Laser Powder Bed Fusion
Table of Contents
Overview
Laser Powder Bed Fusion (LPBF) is a cutting-edge additive manufacturing technology that uses a laser to selectively fuse powder particles layer by layer to create highly intricate and precise metal parts. This technology has revolutionized various industries by enabling the production of complex geometries that are impossible or extremely difficult to achieve with traditional manufacturing methods.
Key Details of Laser Powder Bed Fusion
Table: Types, Composition, Properties, and Characteristics of Metal Powders for LPBF
Metal Powder | Composition | Properties | Characteristics |
---|---|---|---|
316L Stainless Steel | Fe, Cr, Ni, Mo | High corrosion resistance, good mechanical properties | Widely used in medical and aerospace |
Inconel 718 | Ni, Cr, Fe, Nb | High strength, oxidation, and corrosion resistance at high temperatures | Suitable for aerospace and gas turbines |
AlSi10Mg | Al, Si, Mg | High strength-to-weight ratio, good thermal conductivity | Used in automotive and aerospace |
Ti6Al4V | Ti, Al, V | Excellent strength, low weight, biocompatible | Popular in medical implants and aerospace |
CoCrMo | Co, Cr, Mo | High wear resistance, biocompatibility | Ideal for medical and dental applications |
Hastelloy X | Ni, Mo, Cr, Fe | High temperature resistance, good weldability | Used in aerospace and chemical processing |
Maraging Steel | Fe, Ni, Mo, Co | High strength, toughness, and hardness after aging | Suitable for tooling and high-stress applications |
Al6061 | Al, Mg, Si, Cu | Good mechanical properties, excellent corrosion resistance | Common in automotive and aerospace |
CuCr1 | Cu, Cr | High electrical and thermal conductivity | Ideal for electrical and thermal applications |
Tantalum | Ta | High density, excellent corrosion resistance | Used in medical devices and electronics |
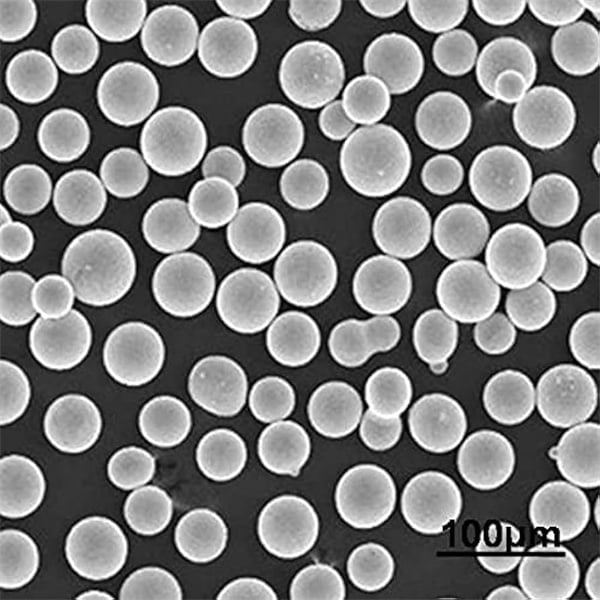
Applications of Laser Powder Bed Fusion
Table: Applications or Uses of Metal Powders in LPBF
Industry | Application | Metal Powders |
---|---|---|
Aerospace | Engine components, structural parts | Inconel 718, Ti6Al4V |
Automotive | Lightweight parts, prototypes | AlSi10Mg, Al6061 |
Medical | Implants, prosthetics | Ti6Al4V, CoCrMo, Tantalum |
Dental | Crowns, bridges | CoCrMo |
Oil & Gas | High-strength components, corrosion-resistant parts | Inconel 718, Hastelloy X |
Tooling | Molds, dies | Maraging Steel, H13 Tool Steel |
Electronics | Heat sinks, electrical components | CuCr1 |
Energy | Turbine blades, fuel cells | Inconel 718, Hastelloy X |
Defense | Lightweight armor, structural parts | Ti6Al4V, AlSi10Mg |
Consumer Goods | Customized jewelry, eyewear frames | Stainless Steel 316L, Al6061 |
Specifications, Sizes, Grades, Standards
Table: Specifications, Sizes, Grades, and Standards of Metal Powders for LPBF
Metal Powder | Specifications | Sizes (Microns) | Grades | Standards |
---|---|---|---|---|
316L Stainless Steel | ASTM A240 | 15-45 | 316L | ISO 9001, ASTM F138 |
Inconel 718 | AMS 5662 | 15-45 | Inconel 718 | ASTM B637, ISO 9001 |
AlSi10Mg | DIN EN 1706 | 20-63 | AlSi10Mg | ISO 9001, ASTM B179 |
Ti6Al4V | ASTM B348 | 15-45 | Ti6Al4V | ISO 9001, ASTM F1472 |
CoCrMo | ASTM F75 | 15-45 | CoCrMo | ISO 9001, ASTM F1537 |
Hastelloy X | AMS 5754 | 15-53 | Hastelloy X | ISO 9001, ASTM B435 |
Maraging Steel | AMS 6521 | 15-53 | Maraging 300 | ISO 9001, ASTM A538 |
Al6061 | ASTM B221 | 20-63 | Al6061 | ISO 9001, ASTM B221 |
CuCr1 | ASTM B224 | 15-45 | CuCr1 | ISO 9001, ASTM B224 |
Tantalum | ASTM B708 | 15-53 | Tantalum | ISO 9001, ASTM B708 |
Suppliers and Pricing Details
Table: Suppliers and Pricing Details of Metal Powders for LPBF
Supplier | Metal Powder | Price (USD/kg) | Location | Website |
---|---|---|---|---|
Carpenter Additive | 316L Stainless Steel | 100 | USA | carpenteradditive.com |
Sandvik | Inconel 718 | 250 | Sweden | additive.sandvik |
LPW Technology | AlSi10Mg | 150 | UK | lpwtechnology.com |
AP&C | Ti6Al4V | 300 | Canada | advancedpowders.com |
EOS GmbH | CoCrMo | 200 | Germany | eos.info |
Höganäs | Hastelloy X | 280 | Sweden | hoganas.com |
Carpenter Additive | Maraging Steel | 220 | USA | carpenteradditive.com |
Valimet | Al6061 | 140 | USA | valimet.com |
GKN Additive | CuCr1 | 180 | UK | gknpm.com |
Advanced Powders | Tantalum | 350 | USA | advancedpowders.com |
Advantages and Limitations of Laser Powder Bed Fusion
Table: Pros and Cons, Advantages and Limitations of LPBF
Parameter | Advantages | Limitations |
---|---|---|
Design Freedom | Ability to create complex geometries | Size limitations of build chamber |
Material Efficiency | High material utilization, minimal waste | Powder handling and recycling challenges |
Mechanical Properties | High-strength, functional parts | Residual stresses, potential for cracking |
Customization | Rapid production of customized parts | Slower build rates compared to some methods |
Production Speed | Faster for small to medium batches | High initial setup costs |
Surface Finish | Fine details, good surface finish | Post-processing often required |
Cost Efficiency | Cost-effective for complex, low-volume parts | Expensive raw materials |
Versatility | Wide range of materials available | Limited to metal powders |
Repeatability | High consistency and repeatability | Need for precise control and calibration |
Integration | Easy integration with digital workflows | Requires skilled operators |
Detailed Discussion on Key Aspects
Design Freedom with LPBF
Imagine being able to design and produce parts that were previously thought impossible. With Laser Powder Bed Fusion, the constraints of traditional manufacturing methods are blown away. You can create intricate lattice structures, complex internal channels, and organic shapes that are both lightweight and strong. Think of it like sculpting with lasers, where the only limit is your imagination.
Material Efficiency
One of the standout features of LPBF is its material efficiency. Traditional manufacturing often involves cutting away large amounts of material, leading to waste. LPBF, on the other hand, uses just the amount of powder needed for the part, significantly reducing waste. It’s like baking
a cake with just the right amount of ingredients, leaving nothing to throw away.
Mechanical Properties
The mechanical properties of parts produced with LPBF are impressive. They can match or even exceed those of traditionally manufactured parts. This is crucial for industries like aerospace and medical, where strength and durability are paramount. Imagine the confidence in knowing that a part created layer by layer with a laser can withstand the same stresses as one forged in a furnace.
Customization and Rapid Prototyping
LPBF is a game-changer for customization. Need a unique medical implant tailored to a patient’s anatomy? No problem. Need to quickly prototype a new part for an automotive application? Done. The speed and flexibility of LPBF mean you can go from design to production in a fraction of the time. It’s like having a personal factory that can make anything you dream up.
Production Speed and Cost Efficiency
While LPBF might not be the fastest method for high-volume production, it excels in small to medium batches. The ability to quickly produce complex parts without the need for molds or tooling makes it cost-effective for lower volumes. Imagine running a marathon where you can sprint when you need to, saving energy and resources along the way.
Surface Finish and Post-Processing
The surface finish of LPBF parts is generally good, but some post-processing is often required to achieve the desired smoothness. This might involve machining, polishing, or heat treatment. It’s like sanding a piece of wood to bring out the grain, enhancing the final product’s appearance and functionality.
Versatility and Repeatability
LPBF’s versatility is one of its strongest points. With a wide range of metal powders available, from aluminum to titanium to high-performance superalloys, the possibilities are vast. Plus, the repeatability of the process ensures that each part produced is consistent in quality. It’s like having a recipe that turns out perfect every time you bake it.
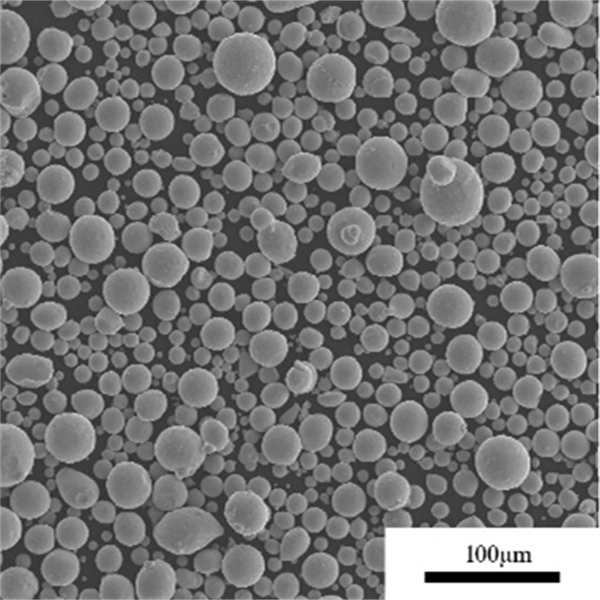
FAQs
Table: FAQ Section with Questions and Answers
Question | Answer |
---|---|
What is Laser Powder Bed Fusion? | LPBF is an additive manufacturing process that uses a laser to fuse metal powder particles layer by layer. |
What materials can be used in LPBF? | A wide range of metal powders, including stainless steel, aluminum, titanium, cobalt-chrome, and more. |
What are the advantages of LPBF? | Design freedom, material efficiency, high mechanical properties, customization, and cost efficiency. |
What are the limitations of LPBF? | Size limitations, powder handling challenges, potential for residual stresses, and high initial costs. |
How does LPBF compare to traditional manufacturing? | LPBF offers greater design flexibility and efficiency for complex parts but can be slower for high-volume production. |
Is post-processing required for LPBF parts? | Yes, post-processing such as machining, polishing, or heat treatment is often needed for the desired finish. |
What industries benefit most from LPBF? | Aerospace, automotive, medical, dental, oil & gas, tooling, electronics, energy, and defense. |
How does LPBF handle complex geometries? | LPBF excels at producing complex geometries with intricate details that are difficult with traditional methods. |
What is the cost of metal powders for LPBF? | Costs vary by material, ranging from around $100 to $350 per kilogram depending on the metal powder. |
Who are the leading suppliers of metal powders? | Suppliers include Carpenter Additive, Sandvik, LPW Technology, AP&C, EOS GmbH, Höganäs, and more. |
Conclusion
Laser Powder Bed Fusion is transforming the manufacturing landscape with its ability to produce highly intricate and precise metal parts. Its advantages in design freedom, material efficiency, mechanical properties, and customization make it a powerful tool for various industries. Despite some limitations, the potential of LPBF is vast, and as the technology continues to evolve, its applications will only expand. Whether you’re in aerospace, automotive, medical, or any other field, LPBF offers exciting possibilities for innovation and efficiency.
Share On
MET3DP Technology Co., LTD is a leading provider of additive manufacturing solutions headquartered in Qingdao, China. Our company specializes in 3D printing equipment and high-performance metal powders for industrial applications.
Inquiry to get best price and customized Solution for your business!
Related Articles
About Met3DP
Recent Update
Our Product
CONTACT US
Any questions? Send us message now! We’ll serve your request with a whole team after receiving your message.
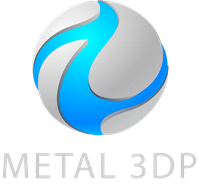
Metal Powders for 3D Printing and Additive Manufacturing