Lightweight Leading Edges: Revolutionizing Aerospace with Metal 3D Printing
Table of Contents
Introduction – The Critical Role of Leading Edges in Aerospace and the Promise of Additive Manufacturing
In the demanding realm of aerospace engineering, every component plays a crucial role in ensuring the safety, efficiency, and performance of aircraft. Among these critical parts, leading edges – the forward sections of wings and other aerodynamic surfaces – are paramount. They directly interact with airflow, significantly influencing lift, drag, stability, and overall flight characteristics. Traditionally manufactured using conventional methods like machining and forming, leading edges often present challenges in terms of weight optimization, complex geometries, and material utilization.
Enter metal additive manufacturing, also known as metal 3D printing, a transformative technology that is reshaping how aerospace components are conceived, designed, and produced. By building parts layer by layer from metal powders, metal 3D printing offers unprecedented design freedom, the ability to create intricate internal structures, and the potential for significant weight reduction without compromising structural integrity. For aerospace leading edges, this translates to enhanced fuel efficiency, improved aircraft performance, and the possibility of incorporating advanced aerodynamic features.
Metal3DP Technology Co., LTD, headquartered in Qingdao, China, stands at the forefront of this revolution. As a leading provider of additive manufacturing solutions, Metal3DP specializes in both cutting-edge 3D printing equipment and high-performance metal powders tailored for demanding industrial applications, including aerospace. Our printers are engineered to deliver industry-leading print volume, accuracy, and reliability – essential for the mission-critical nature of aerospace components. Furthermore, our advanced powder making system ensures the production of high-quality metal spherical powders, enabling customers to 3D print dense, high-performance metal parts with superior mechanical properties. Explore our comprehensive range of metal 3D printing services at Metal 3D Printing.
What are Lightweight Leading Edges Used For in Aerospace Applications?
Lightweight leading edges are integral components across various aerospace applications, each leveraging their unique aerodynamic properties to achieve specific functionalities. Here’s a breakdown of their primary uses:
- Aircraft Wings: Leading edges of wings are crucial for generating lift and controlling airflow over the wing surface. Lightweight designs contribute to reduced overall aircraft weight, leading to lower fuel consumption and increased payload capacity. Advanced leading edge designs, enabled by metal 3D printing, can incorporate features like Krueger flaps or slats to enhance lift during takeoff and landing.
- Stabilizers (Horizontal and Vertical): The leading edges of horizontal and vertical stabilizers play a vital role in maintaining aircraft stability and control. Reducing their weight improves the aircraft’s overall maneuverability and reduces inertia.
- Engine Nacelles: The leading edges of engine nacelles are designed to efficiently channel air into the engine while minimizing drag. Lightweight materials and optimized designs contribute to improved engine performance and fuel efficiency.
- Rotor Blades (Helicopters and Turboprops): For rotary-wing aircraft, the leading edges of rotor blades are critical for aerodynamic efficiency and durability. Lightweight, precisely manufactured leading edges enhance rotor performance and reduce vibration.
- Control Surfaces (Ailerons, Elevators, Rudders): The leading edges of control surfaces directly interact with airflow to effect changes in the aircraft’s attitude. Lightweight designs ensure responsiveness and reduce the load on actuation systems.
- Air Intakes: Leading edges of air intakes for various systems (e.g., auxiliary power units) are designed for efficient airflow capture. Lightweight materials contribute to overall weight savings.
The ability of metal 3D printing to produce complex geometries and optimize material distribution makes it an ideal manufacturing method for creating lightweight leading edges tailored to these diverse applications. This allows for the integration of features that would be difficult or impossible to achieve with traditional manufacturing techniques, further enhancing performance and efficiency. You can learn more about the versatility of metal 3D printing in various industries on our Product Page.
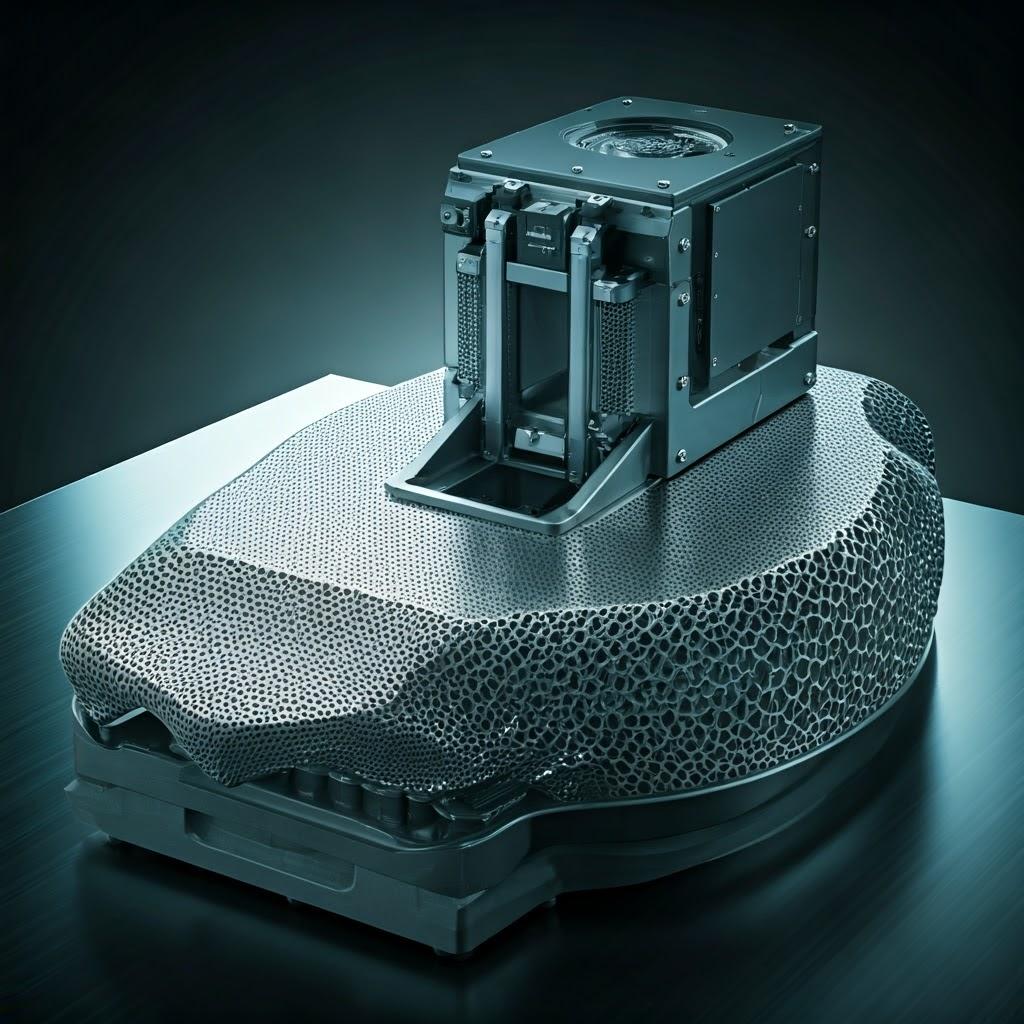
Why Choose Metal 3D Printing for Aerospace Leading Edge Manufacturing?
Opting for metal 3D printing over traditional manufacturing methods for aerospace leading edges offers a compelling array of advantages:
- Weight Reduction: Metal 3D printing enables the creation of complex internal lattice structures and topology-optimized designs, significantly reducing the weight of leading edges without sacrificing structural integrity. This directly translates to improved fuel efficiency, increased payload capacity, and enhanced aircraft performance – critical factors in the aerospace industry.
- Design Freedom and Complexity: Additive manufacturing liberates engineers from the design constraints of traditional methods. Intricate geometries, including conformal cooling channels for thermal management, integrated stiffening features, and optimized aerodynamic profiles, can be easily realized. This allows for the creation of leading edges with superior performance characteristics.
- Material Efficiency: Metal 3D printing utilizes material only where it’s needed, minimizing waste compared to subtractive manufacturing processes like machining. This is particularly important when working with expensive aerospace-grade alloys such as titanium and aluminum.
- Rapid Prototyping and Iteration: The speed and flexibility of metal 3D printing accelerate the design and development cycle. Engineers can quickly iterate on designs, produce prototypes, and test them, leading to faster innovation and reduced time-to-market.
- Customization and On-Demand Manufacturing: Metal 3D printing allows for the production of customized leading edges tailored to specific aircraft models or mission requirements. It also enables on-demand manufacturing, reducing the need for large inventories and streamlining the supply chain.
- Enhanced Functionality: Metal 3D printing facilitates the integration of multiple functionalities into a single component. For example, a leading edge could be designed with integrated sensors for real-time monitoring of airflow or structural health.
- High-Performance Materials: Metal 3D printing is compatible with a wide range of high-performance metal powders, including titanium alloys (like Ti-6Al-4V), aluminum alloys (like AlSi10Mg), and other advanced materials crucial for aerospace applications. Metal3DP offers a comprehensive portfolio of these high-quality metal powders, manufactured using industry-leading gas atomization and PREP technologies to ensure superior quality and performance. Our advanced Powder Making System guarantees metallic spheres with high sphericity and excellent flowability, essential for consistent and reliable 3D printing.
By leveraging the capabilities of metal 3D printing, aerospace manufacturers can achieve significant advancements in the design, performance, and efficiency of leading edge components. To understand more about the various additive manufacturing processes we utilize, visit our page on Printing Methods.
Recommended High-Performance Metal Powders for Aerospace Leading Edges
The selection of the appropriate metal powder is paramount in achieving the desired performance characteristics for 3D printed aerospace leading edges. The harsh operating conditions, including extreme temperatures, high stresses, and potential corrosion, demand materials with exceptional strength-to-weight ratios, fatigue resistance, and environmental durability. Here are the recommended powders for lightweight leading edges:
1. Ti-6Al-4V (Titanium Grade 5):
- Key Properties: Ti-6Al-4V is an alpha-beta titanium alloy renowned for its excellent strength-to-weight ratio, high tensile strength, exceptional corrosion resistance (especially to salt water and many chemicals), and good fatigue properties. It exhibits good biocompatibility and is widely used in aerospace, medical, and other high-performance applications.
- Why it Matters for Leading Edges: Its lightweight nature and high strength are crucial for reducing the overall weight of aircraft while maintaining structural integrity under demanding flight conditions. The excellent corrosion resistance ensures long-term durability in various atmospheric environments.
- Metal3DP Advantage: Metal3DP manufactures high-quality Ti-6Al-4V powder specifically optimized for laser and electron beam powder bed fusion (LPBF and EBPBF) processes. Our powders exhibit high sphericity and flowability, ensuring consistent powder feeding and dense, defect-free prints with superior mechanical properties.
2. AlSi10Mg (Aluminum Silicon Magnesium):
- Key Properties: AlSi10Mg is a lightweight aluminum alloy with good strength, high hardness, and excellent thermal conductivity. It offers good corrosion resistance and is readily weldable. This alloy is widely used in aerospace and automotive industries for structural components and parts requiring good thermal management.
- Why it Matters for Leading Edges: Its low density makes it an ideal choice for achieving significant weight reductions in leading edge applications. The good thermal conductivity can be beneficial in managing heat generated due to air friction at high speeds.
- Metal3DP Advantage: Metal3DP‘s AlSi10Mg powder is produced using advanced atomization techniques, resulting in a fine, spherical powder with excellent flow characteristics. This ensures high packing density in the powder bed, leading to 3D printed parts with superior density and mechanical properties. Our commitment to quality ensures that our AlSi10Mg powder meets the stringent requirements of aerospace applications.
The table below summarizes the key properties and benefits of these recommended powders:
Property | Ti-6Al-4V | AlSi10Mg |
---|---|---|
Density | ~4.43 g/cm³ | ~2.67 g/cm³ |
Tensile Strength | ~900-1100 MPa | ~400-450 MPa |
Yield Strength | ~830-950 MPa | ~290-330 MPa |
Elongation at Break | ~10-15% | ~5-10% |
Corrosion Resistance | Excellent | Good |
Thermal Conductivity | Low (~6.7 W/m·K) | High (~160 W/m·K) |
Key Benefits for Leading Edges | High strength-to-weight ratio, excellent corrosion resistance | Lightweight, good strength, excellent thermal conductivity |
Metal3DP Availability | Yes | Yes |
Export to Sheets
Metal3DP‘s expertise extends beyond just providing these high-quality powders. Our application development services assist aerospace companies in selecting the optimal material and printing parameters for their specific leading edge applications, ensuring the best possible performance and reliability. Contact Metal3DP to explore how our capabilities can power your organization’s additive manufacturing goals, as mentioned on our Homepage.
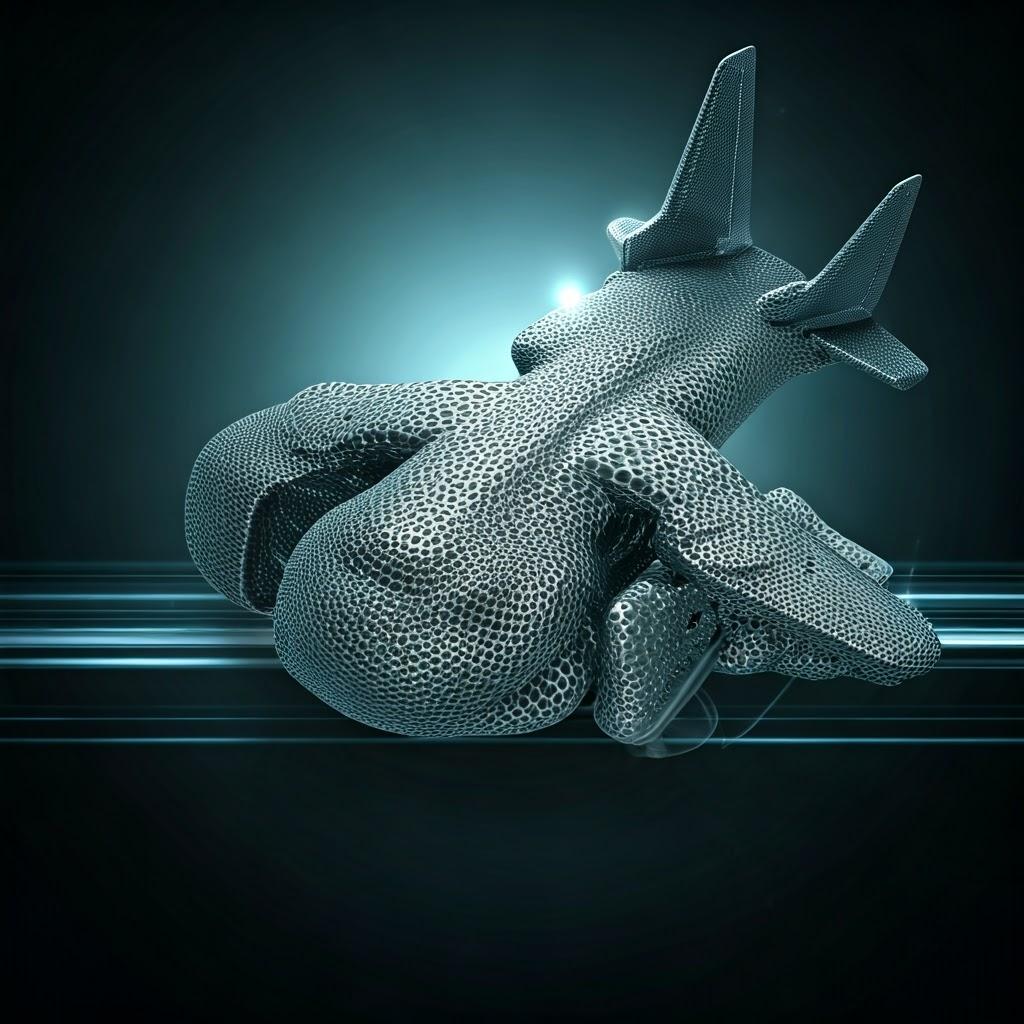
Design Optimization for 3D Printed Aerospace Leading Edges
Designing for metal 3D printing requires a different mindset compared to traditional manufacturing. To fully leverage the capabilities of additive manufacturing and create high-performance, lightweight aerospace leading edges, several key design considerations must be taken into account:
- Topology Optimization: This computational method allows engineers to optimize the material distribution within a given design space based on specific load conditions and constraints. By removing unnecessary material while maintaining structural integrity, topology optimization can lead to significant weight reductions in leading edges. Metal 3D printing excels at producing these complex, organic-like structures.
- Lattice Structures: Incorporating internal lattice structures within the leading edge design is another effective way to reduce weight without compromising strength. These intricate networks of interconnected struts and nodes provide excellent stiffness and energy absorption while using significantly less material than solid structures. Various lattice types, such as gyroid, diamond, and cubic, can be tailored to specific performance requirements.
- Conformal Cooling Channels: For leading edges that may experience significant thermal loads due to air friction, integrating conformal cooling channels within the design can be crucial for thermal management. Metal 3D printing allows for the creation of these complex internal channels that follow the contours of the part, providing efficient and uniform cooling that is difficult or impossible to achieve with traditional methods.
- Feature Integration: Additive manufacturing enables the integration of multiple functionalities into a single leading edge component. This could include integrated mounting features, sensor housings, or even internal channels for fluid or air flow. Reducing the number of individual parts simplifies assembly and can further contribute to weight savings.
- Orientation and Support Structures: The orientation of the part during the 3D printing process significantly impacts surface finish, support structure requirements, and build time. Careful consideration of the optimal orientation can minimize the need for extensive post-processing and ensure the best possible part quality. Support structures are often necessary to prevent warping and ensure the stability of overhanging features. Designing with self-supporting angles and minimizing overhangs can reduce the amount of support material required.
- Wall Thickness and Ribbing: Optimizing wall thickness and incorporating internal ribs or stiffeners can enhance the structural rigidity of lightweight leading edges without adding excessive weight. The minimum wall thickness achievable is dependent on the chosen metal powder and printing process.
- Surface Finish Considerations: The as-printed surface finish of metal 3D printed parts can vary depending on the printing process and material. Designing with this in mind and planning for necessary post-processing steps (e.g., polishing, machining) is crucial for achieving the desired aerodynamic performance and surface quality.
Metal3DP‘s expertise in design for additive manufacturing (DfAM) ensures that our customers can fully capitalize on the benefits of metal 3D printing. Our team of experienced engineers provides guidance on optimizing designs for lightweighting, functionality integration, and efficient production using our state-of-the-art SEBM printers and high-quality metal powders. We help organizations implement 3D printing and accelerate digital manufacturing transformations, as highlighted on our About Us page.
Achieving Precision: Tolerance, Surface Finish, and Dimensional Accuracy in 3D Printed Leading Edges
In the aerospace industry, precision is paramount. Components like leading edges must adhere to strict tolerance requirements, possess the necessary surface finish for optimal aerodynamic performance, and maintain accurate dimensions to ensure proper fit and functionality. Metal 3D printing, when executed with expertise and using high-quality equipment and materials, can achieve impressive levels of precision:
- Dimensional Accuracy: The dimensional accuracy achievable with metal 3D printing depends on several factors, including the printing technology (e.g., LPBF, EBPBF), the material being used, the size and complexity of the part, and the calibration and maintenance of the printer. Metal3DP‘s printers are engineered for high accuracy, ensuring that printed leading edges meet the stringent dimensional requirements of aerospace applications.
- Tolerance: Tolerances in metal 3D printing refer to the allowable variation in the dimensions of a printed part. While additive manufacturing can achieve tight tolerances, these are typically process and geometry dependent. Careful design, optimized build parameters, and post-processing techniques like precision machining can further refine tolerances to meet specific application needs.
- Surface Finish: The as-printed surface finish in metal 3D printing is influenced by factors such as the powder particle size, layer thickness, and build orientation. Typically, the surface roughness is higher compared to machined surfaces. For aerospace leading edges, a smooth surface finish is crucial for minimizing drag and ensuring optimal aerodynamic performance. Post-processing methods like abrasive blasting, polishing, and chemical etching are commonly employed to achieve the desired surface finish.
The table below provides a general overview of the typical achievable precision with metal 3D printing:
Feature | Typical Achievable Range | Factors Influencing Precision |
---|---|---|
Dimensional Accuracy | ± 0.1 mm to ± 0.02 mm (can be tighter with optimization) | Printer calibration, material, part geometry, build parameters |
Tolerance | ± 0.2 mm to ± 0.05 mm (can be tighter with post-processing) | Printing process, material, part size and complexity |
Surface Roughness (Ra) | 5-20 µm (can be improved with post-processing) | Powder size, layer thickness, build orientation |
Export to Sheets
Metal3DP understands the critical importance of precision in aerospace manufacturing. We leverage our advanced printing technology, coupled with our expertise in material science and process optimization, to produce metal 3D printed leading edges that meet demanding tolerance and surface finish requirements. We also offer a range of post-processing services to further enhance the precision and surface quality of printed parts.
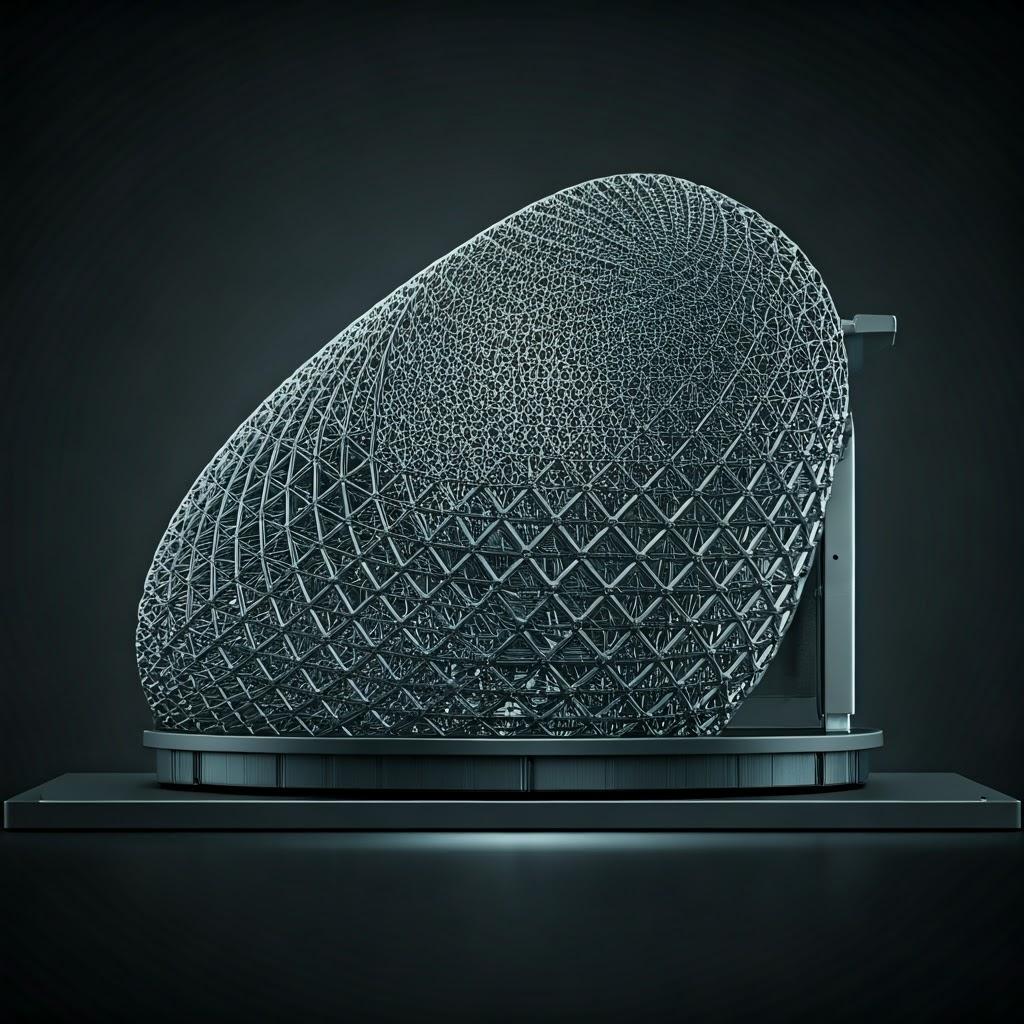
Post-Processing Techniques for Aerospace-Grade Leading Edges
While metal 3D printing offers significant advantages in creating complex geometries, post-processing is often necessary to achieve the final desired properties, surface finish, and dimensional accuracy for aerospace leading edges. Common post-processing techniques include:
- Support Removal: After the printing process, support structures that were used to stabilize overhanging features must be carefully removed. This can be done manually using hand tools or through automated methods like machining or chemical dissolution, depending on the material and support type.
- Heat Treatment: Heat treatment processes are often required to relieve internal stresses that may have developed during the rapid cooling cycles of the 3D printing process and to achieve the desired mechanical properties (e.g., hardness, tensile strength) of the material. Specific heat treatment cycles are tailored to the alloy being used.
- Hot Isostatic Pressing (HIP): HIP is a process that involves subjecting the 3D printed part to high pressure and temperature in an inert gas environment. This process helps to eliminate internal porosity, increase density, and improve the overall mechanical properties and fatigue resistance – critical for aerospace applications.
- CNC Machining: For achieving very tight tolerances and specific surface finishes on critical features, CNC machining can be employed as a secondary process after 3D printing. This allows for the precise finishing of interfaces, mounting points, and aerodynamic surfaces.
- Surface Finishing (Polishing, Abrasive Blasting, Coating): To achieve the required surface finish for optimal aerodynamic performance and corrosion resistance, various surface treatment methods can be used. These include polishing, abrasive blasting, and the application of protective coatings such as anodizing or painting.
Metal3DP offers comprehensive post-processing services to ensure that our 3D printed aerospace leading edges meet the most stringent industry standards. Our expertise in heat treatment, HIP, CNC machining, and various surface finishing techniques allows us to deliver готовые to-use components with the required mechanical properties, dimensional accuracy, and surface finish. We understand the critical role of each post-processing step in achieving the final performance characteristics of aerospace parts.
Overcoming Common Challenges in 3D Printing Lightweight Aerospace Components
While metal 3D printing offers numerous advantages, there are also potential challenges that need to be addressed to ensure the successful fabrication of lightweight aerospace components like leading edges:
- Warping and Distortion: Thermal stresses during the printing process can lead to warping and distortion, particularly in large or complex parts. Optimizing part orientation, using appropriate support structures, and carefully controlling the build parameters can mitigate these issues.
- Residual Stresses: The rapid heating and cooling cycles inherent in some metal 3D printing processes can induce residual stresses within the part. Heat treatment is crucial for relieving these stresses and preventing premature failure.
- Porosity: Internal porosity can compromise the mechanical properties and fatigue resistance of 3D printed parts. Optimizing printing parameters, using high-quality metal powders (like those offered by Metal3DP), and employing post-processing techniques like HIP can minimize porosity.
- Support Structure Removal: Removing support structures from complex geometries can be challenging and may leave surface imperfections. Designing parts with self-supporting angles and optimizing support placement can simplify this process.
- Surface Finish: Achieving a smooth surface finish directly off the printer can be difficult. Post-processing steps like polishing or machining are often necessary to meet the aerodynamic requirements of leading edges.
- Material Qualification and Certification: For critical aerospace applications, the 3D printing process and materials must undergo rigorous qualification and certification processes to ensure safety and reliability. Metal3DP is committed to providing high-quality metal powders and utilizing robust printing processes to meet the stringent requirements of the aerospace industry.
By understanding these potential challenges and implementing appropriate design strategies, process controls, and post-processing techniques, it is possible to consistently produce high-quality, lightweight aerospace leading edges using metal 3D printing. Metal3DP‘s expertise in the entire additive manufacturing workflow, from material selection to post-processing, ensures that our customers can overcome these challenges and realize the full potential of metal 3D printing for their aerospace applications.
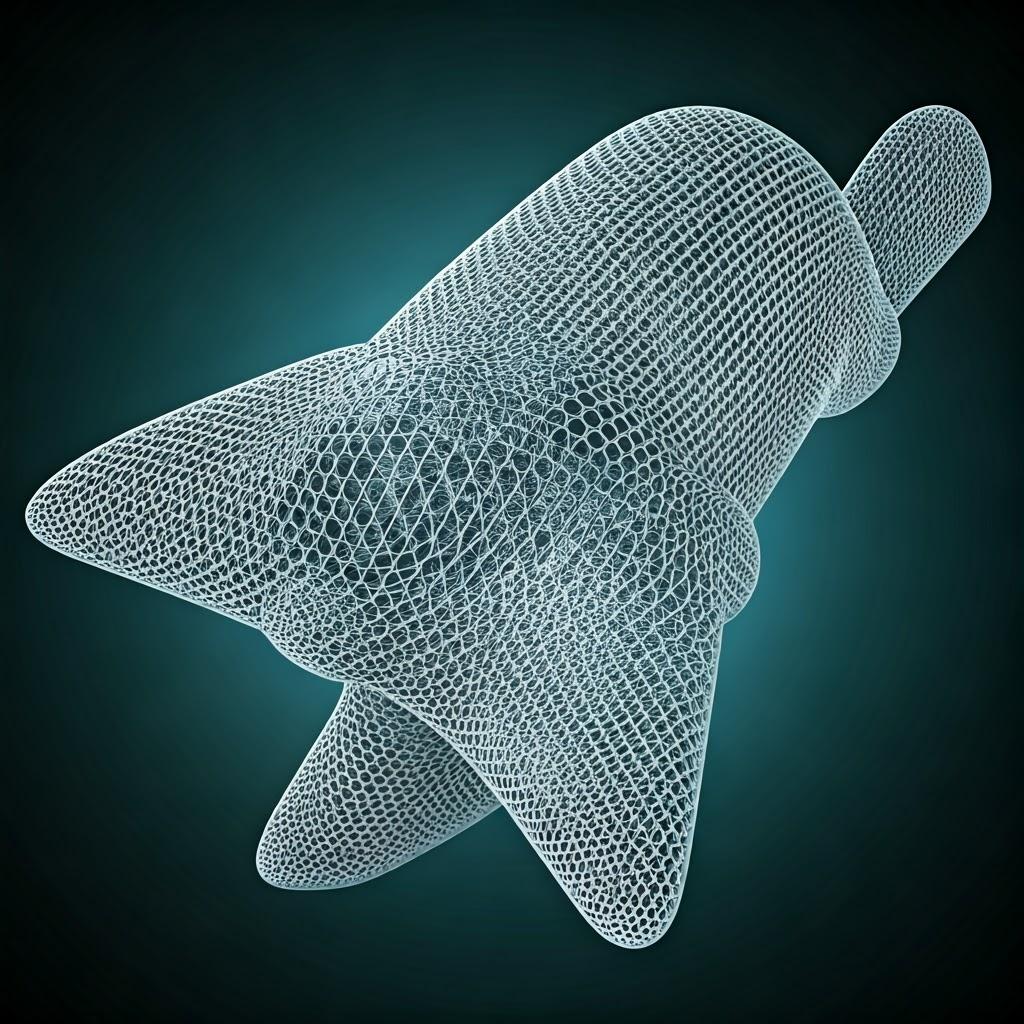
How to Choose the Right Metal 3D Printing Service Provider for Aerospace Parts
Selecting the right metal 3D printing service provider is a critical decision, especially for demanding aerospace applications like lightweight leading edges. A reliable partner will possess the expertise, equipment, and quality control systems necessary to deliver high-performance parts that meet stringent industry standards. Here are key factors to consider when evaluating potential suppliers:
- Material Capabilities: Ensure the provider has experience working with the specific aerospace-grade metal powders required for your application, such as Ti-6Al-4V and AlSi10Mg. They should be knowledgeable about the material properties and have optimized printing parameters for these alloys. Metal3DP offers a wide range of high-quality metal powders, including those recommended for aerospace leading edges.
- Printing Technology: Different metal 3D printing technologies (e.g., LPBF, EBPBF) have varying strengths and limitations in terms of accuracy, surface finish, and material compatibility. Understand the provider’s technology and whether it aligns with the requirements of your leading edge application. Metal3DP utilizes advanced SEBM printers known for their accuracy and reliability. You can learn more about our printing methods at Printing Methods.
- Quality Assurance and Certifications: Aerospace components demand the highest levels of quality and traceability. Inquire about the provider’s quality management systems, certifications (e.g., AS9100), and inspection processes. They should have robust procedures in place for material testing, dimensional inspection, and non-destructive testing.
- Design for Additive Manufacturing (DfAM) Expertise: A good service provider will offer guidance and support in optimizing your designs for metal 3D printing. Their engineers should have expertise in DfAM principles, including topology optimization, lattice structures, and minimizing support requirements. Metal3DP‘s experienced team provides comprehensive application development services to assist with design optimization.
- Post-Processing Capabilities: As discussed earlier, post-processing is often crucial for aerospace parts. Ensure the provider offers the necessary post-processing services, such as support removal, heat treatment, HIP, CNC machining, and surface finishing, to meet your specifications.
- Experience and Track Record: Look for a provider with a proven track record of successfully producing metal 3D printed parts for the aerospace industry or other demanding sectors. Review case studies and testimonials to assess their capabilities and customer satisfaction.
- Lead Times and Production Capacity: Understand the provider’s typical lead times for similar projects and their production capacity to ensure they can meet your delivery requirements, especially for larger production volumes.
- Communication and Collaboration: Effective communication and a collaborative approach are essential for a successful partnership. 1 Choose a provider who is responsive, transparent, and willing to work closely with your team. 1. medium.com medium.com
By carefully evaluating these factors, you can select a metal 3D printing service provider that can reliably produce high-quality, lightweight leading edges for your aerospace applications.
Understanding Cost Factors and Lead Times for 3D Printed Leading Edges
The cost and lead time for metal 3D printed aerospace leading edges are influenced by several interconnected factors. Understanding these can help in project planning and budgeting:
Cost Factors:
- Material Costs: The cost of the metal powder is a significant factor. Aerospace-grade alloys like Ti-6Al-4V can be expensive. Material waste, although generally lower in additive manufacturing compared to subtractive methods, also contributes to the overall material cost.
- Build Time: The duration of the printing process directly impacts the cost. Longer build times consume more machine time and energy. Factors influencing build time include part size, complexity, build volume utilization, and layer thickness.
- Post-Processing Costs: The extent of post-processing required (e.g., support removal, heat treatment, machining, surface finishing) significantly affects the final cost. Complex geometries often necessitate more extensive support removal and potentially more intricate post-processing steps.
- Equipment and Labor Costs: The cost of operating and maintaining the 3D printing equipment, as well as the labor costs associated with design, printing, and post-processing, are factored into the overall price.
- Quantity and Volume: While metal 3D printing can be cost-effective for low to medium volumes and customized parts, higher production volumes may benefit from economies of scale.
Lead Times:
- Design and Engineering: The time required for design optimization for additive manufacturing, material selection, and process planning influences the overall lead time.
- Printing Time: As mentioned earlier, the build time is a key component of the lead time.
- Post-Processing Time: Each post-processing step adds to the total lead time. Complex parts requiring multiple post-processing stages will have longer lead times.
- Quality Control and Inspection: Thorough quality control and inspection processes are essential for aerospace parts and contribute to the overall lead time.
- Shipping and Logistics: The time required for packaging and shipping the final parts also needs to be considered.
Metal3DP is committed to providing transparent and competitive pricing for our metal 3D printing services. We work closely with our customers to optimize designs and production processes to minimize costs and lead times while maintaining the highest standards of quality for aerospace leading edges. Contact us to discuss your specific project requirements and receive a detailed quotation.
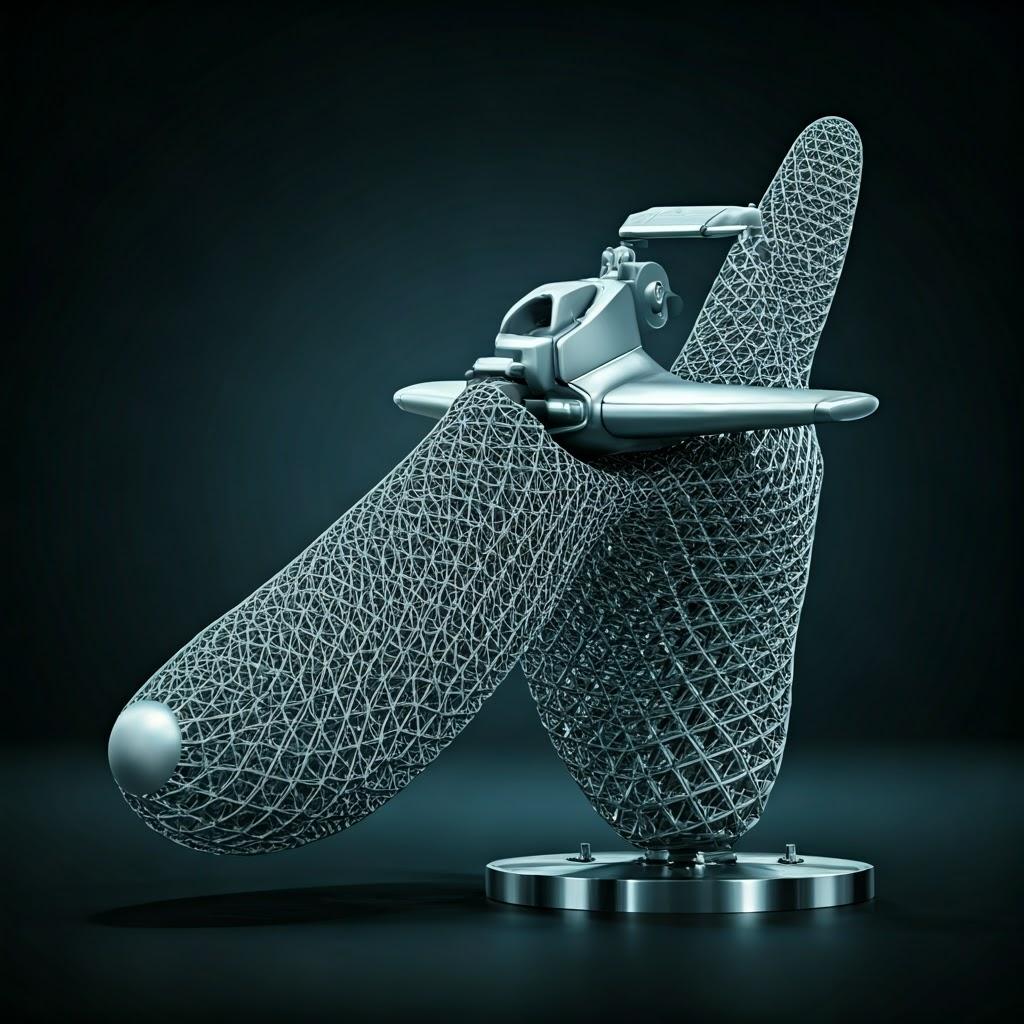
Frequently Asked Questions (FAQ)
Here are some frequently asked questions about using metal 3D printing for aerospace leading edges:
Q: Can metal 3D printed leading edges meet the stringent strength requirements of aerospace applications? A: Yes, when the appropriate high-performance metal powders (such as Ti-6Al-4V), optimized design, and proper post-processing techniques (like HIP and heat treatment) are employed, metal 3D printed leading edges can meet or even exceed the strength and durability requirements of aerospace applications. Metal3DP utilizes advanced materials and processes to ensure the structural integrity of printed parts.
Q: What is the typical surface finish achievable on metal 3D printed leading edges, and is it suitable for aerodynamic performance? A: The as-printed surface finish is typically rougher than machined surfaces. However, various post-processing techniques like polishing, abrasive blasting, and coating can be used to achieve the smooth surface finish required for optimal aerodynamic performance. Metal3DP offers a range of surface finishing options to meet specific application needs.
Q: Is metal 3D printing cost-effective for producing aerospace leading edges compared to traditional methods? A: For low to medium volumes, complex geometries, and customized designs, metal 3D printing can be more cost-effective than traditional manufacturing methods due to reduced material waste, tooling costs, and assembly requirements. For very high volumes, traditional methods may still be more economical.
Q: What are the common materials used for 3D printing lightweight aerospace leading edges? A: Common materials include titanium alloys (like Ti-6Al-4V) known for their high strength-to-weight ratio and corrosion resistance, and aluminum alloys (like AlSi10Mg) favored for their lightweight properties and good thermal conductivity. Metal3DP offers a comprehensive selection of these and other high-performance metal powders. You can explore our range of metal powders on our Product Page.
Conclusion – The Future of Aerospace Leading Edges with Metal 3D Printing
Metal 3D printing is revolutionizing the design and manufacturing of lightweight leading edges for the aerospace industry. Its ability to enable complex geometries, reduce weight through topology optimization and lattice structures, and utilize high-performance materials like Ti-6Al-4V and AlSi10Mg offers significant advantages over traditional manufacturing methods. These benefits translate to improved fuel efficiency, enhanced aircraft performance, and faster innovation cycles.
Metal3DP is proud to be at the forefront of this transformation, providing cutting-edge metal 3D printing equipment, high-quality metal powders, and comprehensive application development services. Our commitment to accuracy, reliability, and material expertise empowers aerospace companies to push the boundaries of design and achieve new levels of performance in their leading edge components.
As the aerospace industry continues to demand lighter, more efficient, and higher-performing aircraft, metal 3D printing will undoubtedly play an increasingly vital role in the production of critical components like leading edges. By embracing the design freedom and manufacturing capabilities of additive manufacturing, the future of aerospace innovation is poised for remarkable advancements. Contact Metal3DP today to explore how our solutions can power your organization’s additive manufacturing goals and contribute to the next generation of aerospace technology.
Share On
MET3DP Technology Co., LTD is a leading provider of additive manufacturing solutions headquartered in Qingdao, China. Our company specializes in 3D printing equipment and high-performance metal powders for industrial applications.
Inquiry to get best price and customized Solution for your business!
Related Articles
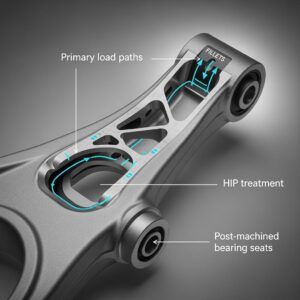
Metal 3D Printing for U.S. Automotive Lightweight Structural Brackets and Suspension Components
Read More »About Met3DP
Recent Update
Our Product
CONTACT US
Any questions? Send us message now! We’ll serve your request with a whole team after receiving your message.