminum alloys like AlSi10Mg and A6061, offers a compelling alternative to traditional methods, addressing key industry drivers like lightweighting, design innovation, and accelerated development cycles.
We’ve explored how AM enables the creation of lightweight vehicle components through sophisticated topology optimization and lattice structure design, shedding critical grams and kilograms from the vehicle interior to improve fuel efficiency or electric range. The unparalleled design freedom allows engineers to consolidate parts, integrate functionality, and create complex geometries previously unattainable, leading to more efficient packaging and novel interior concepts. Furthermore, the ability to rapidly produce functional prototypes and facilitate low-volume automotive production without the need for expensive tooling fundamentally changes the economics and speed of vehicle development and customization.
However, realizing these benefits demands a holistic understanding of the AM ecosystem. Success hinges on embracing Design for Additive Manufacturing (DfAM) principles from the outset, carefully selecting the appropriate materials, understanding achievable tolerances and surface finishes, diligently executing essential post-processing steps like heat treatment and machining, and proactively navigating potential manufacturing challenges.
Crucially, the choice of a manufacturing partner is paramount. Collaborating with a knowledgeable and experienced metal 3D printing service provider – one with proven expertise in automotive applications, robust quality systems (like ISO 9001 and ideally alignment with IATF 16949), advanced equipment, a commitment to high-quality materials, and comprehensive engineering support – is fundamental to achieving reliable, high-performance results.
Companies like Met3dp, with their integrated approach encompassing both cutting-edge printing systems and the production of high-quality, spherical metal powders optimized for additive manufacturing, represent the type of partner capable of supporting the automotive industry’s adoption of this transformative technology. Exploring their comprehensive range of products, including SEBM printers and advanced metal powders, can provide further insight into the possibilities.
While metal AM won’t replace all traditional manufacturing methods overnight, its strategic application for components like interior brackets offers clear advantages in specific scenarios. As the technology continues to mature, costs decrease, and industry expertise grows, we can expect to see 3D printed metal parts playing an increasingly integral role in shaping lighter, more efficient, and more innovative automotive interiors. The potential for additive manufacturing impact automotive design is immense, and embracing its capabilities today paves the way for the vehicles of tomorrow.
Share On
MET3DP Technology Co., LTD is a leading provider of additive manufacturing solutions headquartered in Qingdao, China. Our company specializes in 3D printing equipment and high-performance metal powders for industrial applications.
Inquiry to get best price and customized Solution for your business!
Related Articles
About Met3DP
Recent Update
Our Product
CONTACT US
Any questions? Send us message now! We’ll serve your request with a whole team after receiving your message.
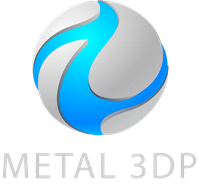
Metal Powders for 3D Printing and Additive Manufacturing