Laser Solid Forming (LSF)
Table of Contents
Laser Solid Forming (LSF) is a revolutionary technology in the field of additive manufacturing. It merges the principles of laser cladding and 3D printing to create high-precision, high-performance metal parts directly from digital designs. The process uses a laser to fuse metal powders into solid objects, layer by layer, resulting in parts with excellent mechanical properties and complex geometries. Let’s dive deep into the intricacies of LSF, exploring its types, applications, benefits, limitations, and more.
Overview of Laser Solid Forming (LSF)
LSF stands out in the additive manufacturing domain for its capability to produce parts with superior mechanical properties and intricate designs. This technology is particularly beneficial for industries requiring high-performance components, such as aerospace, automotive, and medical devices. By using a high-powered laser, LSF melts metal powders that are precisely deposited layer by layer, forming a solid structure. This method ensures high accuracy, minimal waste, and the ability to produce complex shapes that would be challenging or impossible with traditional manufacturing techniques.
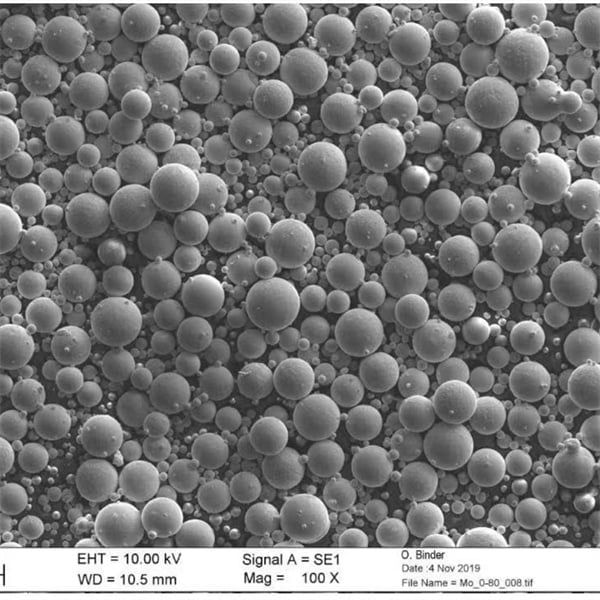
Types of Metal Powders Used in LSF
Different metal powders are utilized in LSF to cater to various application needs. Here are ten specific metal powder models commonly used in LSF:
Metal Powder | Composition | Properties | Characteristics |
---|---|---|---|
Inconel 718 | Nickel-chromium | High strength, corrosion resistance | Excellent weldability, used in aerospace |
Ti-6Al-4V | Titanium alloy | High strength-to-weight ratio | Biocompatible, used in medical implants |
316L Stainless Steel | Chromium-nickel-molybdenum | Corrosion resistance, good mechanical properties | Widely used in marine applications |
AlSi10Mg | Aluminum alloy | Lightweight, good thermal conductivity | Ideal for automotive parts |
Maraging Steel | Nickel-cobalt | Ultra-high strength | Used in tooling and aerospace |
Cobalt-Chrome | Cobalt-chromium-molybdenum | High wear and corrosion resistance | Common in dental and medical implants |
H13 Tool Steel | Chromium-molybdenum | High toughness and wear resistance | Used in molds and dies |
Copper (Cu) | Pure copper | Excellent thermal and electrical conductivity | Used in electrical components |
NiTi (Nitinol) | Nickel-titanium | Shape memory and superelasticity | Used in medical devices and actuators |
Tantalum (Ta) | Pure tantalum | High corrosion resistance | Used in chemical processing equipment |
Applications of Laser Solid Forming (LSF)
LSF’s versatility allows it to be used across a wide range of industries. Here are some applications:
Industry | Application | Benefits |
---|---|---|
Aerospace | Turbine blades, structural components | Lightweight, high strength, complex geometries |
Automotive | Engine parts, custom components | Reduced weight, improved performance |
Medical | Implants, surgical tools | Biocompatibility, customization |
Energy | Turbines, heat exchangers | High efficiency, corrosion resistance |
Tooling | Molds, dies | High wear resistance, precision |
Defense | Weapon components, armor | Durability, complex designs |
Electronics | Connectors, heat sinks | Excellent thermal conductivity |
Jewelry | Custom designs, intricate patterns | High precision, unique aesthetics |
Marine | Propellers, hull components | Corrosion resistance, strength |
Construction | Structural parts, repair work | Durability, on-site manufacturing |
Specifications, Sizes, Grades, and Standards in LSF
Different industries require parts with specific standards and specifications. Here’s a table summarizing some key specifications:
Specification | Details |
---|---|
Laser Power | 200W to 10kW |
Layer Thickness | 20-100 microns |
Build Volume | Up to 1m³ |
Resolution | ±0.05 mm |
Surface Finish | As low as Ra 1.6 µm |
Standards | ISO/ASTM 52900, ASME BPVC, AMS 4999 |
Material Grades | Inconel 718, Ti-6Al-4V Grade 23, 316L, AlSi10Mg |
Suppliers and Pricing Details for LSF Metal Powders
When choosing metal powders for LSF, it’s crucial to consider suppliers and pricing. Here’s an overview:
Supplier | Metal Powder | Price (per kg) | Comments |
---|---|---|---|
Höganäs | Inconel 718 | $150-$200 | High purity, consistent quality |
Sandvik | Ti-6Al-4V | $250-$350 | Medical-grade, excellent properties |
Carpenter Technology | 316L Stainless Steel | $50-$80 | Widely available, cost-effective |
LPW Technology | AlSi10Mg | $70-$100 | High-quality, reliable supplier |
GKN Additive | Maraging Steel | $200-$300 | Ultra-high strength, premium grade |
HC Starck | Cobalt-Chrome | $150-$250 | Ideal for medical applications |
Arcam AB | H13 Tool Steel | $100-$150 | High toughness, wear resistance |
Oerlikon Metco | Copper | $60-$90 | Excellent conductivity, pure grade |
ATI Specialty Alloys | NiTi (Nitinol) | $300-$450 | Premium quality, shape memory |
Global Advanced Metals | Tantalum | $400-$600 | High corrosion resistance, pure |
Advantages of Laser Solid Forming (LSF)
LSF offers numerous benefits over traditional manufacturing methods:
- High Precision and Accuracy: LSF allows for the creation of highly detailed parts with tight tolerances.
- Material Efficiency: Minimal waste is generated, as the process uses only the material needed for the part.
- Complex Geometries: Capable of producing intricate designs that are impossible with conventional methods.
- Customization: Parts can be tailored to specific requirements, ideal for bespoke applications.
- Reduced Lead Time: Faster production compared to traditional manufacturing, especially for complex parts.
- Superior Mechanical Properties: The layered structure can enhance the mechanical properties of the final part.
Disadvantages of Laser Solid Forming (LSF)
While LSF has many advantages, there are also some limitations:
- High Initial Cost: The setup cost for LSF equipment and materials can be high.
- Limited Material Variety: Not all materials are suitable for LSF, limiting its application range.
- Post-Processing Requirements: Some parts may require additional finishing processes to achieve the desired surface quality.
- Technical Expertise: Requires skilled operators and advanced knowledge to optimize the process.
- Build Size Limitations: Larger parts may be constrained by the size of the build chamber.
Comparison of Metal Powders for LSF
Understanding the pros and cons of different metal powders is crucial for choosing the right material:
Metal Powder | Advantages | Disadvantages |
---|---|---|
Inconel 718 | High strength, corrosion resistance | High cost |
Ti-6Al-4V | Lightweight, biocompatible | Difficult to machine |
316L Stainless Steel | Corrosion resistance, affordable | Lower strength compared to alloys |
AlSi10Mg | Lightweight, good conductivity | Lower mechanical strength |
Maraging Steel | Ultra-high strength | Expensive |
Cobalt-Chrome | Wear resistance, biocompatible | High cost, difficult to process |
H13 Tool Steel | Toughness, wear resistance | Requires post-processing |
Copper (Cu) | Excellent conductivity | Oxidizes easily |
NiTi (Nitinol) | Shape memory, superelasticity | Very high cost |
Tantalum (Ta) | Corrosion resistance | Extremely expensive |
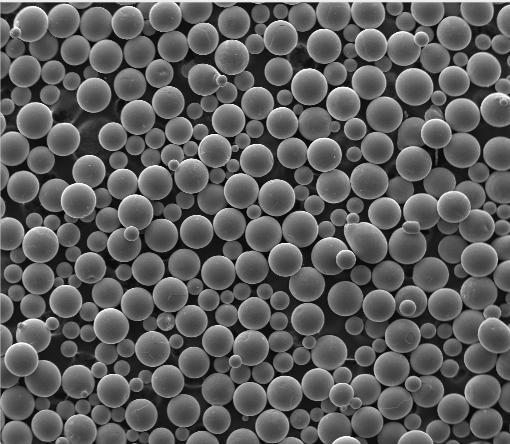
FAQ
Question | Answer |
---|---|
What is Laser Solid Forming (LSF)? | LSF is an additive manufacturing process that uses a laser to fuse metal powders into solid objects layer by layer. |
Which industries use LSF? | Aerospace, automotive, medical, energy, tooling, defense, electronics, jewelry, marine, and construction. |
What are the benefits of LSF? | High precision, material efficiency, ability to create complex geometries, customization, reduced lead time, and superior mechanical properties. |
What are the limitations of LSF? | High initial cost, limited material variety, post-processing requirements, need for technical expertise, and build size limitations. |
Which metal powders are commonly used in LSF? | Inconel 718, Ti-6Al-4V, 316L Stainless Steel, AlSi10Mg, Maraging Steel, Cobalt-Chrome, H13 Tool Steel, Copper, NiTi (Nitinol), and Tantalum. |
How does LSF compare to traditional manufacturing? | LSF offers higher precision, material efficiency, and the ability to create complex designs, but it can be more expensive and requires advanced technical knowledge. |
Share On
MET3DP Technology Co., LTD is a leading provider of additive manufacturing solutions headquartered in Qingdao, China. Our company specializes in 3D printing equipment and high-performance metal powders for industrial applications.
Inquiry to get best price and customized Solution for your business!
Related Articles
About Met3DP
Recent Update
Our Product
CONTACT US
Any questions? Send us message now! We’ll serve your request with a whole team after receiving your message.
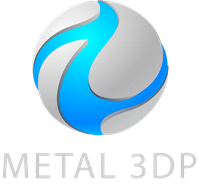
Metal Powders for 3D Printing and Additive Manufacturing