Lifecycle of Metal Powder
Table of Contents
Metal powder is a versatile material used in various industries, from aerospace to automotive to medical devices. Understanding its lifecycle helps industries optimize processes, improve product quality, and reduce costs. This article delves into the lifecycle of metal powder, exploring its types, composition, properties, applications, specifications, suppliers, and pricing. We’ll also compare the advantages and disadvantages of different metal powder models. Let’s dive in!
Overview of the Lifecycle of Metal Powder
The lifecycle of metal powder encompasses several stages: production, processing, usage, and recycling. Each stage involves specific techniques and considerations to ensure the powder meets the desired quality and performance standards.
Stages of the Metal Powder Lifecycle
- Production: Metal powders are produced using various methods, including atomization, reduction, electrolysis, and mechanical comminution. Each method has its own advantages and is selected based on the required powder properties.
- Processing: After production, metal powders undergo processes like blending, compaction, and sintering to create final products. Additive manufacturing, also known as 3D printing, is an emerging process that utilizes metal powders.
- Usage: Metal powders are used in various applications, from creating structural components to specialized coatings. Their properties, such as particle size and distribution, influence the performance of the final product.
- Recycling: Recycling metal powders helps reduce waste and resource consumption. Techniques like sieving and magnetic separation are employed to recover and reuse powders.
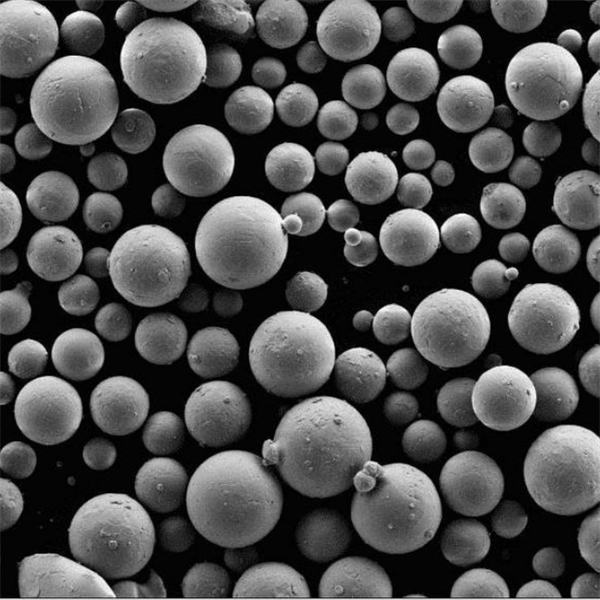
Types, Composition, Properties, and Characteristics of Metal Powder
Metal powders come in various types, each with unique compositions and properties. The table below summarizes some common metal powder types and their characteristics:
Type | Composition | Properties | Characteristics |
---|---|---|---|
Iron | Pure iron or alloyed with carbon | High strength, magnetic properties | Used in automotive parts, machinery components |
Aluminum | Pure aluminum or alloyed with elements like silicon and magnesium | Lightweight, corrosion-resistant, high thermal conductivity | Used in aerospace, automotive, and electronics |
Copper | Pure copper or alloyed with zinc, tin | High electrical and thermal conductivity | Used in electrical components, heat exchangers |
Titanium | Pure titanium or alloyed with aluminum, vanadium | High strength-to-weight ratio, corrosion-resistant | Used in aerospace, medical implants, sports equipment |
Nickel | Pure nickel or alloyed with chromium, molybdenum | High corrosion and heat resistance | Used in superalloys, coatings, batteries |
Cobalt | Pure cobalt or alloyed with chromium, tungsten | High wear resistance, magnetic properties | Used in cutting tools, aerospace, medical implants |
Stainless Steel | Alloy of iron, chromium, nickel | Corrosion-resistant, high strength | Used in medical devices, kitchenware, construction |
Zinc | Pure zinc or alloyed with aluminum, copper | Corrosion-resistant, low melting point | Used in galvanization, die-casting |
Magnesium | Pure magnesium or alloyed with aluminum, zinc | Lightweight, high strength-to-weight ratio | Used in automotive, aerospace, electronics |
Tungsten | Pure tungsten or alloyed with nickel, iron | High melting point, high density | Used in cutting tools, electronics, aerospace |
Detailed Descriptions of Specific Metal Powder Models
Let’s explore specific metal powder models to understand their unique properties and applications:
- Iron Powder (Fe-300L): This high-purity iron powder is commonly used in powder metallurgy for automotive components. It offers excellent compressibility and sintered strength, making it ideal for producing high-density parts.
- Aluminum Powder (Al-6061): Known for its lightweight and corrosion resistance, Al-6061 aluminum powder is used in aerospace and automotive applications. It provides good mechanical properties and is suitable for additive manufacturing.
- Copper Powder (Cu-123): With its high electrical and thermal conductivity, Cu-123 copper powder is widely used in electrical components and heat exchangers. It ensures efficient energy transfer and durability.
- Titanium Powder (Ti-64): Ti-64 is an alloy of titanium, aluminum, and vanadium, known for its high strength-to-weight ratio. It is used in aerospace and medical implants, providing excellent biocompatibility and corrosion resistance.
- Nickel Powder (Ni-625): This nickel-chromium-molybdenum alloy powder offers high corrosion and heat resistance, making it suitable for superalloys and coatings in high-temperature environments.
- Cobalt Powder (Co-21): Co-21 cobalt powder, alloyed with chromium and tungsten, is used in cutting tools and medical implants. It provides high wear resistance and excellent biocompatibility.
- Stainless Steel Powder (316L): 316L stainless steel powder is known for its corrosion resistance and high strength. It is used in medical devices, kitchenware, and construction applications.
- Zinc Powder (Zn-500): Zn-500 zinc powder is utilized in galvanization and die-casting due to its corrosion resistance and low melting point. It ensures long-lasting protective coatings.
- Magnesium Powder (Mg-AZ31): Mg-AZ31 magnesium powder offers a lightweight solution with a high strength-to-weight ratio. It is used in automotive and aerospace applications where weight reduction is crucial.
- Tungsten Powder (W-99.95): W-99.95 tungsten powder, with its high melting point and density, is used in cutting tools, electronics, and aerospace for applications requiring extreme durability.
Applications of Metal Powder
Metal powders have diverse applications across various industries. The table below highlights some key uses of different metal powders:
Type | Applications |
---|---|
Iron | Automotive parts, machinery components, sintered products |
Aluminum | Aerospace parts, automotive components, electronics |
Copper | Electrical components, heat exchangers, conductive inks |
Titanium | Aerospace parts, medical implants, sports equipment |
Nickel | Superalloys, coatings, batteries |
Cobalt | Cutting tools, aerospace components, medical implants |
Stainless Steel | Medical devices, kitchenware, construction materials |
Zinc | Galvanization, die-casting, corrosion-resistant coatings |
Magnesium | Automotive parts, aerospace components, electronic devices |
Tungsten | Cutting tools, electronics, aerospace components |
Specifications, Sizes, Grades, and Standards of Metal Powder
Different metal powders have specific specifications, sizes, grades, and standards that define their quality and suitability for various applications. The table below provides an overview:
Type | Specifications | Sizes | Grades | Standards |
---|---|---|---|---|
Iron | ASTM B783, MPIF 35 | 20-150 µm | Fe-300L, Fe-400L | ISO 4490 |
Aluminum | ASTM B928, AMS 4225 | 10-200 µm | Al-6061, Al-7075 | ISO 8060 |
Copper | ASTM B170, MPIF 60 | 15-100 µm | Cu-123, Cu-140 | ISO 4492 |
Titanium | ASTM B348, AMS 4999 | 20-150 µm | Ti-64, Ti-6242 | ISO 5832 |
Nickel | ASTM B330, AMS 5390 | 10-100 µm | Ni-625, Ni-718 | ISO 6284 |
Cobalt | ASTM F75, MPIF 29 | 10-50 µm | Co-21, Co-25 | ISO 5832-4 |
Stainless Steel | ASTM A276, MPIF 85 | 10-100 µm | 316L, 304L | ISO 5832-1 |
Zinc | ASTM B86, MPIF 60 | 20-200 µm | Zn-500, Zn-700 | ISO 301 |
Magnesium | ASTM B951, AMS 4377 | 15-150 µm | Mg-AZ31, Mg-ZK60 | ISO 2626 |
Tungsten | ASTM B777, AMS 7725 | 5-50 µm | W-99.95, W-93 | ISO 4480 |
Suppliers and Pricing of Metal Powder
Finding reliable suppliers and understanding the pricing of metal powders is crucial for industries. The table below lists some prominent suppliers and their pricing for various metal powders:
Type | Suppliers | Pricing (USD/kg) |
---|---|---|
Iron | Höganäs, GKN, Rio Tinto | $10 – $20 |
Aluminum | Alcoa, ECKA Granules,Valimet | $20 – $50 |
Copper | SCM Metal Products, GGP Metal Powder | $15 – $40 |
Titanium | Praxair, AP&C, TLS Technik | $100 – $300 |
Nickel | Vale, American Elements, MMC Norilsk | $30 – $80 |
Cobalt | Freeport Cobalt, Umicore, Nornickel | $50 – $120 |
Stainless Steel | Carpenter, Sandvik, Oerlikon | $25 – $60 |
Zinc | EverZinc, Grillo-Werke, U.S. Zinc | $5 – $15 |
Magnesium | Luxfer, Rima, POSCO | $20 – $45 |
Tungsten | Global Tungsten & Powders, Buffalo Tungsten | $60 – $150 |
Advantages and Disadvantages of Metal Powder Models
Each metal powder model has its own set of advantages and disadvantages. The table below compares these factors for various metal powders:
Type | Advantages | Disadvantages |
---|---|---|
Iron | High strength, magnetic properties, cost-effective | Susceptible to corrosion |
Aluminum | Lightweight, corrosion-resistant, high conductivity | Lower strength compared to some alloys |
Copper | High electrical and thermal conductivity | Expensive, prone to oxidation |
Titanium | High strength-to-weight ratio, biocompatible | Expensive, difficult to machine |
Nickel | Corrosion and heat resistance, versatile | Expensive, heavy |
Cobalt | Wear resistance, magnetic properties | Expensive, limited availability |
Stainless Steel | Corrosion-resistant, high strength | Expensive, heavy |
Zinc | Corrosion-resistant, low melting point | Lower mechanical strength |
Magnesium | Lightweight, high strength-to-weight ratio | Highly reactive, flammable in fine powder form |
Tungsten | High melting point, high density | Expensive, difficult to work with |
Detailed Comparisons of Metal Powder Models
Iron Powder (Fe-300L) vs. Aluminum Powder (Al-6061)
Fe-300L:
- Advantages: High strength, cost-effective, good compressibility.
- Disadvantages: Susceptible to corrosion, heavier.
Al-6061:
- Advantages: Lightweight, corrosion-resistant, good mechanical properties.
- Disadvantages: Lower strength compared to iron, more expensive.
Copper Powder (Cu-123) vs. Titanium Powder (Ti-64)
Cu-123:
- Advantages: Excellent electrical and thermal conductivity.
- Disadvantages: Expensive, prone to oxidation.
Ti-64:
- Advantages: High strength-to-weight ratio, biocompatible.
- Disadvantages: Very expensive, difficult to machine.
Nickel Powder (Ni-625) vs. Cobalt Powder (Co-21)
Ni-625:
- Advantages: High corrosion and heat resistance, versatile applications.
- Disadvantages: Heavy, expensive.
Co-21:
- Advantages: High wear resistance, excellent for cutting tools.
- Disadvantages: Limited availability, very expensive.
Stainless Steel Powder (316L) vs. Zinc Powder (Zn-500)
316L:
- Advantages: Corrosion-resistant, high strength.
- Disadvantages: Expensive, heavy.
Zn-500:
- Advantages: Corrosion-resistant, cost-effective.
- Disadvantages: Lower mechanical strength.
Magnesium Powder (Mg-AZ31) vs. Tungsten Powder (W-99.95)
Mg-AZ31:
- Advantages: Lightweight, high strength-to-weight ratio.
- Disadvantages: Highly reactive, flammable in powder form.
W-99.95:
- Advantages: High melting point, very dense.
- Disadvantages: Expensive, challenging to work with.
FAQ
Question | Answer |
---|---|
What is metal powder? | Metal powder consists of finely divided particles of metal used in various industrial applications. |
How is metal powder produced? | Metal powder is produced through methods like atomization, reduction, electrolysis, and mechanical comminution. |
What are the applications of metal powder? | Metal powders are used in automotive parts, aerospace components, medical devices, coatings, and more. |
What are the advantages of using metal powder? | Advantages include high precision, material efficiency, and the ability to produce complex geometries. |
Can metal powder be recycled? | Yes, metal powders can be recycled using techniques like sieving and magnetic separation. |
What factors should be considered when selecting metal powder? | Factors include the powder’s composition, particle size, shape, and the specific requirements of the application. |
Who are the leading suppliers of metal powder? | Leading suppliers include Höganäs, Alcoa, SCM Metal Products, Praxair, and Vale. |
What are the common standards for metal powder? | Common standards include ASTM, MPIF, and ISO specifications, which define quality and suitability for various applications. |
How does the cost of metal powder vary? | The cost varies based on the type of metal, purity, particle size, and supplier, ranging from $5 to over $300 per kg. |
What are the environmental impacts of metal powder production? | Environmental impacts include resource consumption and waste generation, but recycling and efficient production methods can mitigate these effects. |
Conclusion
The lifecycle of metal powder is a complex and multifaceted process involving production, processing, usage, and recycling. Understanding the different types, compositions, properties, and applications of metal powders helps industries optimize their processes and make informed decisions. With advancements in technology and increased focus on sustainability, the future of metal powder usage looks promising, driving innovation and efficiency across various sectors.
Share On
MET3DP Technology Co., LTD is a leading provider of additive manufacturing solutions headquartered in Qingdao, China. Our company specializes in 3D printing equipment and high-performance metal powders for industrial applications.
Inquiry to get best price and customized Solution for your business!
Related Articles
About Met3DP
Recent Update
Our Product
CONTACT US
Any questions? Send us message now! We’ll serve your request with a whole team after receiving your message.
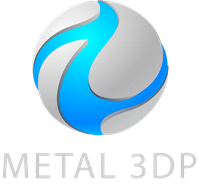
Metal Powders for 3D Printing and Additive Manufacturing