Laser Additive Manufacturing (LAM)
Table of Contents
Overview of Laser Additive Manufacturing (LAM)
Laser Additive Manufacturing (LAM) is a revolutionary technology in the realm of metal fabrication. It utilizes a high-powered laser to fuse metallic powders into intricate and precise components. This process, also known as 3D printing, is transforming industries by enabling the creation of complex geometries that were once impossible or highly costly to produce using traditional manufacturing methods.
LAM stands out for its ability to produce parts with exceptional strength, lightweight structures, and minimal waste. It’s a game-changer for industries like aerospace, automotive, and healthcare, where the demand for high-performance materials and customized components is ever-growing.
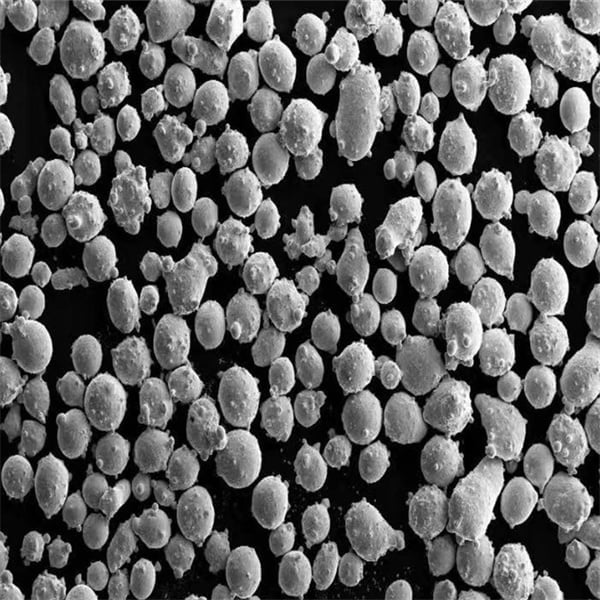
Types and Composition of Metal Powders in LAM
One of the critical elements in LAM is the metal powder used. The choice of powder significantly impacts the final product’s properties, quality, and performance. Here’s a detailed look at some specific metal powder models:
Metal Powder | Composition | Properties | Characteristics |
---|---|---|---|
Ti6Al4V (Titanium Alloy) | 90% Titanium, 6% Aluminum, 4% Vanadium | High strength, light weight | Excellent corrosion resistance, biocompatible |
316L Stainless Steel | 17% Chromium, 12% Nickel, 2% Molybdenum, Iron | High ductility, corrosion resistance | Non-magnetic, easy to weld |
Inconel 718 | Nickel, Chromium, Iron, Niobium | High-temperature resistance | Excellent mechanical properties at high temperatures |
AlSi10Mg (Aluminum Alloy) | 89% Aluminum, 10% Silicon, 1% Magnesium | Lightweight, good thermal conductivity | Good weldability, high fatigue strength |
CoCr (Cobalt-Chrome Alloy) | Cobalt, Chromium | Wear resistance, high strength | Biocompatible, excellent corrosion resistance |
Maraging Steel (18Ni300) | 18% Nickel, 12% Cobalt, 4% Molybdenum | High strength, toughness | Good dimensional stability, weldable |
Copper | Pure Copper | Excellent electrical conductivity | Good thermal conductivity, antibacterial properties |
H13 Tool Steel | Iron, 5% Chromium, 1% Molybdenum, 1% Vanadium | High toughness, heat resistance | Good wear resistance, high hardenability |
Ni625 (Nickel Alloy) | 58% Nickel, 21% Chromium, 9% Molybdenum | High corrosion resistance, strength | Good weldability, oxidation resistance |
Bronze | Copper, 12% Tin | Good wear resistance, low friction | Excellent machinability, corrosion resistance |
Applications of Laser Additive Manufacturing (LAM)
LAM’s versatility makes it suitable for a wide range of applications across various industries. Here are some of the primary uses:
Industry | Application | Description |
---|---|---|
Aerospace | Engine components, structural parts | Lightweight, strong parts with complex geometries |
Automotive | Custom parts, lightweight components | High-performance parts that reduce vehicle weight and improve efficiency |
Medical | Implants, prosthetics, surgical tools | Customized, biocompatible devices that enhance patient outcomes |
Energy | Turbine blades, heat exchangers | Durable, high-temperature resistant components for energy systems |
Tooling | Molds, dies, jigs | Precision tools that improve manufacturing processes |
Electronics | Heat sinks, connectors | Efficient thermal management and precise electronic components |
Jewelry | Custom designs, intricate patterns | High-detail, customized jewelry pieces |
Defense | Lightweight armor, weapon components | High-strength, durable parts for defense applications |
Architecture | Structural components, artistic elements | Unique, complex designs for modern architectural projects |
Consumer Products | Custom goods, intricate designs | Personalized products with intricate detailing |
Specifications, Sizes, Grades, and Standards of Metal Powders
Each metal powder used in LAM must meet specific standards and specifications to ensure optimal performance and quality. Here’s a comprehensive look at these aspects:
Metal Powder | Particle Size | Grade | Standard |
---|---|---|---|
Ti6Al4V | 15-45 µm | Grade 5 | ASTM B348, ISO 5832-3 |
316L Stainless Steel | 15-45 µm | Grade 316L | ASTM A240, ISO 5832-1 |
Inconel 718 | 15-53 µm | Grade 718 | AMS 5662, ASTM B637 |
AlSi10Mg | 20-63 µm | Grade 10Mg | ISO 3522, EN 1706 |
CoCr | 10-45 µm | F75, F799 | ASTM F75, ISO 5832-4 |
Maraging Steel 18Ni300 | 15-45 µm | Grade 300 | AMS 6514, ASTM A538 |
Copper | 20-45 µm | OFHC | ASTM F68, ISO 197-1 |
H13 Tool Steel | 15-45 µm | H13 | ASTM A681, DIN 1.2344 |
Ni625 | 15-53 µm | Grade 625 | AMS 5666, ASTM B446 |
Bronze | 20-45 µm | C90700 | ASTM B427, SAE J461 |
Suppliers and Pricing Details of Metal Powders
The pricing and availability of metal powders can vary based on the supplier and the specific requirements of the LAM process. Here’s a list of some suppliers and an overview of pricing details:
Supplier | Metal Powder | Price per kg | Availability |
---|---|---|---|
Höganäs | Ti6Al4V | $300 | Global |
Carpenter Additive | 316L Stainless Steel | $200 | Global |
LPW Technology | Inconel 718 | $400 | Global |
AP&C | AlSi10Mg | $150 | Global |
Sandvik | CoCr | $350 | Global |
GKN Hoeganaes | Maraging Steel 18Ni300 | $250 | Global |
Tekna | Copper | $100 | Global |
Renishaw | H13 Tool Steel | $200 | Global |
Oerlikon | Ni625 | $450 | Global |
Erasteel | Bronze | $180 | Global |
Comparing Pros and Cons of Different Metal Powders
Understanding the advantages and limitations of various metal powders is crucial for selecting the right material for specific applications in LAM. Here’s a comparative overview:
Metal Powder | Advantages | Disadvantages |
---|---|---|
Ti6Al4V | High strength-to-weight ratio, corrosion resistance | Expensive, requires careful handling during processing |
316L Stainless Steel | Corrosion resistant, good ductility | Lower strength compared to some other alloys |
Inconel 718 | Excellent high-temperature performance | High cost, difficult to machine |
AlSi10Mg | Lightweight, good thermal properties | Lower strength compared to steel alloys |
CoCr | Biocompatible, high wear resistance | Expensive, difficult to process |
Maraging Steel 18Ni300 | High strength, toughness | Requires post-processing heat treatment |
Copper | Excellent electrical and thermal conductivity | Oxidizes easily, not as strong as other metals |
H13 Tool Steel | High toughness, heat resistance | Requires heat treatment, can be difficult to machine |
Ni625 | High strength and corrosion resistance | Very expensive, difficult to process |
Bronze | Good machinability, wear resistance | Lower strength, can be more expensive than steel |
Advantages of Laser Additive Manufacturing (LAM)
Laser Additive Manufacturing offers several significant advantages that make it a preferred choice in various industries:
- Design Freedom: LAM allows for the creation of complex geometries that are impossible or highly costly with traditional methods. This opens up new possibilities in product design and innovation.
- Material Efficiency: LAM uses only the necessary amount of material, reducing waste and saving costs. This is particularly beneficial for expensive materials like titanium and nickel alloys.
- Customization: It enables the production of customized parts tailored to specific requirements, such as medical implants designed to fit a patient’s anatomy perfectly.
- Speed: LAM can significantly reduce the time from design to production, accelerating product development and time-to-market.
- Strength and Durability: Parts produced using LAM often exhibit superior mechanical properties, such as higher strength and better fatigue resistance, compared to those made with traditional manufacturing methods.
Disadvantages of Laser Additive Manufacturing (LAM)
Despite its many benefits, LAM also has some limitations that must be considered:
- High Cost: The initial investment in LAM equipment and materials can be substantial, which might be prohibitive for small businesses.
- Material Limitations: Not all materials are suitable for LAM, and the range of available powders can be limited.
- Surface Finish: Parts produced by LAM may require additional post-processing to achieve the desired surface finish and precision.
- Size Constraints: The build volume of LAM machines can be limited, making it challenging to produce very large parts.
- Complexity in Process: LAM requires a high level of expertise and careful control of process parameters to ensure quality and consistency.
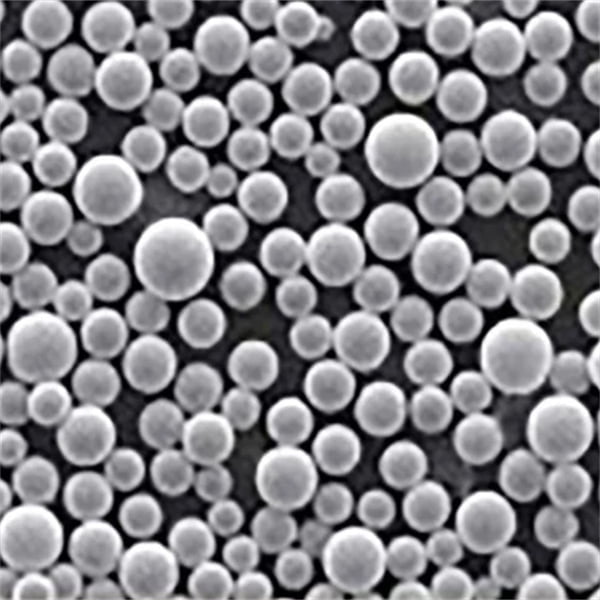
FAQ
Question | Answer |
---|---|
What is Laser Additive Manufacturing (LAM)? | LAM is a 3D printing technology that uses a high-powered laser to fuse metallic powders into precise, complex components. |
What materials can be used in LAM? | Various metal powders such as titanium alloys, stainless steels, nickel alloys, aluminum alloys, cobalt-chrome, copper, and tool steels can be used in LAM. |
What are the advantages of LAM over traditional manufacturing? | LAM offers design freedom, material efficiency, customization, speed, and superior mechanical properties, making it ideal for complex and high-performance parts. |
What are the common applications of LAM? | LAM is used in aerospace, automotive, medical, energy, tooling, electronics, jewelry, defense, architecture, and consumer products for various high-performance parts. |
What are the limitations of LAM? | LAM can be costly, has material limitations, may require post-processing for surface finish, has size constraints, and requires a high level of expertise. |
How does LAM improve material efficiency? | LAM uses only the necessary amount of material to build a part, reducing waste and saving costs, especially for expensive materials. |
What industries benefit the most from LAM? | Industries such as aerospace, automotive, medical, and energy benefit significantly from LAM due to its ability to produce high-performance, customized components. |
Is LAM suitable for large-scale production? | LAM is ideal for small to medium-sized production runs, especially for complex and customized parts, but it can be limited for very large-scale production. |
What is the cost range for metal powders used in LAM? | The cost of metal powders varies widely, from around $100 per kg for common materials like copper to over $450 per kg for specialized alloys like Ni625. |
How does LAM ensure part quality and consistency? | LAM requires careful control of process parameters, high-quality metal powders, and sometimes post-processing to ensure part quality and consistency. |
Conclusion
Laser Additive Manufacturing (LAM) represents a significant leap forward in the field of metal fabrication. With its ability to produce complex geometries, reduce waste, and offer superior material properties, LAM is transforming industries and pushing the boundaries of what’s possible in manufacturing. As technology advances and becomes more accessible, its applications will only continue to grow, making LAM an integral part of the future of manufacturing.
Share On
MET3DP Technology Co., LTD is a leading provider of additive manufacturing solutions headquartered in Qingdao, China. Our company specializes in 3D printing equipment and high-performance metal powders for industrial applications.
Inquiry to get best price and customized Solution for your business!
Related Articles
About Met3DP
Recent Update
Our Product
CONTACT US
Any questions? Send us message now! We’ll serve your request with a whole team after receiving your message.
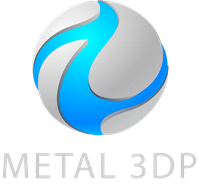
Metal Powders for 3D Printing and Additive Manufacturing