Jet Engine Superalloy Parts: 3D Printed in the USA
Table of Contents
Introduction: The Role of 3D Printing in Jet Engine Manufacturing
The aerospace industry is undergoing a manufacturing revolution, driven by additive manufacturing (AM), commonly known as 3D printing. One of the most critical applications of this technology is the production of jet engine components using superalloys—materials specifically designed to withstand extreme temperatures, high pressure, and mechanical stress.
Why is 3D printing crucial for jet engine parts?
- Complex Geometries: Traditional machining struggles with intricate designs. 3D printing allows for optimized, lightweight structures.
- Material Efficiency: Unlike subtractive manufacturing, which wastes material, 3D printing is resource-efficient.
- Reduced Lead Times: Aerospace manufacturers can accelerate prototyping and production cycles.
- Superior Performance: Superalloy parts produced via Selective Electron Beam Melting (SEBM) and Laser Powder Bed Fusion (LPBF) exhibit exceptional durability and heat resistance.
Companies like Metal3DP are at the forefront of this transformation, providing high-precision metal 3D printing solutions for aerospace, medical, and automotive applications. Learn more about Metal3DP’s metal 3D printing capabilities.
Market Trends: Growth of Additive Manufacturing in Aerospace
The global aerospace additive manufacturing market is expected to grow at a CAGR of 20%+ over the next decade. Several factors are driving this expansion:
Key Industry Drivers:
Trend | Impact on Aerospace Industry |
---|---|
Lightweighting | Reducing aircraft weight improves fuel efficiency. |
Supply Chain Resilience | On-demand manufacturing mitigates supply disruptions. |
Sustainability | Additive manufacturing minimizes material waste. |
Performance Optimization | Superalloys enhance jet engine efficiency and lifespan. |
Digital Manufacturing | Engineers can iterate and test designs rapidly. |
Superalloy Usage in Jet Engines
Superalloys like Inconel 718, Inconel 625, and Hastelloy X are widely used in jet engine components such as:
- Turbine blades
- Combustion chambers
- Exhaust nozzles
- Heat exchangers
With aerospace giants like Boeing, GE Aviation, and Rolls-Royce investing heavily in 3D printing research, the adoption of metal additive manufacturing is expected to skyrocket.
Metal3DP contributes to this growth by producing high-quality metal powders optimized for aerospace applications. Explore Metal3DP’s advanced metal powders.
Key Benefits of 3D Printing Superalloy Engine Parts
The shift from traditional casting and forging to 3D printing superalloy parts provides several advantages:
1. Weight Reduction & Fuel Efficiency
- Lattice structures reduce weight by up to 50% without compromising strength.
- Lighter jet engines improve fuel efficiency and reduce carbon emissions.
2. High-Temperature Resistance
- Superalloys withstand temperatures exceeding 1,000°C.
- Enhanced heat dissipation improves engine lifespan.
3. Rapid Prototyping & Customization
- Engineers can test new designs faster without expensive tooling.
- Customization allows for airline-specific engine modifications.
4. Cost Savings & Waste Reduction
- Traditional machining wastes up to 80% of the raw material.
- Additive manufacturing uses only the necessary amount of powder, reducing costs.
5. Enhanced Structural Integrity
- 3D-printed parts exhibit fewer defects and improved fatigue resistance.
- Grain structure optimization enhances durability.
Comparison: Conventional vs. 3D Printed Superalloy Parts
Feature | Conventional Manufacturing | Additive Manufacturing |
---|---|---|
Material Efficiency | High waste | Minimal waste |
Lead Time | Weeks/months | Days |
Complexity | Limited by machining | Unlimited |
Strength & Durability | Good | Superior grain structure |
Weight Reduction | Limited | Up to 50% |
Conclusion
The integration of 3D printing in jet engine manufacturing is revolutionizing the aerospace industry. By leveraging high-performance superalloys, companies can achieve lighter, stronger, and more fuel-efficient engines.
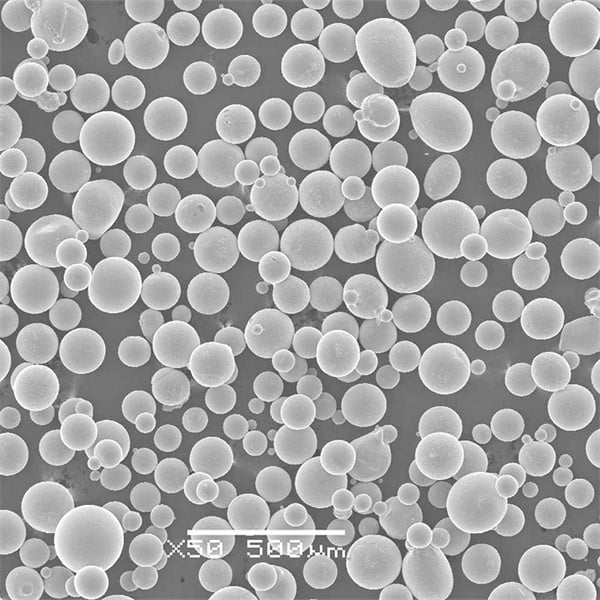
Top Suppliers of 3D Printed Jet Engine Superalloy Parts in the USA
The USA is a global leader in aerospace additive manufacturing, with multiple companies specializing in metal 3D printing for jet engine components. Here are some of the top suppliers:
1. GE Additive (a division of General Electric Aviation)
- Technology: Electron Beam Melting (EBM), Direct Metal Laser Melting (DMLM)
- Key Products: Turbine blades, combustion liners, heat exchangers
- Notable Achievements:
- Developed the world’s first FAA-certified 3D-printed fuel nozzle.
- Uses superalloys like Inconel 718 and Hastelloy X for jet engine parts.
2. Honeywell Aerospace Additive Manufacturing
- Technology: Laser Powder Bed Fusion (LPBF)
- Key Products: Airfoil components, combustion chamber parts
- Notable Achievements:
- Invested heavily in metal additive manufacturing for defense and commercial aircraft.
- Successfully printed heat exchangers with complex geometries.
3. Boeing Additive Manufacturing Division
- Technology: Selective Electron Beam Melting (SEBM), Binder Jetting
- Key Products: Exhaust nozzles, turbine blades
- Notable Achievements:
- Uses Titanium-Aluminide superalloys to create lighter and stronger jet engine parts.
- Working on on-demand 3D printing for aircraft maintenance.
4. RTX (Raytheon Technologies – Pratt & Whitney)
- Technology: Laser Powder Bed Fusion (L-PBF)
- Key Products: Turbine disks, fan blades
- Notable Achievements:
- Focuses on hypersonic and next-generation propulsion systems using 3D printing.
- Developing lightweight, high-strength superalloy components.
5. Metal3DP – A High-Performance Additive Manufacturing Partner
- Technology: Electron Beam Powder Bed Fusion (EB-PBF), Laser Powder Bed Fusion (L-PBF)
- Key Products: High-precision superalloy powders and 3D-printed engine parts
- Notable Achievements:
- Advanced powder-making system ensures high sphericity and flowability.
- Supplies high-quality metal powders for jet engine applications.
- Provides high-accuracy additive manufacturing solutions for aerospace.
Want to explore Metal3DP’s high-performance metal powders? Check out our product page.
Why Aerospace Companies Are Turning to Metal Additive Manufacturing
1. Enhanced Design Freedom & Performance
- Complex geometries such as lattice structures and internal cooling channels are impossible with traditional machining.
- 3D printing allows topology optimization, reducing weight while maintaining strength.
2. Faster Production & Lower Lead Times
Manufacturing Method | Average Lead Time |
---|---|
Traditional Casting | 8-16 weeks |
CNC Machining | 4-8 weeks |
3D Printing | 1-3 weeks |
- On-demand printing reduces dependency on long supply chains.
- Aerospace OEMs can quickly manufacture spare parts for MRO (Maintenance, Repair, and Overhaul).
3. Superior Material Performance
- Superalloys like Inconel 718 and Hastelloy X provide superior heat, corrosion, and fatigue resistance.
- Additive manufacturing improves grain structures, leading to longer-lasting jet engine parts.
4. Cost Reduction & Sustainability
- Material utilization efficiency: Traditional subtractive techniques waste up to 80% of material, while 3D printing only uses the required amount.
- Energy savings: The additive process consumes less power compared to forging and casting.
- Reduced carbon footprint: Lightweight aerospace components improve fuel efficiency, reducing emissions.
5. Meeting the Growing Demand for Next-Gen Aircraft
- The global aircraft fleet is expected to double by 2040.
- 3D printing enables faster development of next-generation propulsion systems.
Why Choose Metal3DP for High-Performance Superalloy Parts?
Metal3DP is a trusted partner for aerospace manufacturers looking to leverage additive manufacturing for jet engine superalloy components. Here’s why:
1. Industry-Leading Metal Powders
- High-purity spherical powders for advanced aerospace applications.
- Superalloy materials include Inconel 718, TiAl, CoCrMo, and Hastelloy X.
2. Advanced Powder Manufacturing System
- Gas Atomization & PREP Technology ensure consistent powder size and high flowability.
- Our powder-making system creates low-oxygen, high-sphericity alloys.
3. High-Precision Additive Manufacturing Solutions
- Electron Beam Powder Bed Fusion (EB-PBF) and Laser Powder Bed Fusion (L-PBF) technologies for high accuracy and strength.
- Custom 3D printing services for aerospace, medical, and automotive industries.
4. Experience in Mission-Critical Applications
- Our solutions are used in turbine blades, heat exchangers, and combustion chambers.
- We work with aerospace companies to implement next-gen additive manufacturing strategies.
5. Global Reach & Trusted Expertise
- Decades of experience in metal additive manufacturing.
- Partnering with leading aerospace firms to accelerate digital transformation.
Learn more about Metal3DP’s expertise in metal additive manufacturing.
Conclusion
The USA is home to some of the world’s top aerospace 3D printing companies, with Metal3DP playing a major role in advancing metal additive manufacturing for jet engine superalloy parts.
How to Order Custom 3D Printed Superalloy Parts for Jet Engines
Ordering custom 3D printed jet engine components requires precision, expertise, and a reliable supplier. At Metal3DP, we streamline the process to ensure high-quality parts with fast turnaround times.
Step-by-Step Ordering Process
Step | Description |
---|---|
1. Consultation & Requirements Gathering | Contact Metal3DP with your design requirements, material specifications, and performance needs. |
2. Material Selection | Choose from high-performance superalloys like Inconel 718, TiAl, CoCrMo, and Hastelloy X. |
3. Design & Optimization | Our experts optimize your 3D model for additive manufacturing to enhance strength, reduce weight, and improve heat resistance. |
4. Prototyping & Testing | We print sample parts using Electron Beam Powder Bed Fusion (EB-PBF) or Laser Powder Bed Fusion (L-PBF) for validation. |
5. Full-Scale Production | Once approved, we begin full-scale production, ensuring strict quality control and material integrity. |
6. Delivery & Support | We ship your precision-engineered jet engine parts with full documentation and post-production support. |
Why Order from Metal3DP?
✅ Industry-leading print accuracy and reliability
✅ Advanced metal powders with high sphericity and flowability
✅ Customizable solutions for aerospace applications
✅ Fast lead times and global shipping
Interested in ordering? Contact Metal3DP today to discuss your project.
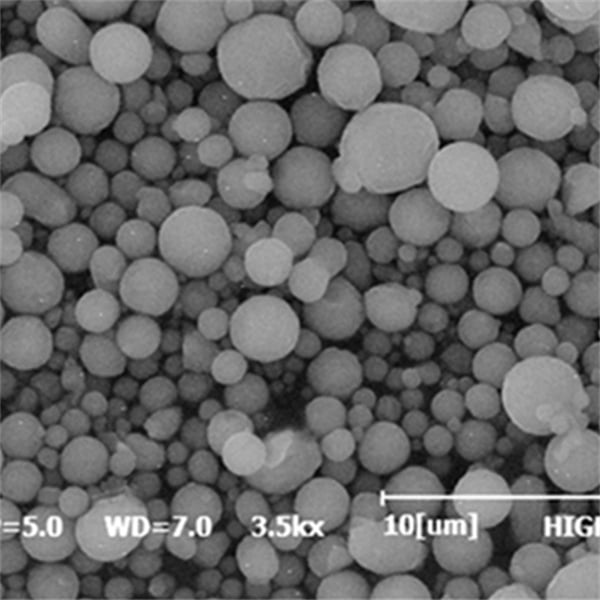
Future of 3D Printing in the Aerospace Industry
1. Next-Generation Materials & Superalloys
- Development of new high-temperature superalloys for hypersonic aircraft.
- Lighter and stronger materials for increased fuel efficiency.
2. Fully 3D Printed Jet Engines
- Companies like GE Aviation and Rolls-Royce are exploring fully 3D-printed jet engines.
- Future engines could feature integrated lattice structures for enhanced cooling.
3. AI & Automation in Additive Manufacturing
- AI-driven print parameter optimization for higher efficiency and reduced defects.
- Automated post-processing techniques to speed up production.
4. 3D Printing for Aircraft Maintenance & Repairs
- On-demand printing at airports to reduce downtime.
- Spare parts printed directly on-site for rapid aircraft maintenance.
5. Space Exploration & Aerospace Innovations
- NASA and SpaceX are using additive manufacturing for rocket engines.
- Lunar and Martian habitats may be built using 3D-printed metal structures.
Explore Metal3DP’s advanced aerospace 3D printing technologies here.
FAQs: Common Questions About 3D Printed Superalloy Parts
1. What are the best superalloys for jet engine 3D printing?
The most commonly used superalloys include:
- Inconel 718 – Excellent strength and heat resistance.
- Hastelloy X – Ideal for combustion chambers and exhaust components.
- Titanium-Aluminide (TiAl) – Lightweight and high-temperature resistant.
2. How does 3D printing compare to traditional forging for jet engine parts?
Feature | Traditional Forging | 3D Printing |
---|---|---|
Lead Time | 8-16 weeks | 1-3 weeks |
Material Waste | 50-80% | Minimal |
Design Complexity | Limited | Highly complex geometries possible |
Cost Efficiency | High tooling costs | Reduced tooling costs |
3. Can 3D-printed superalloy parts withstand extreme temperatures?
Yes! Superalloys like Inconel 718 and Hastelloy X are designed to withstand temperatures above 1,000°C, making them ideal for jet engine applications.
4. Is 3D printing FAA-approved for aerospace applications?
Yes, the FAA (Federal Aviation Administration) has approved several 3D-printed jet engine components, including:
- Fuel nozzles
- Turbine blades
- Heat exchangers
5. How do I ensure quality when ordering 3D-printed aerospace parts?
To guarantee quality:
- Work with certified suppliers like Metal3DP.
- Use high-purity metal powders with consistent particle size.
- Perform non-destructive testing (NDT) and material analysis.
Learn more about Metal3DP’s aerospace-grade metal powders here.
Conclusion & Call to Action
Why Metal3DP Is Your Best Partner for Aerospace 3D Printing
🚀 Expertise in high-performance metal powders and additive manufacturing
🚀 State-of-the-art printing technologies for jet engine applications
🚀 Custom solutions, fast lead times, and global shipping
Looking for a trusted supplier for 3D-printed superalloy jet engine parts? Contact Metal3DP today to discuss your project!
Internal Links Added in Part 3:
- Metal3DP Contact Page – Get in Touch
- Metal3DP Aerospace 3D Printing Methods – Explore Technologies
- Metal3DP Aerospace-Grade Metal Powders – Discover Now
Share On
MET3DP Technology Co., LTD is a leading provider of additive manufacturing solutions headquartered in Qingdao, China. Our company specializes in 3D printing equipment and high-performance metal powders for industrial applications.
Inquiry to get best price and customized Solution for your business!
Related Articles
About Met3DP
Recent Update
Our Product
CONTACT US
Any questions? Send us message now! We’ll serve your request with a whole team after receiving your message.
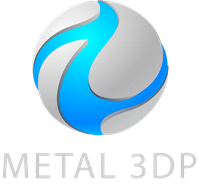
Metal Powders for 3D Printing and Additive Manufacturing